There are lots of boats and yachts on the market right now and as I am a great fan of good design and design features, there is seldom a yacht which cannot raise my interest. But from time to time there are boats which really do fascinate me because they incorporate something special, something new and something never seen. Like for example the Alubat Cigale 14 which I love for her one-of-a-kind interior layout, the Pogo 40 for her craziness in sailing characteristics or the Berckemeyer because she is an absolute dream yacht. Recently another such fascinating boat raised my awareness: The Beneteau Oceanis 51.1.
The Secret of internal Volume
Yeah, you already know that I am working for a German Beneteau Dealer and you might think that I am obliged to write only good stuff about this companie´s products – but that won´t be true. I am free to write anything I want and here in my private project it´s just me who decides. Believe me: The Oceanis 51.1 is indeed a true game changer and I would write the same about her if she was made by Jeanneau, Bavaria or any other brand for sure.
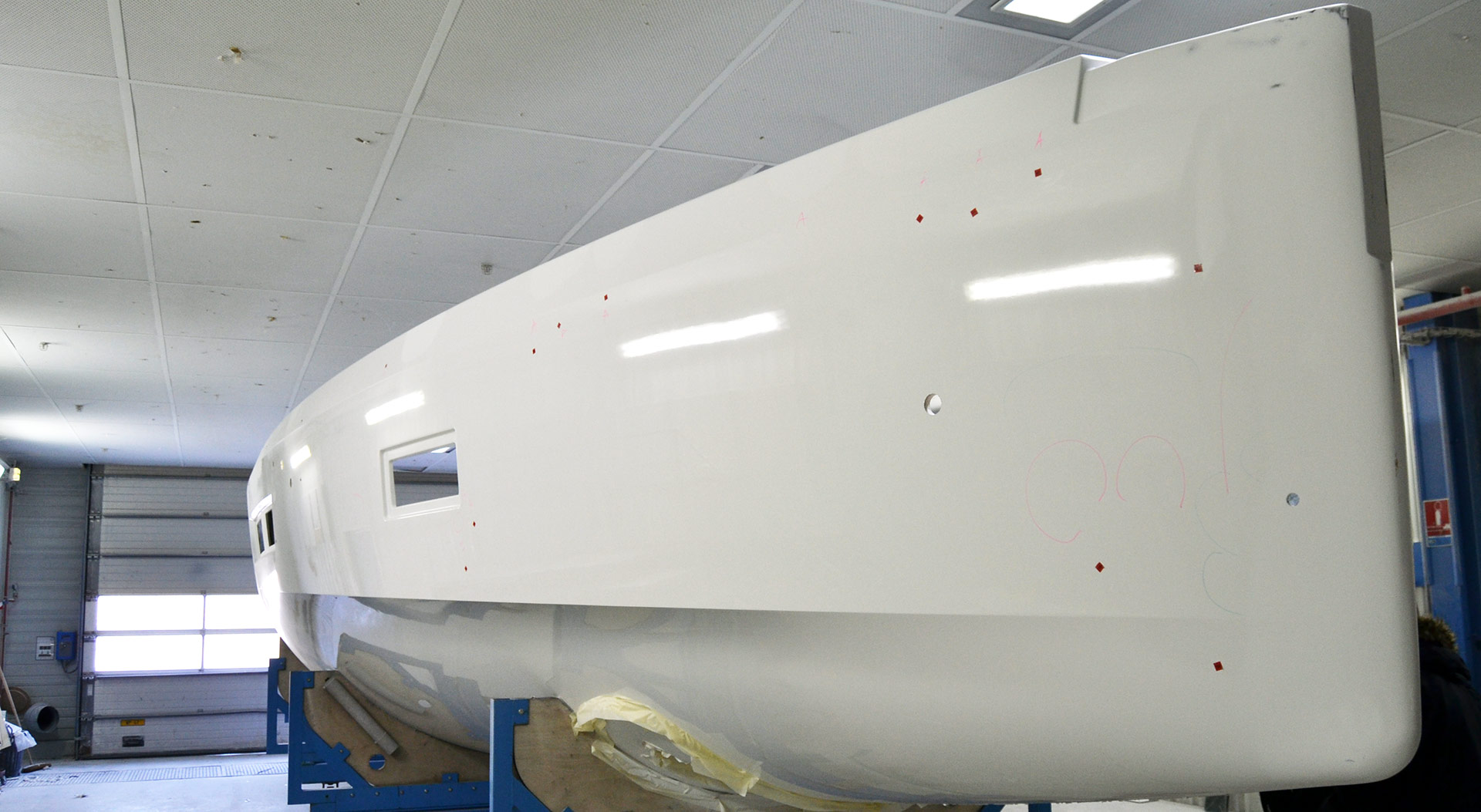
I first saw this yacht in reality during Cannes Yachting Festival last September (read my article on the show here) and could tell through my own observation that she was drawing a lot of attention from the visitors the whole show long: She was the star of the Beneteau jetty, although there had been even bigger boats on display, like the luxurious Oceanis Yacht 62 or the big Sense-yachts. But why? One of the reasons indeed is her outward appearance. As Oceanis product manager Damien Jacob was telling me, the design team had a clear role model when starting to work on the new cruiser: The Rambler 88 racing yacht (read my interview with Damien here).
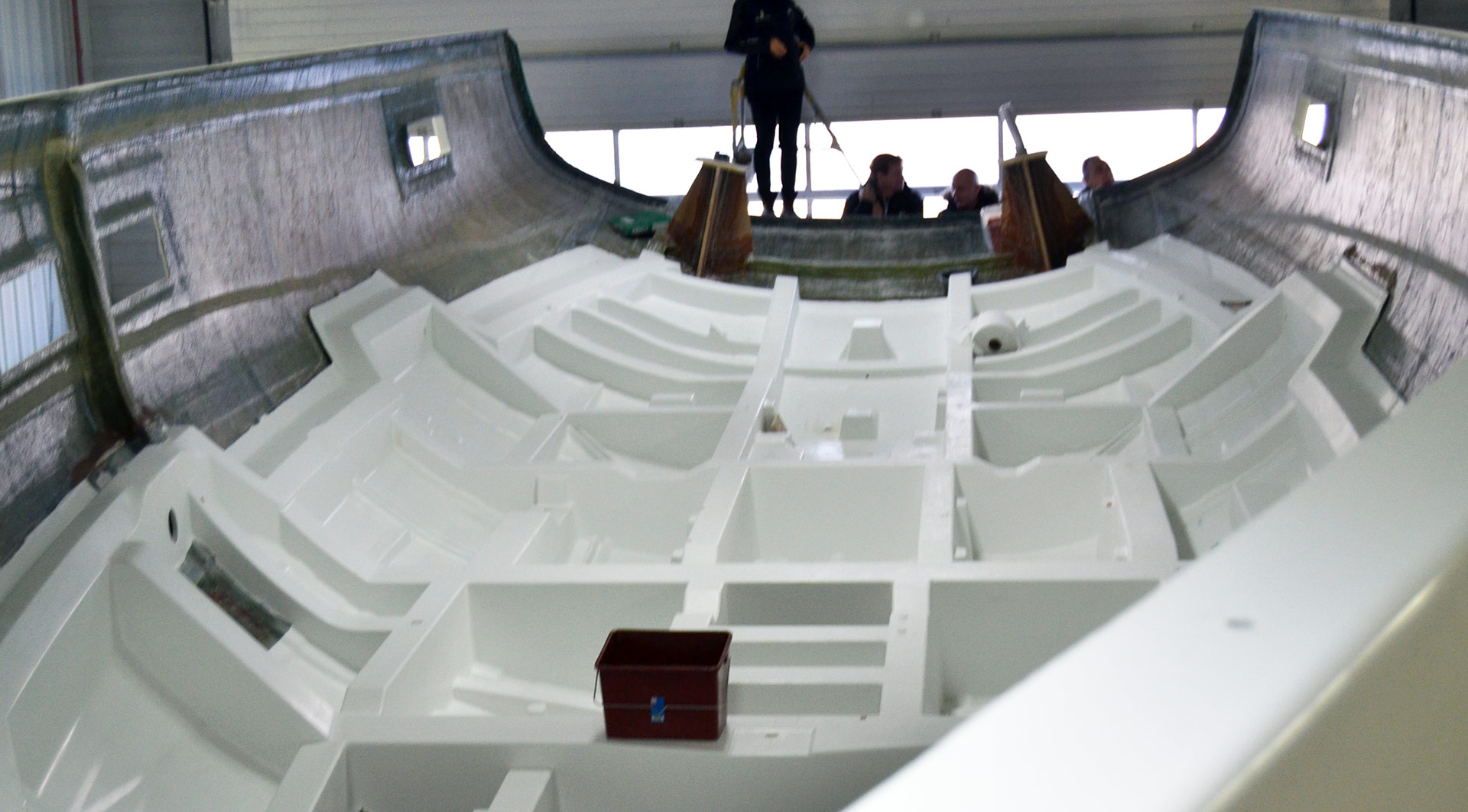
That´s truly a really great role model as the low freeboard, wide stern and sexy low superstructure is indeed an attraction. We didn´t had a slow down of fresh visitors during the show and I know from the sales department that the yard is sold out with Oceanis 51.1 yachts for the coming year 2018 after just a few weeks after announcing the 51.1! What a great success. So, there must be more to this yacht than just the outward design and some faint reminiscence of the Rambler-racer: And for sure, the secret lies in her internals.
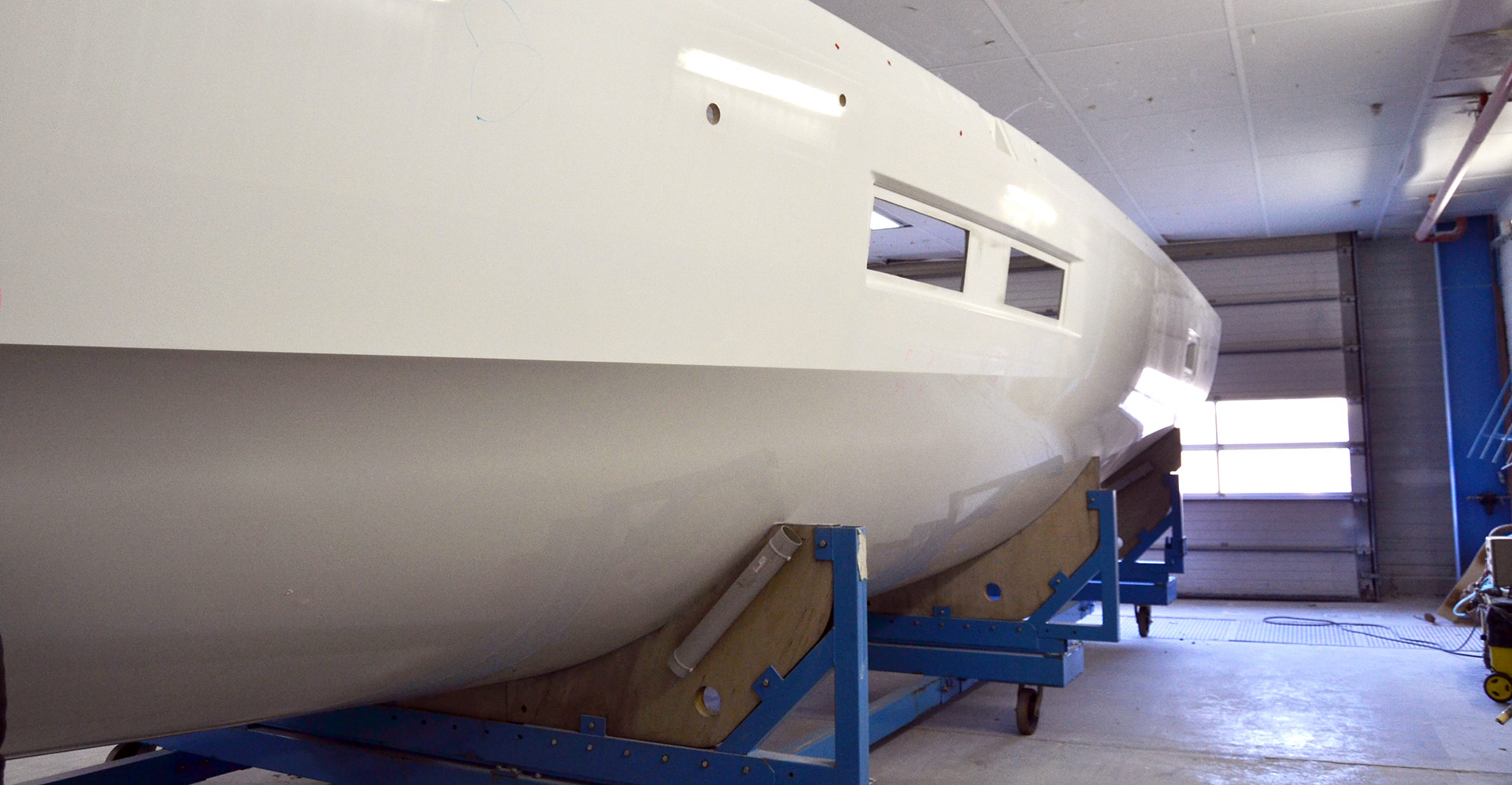
When I was visiting various Beneteau production sites last week (among others the Figaro 3 series production as well, read my exclusive article here) I also had the chance to see the making of this new Oceanis 51.1 which – for me personally – is the Beneteau Flagship right now as she represents in my eyes the very latest of the combination of sailing ability, interior volume and cruising quality for the whole crew. As the building process is not principally different from ordinary GRP-production boats, I will hence focus on the internal fittings of this yacht in this article.
One month on the Assembly Line
After being laminated and glued together, the outer and the inner shells of the hull of an Oceanis yacht will be brought from the GRP-production lines to the final assembly hall. Here, among other types of the Beneteau range, the Oceanis 51.1 has her own assembly line. Four hulls in a row are piled up here, each one in a different stage of fitting. Beginning in the aft part of the line, the bare hull will receive her tanks for fuel, fresh and waste water, all the piping, valves and wires are mounted. Woodworks starts by inserting and laminating the bulkheads and installation of the flooring.
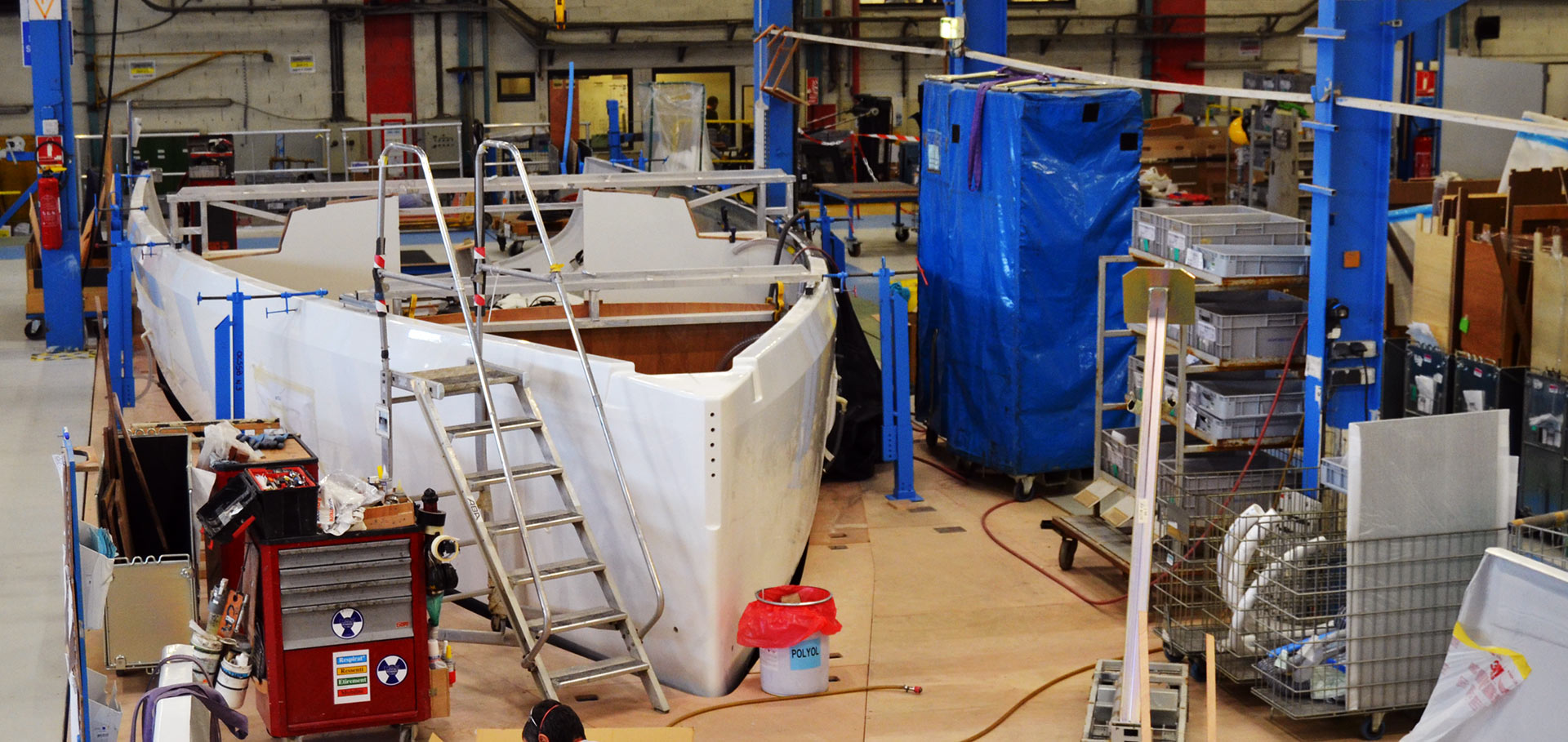
It seems like a chaotic process but I know from first hand experience with my own refit project on my King´s Cruiser 33 yacht that this is just the impression for people who don´t know ship building. Everything has it´s designated place, will be brought into the hull at a designated time and fitted to the boat to a designated place. There is indeed order in the chaos and I find it rather inspiring to watch the engineers working on the boat.
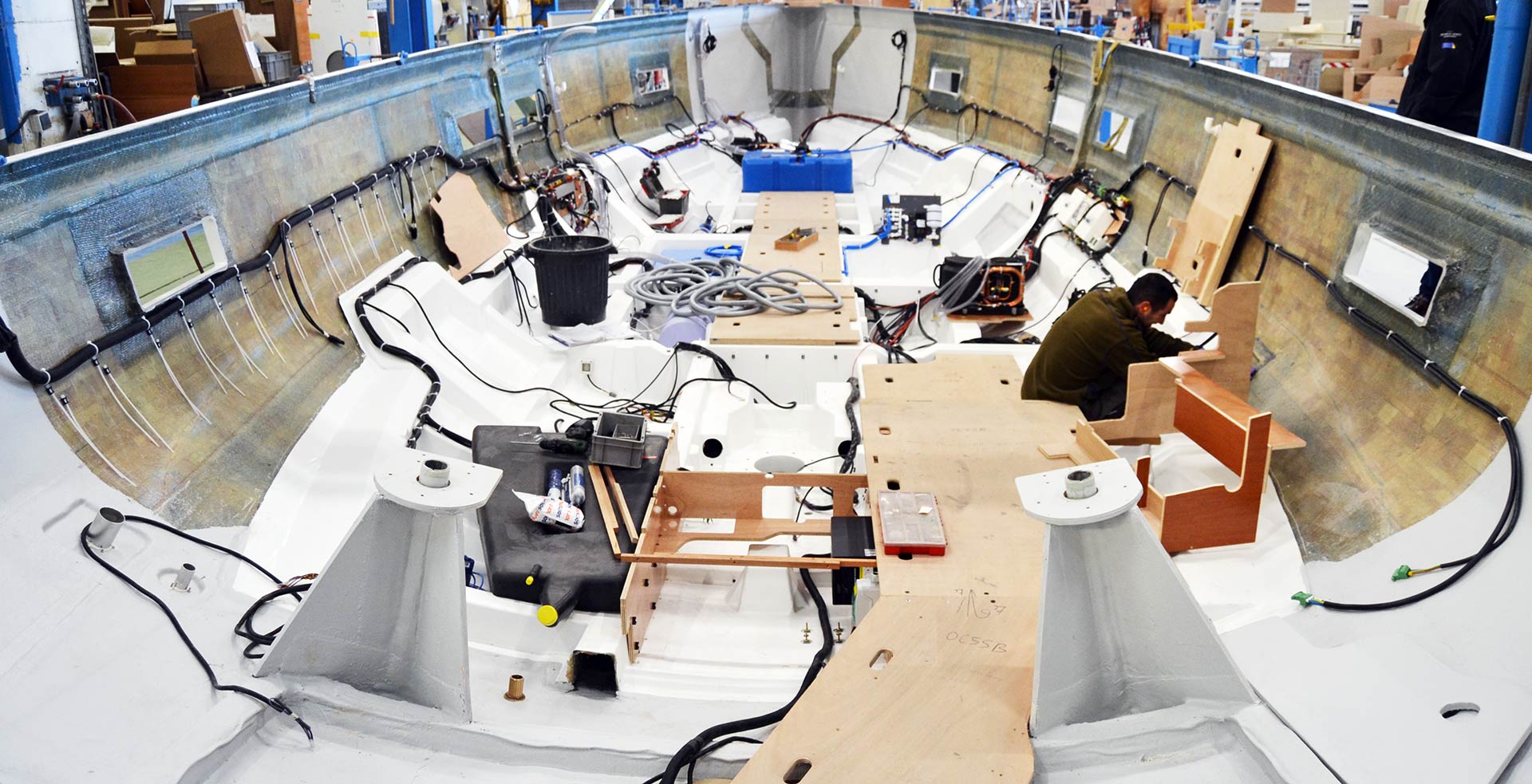
With Beneteau´s assembly line, as they tell us, there is the frequency of one-four, which means that the hull is standing on its place for roughly one week, five days, to be fitted with the then required things. After one week the hull will leave the place to crawl one position forward in the assembly line. It hence takes roughly one full month to have a yacht finished on this assembly line. The interesting part comes in the co-ordination of this process: Whilst people are working on four hulls simultaneously, they have to manage to finish their respective tasks all at the same time. Amazing!
The astonishing main Saloon of the Oceanis 51.1
On mounting station 2 of the Oceanis 51.1 line a still open hull is at display. At this stage of the process, the bulkheads have been mounted and the principal joinery had been fitted too. As I position myself directly off starboard side I can take a detailed look onto the port side of the saloon-to-be. As I said early, the Oceanis 51.1 is a true game changer and here one can clearly see why: This boat, because of her wideness, features a rather unusual but exciting arrangement for the saloon. The galley, classically on port side, is arranged as a large C. There is loads of stowage, cooling and freezing space and the worktop-area is amazingly big. Also, facing forward at the main bulkhead, there is the principal control station featuring a small chart table, VHF – which in this case is just a handheld device which will be mounted either down below at the navt station or up in the cockpit. I am honest that I dislike this configuration and fancy a more conservative nav-station-design but there is a certain charm to it: Watch the nicely curved sofa running all the way from the nav station around the galley to face the large dining table (for up to 10 persons if folded out completely!). Together with the large L-sofa vis-à-vis it forms a unique combination of seating possibilities in the yacht.
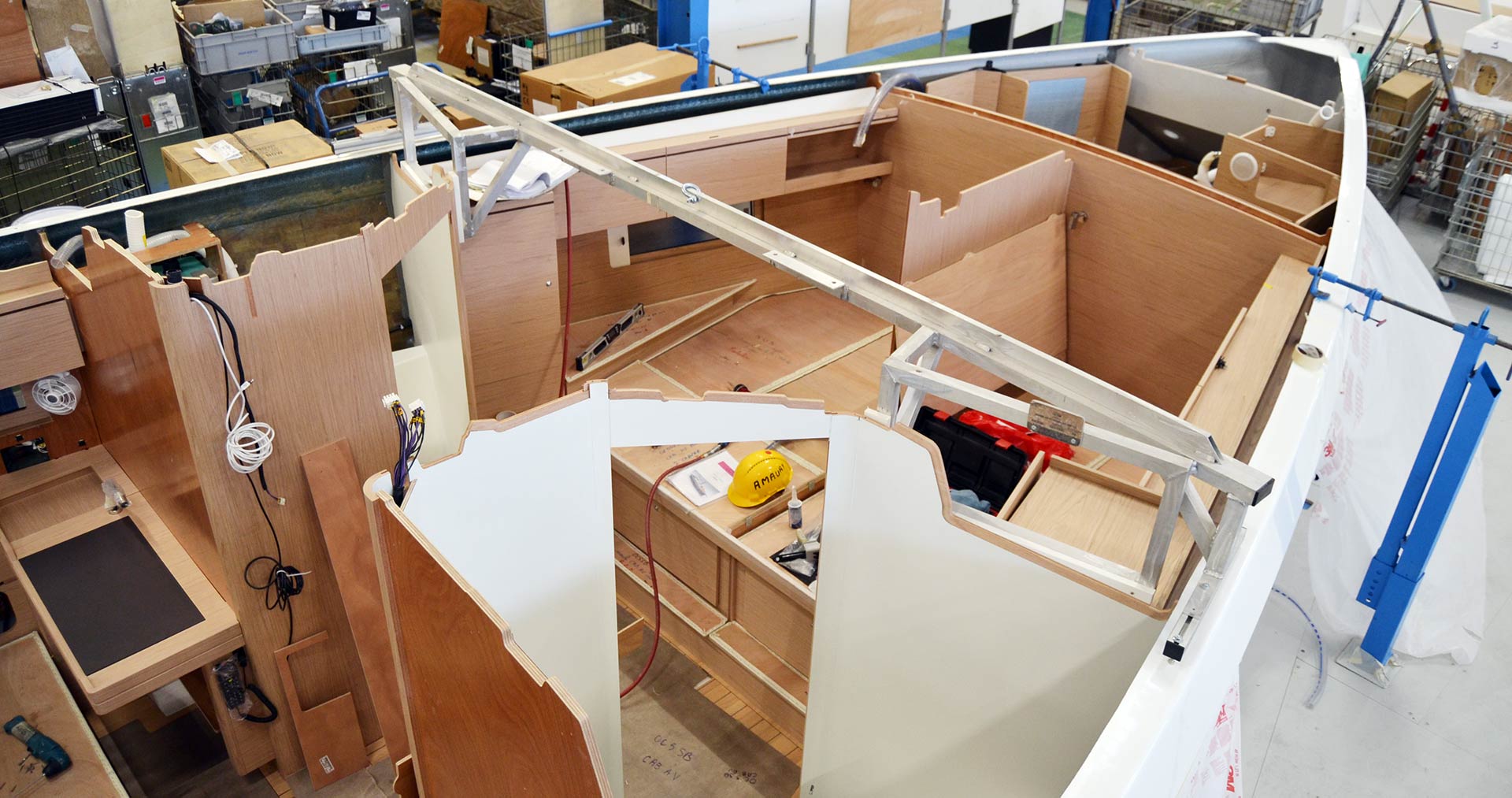
Another thing makes the Oceanis 51.1 certainly special: Because of the fact that the distinct chines of this boat are fitted starting right at the bow, there is so much space gained. 40 centimetres to either side right in the front cabin (see my previous article for a comparison of the Sense 51 and Oceanis 51.1 front cabins, it´s a huge difference!). This enables this boat to feature a double front cabin configuration – certainly only interesting for a charter-use of this yacht. But what makes it special is the sheer size of these new two front cabins: They offer the same amount of space as the aft cabins with real grown-up-sized berths. Also, the longitudinal bulkhead separating them two front cabins is easily removable in a matter of a couple of hours.
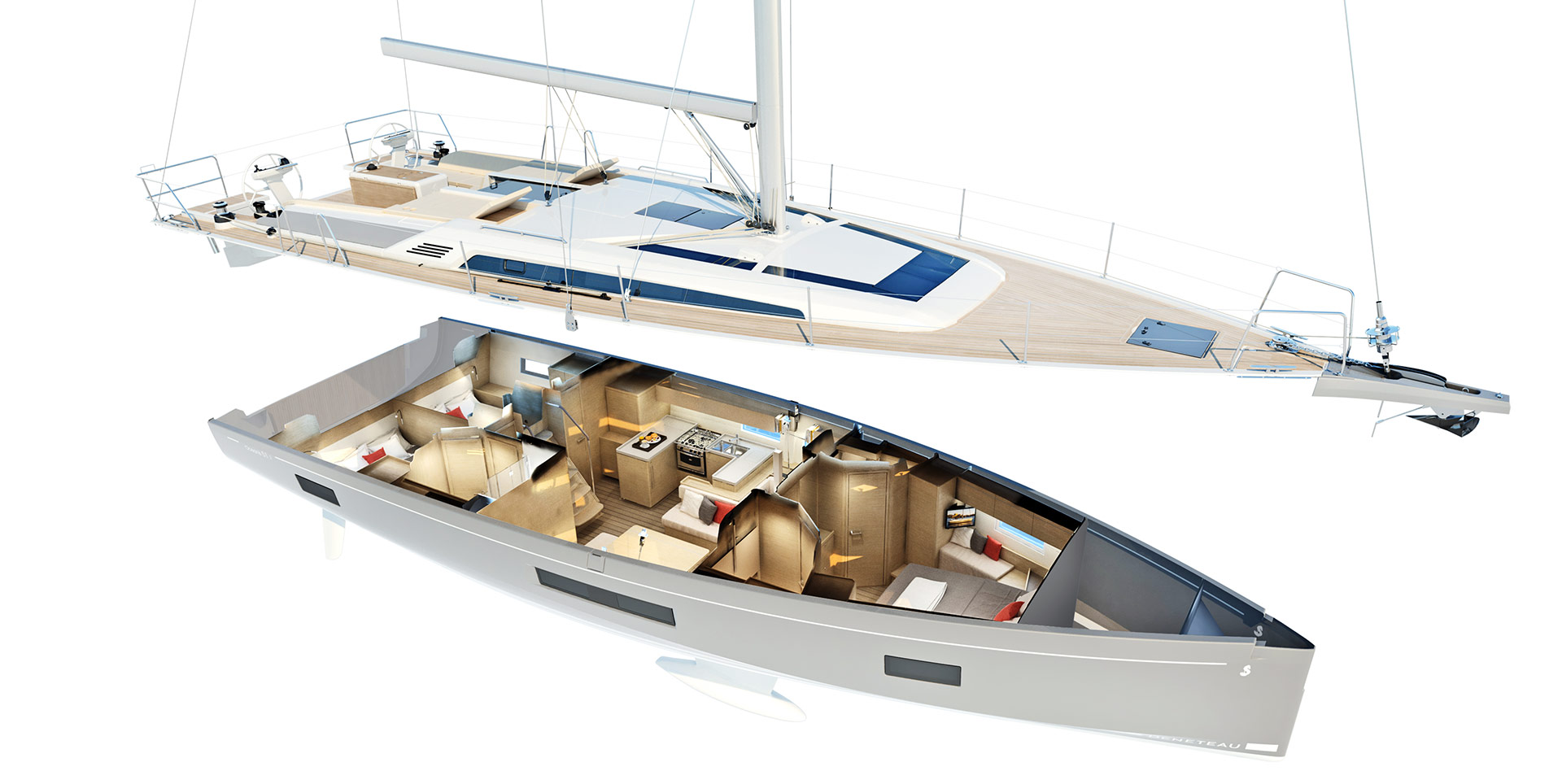
This all can be better judged by looking at the cutaway rendering of the Oceanis 51.1: What I find particularly interesting is the sheer volume of this yacht that can only be found in fairly bigger boats of the 55 to 60 feet range: Just look at the owner´s cabin size in the rendering which is really huge for a 15 metre boat! Also, the aft cabins and the – optional – Pullman/third heads cabin are a distinct feature of this boat. I have never sailed the yacht by myself in various conditions so this is still a complete riddle for me, but I tell you, if she is sailing well on all points of sail and in either light and heavy wind conditions, the 51.1 is a real dream yacht!
Small but fresh Ideas
What I loved about the internal fitting of the yacht was the new flooring style. As brushed European Oak is currently a big trend in interior yacht design the Oceanis makes no exception here: All of the four models currently on assembly had been fitted with the light variant of wooden interior. There is also a darker, more classical design available. But what was really cool was the flooring, also bearing an Oak-style with large wide “tiles” and a light grey lining.
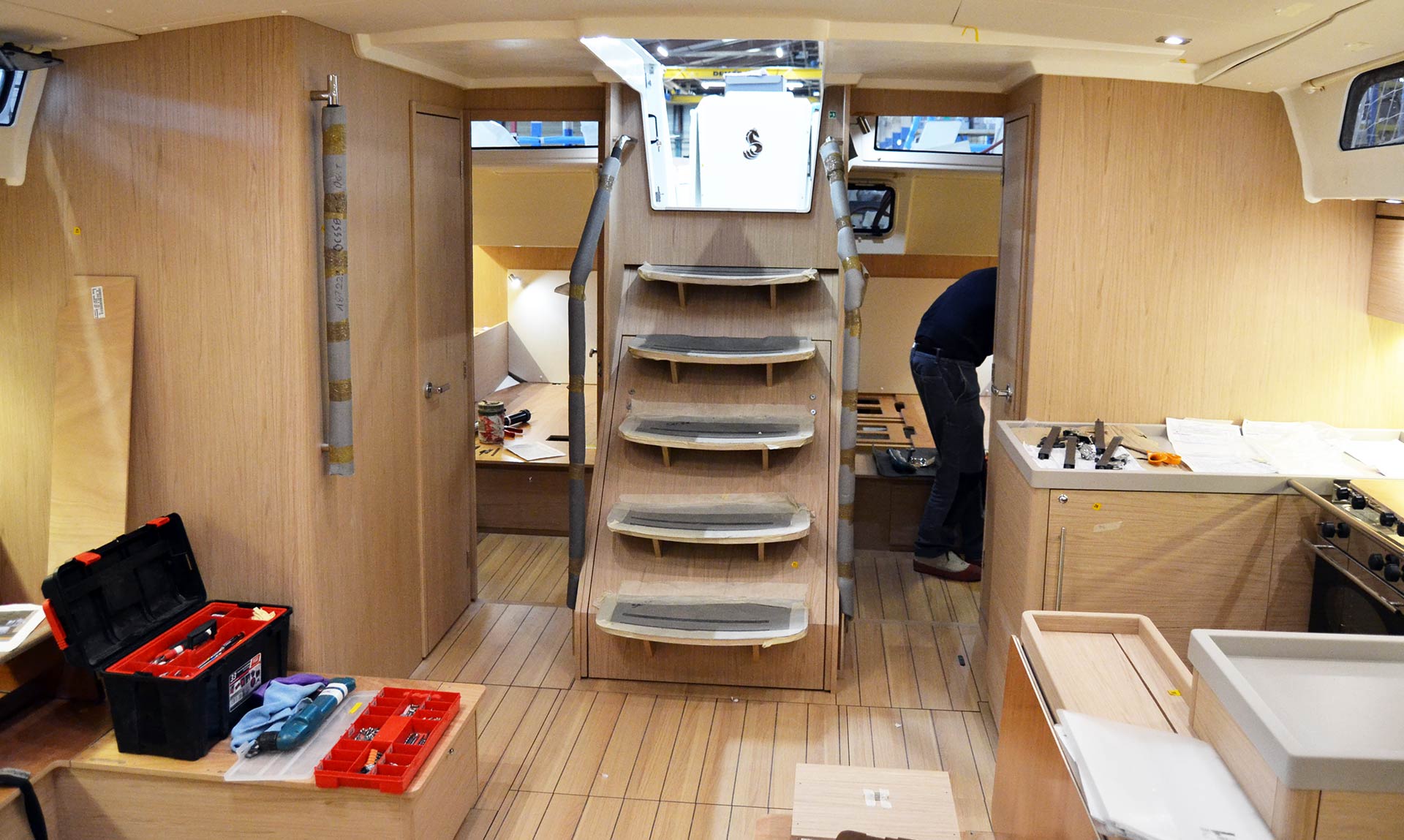
Really cool was the “swing shower” in the owners bathroom which is not just a space saving device but also sparing the owner/crew lots of cleaning work: Upon entering the heads there is the ordinary WC (pumping or electric) and a small sink for washing one´s hands. You then just grab into a nicely “hidden”opening, release a small lock bar and pull at the whole “wall” to which the sink is fitted. Then the shower will fold out smoothly …
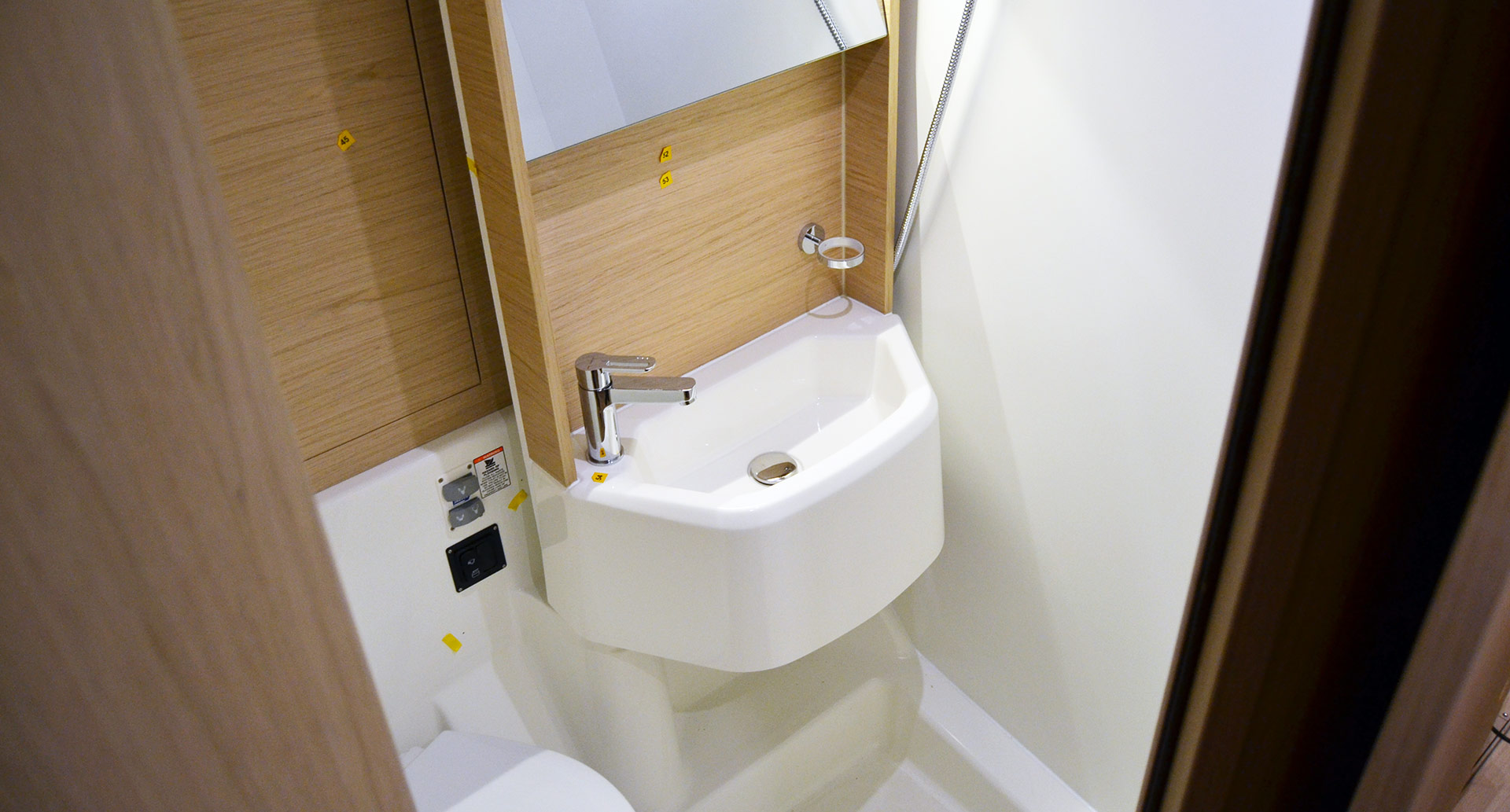
The good point at this configuration is that it saves a lot of space in either position: Folded away the bathroom is huge and free of the shower hose, there´s enough room to get undressed or dressed or just walk around while washing one´s body. In “shower mode” the now arranged bathing is way bigger in volume than it would have been when it had been fitted the classic way. Nice side effect: Spray and the majority of the water used for showering won´t get the rest of the heads wet.
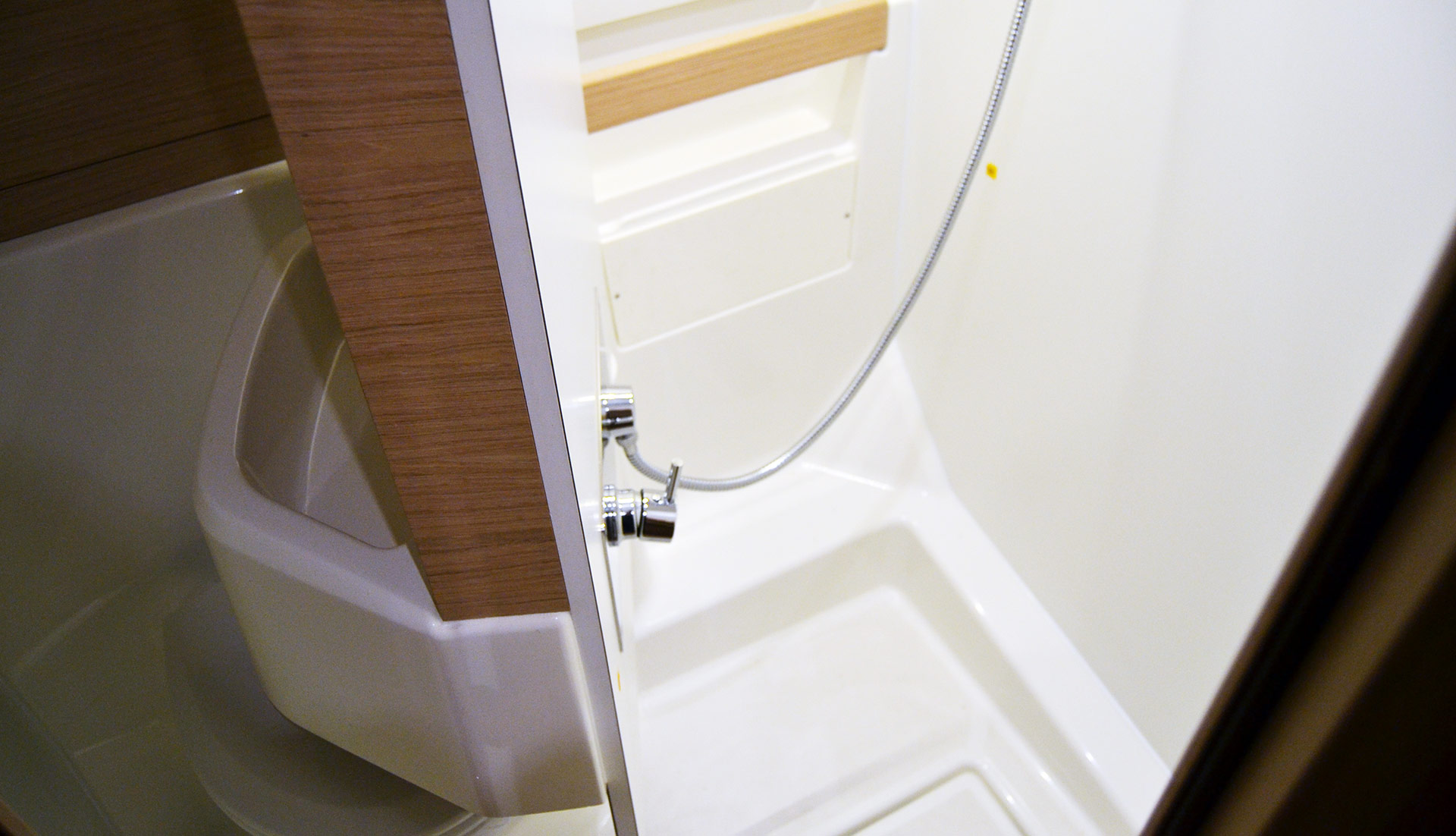
Another example of the game changing aspect of this yacht due to the amount of available space is the skipper cabin. Remember, we are on a 50 feet yacht: But there is such an amount of room even right behind the huge chain locker in the bow that a skipper cabin with own heads, waste water tank, lots of stowage and a full sized berth (fitted transverse at the bulkhead) can be fitted optionally without any problem. If not, the room may be used for stowing sails, fenders and spare roping. And there will fit a load of stuff!
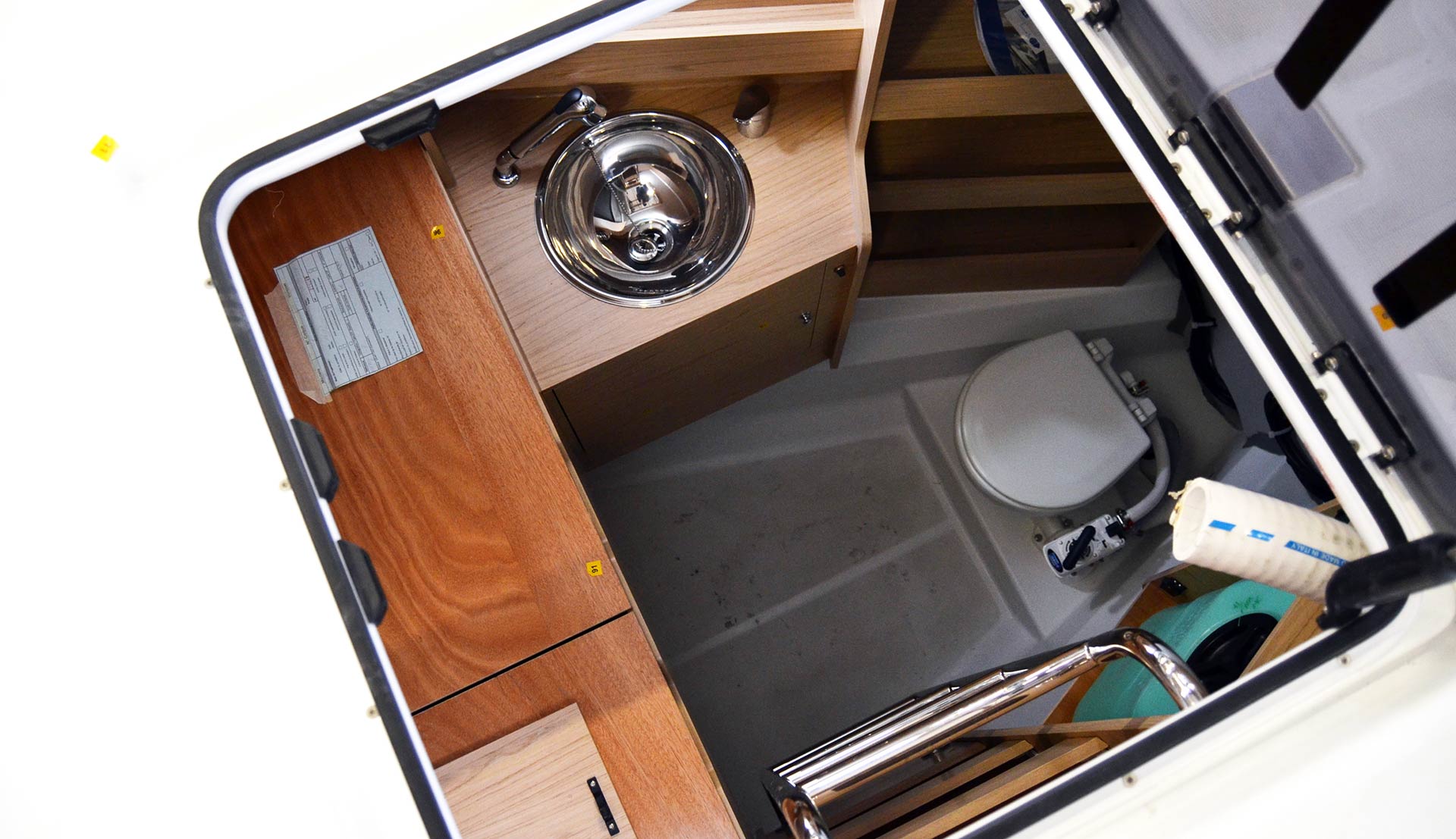
Of course, we are talking about a yacht that will probably attract a lot of charter companies because the boat can be fitted with 10+1 berths, which is a huge capacity for a 50 footer. But I know quite a handful of classic owner-sailors who ordered this yacht in the three-cabin version – it will be interesting to see how they outfit the boat in the end. Did I mention that Beneteau offers three different basic layouts of this yacht, ranging from a shoal-keeled easy-to-sail variant to the “First Line” with performance rigging, deep keel and “racy” layout?
Adding the final touch
My tour of the yard nears its end as I approach the fourth and final assembly stage. Here the deck structure – readily fitted with Teak, winches, blocks and clamps – is lifted onto the then finished hull and the marriage takes place. Adding a final touch of the hull, the workers will now mount the huge U-shaped blackened portholes to the frontal deck structure, all hatches and sealings will be done and the electric circuits for the lighting connected.
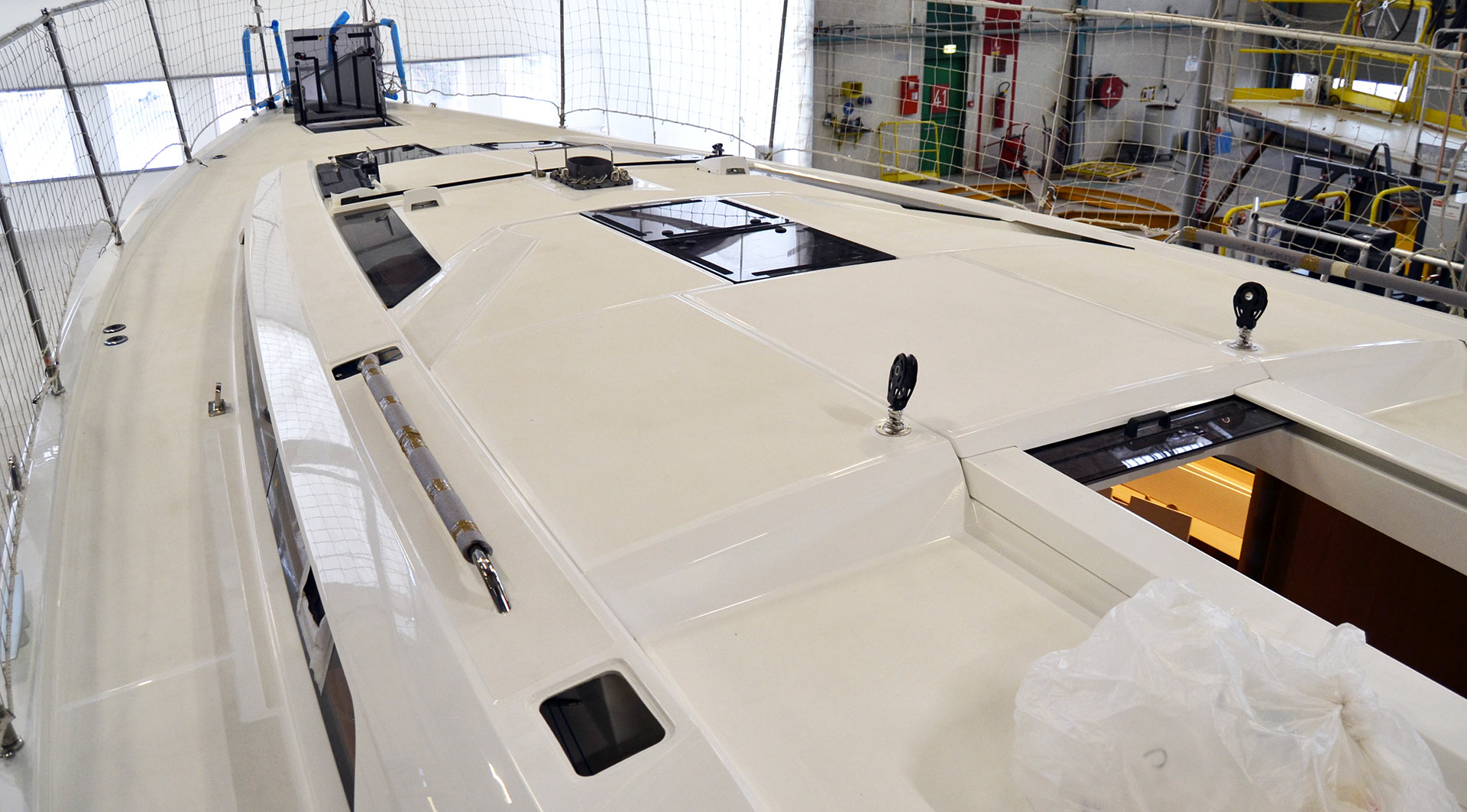
All yachts then are processed to the large testing pool at the end of the big assembly hall. Here the boats will undergo a decent test. Engine, auxiliary machinery, pumps and mechanical systems are checked thoroughly. By a crane a large “rain machine” is positioned above the boats to simulate downpour in order to check the watertightness of the yacht. This process may take hours to days, depending on the size and complexity of the yacht.
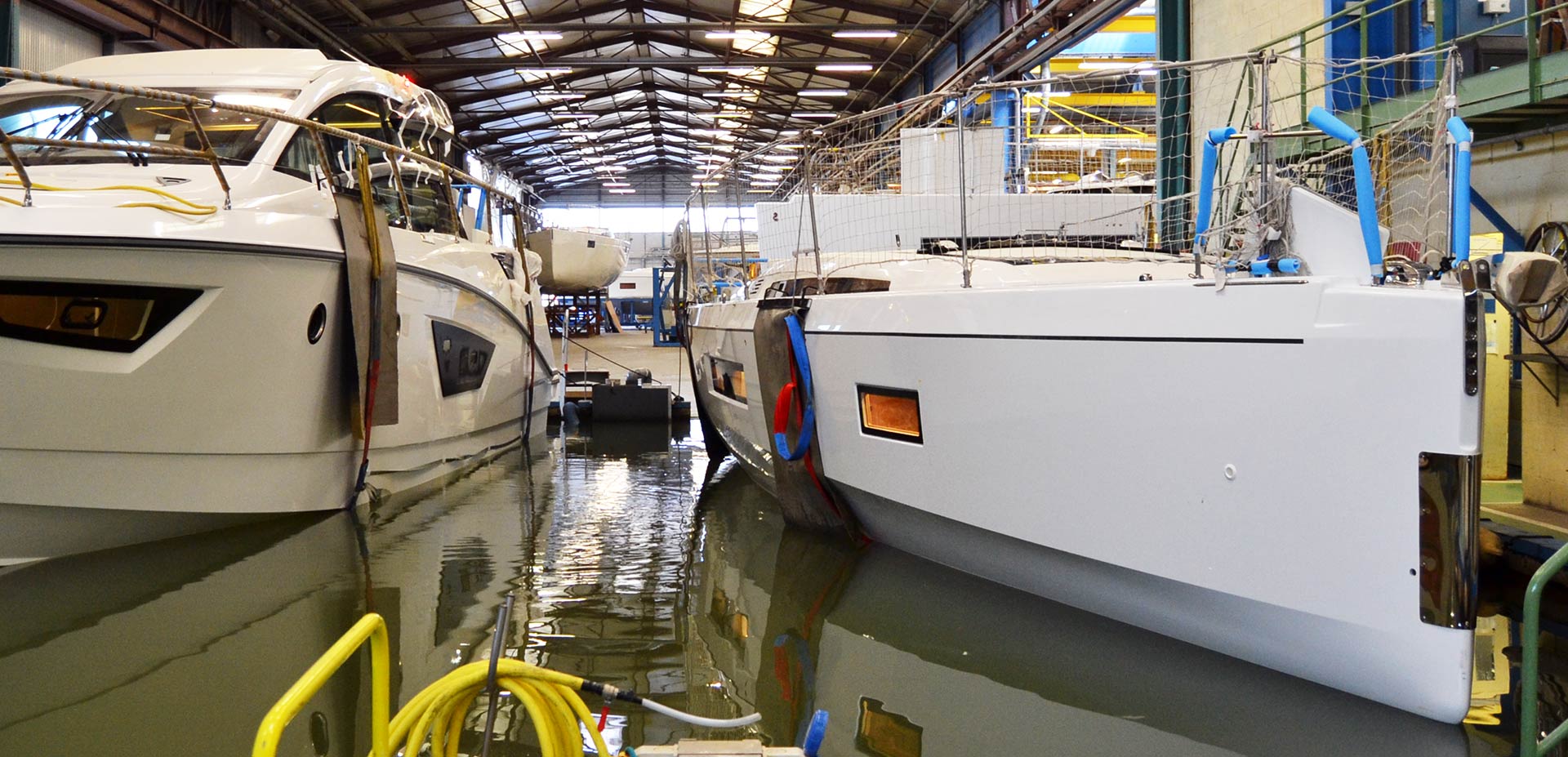
Depending on the order and the place where the boat is to delivered to, as one of the last steps in production is the fitting of the keel. Large boats won´t have a keel attached anyway as the heavy duty trucks won´t be able to cross below bridges. Beneteau, this I learn, is one of not too many companies delivering fully painted and coated – which is an important thing as cast iron keels may take on rust just before being attached to the yacht.
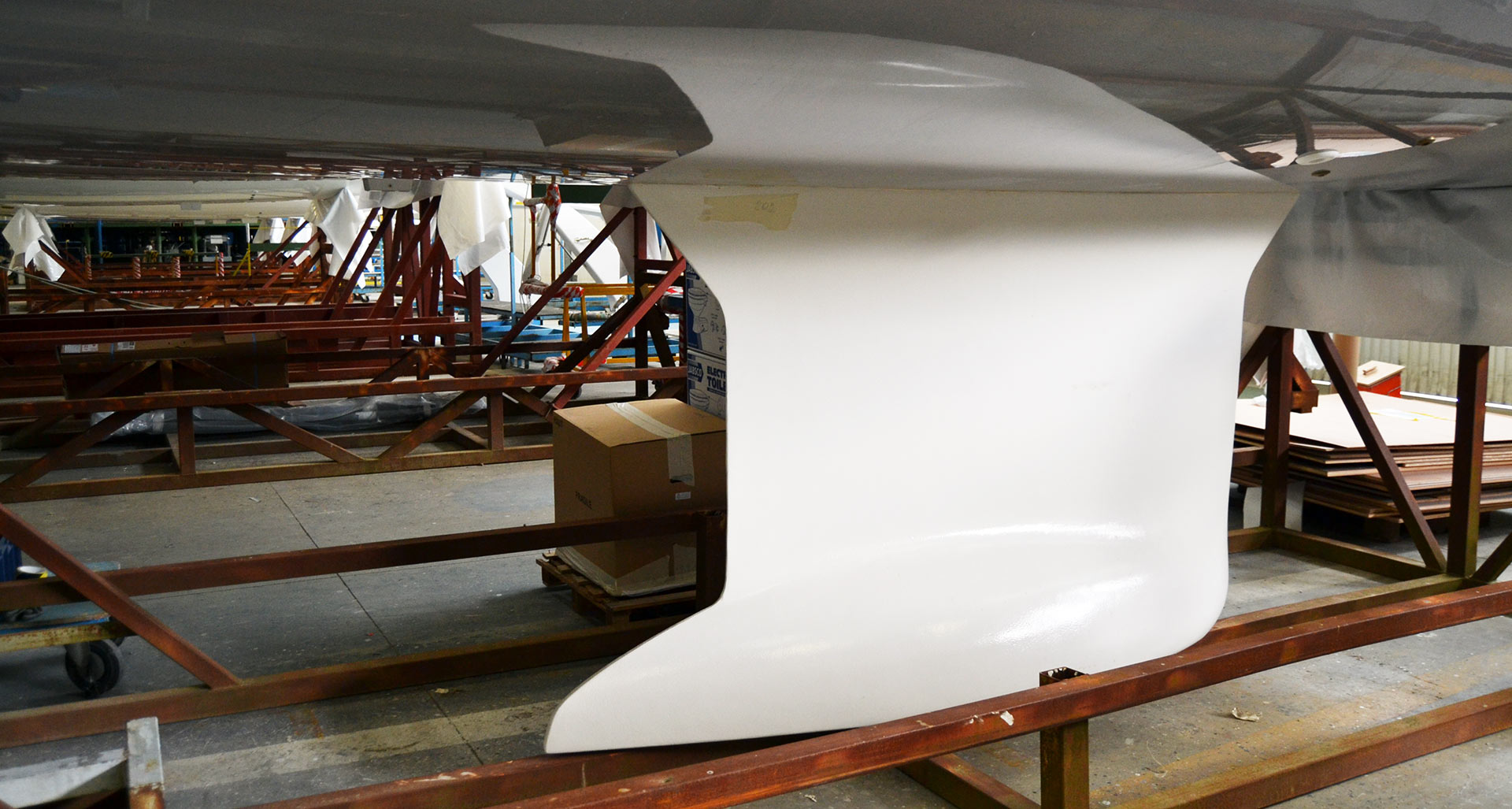
After the final deliveries had been made, like cushion, sprayhood and alike, naming the full basic equipment have been brought to the now completely finished boat, it will be wrapped in thick plastic foild by the help of a heat gun. Now the boat is practically completely covered and can either be stored for weeks and months to go or be sent on her first long voyage to be delivered to every corner of Europe by truck load. Only a few boats nowadays are sent straight from the yard into the seas to be taken on by their new owners.
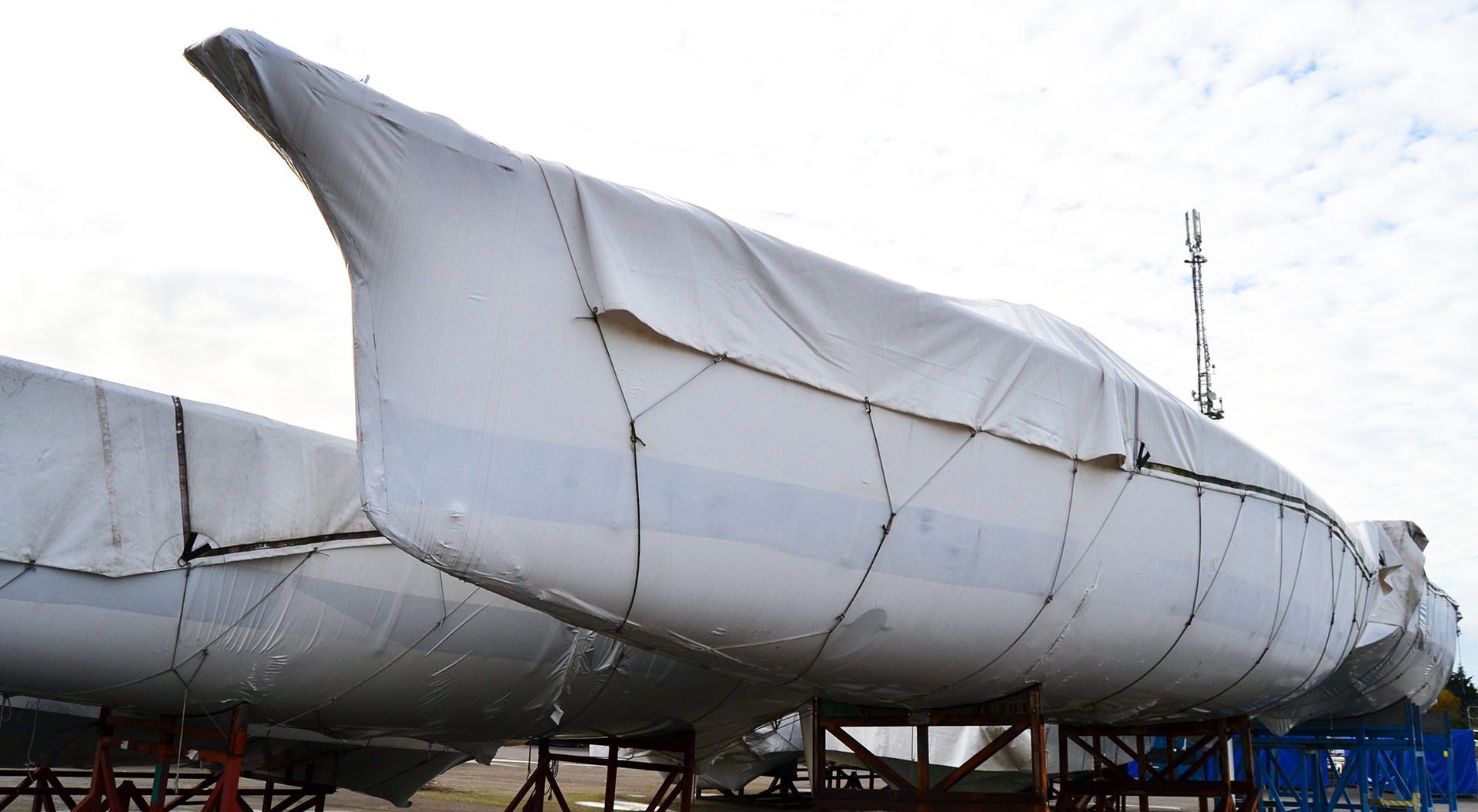
This is how my visit to the production facility of Beneteau ends. To see the new Oceanis 51.1 been made offered me some interesting new aspects and insights to this fascinating yacht. It had also been some interesting hours to see how the market leader in production boats is organizing the production here in contrast to other yards I´ve seen so far (read here about X-Yachts, Luffe, RM Yachts and Dufour). I leave France with fresh pictures and stories to tell – and I pity so much that the sailing season is over now and I don´t have any chance to sail one of the 51.1´s in the near future.
How does she sail?
In the end, for me as a passionate sailor, internal space isn´t too much counting. I see that there is a rather big market for voluminous boats and that the big production boat brands are reacting accordingly. What will make the difference is the performance of these boats when under sails: Preferably on every single point of sail and both under light and heavy wind conditions. As far as referring to the sailing magazines, her sailing abilities are great. But who knows …
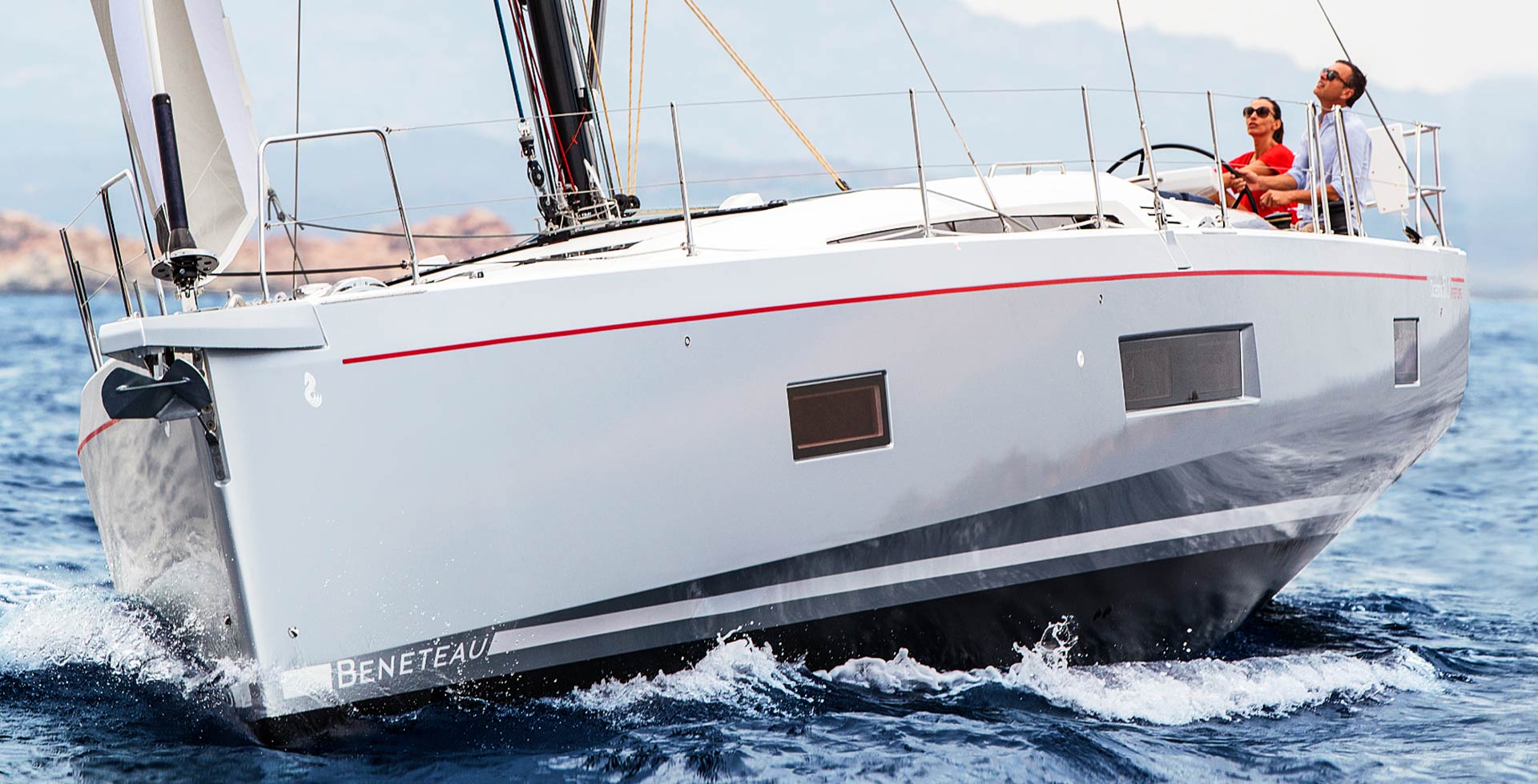
In the end, the new Beneteau 51.1 is indeed a huge success for the yard – besides the fact that the boat hast just been available for a couple of weeks now, all production slots are virtually sold out for the coming year 2018. I say goodbye to hull number 005 floating in the testing pool, shake the hands of so many friendly and open Beneteau workers and return home, still one more dream added to my ever growing library of yachts to-be-sailed.
You may also like to read these articles of the same topic:
Interior design concepts in cruising yachts as seen on BOOT boat show Düsseldorf 2017, Part 1 and 2
Visiting the Luffe Yard in Denmark
More than a detail – on the chines of the Oceanis 51.1