When I visit the shipyards of our brands I regularly get questions by our guests and clients about the utilization of wooden sandwich core material, namely Balsa. Many guests are kind of astonished to see that this material is still in use. Somehow, apparently, many people have the impression that Balsa was a material “of the past”, a kind of “has been done in the Seventies and Eighties”. Seeing the boats being made with Balsa, our guests often ask many questions. So I thought it might be useful to write an article about this particular topic.
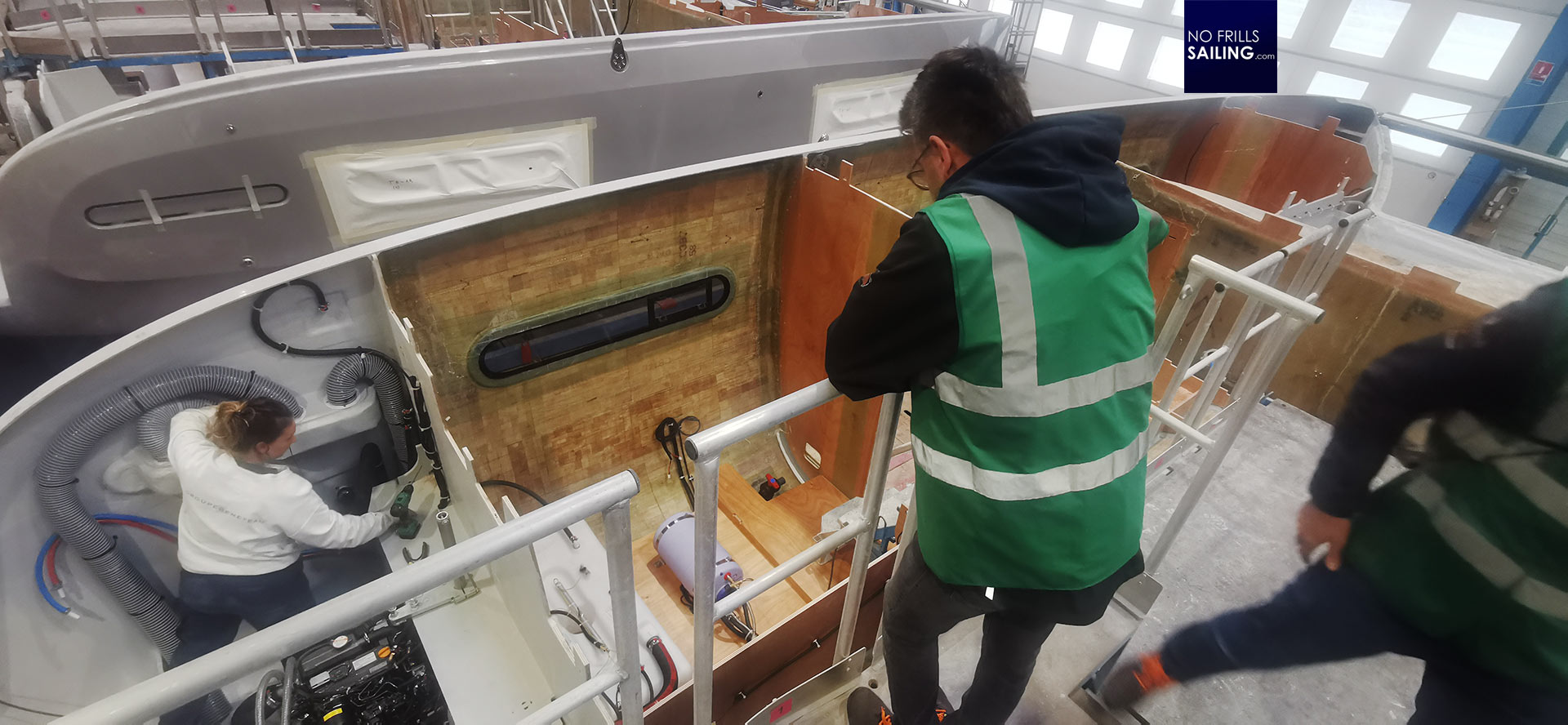
A sandwich composite is needed to create a stiff yet lightweight structure. You want a boat that is as light as possible, so that the power of the wind may accelerate your yacht as easy as possible and make it quick. On the other hand, you want a stiff boat of course, so that the power of the wind that is induced into the boat by the sails, mast and rigging, does not make the boat flex or distort which can lead to performance loss (at best) and structural damage (at worst). Sandwich structures, meaning having thin layers or glasfiber/resin encapsulating a core material, are the best way to produce a strong, stiff yet lightweight hull. Only a few parts of a boat´s hull are massively laminated, most areas are sandwiched.
Balsa end grain: A modern building material
You may have read my article on synthetic sandwich materials such as Divinicell. Those are mostly used for upper-priced or high-performance yachts. These materials have certain properties, good and less good, as well as Balsa does. Balsa for sure is not an outdated material nor is it a low-cost cheap material to save money on your boat. Like synthetic core materials, Balsa has certain very good properties and some downsides. But for sure: The legend that it´s just a dated cheap circumvention of spending money is a myth.
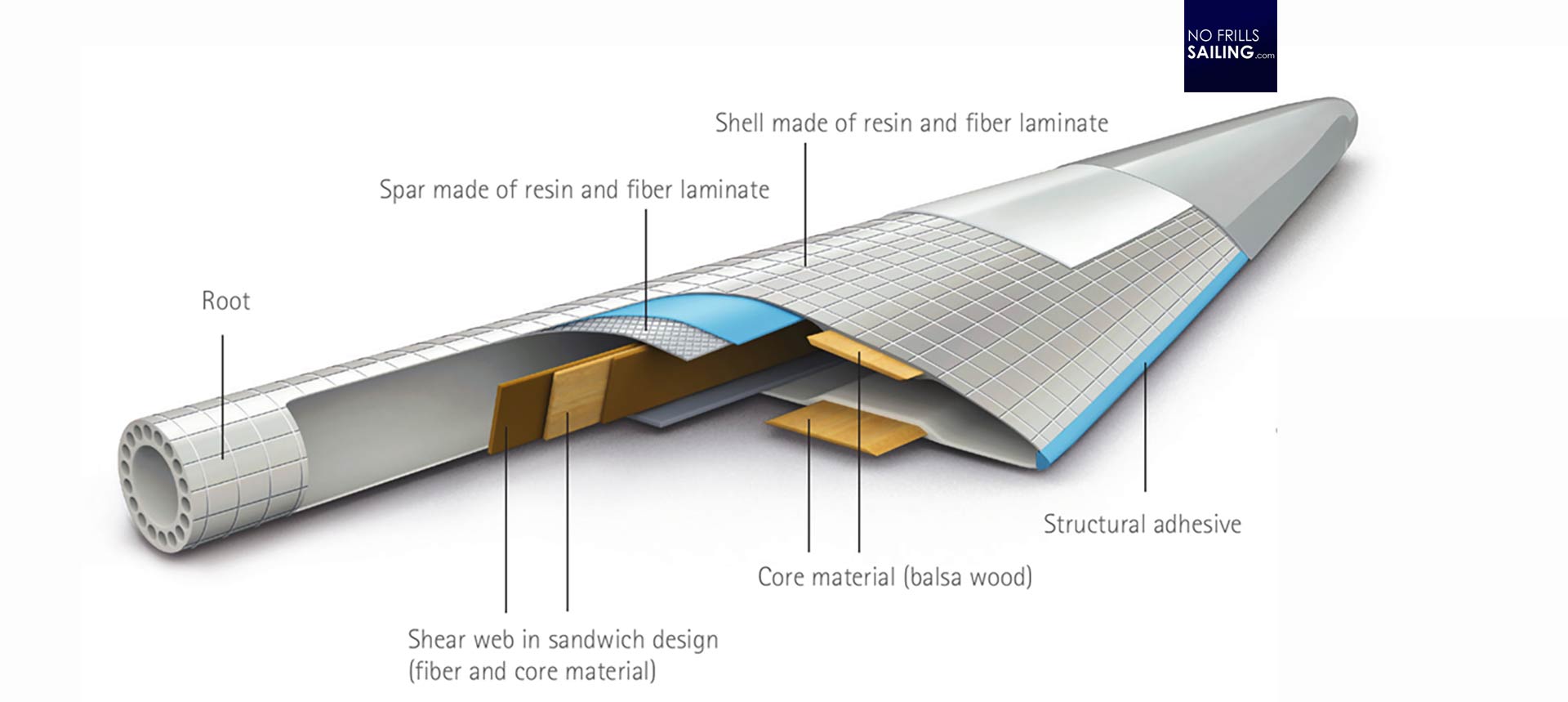
Balsa is widely used in the composite industry, as you may see on the picture above, it´s a common material to be used in roto blades for wind turbines. Imagine the huge impressive windmills as they are used in the offshore wind parks. These are massive structures which have to withstand Hurricane-force wind speeds, storms and heavy seas. They are bending and flexing much, much more than a boat will ever do. Balsa as part of the construction is a reliable material in certain areas: The big companies certainly wouldn´t utilize this material if it wasn´t reliable and durable.
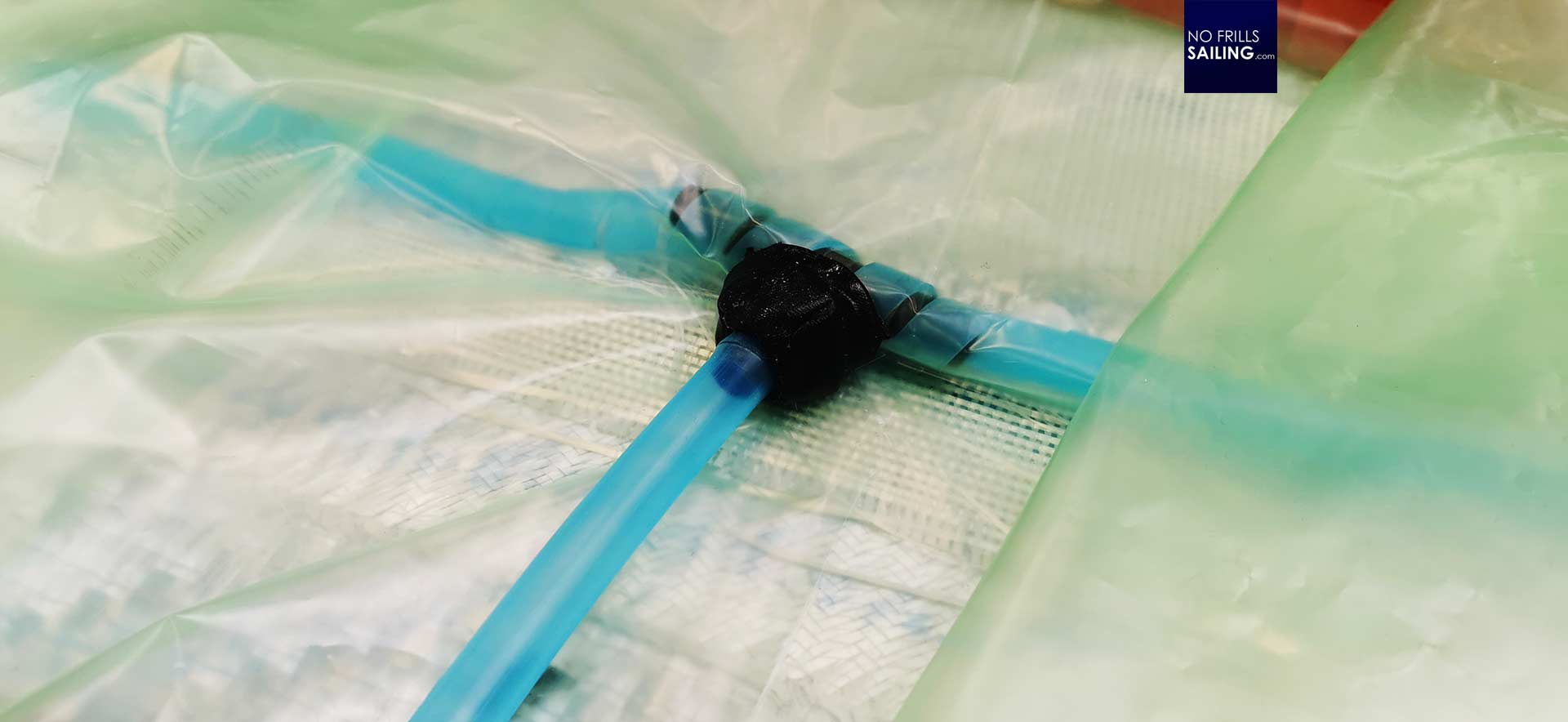
Balsa core material is processed with all the common modern boatbuilding techniques, like vacuum infusion. There is nothing “dated” about Balsa. On the contrary, many engineers and boatbuilders I talked to about Balsa confirmed that it indeed is a very nice material to work with, easy to process and that you can achieve very nice outcomes by utilizing it properly. So, let´s take a more detailed look at this timber.
Why Balsa?
Balsa is a material utilized by humans for thousands of years. As you may acknowledge by looking at the picture done by scanning electron microscope below, the structure is very nimble. The timber is made of very thin cell walls which make up millions of hollow fibers. There are also thicker, also hollow, sap channels, the “arteries” of the trees. This is a very, very light structure – creating a material that floats. Holding a piece of Balsa wood is fun because even thick battens almost weigh nothing.
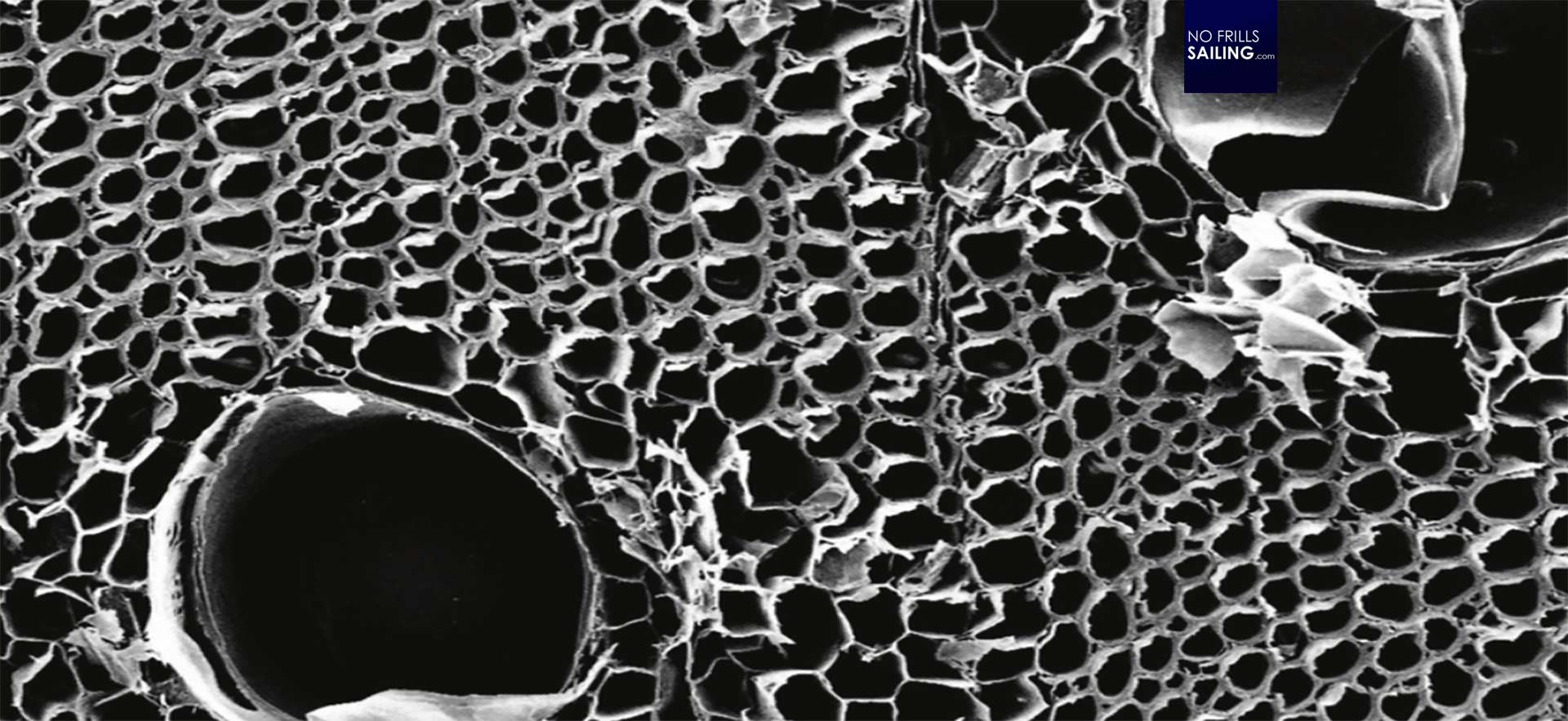
In this, Balsa is a tradition building material for floats and simple boats, used for hundreds and hundreds of years. Modelmakers love Balsa because it is easy to process and – again, due to its lightweight – the material of choice for model airplanes. In boatbuilding, Balsa is in use since the inception of glassfiber reinforced hulls as a sandwich material. Although, as with everything that is introduced and new, Balsa core boats of the first generation had their issues.
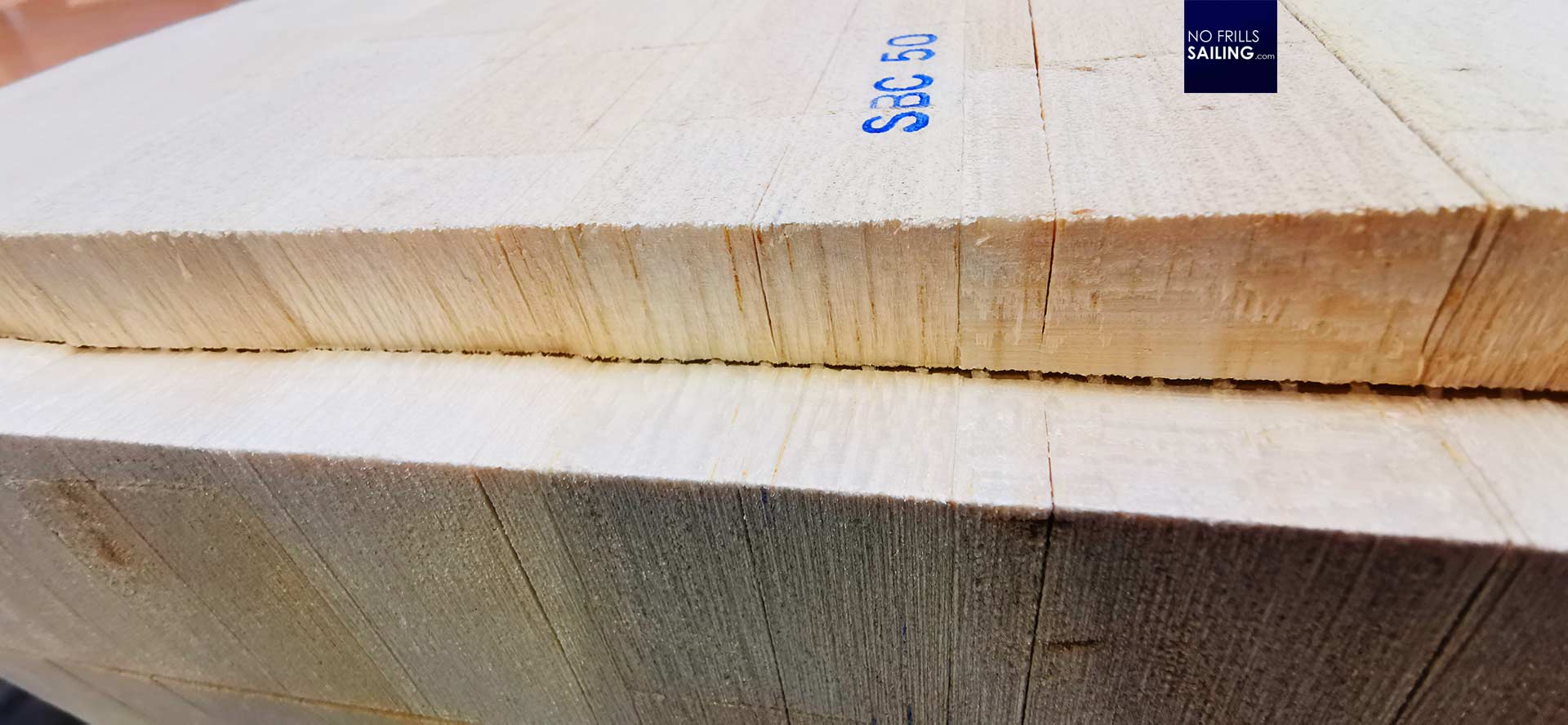
Modern Balsa core mattings are made of a plastic gaze onto which the Balsa wood is fitted, cut into squares. It is imperative that the Balsa in use is comprised of the harder parts of the tree log, the so-called “end grain”. Also, the squares must be put onto the gaze with the grain direction oriented in a right-angled direction to the laminate. This ensures that the resin can penetrate the fibers, the little “channels” of the Balsa and harden thoroughly to make a tight, stiff fit.
Sandwich core with Balsa end grain
The gaze mats are very easy and convenient to use: Because of the gaze, the mat will follow the rounded shapes of a hull just perfectly. You can see in the picture below, that, if done this way, the round shape will make the individual Balsa cubes open up little spacings. Depending on the grade of the curvature, these gaps measure from a fraction of a millimeter up to a millimeter.
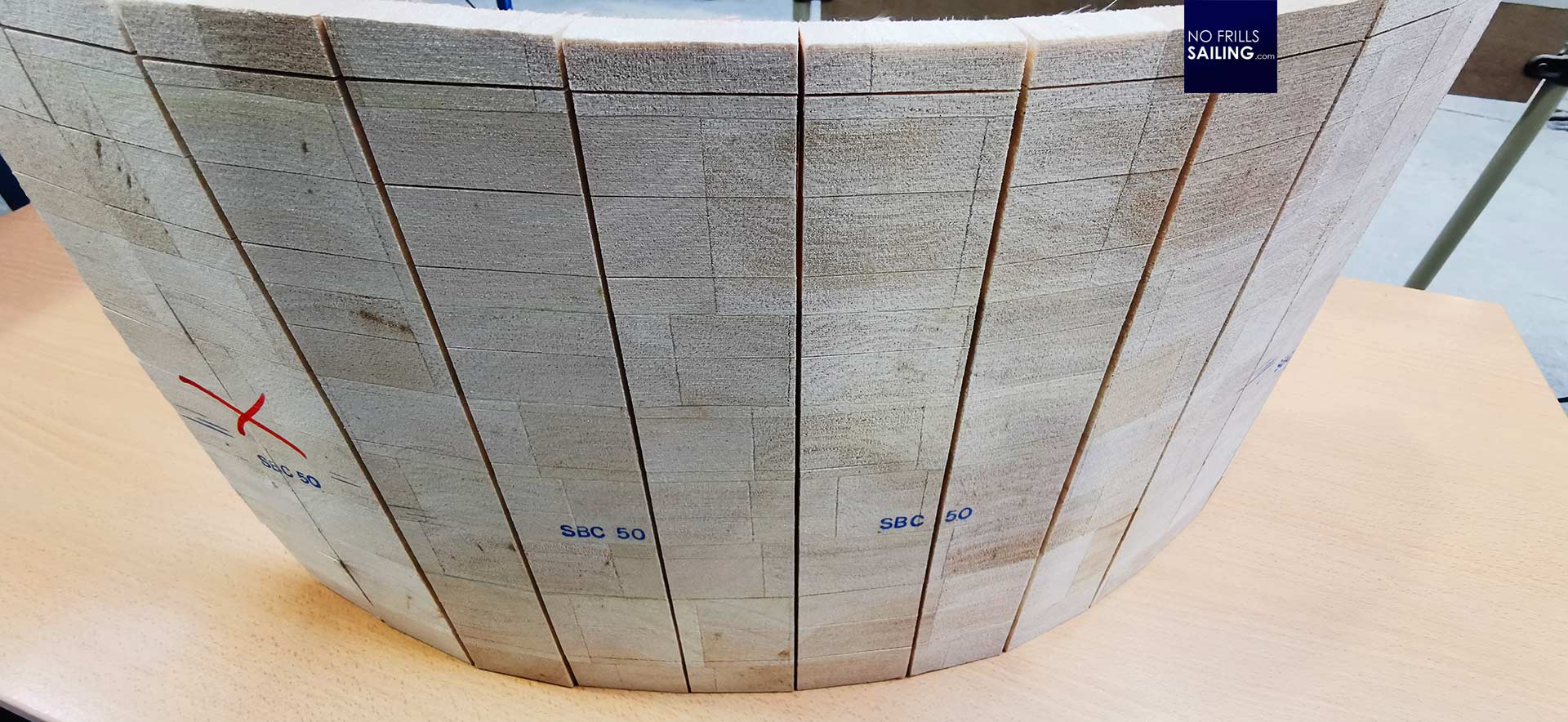
This is a very important feature. Now imagine the resin is infused during the hull making process. The resin will of course full up these gaps. When thoroughly hardened, there are now glass “barriers” between the Balsa cubes. In the case of a hull damage, let´s say a small ramming or collision, that is going through the Gelcoat and the first GRP-layer, water may enter the sandwich area.
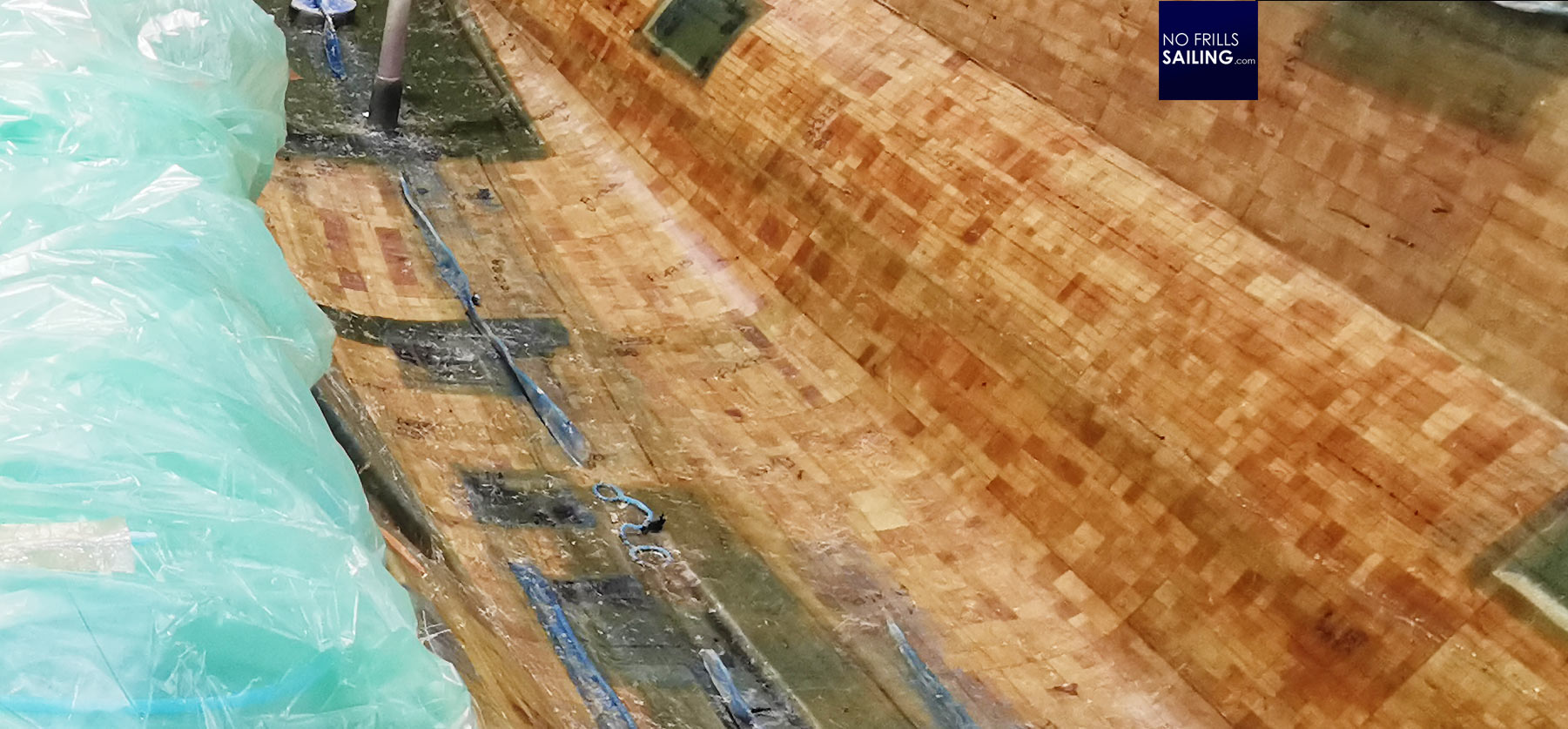
As Balsa is a very poor at being water resistant. It will rot within a short period of time when exposed to water (this was the major problem with the first generation Balsa cored boats). I´ve had my own bad experience with rotten Balsa core in my first boat, the King´s Cruiser 33, where around one of the chain plates the core was rotten. But now, in modern boats, by having those glass “barriers”, the water can only damage a few cubes and won´t be soaked through larger areas or, at worst, the whole sandwich core as it was often the case with old boats.
A natural, sustainable material
Sustainability is a huge buzzword these days and right so. Respecting nature, resources, energy consumption, waste management and recyclability and many more topics are permeating our lives, transforming whole industry sectors and products. Supplanting “forever-chemicals” with degradable or recyclable substitutes, like the Ellium resin or protecting natural resources by supplanting rain forest grown natural Teak are just two of the many facetes of his transformation. Balsa plays a key role here.

As it is a tree, of course, Balsa is a natural resource. In itself, it is sustainable. Balsa trees naturally grow in the northern part of South America but there are also large Balsa tree plantations in central Africa like Zaire, on Java, in Malaysia, on the Philippines or Vietnam. It grows naturally in forests. Most of the Balsa used for lamination, construction and commercial use is grown in plantations. There are pros and cons when talking about monocultures, I know, but not being a specialist in this area, I guess (or to say: I hope) that the companies responsible for growing and delivering Balsa from their plantations do it in the most sustainable way.

I´ve written about the efforts made by Groupe Beneteau in supplanting Teak with Iroko in an article. They cooperate only with FSC certified producers and have strict rules for labour management, use of pesticides and so forth. I guess and hope it is the same for their Balsa sources. Anyway, looking at the production (namely, the natural growth) of Balsa, this material definitely has an advantage over synthetic core materials made of PET or PVC.
Pros and cons of Balsa wood in boatbuilding
As with everything, there is no such thig as the perfect material. Life and our Universe is made out of antagonisms which are indeed not fighting each other, but rather complementing each other to form a whole. There is no day without a night. There is never a plus without the minus. The Ying and the Yang, a holistic universal principle. In this, Balsa, of course, has properties which are unique, useful and very good. But there are also downsides or, let´s say, implications which one has to be aware of when utilizing it.
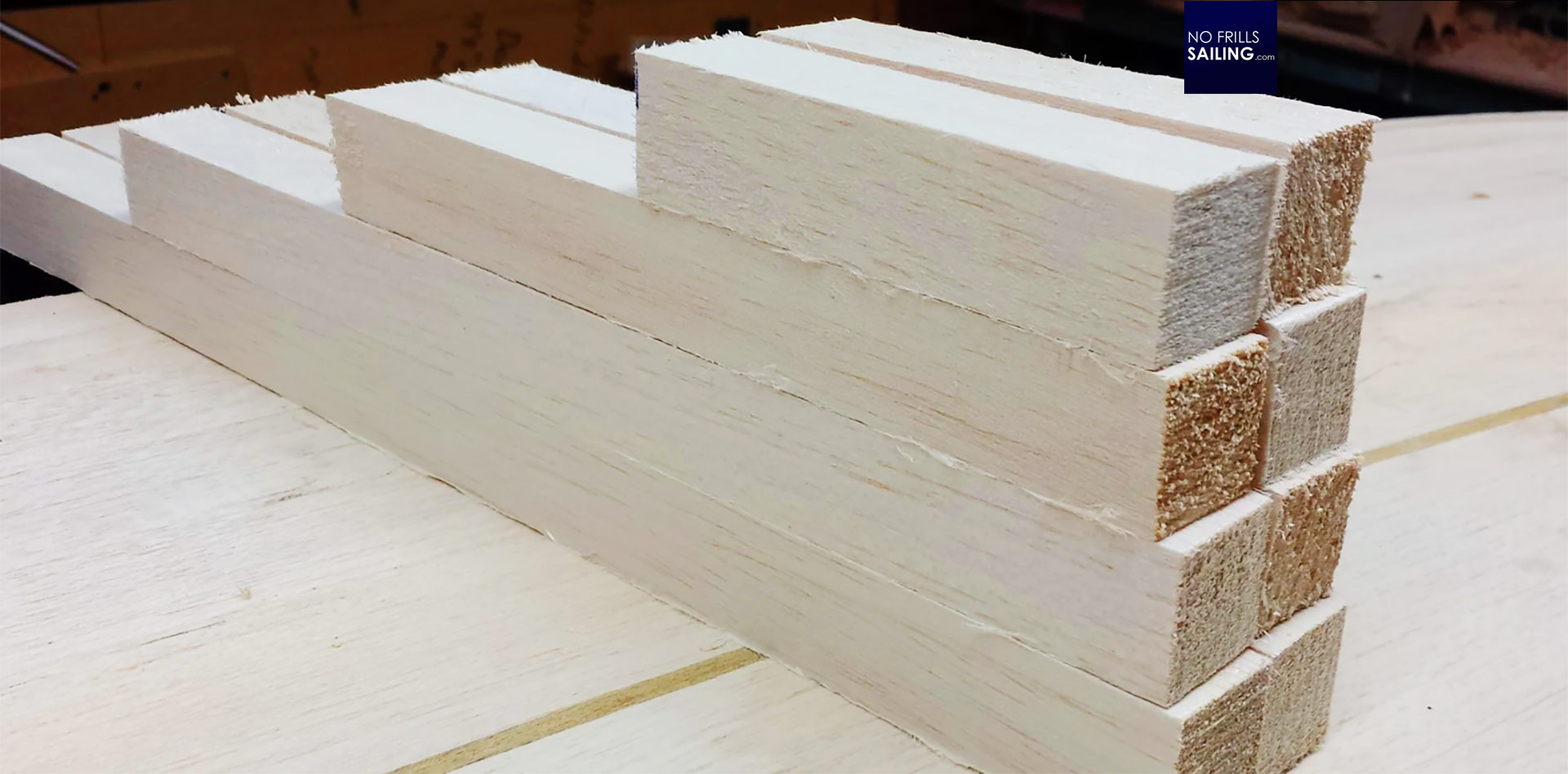
Let´s start with the downsides. I´ve mentioned the possible problems when sourcing Balsa. Can there be complete control over a sustainable, fair and “clean” production? I don´t know. Are the plantations pesticide-free? Will there be no deforestation, soil degradation and such? That´s always a concern when sourcing raw materials. Looking at the material properties, there are a few things that can become a problem: I´ve already mentioned the poor durability of Balsa when in contact with water. Also, as a natural material, the quality varies from tree to tree, there is never a consistency in things like material strength, weight, density, thickness of the fibers, grain quality et cetera. You can literally see it when looking at the bare Balsa cored laminated hulls. Delamination can be a problem when the structure is subject to large blunt force like collision or constant extreme flexing.
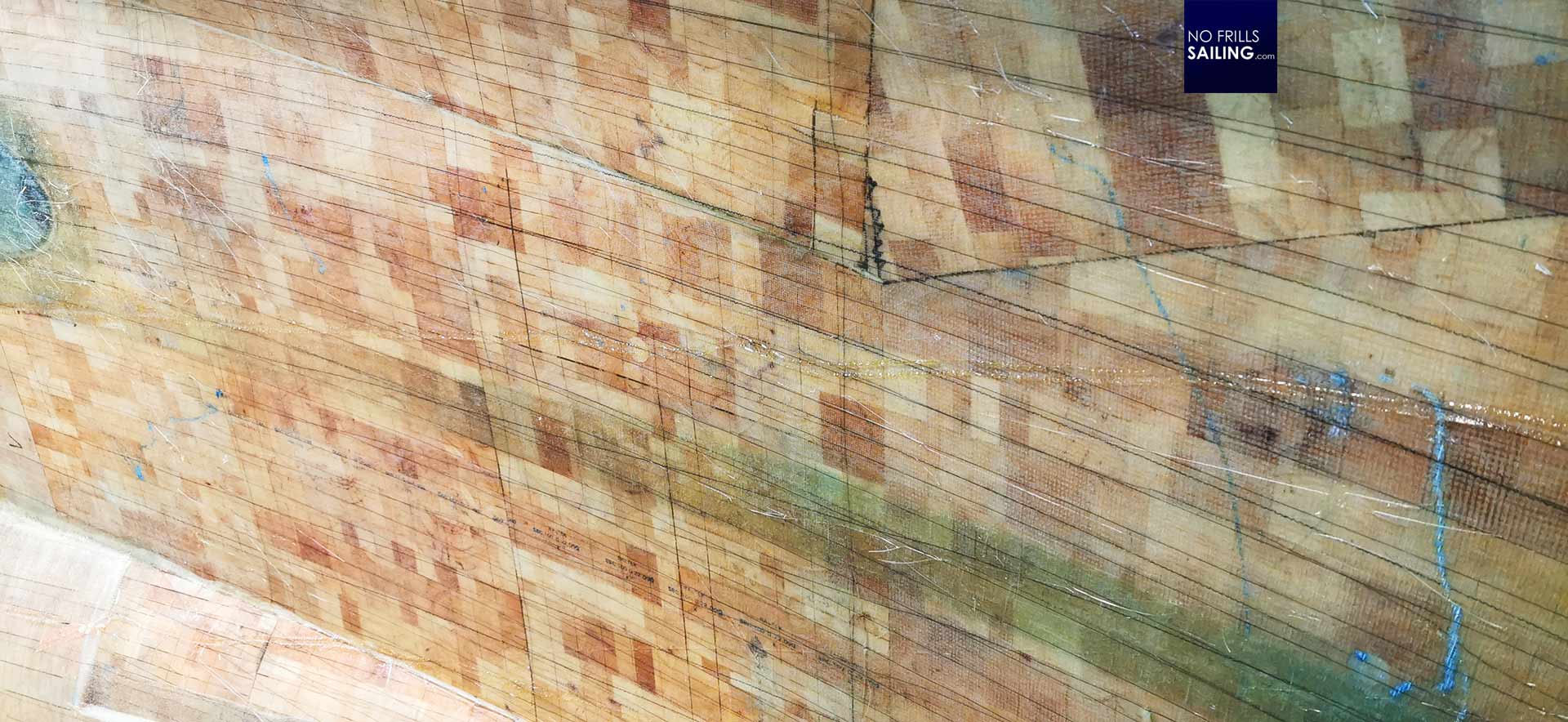
On the other hand, there are some very nice features of Balsa, one of which its natural source is already mentioned. Also, the processing of Balsa and preparations of the material to be utilized in boatbuilding is very easy, much less energy consuming then producing synthetic core material. Thus, it is cheaper indeed. In a cruising yacht, where extreme weight-saving is not a big concern, it´s the core material of choice especially for the large production boat manufacturers.
Plastic boat? Wooden hull!
And a such, back in the shipyard, our clients and guests have seen the making of a boat from its conception, made out of loose glass fiber mattings, some resin and wooden cubes, to the beautiful, finished boat, floating in the testing pool ready to be delivered to a proud and happy owner. In fact, our “plastic” boats are much more “wooden” boats, to the bone, as the saying goes. Balsa is far from dated, far from a cheap substitute. It´s a valid, modern sustainable material that has its place in boatbuilding.
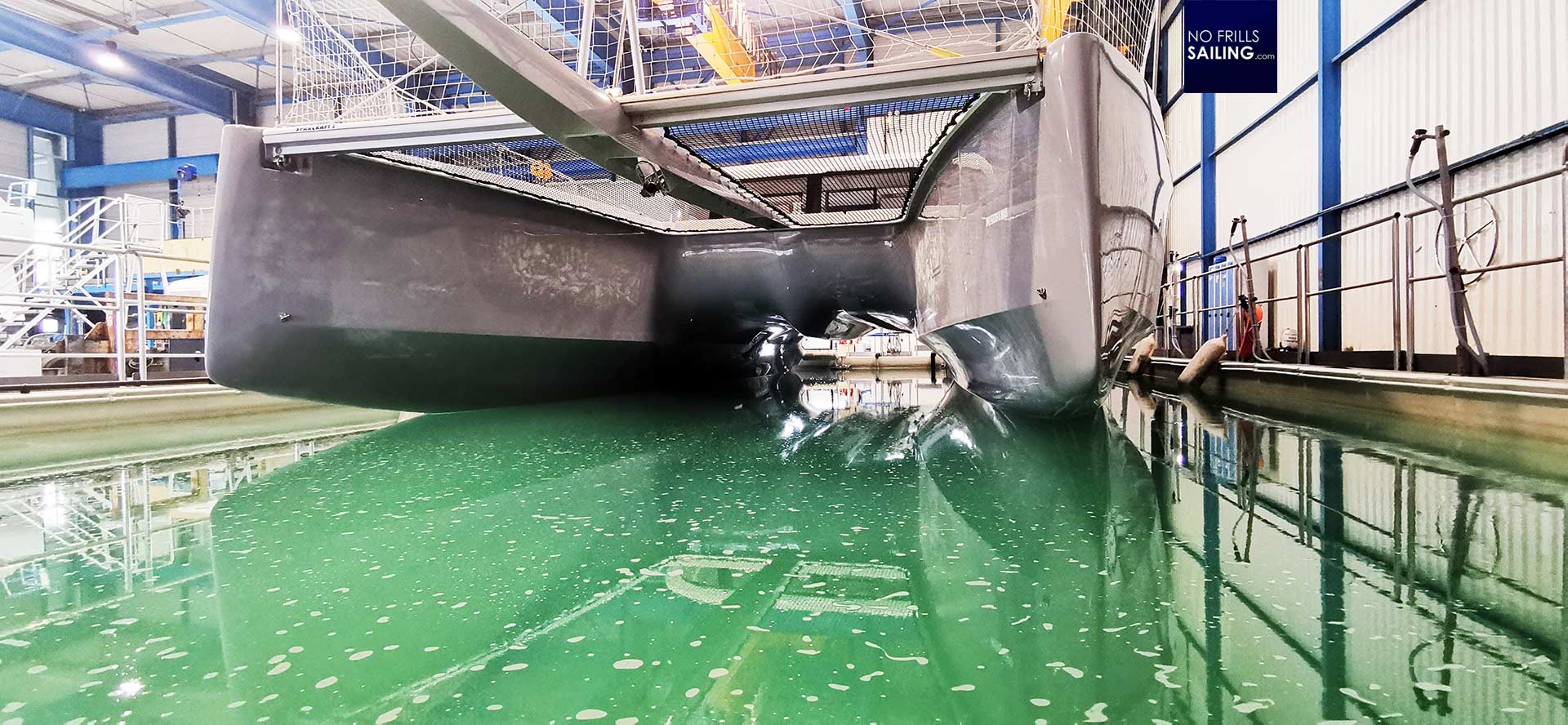
My own new boat, the Omega 42 has a sandwich core hull too. As this boat is a performance oriented boat where weight is of utmost importance, the shipyard back then decided to have her core made up with synthetic foam. There is no “good” and no “bad” in those decisions, there are many pros and some cons in each of them. In the end, life is never sustainable. We are energy and resource consuming beings: Building a boat, unless its not a raft like they´ve made some three thousand years ago, will always only be a compromise.
You may also find interesting to read:
Divinicell, Corecell and other synthetic core materials in boatbuilding
Vacuum infusion: How it works