When I was doing another yard visit in one of Beneteau´s production facilities with some clients I was witnessing a question during the conversation between the visitors and one of the employers which encouraged me to do this article: As it seems, there is a common misconception among sailors about the fitting of bow thrusters. Well, at least when it comes to Beneteau. Okay, the production process of boats made of glassfibers and resin isn´t a new technology, even vacuum infusion is a process introduced a decade ago. But there are details still making me (and others) raise my eyebrows.
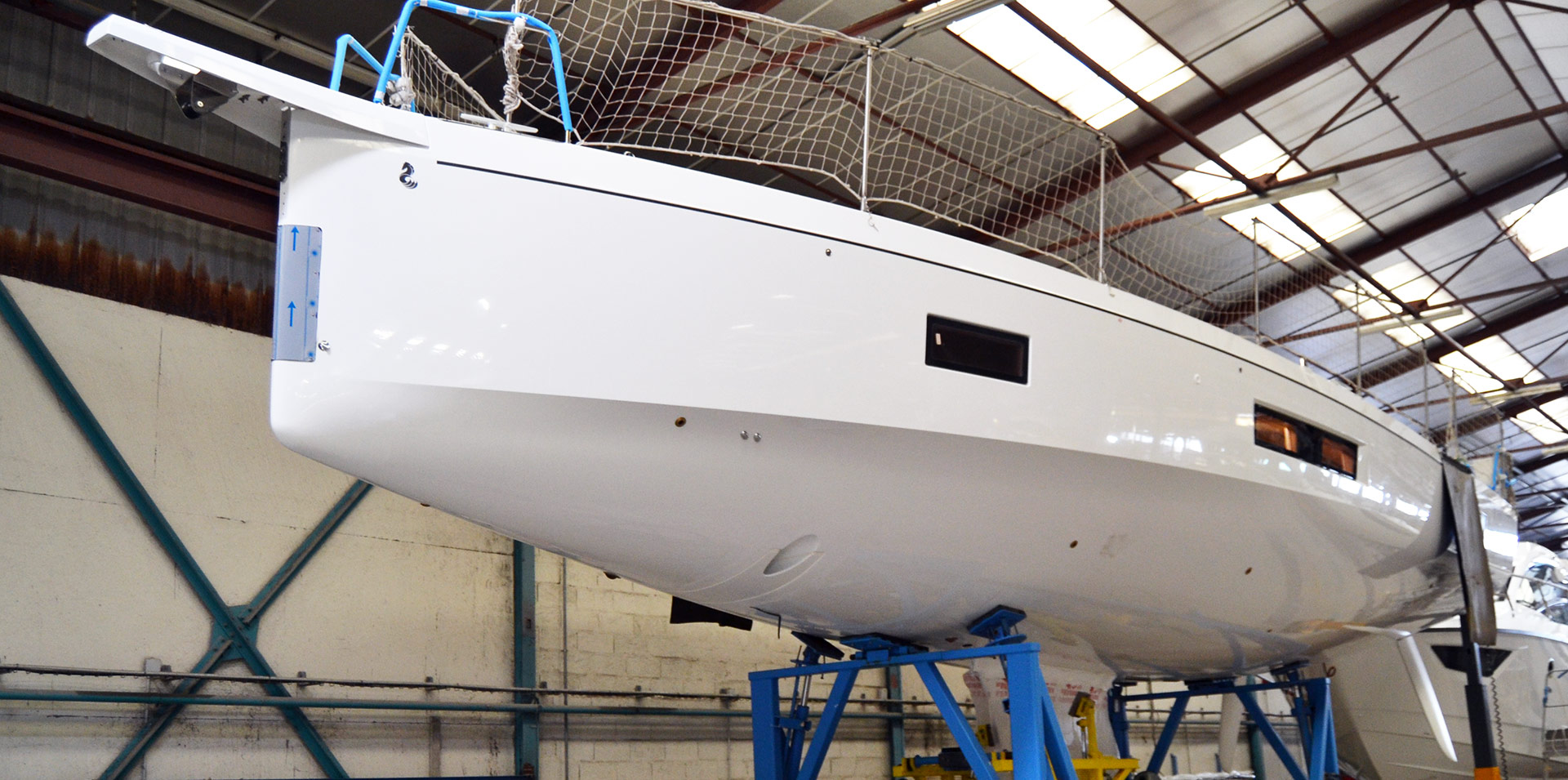
At the end of the production line there was a beautiful Oceanis 51.1 jacked on a stand ready to be shipped to her new lucky owners. Standing below the bow we could clearly see sideward the openings of the bow thruster – on a boat this size surely a very helpful installation. But then there was this myth about “holes in the bow”. So, let me start at the very beginning of the process …
A general misconception of bow thrusters
If you take a closer look to the Oceanis 51.1´s bow you will instantly notice a small joint all around the bow thruster section. This is a first indicator that there isn´t such a thing like a bow in the hull. As the widespread misapprehension goes, some people think that for installing the bow thruster the hull needs to be cut open in the bow. Somehow, as they think, a kind of tube is installed, closing off the holes and housing the thruster unit itself.
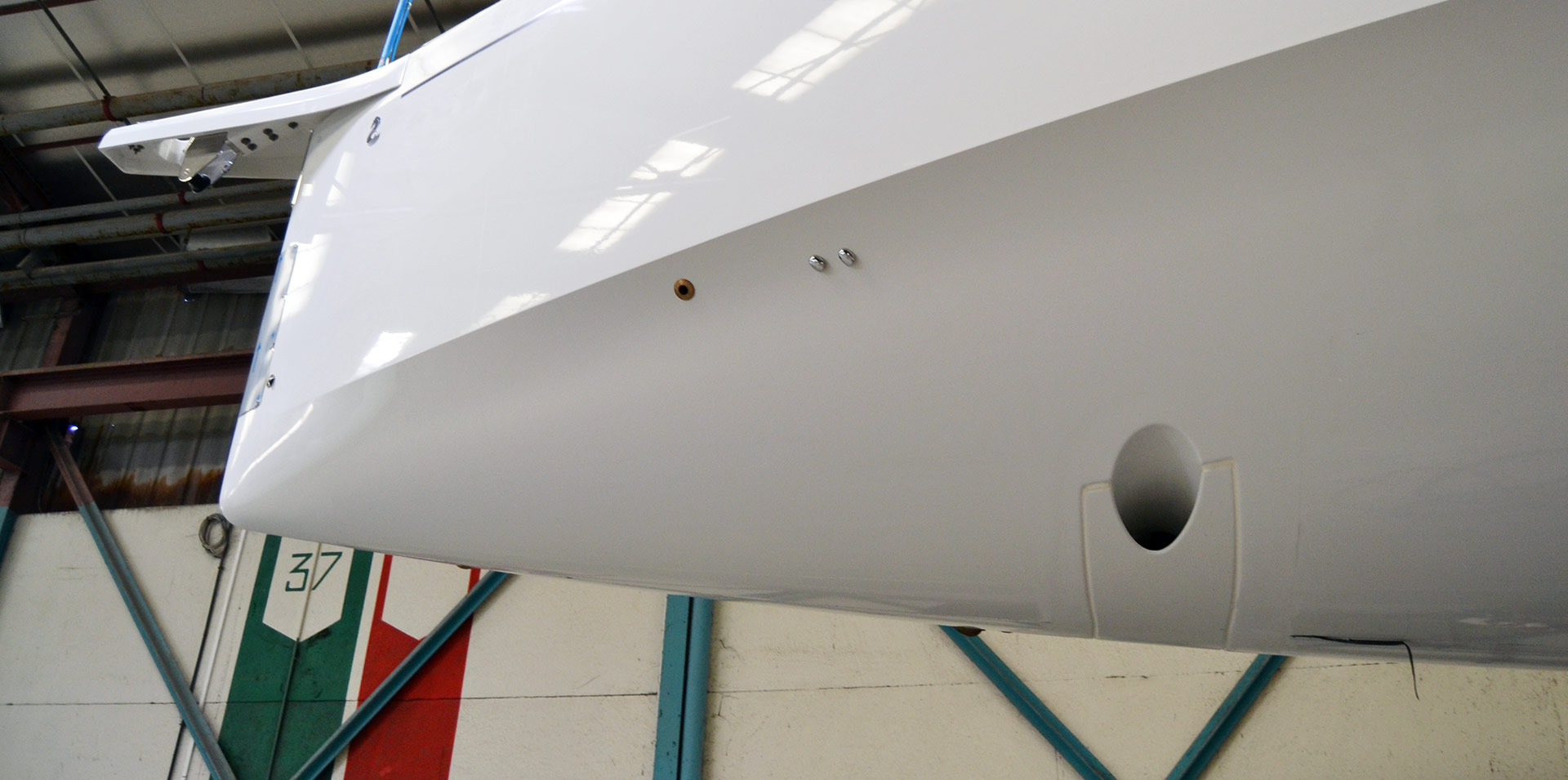
This is – at least here at Beneteau – a thing of the past. “We do not have to cut huge holes in the bow”, one of the guides assures our clients and offers to show how the integration of a bow thruster is done now in modern times with their latest boat, the Oceanis 51.1 (read here another article on a very interesting detail of this boat – the chines running from bow to stern all along the hull)
There is no hole in the bow
In the finishing chamber where all hulls go after being released from the mould, we can see the “secret” with our own eyes: The very hull is moulded in a way that there is a big cavity moulded into the hull. Not fine tuned right now one can clearly see that this is a huge opening for sure – but a very clever solution in the end: “Here the bow thruster unit will be installed into the thrusting tube”, our guide explains, showing the exact place.
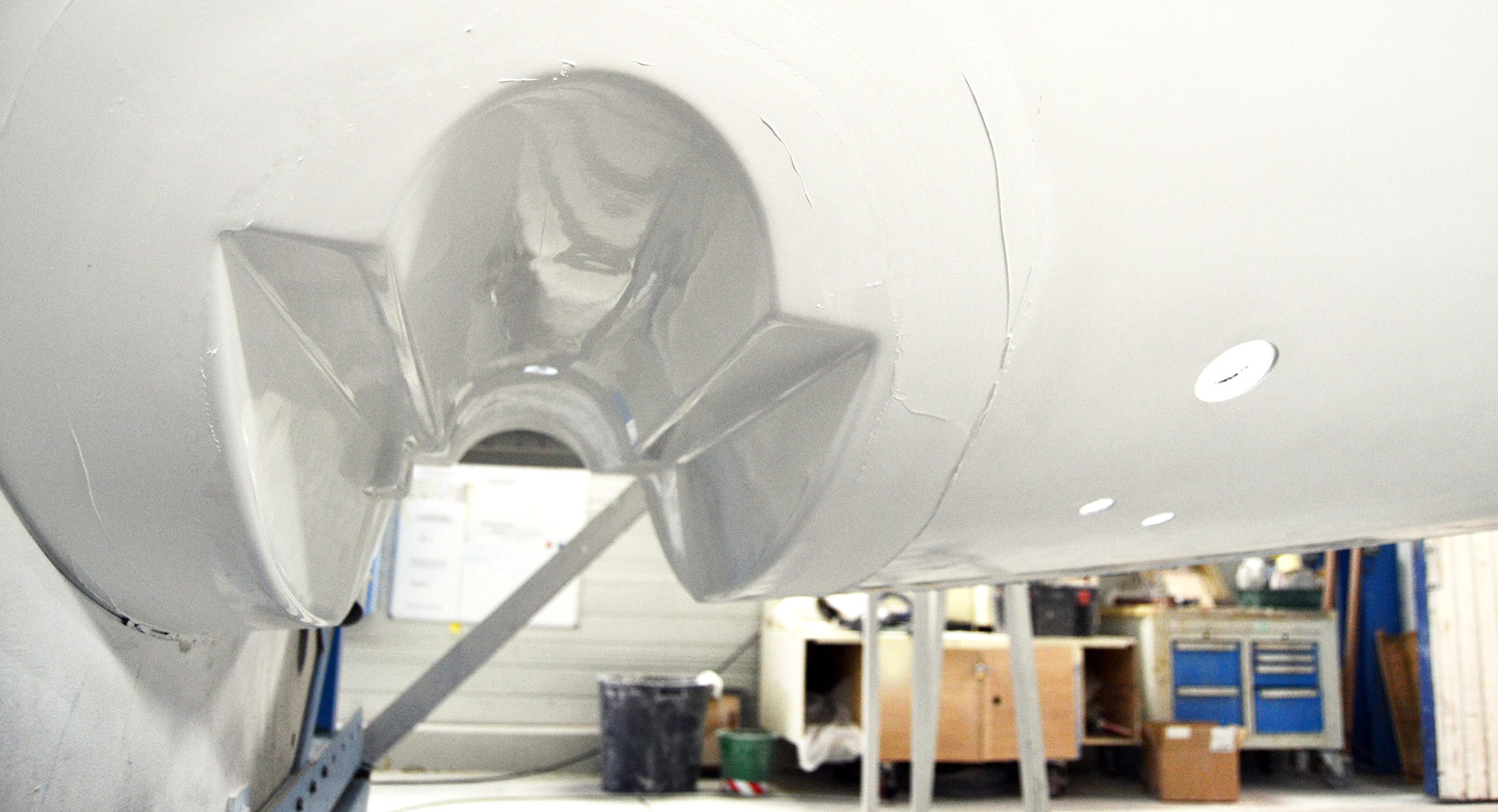
“As you may see, we only need only a few very small holes to be drilled into the hull here for fixing the bow thruster and having the cable for the electric power supply connected to the power circuit of the boat.”, explains our expert guide. Now that´s something new for most of our visitors and I by myself find this highly interesting too every time I come here: Yes, there is a hole in the bow. A huge one. But no, that hole won´t be a risk for the boat.
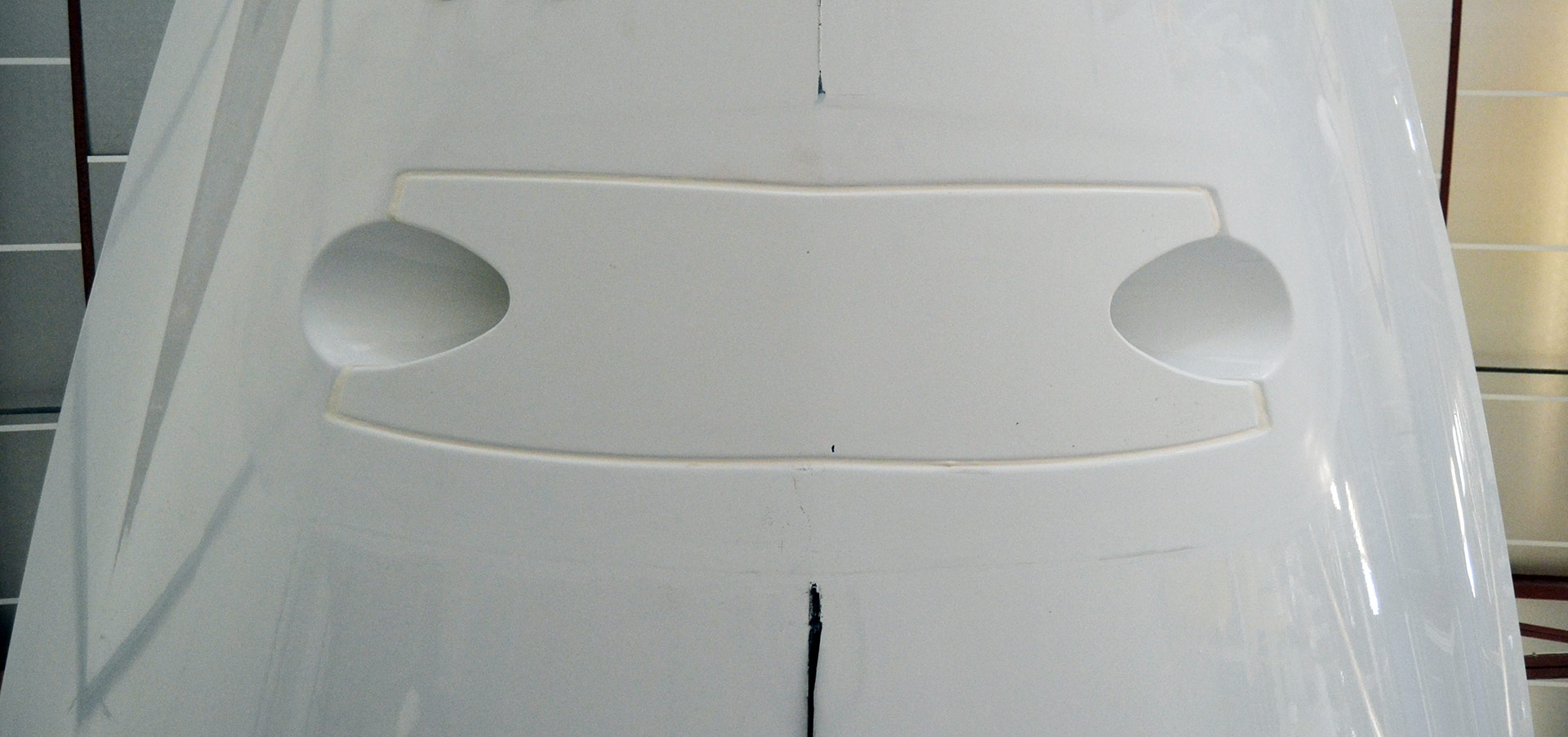
During the final fine tuning of a freshly from the mould released hull the workers will cut away surplus material left over at the edges of the hull as well as polishing out minor impurities. Also, if there had been done minor damages to the Gelcoat or dents being done upon the new hull, it´s the workers on this very station who will make the hull shiny bright and absolutely spotless. They also prepare the bow thruster-section for later installation of the unit – as we clearly can see by taking a look to one freshly applied thick layer of gelcoat, later to be smoothly polished away.
Watching Beneteau´s Oceanis 51.1 being built
Next step will be the fitting of the thruster unit itself with the final application of the panel that closes the gap in the bow. This is done with a hydrodynamically optimized GRP-panel that neatly fits the very shape of the bow and thus completes the hull design. In this way, Beneteau achieves to both offer the useful amenities of having a bow thruster for perfect mooring manoeuvres as well as guaranteeing a both simple and safe installation (without cutting big holes in the bow!) by at the same time having an easy access to the unit in case something breaks down: When bigger maintenance or the replacement of the whole unit is necessary skilled personnel will just take off the panel and can then work on the bow thruster from the outside – not being cramped in the bow.
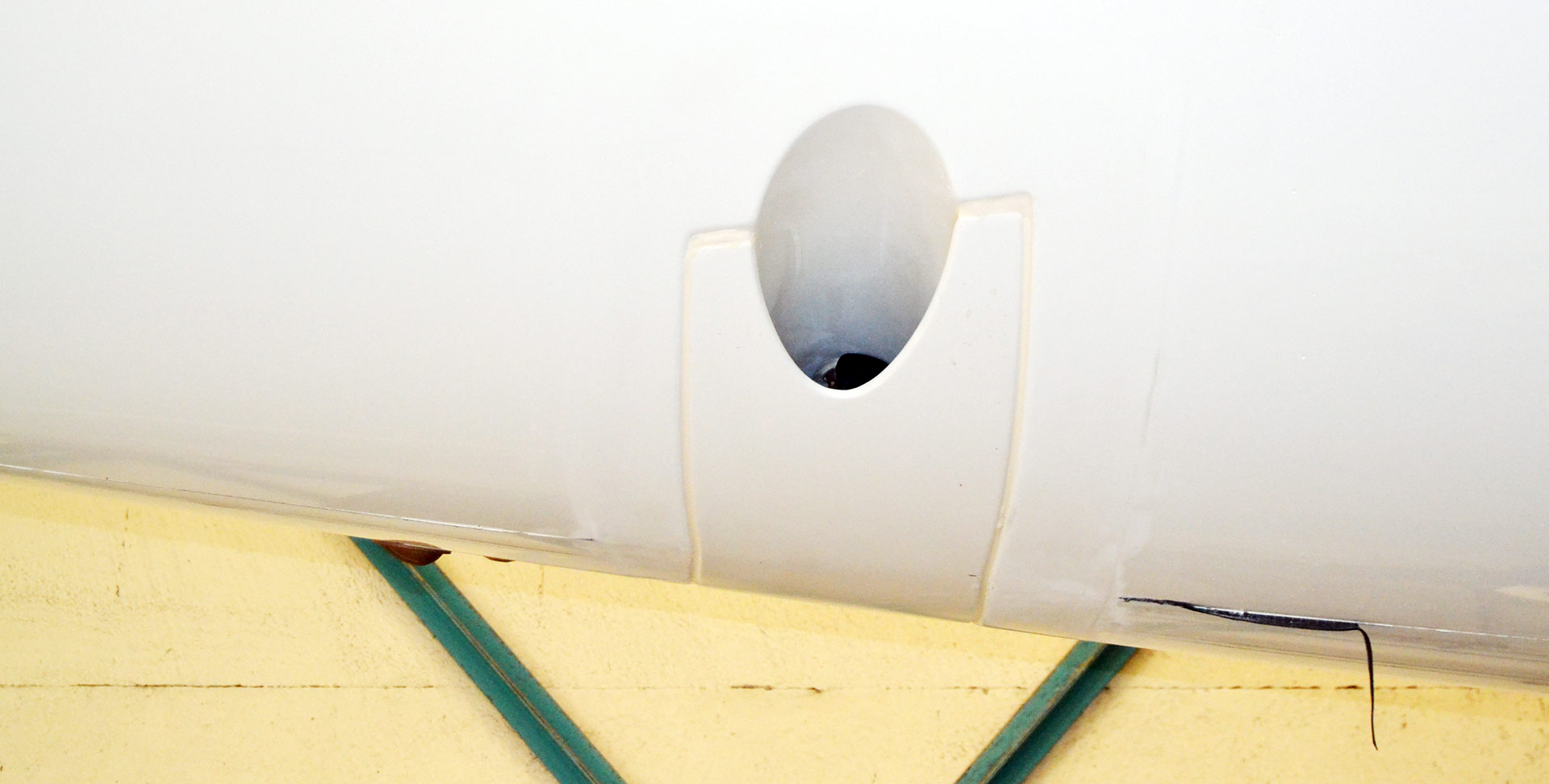
In the end we finish our yard visit at Beneteau and have again learned so much new things about modern production boat techniques. I know that this bow thruster-installation thing is just a minor detail but I regard this as a highly interesting one showing that constant advancement even in minor details will push production boat engineering even further step by step.
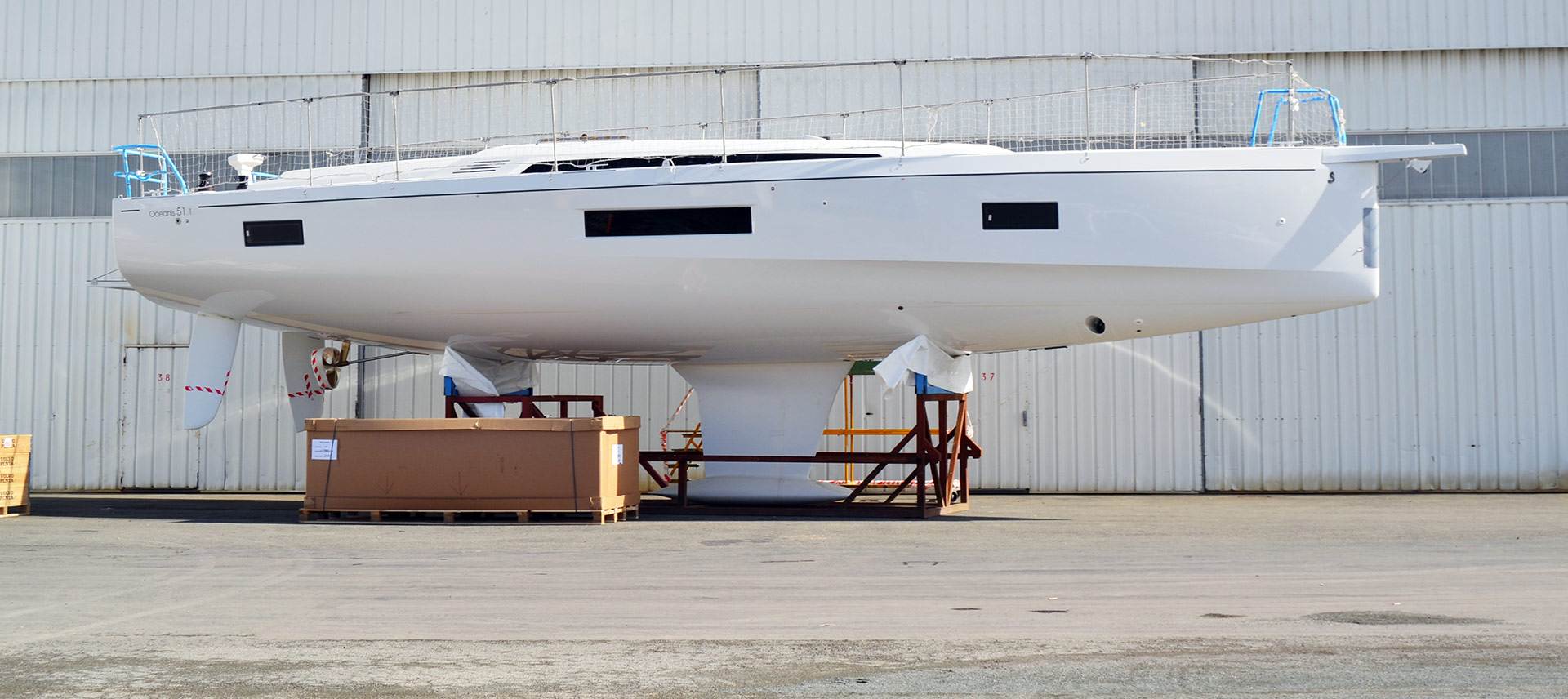
Another finished Oceanis 51.1 is jacked in the early spring sun outside the halls of Beneteau and as we walk passing by to say Goodbye to our fine guides I take a quick side glance at the perfectly streamlined bow, noticing the small opening for the bow thrusters knowing, that there really isn´t such thing as a big hole being cut in the boat´s bow for sure.
You may also like to read:
On chines: Damien Jacob of Beneteau talks the new Oceanis 51.1
At the Beneteau yard: Seeing the Oceanis 51.1 being built
Essential manoeuvres for sailing yacht skippers