You know me, I am easy to excite and if there is something or somebody doing amazing stuff in the colorful word of yachting, racing and sailboats, I will jump to my car and drive there to catch a story firsthand. It took me unusually long for writing the following article because my level of excitement after visiting the headquarter and production facilities of SPW Propellers in Bremerhaven was at a (seldom reached, even for to my standards) absolute high level. This, dearest readers, is something very special and I hope the following article can live up to what I have seen there.
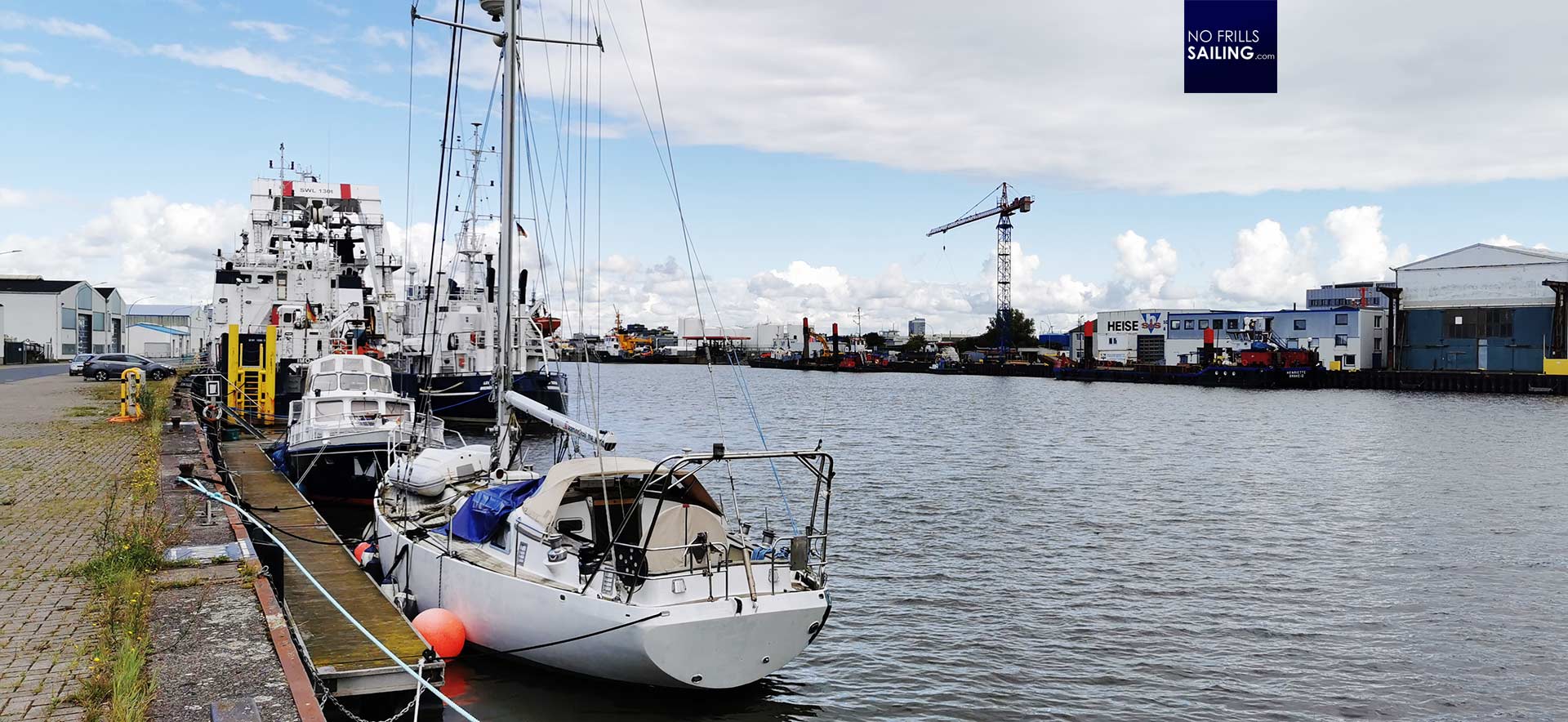
It was a windy late summer´s days a few days ago and by chance an appointment with a prospect customer I was already in the vicinity of Bremerhaven. This is a mid-sized coastal town in Northern Germany with quite an impressive commercial deepwater port (with the longest quay wall in the world) and the center of Germany´s fishing industry. I´ve been here multiple times and I walways like the atmosphere, which on the North Sea is quite different from our Baltic Sea mood.
The importance of the right prop for your yacht
Choosing the right propeller for a boat is of utmost importance: For once, being sure that there is always availability of the transmission of the engine power to the water to create propulsion cannot be stressed enough. Be it a safe docking maneuver under tricky windy conditions for example, when instant forward or aft motion is needed, steaming away from a lee shore in a storm or “just” the bridging of a long dead calm, if your prop failed, you are – literally – screwed.
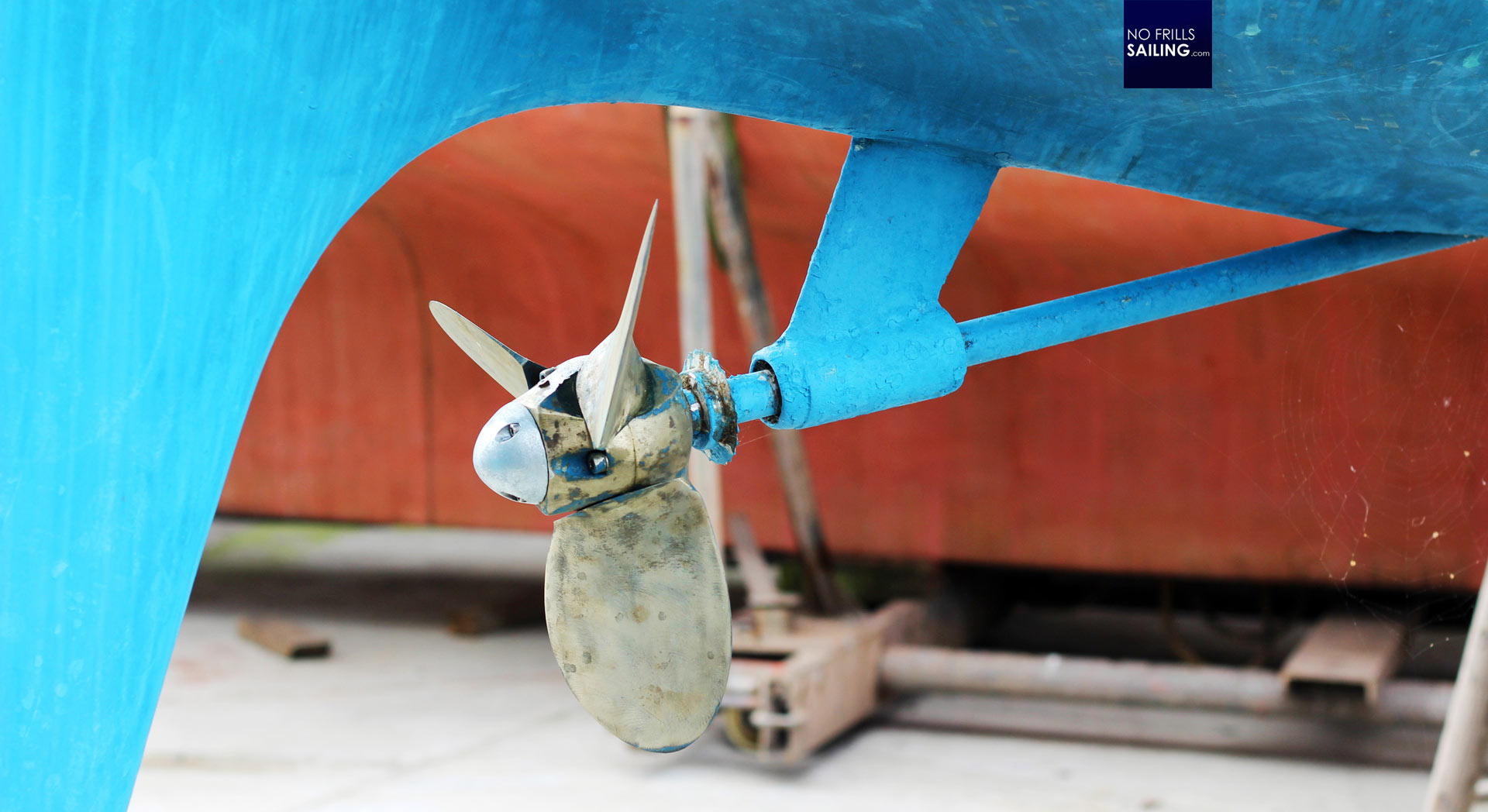
Standard props on sailboats are fixed propellers which mostly come as standard. Those are pros and cons, like everything. The downside of a fixed propeller is the drag it creates when sailing, thus reducing the speed of a boat. It also creates a humming noise which especially during free night-watches can be very annoying in the aft cabins. Also, flotsam is prone to get caught by a fixed blade prop, creating even more severe problems. In this, feathering or folding props are the solution.
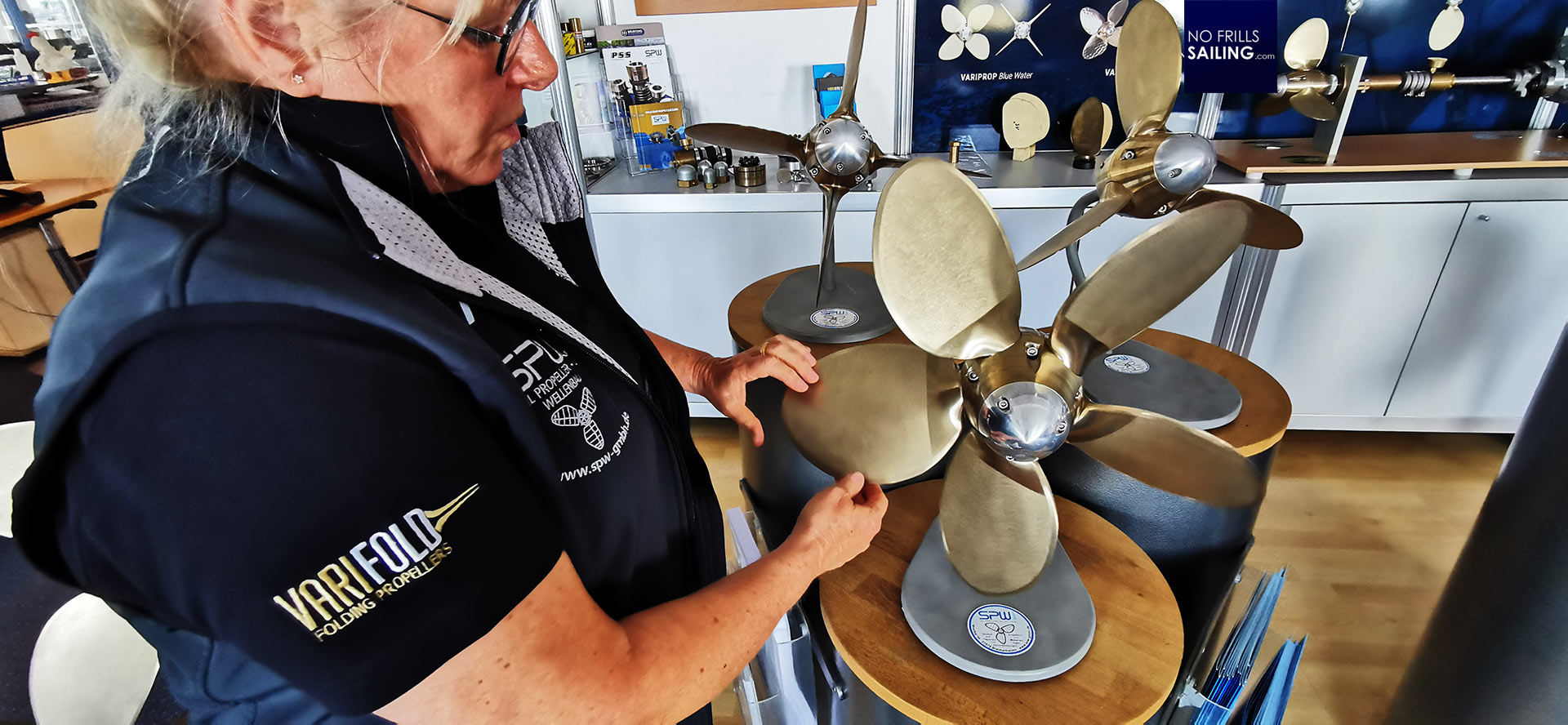
Entering the SPW headquarter I suddenly had a memory of my first ever boat, the King´s Cruiser 33 “OLIVIA” which had a 3-blade feathering propeller. Chances are great that back then I already owned one of the nice products made here in Bremerhaven. Owner and CEO of SPW Propellers, Claudia Adamczyk, gives me a warm welcome and after a little chit chat we start our tour in the small, nice “Propeller Museum” in the company´s entrance area. Here the current product line of SPW is on display and Claudia starts by explaining the folding and feathering prop functions.
Feathering versus folding propeller: What´s the difference?
Most “upgrades” from standard fixed propellers nowadays are the folding propellers. There are fewer than a handful of manufacturers on the market, like Gori, Featherstream or Flexofold to name three, our brand Beneteau usually provides the latter in upgrades to the Oceanis or First sailing yachts. Those are folding props. Their blades will fold backwards as soon as there is no rotational force making them pop out, folding back “out of the way” to not interfere with the flow of the water around them. Nevertheless, some drag will remain, especially with folding props with more than two blades, bent blades (for better pitch) and of with shaft drive boats where the shaft and thus the propeller are angled downward.
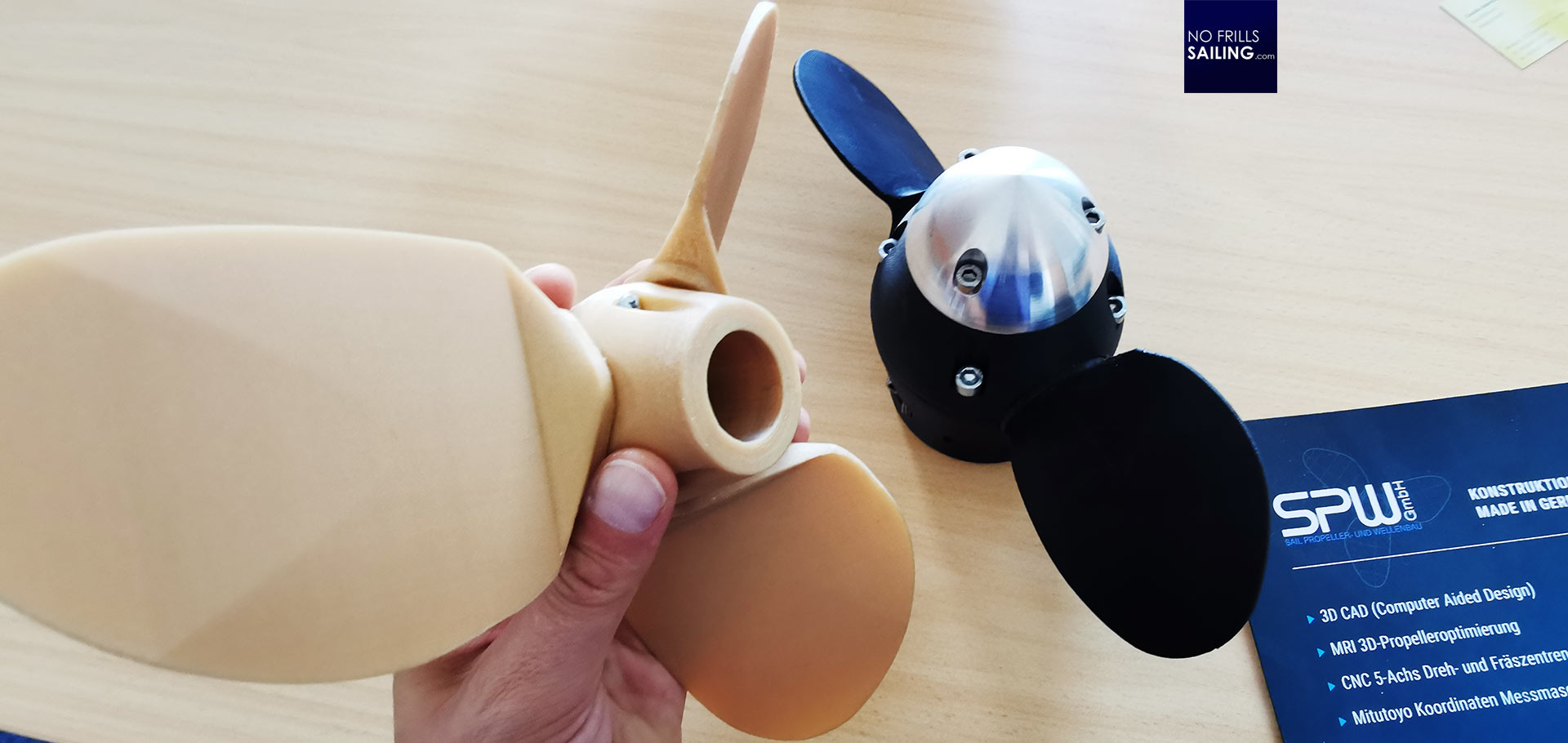
The feathering prop has a different approach. Here, the blades are rotating and not folding. Again, popped out by the centrifugal force of the rotating drive, the angle out at a designated pitch. If the engine stops and be put to neutral, the blades will rotate into the water stream thus minimizing resistance and drag. This is due to the special profile of the blade, named after the inventor, “Gorn profile”. Claudia hands me a small 3D-printed model of a feathering propeller which pretty nicely demonstrates the mechanics in a simple way.
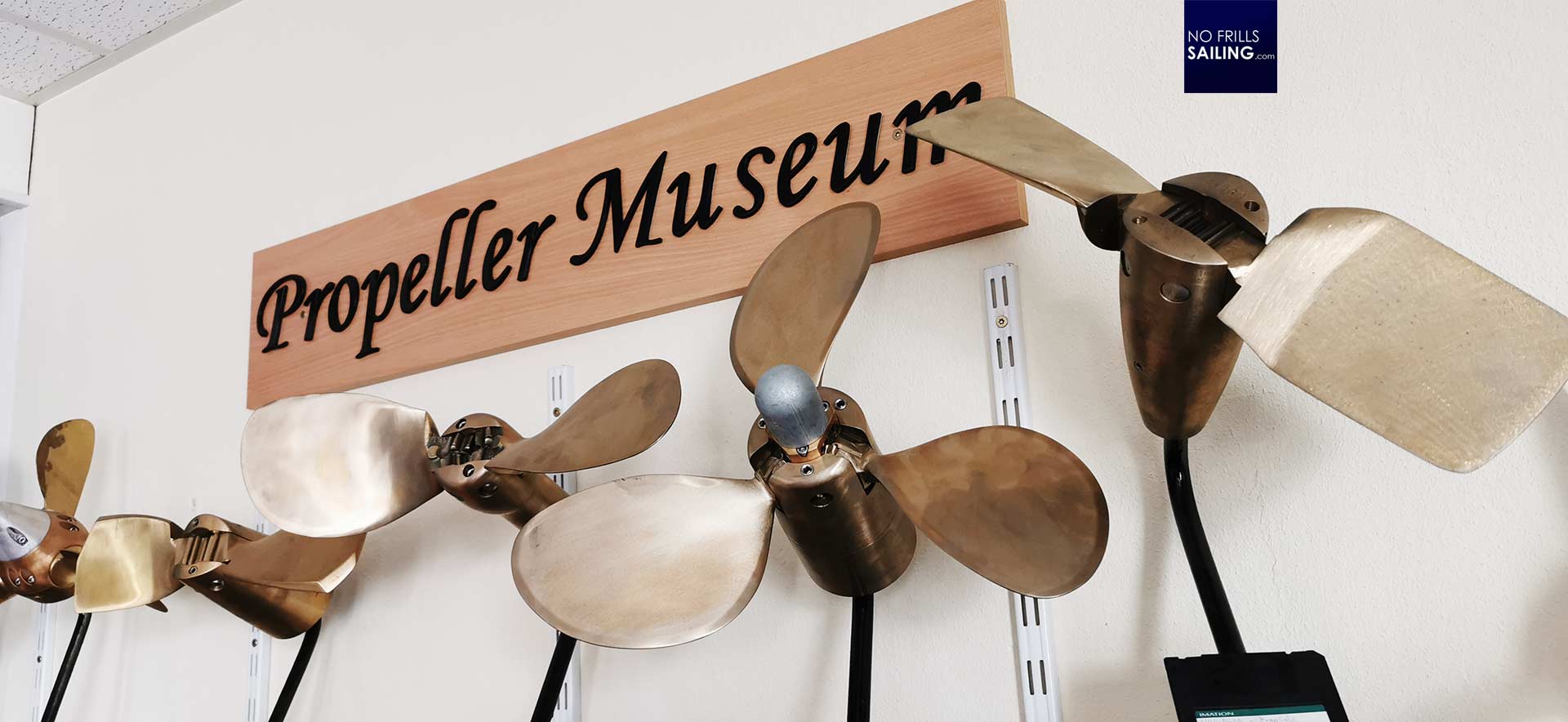
Outside in the museum, a “best of” SPW Propellers is presented. The company had been found by Claudia´s father back in 1988. As her story goes, her dad was an engineer and dedicated sailor. During a docking maneuver the prop´s mechanism failed (it was one of the first generation feathering props) and so, after some weeks of thinking it over and wrapping his engineering head around the problem, he came up with a better solution. Since then, SPW Propellers is one of the few offering those products. Prior ty my visit here I did some research. Many of my trusted contacts in the boating industry confirmed to me that SPW is the “S-Class” or props …
„You can´t get this in China.”
I ask Claudia to give me the full tour and to not spare any details. I love to dive deep into the technical facts of things and it´s hard to get me bored. Since I already had ordered an SPW prop for my own new boat, I made the wish for seeing the production using the example of a 3-blade feathering propeller such as my Omega 42 will be equipped with. “Okay, agreed! Let´s start with the design and brain that goes into a boat´s propeller.”, she says.
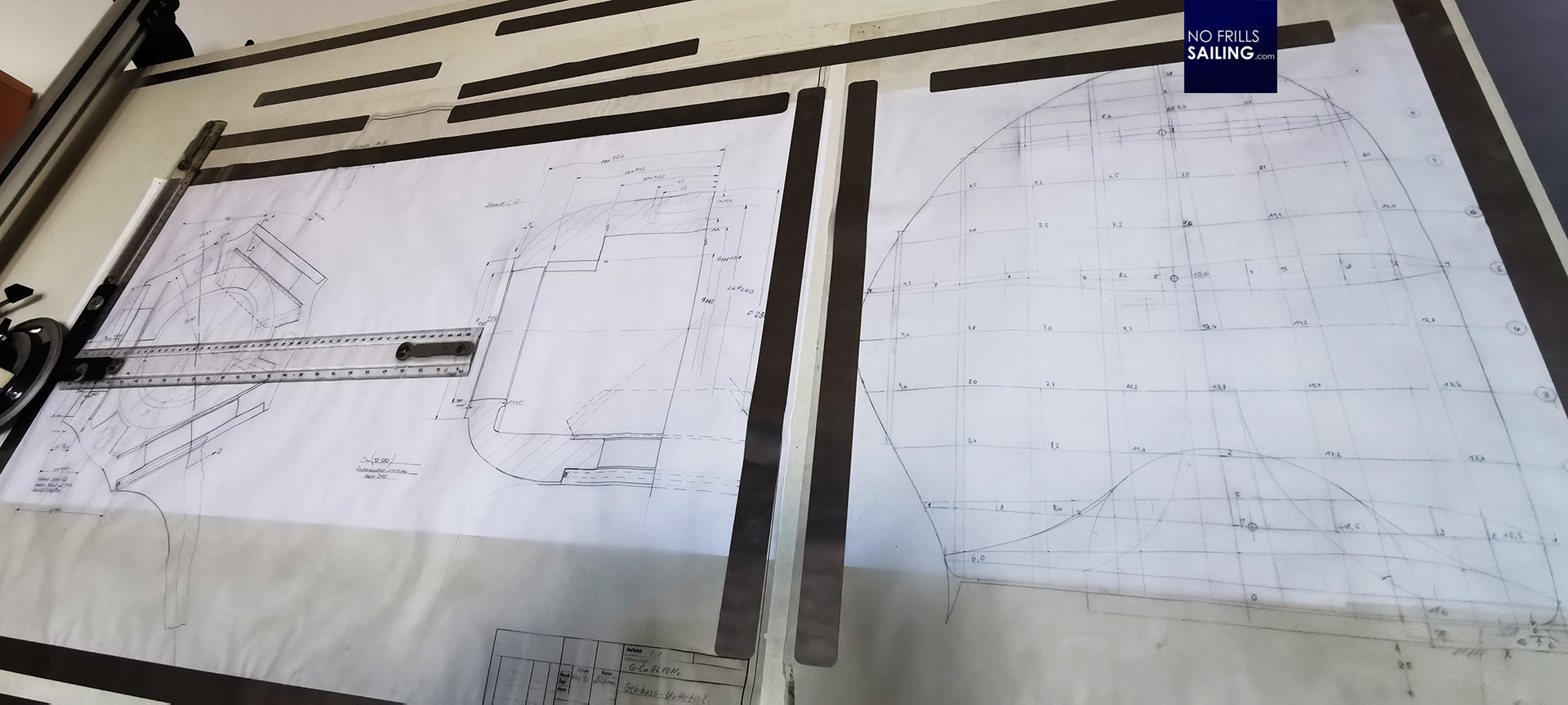
A propeller may seem like a standard part of the equipment. Since the principle of propulsion by rotating blades was invented and patented by an Austrian forester (!) back in 1827 one might think that the evolution of the ship´s screw and the perfection of the working principle has been refined and perfected over the course of 200 years, there is still much potential for improvement. Claudia explains that until a few years when CAD and CFD had taken over the brainwork, propellers had been designed by hand. A fascinating construction drawing made by her father catches my attention.
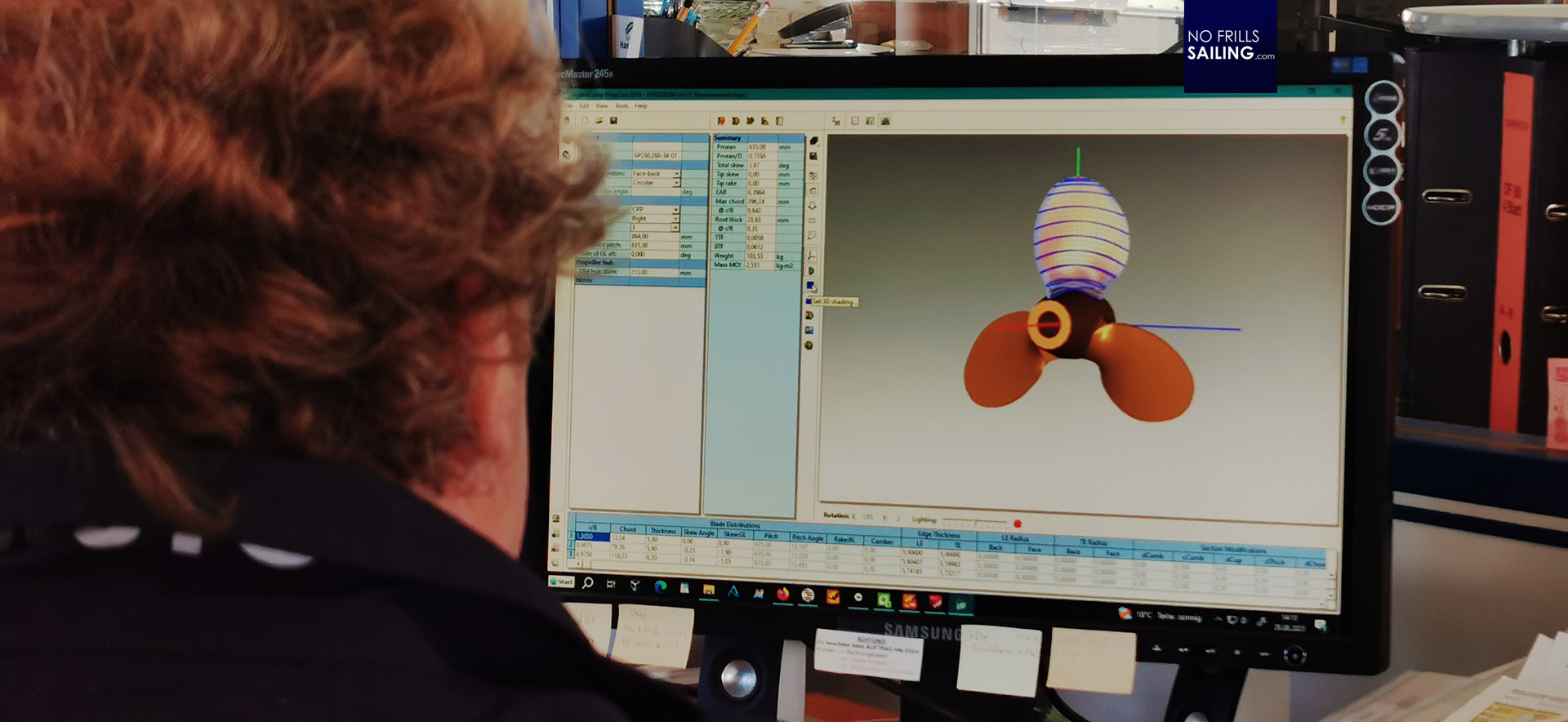
Next door, I get to meet the two engineers of SPW Propellers, one of the being Claudia´s husband. Kind as he is, he opens the files of “my” 3-bladed Variprop and gives me a fascinating short tour through his work. All propellers are nowadays designed using computers and special programs, he tells me, but pulls out one of the numerous thick books out of a shelf over his desk. “Special books about propellers, the workings of fluids or mathematics behind props are still top notch reference.”

The computer models of the propellers are highly detailed models based on coordinates of points, a “cloud” as he calls it, connected by vectors and turned into bent areas. He moves around the 3D-model of my prop on the screen, highlighting different areas, zooming in and out. The model, as he tells me, not just shows the form of the propeller, but already contains all different parts of the propeller. By switching on and off, thus “hiding”, different layers of the computer model, he strips the propeller down step by step: Blades, casing, hub …
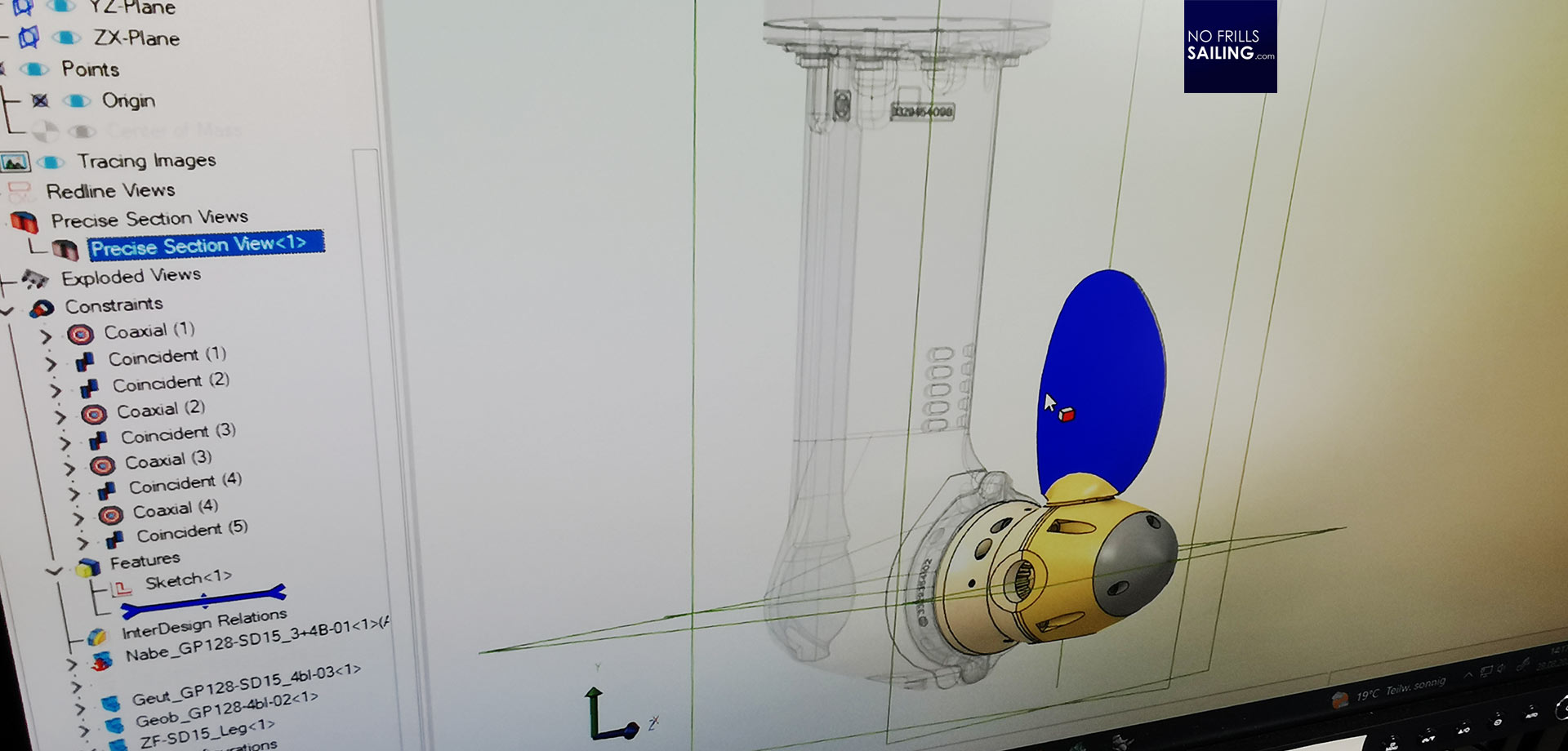
“Right now”, he says “we are in the midst of adapting our complete product range to the new saildrive that is due to being put on the market by ZF”, he says. ZF of Friedrichshafen at the Lake of Constance is another world leading brand and manufacturer of high-grade products t be found literally inside every boat (and maybe also in your car). “We have been provided with a 3D-model of the new saildrive to check if our product still fits perfectly or if we could further improve our props.”
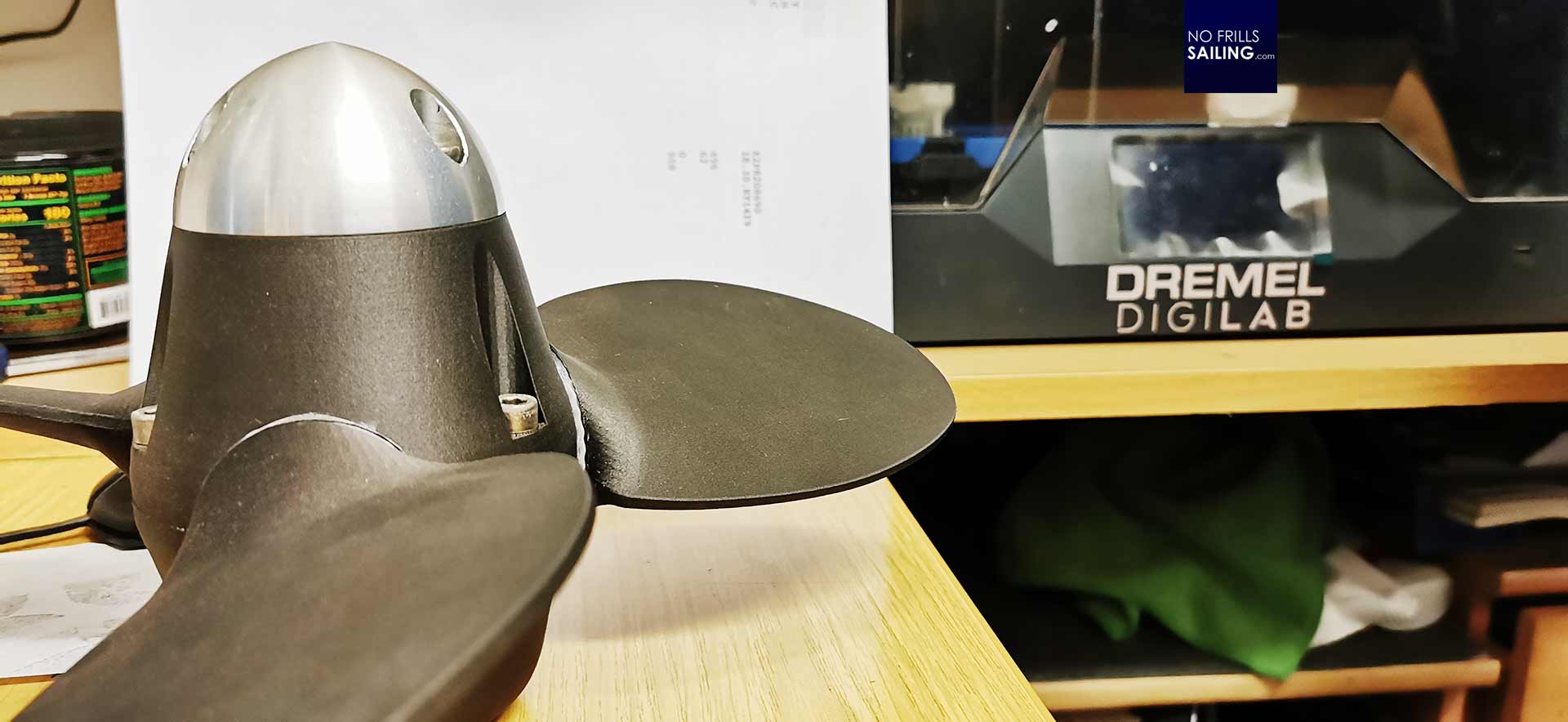
To do so, SPW owns a “farm” of different 3D-printers for rapid prototyping. With a high degree of accuracy and certainly faster than any modelmaker could do, the engineering department can feed these printers and after some waiting time receive the models. “We can check if our adjustments or changes are valid”, he says. And he smiles: “I literally can see how a prop will do underwater. I can sense if it is balanced or imbalanced, if it cavitates or is just right.” Fascinating!
A guided tour through the SPW prop-production
The know-how of this engineering department, the immensity of the accumulated knowledge and experience in her husband´s brain alone is a cornerstone of SPW Propellers, Claudia tells me. The constant strive for better and better shapes, the functions of the folding or feathering mechanisms and adaption to new drivetrains or even completely new trends, like electric propulsion makes SPW highly versatile and market leading: “Other brands did not develop a new shape in 15 years”, she says: “But invested in great marketing instead …”
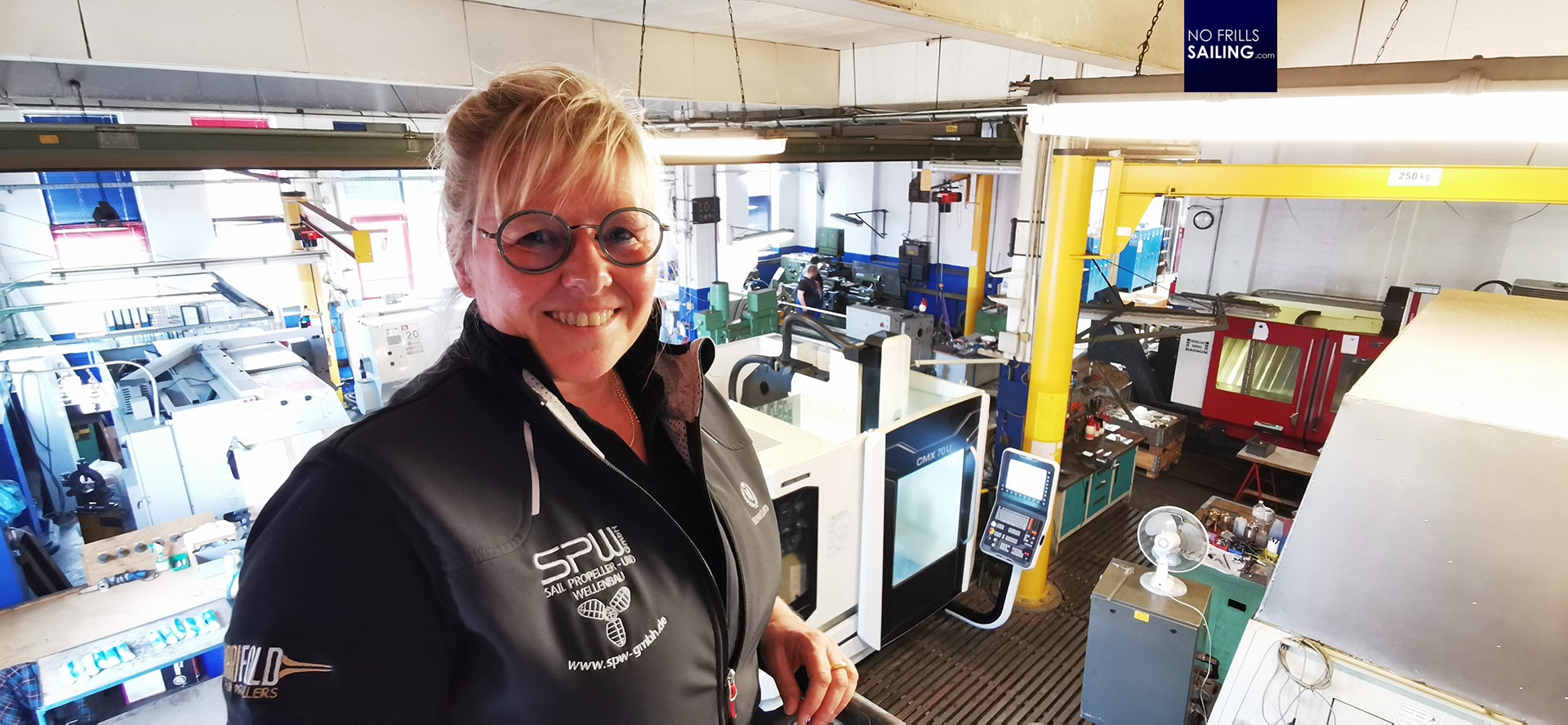
We enter the big production hall. “It´s vacation time now so we run at half speed, it´s literally calm”, she says and has to speak loud against the noise of the various metal-working machines. I smile. We stand on a balcony and I have a great oversight on the production. People are working in front of turning lathes, CNC-milling machines and racks. “Let´s start with the blanks“, Claudia says and we proceed to the first station.
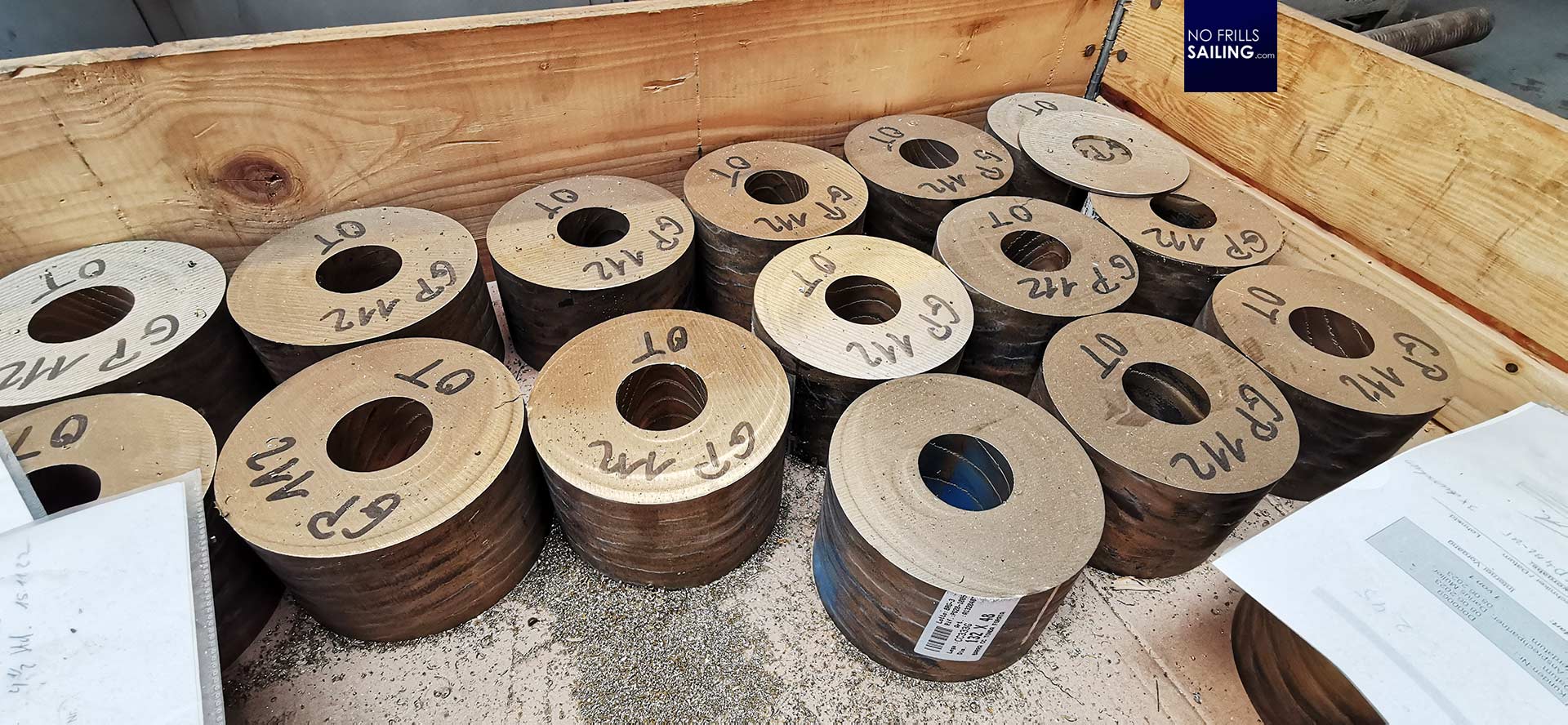
Heavy blocks of bronze chunks are placed in a wooden chest. Claudia tells me that SPW uses exclusively Aluminium-Nickle-Bronze as material for the propellers: “Many of our competitors utilize Manganese-Bronze alloy, which is easier to cast and also significantly cheaper.” Thus, their products are much attractive for the budget-oriented client but: “Maganese-Bronze is softer so it´s more prone to damage. Our propellers are Ice-certified and so I can proudly say that we are the first choice for many, many expeditionary yachts or skippers sailing the North-West-Passage.”
Handmade by experienced craftsmen
Just a few steps next to those blanks, which will later be turned into propeller-casings, we meet a young chipping professional proceeding the first refining step of turning the raw cast blades into propeller blades. “We solely work with German furnaces”, Claudia tells me: “There are just three of them in our country able to deal with the delicate demands of Aluminium-Nickel-Bronze. The casting process is highly complicated.” Weighing a rough cast blade blank in my hands, we step in front of his workplace: A milling machine.
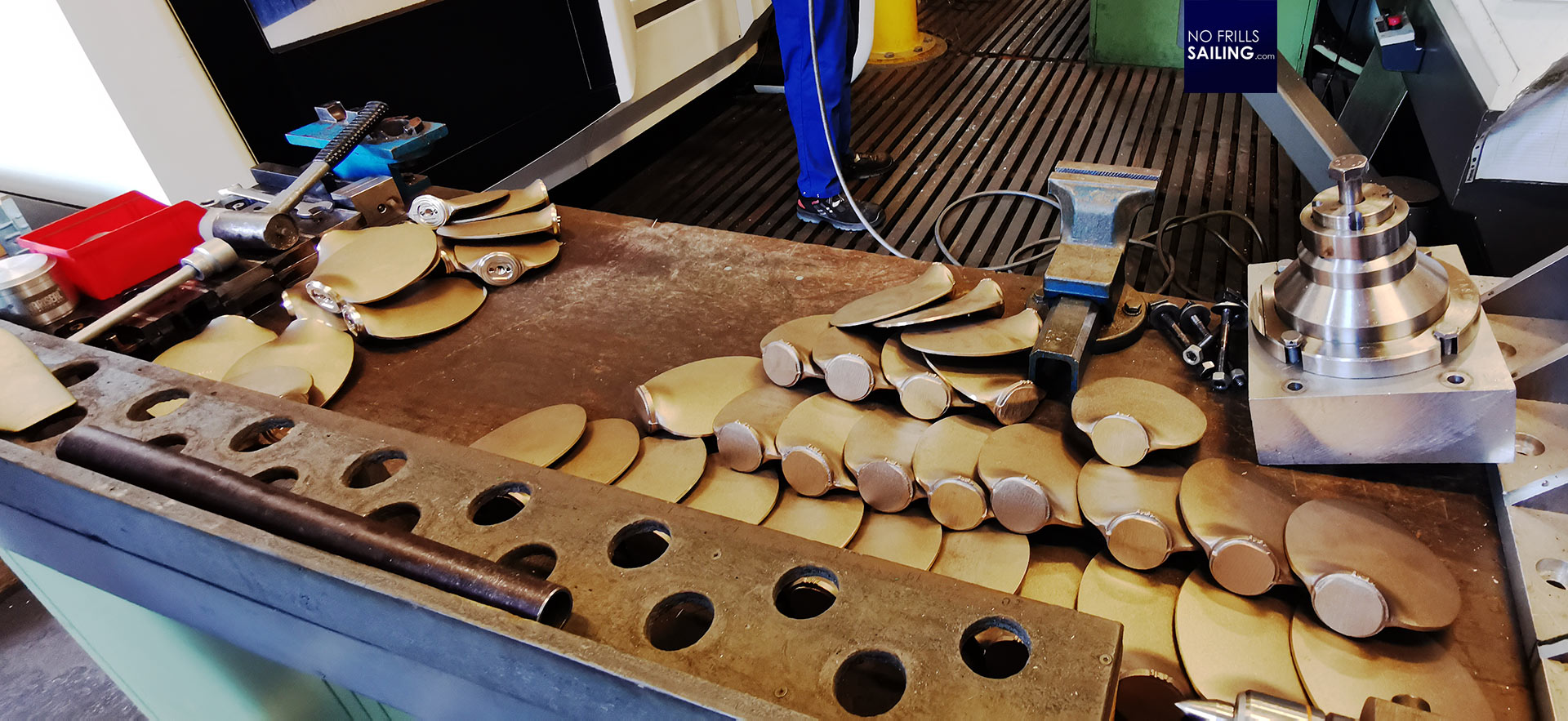
The rough blades are put into a CNC-milling machine. Adjusted by the young man, he closes the door and starts the program. With a precision that can only be guaranteed by a machine, the laser-guided robot-arm starts to take off material from the blank by a fraction of a millimeter. Layer by layer, the blunt rough blank more and more turns into a shiny blade.
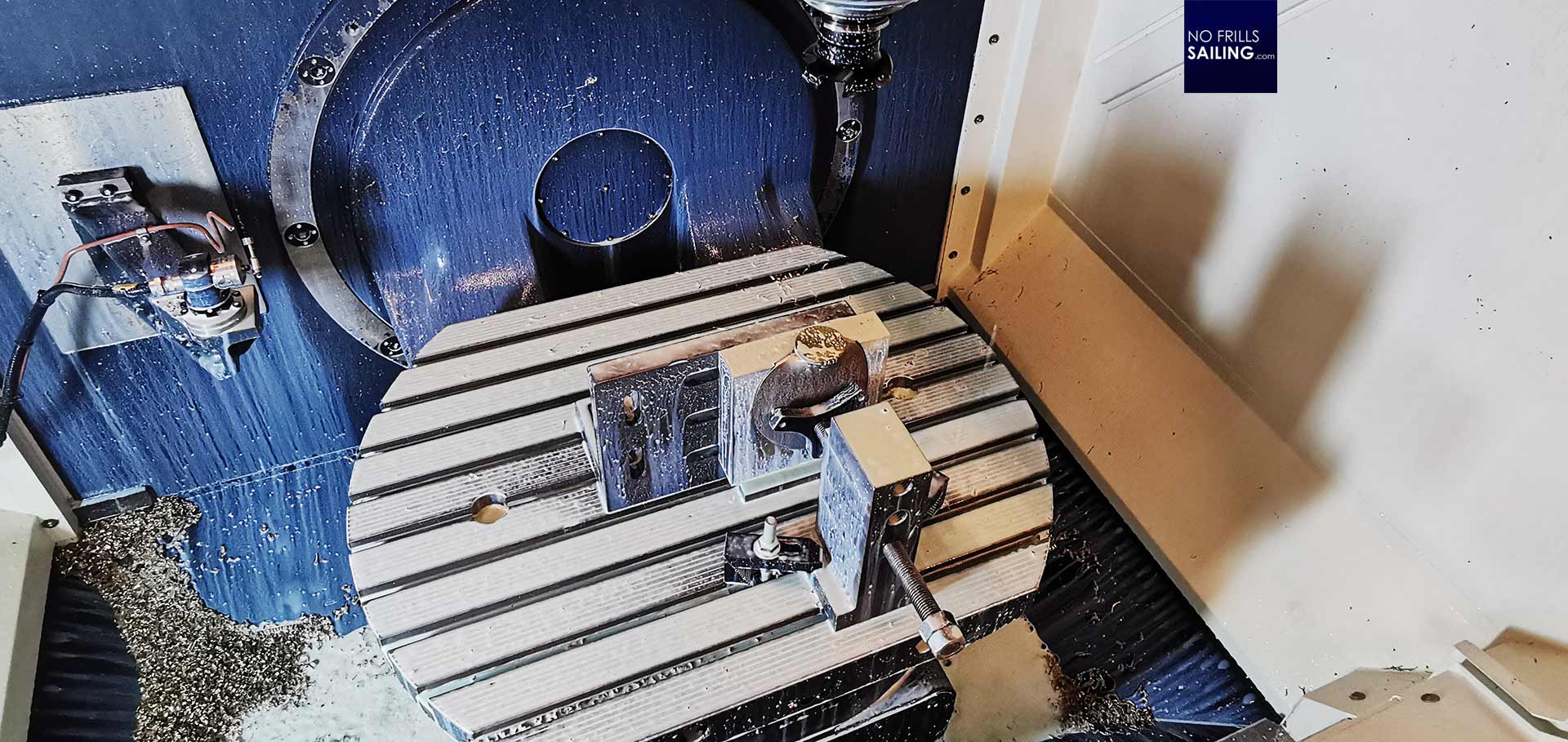
Coolant is constantly sprays onto the fast rotating tool and the bronze metal part. It´s an emulsion resembling cow milk that not only cools the material but also prevents both the tool as the bronze from corrosion. In this first step the machine will create a joint where the next robot can grab a firm hold onto the blade. Taking care of the smooth running of the machine, the right program and flawless operation, he takes out the blade after the process is done and places a new blank inside the box.
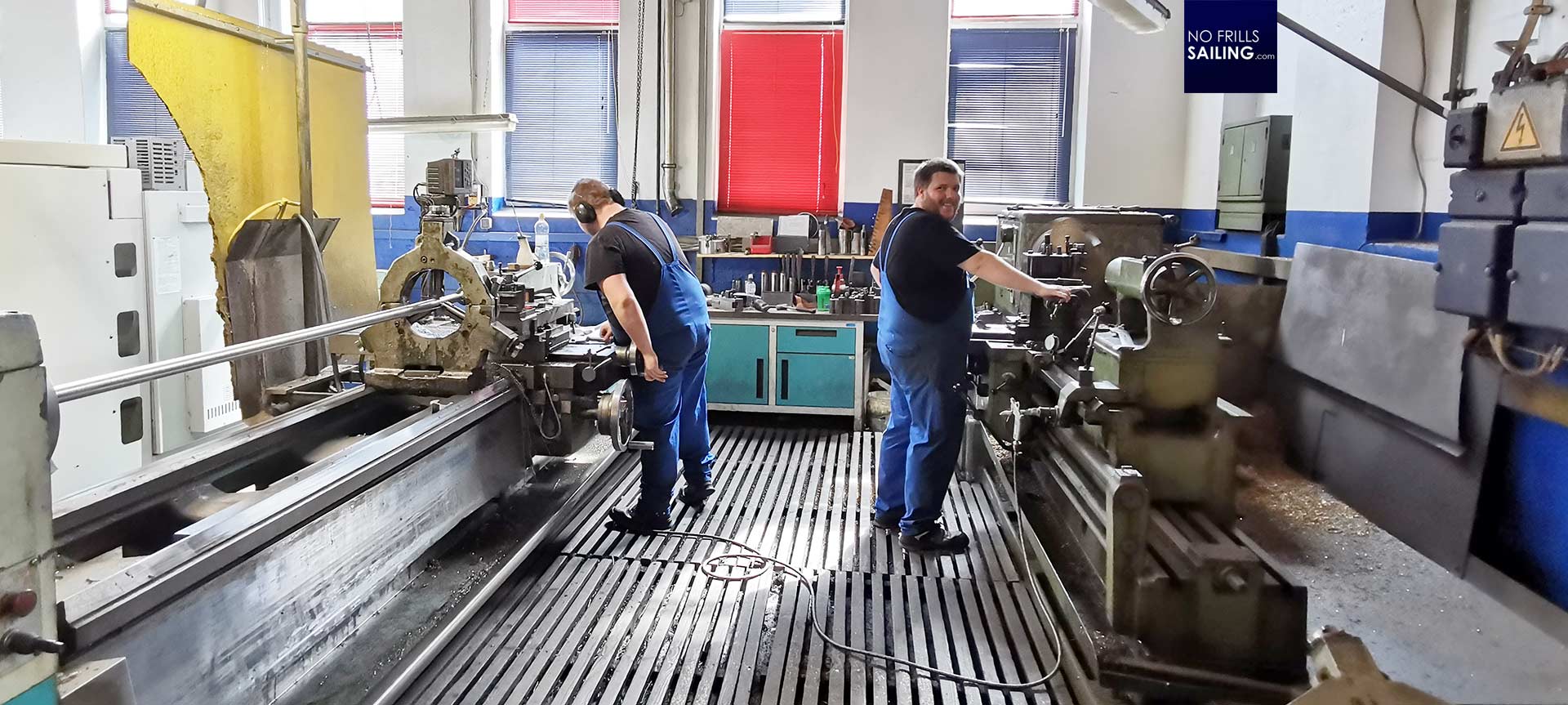
“Depending on the type and size of the propellers we are working on”, he tells me, “I can manufacture one blade every four minutes.” In pride he stands before his machine: A mast craftsman metal-worker, making sure that my propeller is a flawless piece of metal right here at the first of many production steps. I do not even try to quick calculate how many propellers he can make in a week, if he works five days eight hours daily and produced a blade every four minutes …
Meeting Kuka: Industry 4.0
“Here in Bremerhaven we produce and deliver a total of 1.300 to 1.700 propellers per year”, Claudia says. Pride in her eyes for a company that has achieved market leadership through innovation and quality. Part of this leadership is the constant investment in new technology and production machinery – SPW was one of the first medium-sized business to adopt “Industry 4.0”standards. “Let´s meet Kuka”, she says.
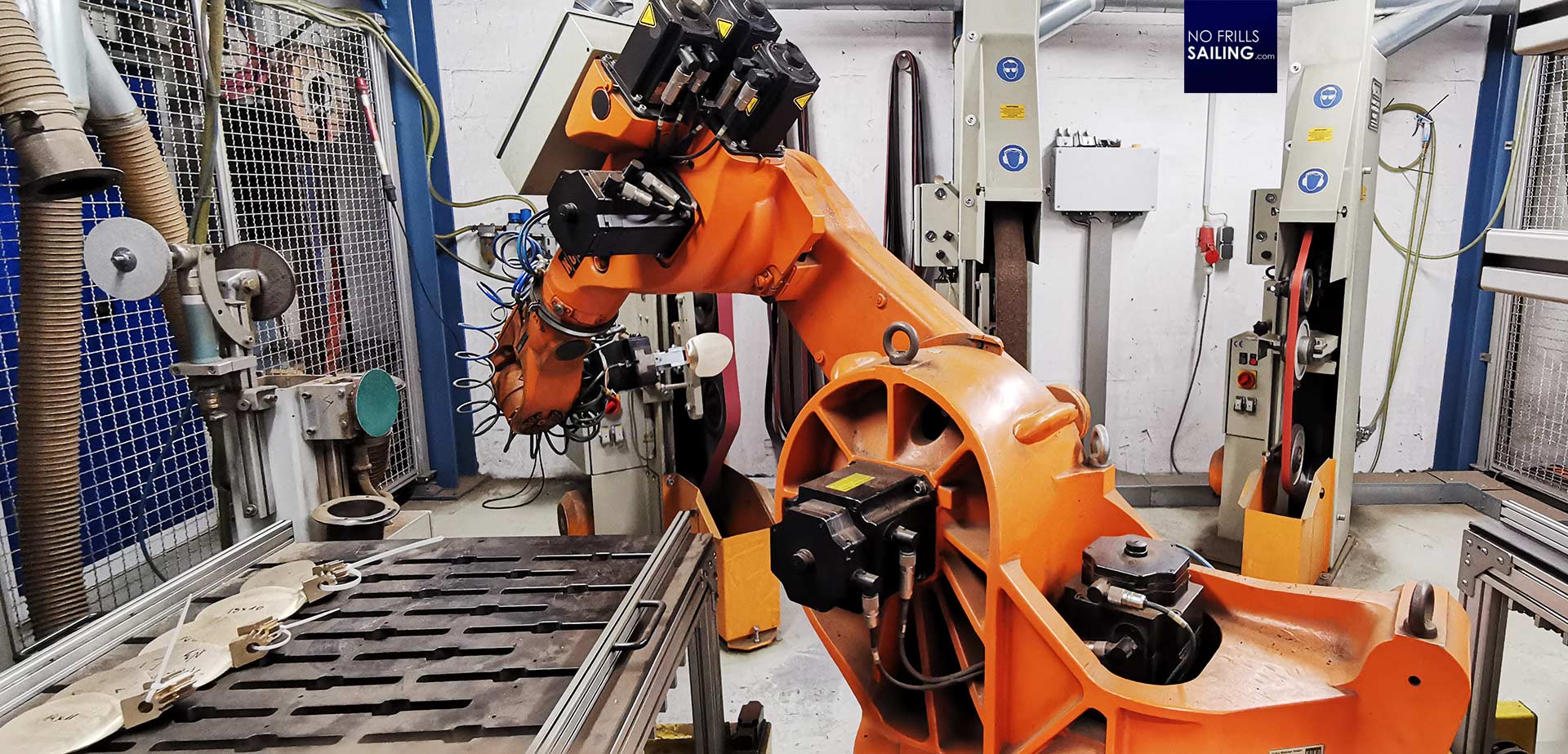
Behind a protective safety cage, a hoge orange robot is humming. Kuka is the name of this high-precision robot: As Claudia explains, this robot is receiving the roughly milled prop blades from the working station we just left. “It will take the blades from a designated area, grabs it to the CNC-milled handle and starts to sand down the surface of the blade according to the CAD-data you have seen on the computer screens in our R&D-department.”
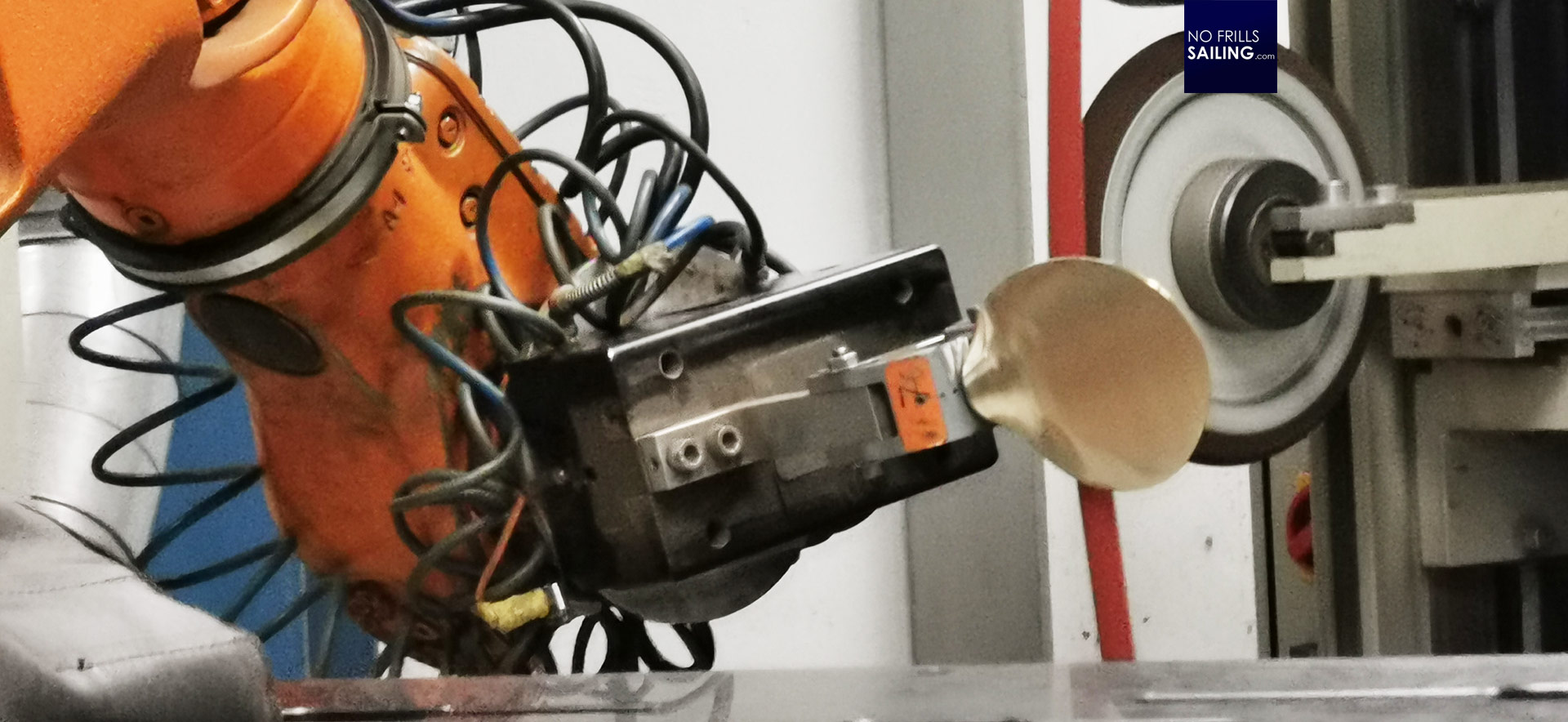
Watching Kuka at work is absolutely tantalizing. Just like a human would do, the arm presses the metal work piece firmly, but somehow with “care”, against the belt sander. It goes up and down and slowly but steadily has the full area of the blade sanded. “This production step can also be done by our metal workers”, Claudia explains, “but it is inevitable that even the most skilled craftsman will have small inaccuracies in his work. Sometimes the pressure is too low, so that material will be left on the piece, sometimes the pressure is too high so that more material is taken off.” The result can be an unbalanced mass, inconsistent flow of water and in the worst case cavitation.
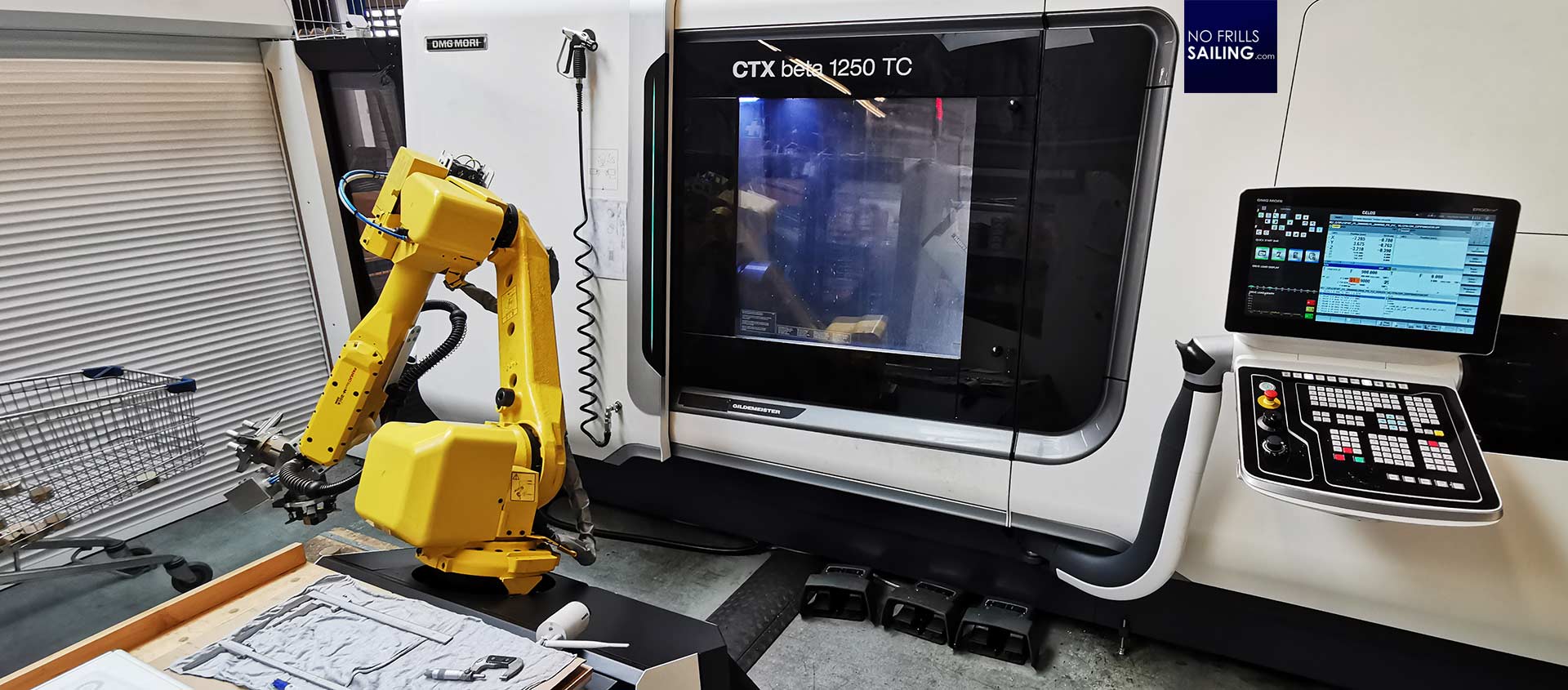
“Kuka”, is observed and managed by Valerie, also a skilled metal expert working for years here. He explains that working with a robot over the years has increased the quality of the products significantly and changed not only this, but also the pace: “Kuka works effortlessly his shifts even much longer than eight hours. He is never sick and never needs a vacation.” On the other hand, Claudia insists, even Kuka needs meticulous regular cleaning and as with every high precision machinery, the tiniest things can cause a breakdown.
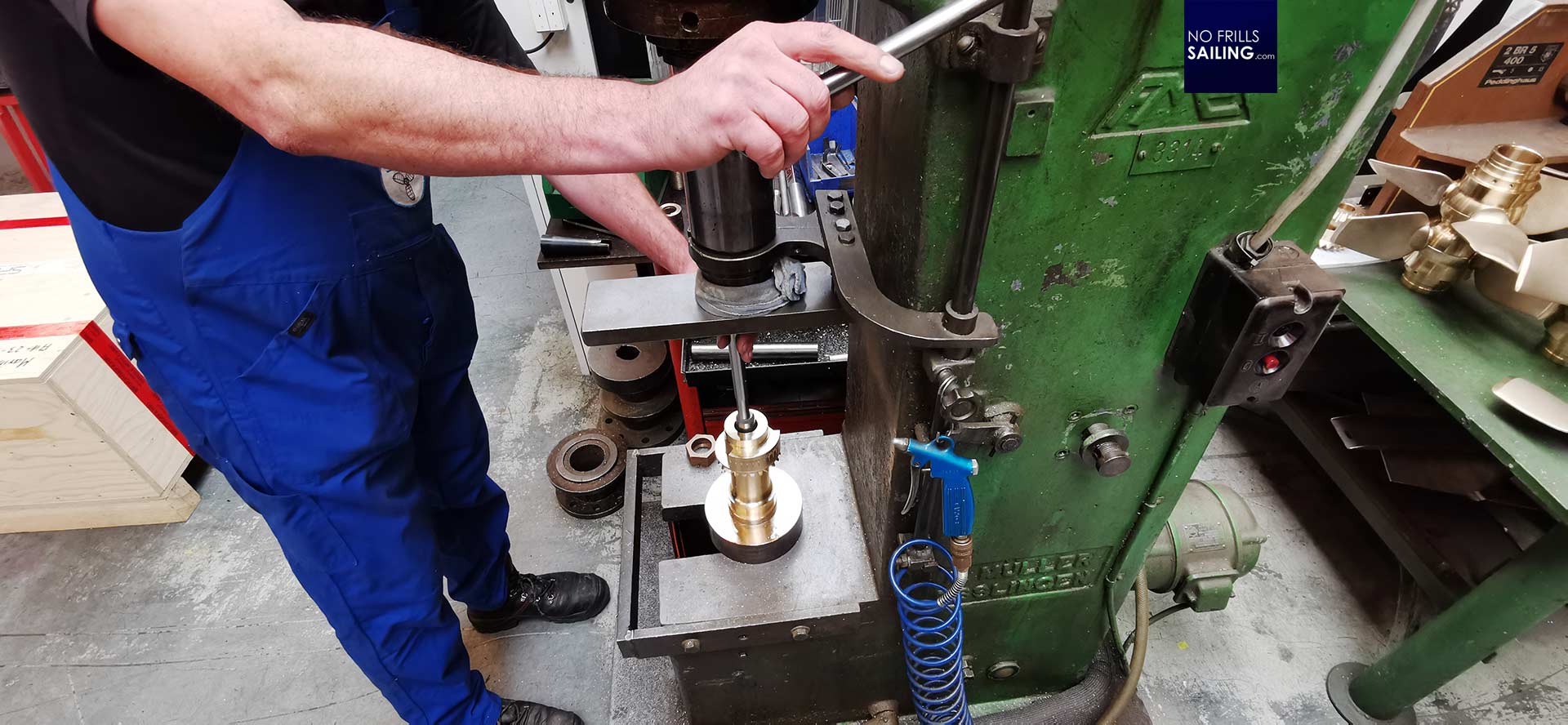
There are many more computers and robots in this production hall like Kuka. Industrial 5-axis-arms capable of even the most complicated procedures, some made by DMG Mori – which reminds me of the Imoca 60 racing yacht sponsored by this company, closing the circle here. “We try not to overcomplicate things”, she says: “We utilize computers and robots where it is necessary and reasonable, but I would always prefer to trust the skills of my fellow colleagues.” Which may seem like a contrast, I understand, in reality is what makes this company so strong: Another metal worker is driving a spline into one hub, using a hydraulic precision machine from the 1950ies.
Fitting the propellers
Having seen the principle production steps for each of the different parts of a feathering propeller, we proceed to the next adjoining hall. Milled and sanded, the shiny polished parts of the propellers are stacked into commissioning racks. This awesome sight reminds me of those good old heist movies: After breaking into the vault of Fort Knox, the bars of pure Gold are gleaming seductively.
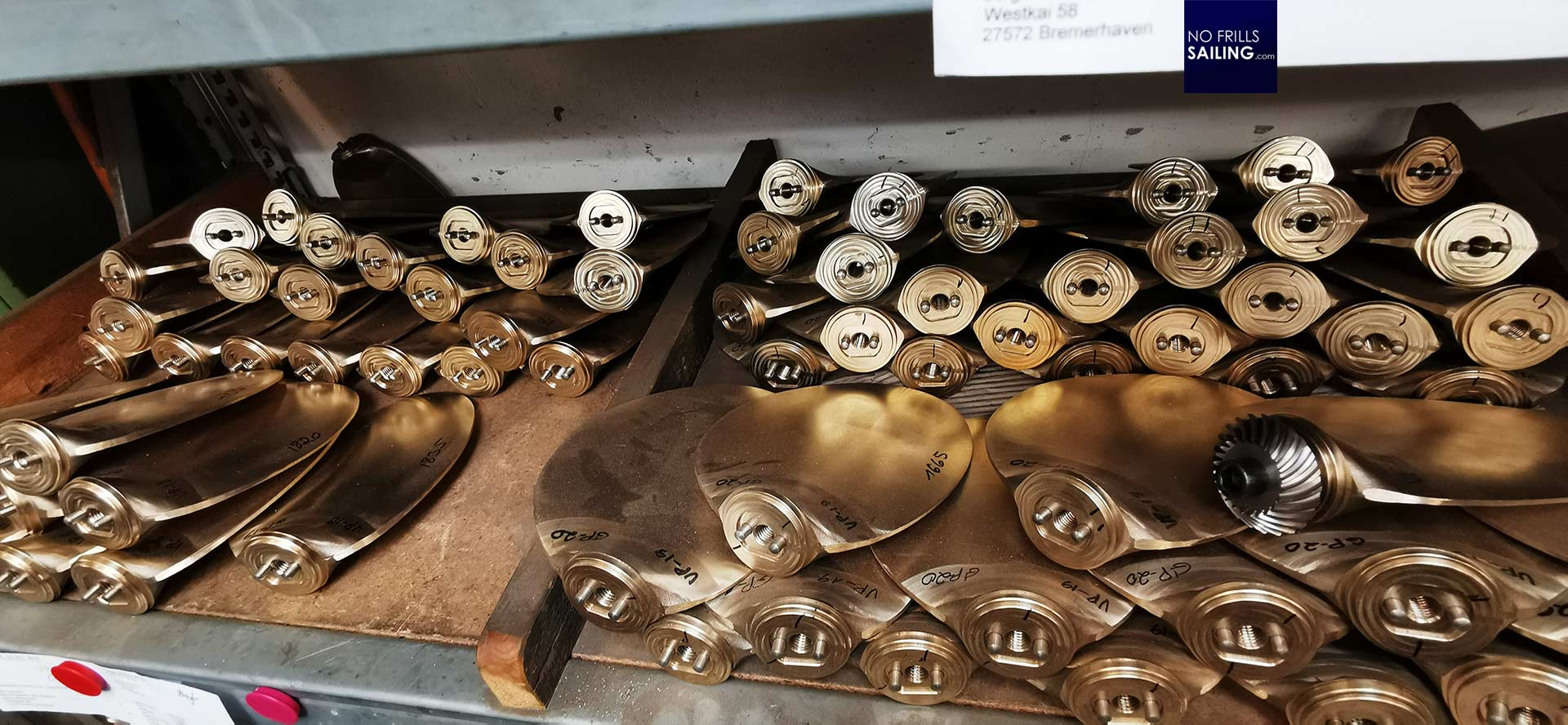
The commissioning racks are indeed the Fort Knox of SPW: Both standard propellers as well as customized parts are put here to be assembled by the skillful hands of the people working here. “Each propeller – thus yours as well – has its own production number”, Claudia explains: “We have consistent protocol for each part of the propeller stating a seamless record of its passage through the production. In this, we can track down every change or customization.” That is why all these parts have their own dedicated number.
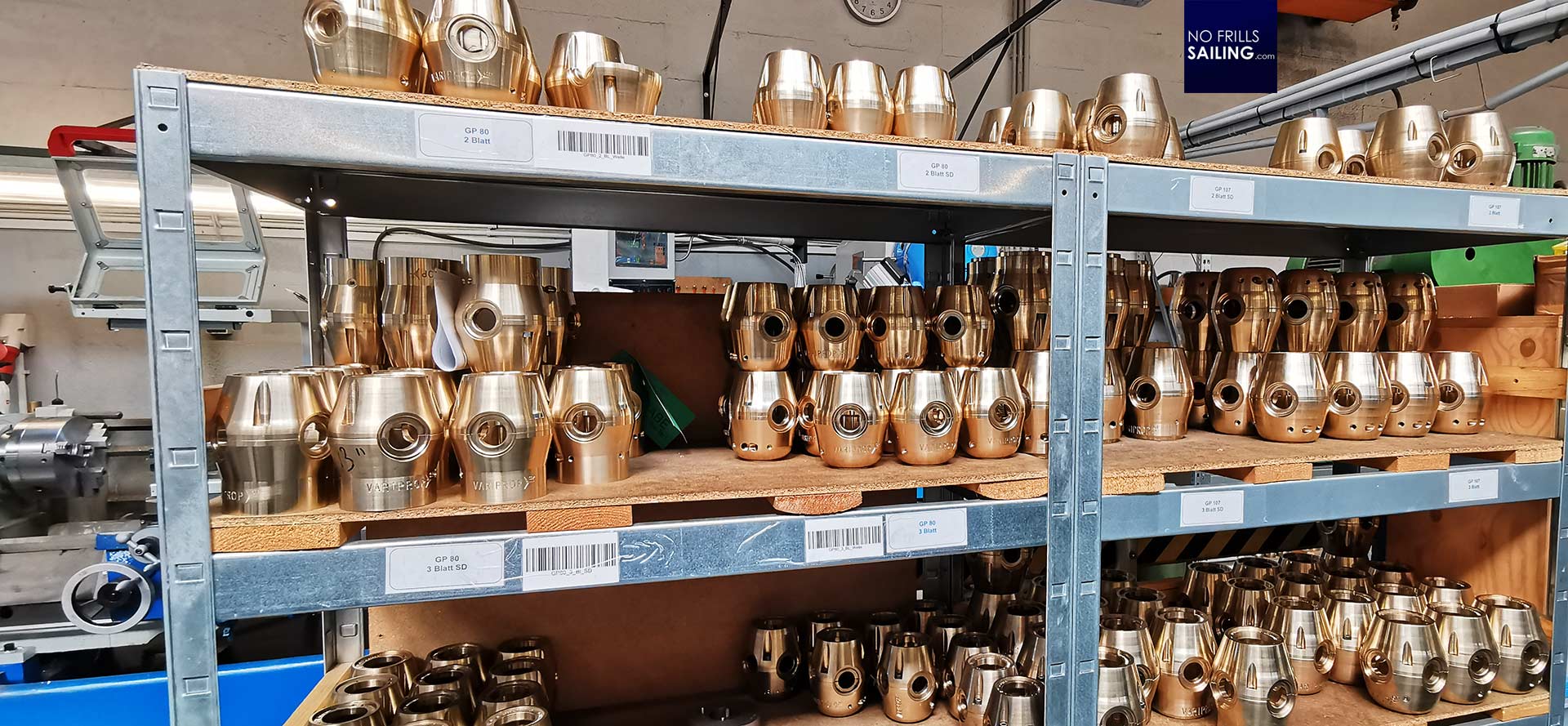
The next rack is full of shiny brand new casings for the Variprop feathering propeller. Claudia takes out two casings: “Both principally are the same prop your Omega 42 will have. The one in my left hand is a casing especially designed to fit a saildrive. The other one is optimized for shaft driven boats.” As there is nothing in front of a shaft other than the shaft itself, the casing needs a different, hydrodynamically perfected form whereas the saildrive-mounted casing is the aft part of a the saildrive fin. Kind of completing the body of revolution of both saildrive plus prop-casing.
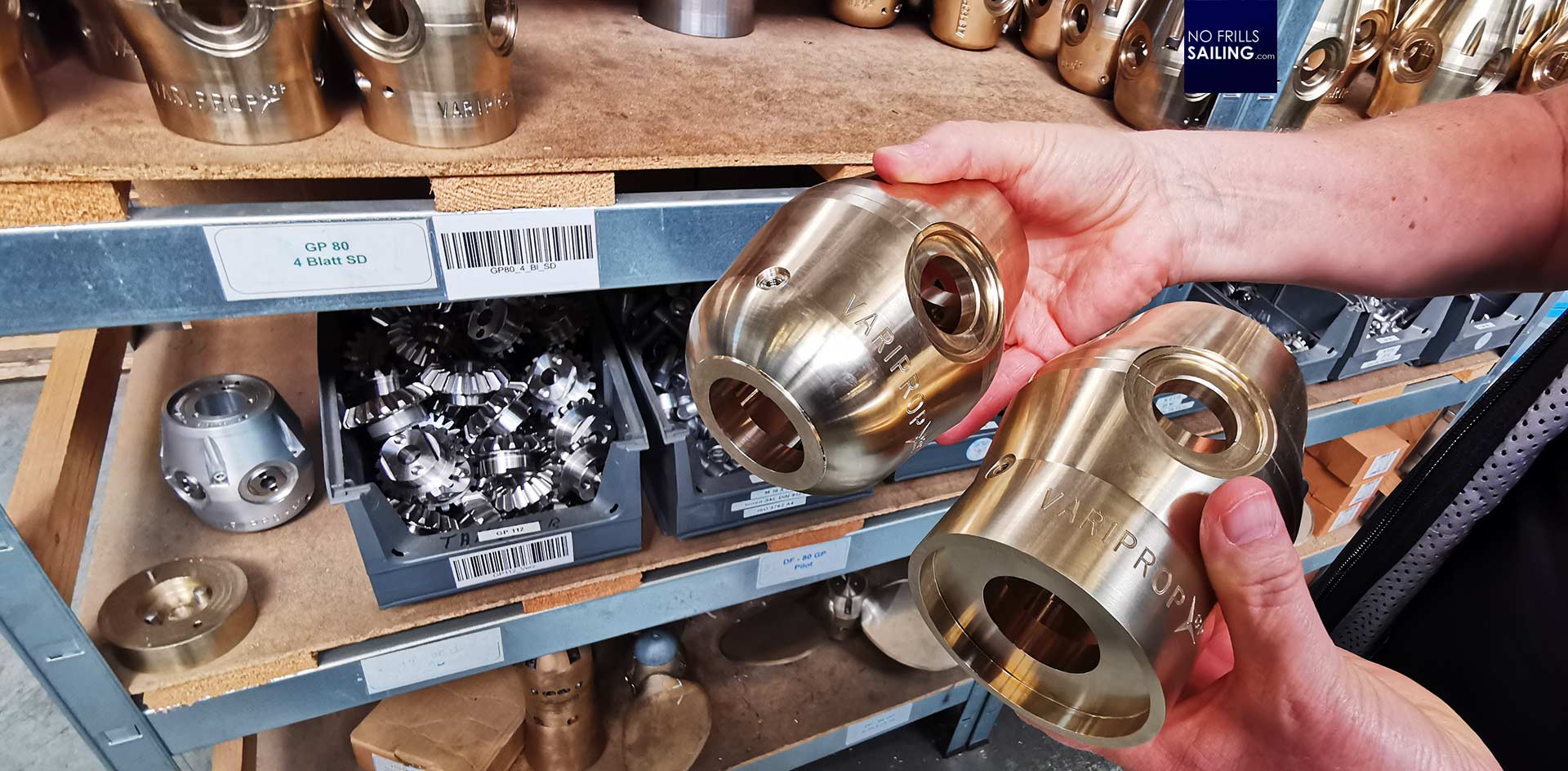
“We also designed the casings specifically to take on different anodes and even rope cutters”, she tells me: “These are all those tiny details making such a seemingly simple thing like a propeller a very difficult and complex product.” Now I begin to understand that such a constant effort, the strive for keeping up with changes and optimization may be copied, but not fully obtained. “It takes a full year, Lars, to develop a propeller …”
Unique feature of an SPW feathering prop: Adjustable pitch
Standing at one of the assembly desks, Claudia gets a hub and one backside of a casing: “This is again one of the same propellers you ordered with us. I want to show you something.” She takes the hub which is a beautifully manufactured piece of craftsmanship: With a watchmaker´s precision. “You remember when I asked you to give me all the data about the Diesel engine and the saildrive-type of your Omega 42?” I nod. “This is why we needed it …”
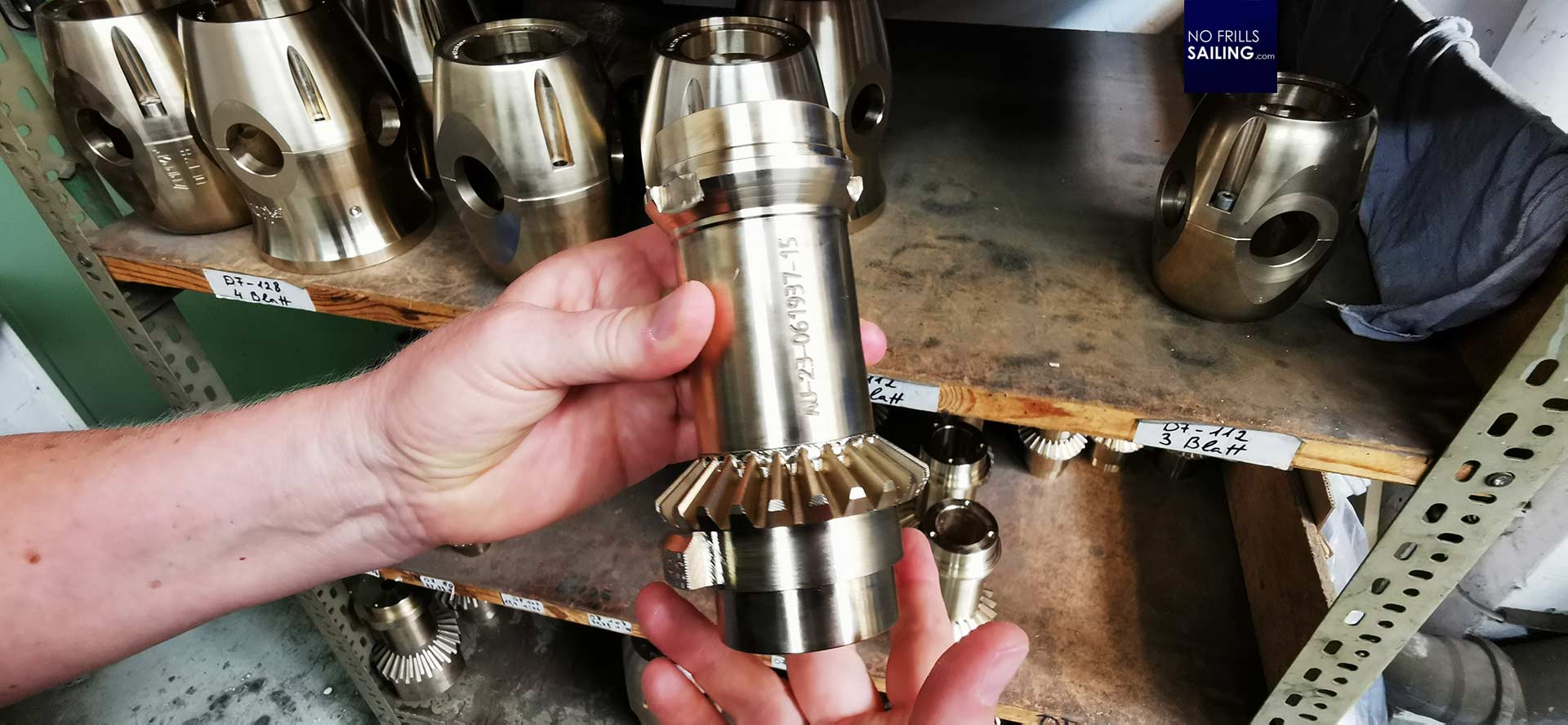
Each SPW Variprop feathering propeller is individually adjusted to perform most efficiently for the different combinations of shaft, angle of shaft, type and power of engine and saildrive. “In this, there is a difference in going forward or abaft”, she says. The pitch of the blades are different for both. This is calculated and noted in the protocol. She shows a scale on the hub: “These are the degrees of the pics. The finishing step is that the metal worker has to take off material here from the hub according to the pitch calculated.” For each – and – every – single – prop.

Basically, there is not “the one” standard propeller, even if the type may be the same, it is always adjusted for forward and backward motion to fit the individual drivetrain and engine. But there is even more: “Our Variprops can be finetuned too”, she says: “If you want to adjust the pitch, you simple need to literally turn one screw and be able to further improve the prop even after years. I will show you later.”
Refit and repair: Propeller caries …
It´s not only the development and production of folding and feathering propellers for new boats, SPW is also engaged in refitting and refurbishing propellers. The company can handle props of a size up to 1.60 meters in diameter, which is quite a size indeed! Claudia shows me a palette with two fixed blade props, one of them already finished, the other awaiting treatment.
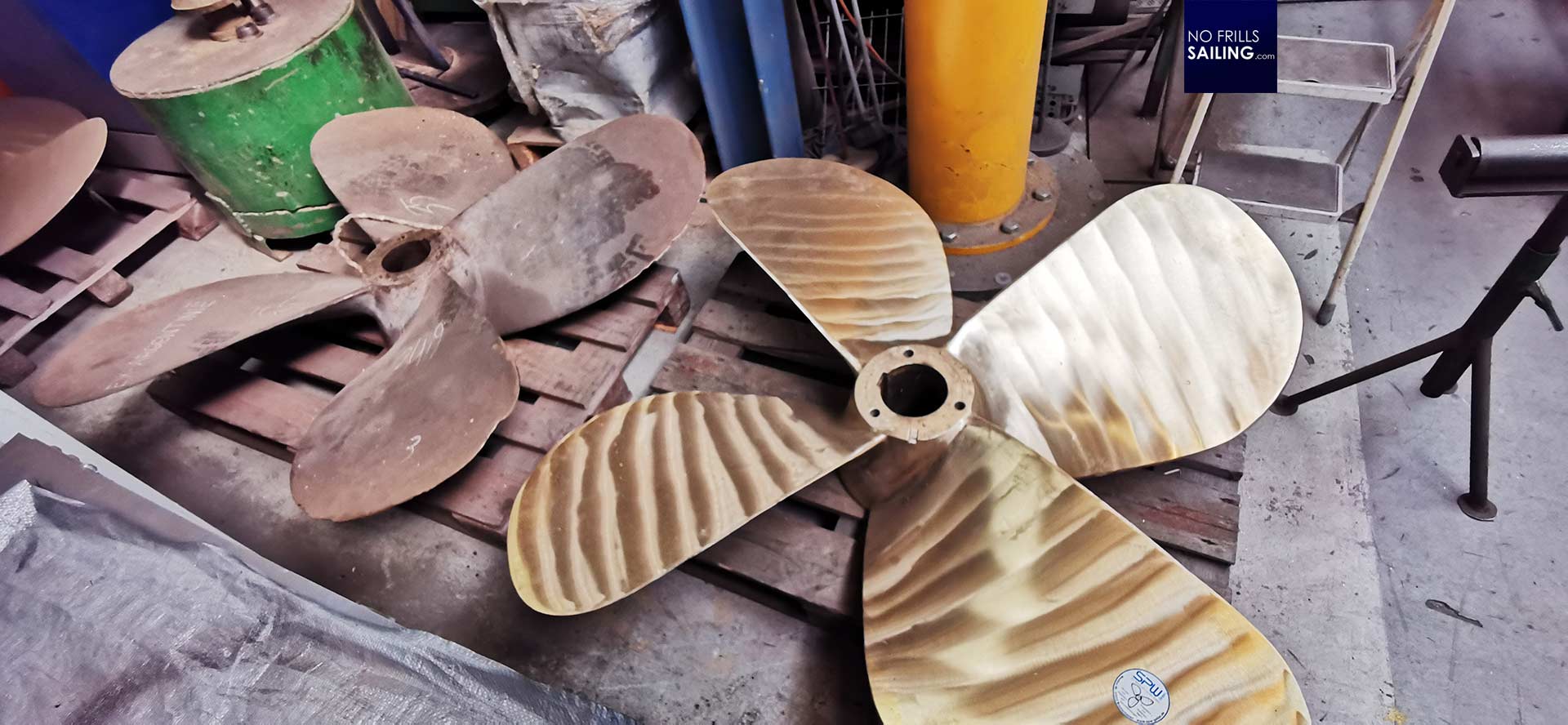
“We have laser and computer-guided equipment to scan and digitalize any propeller sent to us”, she tells me. In this, her husband in R&D can swiftly work out the profile and come up with ideas if and how a prop should be refurbished or “updated”. Sometimes, Claudia tells me, it is just a polishing job and the “ironing out” of some minor damage, sometimes, it´s more than that.
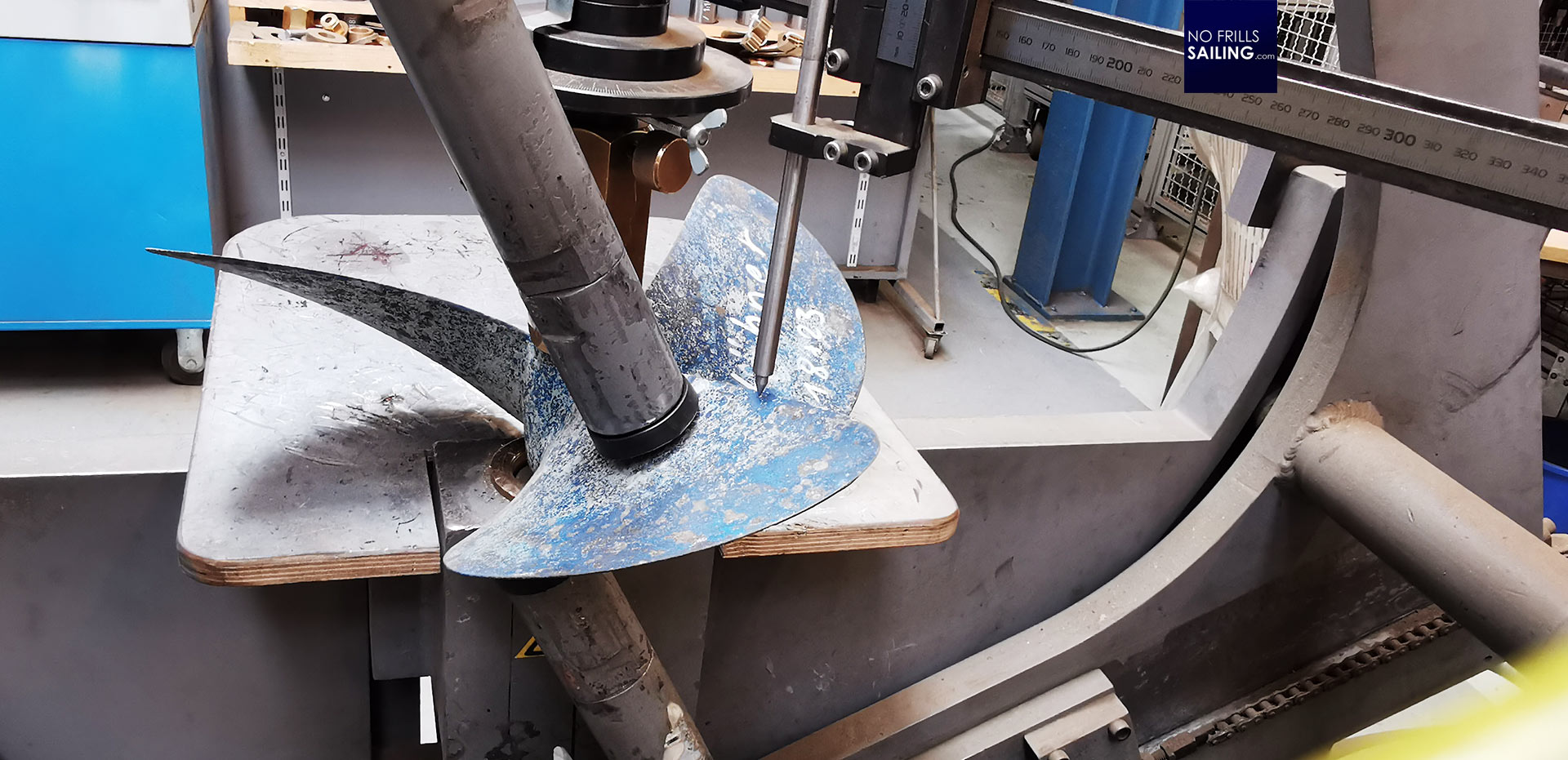
Again, the company has a fleet of available instruments and machinery to get the job done: Another good old hydraulic press from the past Century is used to apply corrections to dents and warpage in the blades. “We often have pleasure craft sailors in our refurbishment program, but mostly it´s professional shipping. Fishing boats for example and many tug boats.“ As these are operating with high power screws and working really hard, their propellers are frequent guests as they are prone to cavitation damage.
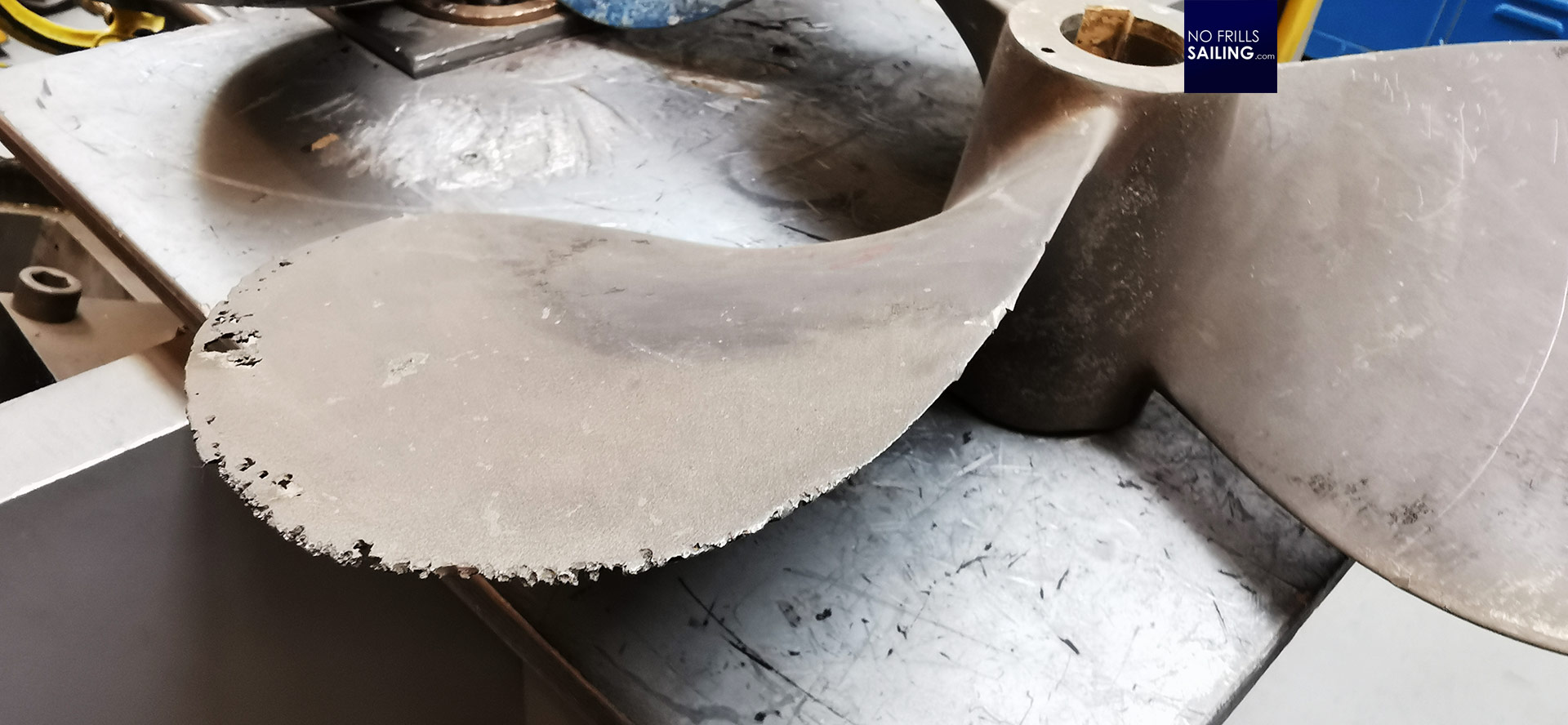
Valerie returns from the back of the storage with a particularly beautiful specimen showing the dssastrous effects of cavitation. As the trailing edges of the propeller blades make the water boil (lower temperature under pressure, just like in our home kitchen pressure cookers), this water turns to little bubbles of steam which immediately pop being cooled down. Those micro-implosions, over time, literally eat away the blade, blowing off material bit by bit. I´ve never seen the effects of cavitation in reality before.
A bright future – with dark clouds
Claudia is seemingly proud of the company. And she has every reason to be: This highly efficient production process is combining the knowledge and craftsmanship of skilled and trained people, most of which started here as apprentices in their youngster years.
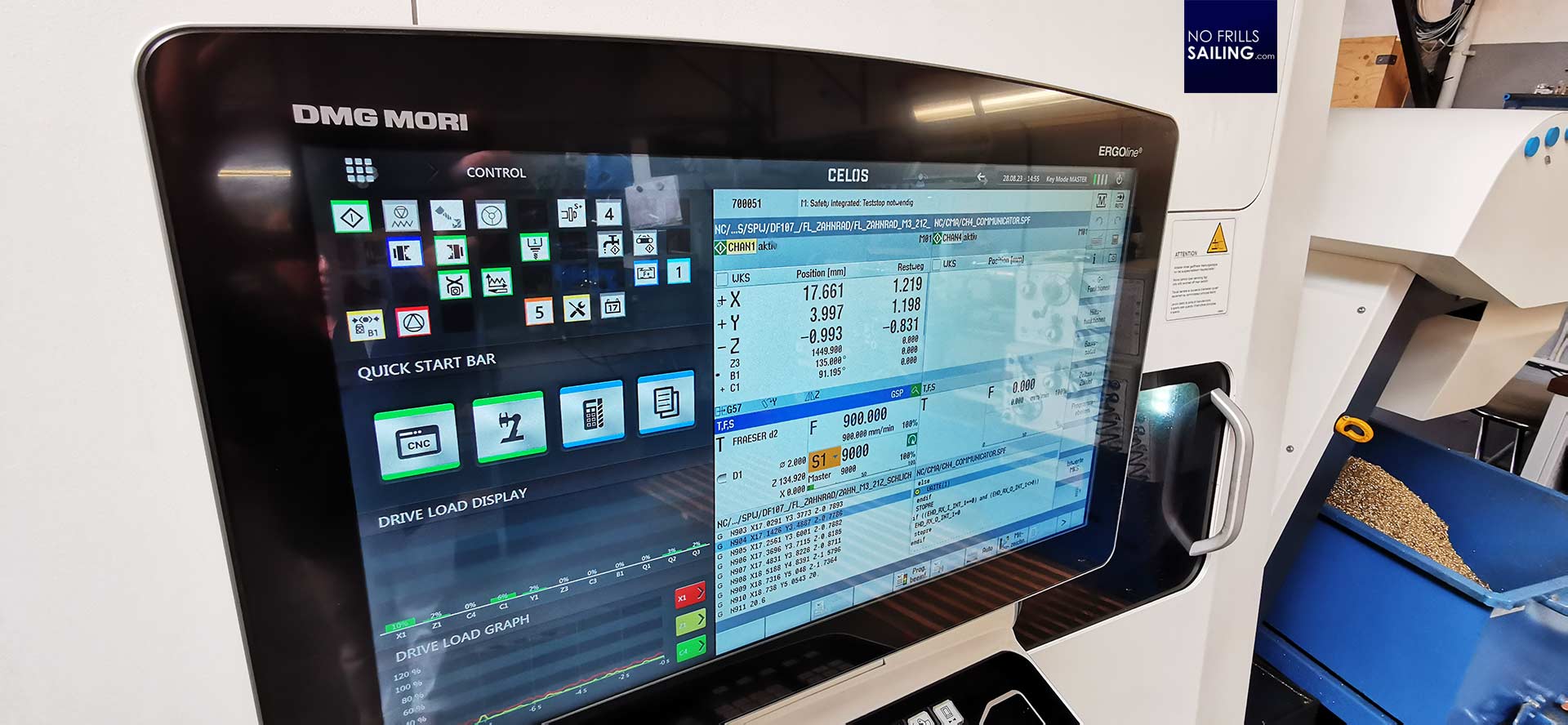
SPW is constantly investing in updating their equipment and machinery to improve the fabrication. “I know that we lack the shiny front-page marketing of other brands”, Claudia admits, but I´d say that their growing customer base and satisfaction with the products they deliver is an even more efficient and credible word-of-mouth strategy which no advertising campaign can match. Nevertheless, there are also obstacles and challenges to overcome.
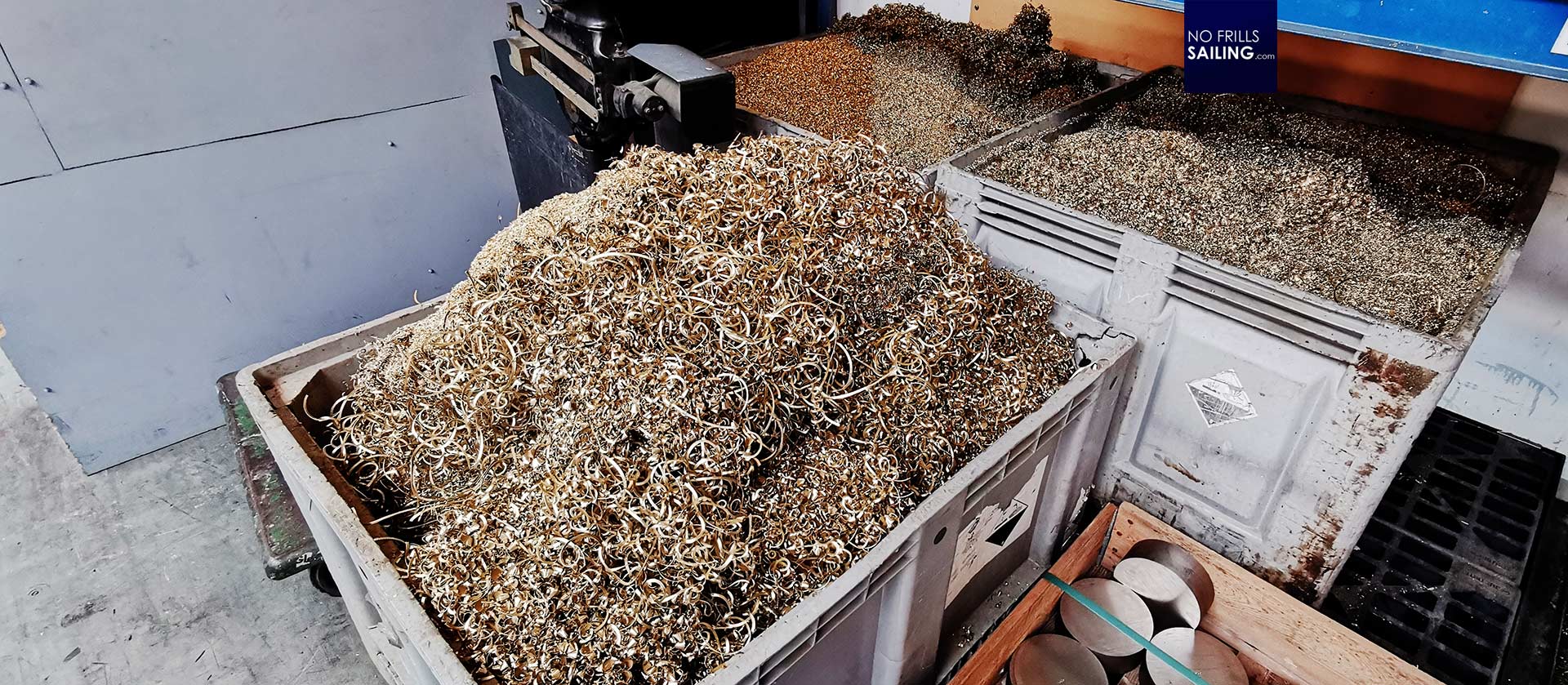
„We sweep up every little offcut and splinter from our floors”, says Claudia as she shows big containers. “Selling these – otherwise scrap metal – has become a very profitable business. This shows how precious the material we work with has become.” Not to mention the crazy prices for electricity which makes cost intensive production (just think of the staggering amount of energy consumed by the furnaces to melt and cast the blanks) super expensive. Germany in particular and Europe as a whole have become increasingly hard for business owners. Although I cannot see any house-made shortcomings at this company, there are definitely dark clouds on the horizon.
The SPW Variprop feathering propeller for my Omega 42
After some three most interesting and exciting hours we end up where we started, right in the entrance area where the little “Propeller Museum” is located. Like my mom used to prepare the traditional Christmas table of presents, during our tour of the factory somebody had prepared a desk with a little surprise for me: The propeller I had ordered at SPW some weeks ago, at that time only following the suggestion of Heiner, the owner of the shipyard that builds my Omega 42. He had said: “If you want the right stuff, go for this brand!” Now after seeing all this, I am sure this was the right decision.
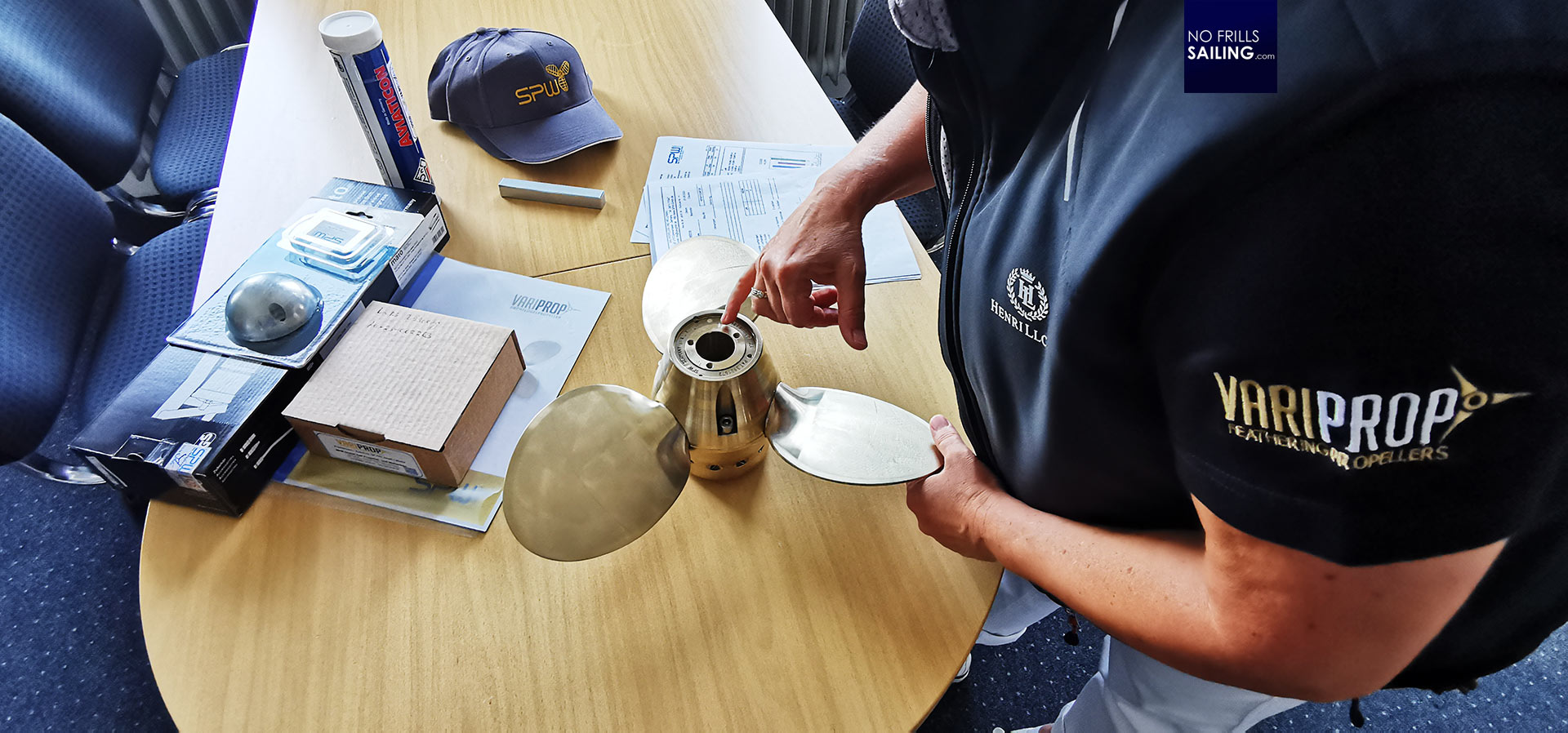
Claudia explains the features of my propeller, shows me how to tune the pitch, where to put the grease and the anode and makes sure I will check the warranty. I notice a little label on one of the blades. It reads “DNV-GL”-approved. Asking what this means, she explains that SPW propellers are the only on the market with an independent certificate of safety and quality. No other propeller has the official approval by a technical certification body. Let that sink in …
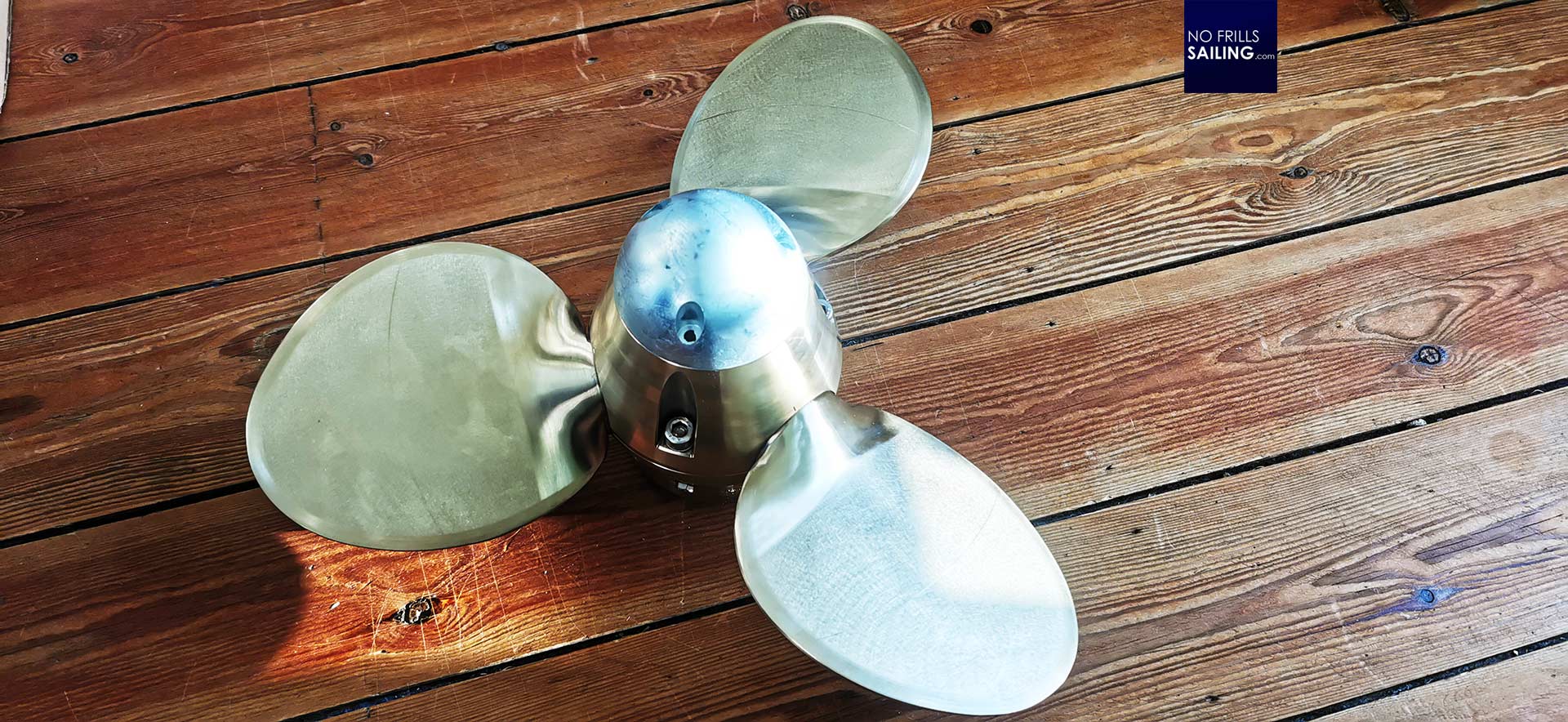
Back home in my flat I unbox the precious shiny little thing. This propeller will be mounted to my boat soon. Having seen how dedicated and skilled the whole crew in Bremerhaven worked to manufacture this piece of art, how much effort of designing and shaping this product and how much care went into this, I feel like I can now fully appreciate the art and craftsmanship properly. If you happen to sail to Bremerhaven, tie up your shore lines to the West Kay and pay a visit to Claudia Adamczyk and her great team: It´s a visit that may change your attitude.
You also might be interested in these articles:
Appreciating the work that goes into designing a Seldén mast
Tradition meets high-tech: A day at Wempe Chronometers
How it´s made: A child´s life jacket