At last some news from the Omega 42 building in the shipyard at Lake Mueritz: The guys started works on the propulsion system and I´ve received some interesting pictures last week. You may remember how I´ve decided between either a Yanmar or a Volvo-Penta Diesel engine to be fitted into ALPHA? You may check this post from July last year when I finally received and delivered the engine to the workshop. Well, part of the delivery was this thing:
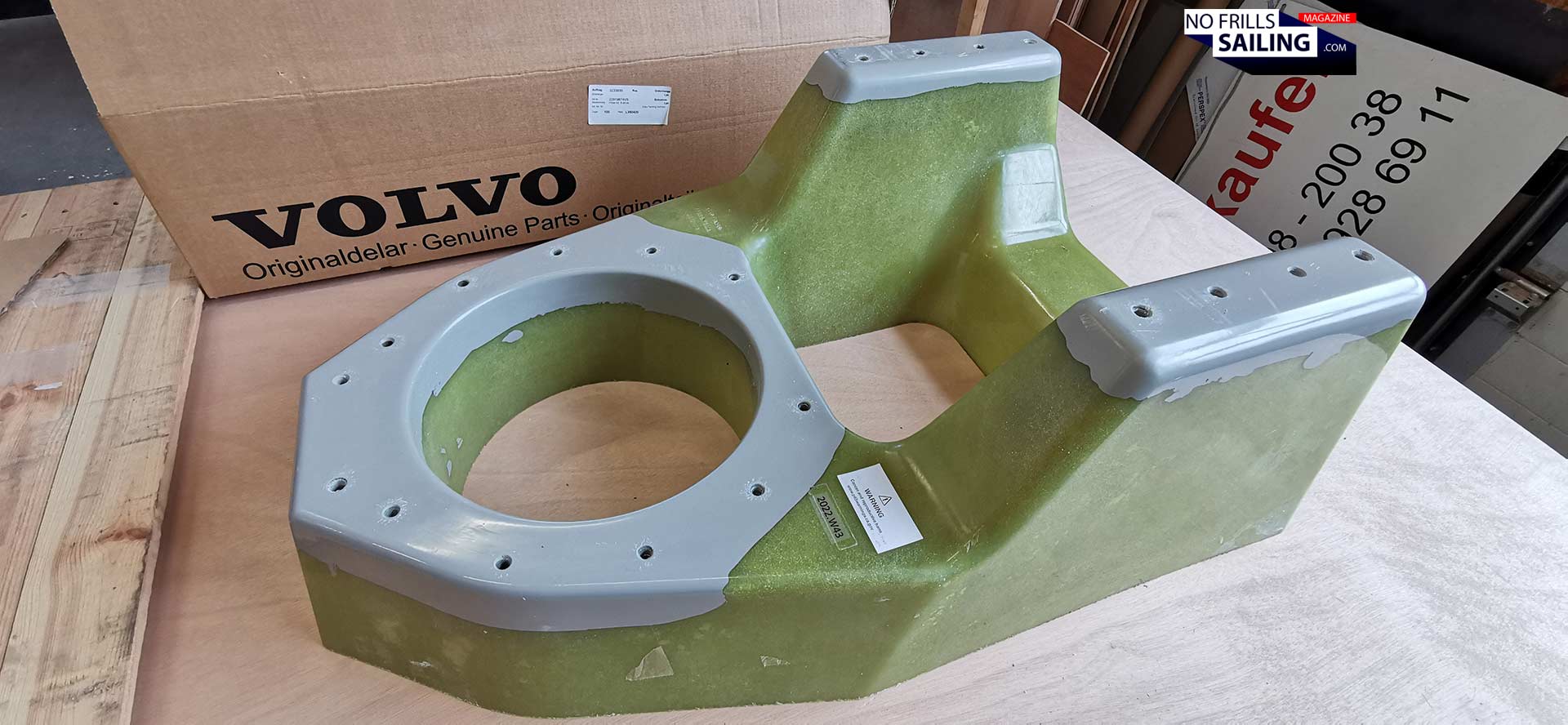
My kids asked me wether this would already be the toilet, which, I must admit, this part bears a little resemblence of. But of course, Volvo-Penta isn´t entering the plumbing business – this of course is the original GRP-made engine base onto which every single Volvo-Penta must be mounted to. This short article shows the meticulous work – not of fitting the engine, but one step before. How they cut a hole into my hull …
A strong base for any boat´s powerhouse
You may imagine that a Diesel engine is a pretty heavy duty piece of machinery. Although my engine only has 29 horse power, it is perfectly capable of driving the boat through hefty currents, make it hold its due course and even propel her with quite a nice speed in emergency situations. By that, the engine is not only just heavy in terms of ist weight, it also needs to get ist torque tamed.
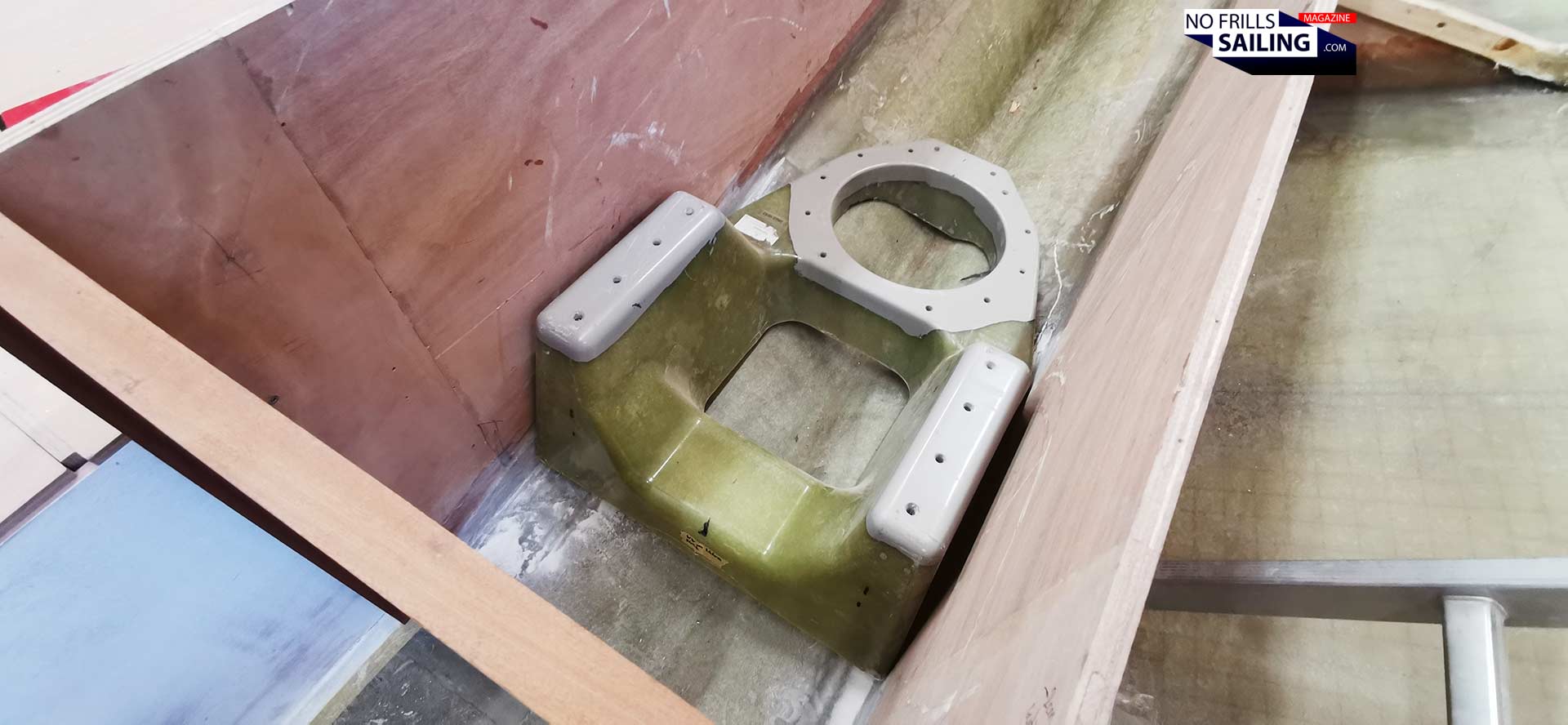
The power generated inside the cyclinders, burning Diesel fuel and creating a rotating motion must be transferred to the saildrive and via my propeller the rotation creates thrust. As any effect creates a counter-effect, this pushing motion comes back to the engine where it is transferred into the hull. You can imagine the huge forces, created by that. In addition to the torque and also the constant vibrations. So, every engine needs a base to be mounted to. And since Volvo-Penta cannot and will not rely on the boatbuilders to make those base-mounts on their own, you are provided with a standard GRP-part to be utilized.
Laser-optimized fitting
As you may have seen in the picture above, this standard part by no means fits the interior shape of my hull. I´d say, if the are where the engine is to be fitted is not 100 per cent flat (which in a rounded hull cross section is very seldom, I´d say) then each boatbuilder and shipyard will have to cut the base to a perfect fit first.

That is not a job to be taken with levity. Once too much material is cut off, it will be hard to fit the engine again. Also, a dozen or so more factors have to be taken into account: Since the propeller-shaft (in my case the saildrive) has a defined length and the propeller needs a certain minimum of depth to be mounted, this is an engineer´s work: It starts by defining where the waterline would be inside the boat and leveling it completely with accuracy.
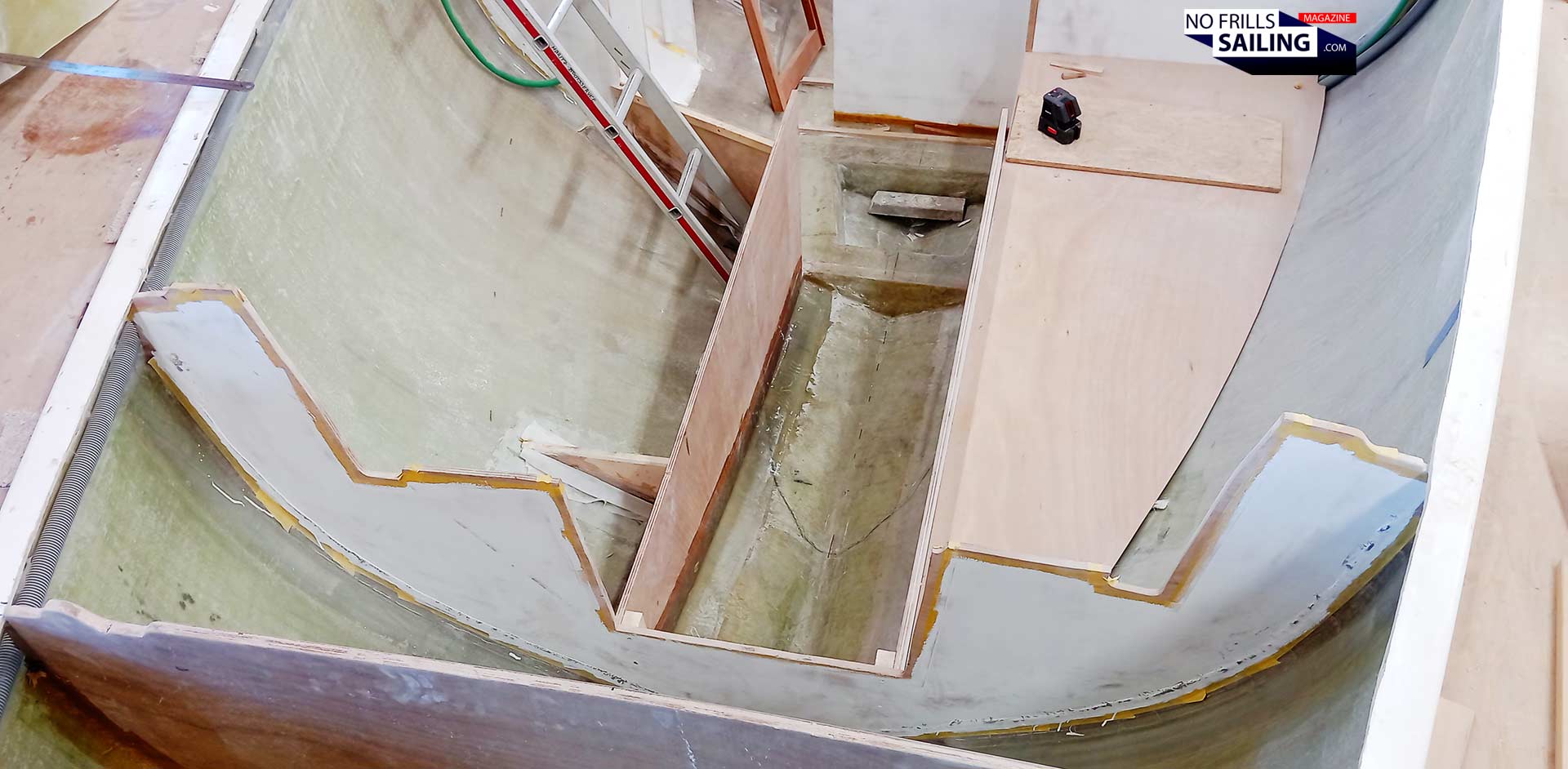
If done accordingly, the engine manufacturer´s suggestions of how to mount the engine and where the saildrive should be need to applied as well. Again, with utmost care and double-checking the accuracy. You can imagine, producing too much offcut of the base mount only results in buying another GRP part at the worst – cutting the large saildrive opening into the hull at the wrong place is … well, much, much worse!
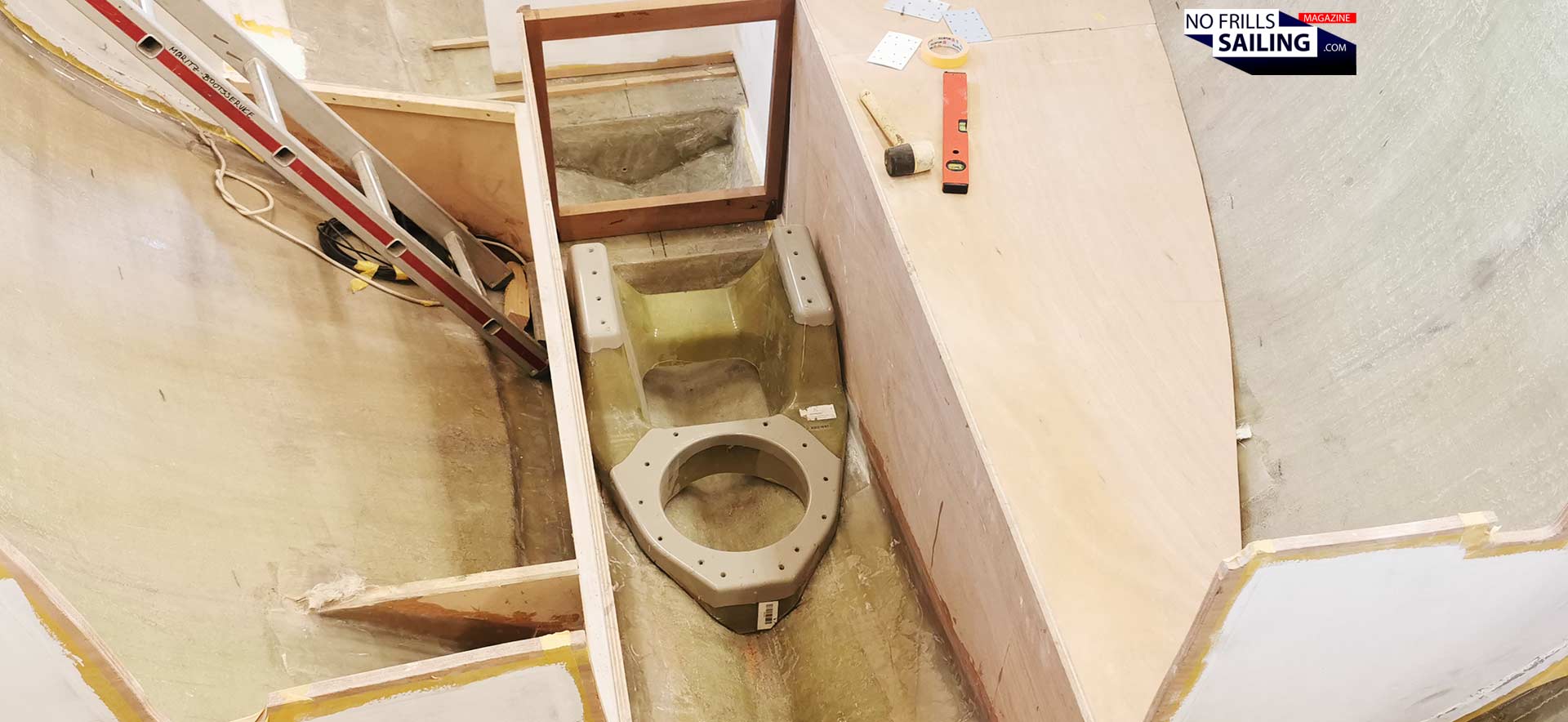
The guys in the shipyard measured and re-assured themselves that these were right and started to take away material from the Volvo-Penta base mount. From time to time they would come back into the ship´s belly to check for the outcome, slowly taking away more time and again. So that, after two hours of work, the base had received ist final shape: It fits perfectly!
Cutting through my boat´s hull
Now the fun part: Let´s take out the drill and the saw! Volvo-Penta provides gauge model templates when buying an engine. These templates have the exact shape of the saildrive cutout through the hull. Basically, if used properly and accurate, nothing can really go wrong. I´d have loved to be present when they started to apply the first cut though!
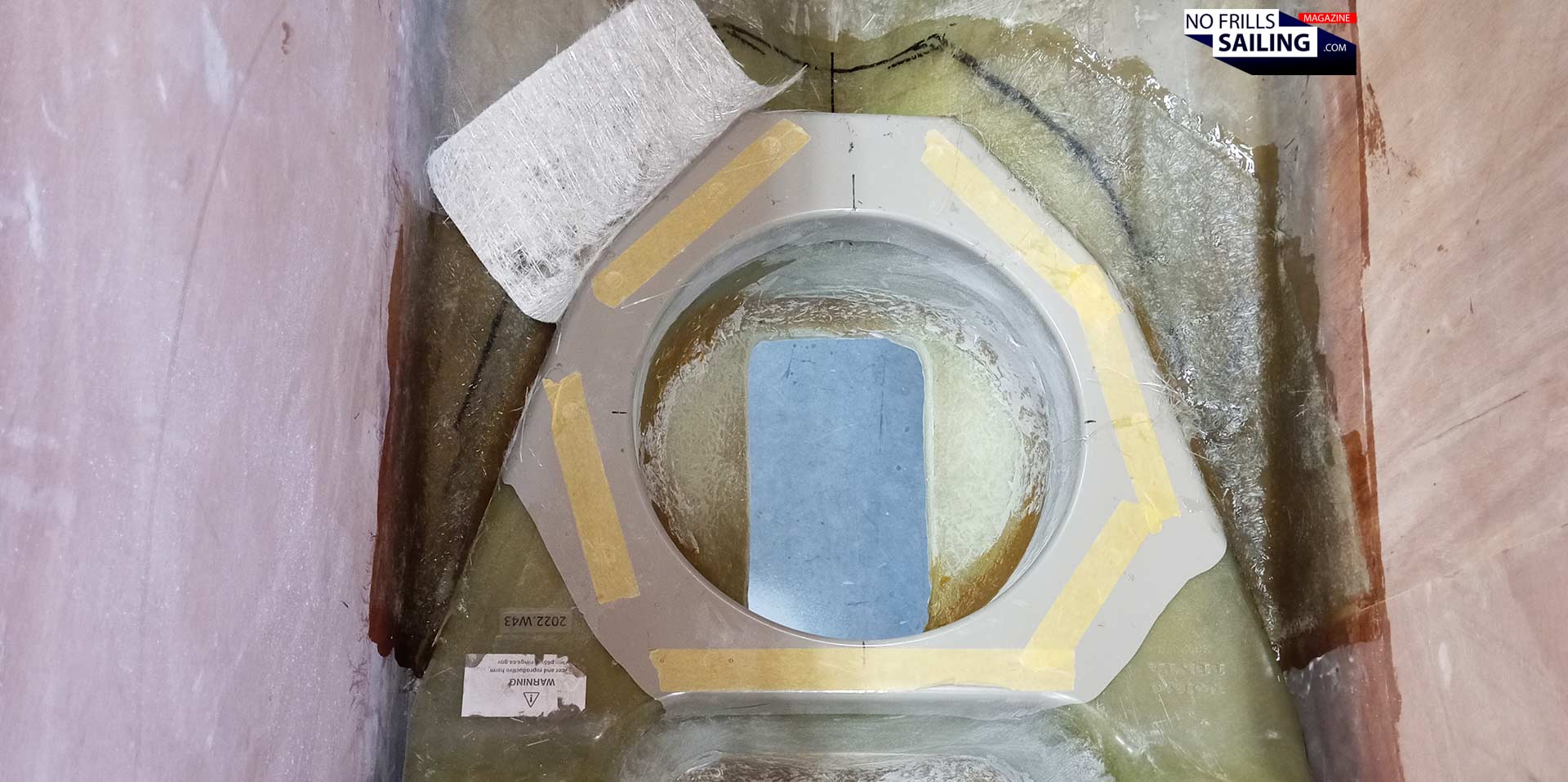
After the hole had been set, the base mount was laminated thoroughly into the hull. Glued and inseparably attached to the inner walls of the new engine room, the GRP-part from Sweden now became a firm part of my yacht. This whole operation lasted two days as they tell me and after it was allowed to dry a few days the GRP-structure is now monolithic and strong. Ready to take on the Diesel-engine!
What´s next?
You may notice this greenish-foam-thing in the picture below laying in the cockpit of the boat. That is the 1:1 model of the Diesel fuel tank that I am about to send to a little company down south of Germany. A custom made stainless-steel tank is the next big part of the propulsion-system to be made. Maybe, if I´m lucky, I can also tell the story of how such a tank is made. For now, the guys in the workshop will make sure that the engine base is thoroughly fitted and resume the works.
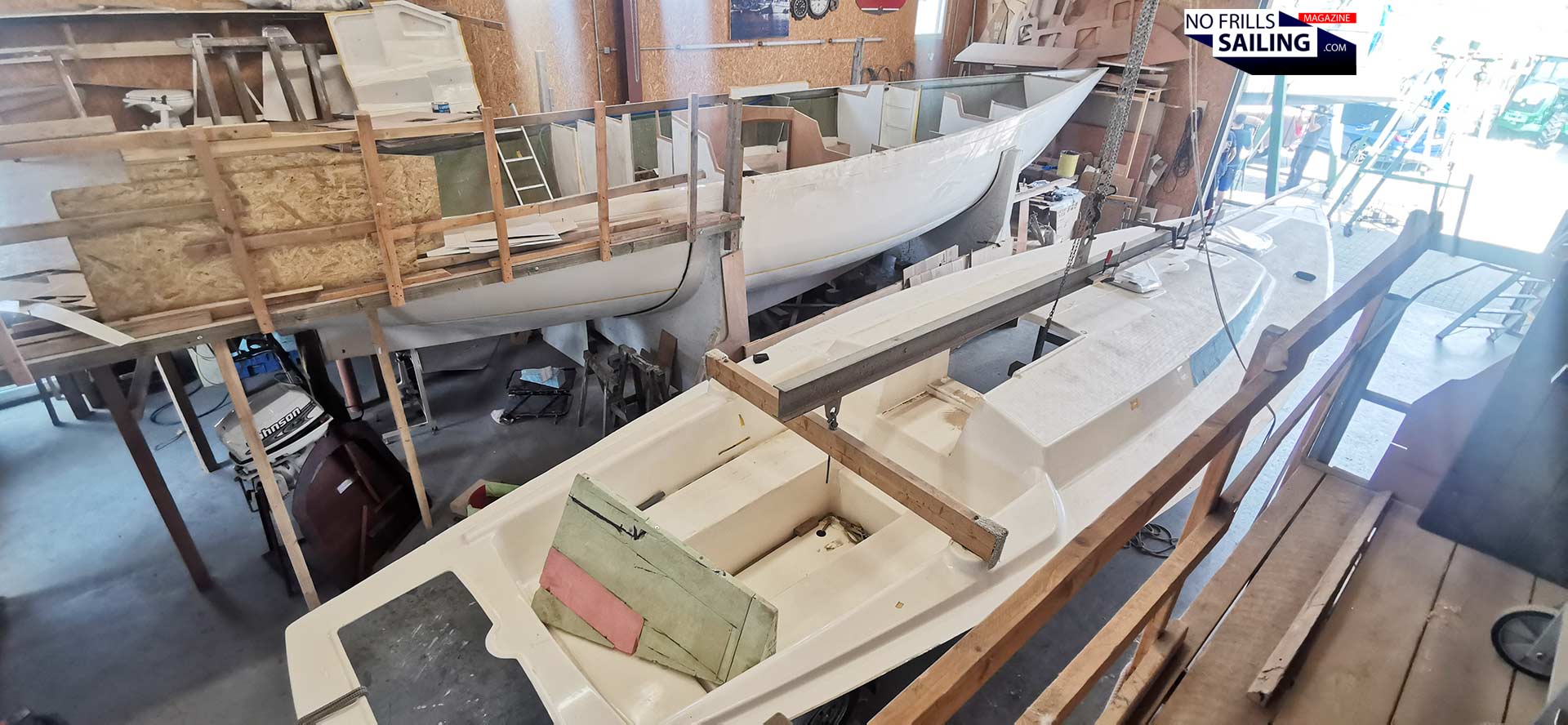
Engine and saildrive, exhaust-system, fuel-system including the tank, filters and the first parts of the electric system including batteries will be next. Plan is to have it all set and done in fall, along with the last furniture. I will be personally at the boat during the coming week to collect even more details and interesting stories. For now I can tell my kids: The water-closet is finished!
You may also be interested in these related articles:
Why I opted for Volvo-Penta
What if you cannot stop your ship´s Diesel engine?