I know what you might be thinking right now: Cranchi? That´s a brand of motoryachts, why are you writing about motorboats in a magazine called NO FRILLS SAILING? Well, the answer comes quickly: Because I was so amazed what I have seen in Italy last week that always thought to myself: “What if these people would start to build sailing yachts?” Flat and frank: They´d probably making vessels which could easily match the most noble and advanced yachts in the world. This is why …
Getting a feeling for the boat: Cranchi M44
I did take the chance to join a group of boating enthusiasts to make a dash down to Italy for 2 days, following an invitation of Cranchi Yachts last week. A bumpy flight to Milan and some 4 hours driving to a place some 50 kilometers east of Venice, our first encounter with Cranchi – and my very first with a motor boat – took place at the Cranchi Test Centre. Yep, you heard right: A full rigged testing ground.
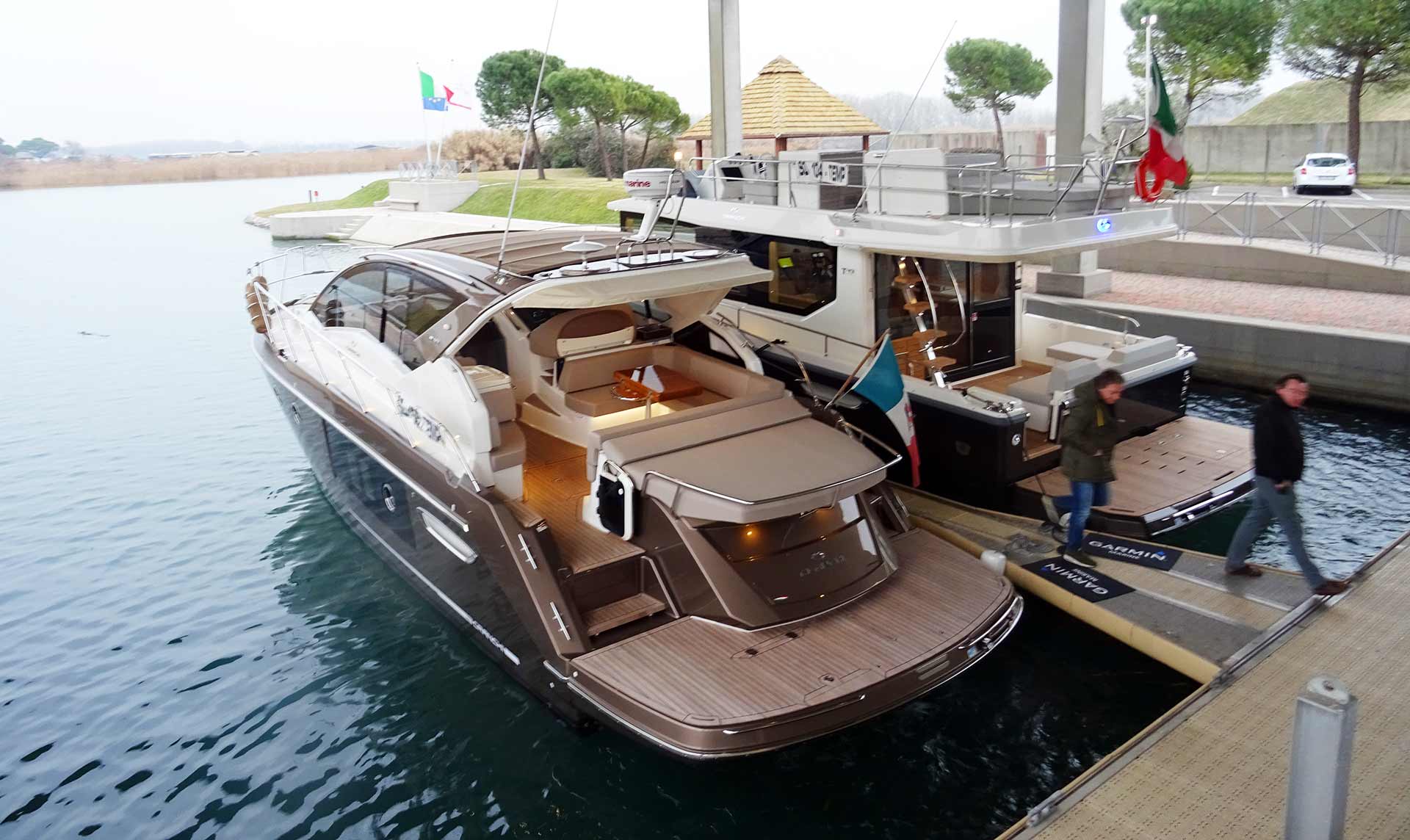
Upon arrival Cranchi did had two boats already in the water, engines running and getting warm, lights on, heating active (as it had chilly 2 degrees Celsius that day) and everything prepared. That´s what I call professional. The test centre blew me away: Cranchi has all boat models (except for the really big ones of +60 feet) ready for a go if a costumer or willing buyer needs a demonstration. Boats will be craned, put in the water and manned with a skipper. Off you go. And this is what we did.
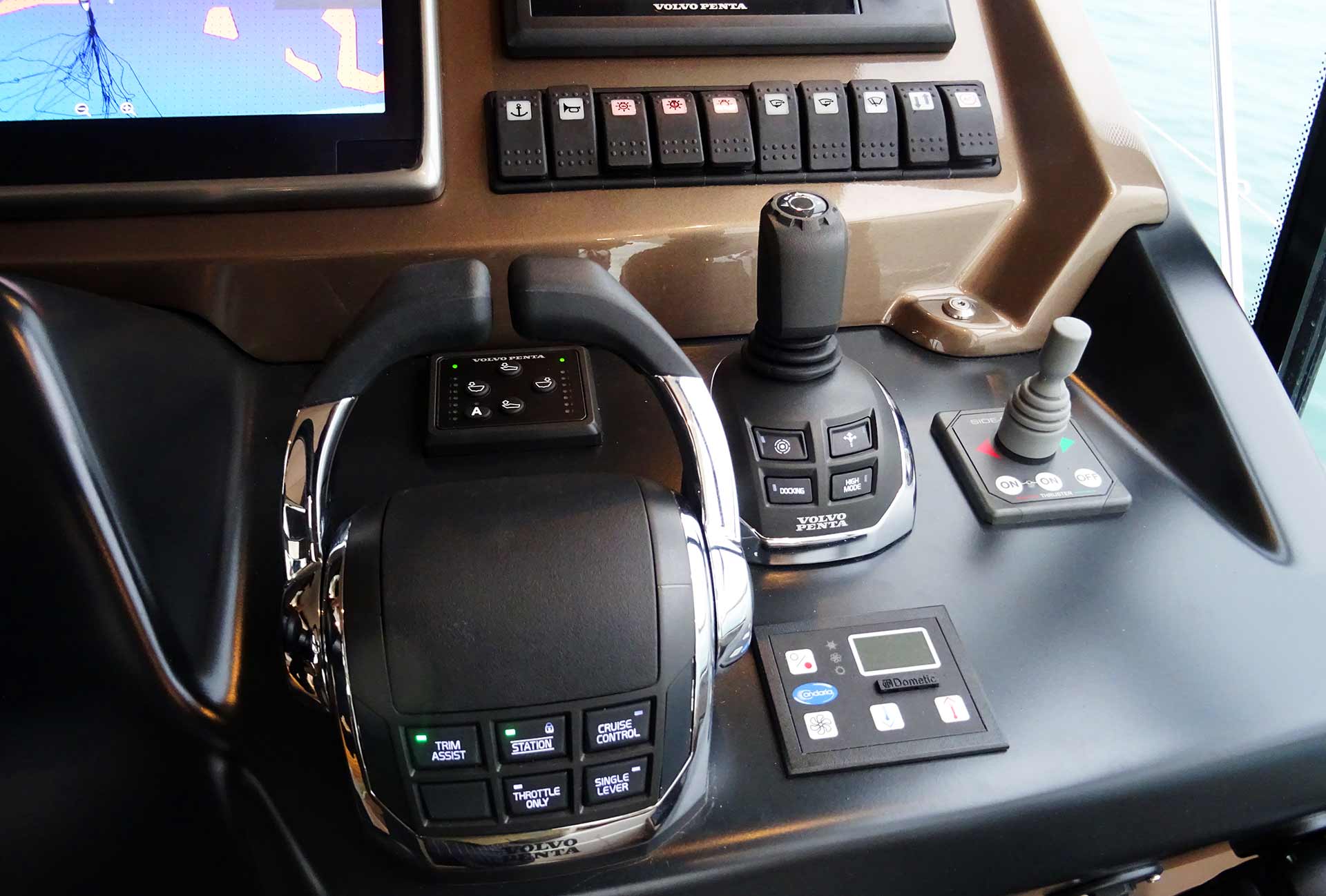
I jumped into the M44, a 44 feet fast motor yacht with four of my mates and we slowly steamed through the channel towards Laguna di Marano. We used the relatively boring time (7 knots speed limit, some 40 minutes to the lagoon) to get used to the controls. I am familiar with sheets and winches, but I don´t have a clue what interceptor flaps do and how to utilize this whole lot of technical stuff. Lucky we were, our skipper was as professional as the impression of the whole test centre itself. Upon leaving the channel, I pushed the levers on the table and the two +300 hp Volvo-Penta monsters came to awake.
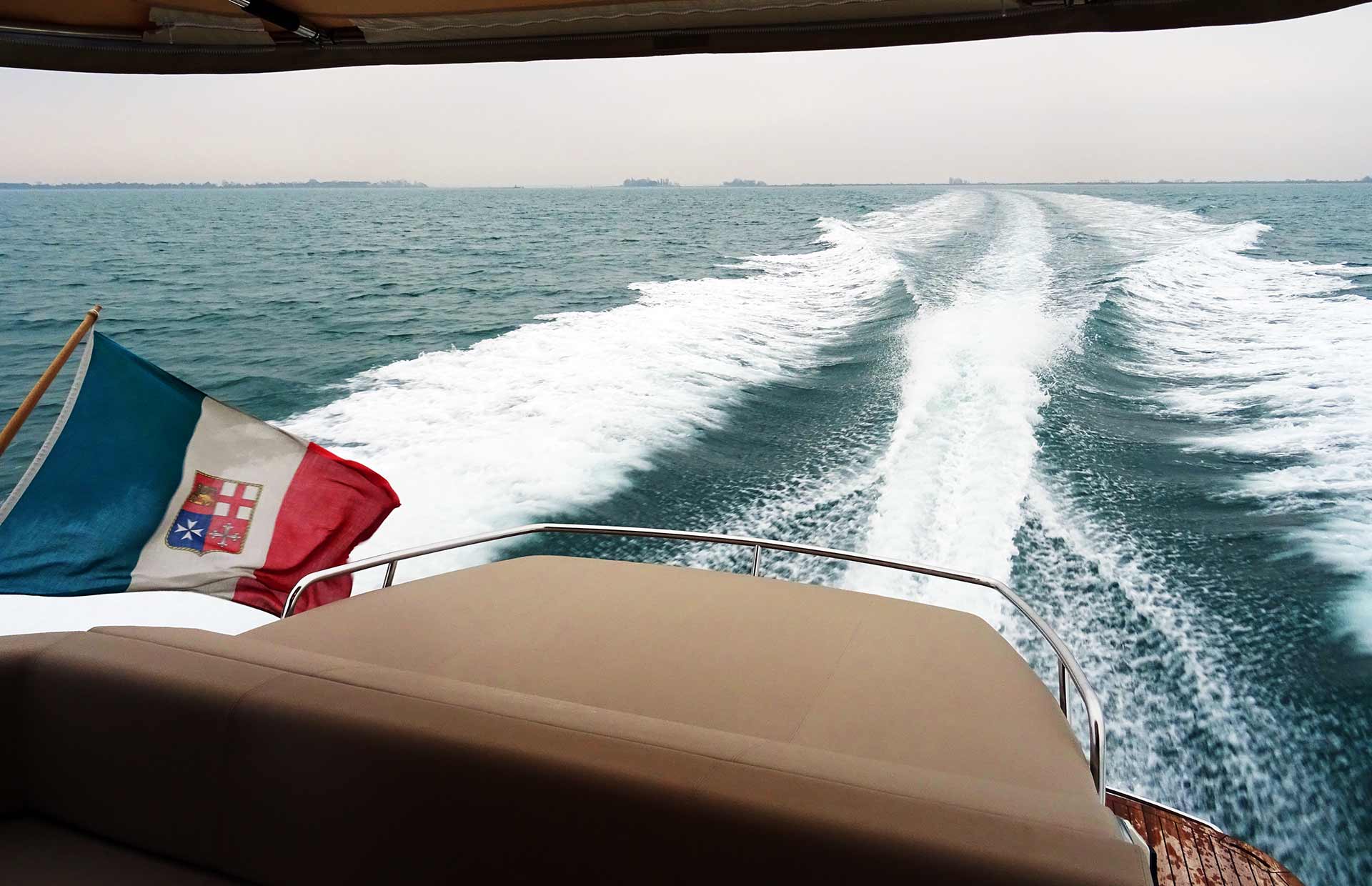
I know, I know: Some 140 liters per hour is threefold the amount of Diesel my own boat will consume in a whole sailing season, but anyway, steering that boat was a thrilling sensation. The Cranchi jumps to 30 knots within 20 seconds, which is quite amazing. The amount of power, the sound, the constant banging over the waves is quite impressive I must admit.
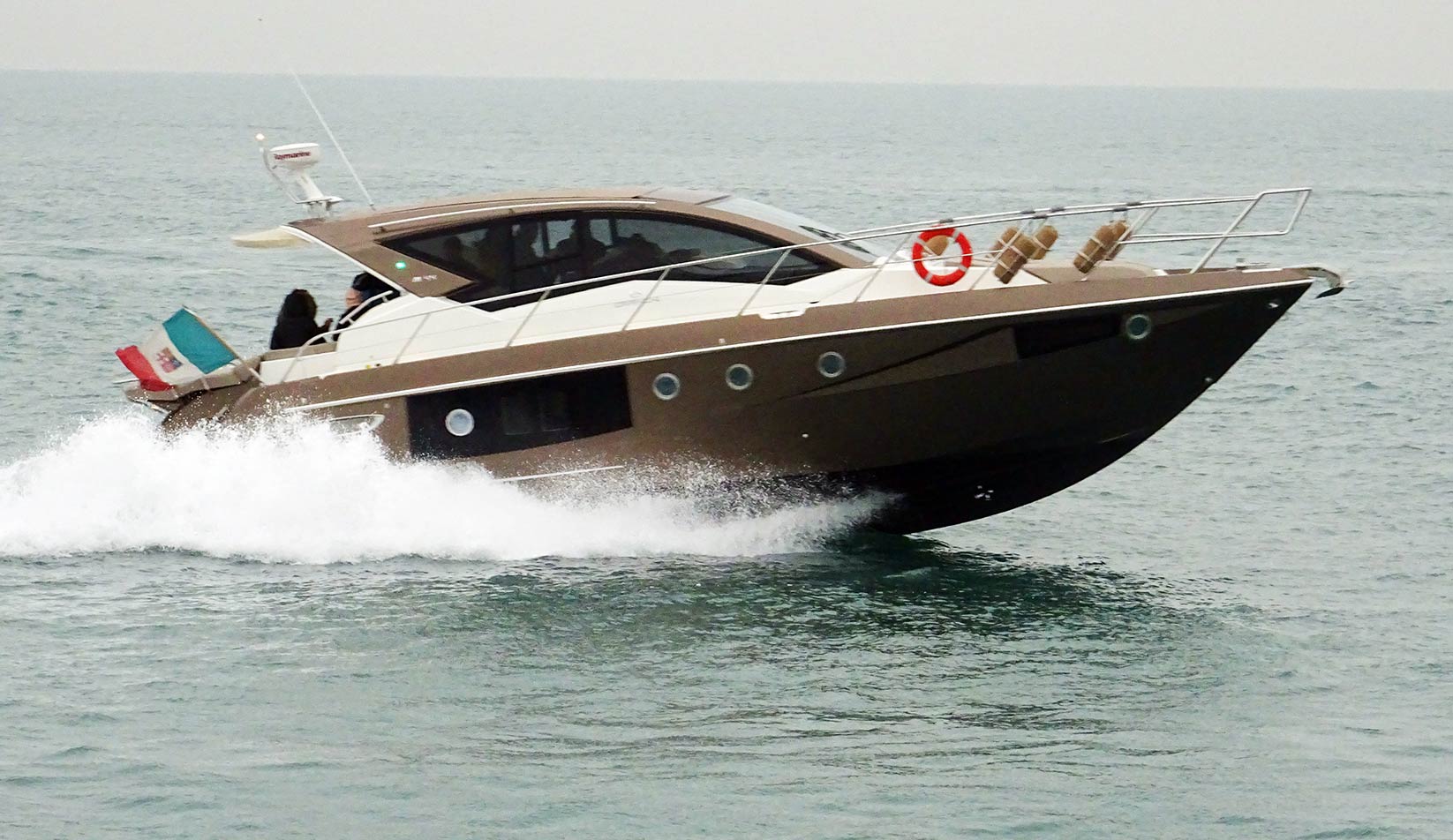
So we had quite some fun shooting around our mates who were busy testing a 43 feet Trawler – a more luxurious, spacious long-haul yacht by Cranchi. Jumping over the waves, accelerating and stopping, going into tight corners and trying to make some aweinspiring wakes time flew by.
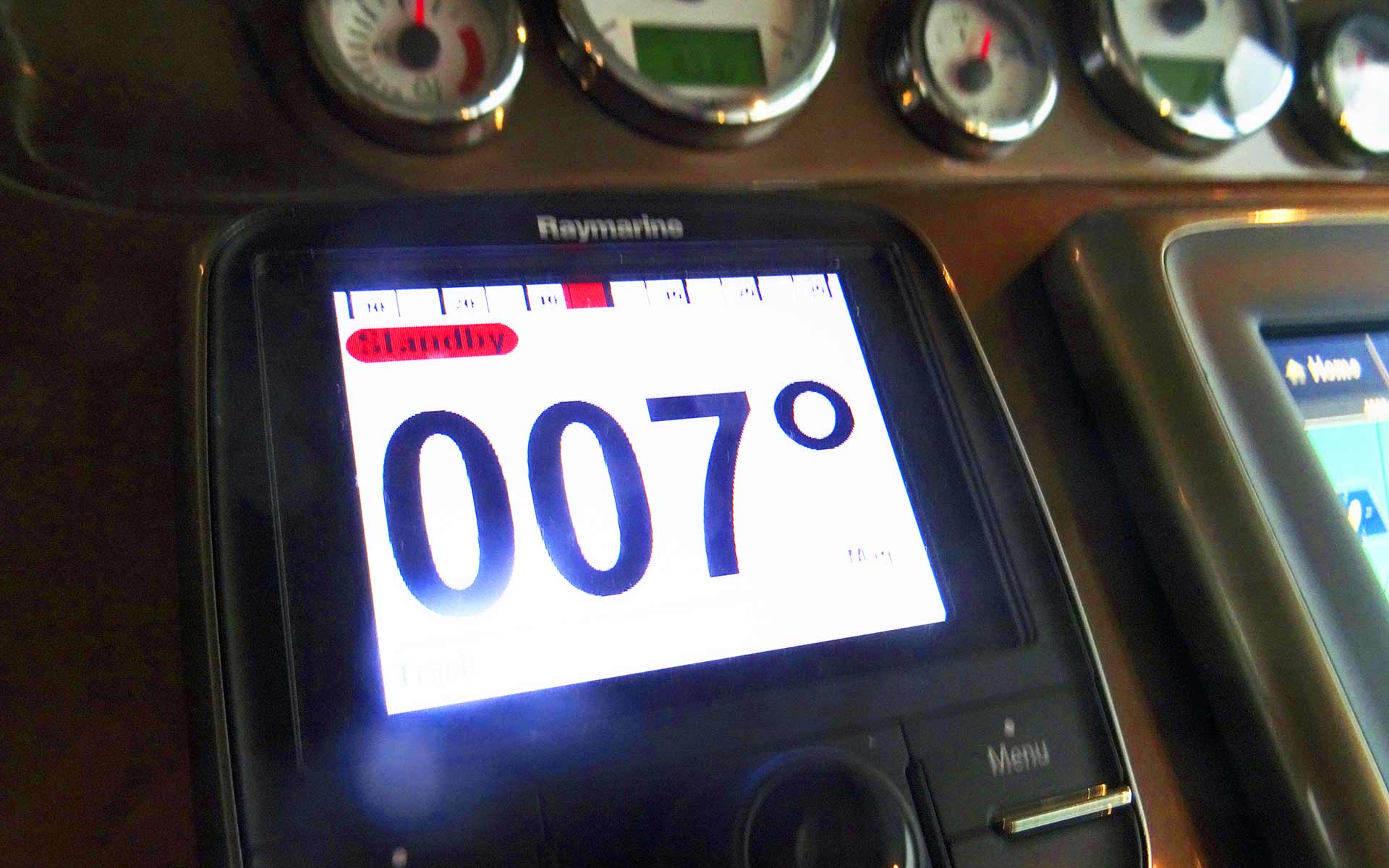
And it´s no wonder that the James Bond theme was jagging around in my head after we were finally back at the test centre tied up at safely again. My legs were shaking, partially because of the chilly temperatures, of this great experience and the realization that the two yachts did burn some half a ton of fuel during the last 3 hours. Anyway, that´s a normal thing with motor yachts. Now we knew what kind of product they were making and had a feeling for what is leaving their production facilities. And then things got really interesting.
Family business: 150 years of Italian boatbuilding legacy
Cranchi is one of the oldest boatbuilders in Europe, maybe worldwide. They started business back in 1870. That is some 150 years of craftsmanship, experience and a whole lot of tradition. What was most impressive for me: The company is still owned and run by the family. Three of the four siblings of the current generation are responsible for research and development, the strategic decisions (as well as model policies) and of course the brand. We didn´t have the chance to visit the boss due to a cold but it was a pleasure to see talk to the siblings and to get a feeling for the “vibrations” of the company. There is no faceless hedge fund keen on revenue running this company, it´s the offspring of generations of boatbuilders.
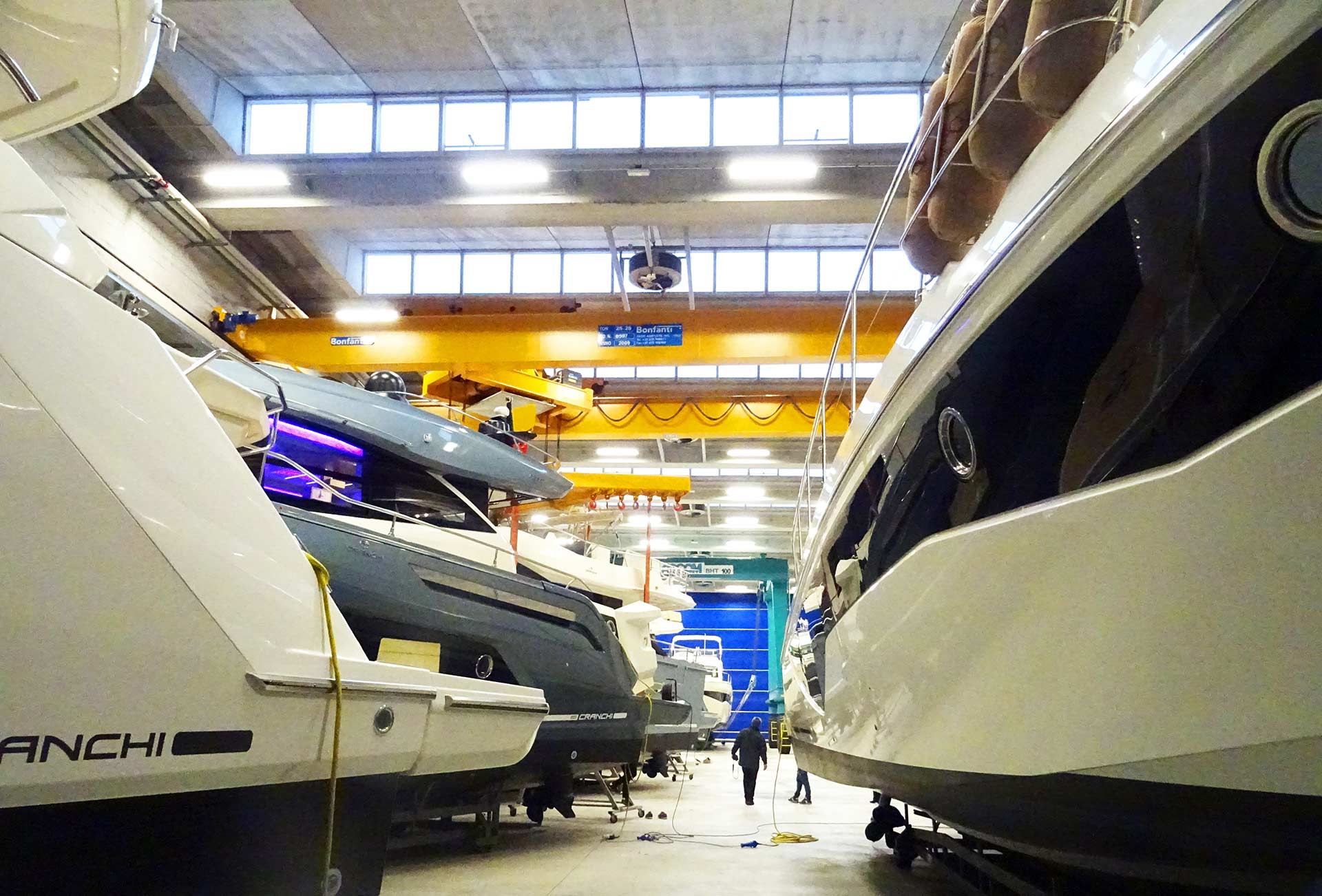
Of course, Cranchi is making quite expensive, high quality boats from 27 to +60 feet. These machines are bigger than the house of my parents, but in every boat there´s the spirit of the family. That is why the company didn´t move from their home base to the sea, which would be a lot more cost-effective and logistically advisable I guess. They are adhered to where their origin is, namely at Lake Como in Northern Italy. As we strolled around in the test centre I noticed a sailing vessel, cautiously brought to a stand in a corner: “That´s a sailboat my grandfather made 1938 with his own hands”, Paola told me full of pride. There you have it: I think, quality always has it´s beginning in an emotional connection to what you are doing.
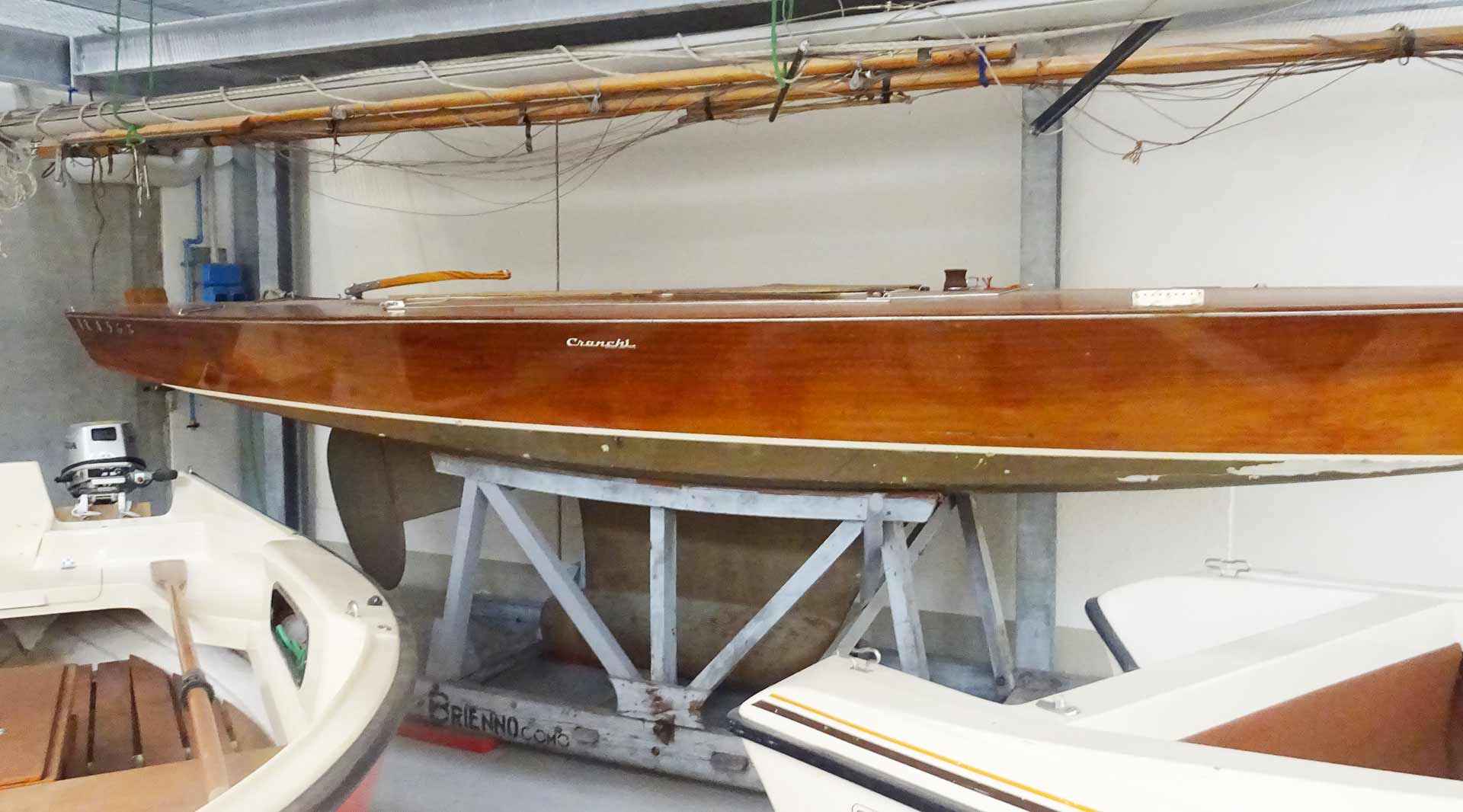
Cranchi nowadays has three production facilities with a staggering tens of thousands of square meters capacity split to two locations. One in Piantedo near the Test Centre and two more at Lake Como. Their brand is flanked by the claim “Technological Supremacy” and as I already had some 3 hours experience with their fine products I was keen on seeing the Cranchi yards for which we were heading the next day.
Modern boatbuilding: The Cranchi yards
Motor yachts are built in pretty much the same way as sailing yachts. The principal material of choice is glass reinforced fiber (GRP) and epoxy resin, put together in huge molds. Paola was a more than pleasant guide through these very halls as in every word she spoke, in every explanation she gave we could sense her passion and pride for what they were doing here. Her knowledge of details and the level of technological understanding was most impressive.
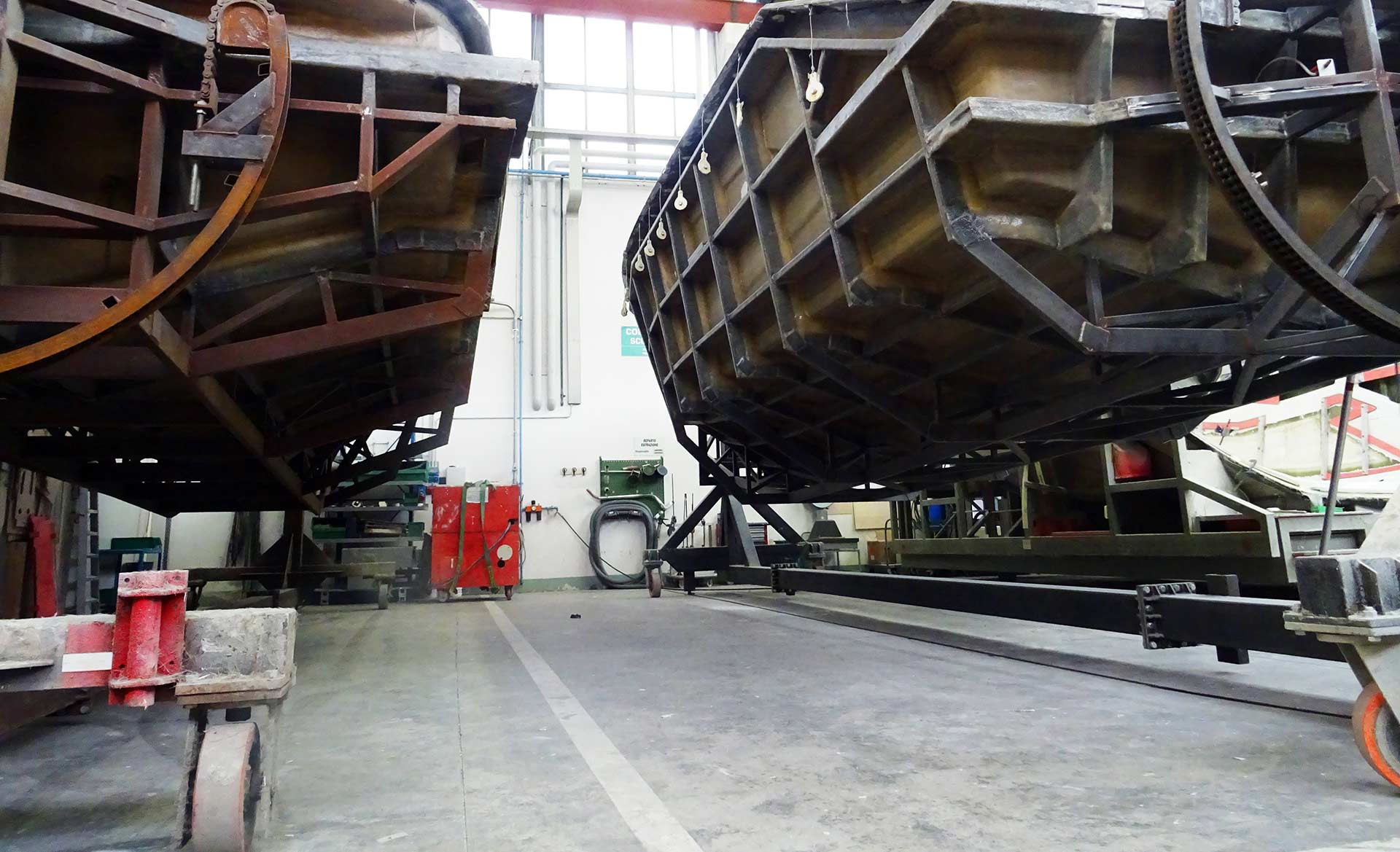
As you may know, to achieve a rigid, perfect hull, the molds have to be perfect. Because every glitch will sum up in each and every hull made by that mold. So naturally, keeping the molds clean and in a perfect condition is one of the prime tasks in the yard. Paola explained, that Cranchi is quite traditional at the bottom of a boat, as building techniques are proven to deliver the most rigid and safe hulls. Yet, the more you go to the top, the more Cranchi is utilizing latest technologies, such as carbon fiber construction.
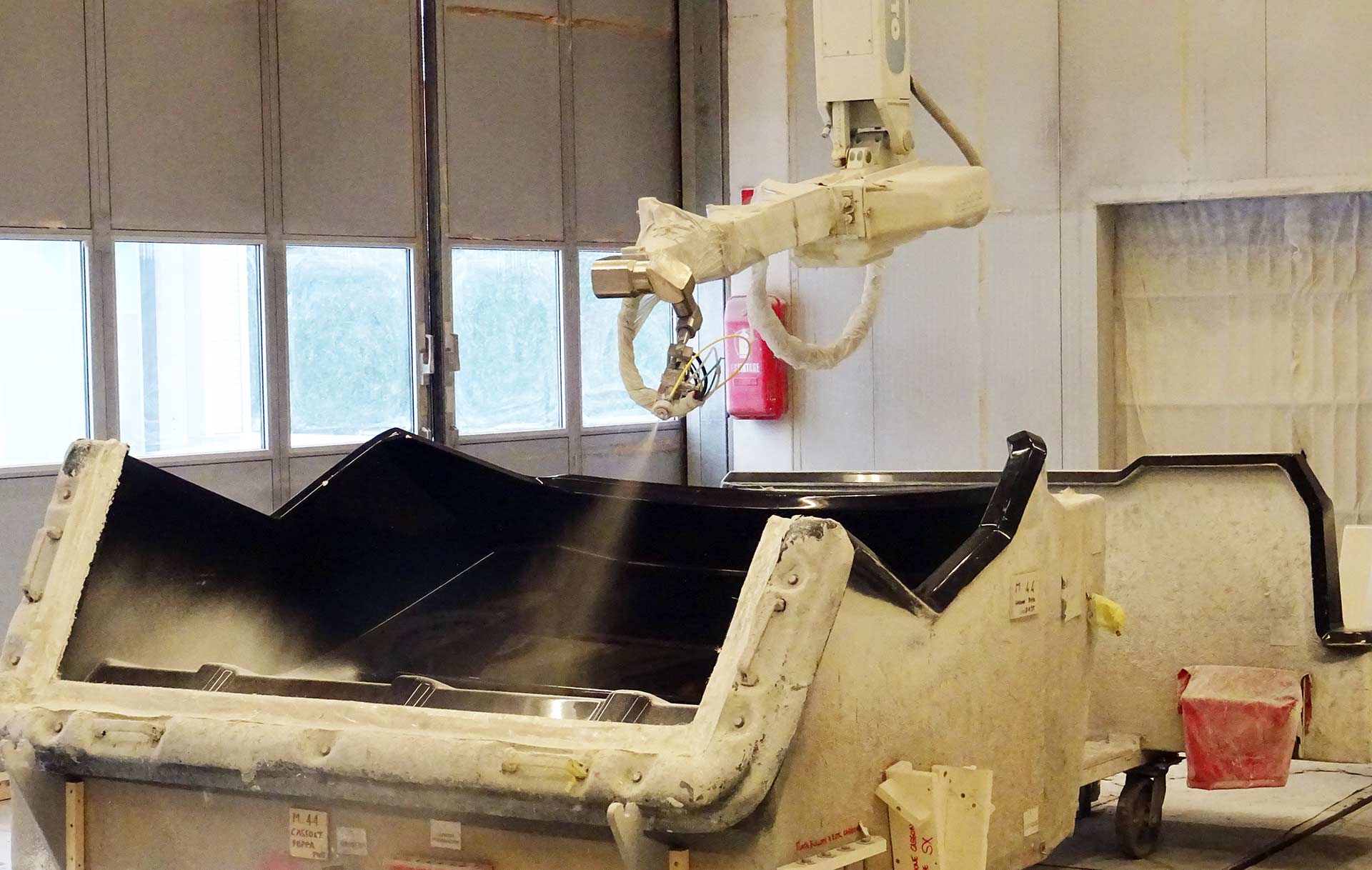
“Technological Supremacy”, there you have it: Gelcoat, the very first layer of the later hull, is made by a fully automatic robot here at Cranchi: “My father was travelling whole of Europe and visited the most modern production facilities”, Paola tells us: “At a plant of BMW he was most impressed by the degree of automation and the high standards of quality delivered by advanced robotic technologies. So we employed the same firms as BMW and set up robotic stations in the building process. This ensures constant quality and a perfect outcome – which is wanted above all when we are talking of Gelcoat surfaces.”
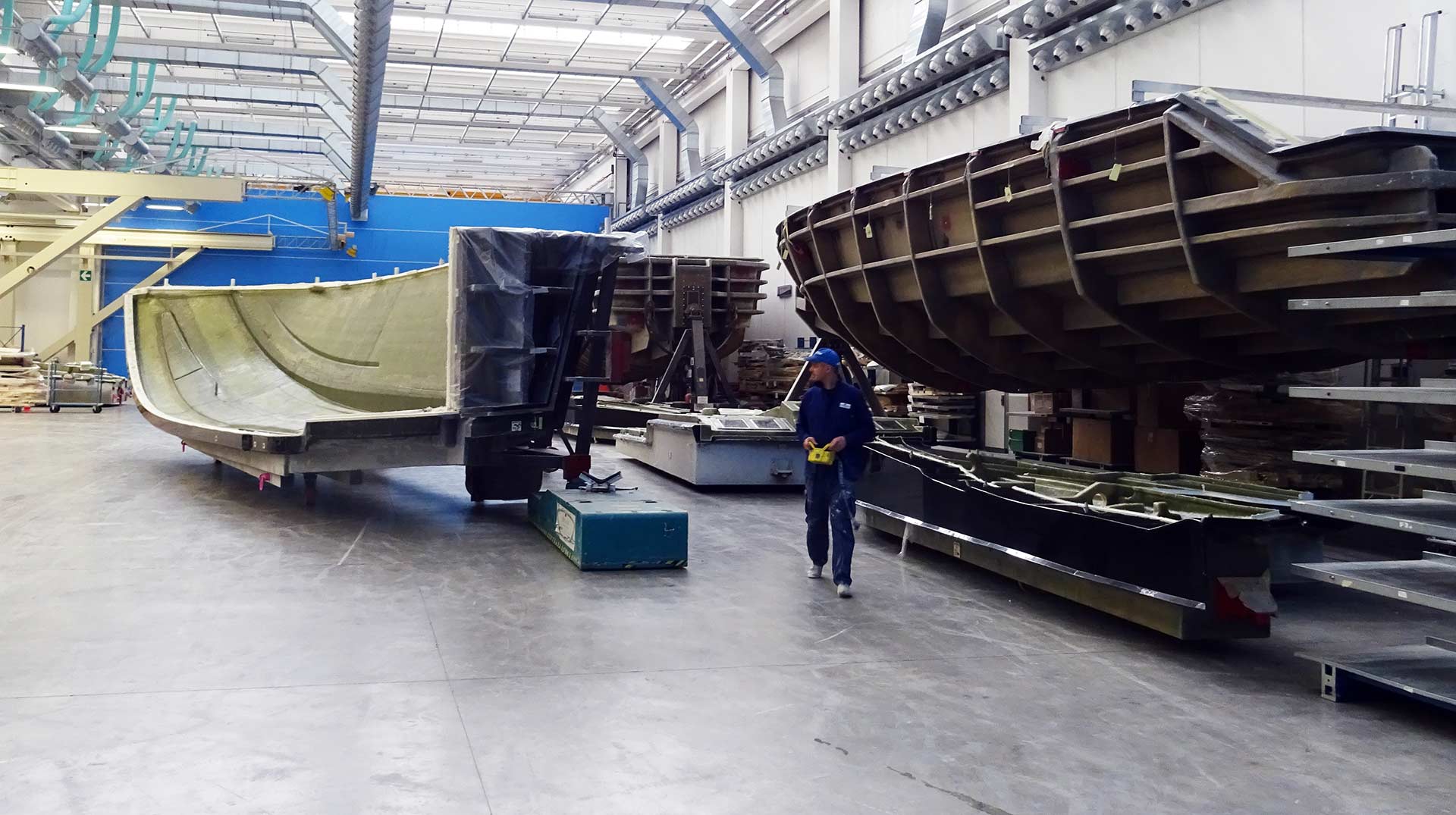
But the Gelcoat robot is not the only one working here. Touring the yard, I noticed quite a lot of them. I particularly liked the mold-pulling flat robots which would stop upon noticing a human crossing its way. The accompanying employer walking with this robot appeared like a man walking his dog.
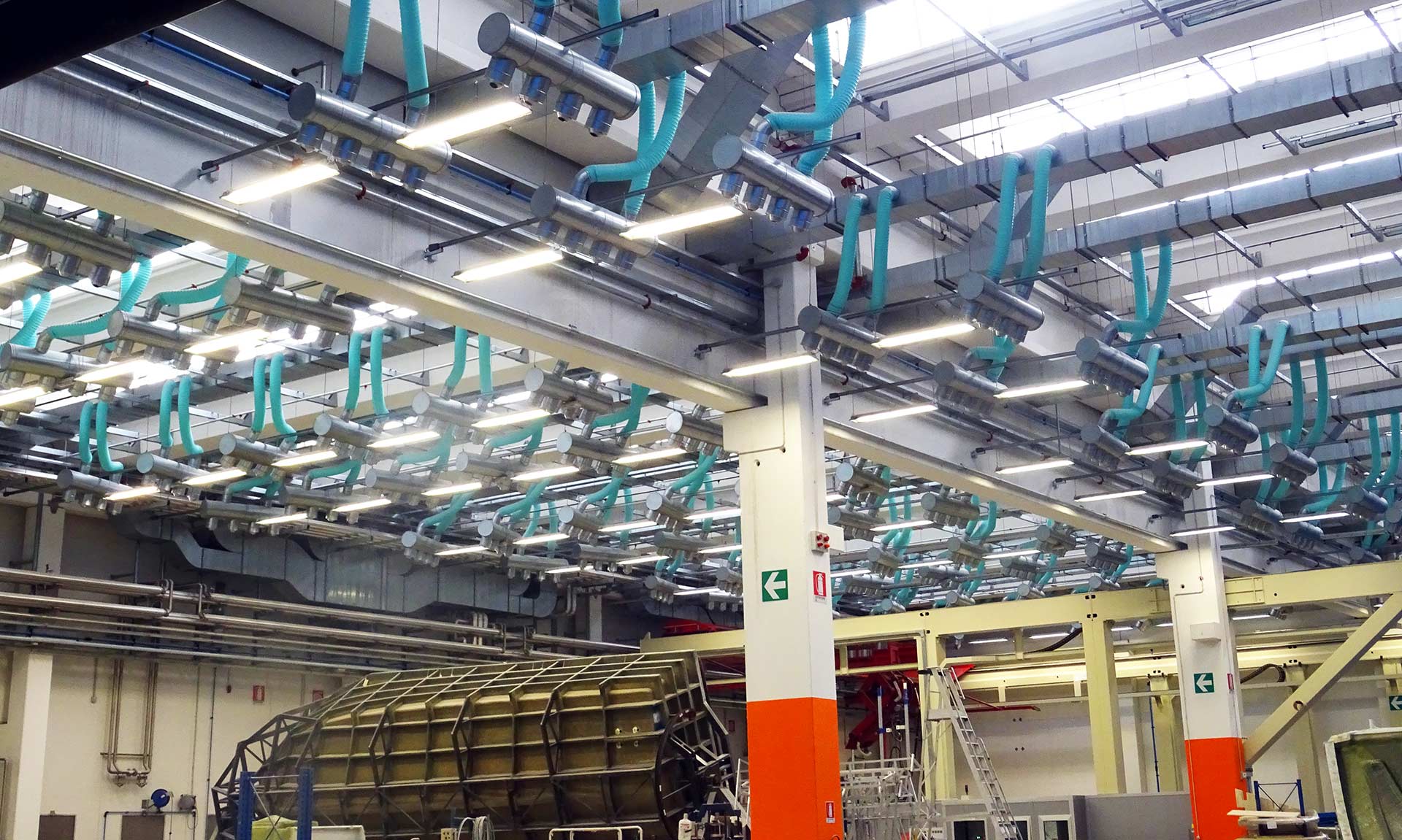
“We want perfect hulls. No scratch, no dust and nothing whatsoever alien to a hull should be allowed to enter the halls.”, Paola explains. “Also, naturally we have to provide clean air for our workforce here, filter out the fumes of all the chemical stuff involved in making a hull. By thinking about that problem, we found we´d had no other choice but to construct an air cleaning system for the whole production facility.” And there you go: Looking up to the roof we noticed an impressive installation of air inhaling, transporting, filtering and re-exhaling equipment. “We have 24/7 constant air cleaning, temperature and moisture: Just perfect for the hulls to harden and our employers to work.” I´ve never seen such an expenditure before!
A human/robot workforce in perfect harmony
But let´s take a closer look at these robots. Because there´s more to it. I didn´t had the impression that Cranchi is a fully automated yard. I can´t be. Boatbuilding – as well as sailing yachts and motor boats – is an art and will be like this forever. You cannot skip the human. At Cranchi they found a very interesting interpretation of integration of humans and robots. They are working together.
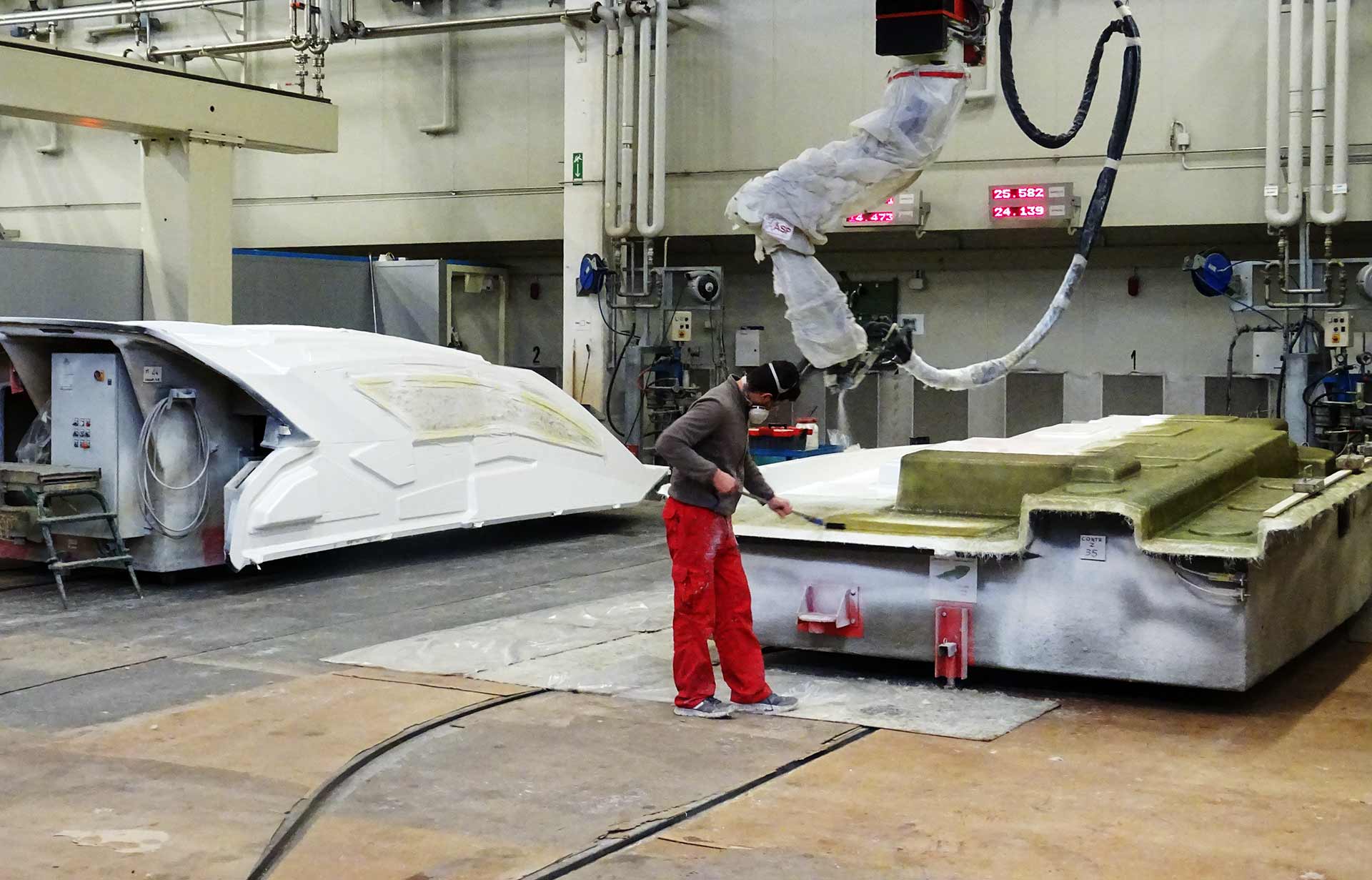
At another station there was a 4-axle-robot spraying epoxy/glass-fibers into a mold, forming a part of a boat´s superstructure. At the very same time a human worker did laminate mattings thus working as a team with the robot. Like a well-rehearsed pair both machine and human being were working together. “This is unique in Italy´s boatbuilding industry as far as I know”, said Paola, “Partly because these robots are extremely expensive of course, but also because of Italian law.”
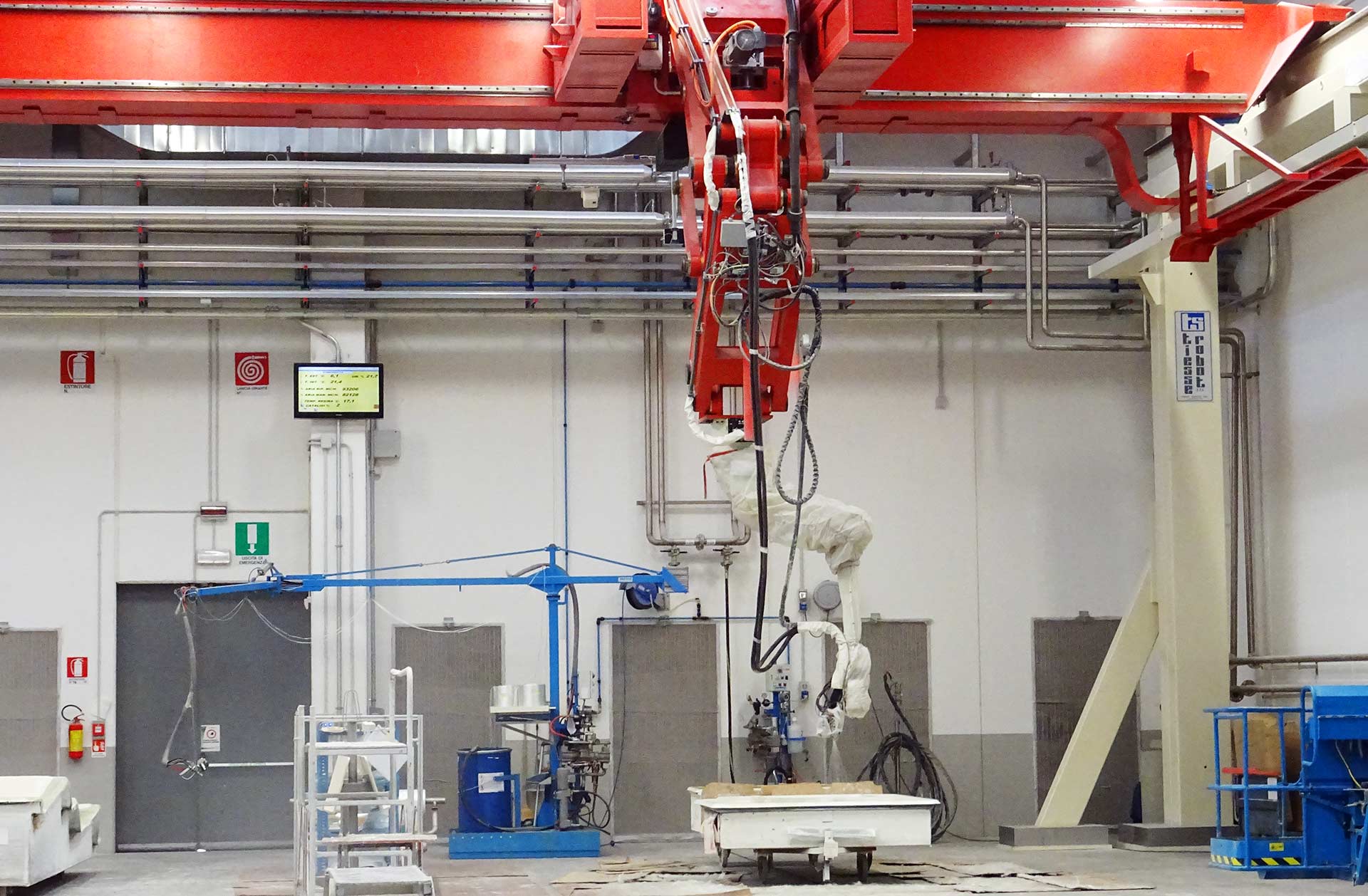
“When it comes to legal rules in Italy, there are strict safety guidelines that make automated production very costly”, said Paola. “All workers within the perimeter have to wear special badges. A safety system is constantly monitoring the distance of them two and if this distance is too short, it will stop the whole system.” Also, the whole area is encircled by a laser monitoring system: If a person without a badge is entering the perimeter, it will be stopped as well. Isn´t that fascinating?
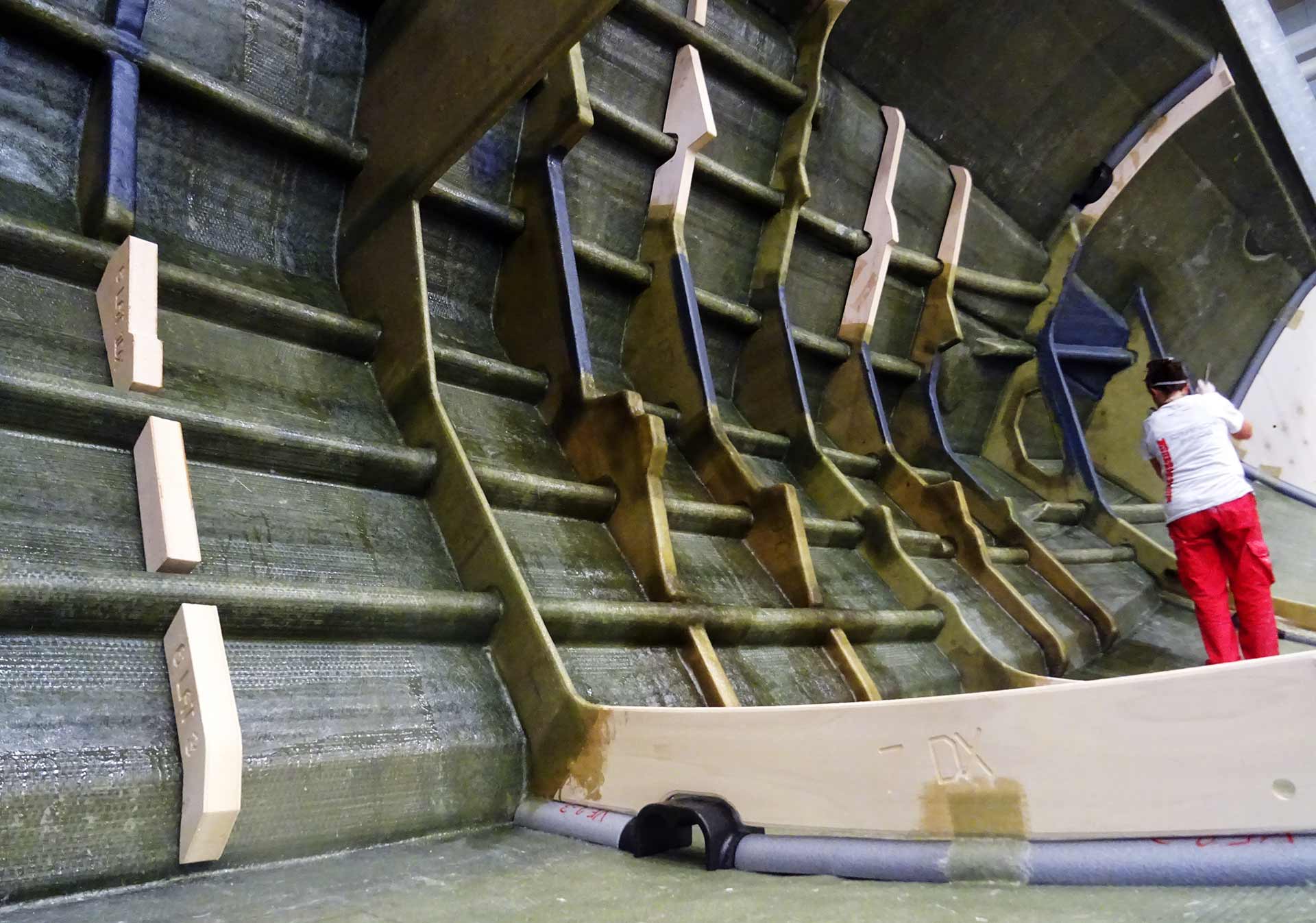
„But there are things which can never ever be replaced by a machine, no matter how advanced it will be.” We could observe skilled people adding stringers and ribs to the bare ship´s hulls, laminating by hand thus achieving best quality: I noticed that virtually every elder worker did have a younger team mate. The new generations of boatbuilders are constantly learning from the skilled and experienced seniors that way. Also, from the human side, that was a touching picture. As well as all the green plants in huge buckets every now and then: Do you know a production facility with green trees?
Quality? Skip suppliers!
I think I don´t have to tell you, dear reader, that product quality is a big issue especially in boat building. Economic pressure, a consolidating market, increasing customer demands and of course intense competition and thus the pressure of low prices are inevitably lowering the quality of the products. At Cranchi they don´t seek their luck by outsourcing all kinds of stuff, they rather do the exact opposite thing: They are producing virtually everything by themselves.
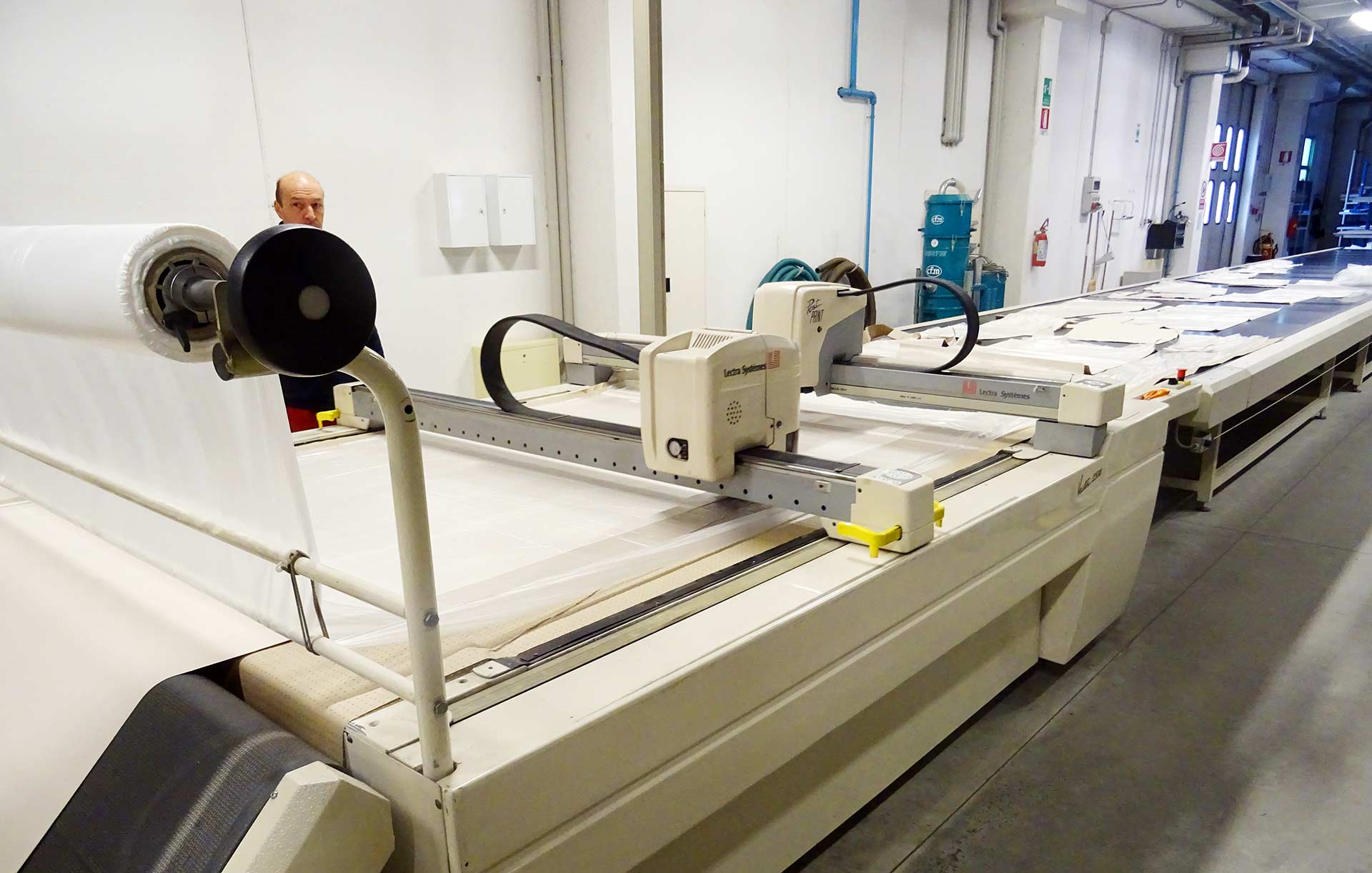
We visit a hall with two huge machines: There they do not just cut mattings to exact measurements by laser guided machines, this facility is also able to produce multi-layered mattings for all kinds of applications in the process. Impressive, isn´t it?
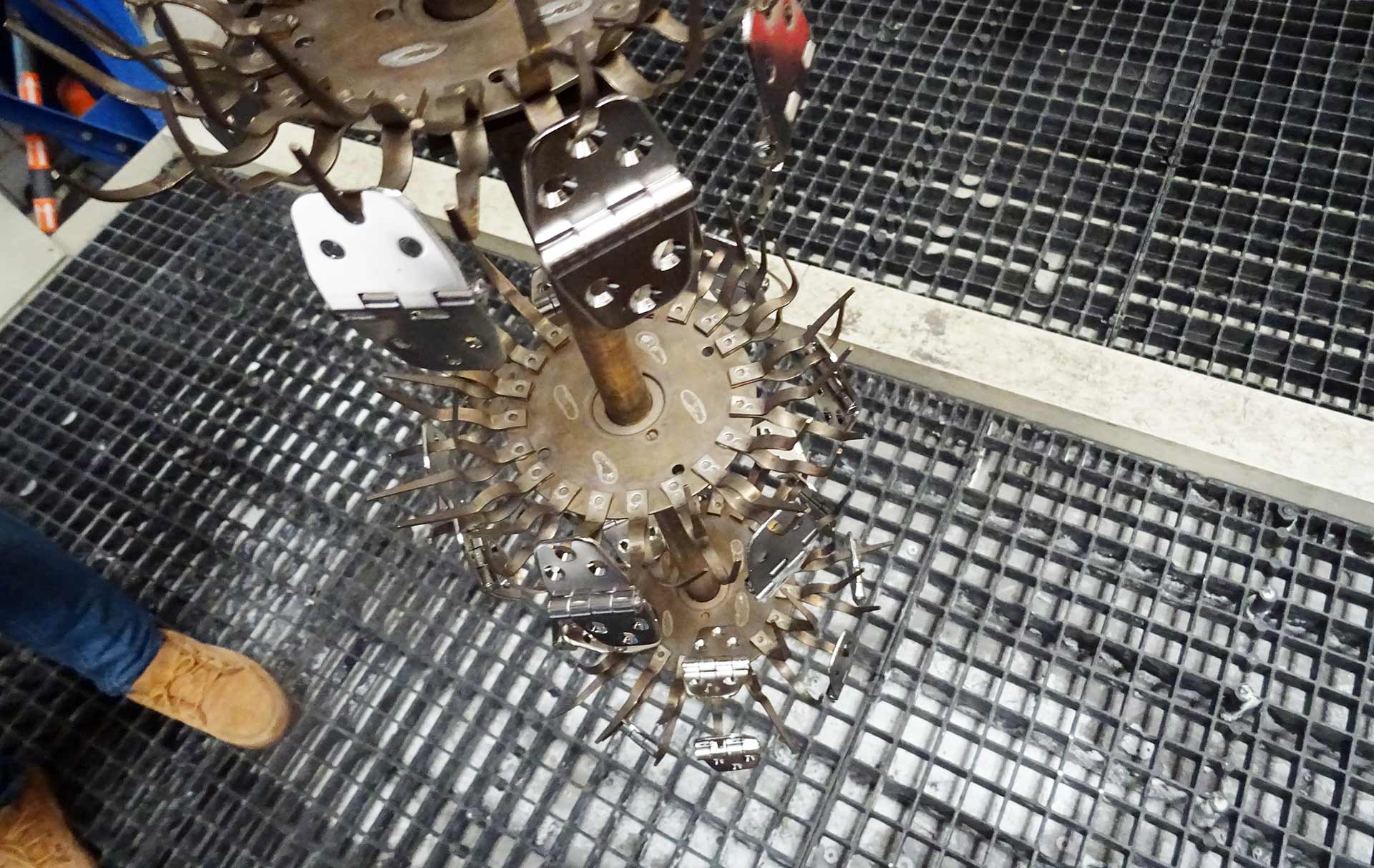
“We are not very happy with externally made stainless-steel parts, especially when it comes to chroming.”, explains Paola, and shows a huge production facility where they do their chroming by themselves: Beginning with all those tiny parts just as screws and hinges to the big stuff like railings.
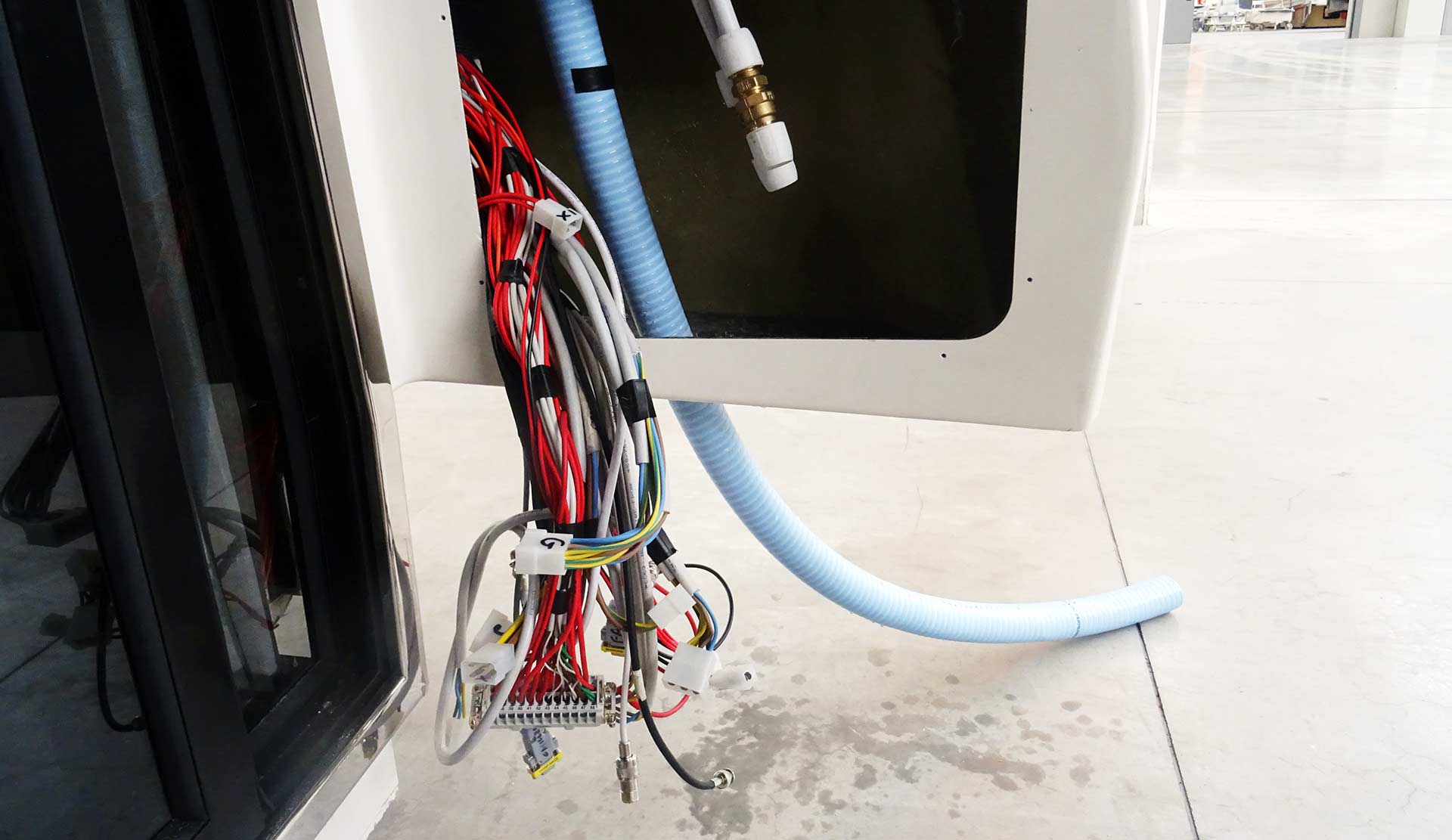
We even get to see a station where they will make their own cables – custom made wiring! I´ve never seen this level of internalizing production in such a deep way. Imagine the investment in all those machines compared to their relatively low rate of capacity utilization: These machines will be turned on just from time to time when their products are needed in the production. We´ve had our mouths open …
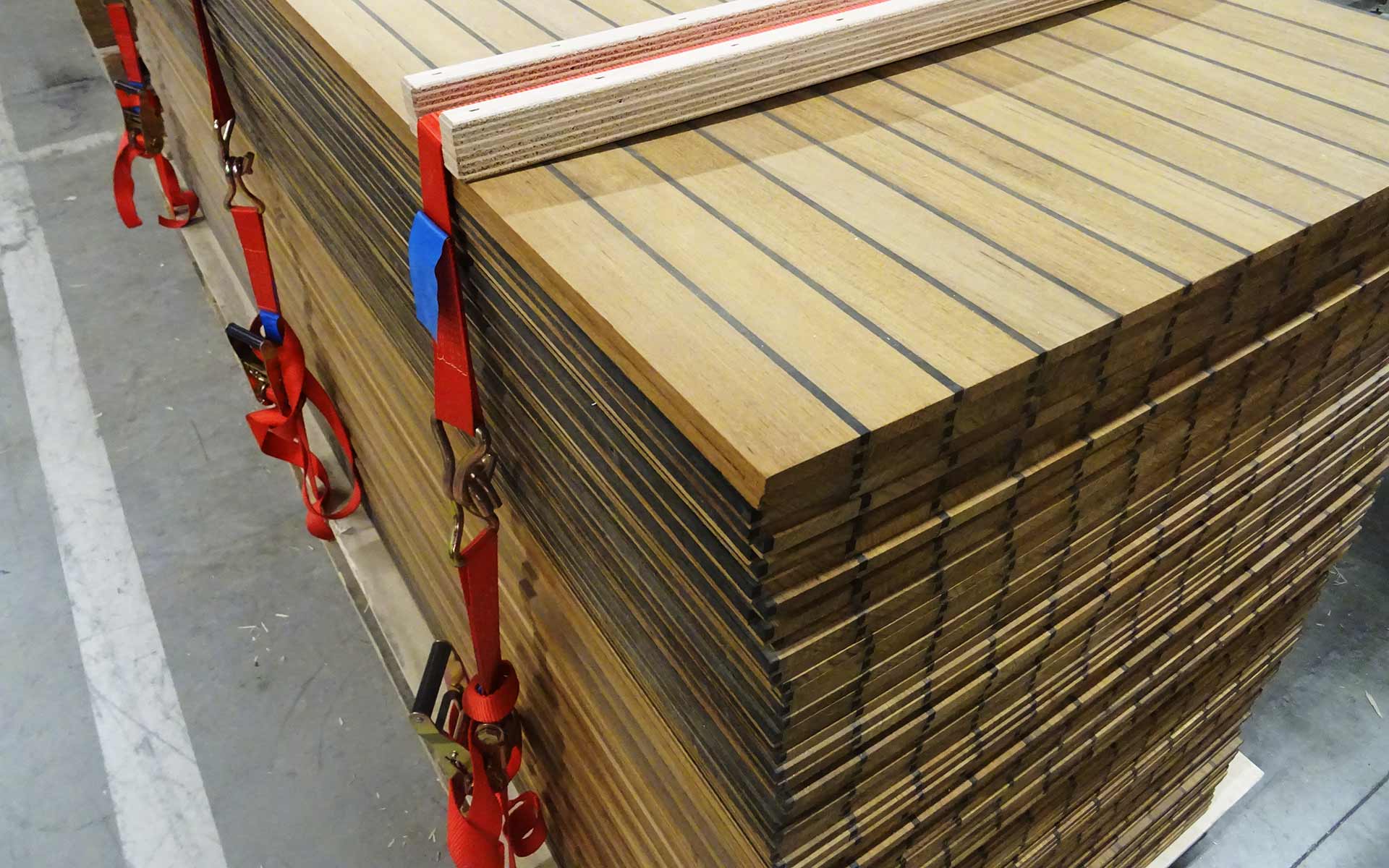
I know perfectly well how attractive a professionally made wooden interior can be. And how expensive. Again, as we come to walk through the joinery I was amazed to see massive Teak decking with some 5 or 6 Millimeters of thick, massive Teak. What a paradise! They are doing all the decking work – of course – here at the production plant by their own skilled workers.
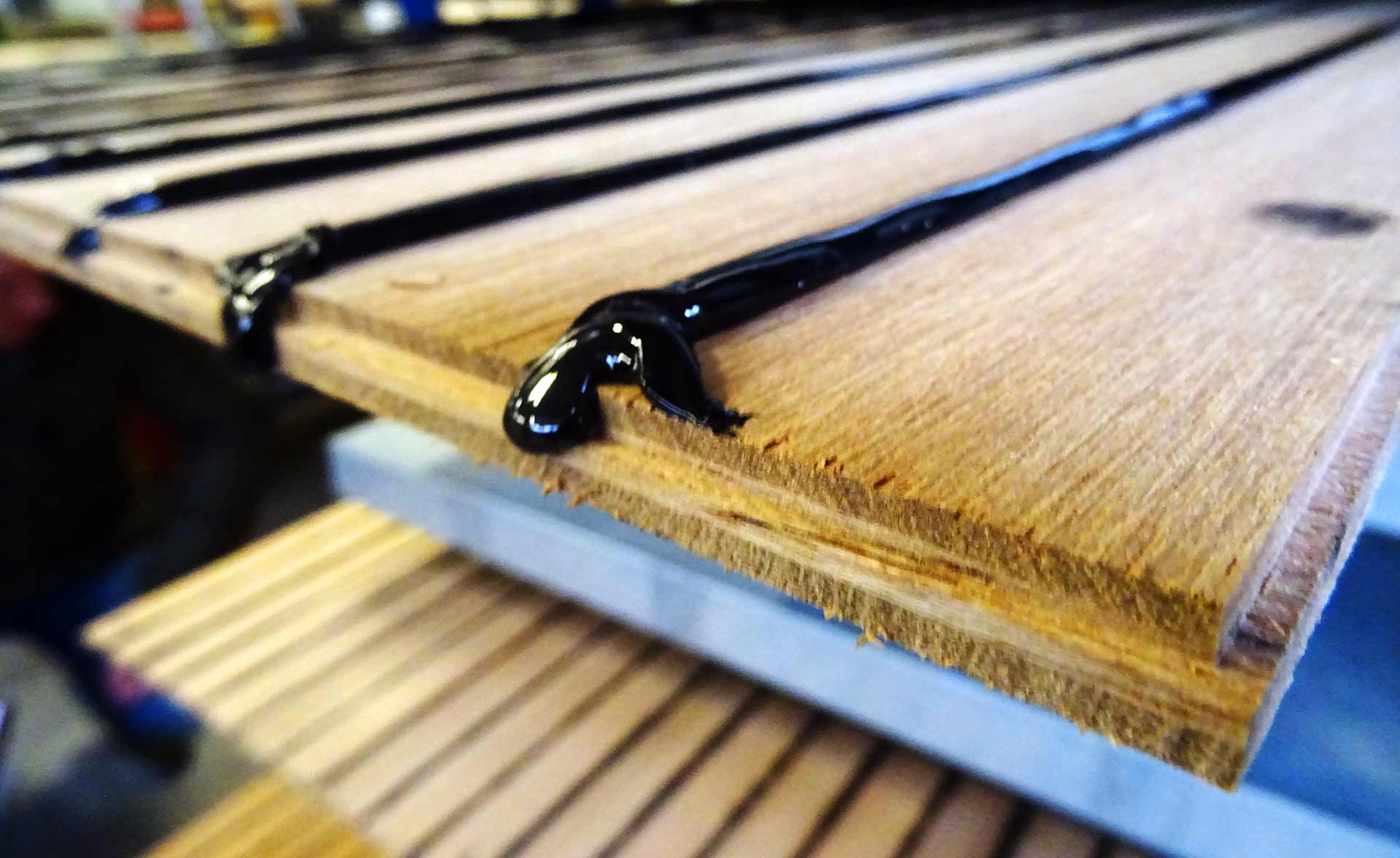
Even when it comes to veneers, there´s a high standard at Cranchi: The inlay won´t be planed as it is the case with most inlays for veneers – they use strong and also very thick (and expensive) sawn inlay of some 3 to 4 Millimeters in material strength. You could easily sand off bruises from those – can you do this with your own yacht´s veneers? I did sand off the precious inlay a couple of times by myself and would have loved to have such thick furniture in my own boat.
The art of boatbuilding: Perfect logistics
I use to be a clean craftsman when it comes to refitting by own boat. No, I really am: Every time I finish a working day I will put all the leftover stuff, tissue, used brushes and waste into the bin, have the boat swept with a broom and cleaned with a vacuum. I will also put the tools to their boxes and to places – all in a neat order and good fashion. Still, my boat looks terrible. And still, I am missing stuff and wasting time (and nerves) by searching for all kinds of things.
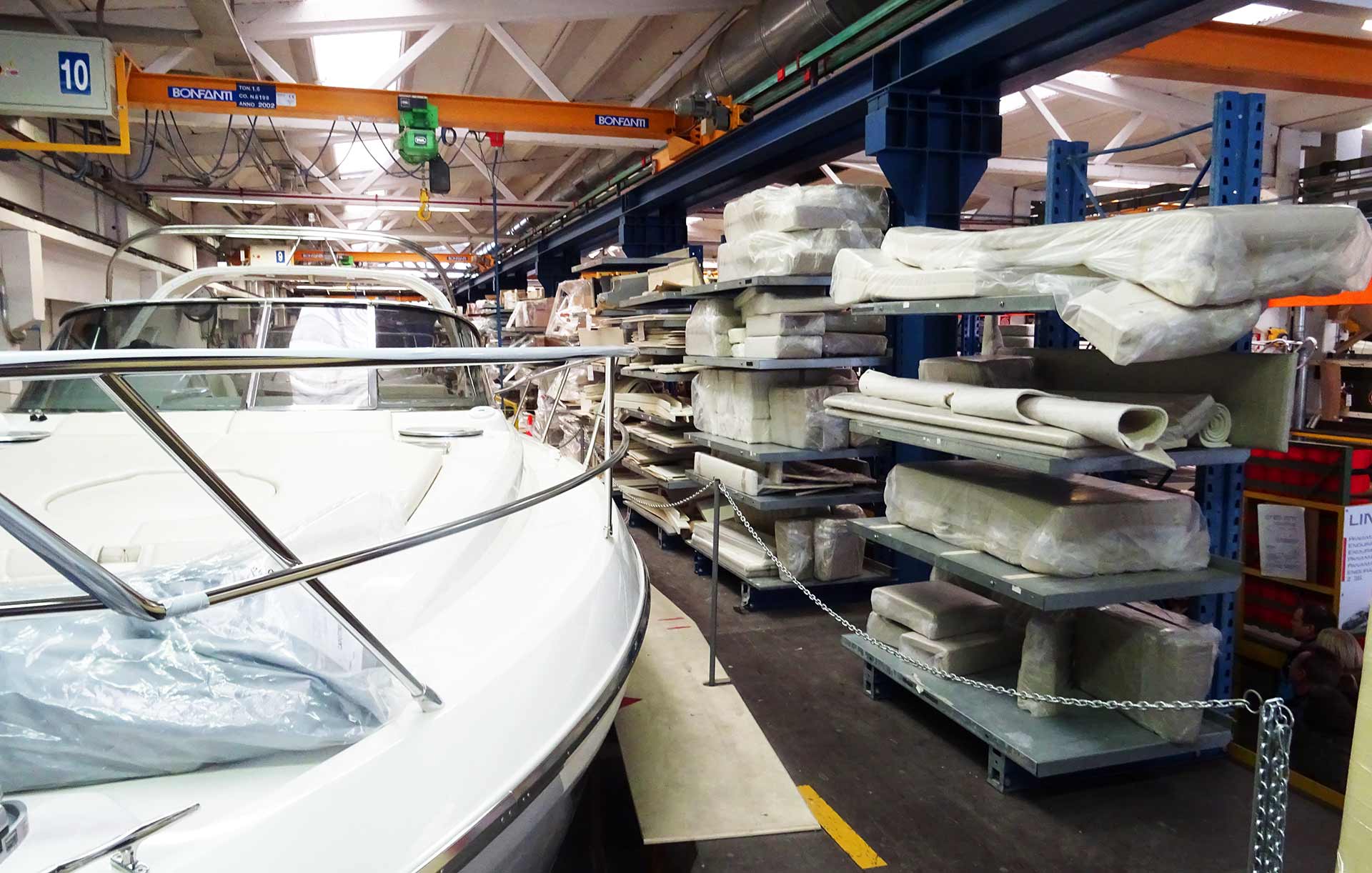
Imagining the amount of both logistical efforts and working discipline on a boatyard where not one but dozens of boats are actually built is a sheer nightmare. Maybe that’s why most yards appear in a similar way like my own boat: Chaos, a mishmash of stockpiles of stuff, corners full of leftover material and it´s increasingly harder to distinct between trash and useful. Not so with Cranchi. I´ve seen all of their 3 huge plants and I never saw a single, tiny bit of waste. Never. Not a bit.
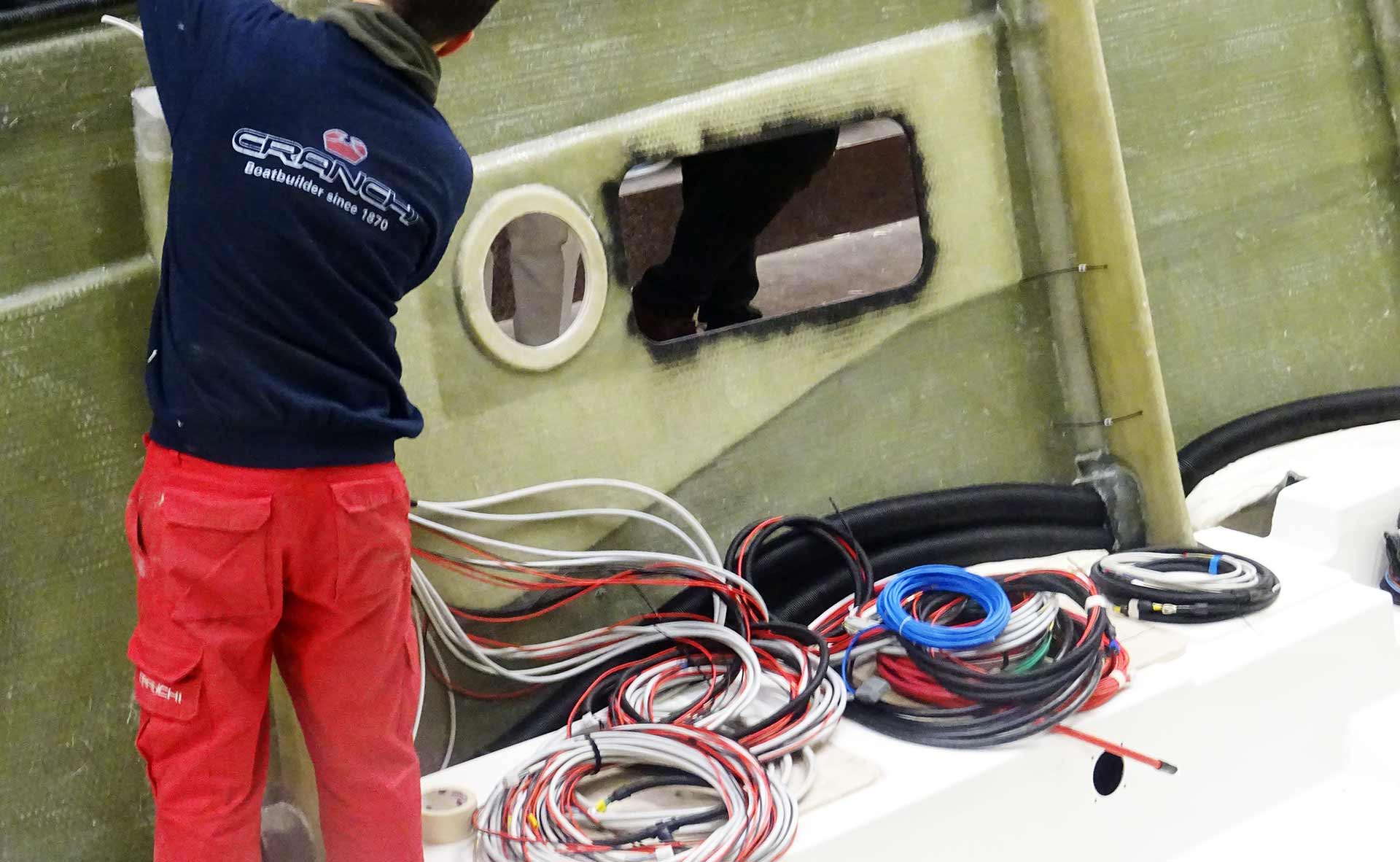
Instead, the assembly lines appeared clean, tidy and well-organized: “When a boat enters the assembly line, everything – I mean everything – needed to complete the very steps of making the boat will be brought up to the rig. From the screws to the pre-fab furniture-units”, Paola explains. “In this way, we ensure that our people know where to grab the different parts. No one will run here and there in search for a tool or a certain part.” Oh yes, I know what she was talking about: I would estimate that I am losing at least 10 per cent of all the time working at my boat running around ruining my nerves.
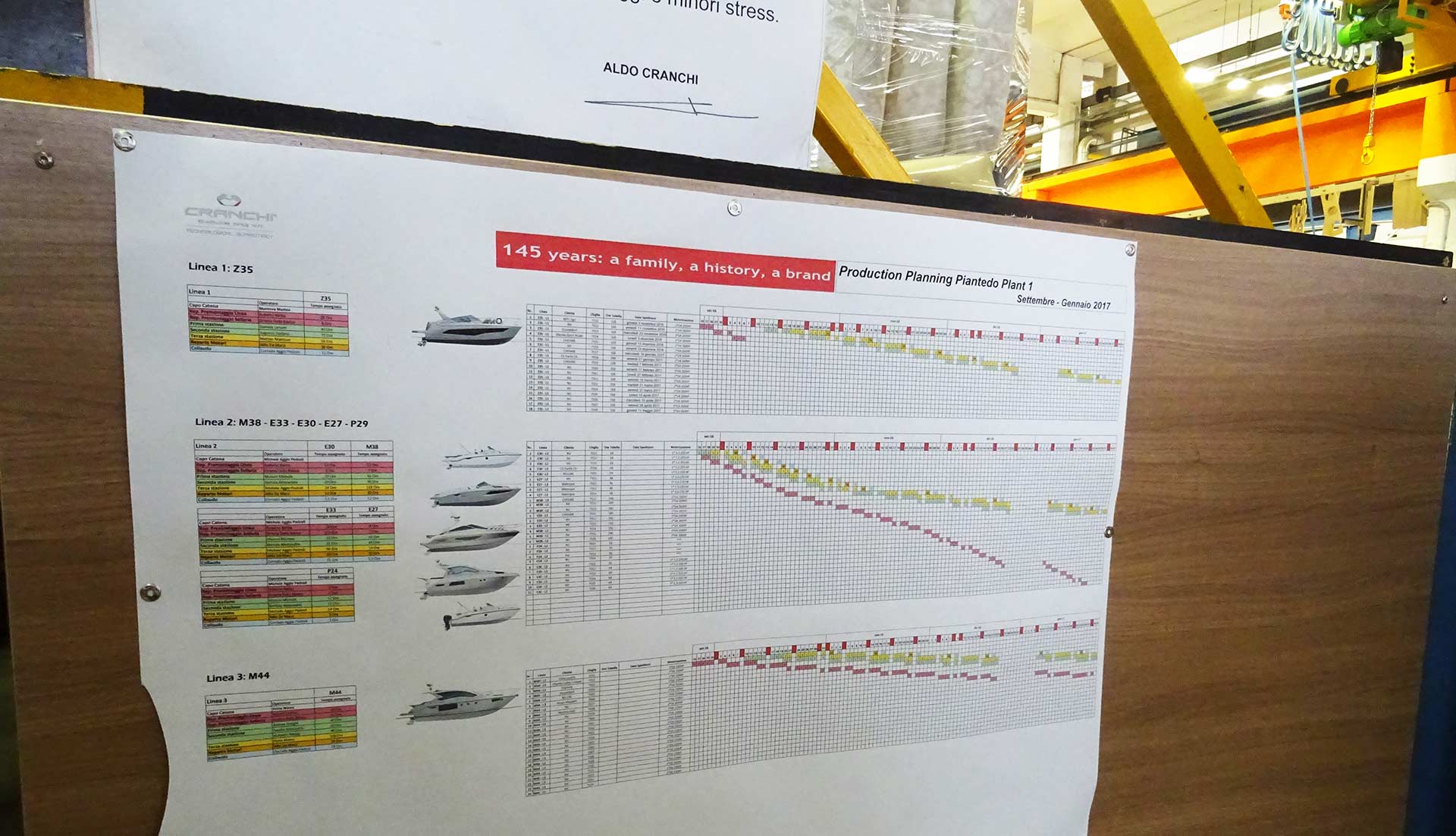
I was amazed by the tight yet detailed production schedules: Everything was noted, precisely specified and closely watched. But there are also ingeniously simple solutions rather than complicated logistics: Cranchi uses paper-sheets where workers will draw a smiley upon finishing a step in the process. This smiley-sheet will stay with the boat until testing, making it possible to trace back every single step of the production as well as making it impossible to forget something.
Preventing after sales-hustle: Thorough testing
Speaking of testing: Reaching the end of the assembly lines, I couldn´t trust my eyes. Huge pools filled with water. Testing pools. “As soon as a unit has reached a certain point in the process, we put it into these basins. So, testing begins not after the boat is finished, but during it´s building process.”, Paola explained. Again, I was touched by the details: Even the pool was branded with their logo.
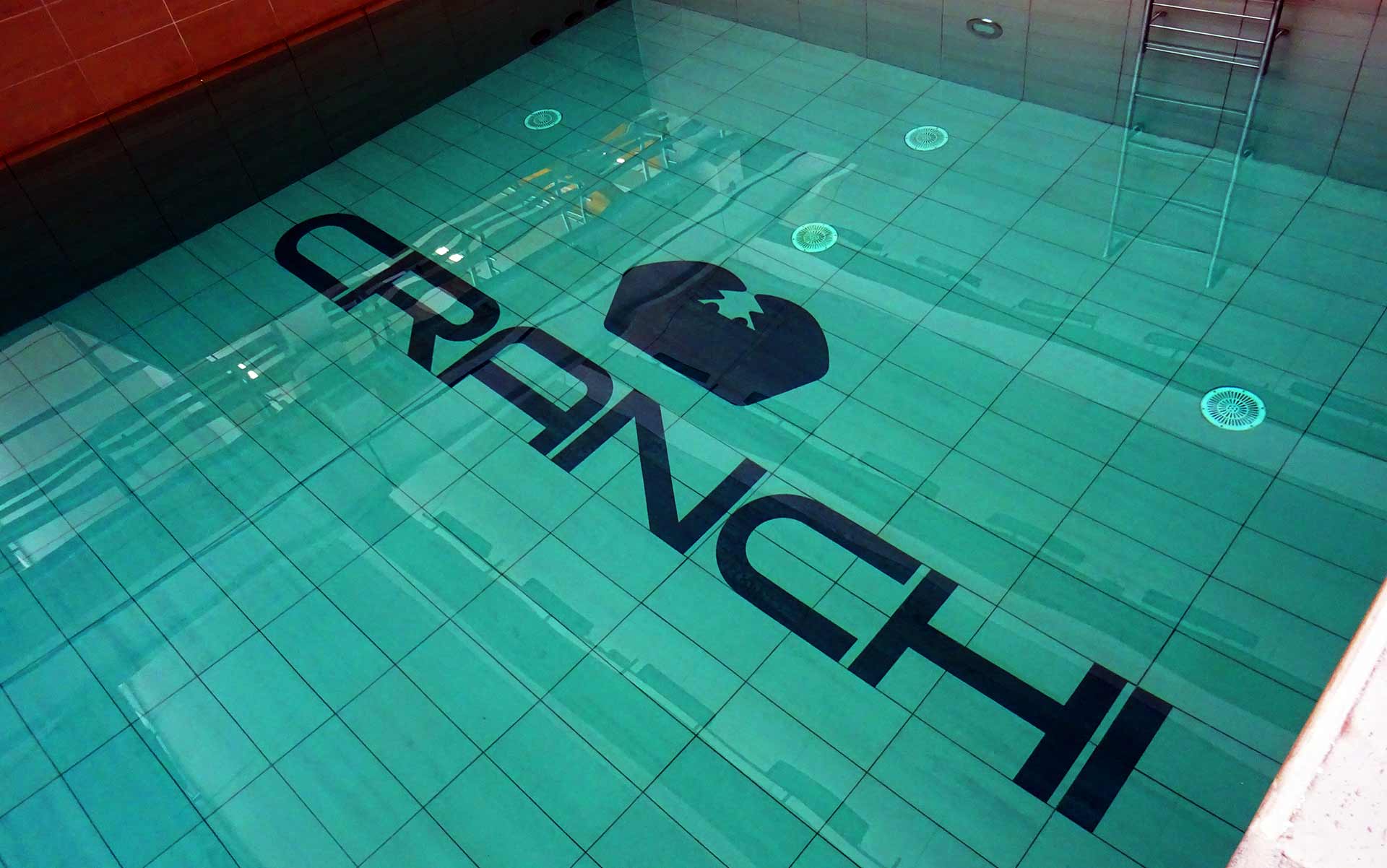
In one of the pools a half-finished yacht was tied up. “We can test-run engines, pumps and a couple of other systems in this state of the process”, she told us: “If anything isn´t quite right, it´s faster and easier to correct it here than afterwards outside, maybe in a foreign marina after delivery.” And of course: No owner is involved and potential glitches are spotted here, by the yard, not by the investor: That´s producing happy clients.
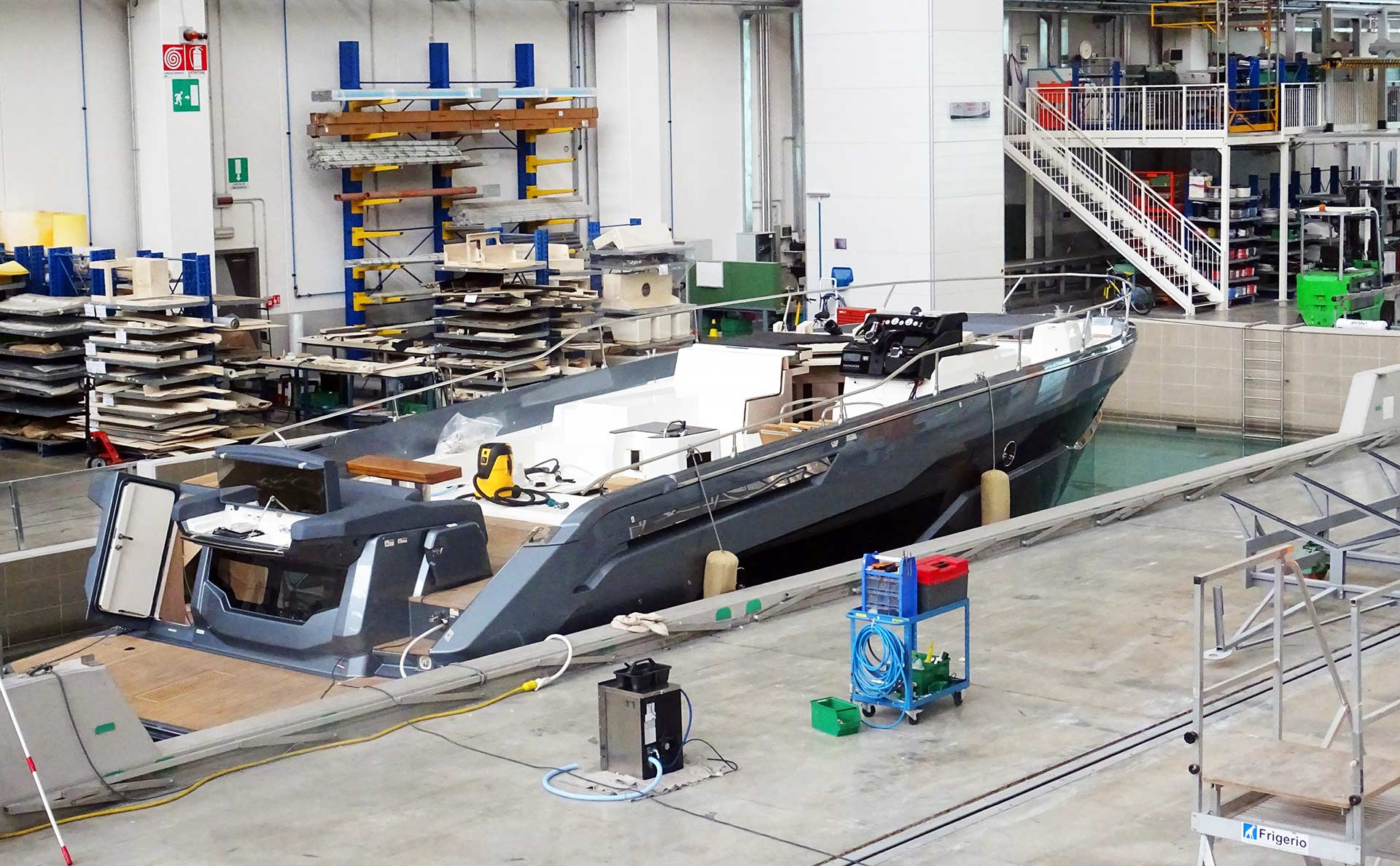
Again I was puzzled by the love to their work. I know, it´s frowned upon to have the ropes turned to a snail amongst sailing skippers, but the motorboat people love it. And yet, even here, a worked took his time to have the bow rope turned in. All in all I must say I was deeply impressed by the degree of self-reliance, of tidiness, of investment in robotics and other technological stuff and the passion with which Cranchi is making boats here. The economic crises didn´t miss that company for sure, but instead of choosing the know way of outsourcing supply and downgrading quality to offer low prices they did exactly the opposite: Investing in even more quality, in even better ideas and researching new areas.
Passion + Love = Quality
“We are here on the very soil were 150 years ago and four generations earlier out ancestors started with a vision”, says Paola. And I feel her pride, her will to protect the rich history and the name, that is her family´s name. Yet I also sense her ambition to go further, to seek out new horizons. She can be confident: Cranchi survived a lot of crisis, two world wars and other bad things.
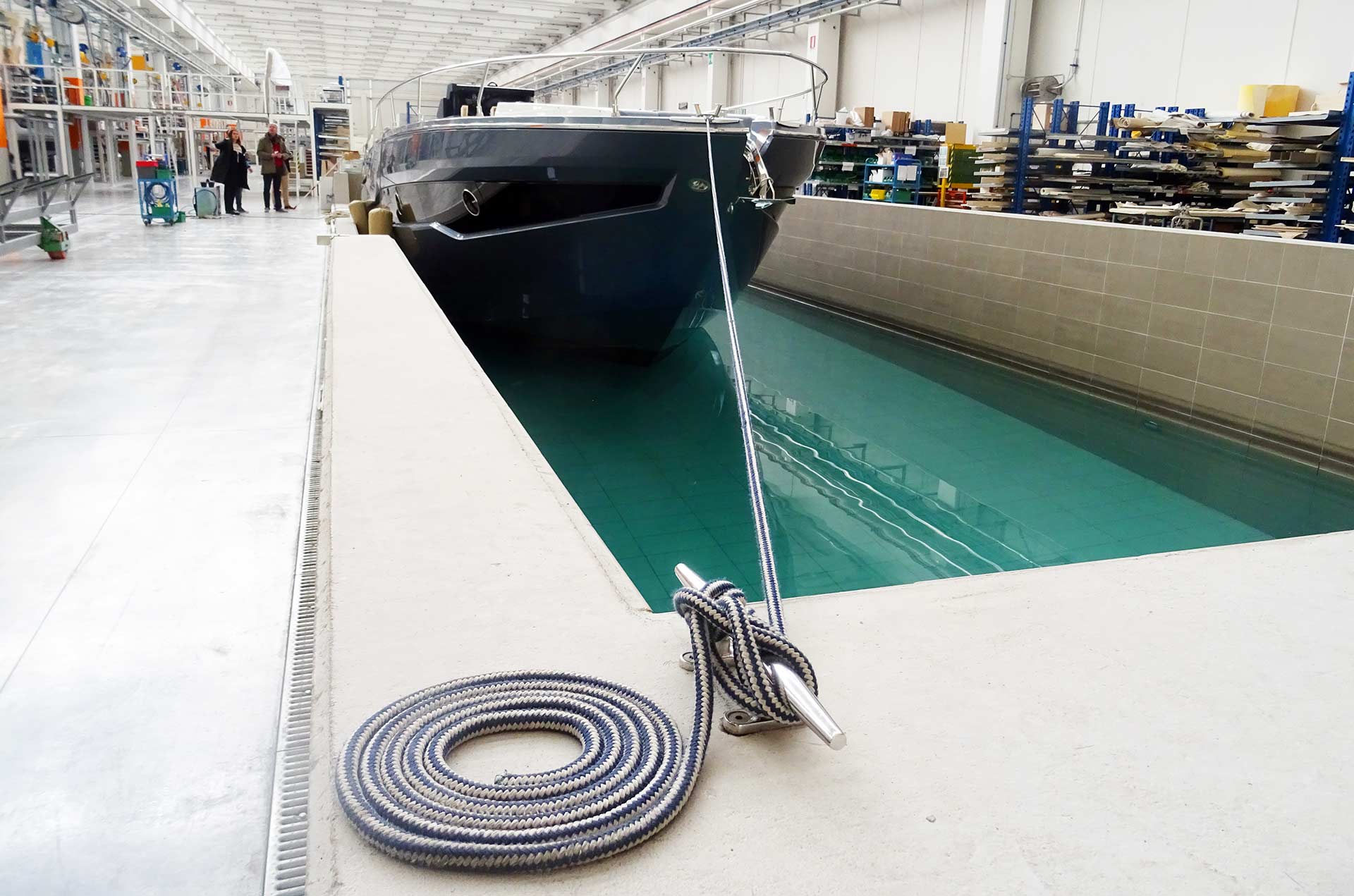
In the end, I leave Lago di Como and Cranchi being deeply impressed by their work and their efforts. And all the time during my way back to Germany there´s this one single idea circulating in my mind: What if these people would make sailing yachts? With this attitude, this commitment, innovative energy and dedicated people, they would certainly be among the best of the best. What a great and interesting experience – Grazie Mille, Paola!
Other interesting articles on that topic:
Visiting X-Yachts in Haderslev
A day at Luffe Yachts
Talking Magnus Rassy of Hallberg-Rassy about Scandinavian Sailing Philosophy