Concluding my three-article series about Outremer catamarans, I chose a production detail which I found decisively interesting whilst visiting the shipyard in La Grande Motte. You may have read my various posts about manufacturing a glass fiber reinforced plastic boat and specifically the articles about the sandwich core production. Here at Outremer, I noticed that they had stepped this technique up a notch …
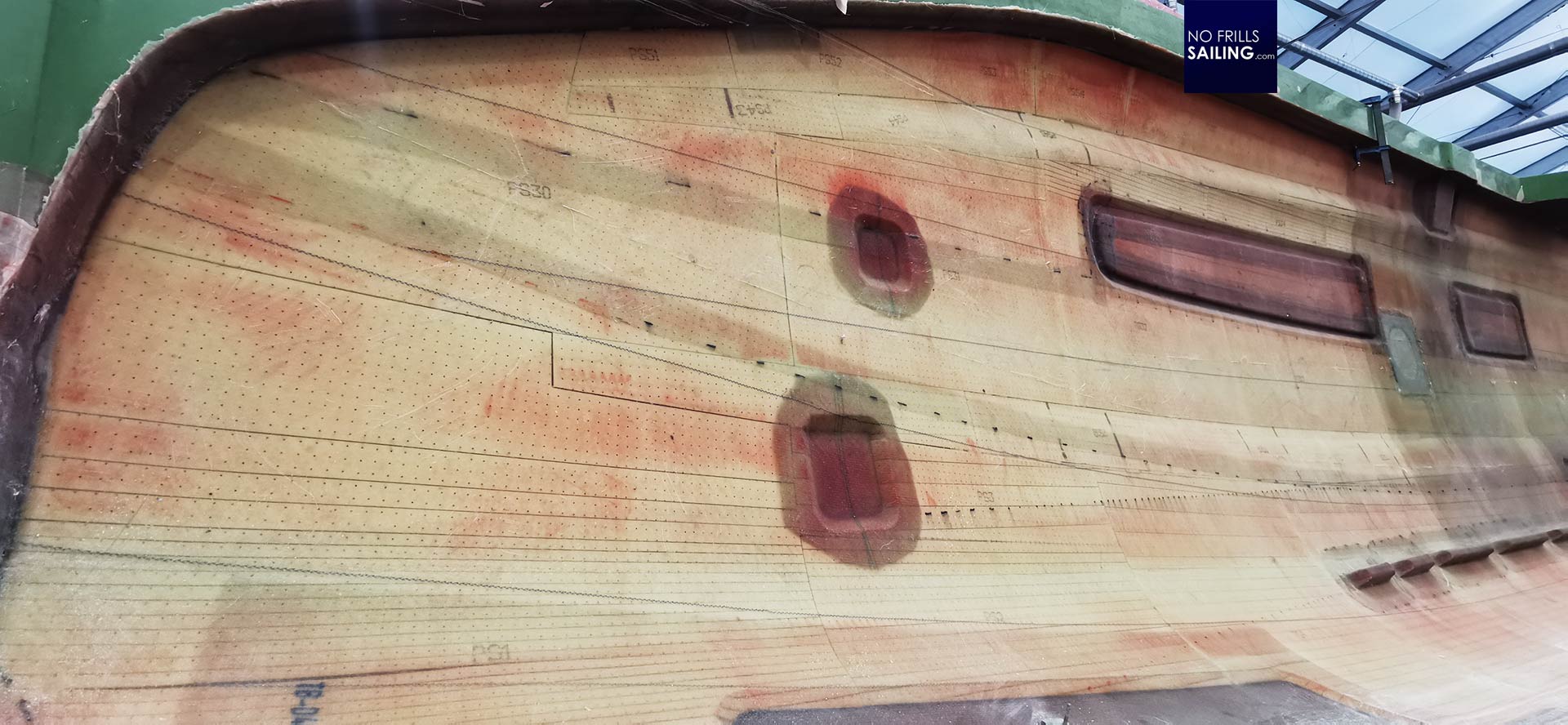
For most sailboats I´ve seen in shipyards being made with a sandwich core construction, disregarding the material in use, all of them had been made with pre-cut core mats. Those are basically made of a plastic gaze onto which cubes of the core material are fitted. The idea of those pre-cut “cubical” mats is that rounded shapes can easily be fabricated, saving a lot of time, hence money. Not so with Outremer.
Massive lamination vs. foam core sandwich
But let´s start with a short recap of why, how and where sandwich core layup is used in modern boatbuilding. During our shipyard visit, the guides had prepared samples of the different types of lamination products. First is the “massive” GRP layup, of which we can hold, touch and feel a sample. It´s about one centimeter thick and one can clearly distinguish the multiple layers of hardened glass fiber mats.
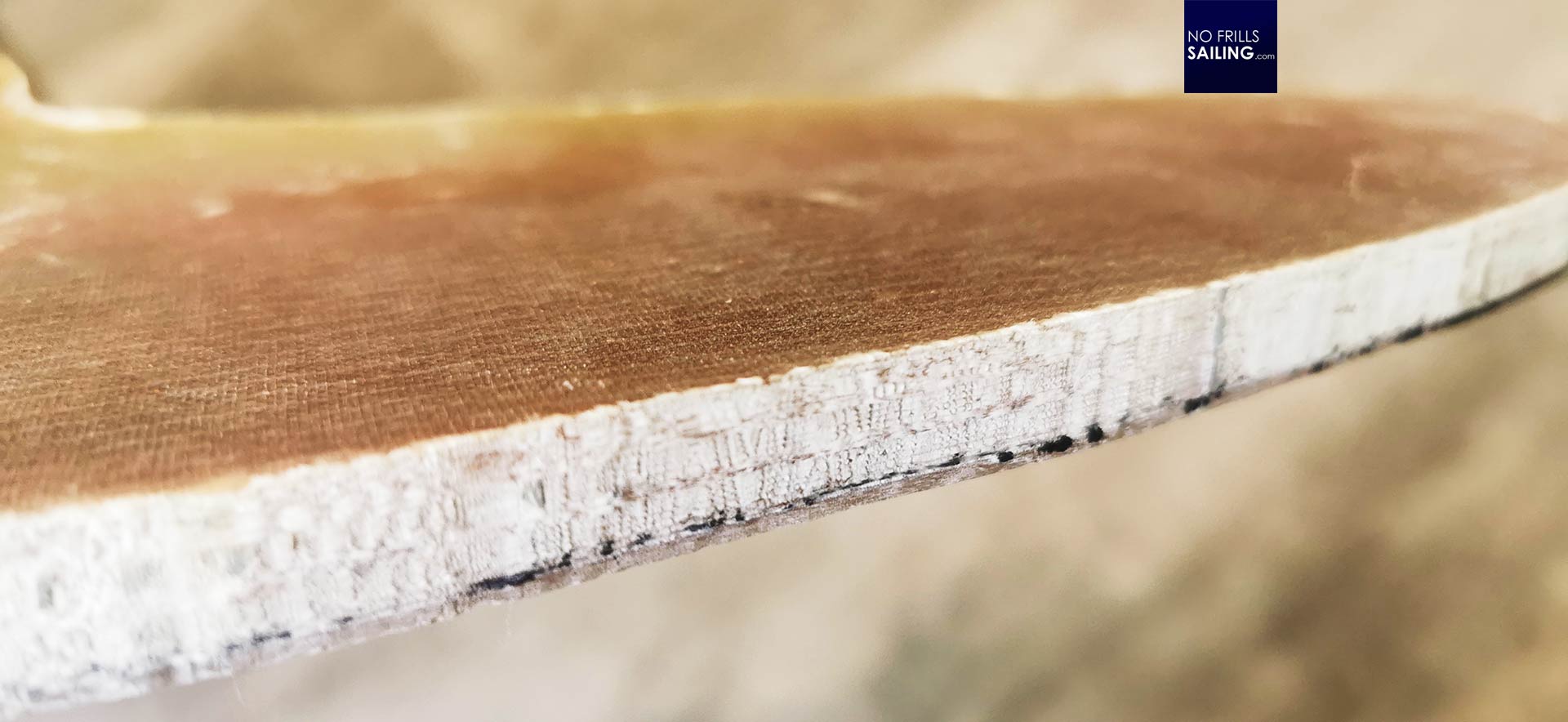
Massive lamination is still in use, predominantly at the front and bottom of the hull. Basically, all areas which need to be as strong as possible. Areas where the keel is attached, for example, and all areas where forces are induced from different directions. The pro of massive lamination is a very rigid, hardened, impact-resistant and compacted material. On the other hand, massive laminated GRP is very heavy. Remember the good old days of the first and second generation GRP-yachts with massive laminated hulls as thick as one´s forearm? Those hulls can withstand even the bloodiest groundings and rocks, but are as heavy as hell.
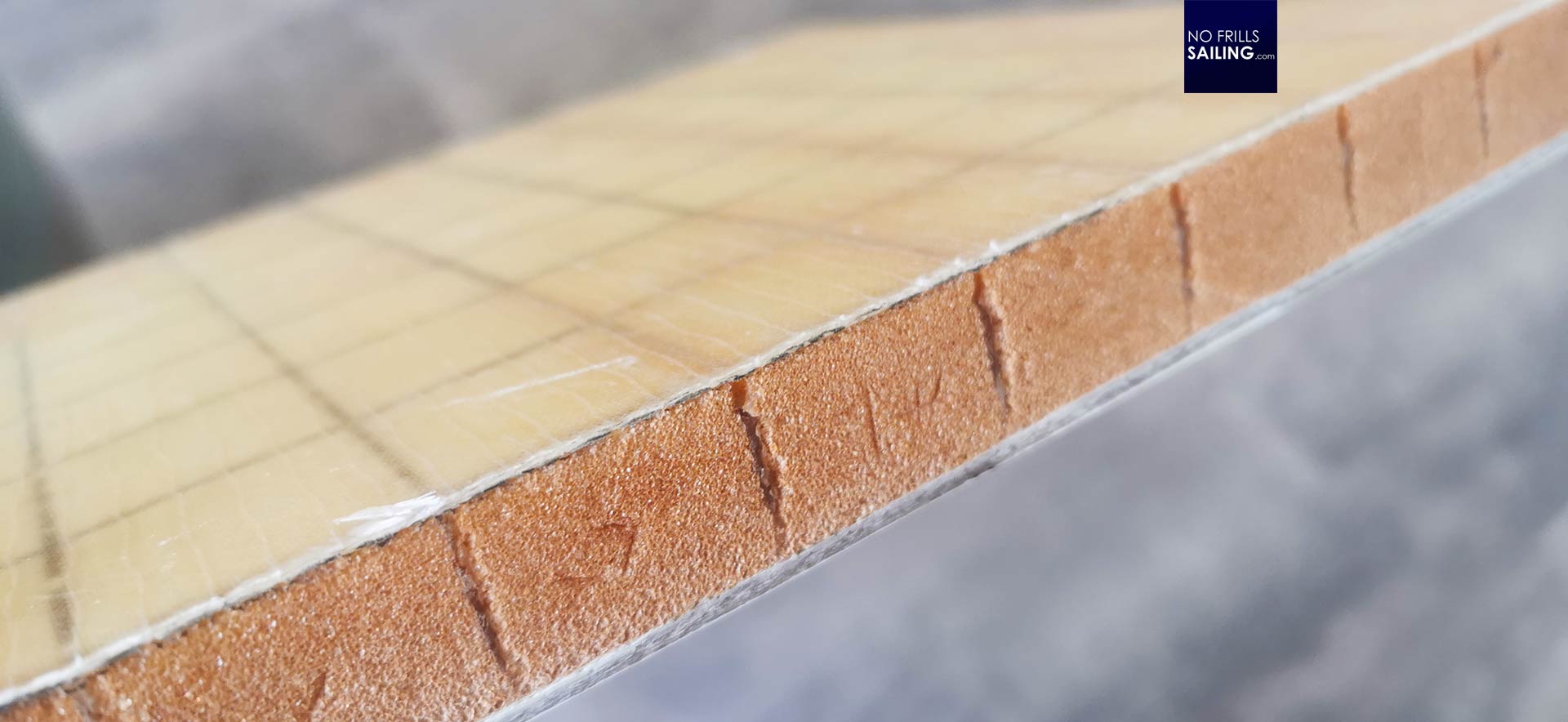
Sandwich core lamination is the solution to reducing weight. And I mean massively reducing weight! By “splitting” the GRP mats into halves and inserting a lightweight core material in between, this is achieved. Now, here the previously mentioned sandwich mats come into play. Either natural core material, like Balsa or Cork is used, or synthetic materials like PET foam, PVC foam, PU foam and many more. The intention is to have the core material soaked with resin, harden it and achieve a solid, stiff and hard – but lightweight – structure.
The problem with pre-cut foam core material
The downside of such sandwich areas is that they are only rigid when loaded with stress from one particular direction, just like Carbon fibers. Upon blunt or pointed impacts, sandwich surface tends to get damaged easily. Knowing this, it´s just a tradeoff for the lightweight properties. But there is a problem more “serious” to it – at least for Outremer.
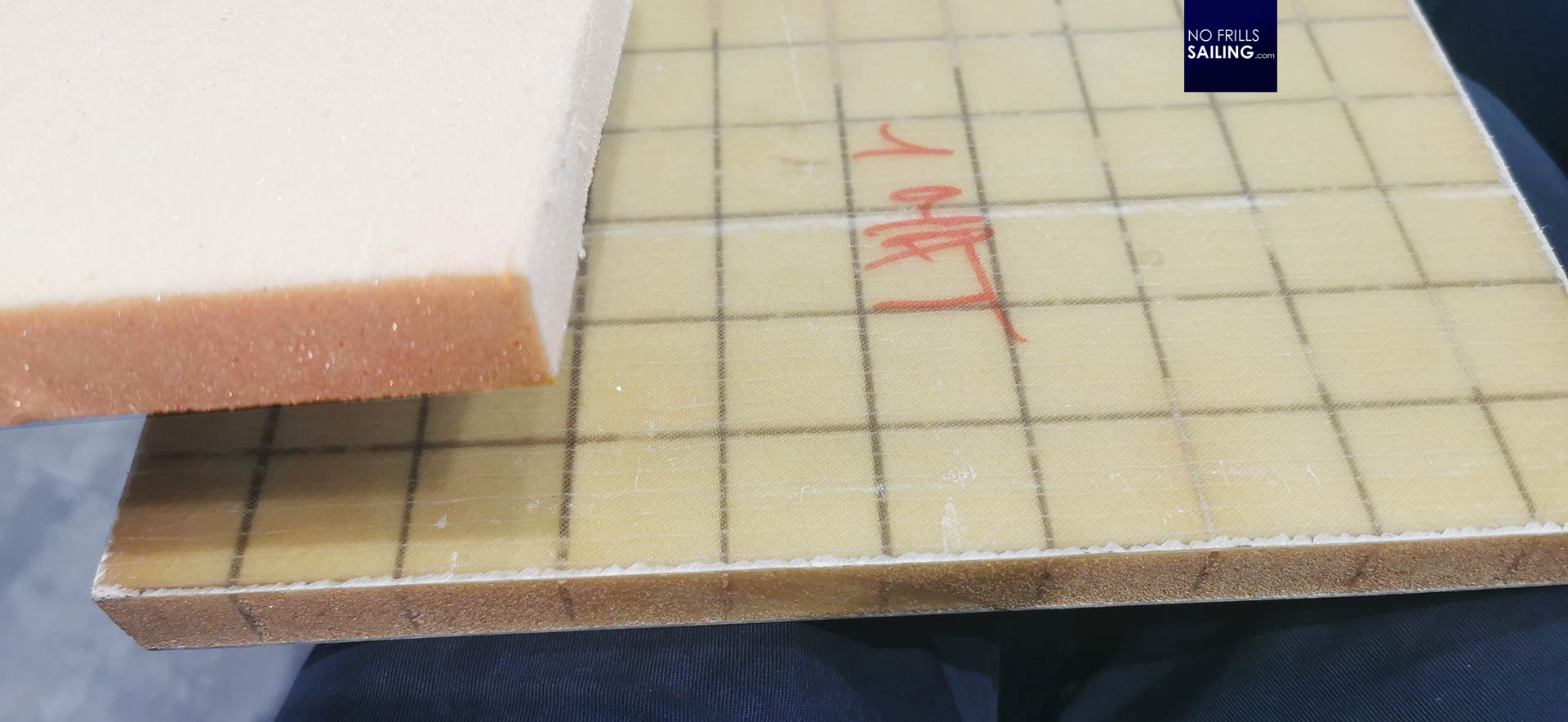
The pre-cut PVC-“cells” of the core material will always have one or more millimeter of clearance. This is filled up with resin that will harden and turn to “glass”. On the one hand – especially with Balsa core material – those glass “barriers” are welcome since they block water from entering neighboring cells in case of damage and moist intrusion. But for Outremer, focused on making their catamarans as lightweight as possible, this is a problem. Synthetic foam core material cannot rot anyway, so these countless intermediate glass barriers are a worthless waste of previous material and – worst of all – adding to the boat´s weight.
Using uncut PVC foam core
The solution to this problem, and here´s the reason for this article, is to utilize uncut foam mats. Standing above one of the deck molds in the shipyard that is currently prepared for vacuum infusion process, we can clearly see the red-ish foam core areas prepared. These large foam parts are embedded within the massive glass fiber layups.
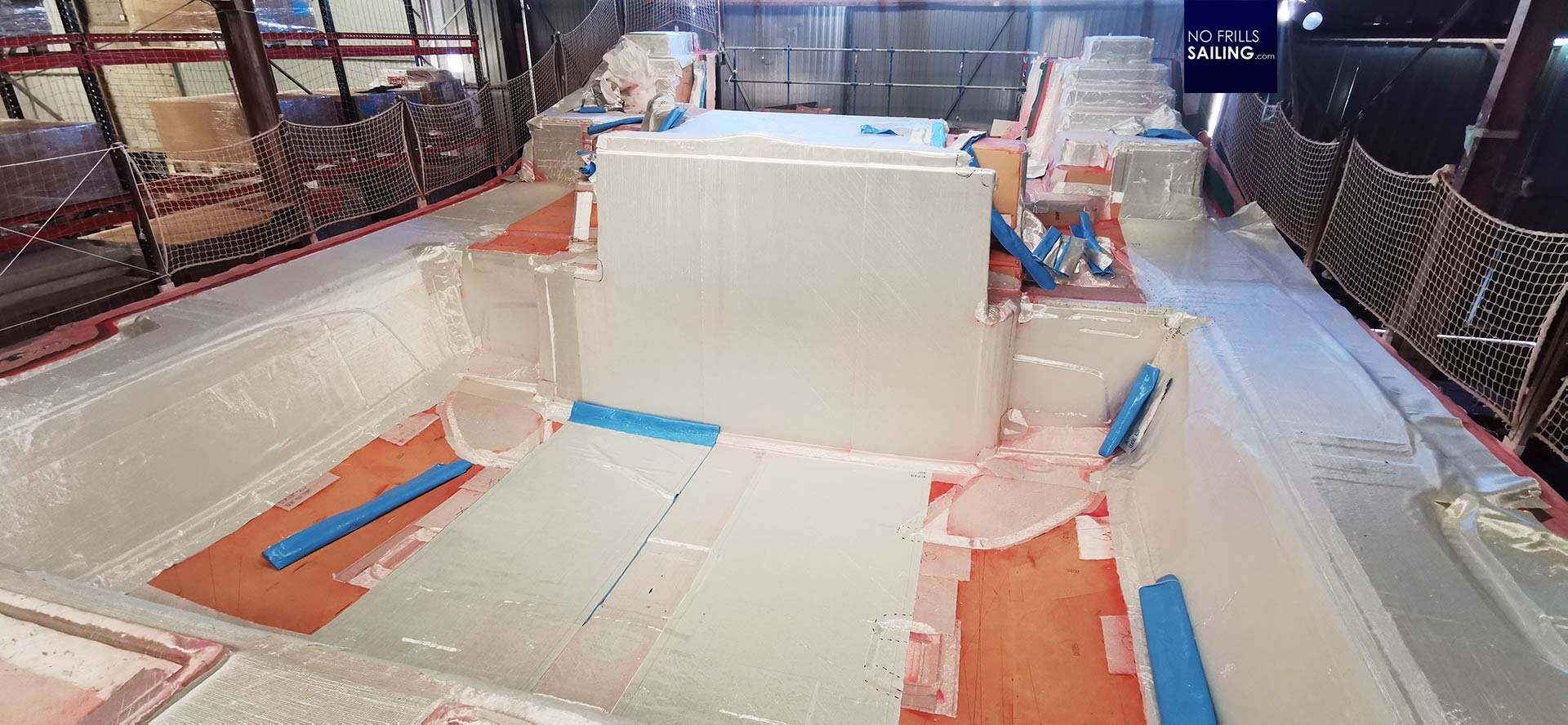
As our guide assures, each catamaran has a very specific and pre-determined plan of where which GRP-mat and fiber-type is to be used. Also, the direction in which the garment has to point as well as the exact positions of each of the mats are meticulously planned as pre-calculated by the structural designers. I found interesting to hear that the shipyard, although everything is planned and arranged already, will discuss the individual layout of the running rigging with each client buying a catamaran. Thus, sometimes, locations of winches may differ and so does the layup of those areas as well. Now, looking very closely at those PVC foam sandwich parts, I can clearly see a lot of cuts going through these red areas. Leftover? By chance? Not at all!
Chaotic cuts? Delicate order!
These cuts appear to have been applied randomly, rather chaotic. But, as the guide assures us, they are not. The raw PET and PVC foam material arrive from the producers as big plates. The suppliers have big machines which got processed the 3-dimensional CAD data of the whole boat. Applying those cuts to the individual parts make them bendable in the first place, but also as those cuts are set digitally controlled by a computer, each one is as accurate as can be.
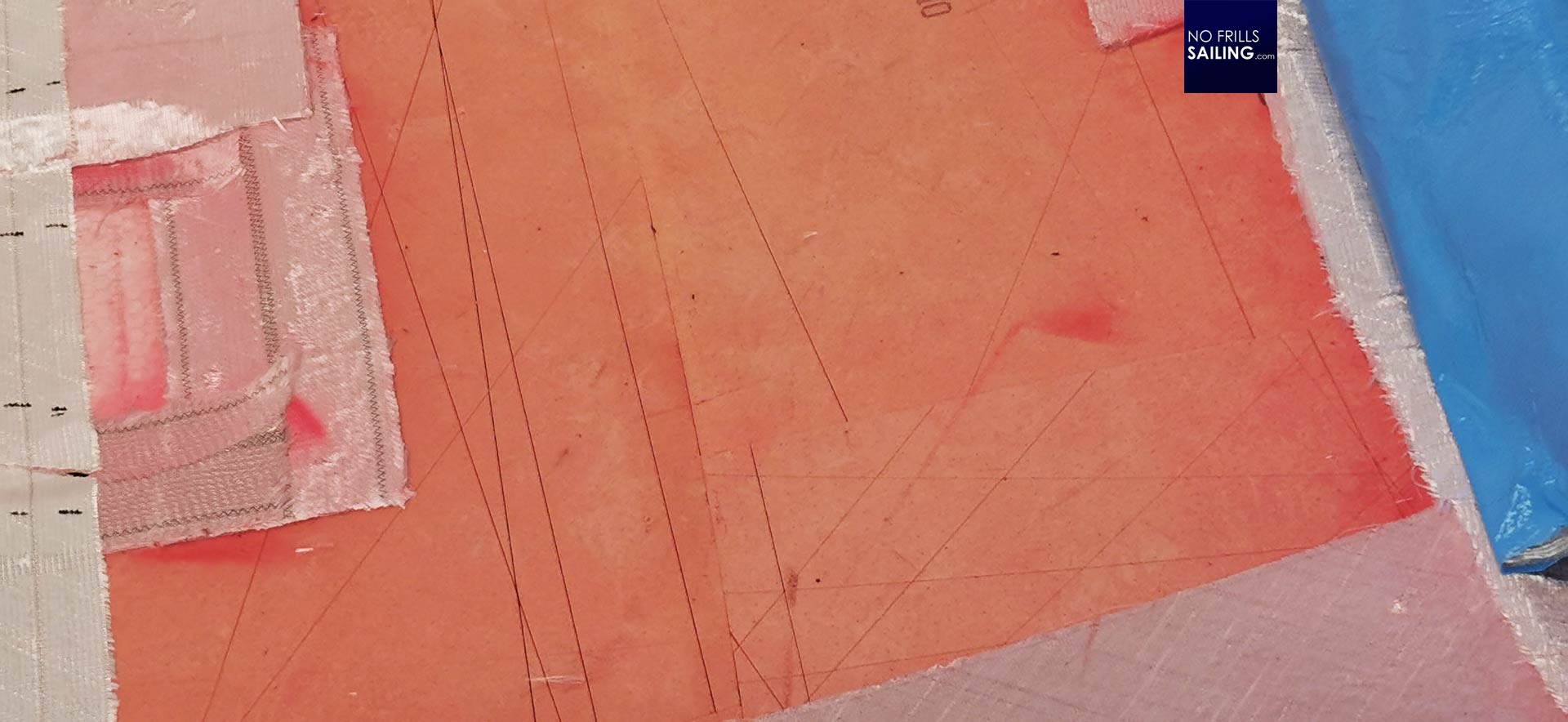
It may seem to be chaotic but those criss-crossing cuts all over the sandwich material follow an exact plan. When covered by a number of layers of GRP-garment and infused with resin, everything will harden through and become a solid, stiff unit. Looking at the finished end-product, still uncovered by some topcoat paint, it may still look chaotic but it also reveals that the idea of saving weight and increasing stiffness by reducing the resin-filled gaps between the foam parts pays off just nicely.
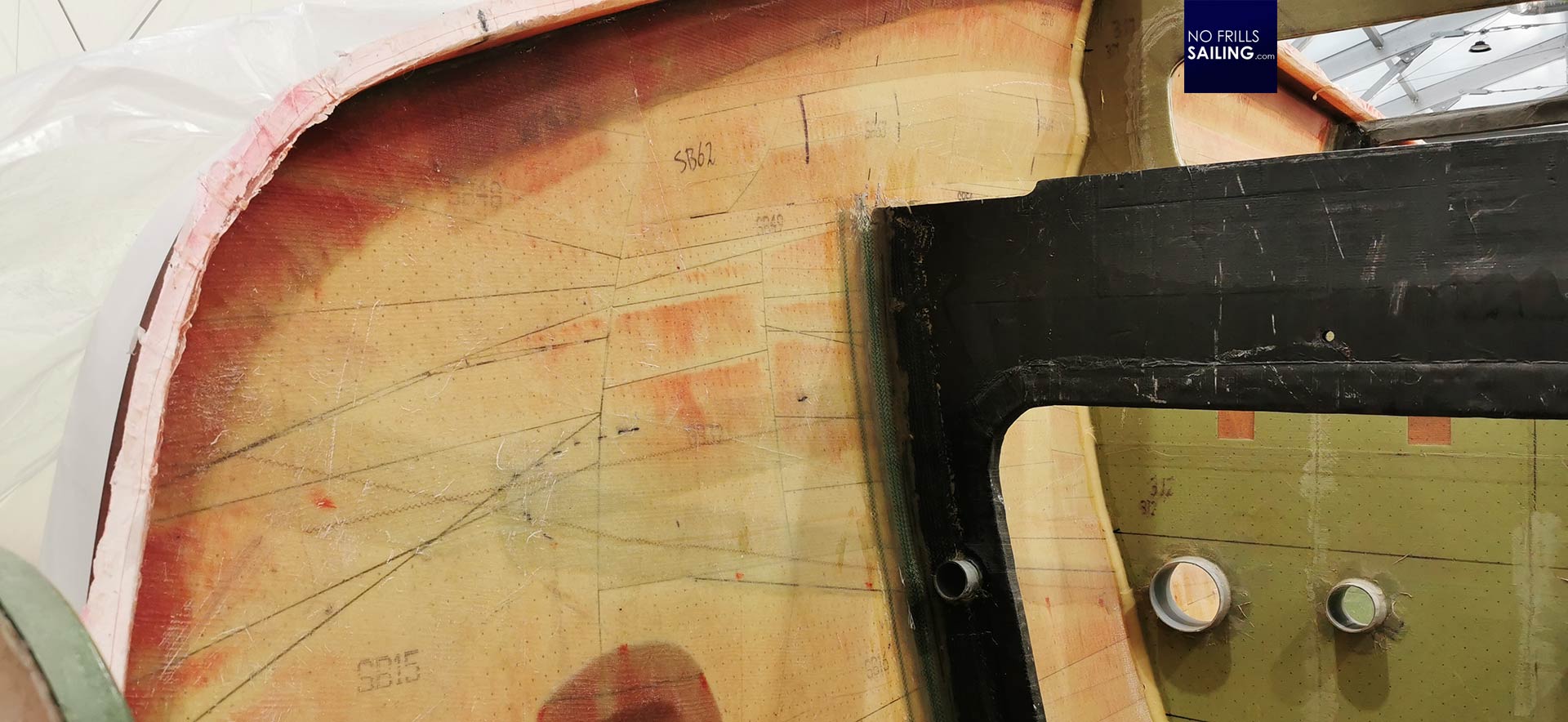
As our guides tells us, in the end this hustle makes sense for a performance-oriented product like Outremer: Upon “closing” those thousands of little “glass-gaps” within the sandwich structure the shipyard is able to save 300 to 400 kilograms of resin. That´s nearly half a ton of weight for a 52 feet catamaran!
Lightweight and stiff
This weight saved, plus the additional amount of weight saved by intelligent utilization of modern sandwich structures allows the shipyard to either install more equipment – to enhance comfort aboard – or to increase performance under sails. As I mentioned in my walkthrough aboard the Outremer 52 sailing catamaran, I´ve had the impression that both the 52 and the 55 differ much from the “classy” Outremer 45.
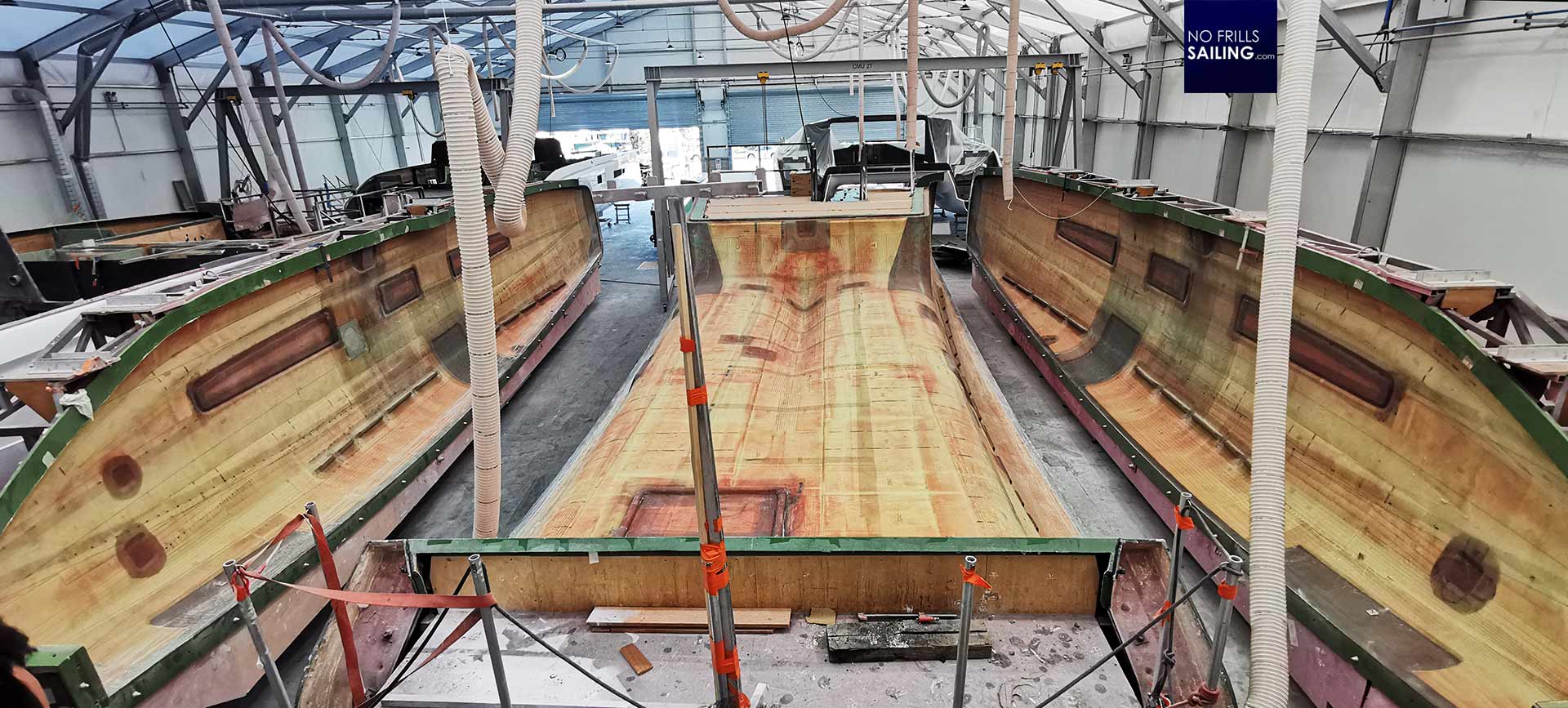
Now I understand that more comfort – hence more weight – is not necessarily connected to a loss of performance or sailing fun. If done properly and wise, this weight can be saved in the first place. The end product I´ve seen in the shipyard is both compelling and impressive from a standpoint of the craftsmanship invested but also in the clever utilization of state-of-the art materials. It´s a shame I couldn´t take pictures of the Gunboat part of the shipyard – photography was strictly forbidden – because this was even another step up in that matter. Anyway, another interesting detail of modern GRP shipbuilding.
Thanks again, Outremer, for having me in your shipyard.
Similar articles of interest:
Cutting Divinicell: How foam core matts are precisely cut
Balsa core material: Still valid?
Vacuum infusion in boatbuilding