You may have read last weekend´s in-depth article about how a life jacket inflator works – that´s the device that is responsible for automatically triggering the inflation of a life jacket upon contact with water. After publishing this article I received a couple of comments and mails of readers who asked as very interesting question: How is the manufacturer of such a product making sure that it indeed works? Are there any laws or regulatory rules to obey? Any independent certifiers? So: How can you be sure that the life jacket you bought will actually be working 100 per cent in case shit hits the fan?
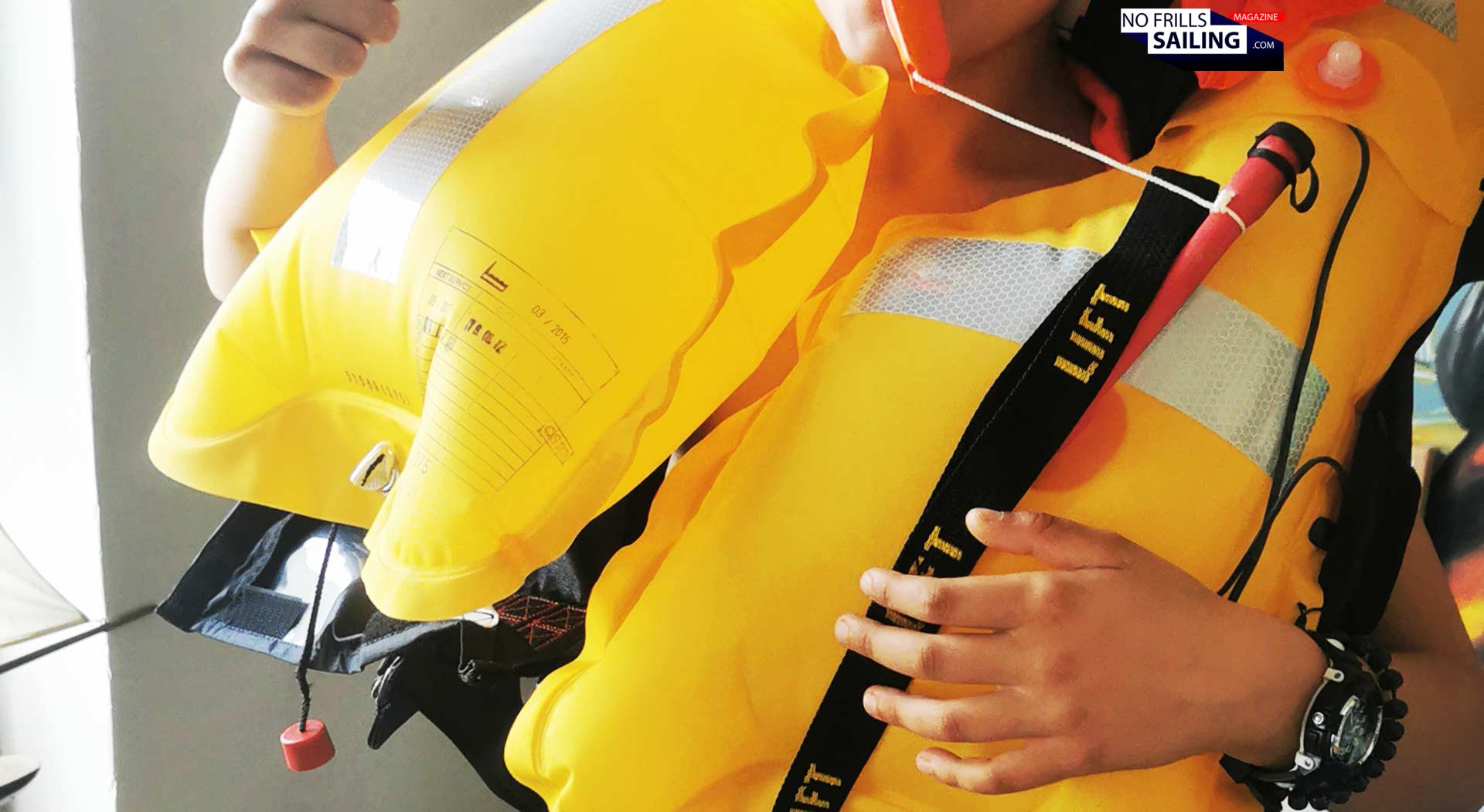
Well, I thought, if there´s apparently such a high demand for clarification, let´s do a follow up article with a clear emphasis on quality management, thorough testing and all the means a manufacturer of life saving sailing equipment undertakes to ensure the spotless functioning of its products. But before we start, here´s a nice little side-story for a kick-off. After breakfast the other day my kids, who are also glowing fans of my blog, asked me to show them the actual life jacket´s inner life and the inflator. I have multiple life jackets of different classes at home, one of which was overdue for inspection. Bought in 2015, last time serviced 2017. So I allowed my kids to let it go off …
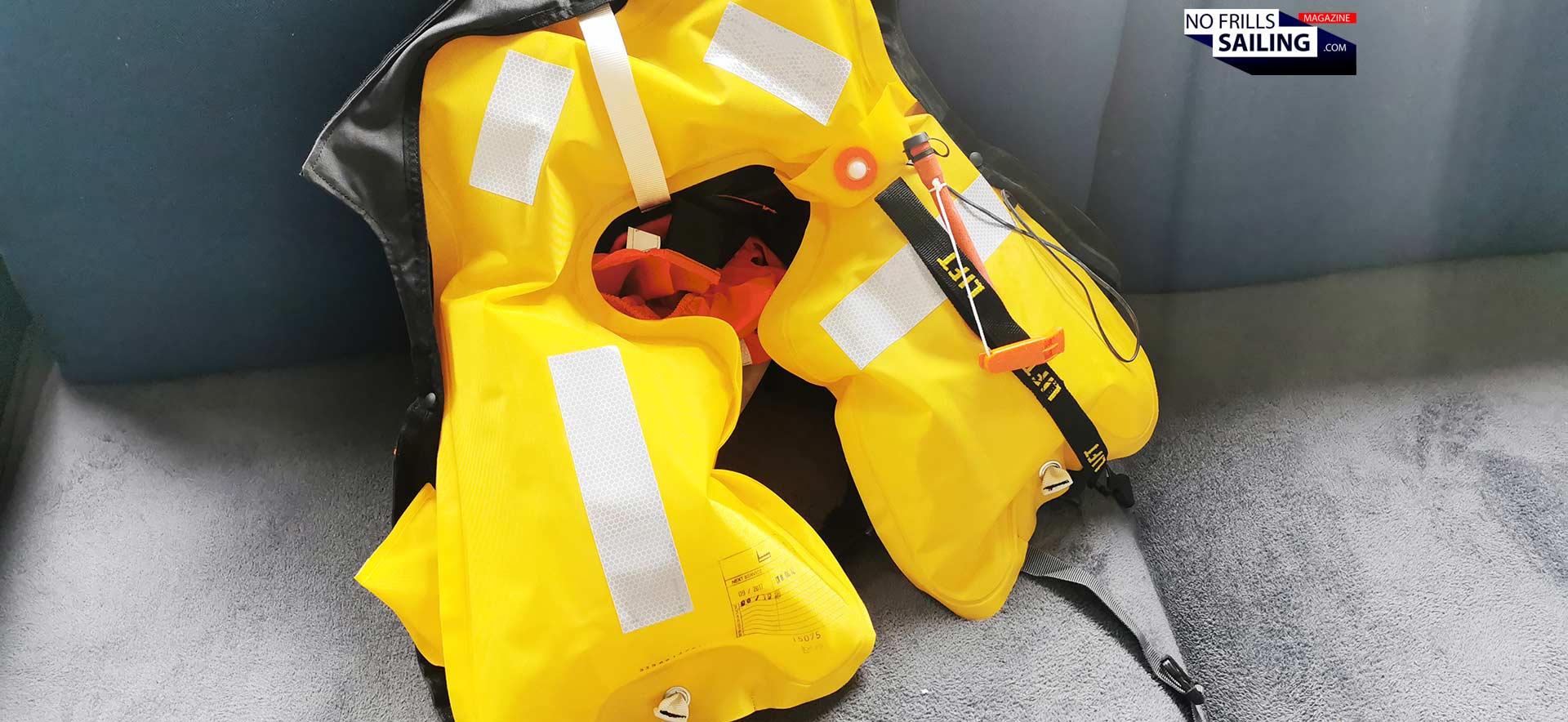
Great fun! And a live demonstration with quite an awesome pedagogical effect. I was able to show them in real life how it works and what is what. But the most interesting part was what followed: The float, the yellow buoyancy device, remained tightly filled and inflated for over 30 hours before slowly the pressure decreased and it became softer. Even after 48 hours the Secumar float was still roughly half filled! I mean, I don´t wish that anyone has to stay in the water after an MOB or loss of ship for any longer than some very few hours, but isn´t that kind of reassuring? So, that´s a nice start for this article I guess.
How are life jackets tested by their manufacturers?
Let´s go back a few weeks: I was visiting Secumar production near Hamburg. Luckily, I took over 450 pictures so that my library of raw material is till pretty yielding. And I am happy that I´ve shot all the things Olivier an Mona, the Sales Managers for Secumar´s leisure product range, pointed to. As we roamed the production facilities, I´ve had the pleasure to enjoy a full tour with intimate explanation of every production step by the two.
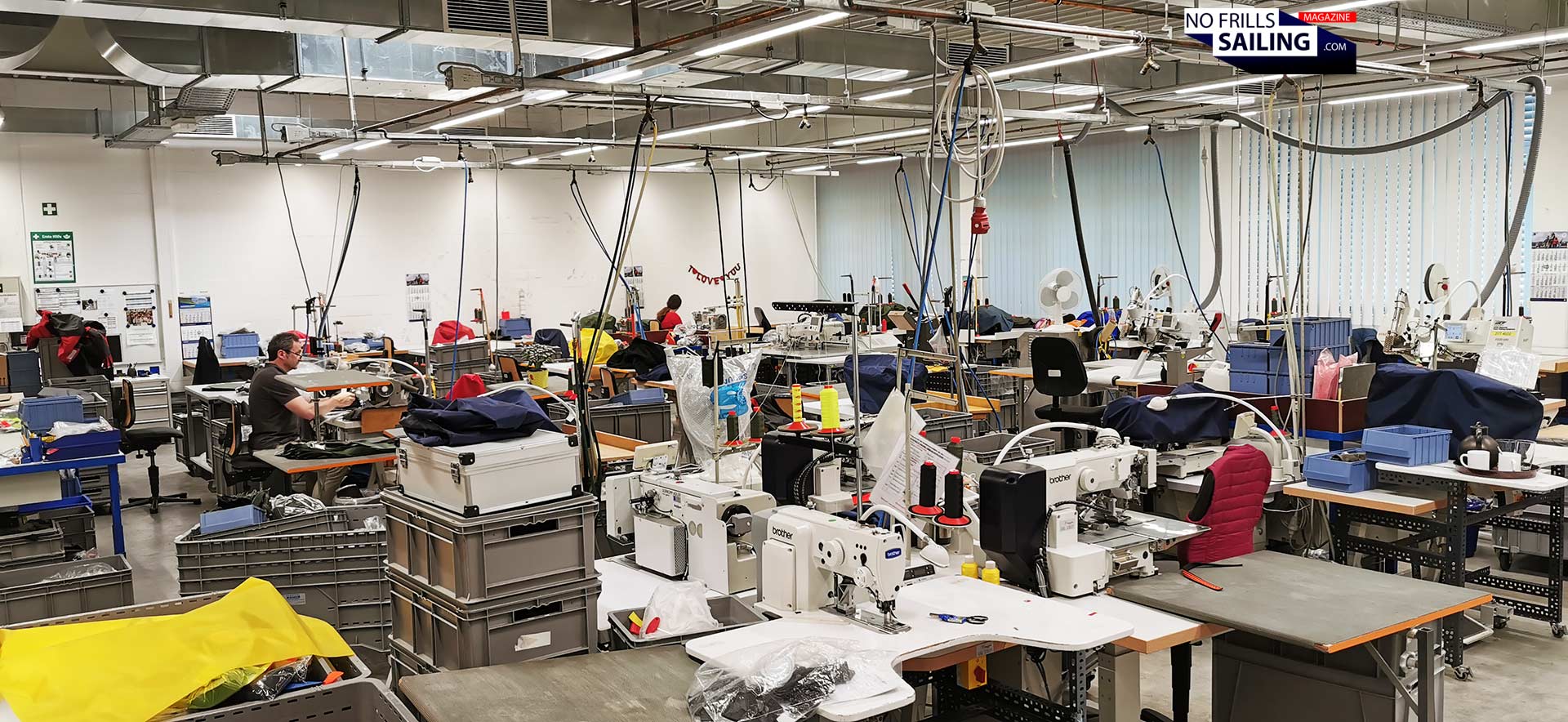
Although it was Friday after 4 p.m. and most of the staff had already left to enjoy a summertime weekend, some were still working. A blessing, so that those very workers and specialists could explain and really show to me what they were doing. By the way, if you happen to be in Hamburg for some reason and have some time to spend, skip one or two of the overly exaggerated touristic and commercialized things to do and ask if these guys show you around. Especially the company´s own museum is extremely interesting as it shows 100 years of seafaring from their, namely from a safety-perspective.
The heart of it all: The Inflator
So, let´s start with the inflation triggering device, the so-called inflator. How can the manufacturer make sure that it will go off, even after years? And by the way, what are these service guys checking anyways? Well, Olivier explains. One of the multiple checks done is the trigger-check. The aim is to see whether the inner mechanics of the inflator are still able to punch a hole into the CO2-cartrige. Of course, the cartridge cannot be used for this as this would be an incredible waste of material and resources.
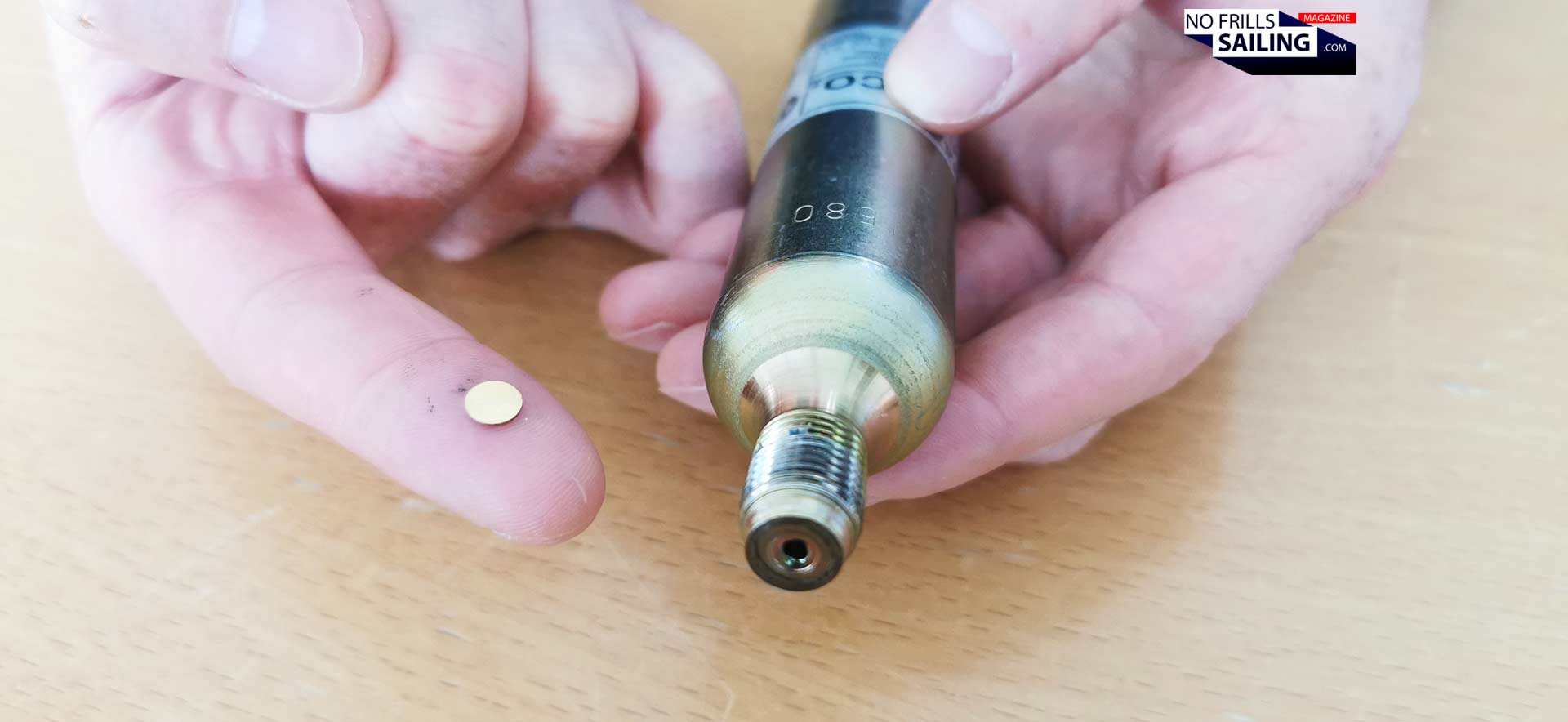
The service stations remove the cartridge and screw on a little mock device. It has the same diameter as the cartridge´s connector. On top sits a little flat blank, a metal plate that has exactly the same thickness as the seal of the cartridge. Now the device is triggered – unscrewing the mock the little blank plate is checked. If a nice half-round hole is visibly punched out, the inflator still works.
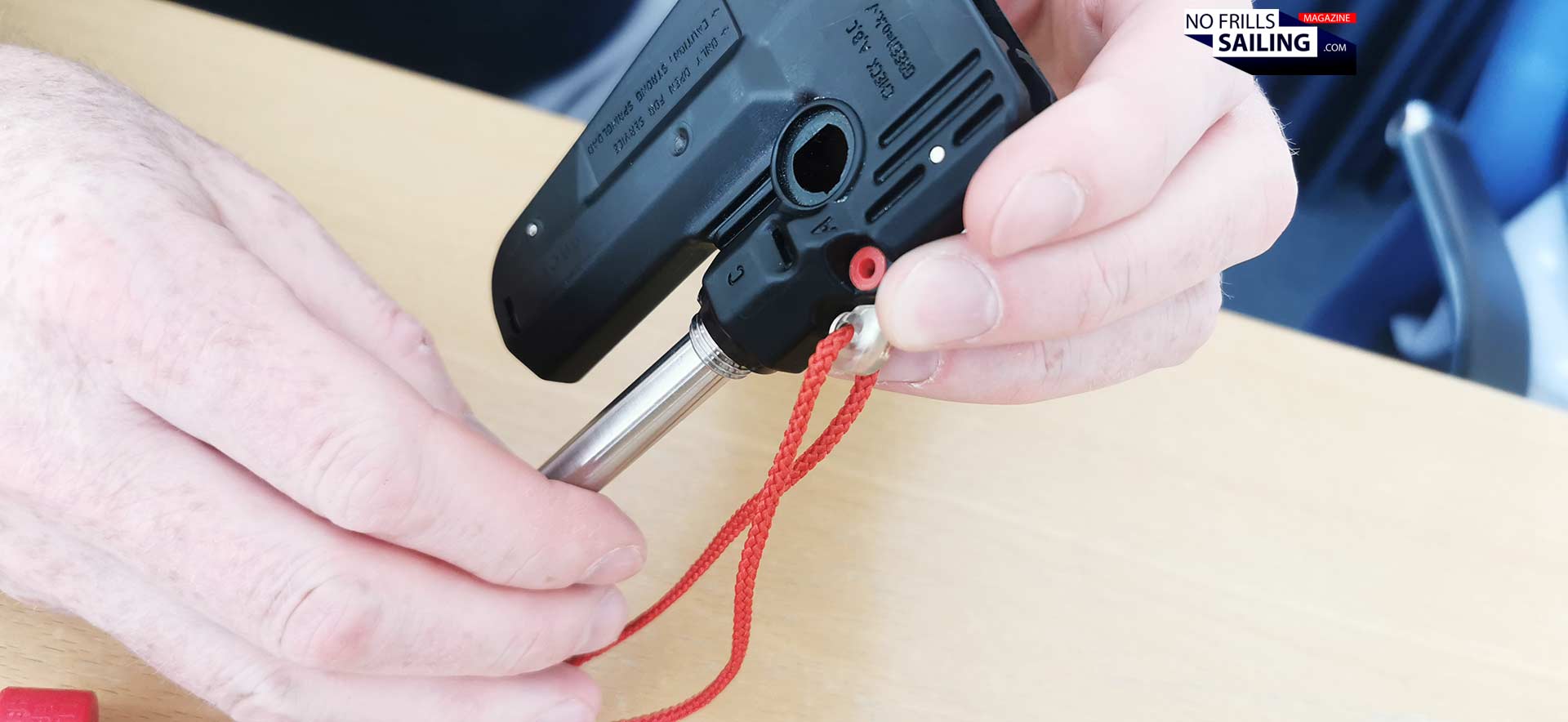
This has to be done twice during such a check. Apart from the fact that your life jacket will be filled and inflated to see if it can hold on tight, perfectly filled, overnight, a new cellulose pill is substituted and the whole life jacket nicely re-packed. After such a check, that is normally due every two years, you can be sure that your vest will be working fine. Here at the production, the same tests are carried out, but at a much larger scale. And it´s not just the inflator and the float which are tested, Olivier tells me that all in all some 15 different testing-machines and quality check-stations are set up over the whole line of production. From pre-delivery checks of arriving parts to quality management of the ongoing production to fascinating tests in their R&D department. We will see it all in the course of this article.
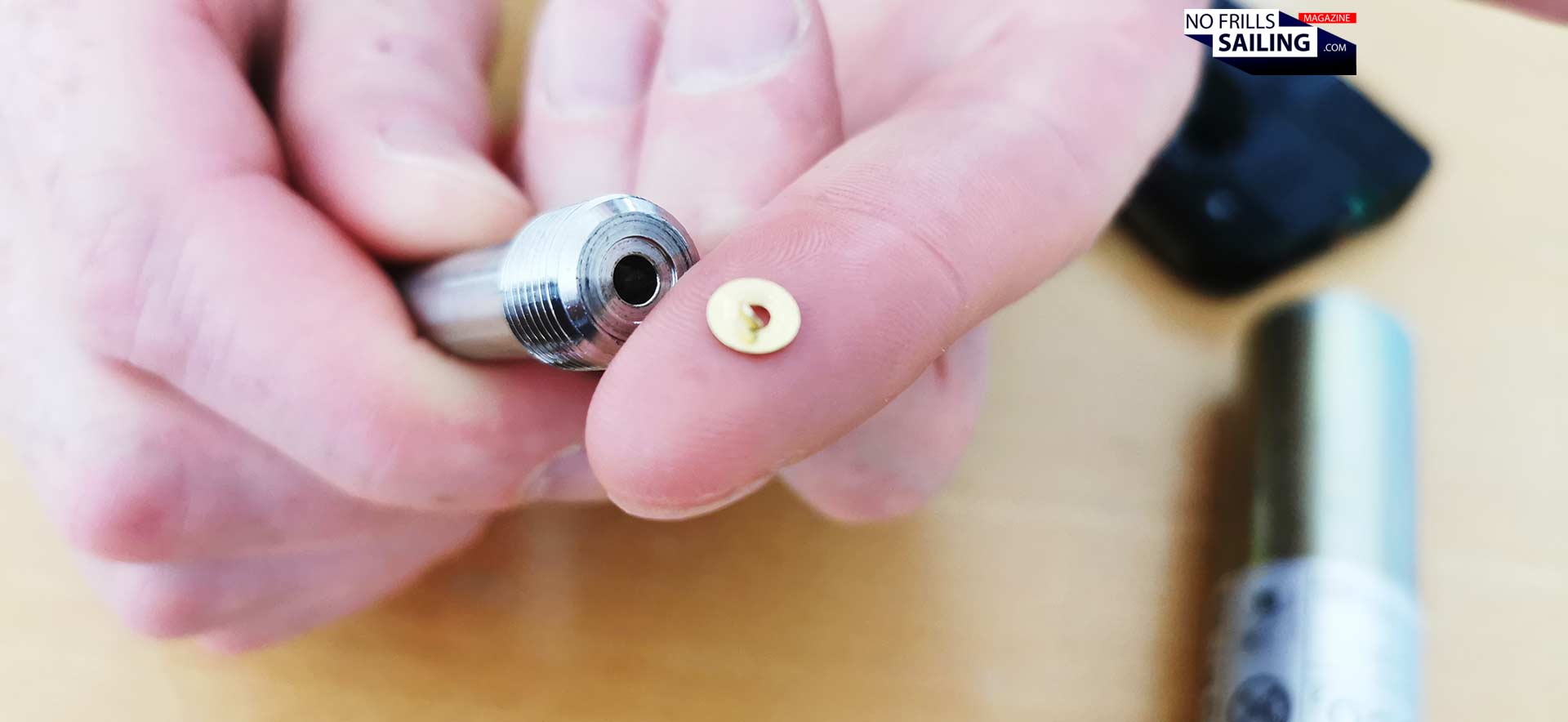
Remember my little kids test from the beginning of this article? This Secumar life jacket was already 8 years since its last service-appointment, hence 6 years overdue. And it triggered just like that, worked absolutely spotless and beautifully. Even after such a long period and blatant disregard for my duties as a skillful skipper! This reliability can only be assured by the highest possible quality, to begin with.
The deepest vertical integration
Secumar is – to my knowledge – the one and only manufacturer of life jackets with a near 100 per cent indigenous production. Their level of vertical integration is staggering. “Made in Germany” is not just a marketing label, which, legally only requires the last manufacturing step to be carried out in the respective country. They really make most of their products themselves. When it comes to raw parts or base materials, Secumar almost exclusively sources from German suppliers. That´s really a difference which sets apart a life jacket from many other brands: These are mostly made of different ready-made components you could buy on the world market, put them together, print your logo on. Not here.
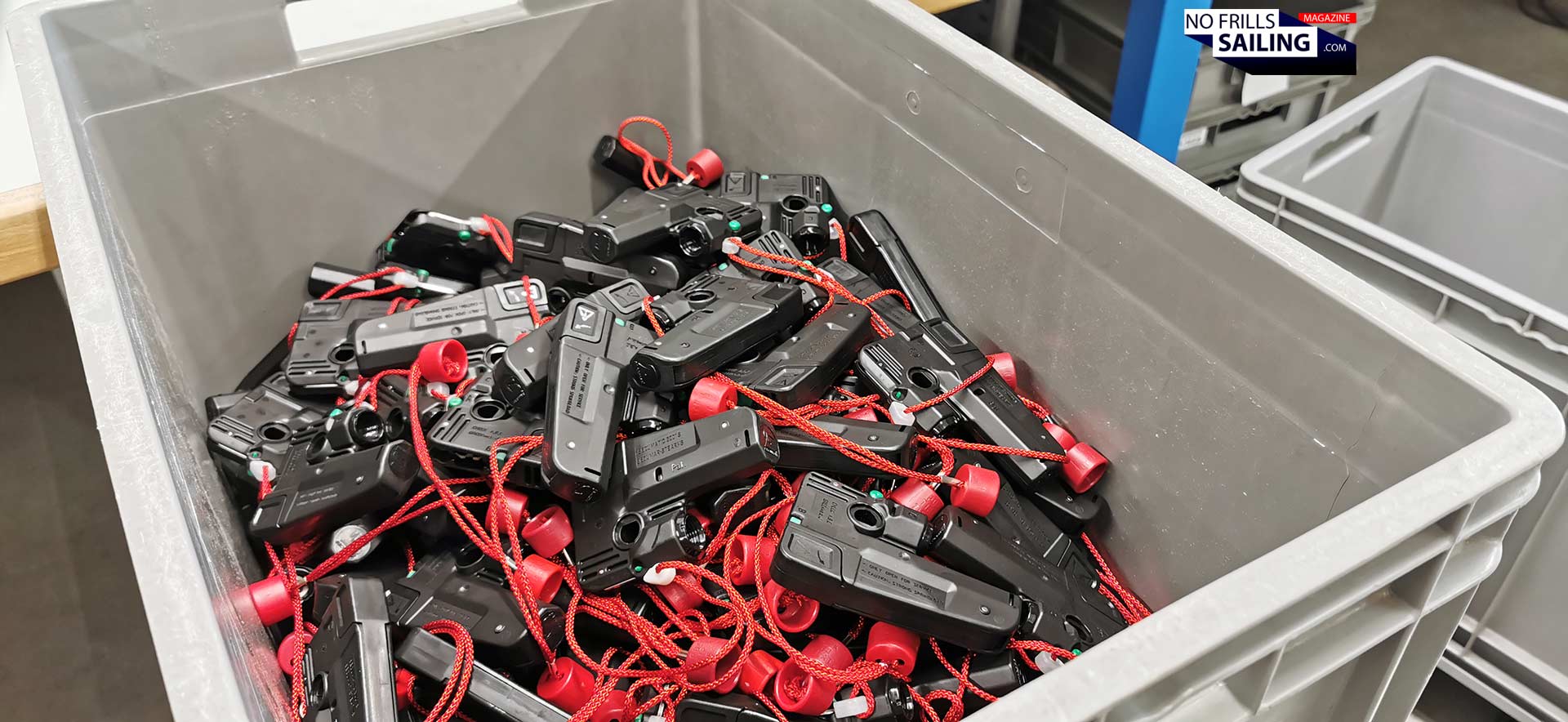
In terms of the trigger devices for example, some 15 workshops for people with disabilities are involved in assembling these components. Secumar has maintained close and long-standing relationships with these social institutions, which I think is reflecting a genuine sense of social responsibility. Interestingly, this collaboration also offers a practical benefit: Internal quality checks have shown that the hand-assembled inflators from these workshops consistently meet the highest standards. In fact, the defect rate is virtually zero – a testament to the care and precision with which the work is carried out.
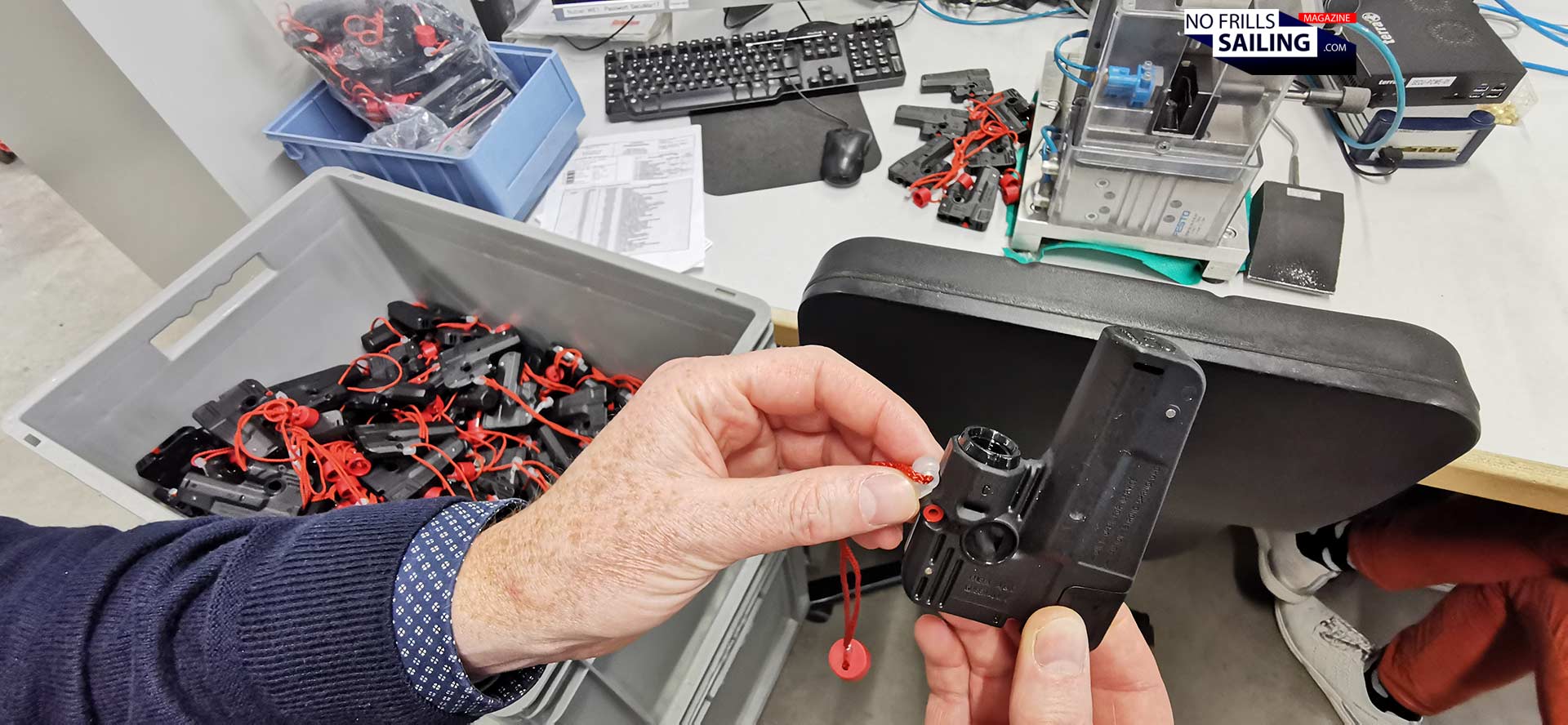
After a first pre-delivery check of the new shipment, the inflators arrive at their first quality check station. Secumar has developed and built a machine that can carry out the test shown above with the mock-cartridge much faster and in an never-changing standardized test pattern. Changing the work on these stations frequently to not allow a false routine to take over, an employee will sit down and put the inflators to the test.
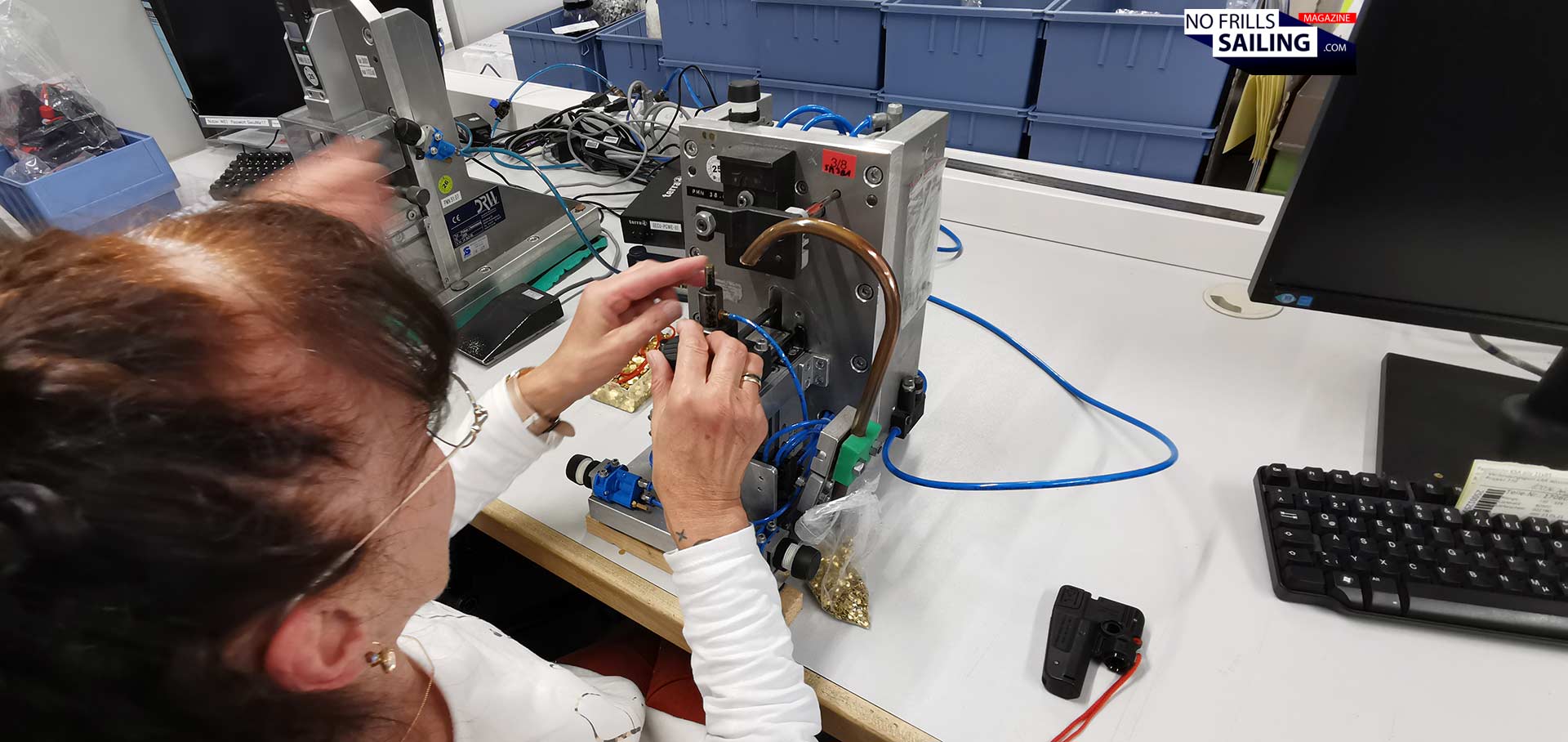
This is done by again putting one of these little flat-blanks onto a muzzle and inserting a new inflator device into the machine. The cycle is closed and sealed. Now the device is triggered. Two times, to be precise. As you may have already learned, the automatic inflators can also be triggered manually, which involves pulling on a string. And of course, this must be tested.
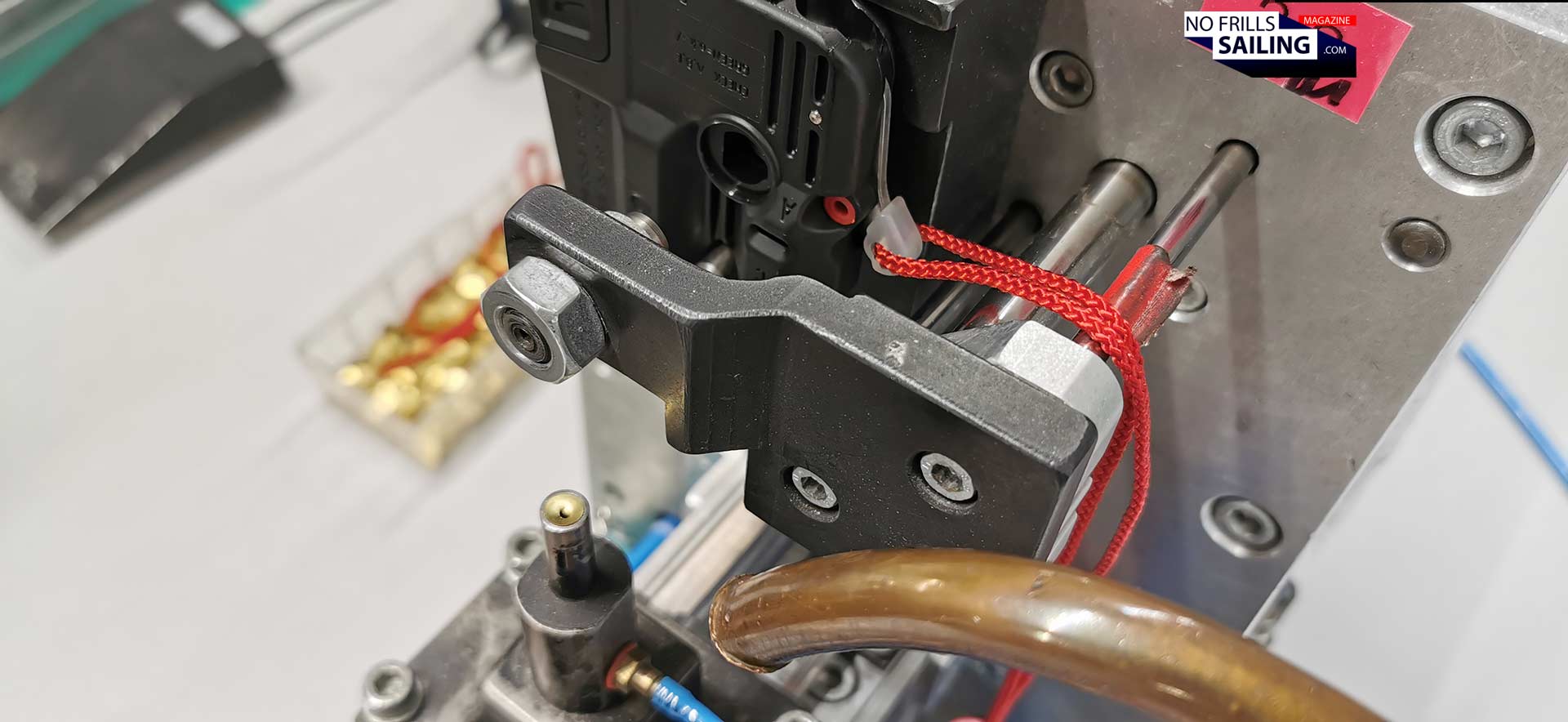
If an inflator is inserted, the employee pushes a button. Compressed air will now shoot through the muzzle at exactly the same pressure the CO2 would if a cartridge was connected. This pressure must be sufficient enough to punch the hole through the little plate. As you can see in the picture, it worked just fine. The test is now repeated with a fresh flat-blank, this tile the employee pulls the trigger, releasing the pressure. Again, the punching of the hole is checked.
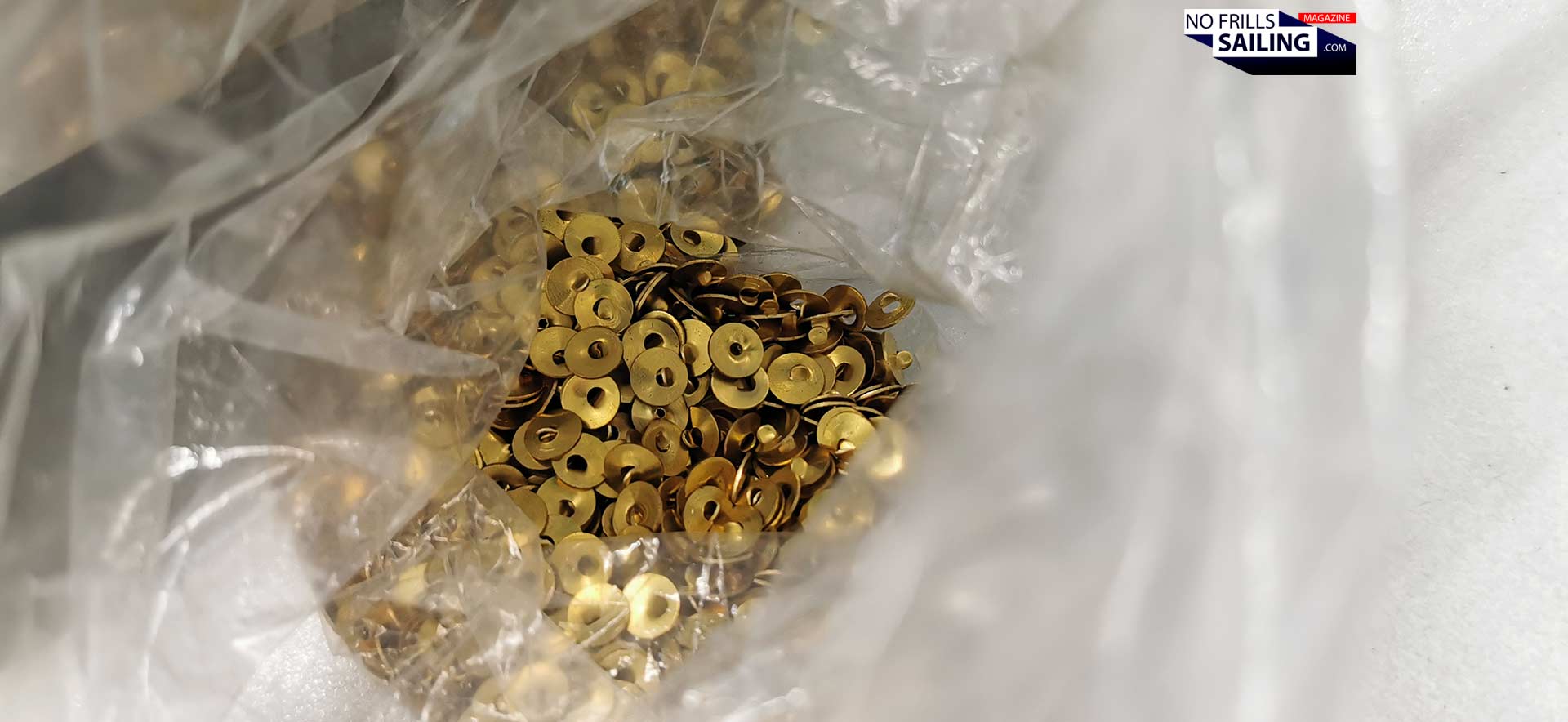
If both tests are passed, the little flat-blanks end up in a plastic bag. You can imagine how many of these little metal plates are utilized in the course of a year. Secumar´s annual production goes into the thousands, with another hundreds of life jackets serviced for clients every year. That´s precious metal worth saving and recycling of course.
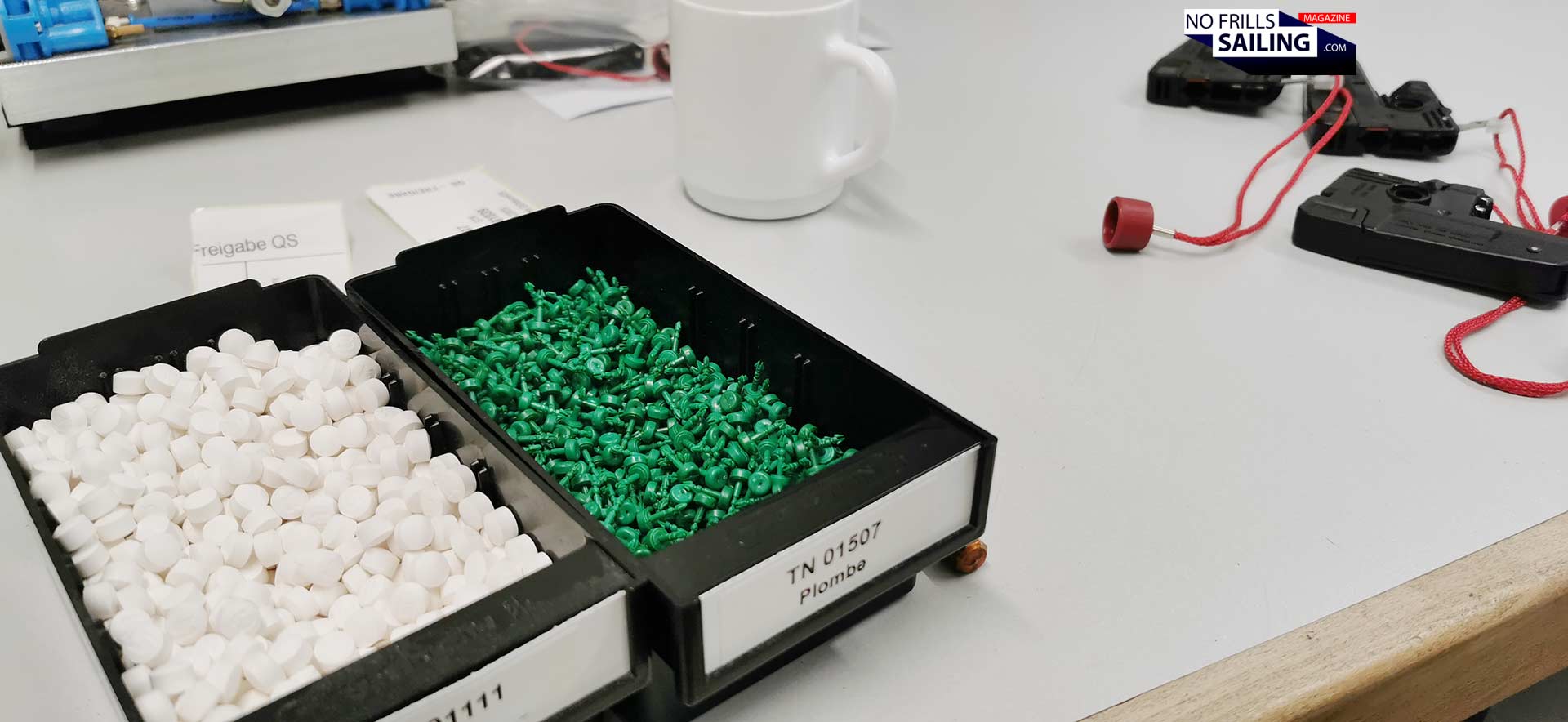
Yes, the manufacturer is also a service provider, happy to receive back their products for the bi-annual service-check-ups. Not many other brands offer this service. After the two trigger-tests are passed, the employee inserts new safety pins for the manual release and will also put in the famous cellulose pill – later more on that. The trigger is set, pill inserted and the inflator has passed its second test.
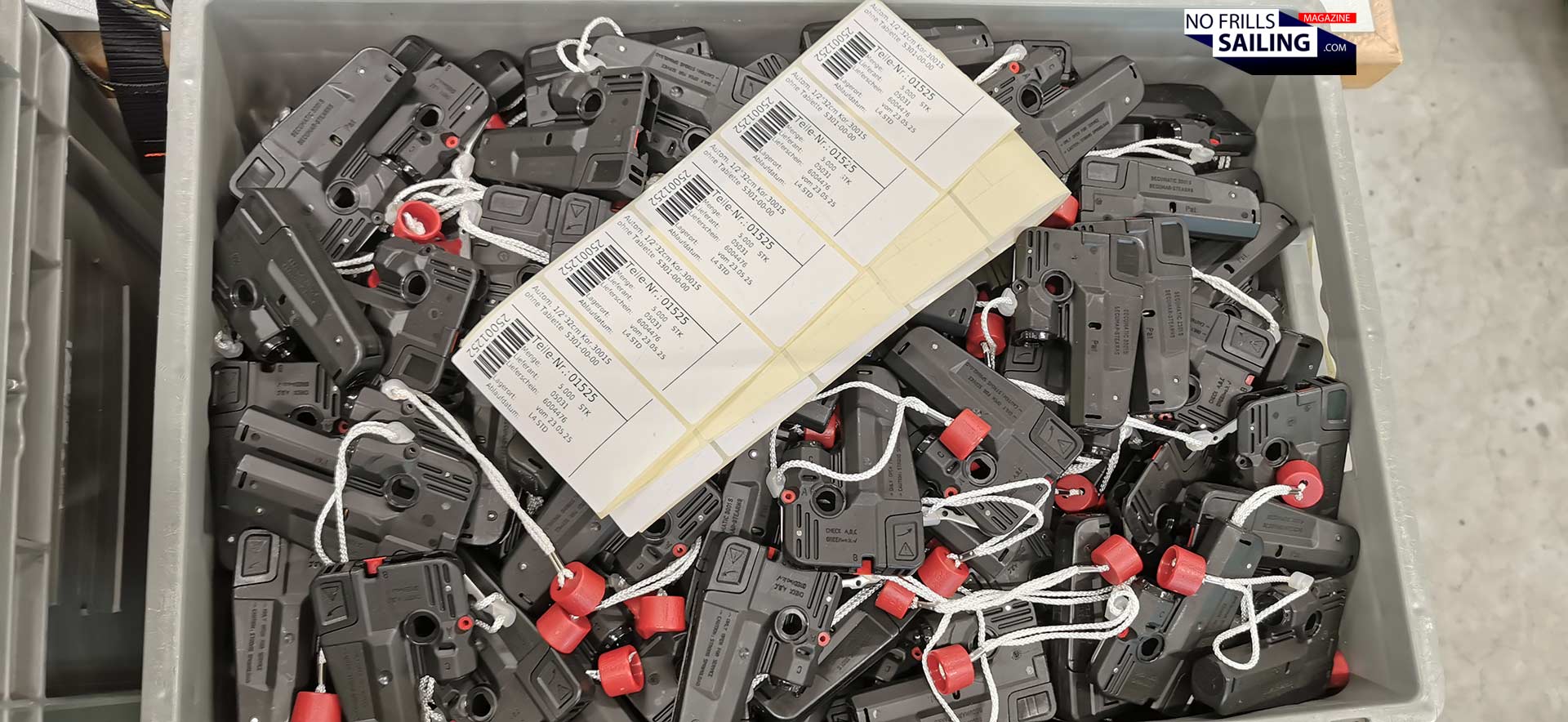
Ready for mounting! I oversee this whole step at this one work-station. On the left hand side the raw materials arrive from the suppliers. In the middle of the desk, at Secumar´s compressed-air testing-station, each and single one is meticulously tested. Two times. And the sorted nicely into a new basked that will later go to the next manufacturing step: The fitting. Secumar produces in batches. Each batch has a lot number and a specific set of data. As Olivier explains, for each batch a certain set of checks and tests, including high-load and even destruction tests, are stipulated. Not by any regulatory or state-official body, but by Secumar´s own set of rules and some DIN EN ISO-guidelines. Also, an independent organization called DNV, is regularly and constantly surveying Secumar´s adherence to the various, very strict German, EU and international rules.
Perfect fuel for inflating your life jacket: CO2
After having seen how the flawless functioning of the inflator is ensured, let´s have a detailed look at the very fuel that makes our life jackets inflate and float on the surface of the ocean. This gas is CO2, carbondioxide. It may not have the best image right now as being damned by climate activism, but it is indeed the best solution for being utilized in a life jacket. CO2 is non-flammable, non-toxic, lighter than water (will make things float) and works in a wide temperature range. Remember: Your life jacket shall inflate in the hot tropics as well as in Antarctic waters. It is also cheap to manufacture, reliable and completely harmless.
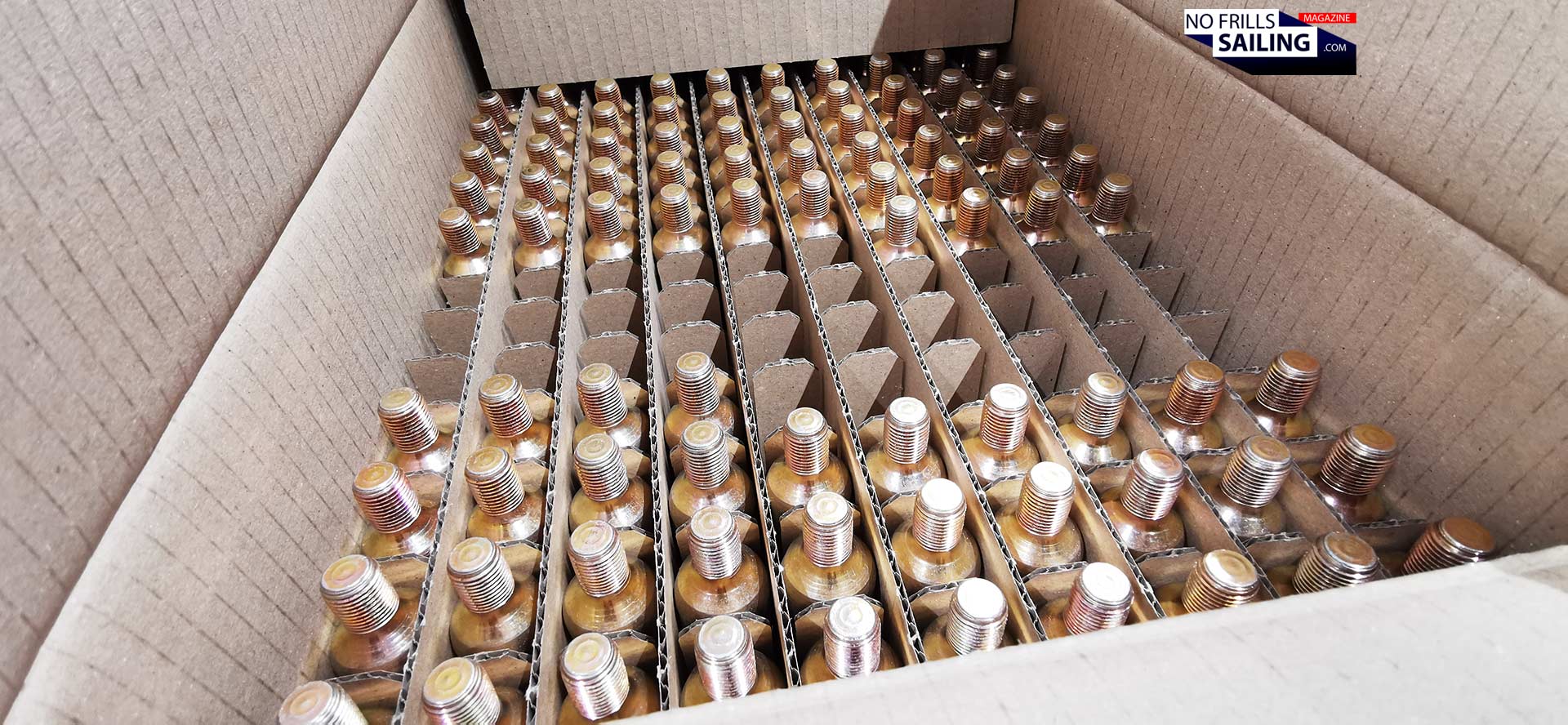
At Secumar they receive the cartridges from a German supplier. I see many pallets of cardboard packages, each containing dozens of CO2 cartridges. Again, after a thorough pre-delivery check, each single cyclinder is tested. In the case of a gas-filled metal piece, the test is relatively easy: It just needs to be weighed. The weight of the cylinder plus the xy grams of the CO2-filling, that´s it.
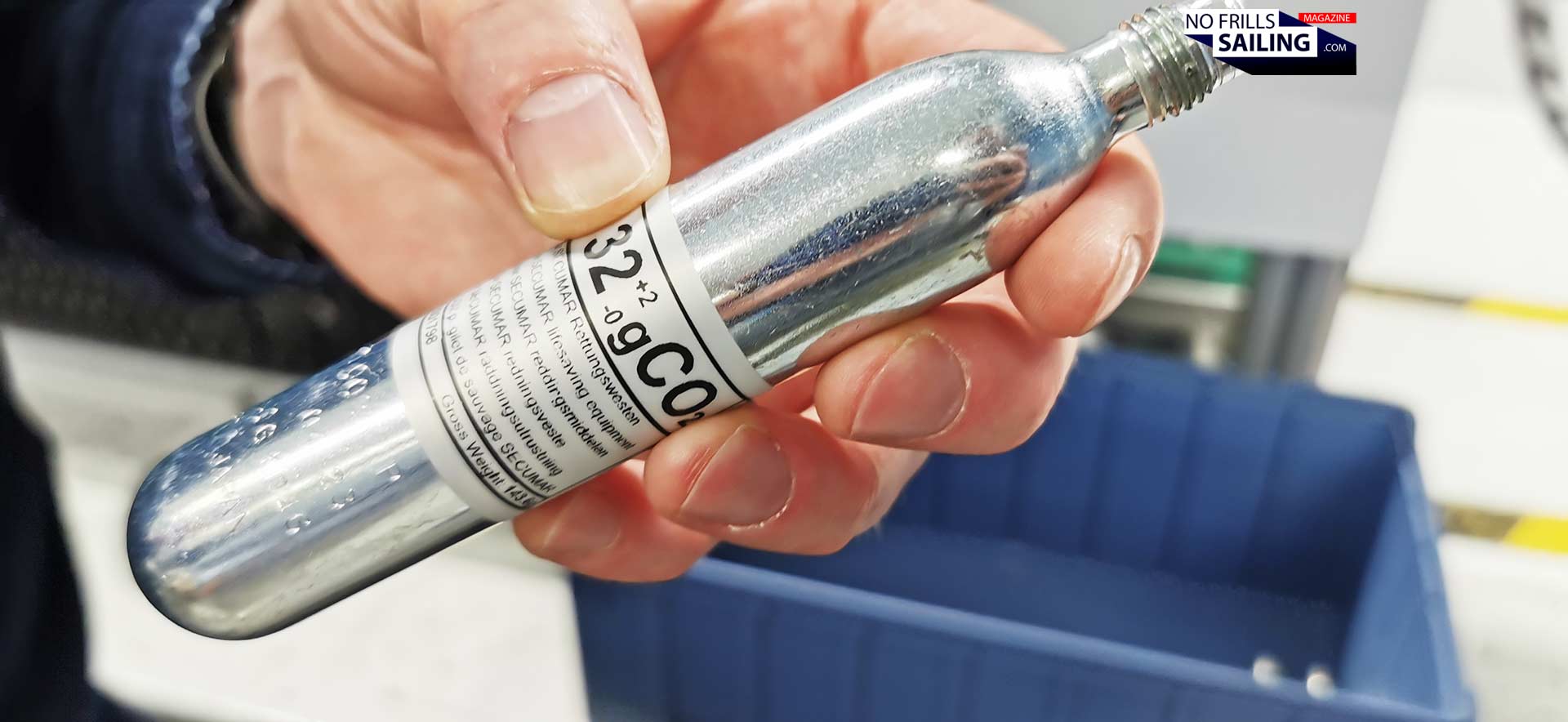
After it has passed, Secumar will print its own label onto the cylinder. By the way, here´s the “trick” for you to determine if your CO2 cartridge is still valid and nicely filled at home: Take out the kitchen scale, check the weight as stated on the label (hopefully your cartridge has such a label!) and if it fits, you´r fine. If it is significantly lighter, well, you may get a replacement.
Tiny detail – huge responsibilities!
Another very important part of the inflator is the cellulose pill. No, it´s not made of salt! (If you want to know more about this urban myth, check my last article. In terms of Secumar, it´s made of highly fine cut cellulose fibres, microcrystalline cellulose, as they call it, which is then compressed into the shape of these pills. These pills “lock” the trigger spring which will punch a little steel hook through the cartridge – this tiny white thingy!
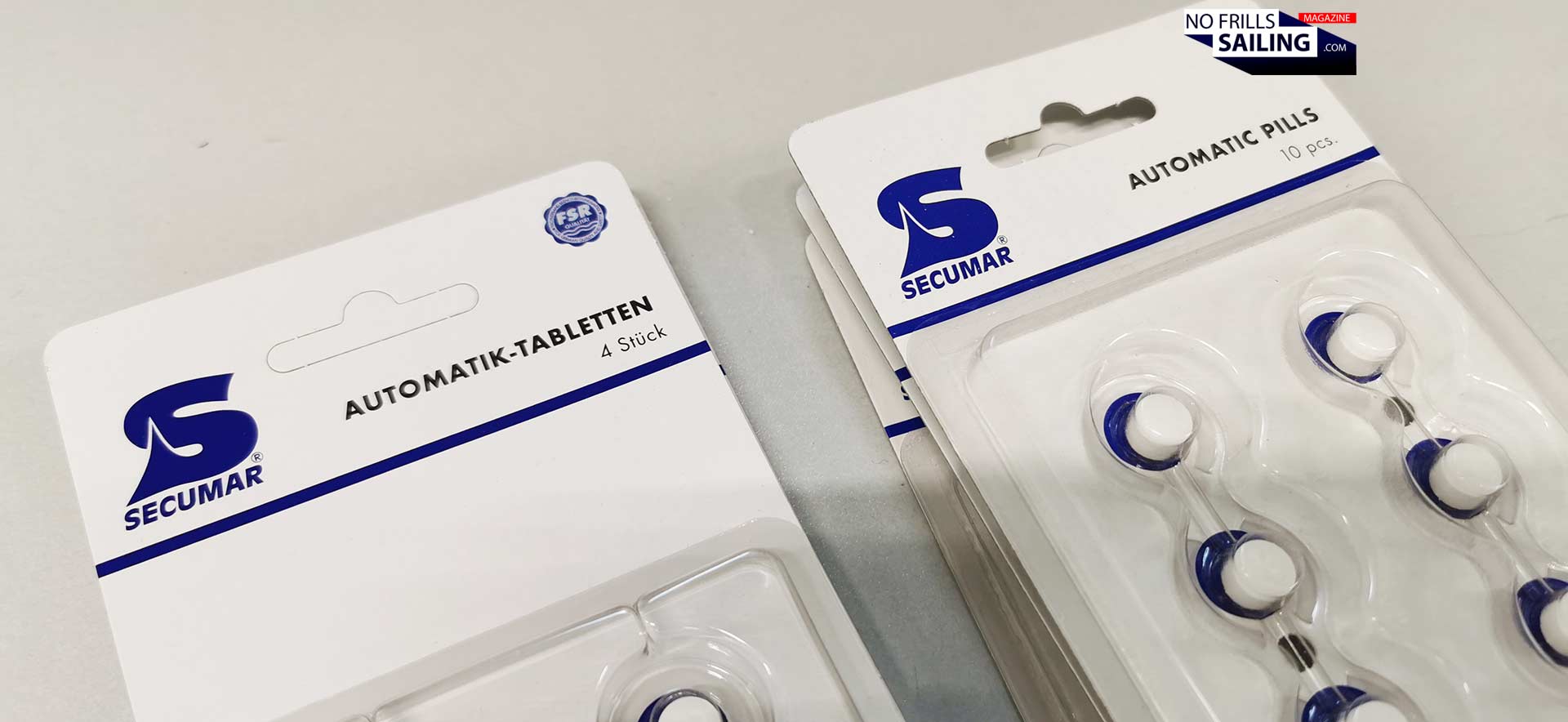
Here´s the thing: You cannot just insert any cellulose-pill here. There are very strict rules as to when and how an automatic life jacket has to be triggered and must start to inflate. A few seconds after a person has fallen into the water, inflating process must have been triggered. But on the other hand, sailing is a wet sport – you don´t want to have it set off with each spray that comes over. The rules even indicate at which depth such a jacket should be opening.
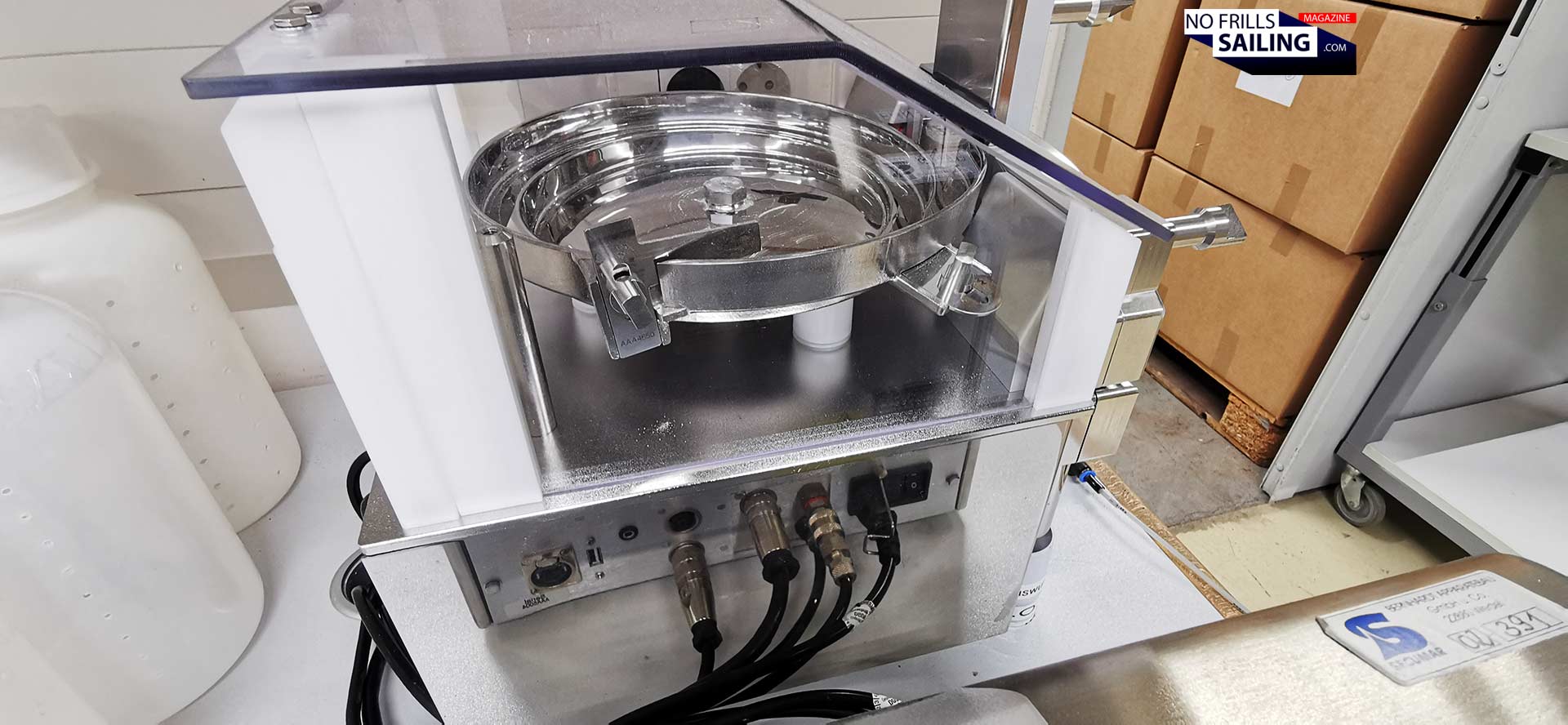
This is the reason why Secumar doesn´t buy just any ordinary foreign-made pills on the big market. They make their own. In an again long standing partnership with a German pharmaceutical company, their cellulose-based pills are made adhering to the highest medicinal industry standards: Only these companies can ensure a meticulously accurate manufacturing, a precise weight and that each and every pill has exactly the same properties as any other.
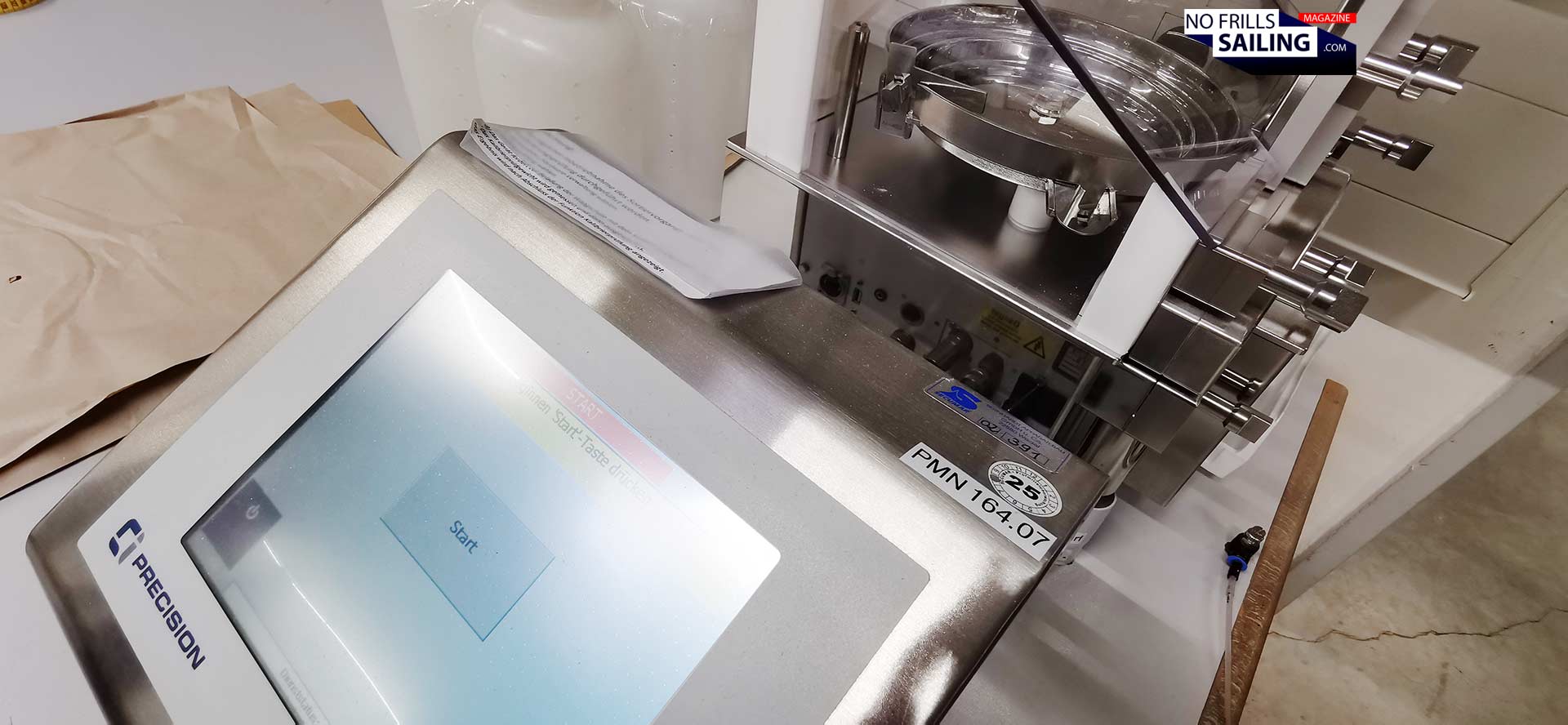
They could stop here: A company manufacturing highly specified cancer therapy medicines or other pharmaceutical products (under their even stricter sets of regulations) can be trusted, right? Well, apparently, again, they double check. That is why they present an electronic high-precision scale to me. Every single (!) cellulose pill is weighed on this scale before being cleared for further use.
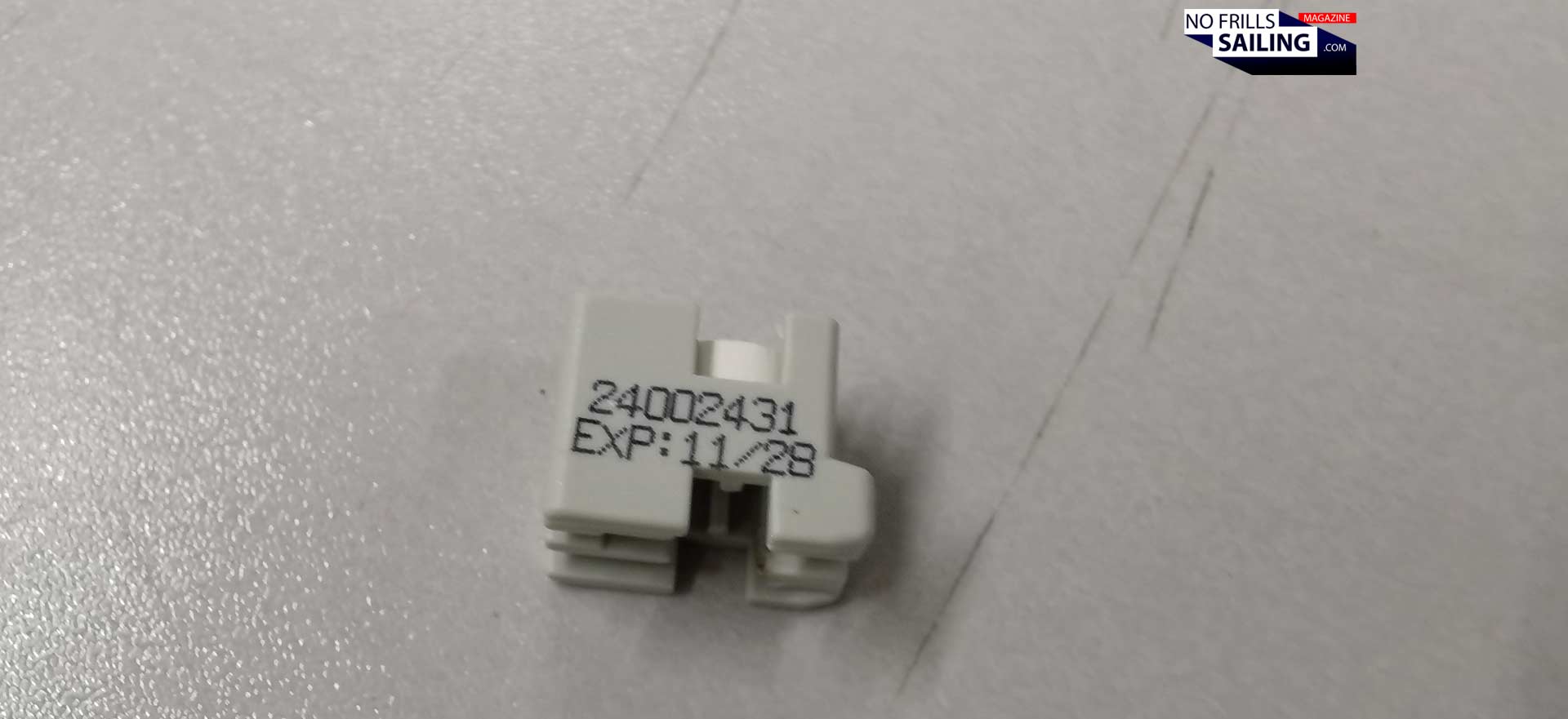
As the one employee working on this station is already off into his well-deserved weekend, Olivier searches in the production for somebody who is cleared to work this scale. In order to show it to me, thy insist to switch it back on and show how accurate it works. After they had found a colleague, it takes a while for the scale to boot itself. It adjusts itself, runs self-tests and it talkes some time. Why? Because this machine can weigh tiny fractions of a gram … But after it signals that it is ready, we put some pills on the scale. I am amazed: The margin here is a fraction of a fraction of a milligram! And yet, if not checked, if even just a tiny bit too heavy – it would take too long to dissolve and trigger. If a tiny bit too light, it would dissolve too soon. And of course, those pills have an expiry date. Olivier insists to have these replaced regularly as well.
Will it float?
Apparently he tells me that in some regions where the atmosphere is especially moist, pills are changed much more frequently. With some commercial or military customers of Secumar even do it after each mission or application. In the end, such a life jacket is indeed a true life-saver! And all must be done to make sure it can do its job as intended just in case.
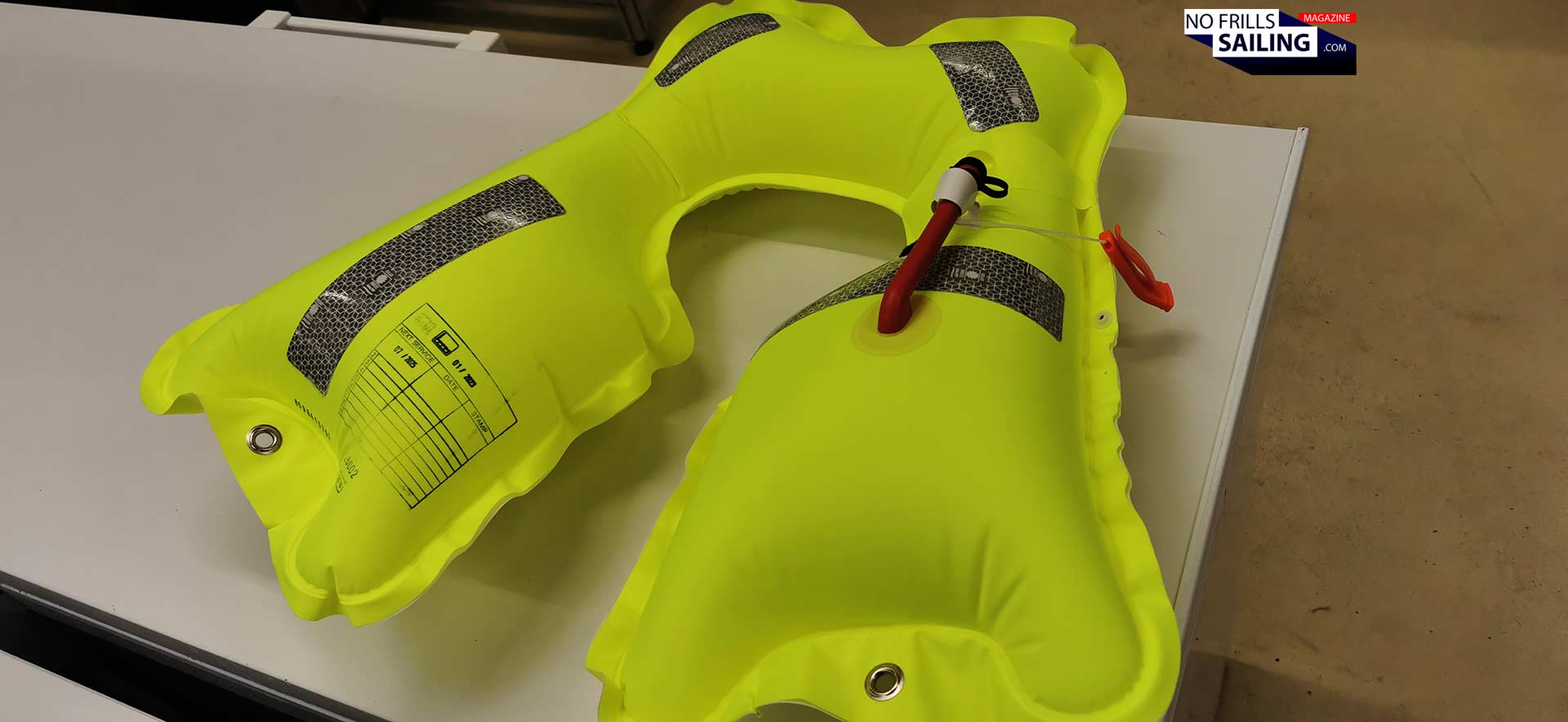
It´s job, that´s basically to get inflated, float and keep the guy at the surface. How it is triggered and how inflation works we have seen now. So let´s have a look at the very floating device. These are special fabrics, purpose made for Secumar. Available in many colors, most are very signaling and eye-catching to make finding you in the middle of the ocean easier. Like bright yellow, red, orange or green. There are military life jackets with darker colored floats, dark violet and aubergine. But no matter the color: Each one has to pass a thorough inflation test.
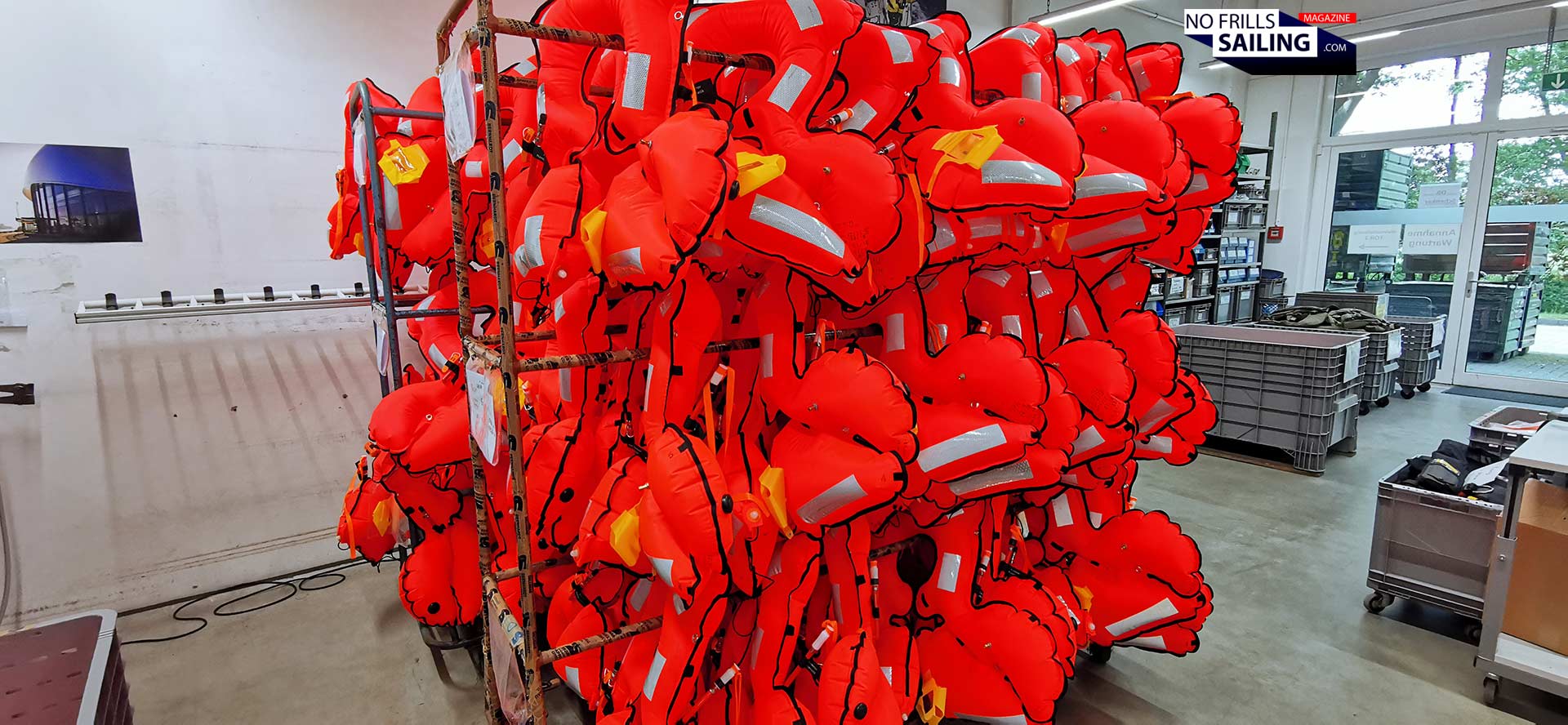
If you buy a life jacket – at least the ones from Secumar – you can be sure that your floating device has been filled up with air and put to a long-term test here at the factory. As we enter another part of the workshop, large racks are placed in rows. Hundreds of inflated floats are hanging there, filled to the brim, nicely shining in their colors. This test lasts at least 24 hours. That´s the time the floats need to hold the air at minimum in order to being accepted for further production.
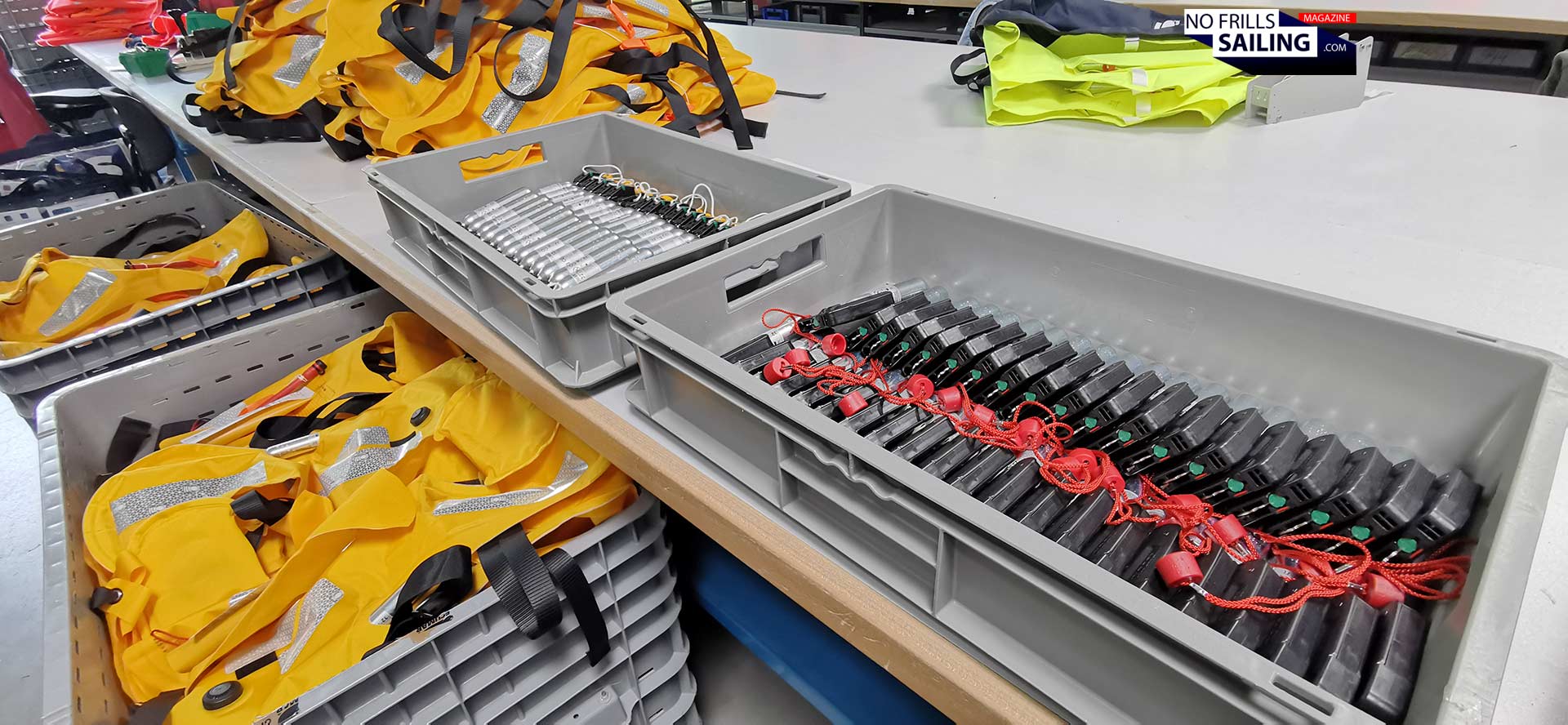
If these tests are passed – inflator, cartridge, pill and float – all parts come together on the assembly line in yet another part of the production. Here, lot for lot and batch for batch, the employees are starting the final assembly of the components. The trigger device is fitted, cartridge attached. All the surplus parts will be mounted according to the very product, like the whistle, a blinking light or the mouthpiece to put in air yourself. Then everything is nicely folded and packet – the life jacket is ready to be sent out.
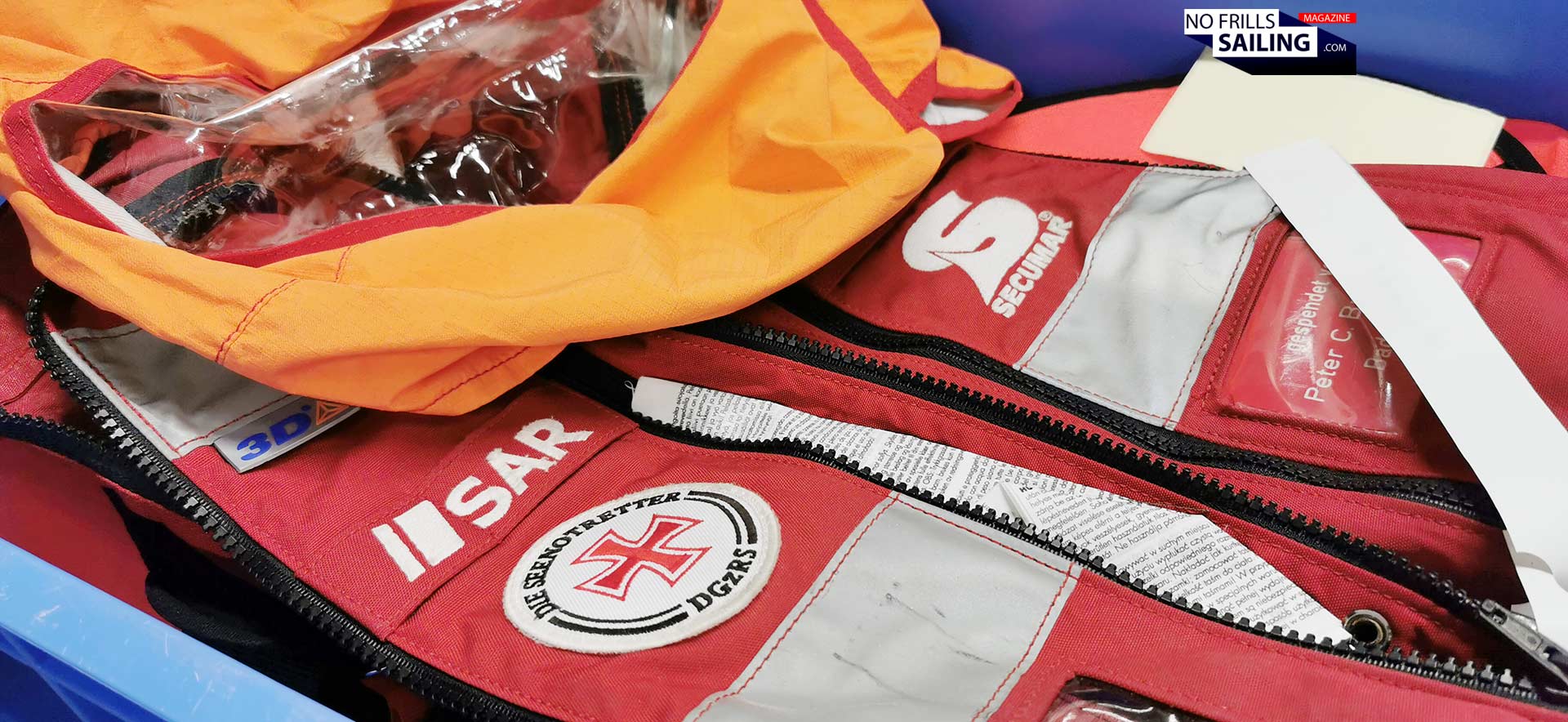
I find it interesting how much intertwined the production of brand new life jackets is with the checking of jackets sent here for service by Secumar customers. One part of the buildings is dedicated to service and checking the life jackets solely. Here I can see are numerous baskets filled with the well-known red life jackets as these are utilized by German SAR crews on the various rescue vessels in the Baltic and North Sea. Apparently, can there be any better endorsement for you product than the utilization by the professional life-savers themselves? Olivier tells me that many airlines and also professisonal shipping companies get their life saving equipment from Secumar.
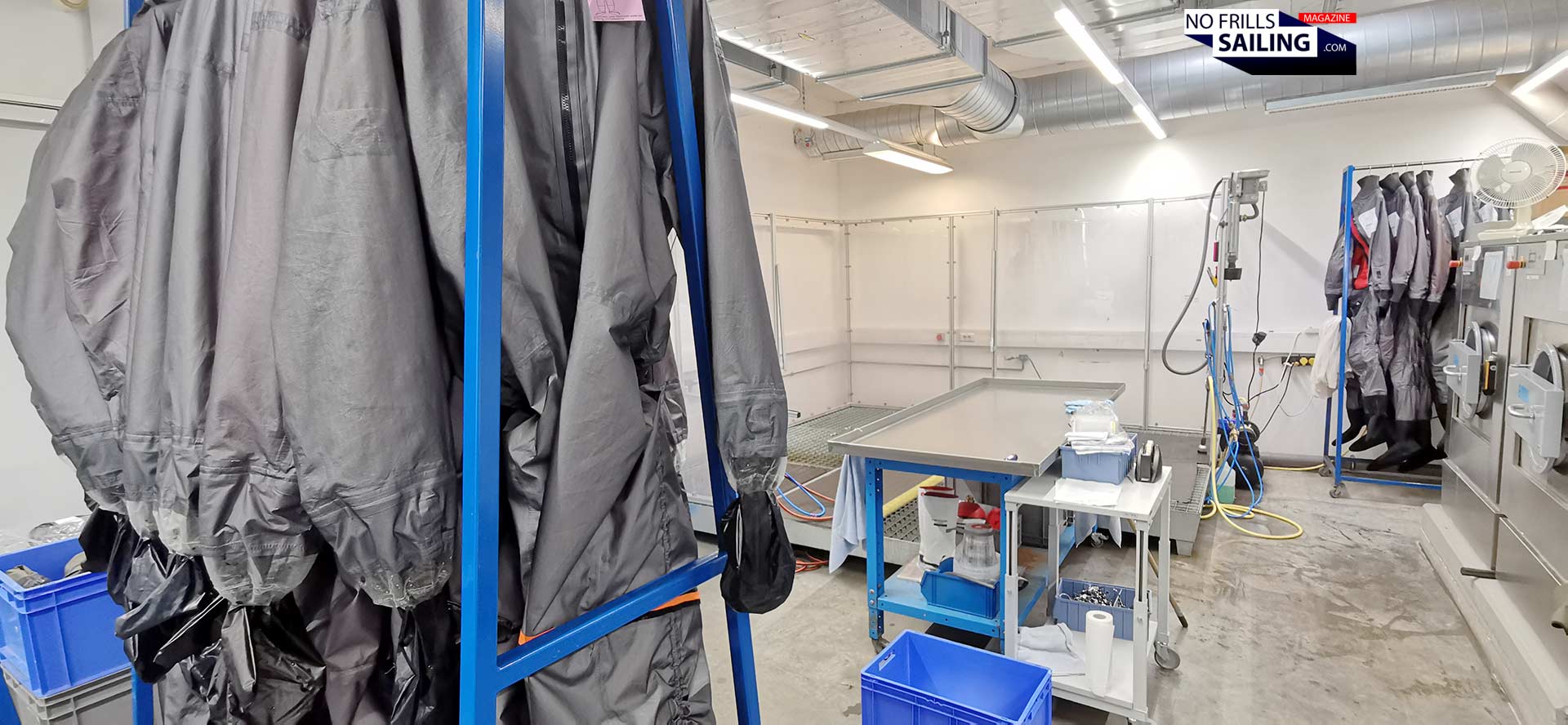
In a dedicated corner I can see racks with roughly two dozen survival suits. These are used by the German Air Force and, of course, made by Secumar. Here, a special test-setup as been made to inflate these suits with some low-pressure and spray them with a soap-lotion. Just like you did when you where young looking for this tiny leak in your bike´s wheel – same here. When bubbles are visible, that´s the spot that needs to be repaired. Apparently, Secumar-products are also flying around in the air, they aren´t restricted to the water. Joking apart: If you can count the SAR-service, the Navy and the Air Force as your loyal customers, you might be doing stuff in a pretty damn right way.
Trust gets around …
We proceed with our little walkthrough and arrive at a big box made of stainless steel. It radiates some warmth while at the same time rhythmic noise is coming out of it. Just so as if Darth Vader would breathe very fast. It´s of course compressed air that is pumped in and released all over again, every seconds or so. It´s a onther test-chamber. Olivier opens it.
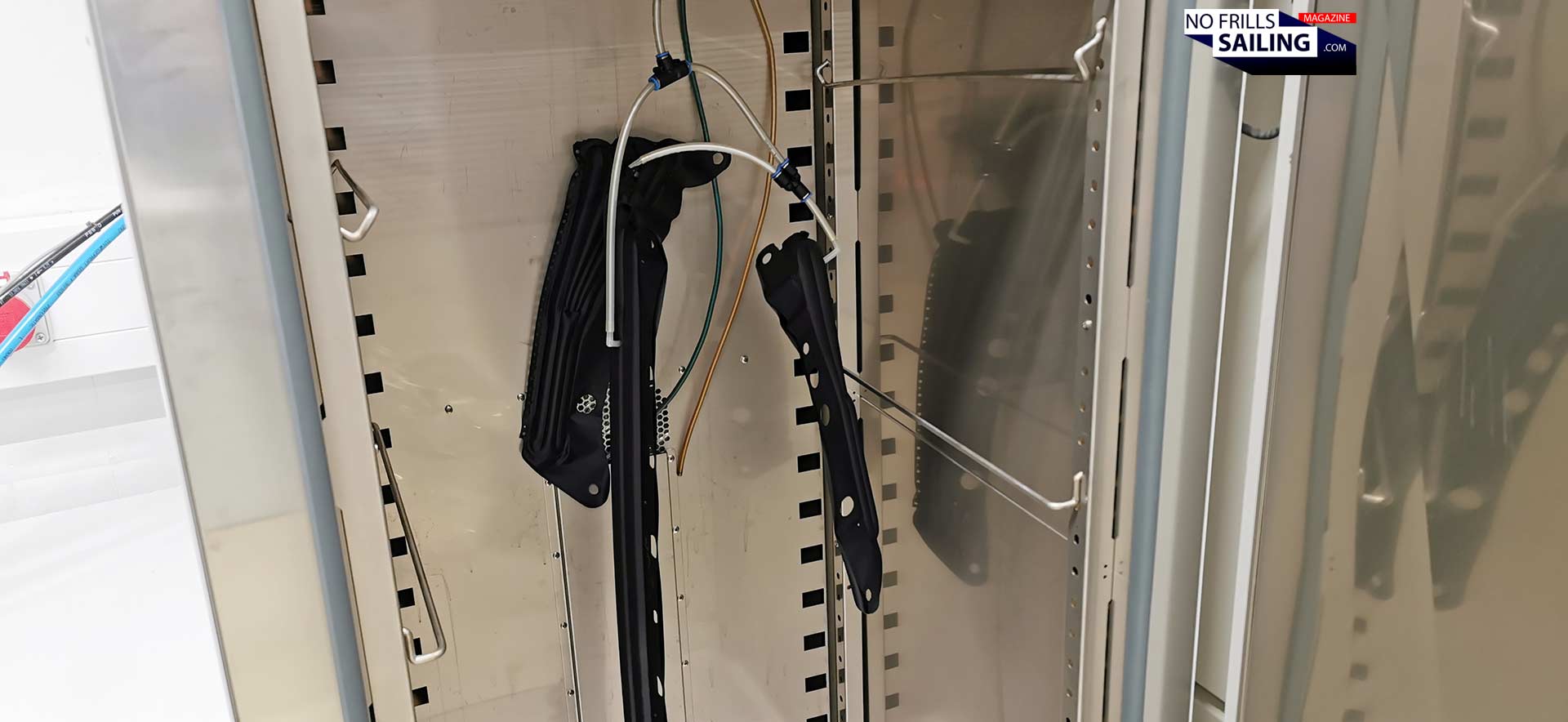
Here I can see some specimen of inflatables attached to pipes, rhythmically inflating and deflating. “That´s part of a spoiler for Porsche”, Olivier tells me. This is a nice example of collaboration with another industry, just like Secumar employing a partner from the pharmaceutical sector, this time it´s the other way round. Apparently, a few years ago, Porsche was developing their latest )11 Turbo model. The wanted to add a front spoiler system that would go down when a certain speed was reached to improve surface grip of the car. They couldn´t make it themselves, so they turned to the one industry leader competent with inflating things.
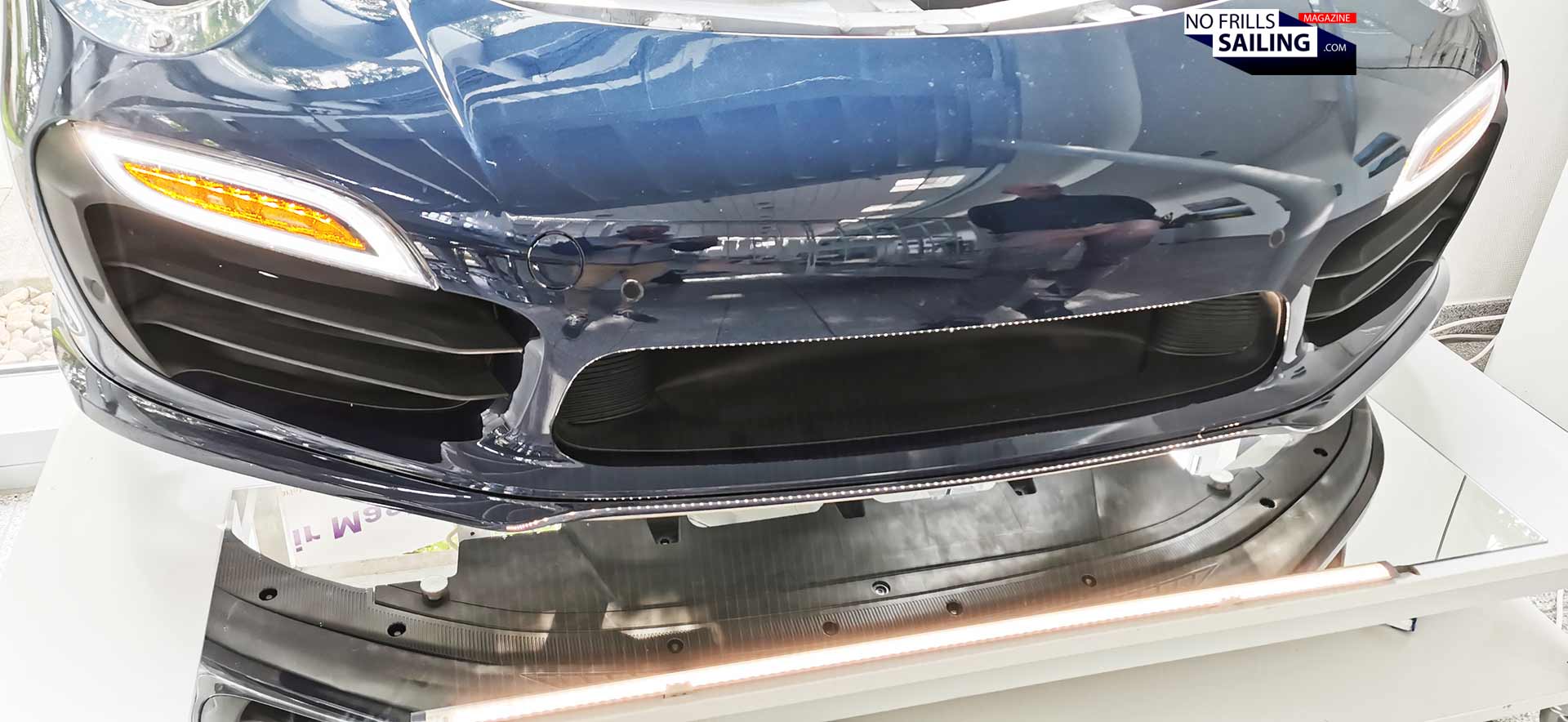
Now this inflatable front spoiler is part of the series production Turbo S and Secumar proudly presents a mock-up of the whole front section of the 911 in their lobby, demonstrating the principle. It shows that the knowledge of this company bar far isn´t limited to “just” making life jackets. In the test-box, another sample of the Porsche-product is thoroughly tested. Olivier looks at the counter. It says that another 45.000 inflation/deflation-processes are still ahead. Cool to see this interdisciplinary cooperation. But back to our topic …
Will it be watertight?
After getting to know the test procedures and level of checks for the inflation device, it´s paramount that the float stays afloat. So how can you make sure that – at least when the life jacket leaves the factory – the buoyancy is guaranteed? Again, it all starts with complete control over most of the production chain. That said, Secumar inflating life jackets are 100% made in Germany.
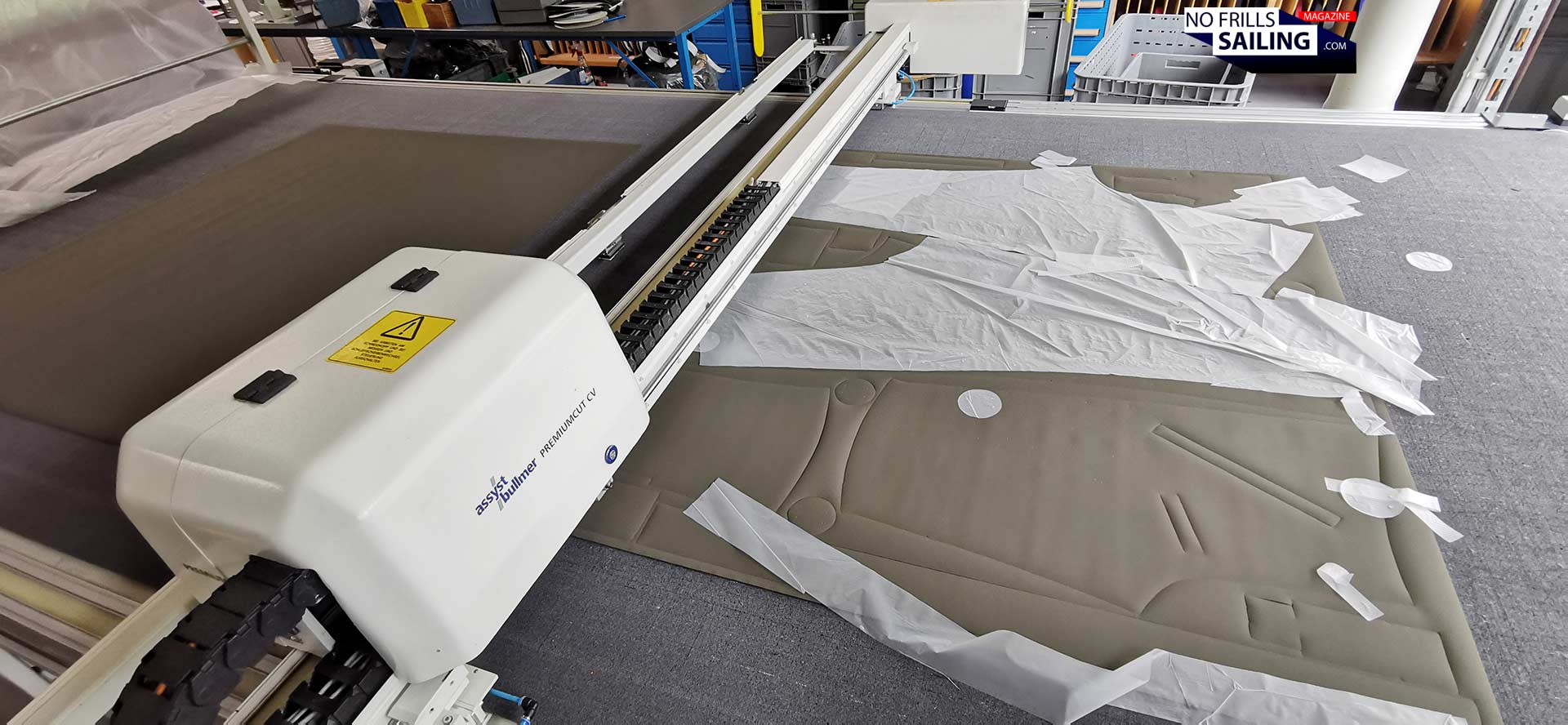
That said, we tour the production for the floats. Olivier shows the different methods of tailor-cutting the base materials. This is either done by a “plotter”-like cutting device or by die-cutting. Both methods have their advantages. For example, a die-cutter can stamp out many layers of fabric at once, saving time in the production. The plotting machine is extremely precise.
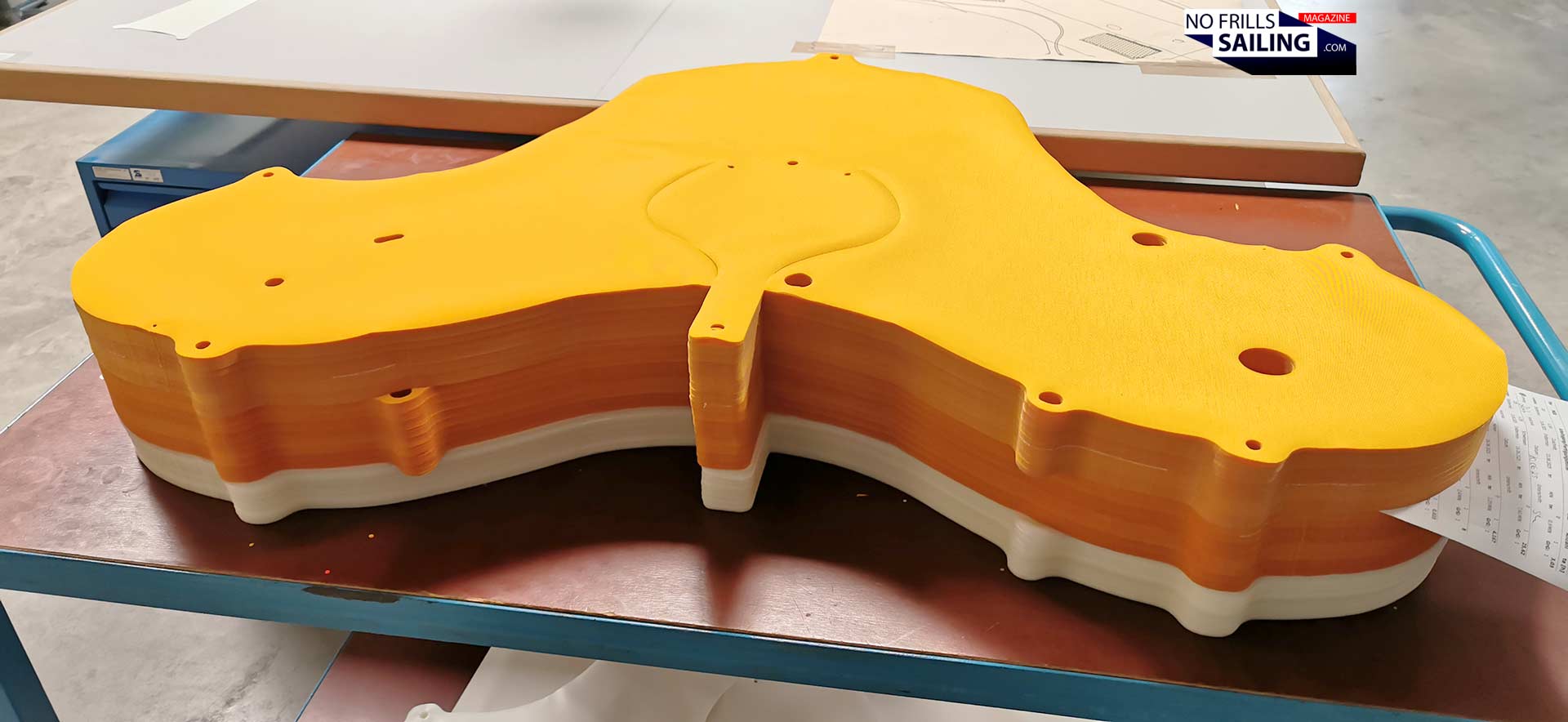
After the parts have been cut out, the floats are usually welded together. This is also a fascinating machine: Not unlike the vacuum-sealing at home with leftover food. But these huge machine, basically working like a waffle iron, are much bigger. Central part of the thermal welding process is a welding form, as you can see in the picture below:
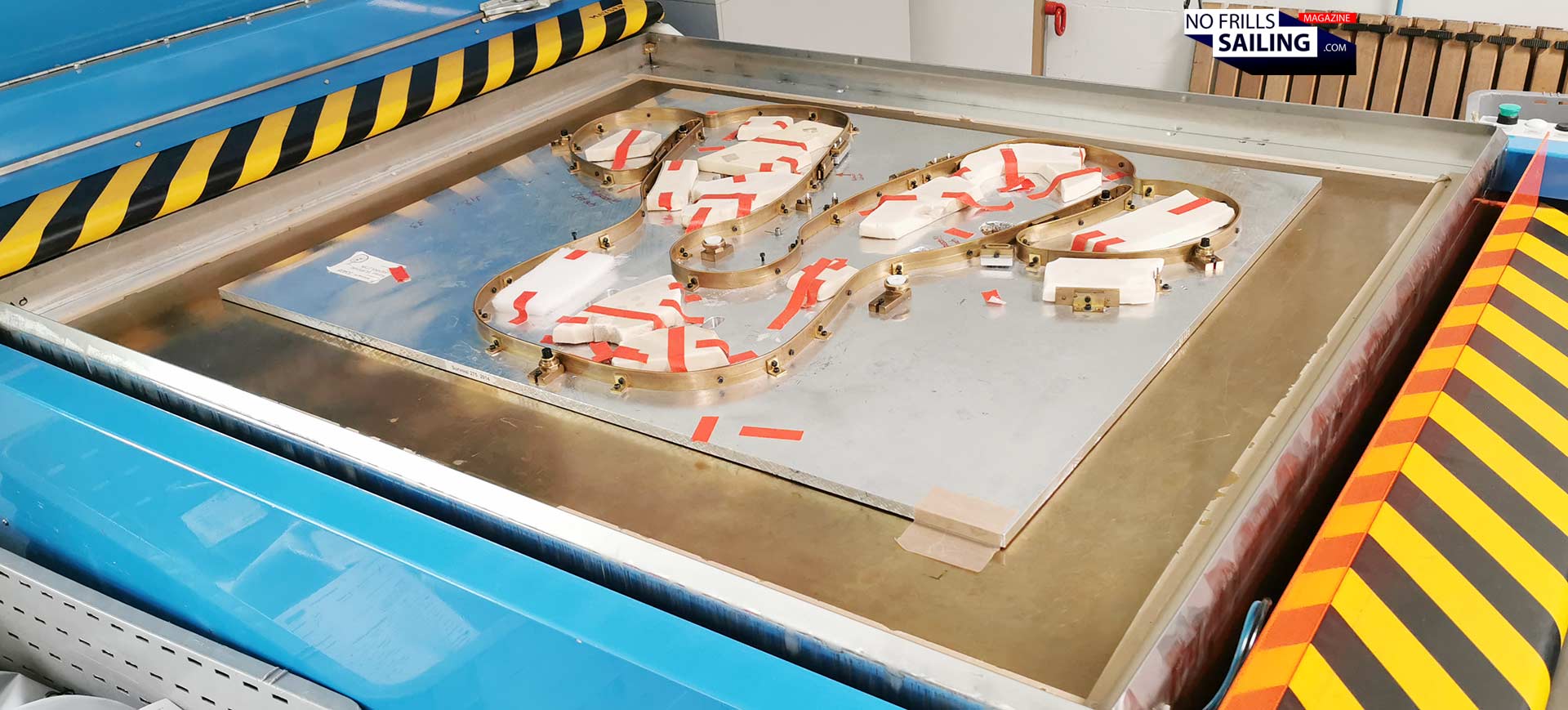
Here, the precision cut fabrics will be positioned exactly. To ensure a perfect fit – just scroll up to the picture before – the parts have leads at the outside with holes. These have to be put over the corresponding pins in the welding machine. The lid is closed, heat applied and yet another float has been manufactured. The welded area has a width of 3 to 4 millimeters so that one can be absolutely sure that the stuff that goes inside will stay inside. At least over a certain amount of time. To make sure that the manufactured floats are tight and working properly, you already know that each single one is inflated and tested over 24 hours to hold its pressure. Every single one.
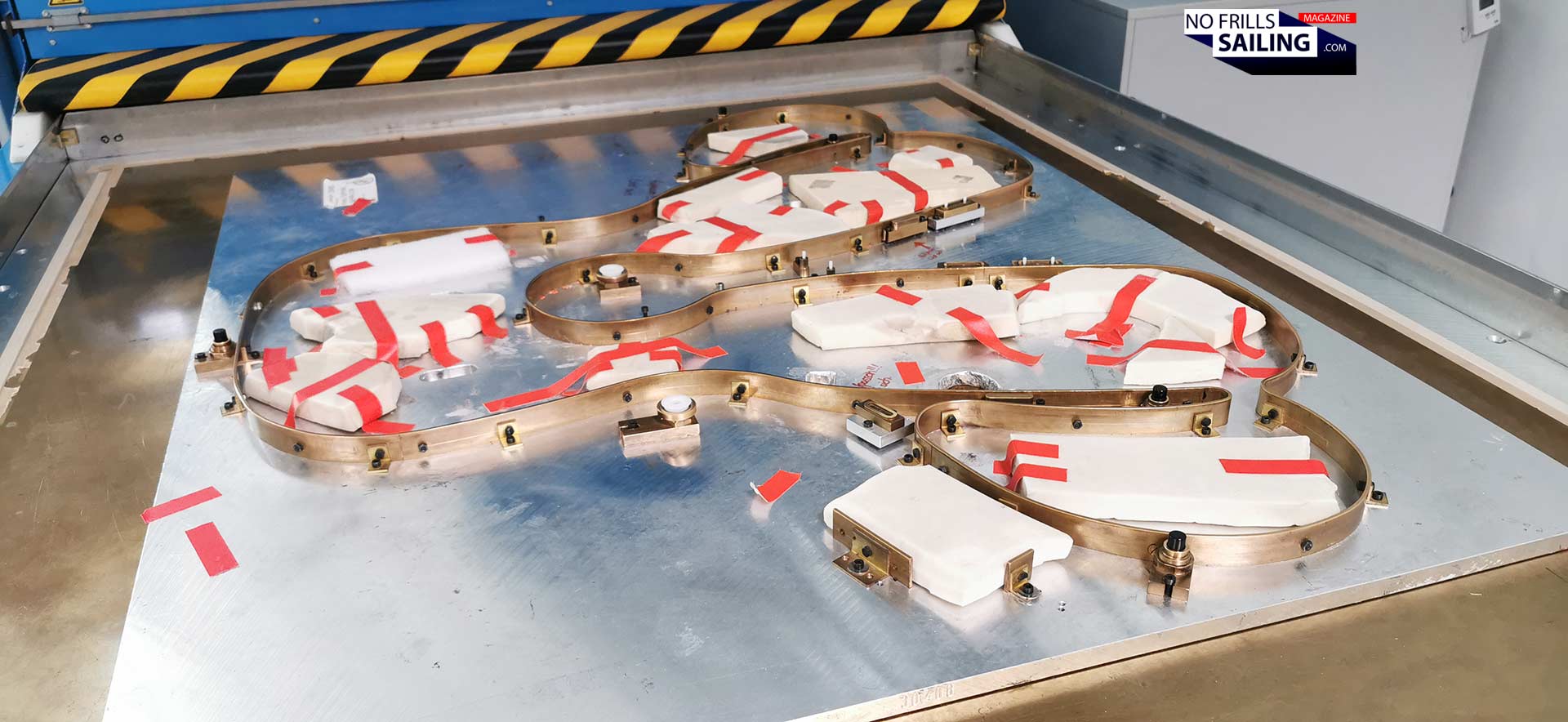
That brings me to another urban myth, besides the “salt tablet”, connected with life jackets: The speed in which these inflate. Most people for some reason think that there is some kind of rapid inflation, or an “explosion”, just like a car´s air bag would do. Well, that´s completely untrue. “Actually not quite …”, Olivier says and leads me to another interesting spot.
The big-boom chamber
Vis-à-vis is a separated room that from the outside looks like an employee´s restroom. But it´s not. This is the destruction testing chamber. As I´ve mentioned earlier, Secumar will run not just the ordinary test program as shown, but will regularly also run destructive testing and excessive load testing. At least one sample of every lot or production chunk will get … blown up. Blown up like your mind when you realize that you´ve missed new articles on NO FRILLS SAILING.com – this is why you should subscribe to my monthly newsletter here! But back to the article …
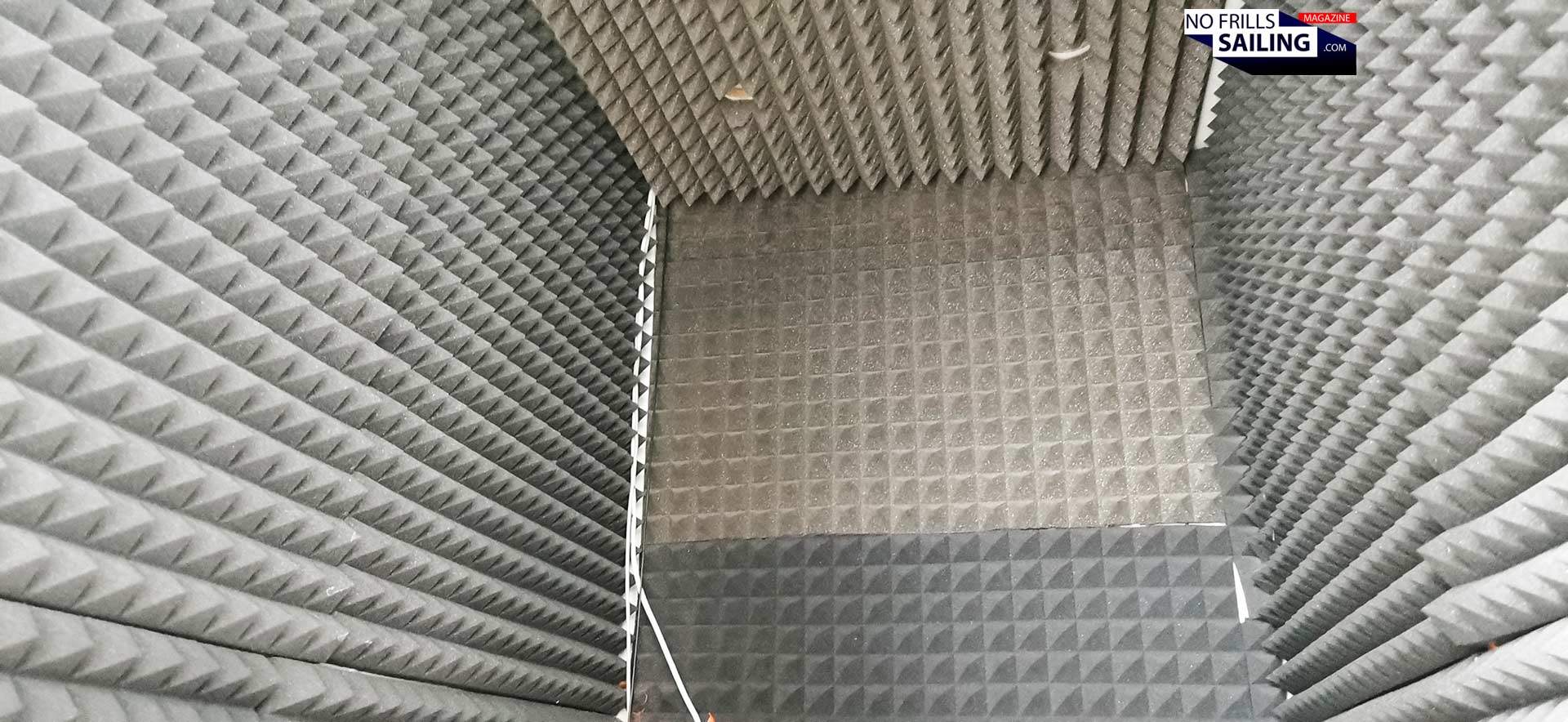
Olivier opens the door to the chamber. Noise cancelling panels cover the whole room. It looks like a mini recording studio at some record company. But I understand: Here the sample products are destroyed with totally unrealistic and excessively heavy loads. For a life jacket that´s of course pressure. There´s a large bucket in that room. Inside we find the remainders of the “victims” of the last tests …
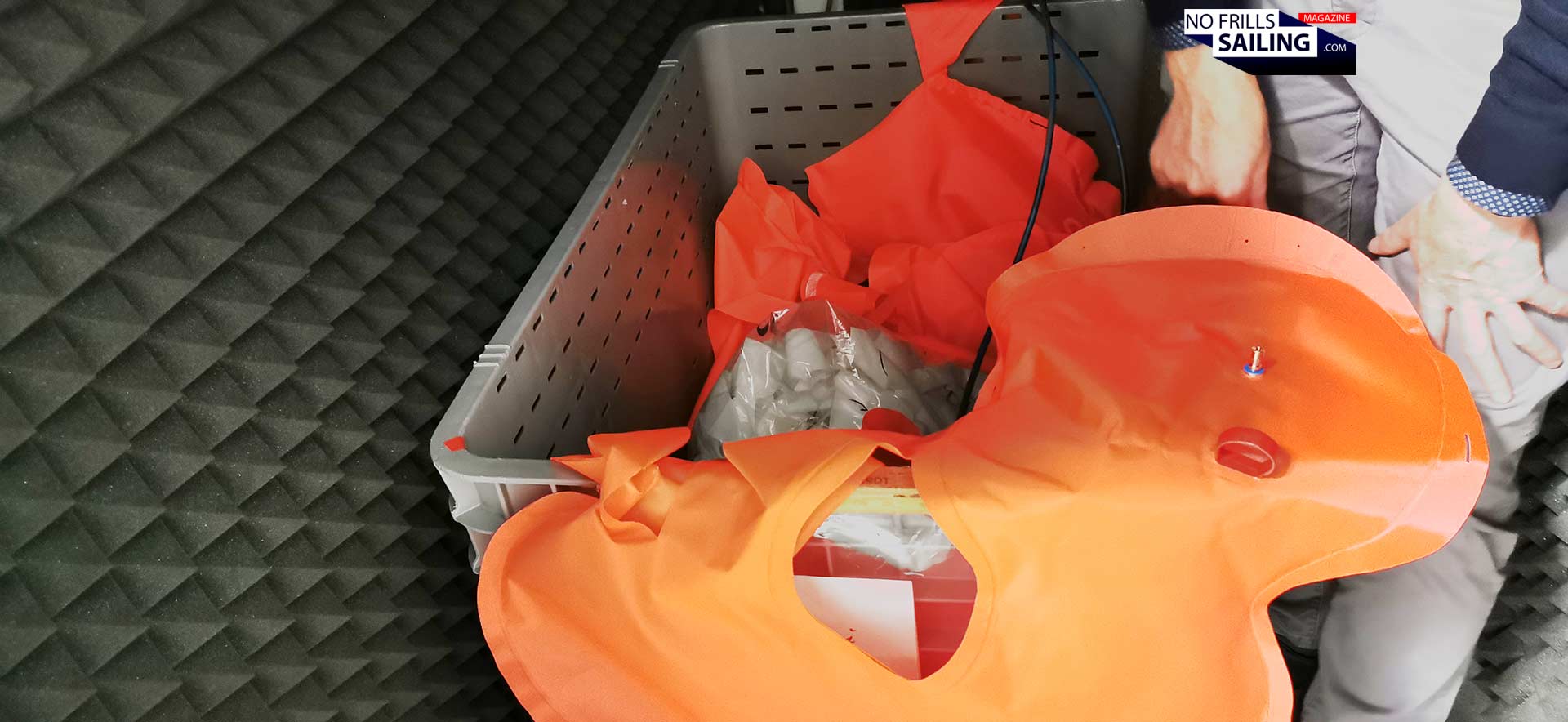
The floats are ripped apart. Gaping holes open up. Olivier shows me some samples of the blown up floats. What´s interesting to see is that none of the samples have been ripped open at the welding seams. This means that the welding process does not create a weakness in the material. All welds are absolutely intact and fine – the life jacket floats explode somewhere else.
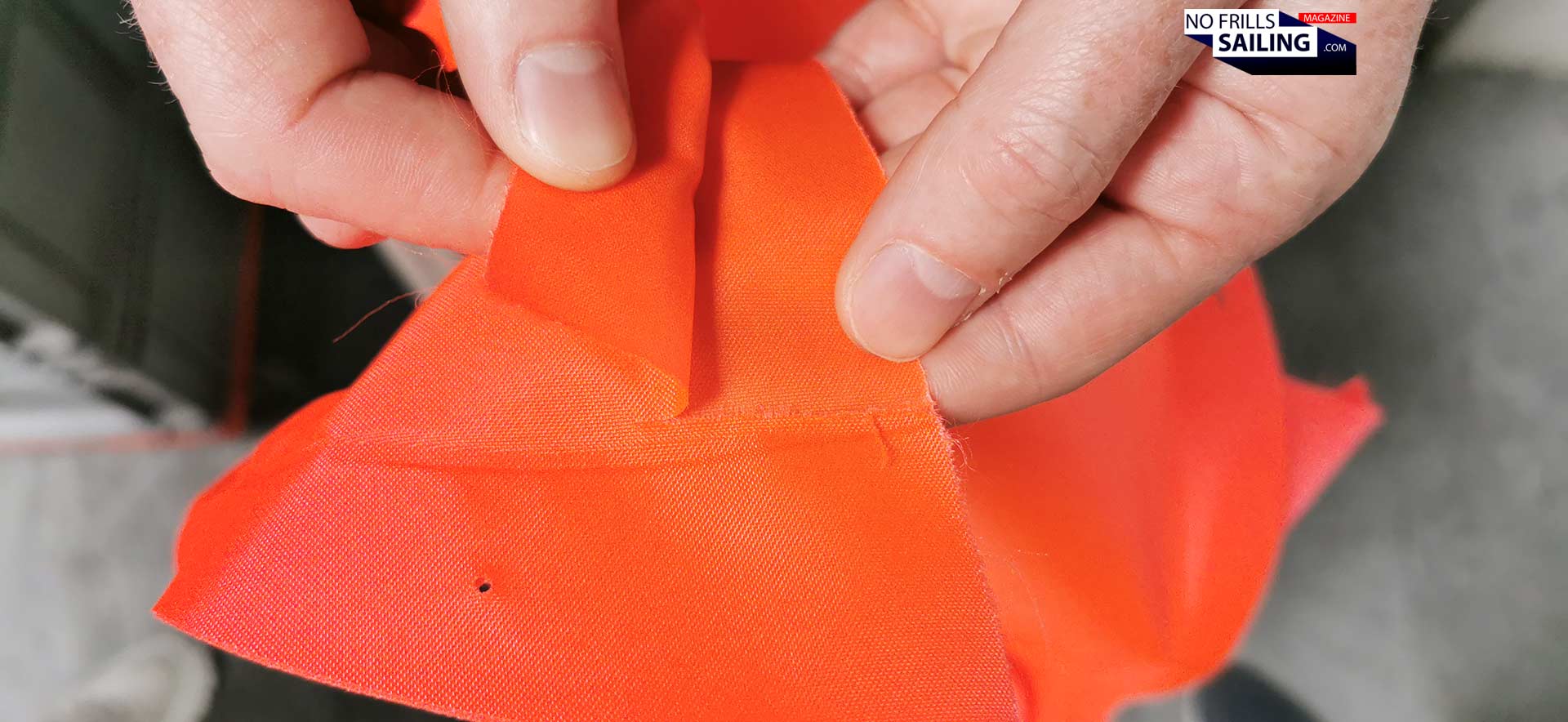
And because of the fact that pumping in so much pressurized air into such a large device – after all a multitude of volumes compared to a birthday party balloon – you can imagine how load of a bang this must create! Hence the noise-insulation. I´m a bit sad that we cannot blow up a float right now, but maybe next time …
The wonderful workshop of Gyro Gearloose
Entering another room, we now completely enter the world of Gyro Gearloose. It´s the practical division of Secumar´s R&D department. Here, all sorts of test-stations are set up, many of which are in frequent use, some will only be utilized for very specific products. For example, one test that is very important is the O-ring excess load.
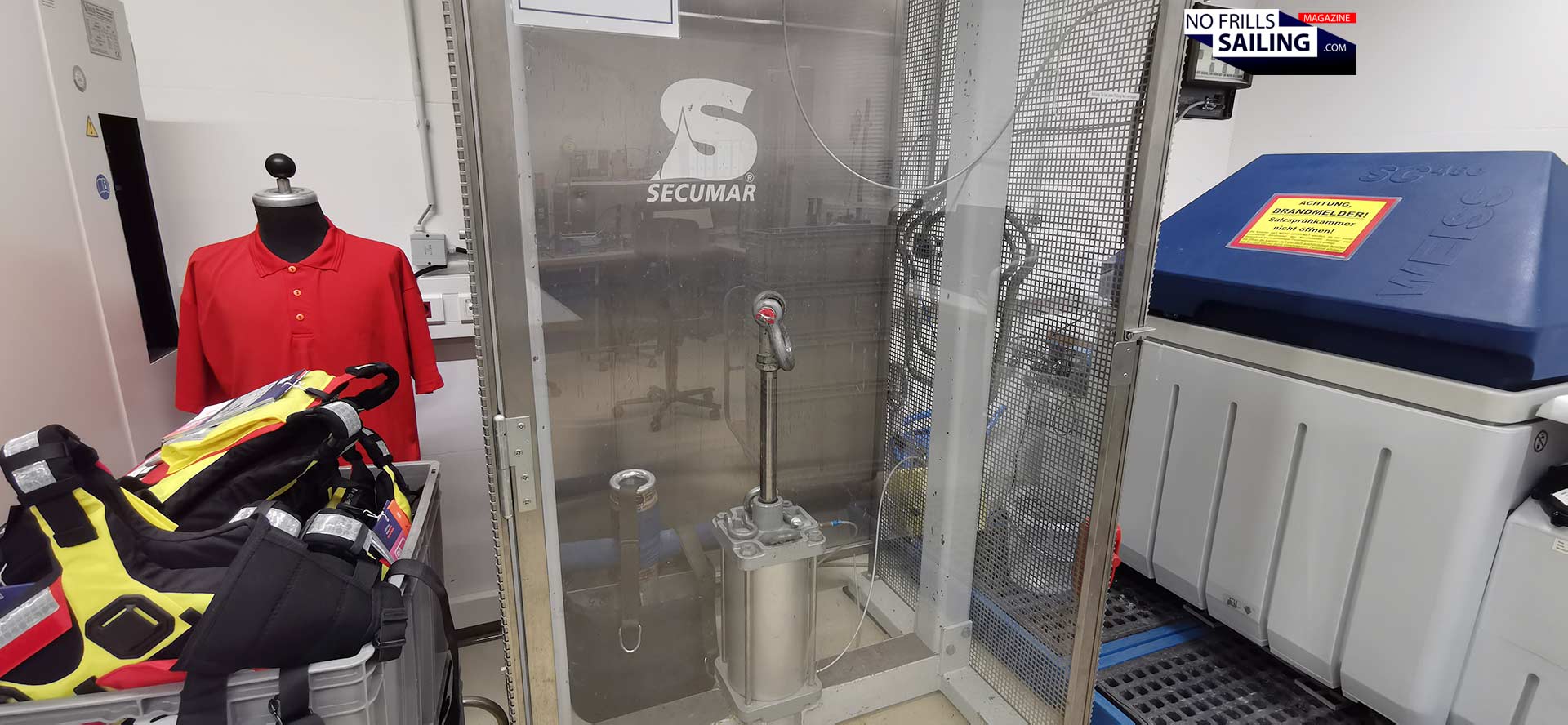
It´s a chamber where a huge hydraulic cylinder basically pulls down in a controlled manner. What is it for? On your life jacket there should be an O-ring. This is a ring where you can attach a tether to. This ring and the supporting structure of the harness must be strong enough to hold your weight plus a lot of kilograms of water that is soaked into your clothing. This device will test the strength of these. A central and maybe most “fun” test Secumar has to offer, of course, is the pool.
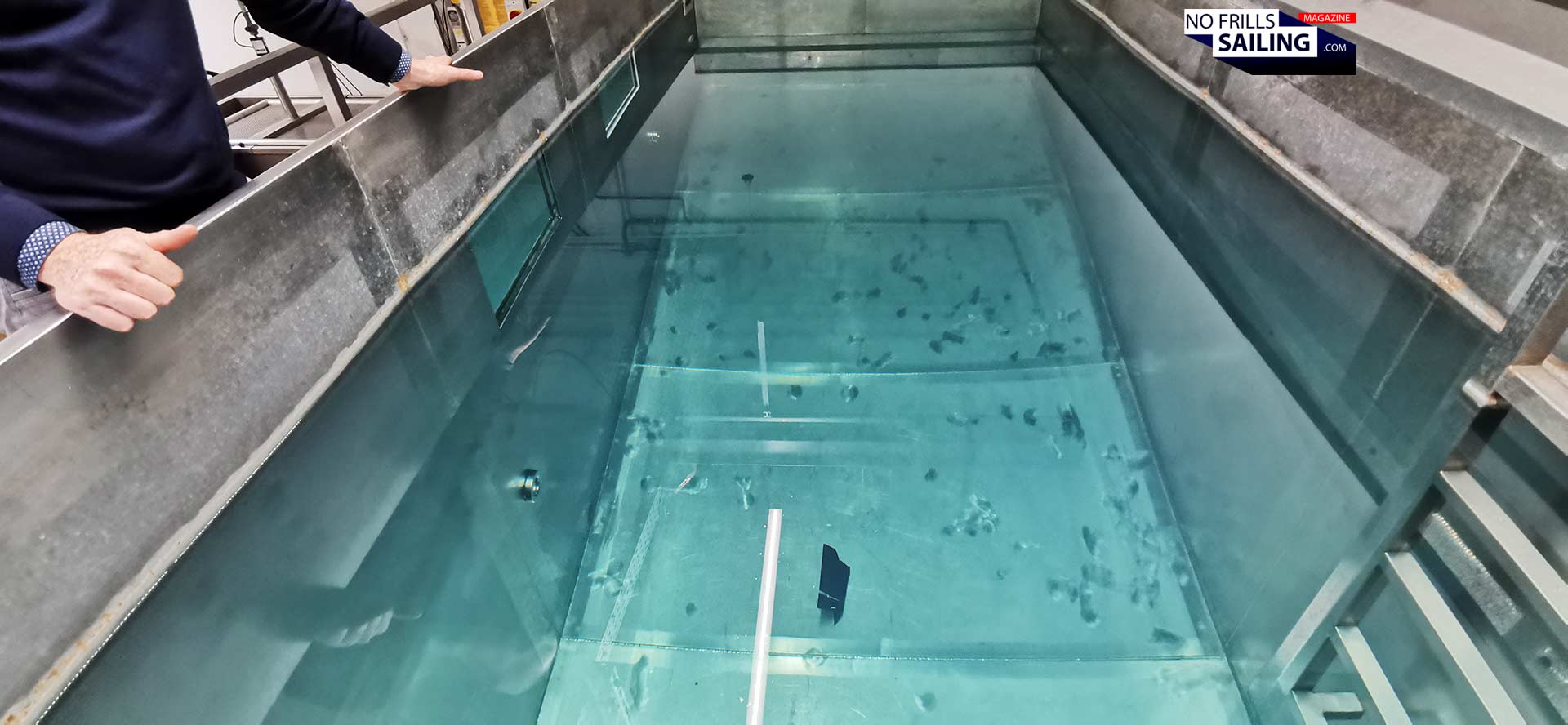
It´s a nice occasion because this pool (and the family of test dummies) is the reason why I decided to exclusively buy my sailing safety gear from Secumar. Back in the day, right after we finished sailing the first leg with our first ever boat, by son fell into the harbor. Schocking moments! In the course of this event I wrote to Secumar – not as a journalist, but as a shocked and concerned father who wanted to know what happenend and why.
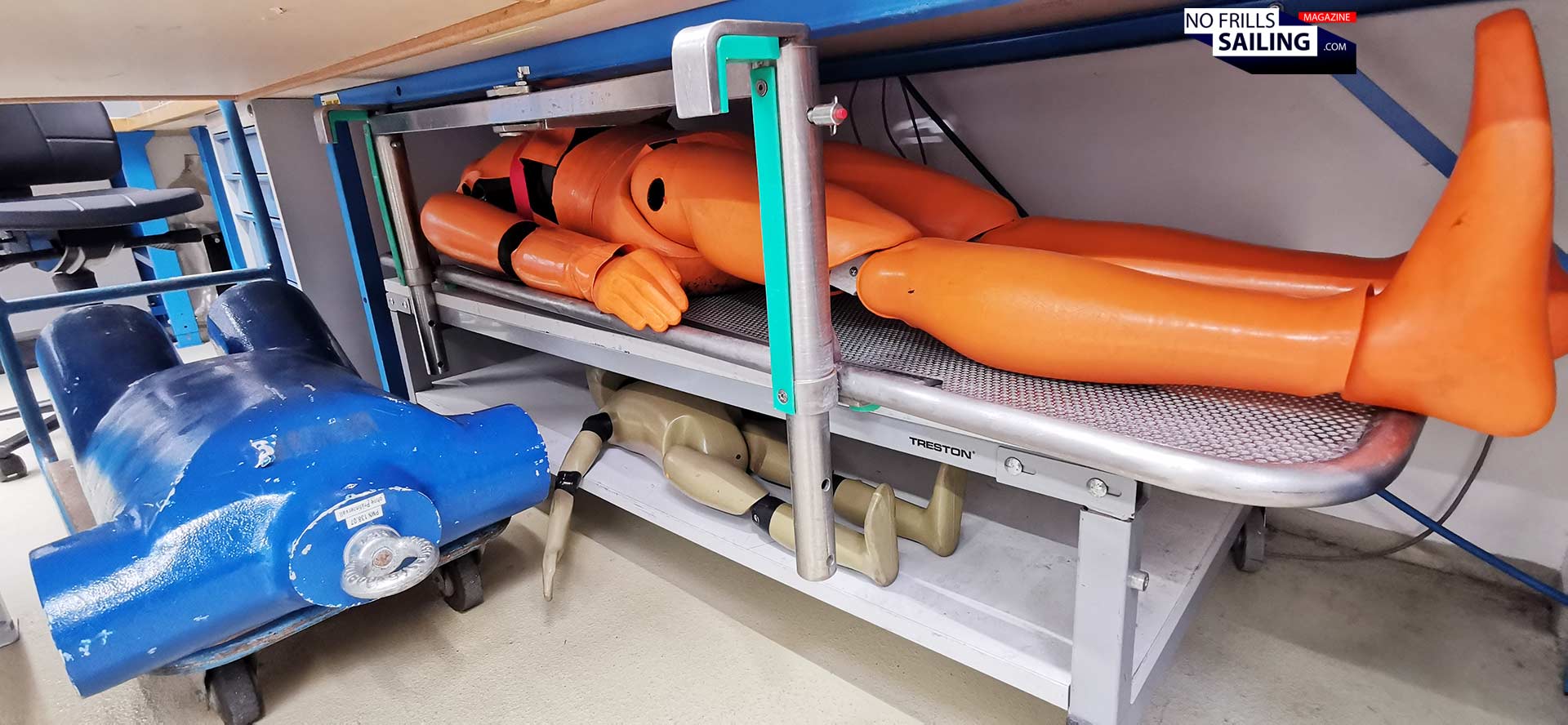
That was in 2016, almost 10 years ago. Back then, a younger Olivier had invited me to come to Hamburg and see the production. The highlight was a series of practical demonstrations with the kid dummy where he showed me what has happened and what went wrong. Also, he trained me what to look for in life jackets and how to make my kids wear them properly. This all happened right here, at the diving pool. Of course, Secumar tests various products, trigger- and inflating-times and such. The floor of the pool therefore was covered with a thick layer of milky cellulose. The leftover of hundreds, if not thousands, of dummy MOB-incidents.
Speeding up time
Apart from these “fun” experiments, the workshop has some other very interesting testing setups to offer. One of which is a literal time capsule. This machine can simulate the salty and moist atmosphere, the high and low pressure, the warm and the cold weather. In this, it can exceed natural thresholds and thus speed up time.
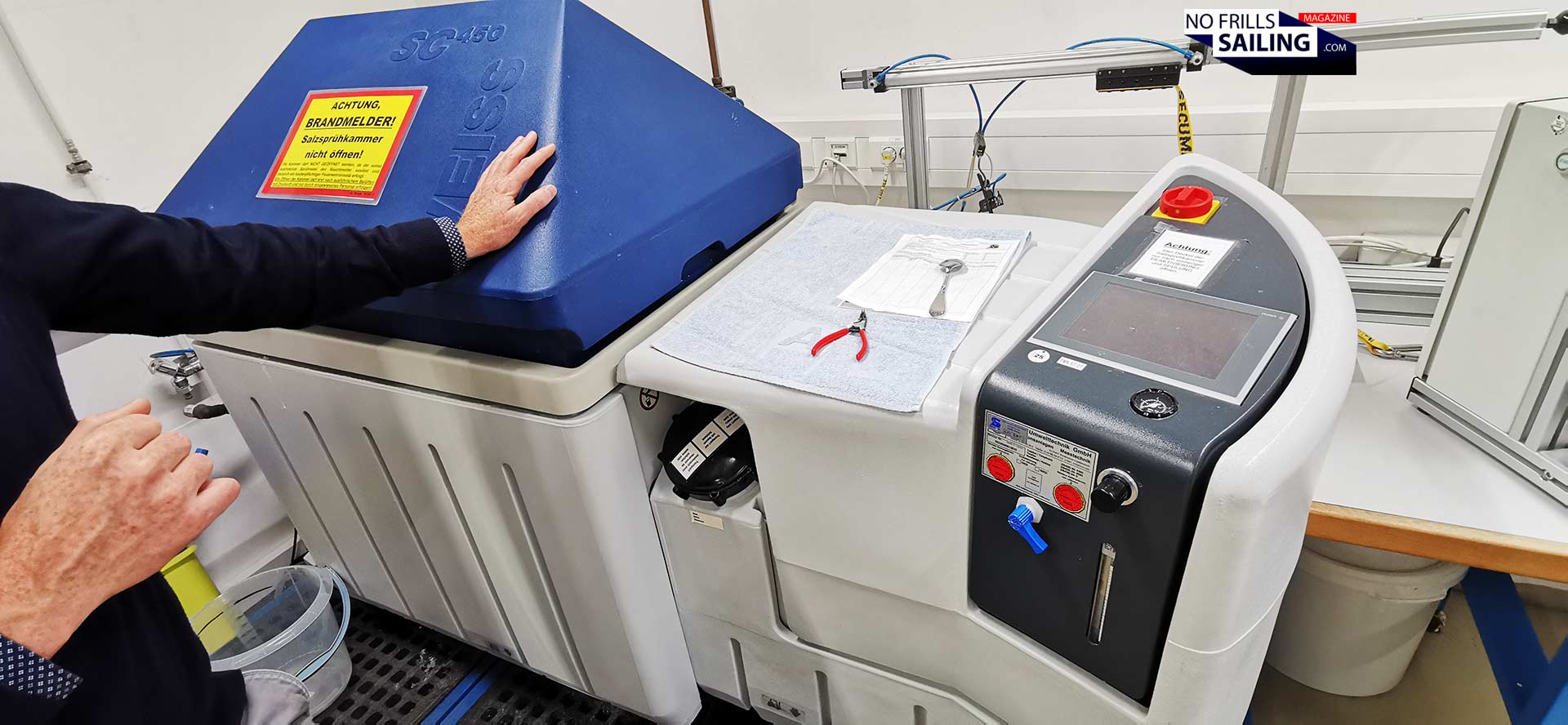
Why is this important? The company want to know how materials behave and may change over time. Like the metal parts, the cartridges and also of course the fabrics. Will the saltwater do harm? When does the stuff start to corrode? This machine can compress decades of sailing in the remotest and wildest areas to a few test days.
Another test they take very serious here is mechanical stress. Imagine an ordinary life jacket aboard a boat. Maybe it´s not treated very well in terms of being handled with care. And I see it myself very often how neglected life jackets in daily use really are: Taken off after a night watch or after berthing, those are often thrown into a locker or to the ground. Staying down there in a locker, it can get pretty violent – with the life jackets thrown about. This can be simulated with much more violence in a purpose built centrifuge, where the products are torn apart and thrown around.
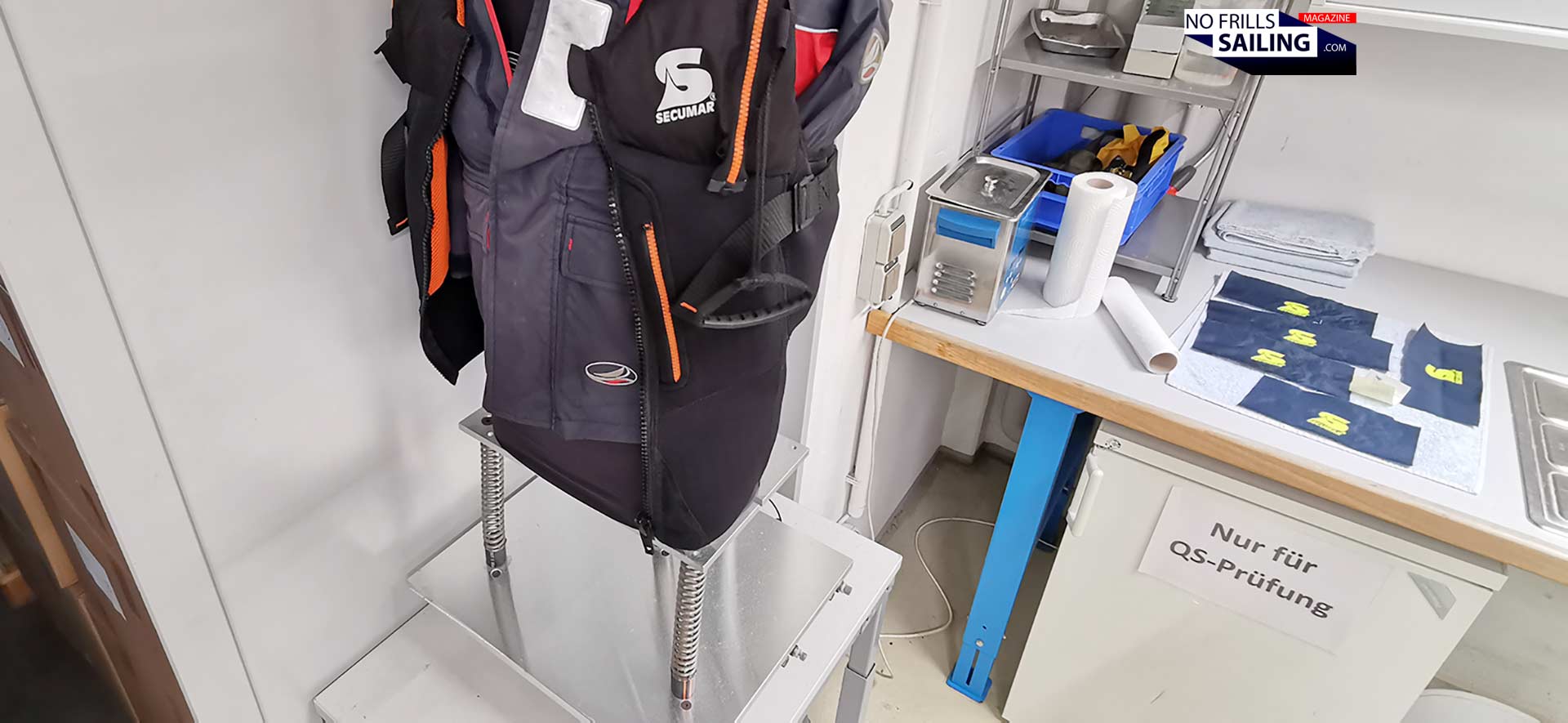
And as it is often not only just the obviously violent motions, but also the little – but constantly ongoing – vibrations, Secumar also has a test for this. Remember my article on the inflator where I pointed out that with cheap made life jackets over time the cartridges often come loose? Little by little they tend to unscrew themselves. And if nobody checks, a CO2-cartridge that has no airtight contact will maybe triggered in case of a MOB, but the whole gas will just be released with no inflation whatsoever. Among others, it was this vibro-test at Secumar which has delivered the proof that that the engineering ingenuity leading to the inception of the proprietary “Positorque” seal and the bayonette-joint solved that problem.
Thousands of units. Meaning thousands of lives.
I could have spent hours more in this test laboratory. Secumar runs more than 15 different tests and checks here in their production, connected with numerous other hurdles their suppliers have to take before their deliveries are even accepted here in Hamburg. In this, we conclude the tour by taking a look at the storage facilities.
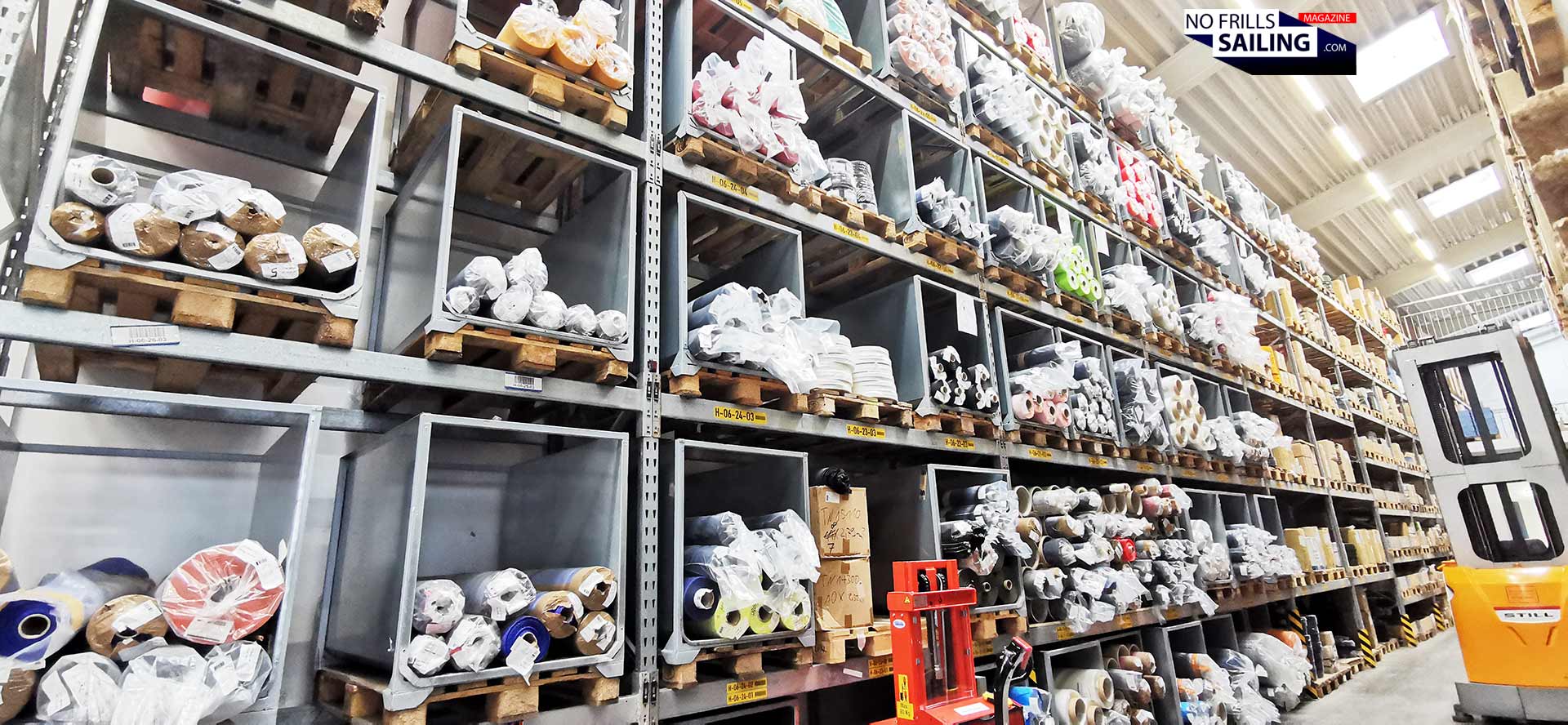
That´s a high storage facility containing thousands of different items, including the raw materials for sustaining months of production. But there´s also a part reserved for the military clients (which I obviously cannot take pictures of) as well as dedicated areas for the commercial customers, like shipping companies. This storage holds a big stock of freshly produced products ready for immediate shipping – which is an art, by the way, as Olivier explains: The life jacket´s clock starts to tick on the day it is assembled. That´s two years until it should be serviced. So naturally, Secumar tries to limit stockpiling.
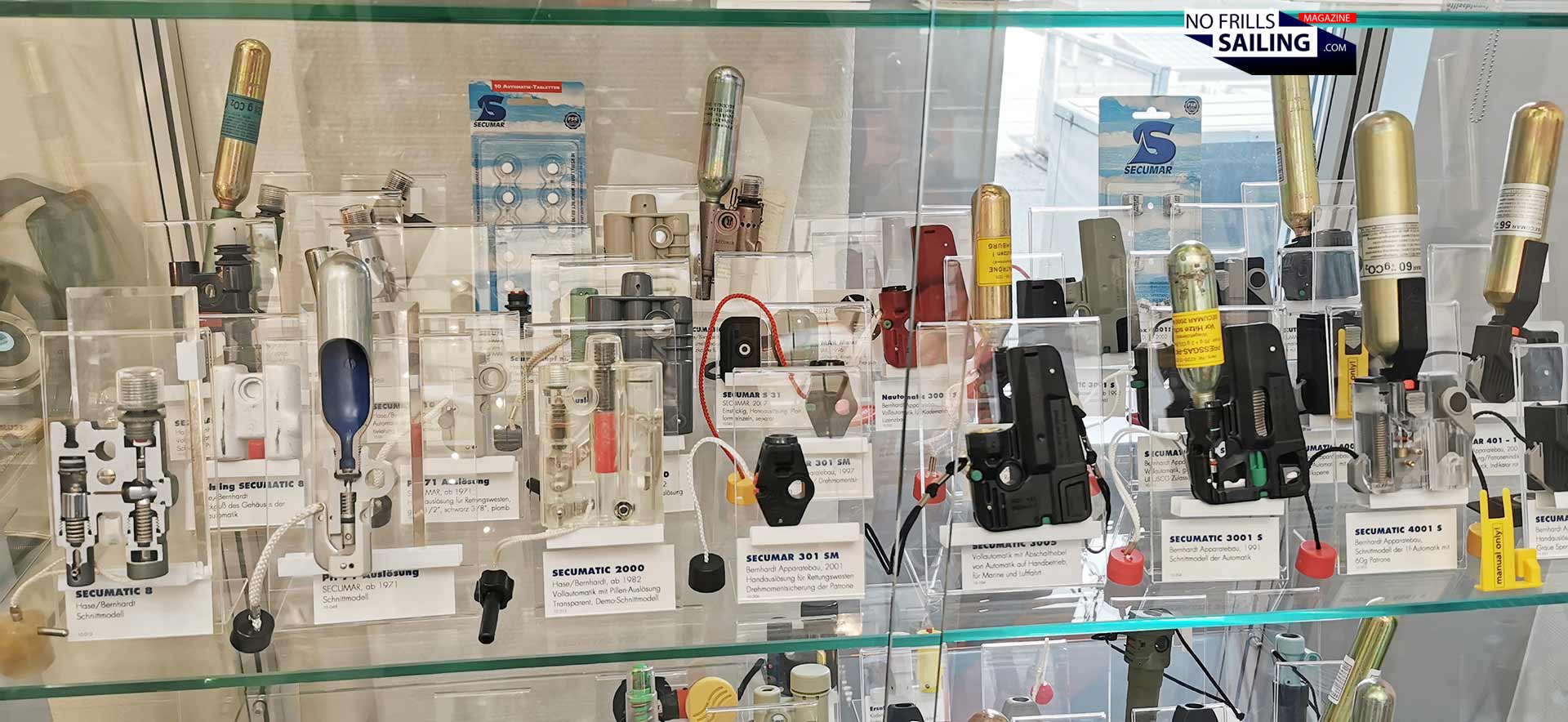
This all doesn´t come out of nowhere. Of course. Secumar will celebrate their 100th annieversary in 2026. That´s 100 years of industry leading and much more, of leading the forefront of safety at sea. In fact, it was the grandfather of todays CEO who, under the impression of the awful losses of both the World Wars and the tragic sinking of the big sailing ship PAMIR invented the automatic life jacket. The development of the trigger devices as well as decades of historic – but at their time prime – products can be seen in the company´s museum.
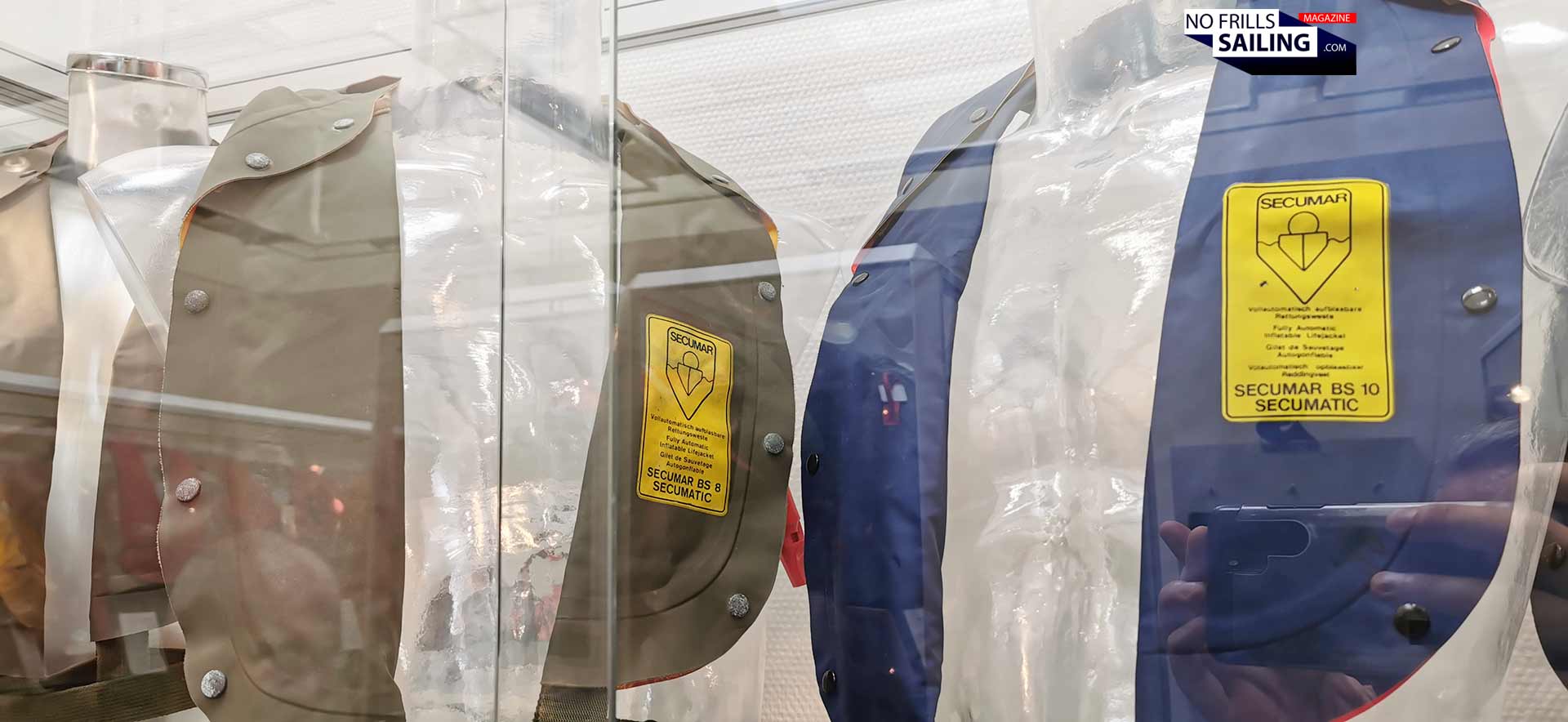
A place these people can rightfully be very proud of! Constantly striving to improve their products, the safety, fail-safe mechanisms and quality has made Secumar the prime brand for life jackets and floating devices. This goes from submarine crews to professional shipping, from leisure sailors like myself to windsurfers and also includes dogs! Yes, there is a new life jacket for your beloved sailing dog.
What´s your family´s life worth?
I´m not frequently talking about prices, money and budget here on NO FRILLS SAILING.com and I won´t change that. Because I assume that you, dearest reader, assume and know very well, that sailing is a luxury occupation and that it is not a cheap matter. But in case of Secumar I will make an exception: Yes, Secumar products are among the most expensive life jackets you can buy. A cheap low-brand 150 N automatic life jacket in Europe costs as little as 49 Euros. Including 19 percent VAT! Secumar´s cheapest entry level product has 170 N and clocks in at 199 Euros …
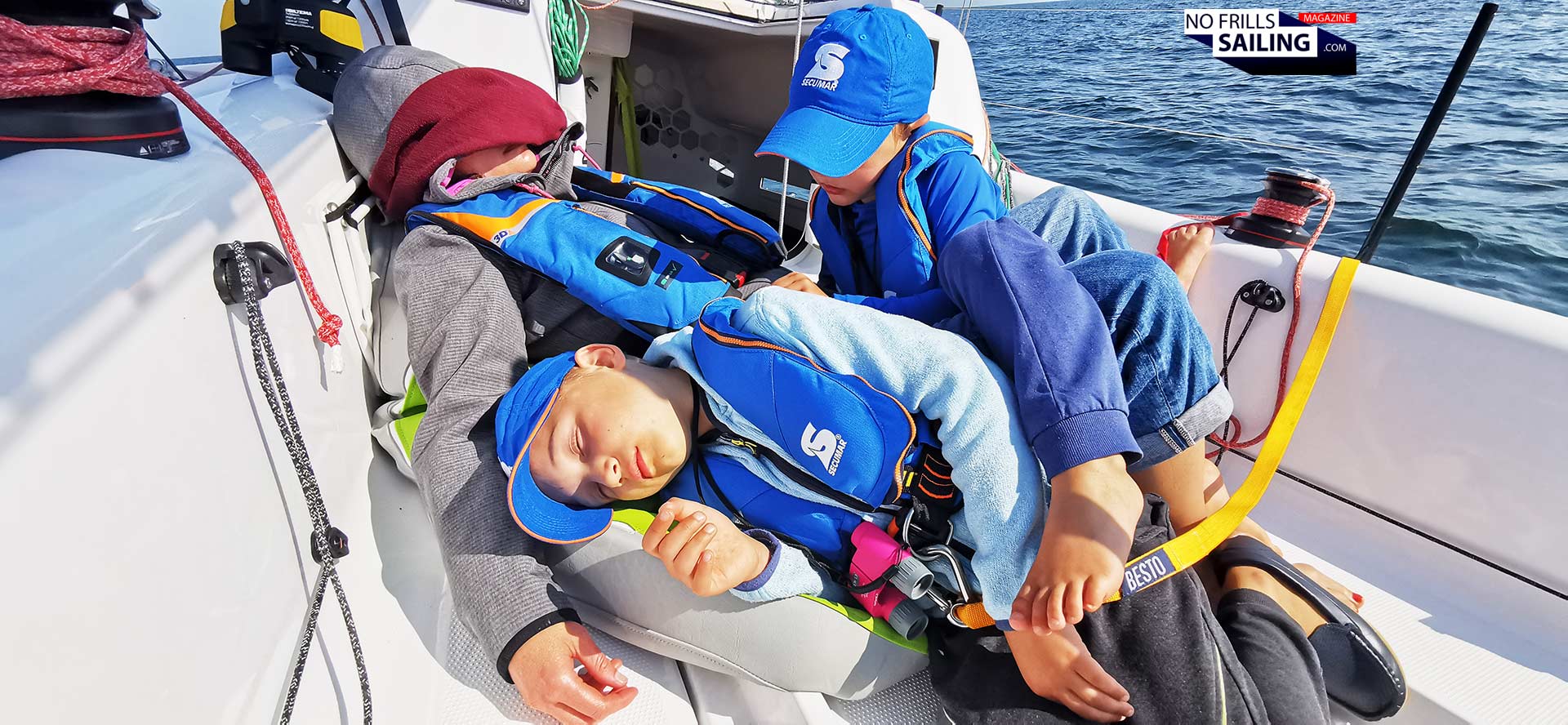
But what´s the safety of your family, of your loved ones, of your kids and wive worth? What´s your own life worth? Apart from the social aspect, the “buy local” and “Made in Germany”-stuff, apart from their 100 years of experience and competence – having seen how meticulous and passionate these guys are about quality and failsafe product functionality, I mean, how can I not be absolutely sure that this is the product I go for?! Saving a couple of hundred bucks with cheap safety equipment is something that shouldn´t be of any concern here. And as you can see, on my boats, only Secumar life jackets are used. I am a brand snob, I know: There are many brands I prefer over other. I am sure that´s something you do as well. But in this case, my preference is not negotiable. And you´ve seen why.
Check out all articles related to life jackets and Secumar by clicking on the hashtag #secumar
You might also want to check these related articles:
How it´s made: A life jacket
Life jacket drills test and drills for sailing kids
First aid lifesaving response in case of kid´s drowning