Yesterday I´ve had the pleasure to visit my new boat in the shipyard again. It have been some month with just little progress. I had slowed down the work of the shipyard due to external factors, but now it´s all on again and flank ahead. Driving to Lake Mueritz, my car was full with more electronic equipment for the boat, such as the Orca navigation hardware, the Vesper Cortex VHF and other things. Of course I was keen on seeing what the guys have done on my boat so far. But before I took a look at my boat, I noticed this „little“ parcel, ready for shipment. A huge box with a shaft sticking out:
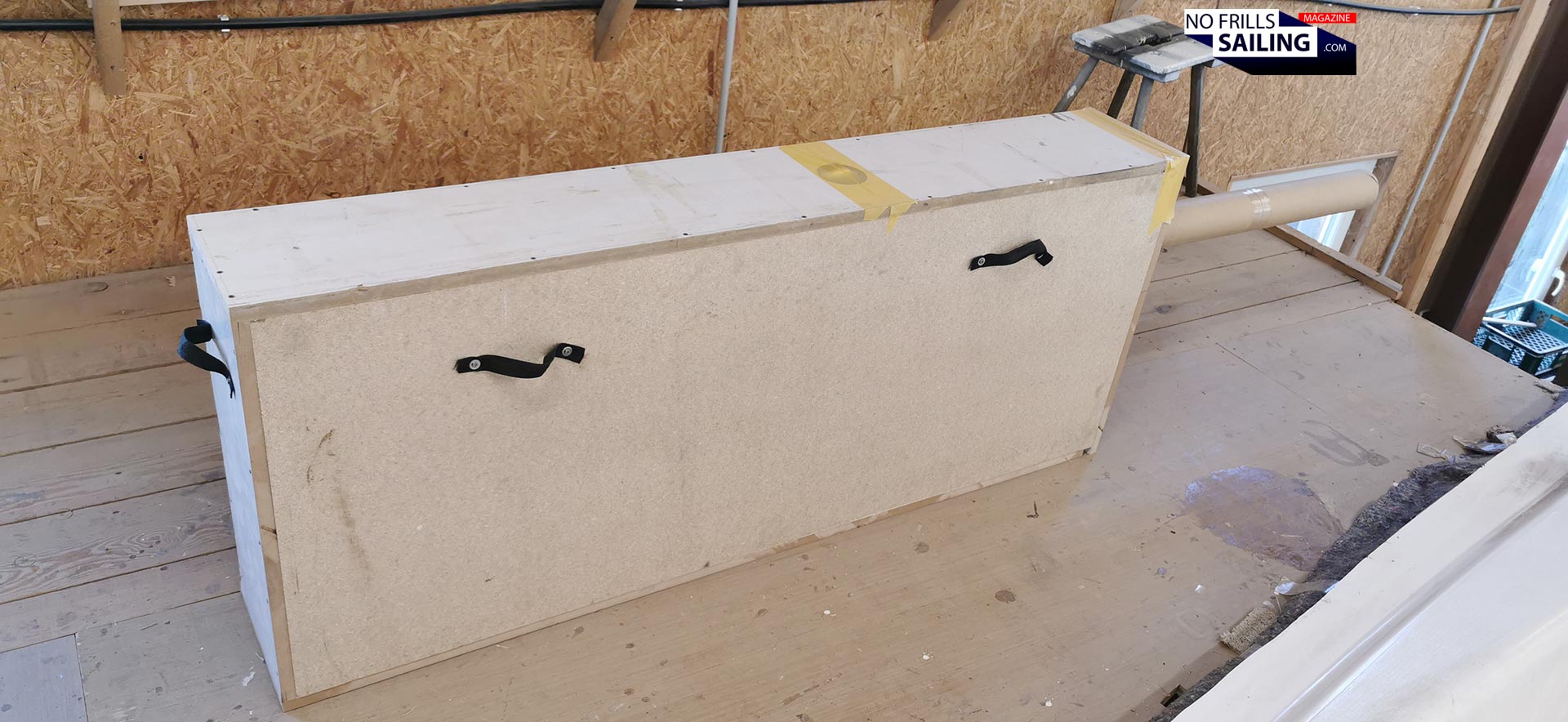
This is a rudder, of course, custom made for a Swedish Omega 42-owner who apparently needed a new one. As my shipyard has now officially launched the new website, more and more Omega 42-skippers in Europe but also around the world acknowledge the competence and special knowledge of Heiner and his team regarding this specific boat. It is really cool to see that so many fans and owners of an Omega 42 increasingly ask the guys for maintenance and spare parts. And this rudder made to be fitted into a classic Omega 42 in Sweden was the reason why the team decided to do two of them with one stroke. And this is the story of the rudder of my ALPHA.
On historic grounds
You know it, I particularly love „behind the scenes“-articles. In this I will now try to show you, dearest readers, how a boat´s rudder is made from scratch. In this first part it´s all about glassfiber works, the second part then shows how the rudder is finalized and the final, third part, will tackle the fitting, rudder bearings and the trunk construction. But let´s start at the beginning: As with everything connected to GRP boatbuilding, you first of all need a mould. Moulds are the most expensive and elaborate part of plastic boatbuilding, I´ve done a separate article on that topic explaining why, klick here. Now, for the Omega 42, Heiner has acquired all moulds related to this boat. From the big moulds to produce new hulls and decks to the smaller ones, like this:
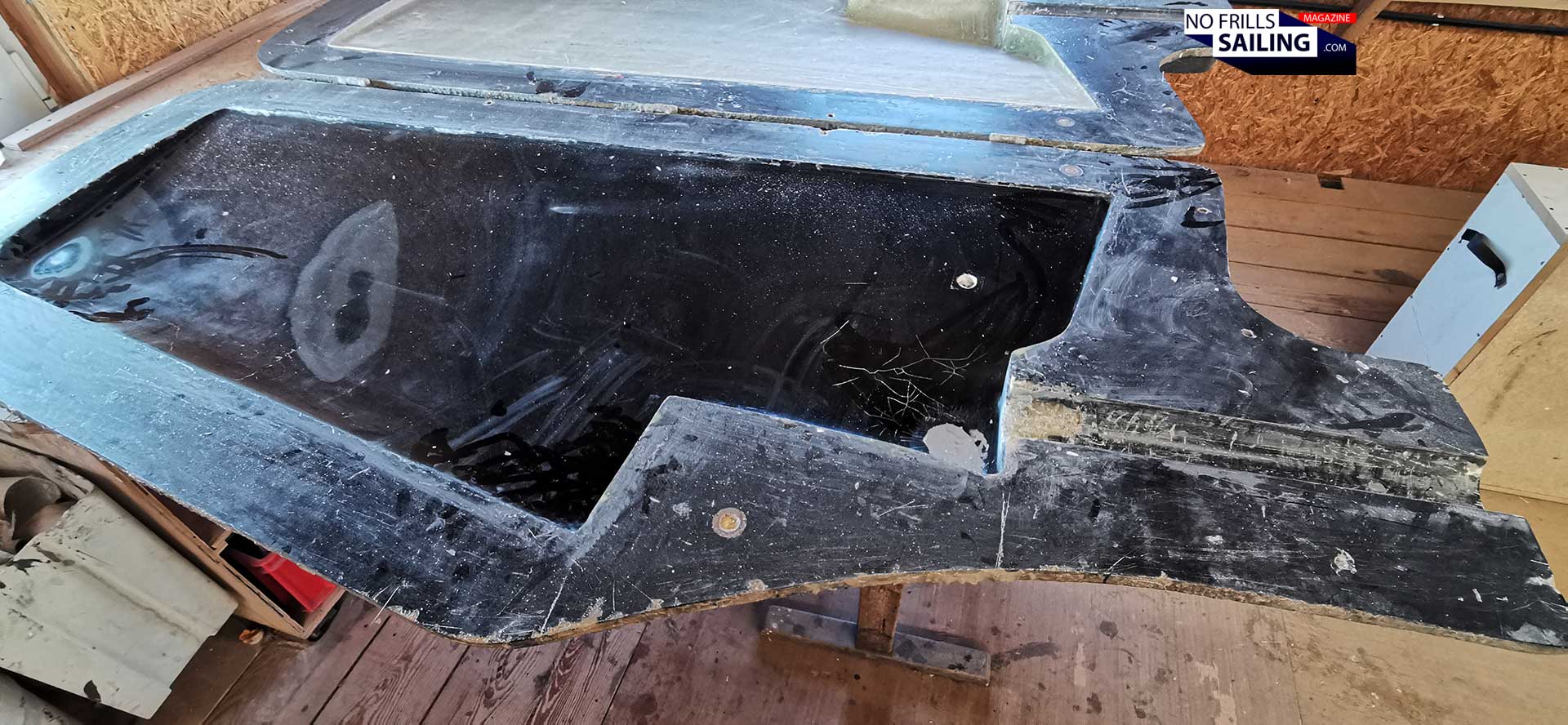
These aren´t only very expensive and rare, this is even a historic artefact: Every single rudder blade ever made for every Omega 42 sailing out there has come out of this mould. Fantastic! The historic value of this big oversized „sandwich-maker“ is apparent. The idea fascinates me, that this mould is as old as I am. I touch the inside: At least 161 rudders had been laminated with this mould. I can see some crow´s feet, little spots here and there. 45 years of boatbuilding tradition, from Vindö in Sweden to now Germany. What a fantastic journey!
Hand laminated rudder shells
A sailboat´s rudder blade usually consists of two symmetrical halves. Both are – in the case of the Omega 42 – hand laminated. The material thickness is about 0.5 to 0.8 Centimeters. As with all GRP parts, there´s a base layer of Gelcoat with a laminated stack of glassfiber mats, hardened by resin. My rudder blade halves have already been laminated and offcut material had also been taken off. I take out one of the halves.
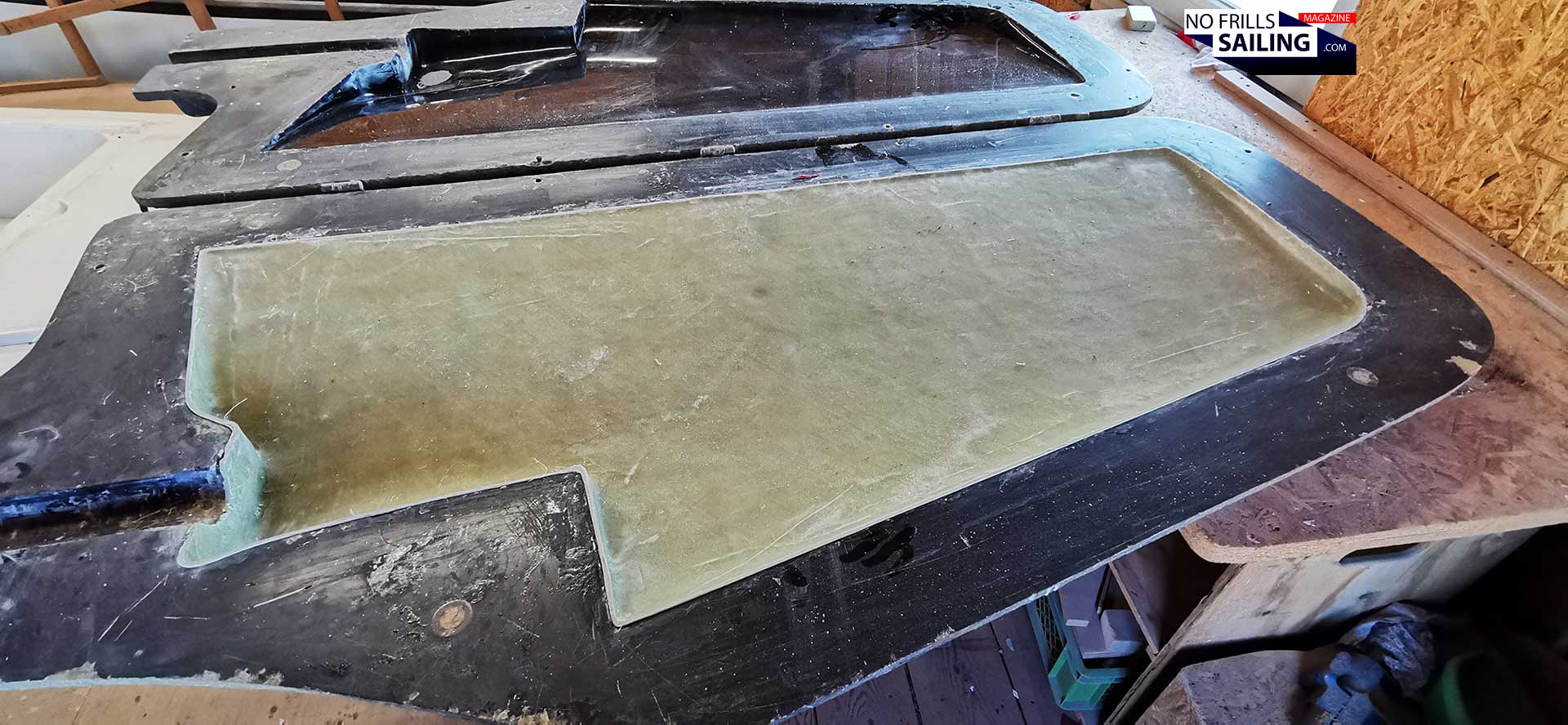
It´s completely dry. This smell of fresh GRP is just … addictive. I smile. In the end, this part will be submerged and I wonder how many changes of course this underwater wing will have to proceed in the course of ist life? You may have read my last articles about my first real regatta experience aboard the Omega 42? I was again and again amazed by the lightfooted steering capabilities, the agile and vivid response. This boat is massive! But at the helm, she feels so light as if she was a little dinghy. This agility is due to the perfectly balanced hull shape, but also due to the effectiveness of this single part: The rudder blade! The Omega 42 does neither need a very deep nor a very big rudder. Compared to modern yachts, both size and measurements of this blade are surprisingly small.
Rudder shaft and profile inlays
On the other hand, this rudder blade will be somewhat heavy in the end. Heavy in terms of its weight. This has two reasons. On the pictures below you will notice that there are moulds for the area where the rudder shaft enters the blade. I will show this in detail in the upcoming second part of this little series, but this shaft – that sticks in the mould like a lillipop – will make it particularly heavy.
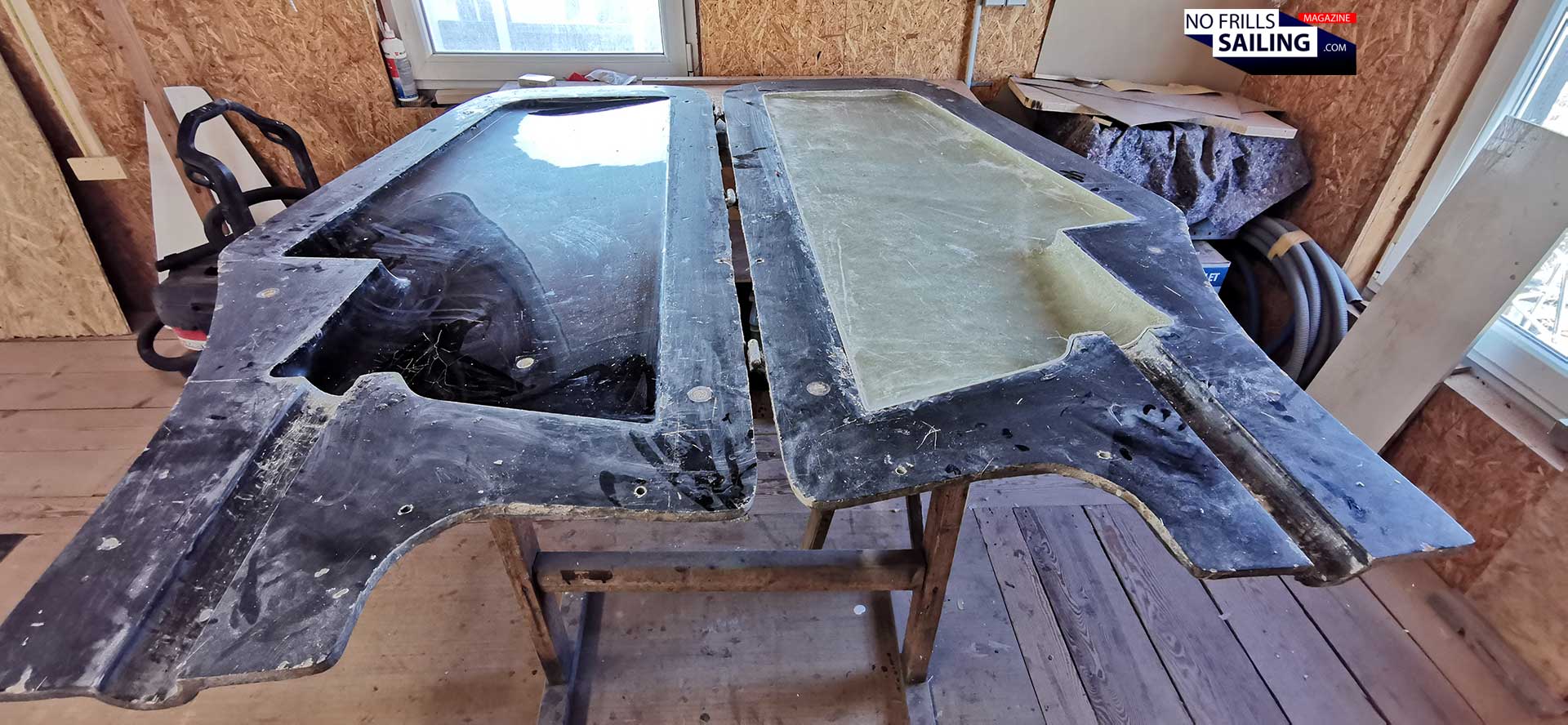
For the Omega 42 the guys decided to utilize a full-material rod for the shaft. Not an empty or hollowed pole. The reason is that we want a diameter of the shaft that is as small as possible. On the other hand, looking at the sheer forces the shaft will have to endure when making the massive fast sailing boat hold ist course, we want a shaft that is as strong as possible as well. With hollow pipes, there´s always some vibrating, possibly deformations and in worst case failure. That is why for the Omega 42 we will use a massive stainless steel rod that has been CNC-milled to perfect roundness.
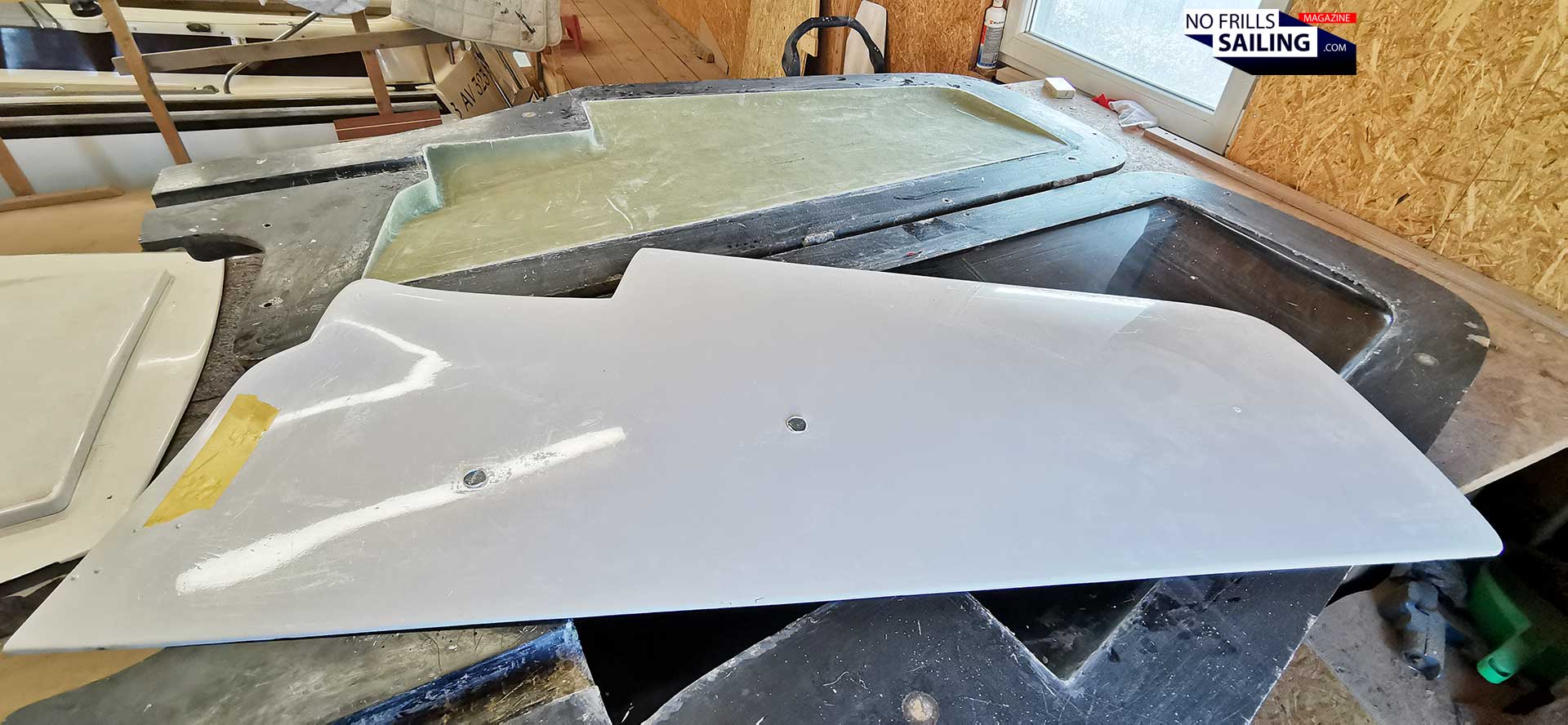
Secondly, this shaft will go very deep into the internals of the rudder blade itself. The shipyard will make two (or three, not sure if I got this info right from the boys) profiles from stainless steel, which will be welded onto the shaft. Those profiles, horizontally, will stabilize the shaft in the exact mid-point and also strengthen the blade´s stiffness. You may have noticed the two holes in the blade in the picture above? These are the inlets for the filler. This will be a two-components PU-foam, sprayed into the hollow inside of the two halves. This foam will crawl into every corner of the interior of the rudder and harden. It´s of course waterproof foam.
A quick dress rehearsal …
I can´t wait but to take out one of the rudder´s halves and take it down underneath the boat´s building frame. There, I put it in place to where the completed rudder will once be fitted: A nice little fitting check – and it looks awesome! A hull without a rudder is just incomplete to my eyes. Now, with it put there, she suddenly feels much more mature. Nice work, guys!
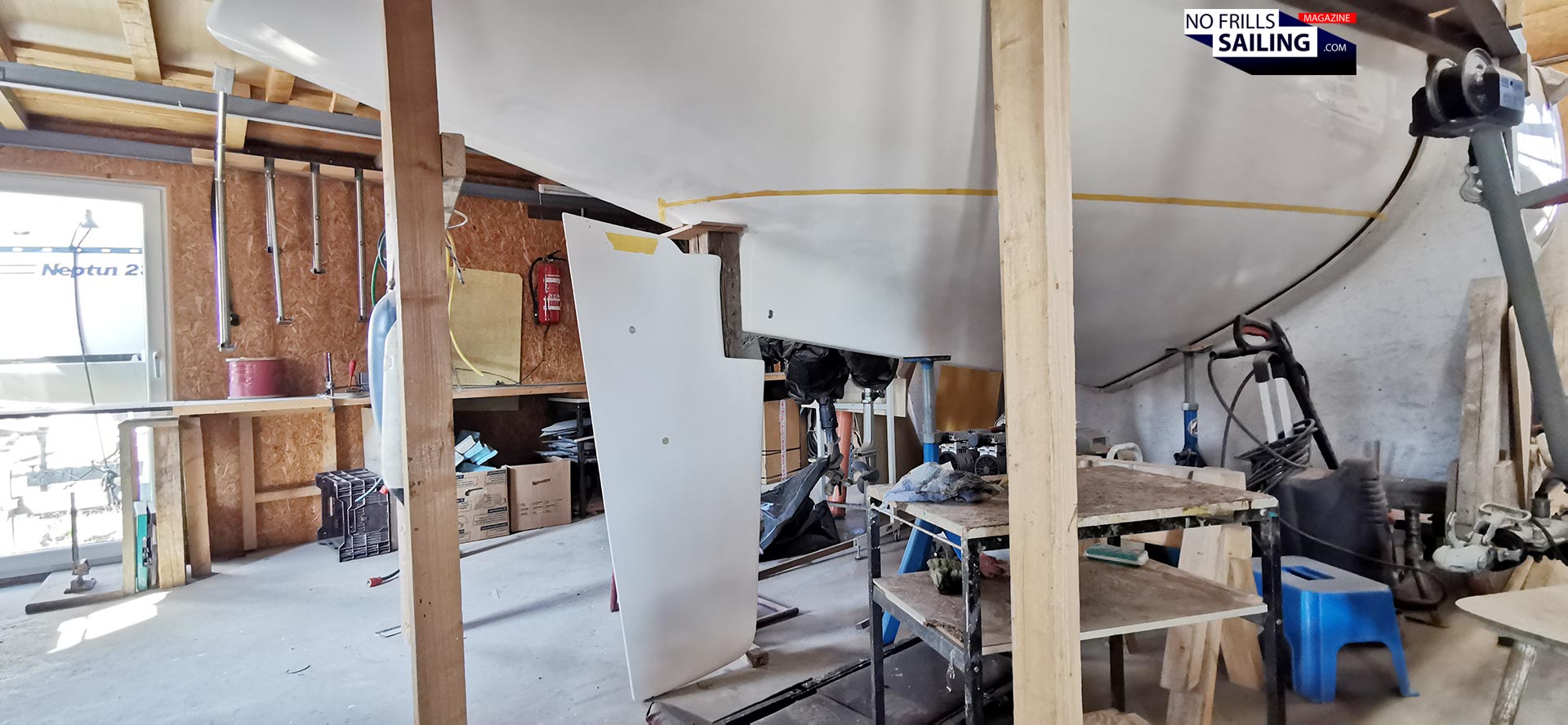
The boatbuilder says that in the coming days the above mentioned steps of procedure will be applied and the rudder for my ALPHA be made. I am looking very much forward to present more details in the coming part 2 article. After the rudder has been completed, I will take measurements for the tiller, for which I have a nice idea too. After visiting the shipyard of Linjett in Rosättra beginning this month, I have seen how they make the tillers for their yachts. These guys, perfectly aware of who Peter Norlin was and what a legend the Omega 42 is, offered to custom make a Linjett-tiller for my boat too. How cool would that be?!
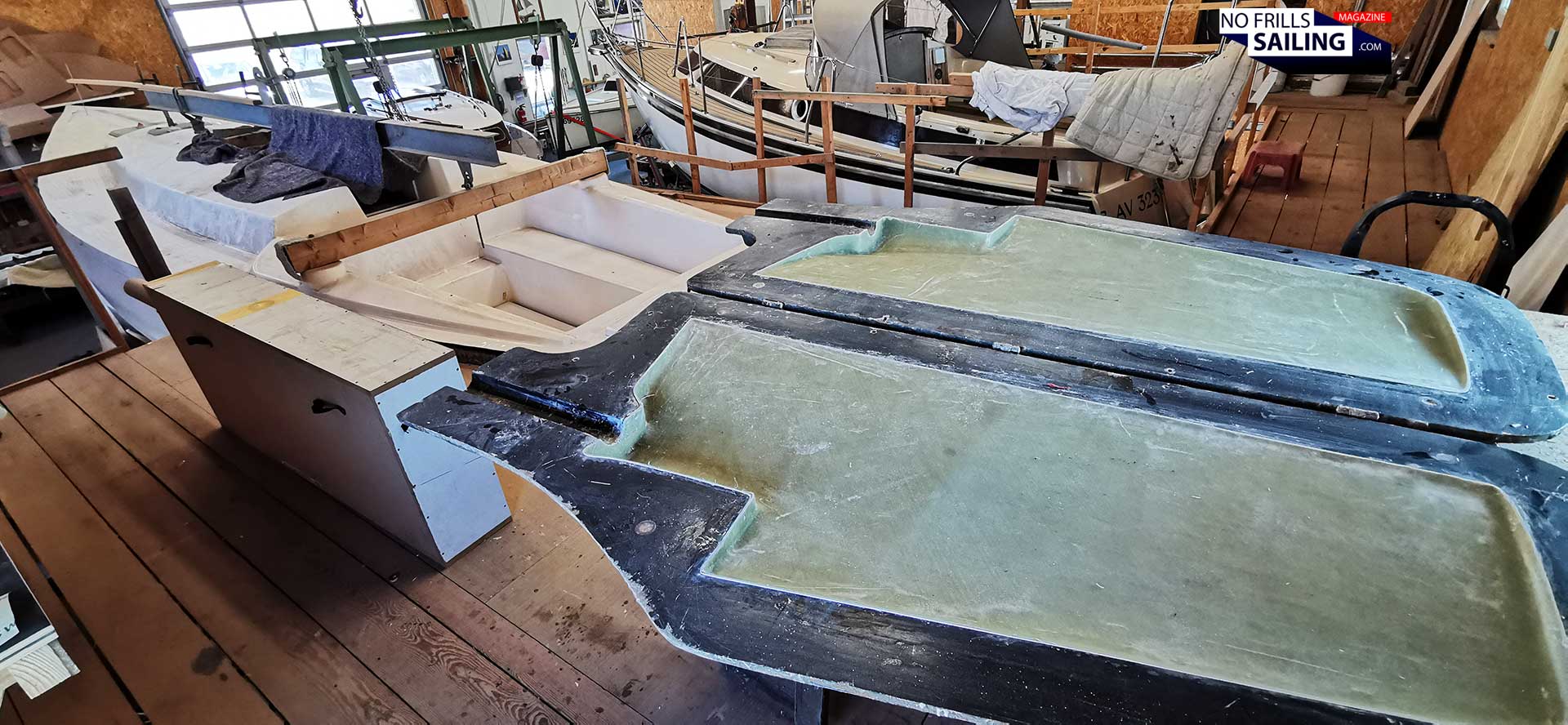
For now I am very happy that works are resuming. Though I don´t think that we will get ALPHA to the water in 2025, she will surely have her splash at long last in early 2026! Until then, it´s still quite a way to go, and I will keep you informed. By the way: The new NO FRILLS SAILING-Newsletter is in the making. If you inscribe here, you won´t miss a single article from now on, the newsletter is set to be sent once a month. Would be cool if you join – and tell your sailing friends about it.
For now: Happy weekend, guys!
Also interesting articles connected to sailboat rudders:
Rudder trunks: Comparison between GRP and aluminium yachts
That day I destroyed a rudder (and much more… )
All building progress-articles of my Omega 42