Last week I received a big package and the excitement was high: The new steering wheels arrived! The parcel was sent by Carbonautica, manufacturer and market leader in composite steering wheels, a much appreciated detail on so many boats and yachts. I unboxed the wheels and it felt so good to hold the first part of my new boat in my hands, and with those wheels, one of the most deciding and most used parts all over. Without her wheels, a yacht is lost.
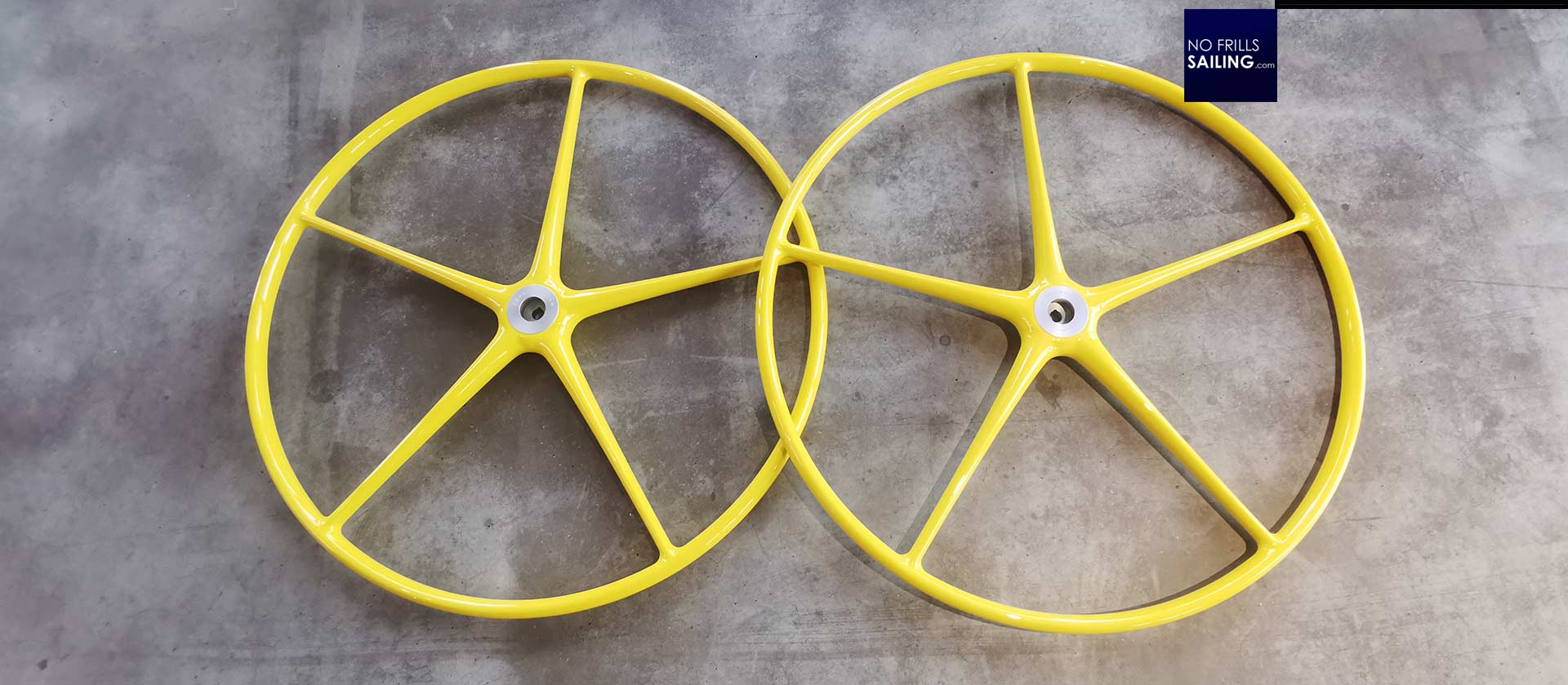
Absolutely amazed by the friendliness and openness by the company when I emailed them my custom wish, amazed also by the speed at which my whole purchase was processed and my wheels got finally produced, I decided to ask for more insight into the production of these great products and I am happy the guys responded and sent some pictures I would be allowed to use. Of course, not every secret to their fine quality is about to be blown, nevertheless, an interesting insight.
Monocoque composite steering wheels: A Slovenian specialty
Around two decades ago it became sort of fashionable to have a composite steering wheel on one´s yacht. Up until then these fine handcrafted items had been hugely expensive accessories limited to potent owners of already staggeringly expensive one-offs. Slovenian company Carbonautica was founded in 1998, as with everything, their original occupation had been the manufacture of carbon parts for racebikes or helicopters. First orders of the marine industry came in and so one company´s branch began to specialize in making steering wheels.
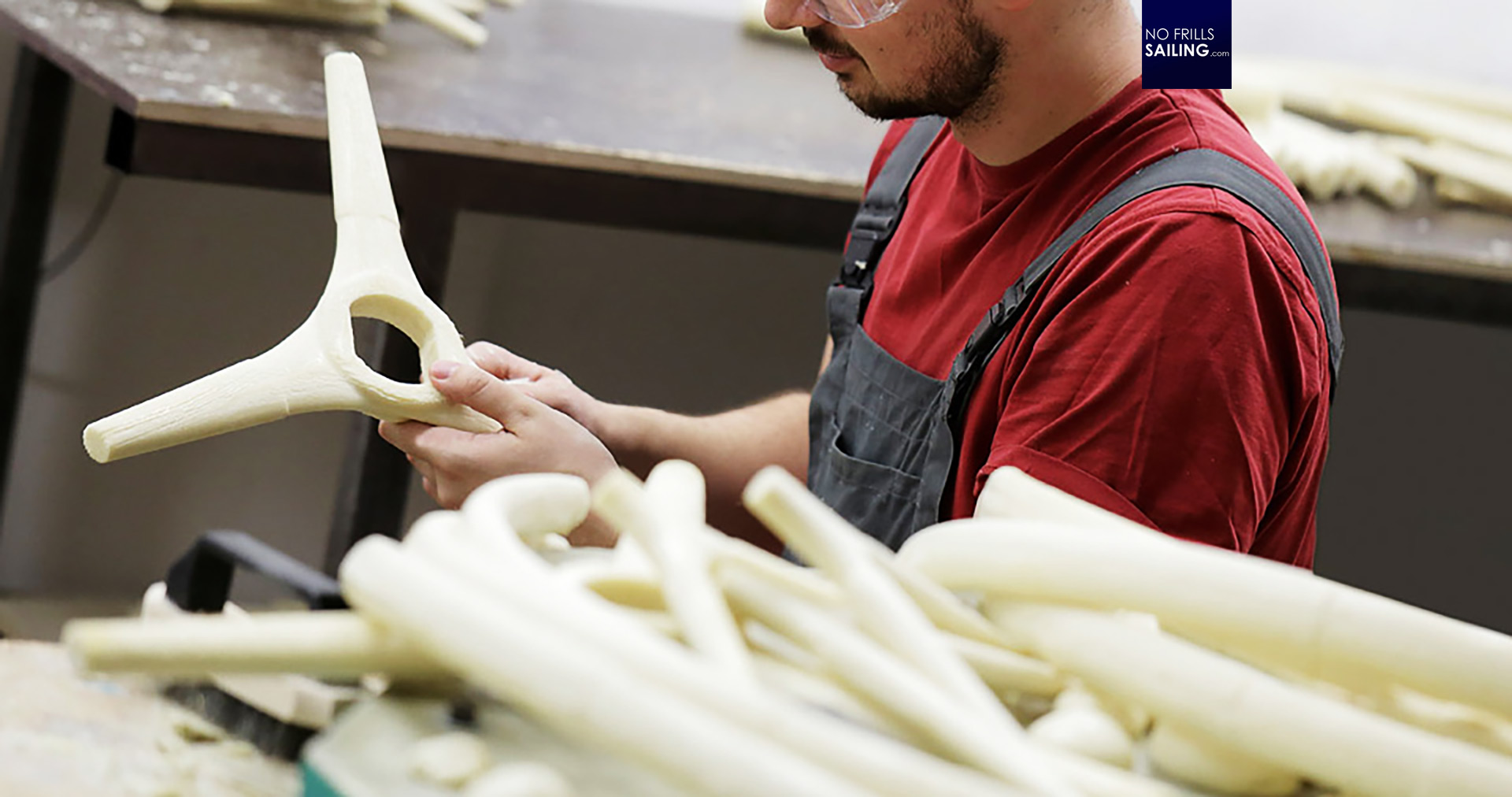
Those wheels are monocoque quality, which means they are made to be one solid single piece. This is important to get the strength and resistance needed for a part that is used so frequently and shall be able to withstand not only strong mechanical forces, but also steep variations of temperature, intense UV-radiation by the sun and all other forces of nature. It all starts with a CNC-milled foam core, which consists of the central part, the spokes, the joints and the round wheel grip itself.
Carbon of Glassfiber?
These parts are fitted with the raw glassfiber or carbon garments. As with almost every production step in yacht making, this is also all handcrafted by people. These parts are then assembled and brought together to make out the steering wheel itself.
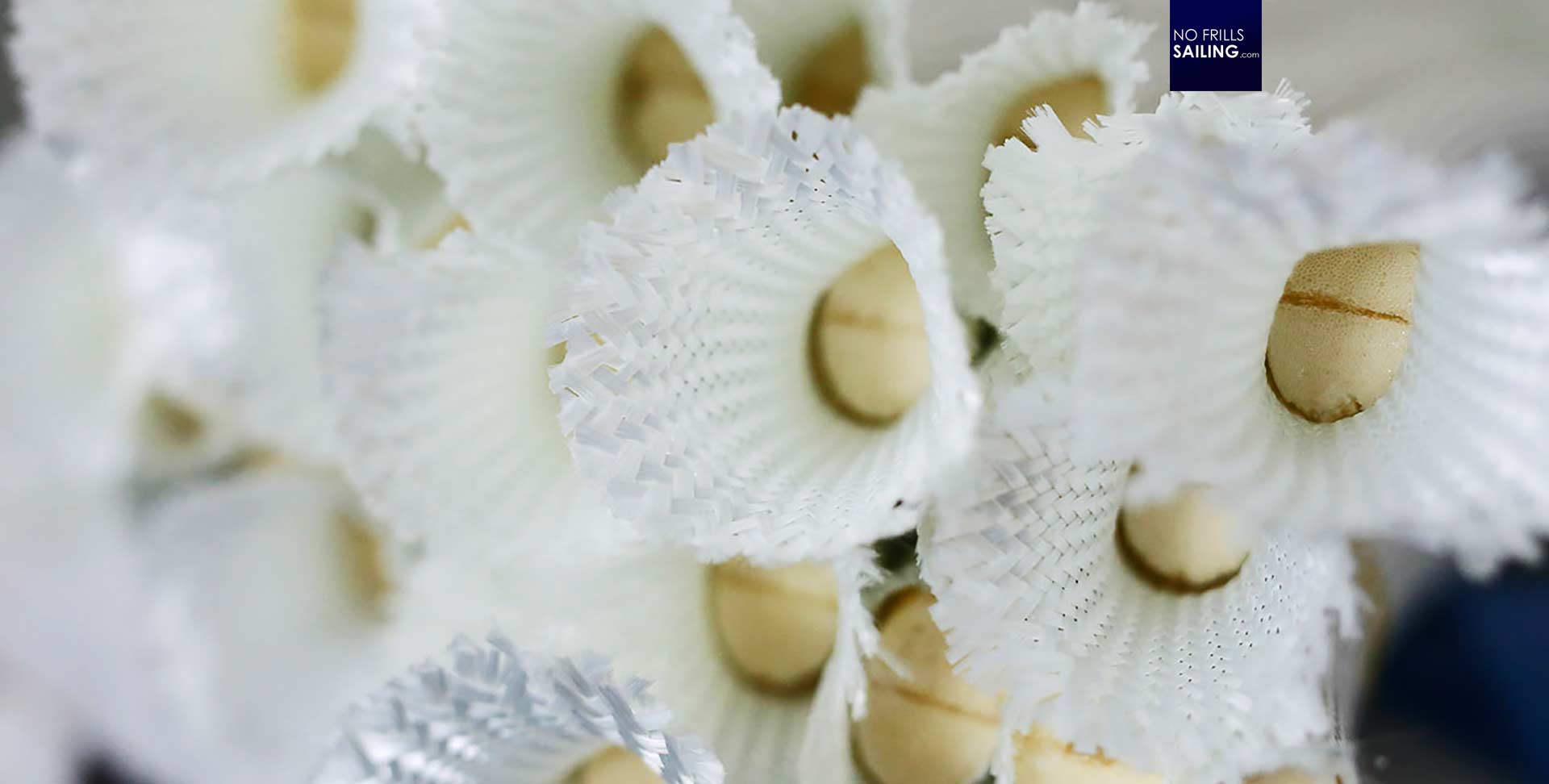
As with everything, the clients, which are for the most part yards, can choose from a wide range of diameters so to fit small yachts as well as bigger boats, and a number of designs. Of which the 3-spoke and the 5-spoke wheels are the most common. The more traditional design is the straight 5-spoke wheel, more performance-oriented boats will mostly be equipped with a 3-spoke Y-joint wheel, such as the new First 36, which is my new boat.
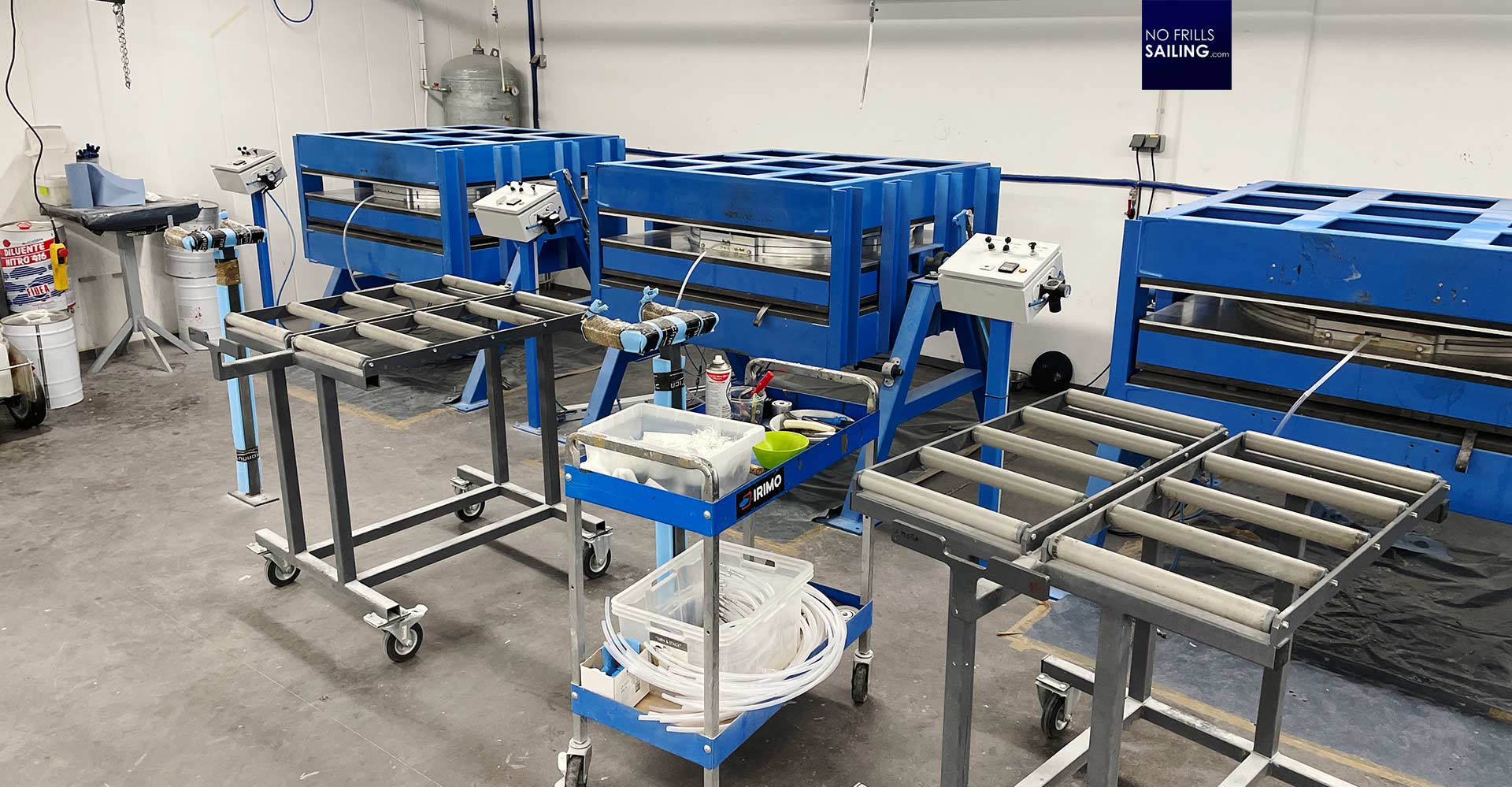
Depending on how much budget the clients want to spend – a single small-sized GRP-wheel will clock in at some 1.000 € each – you may choose between carbon or glassfiber. Depending which material, the raw wheels will now either enter the vacuum infusion production line or be brought to the conclave, the oven in which the carbon will be baked.
Fad or feature?
Either way, when finishing infusion or baking time, the raw wheels will be peeled out of the moulds and brought to the storage. Carbonautica holds a number of raw wheels in stock ready for further refinement, production never really stops. So, why should a skipper opt for a composite wheel? Isn´t this just one another way to draw money out of the pockets? Well, I don´t thinks so, it is much more than just a fashion statement.
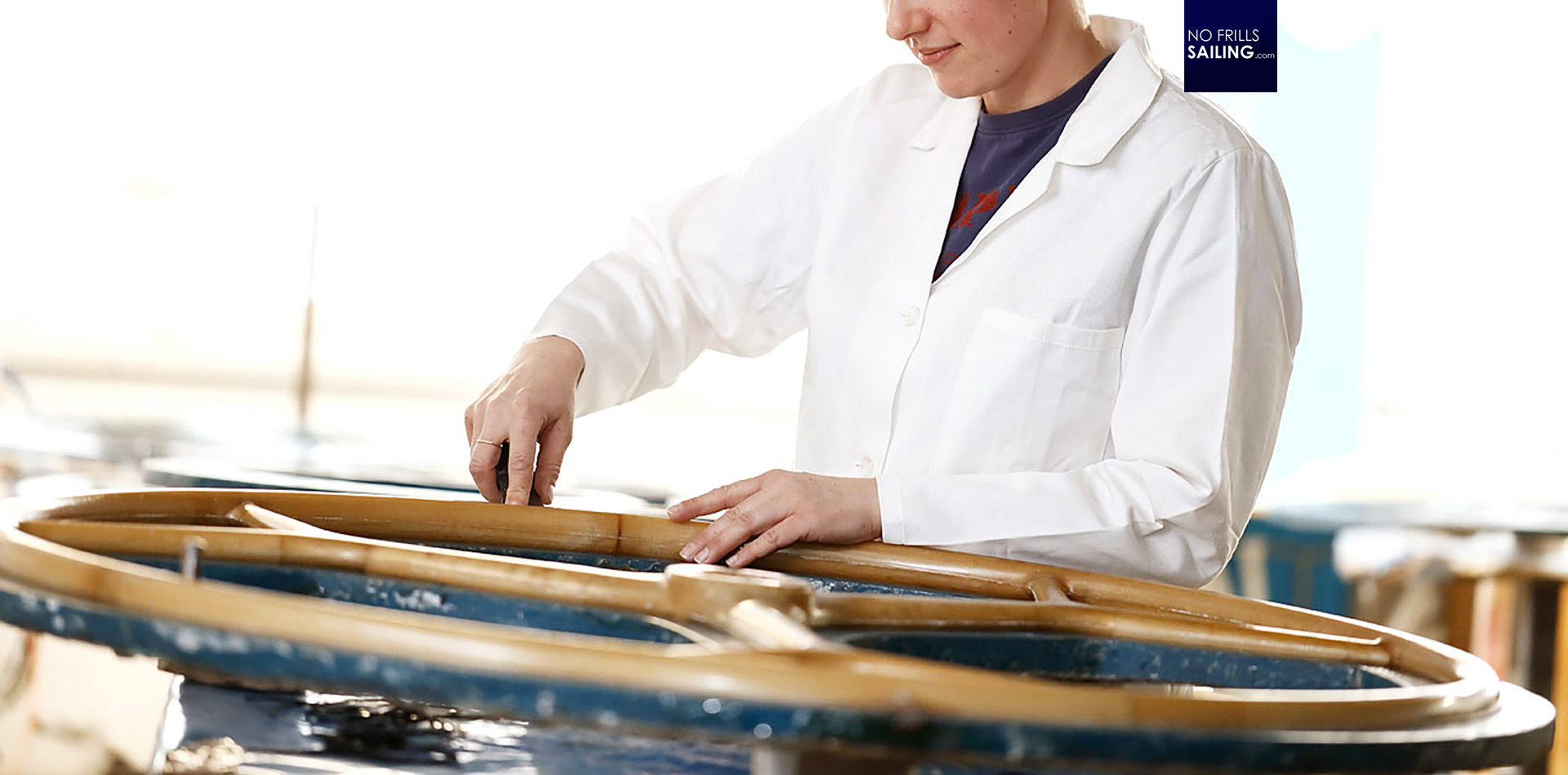
I´ve been sailing standard steel-wheels and composite wheels ever since and the difference is instantly noticeable. Due to the absolute lightweight properties of the composite wheels compared to the hefty weight of a standard steel-wheel, the initial power needed to set the wheel in motion and thus turn the rudders is much less. You really feel how smooth running your rudders have become. Secondly, when spinning, inertia generated by rotating wheels is much less than with a steel-wheel – in essence, being at the helm constantly turning the wheel will be much, much less tiring with composite.
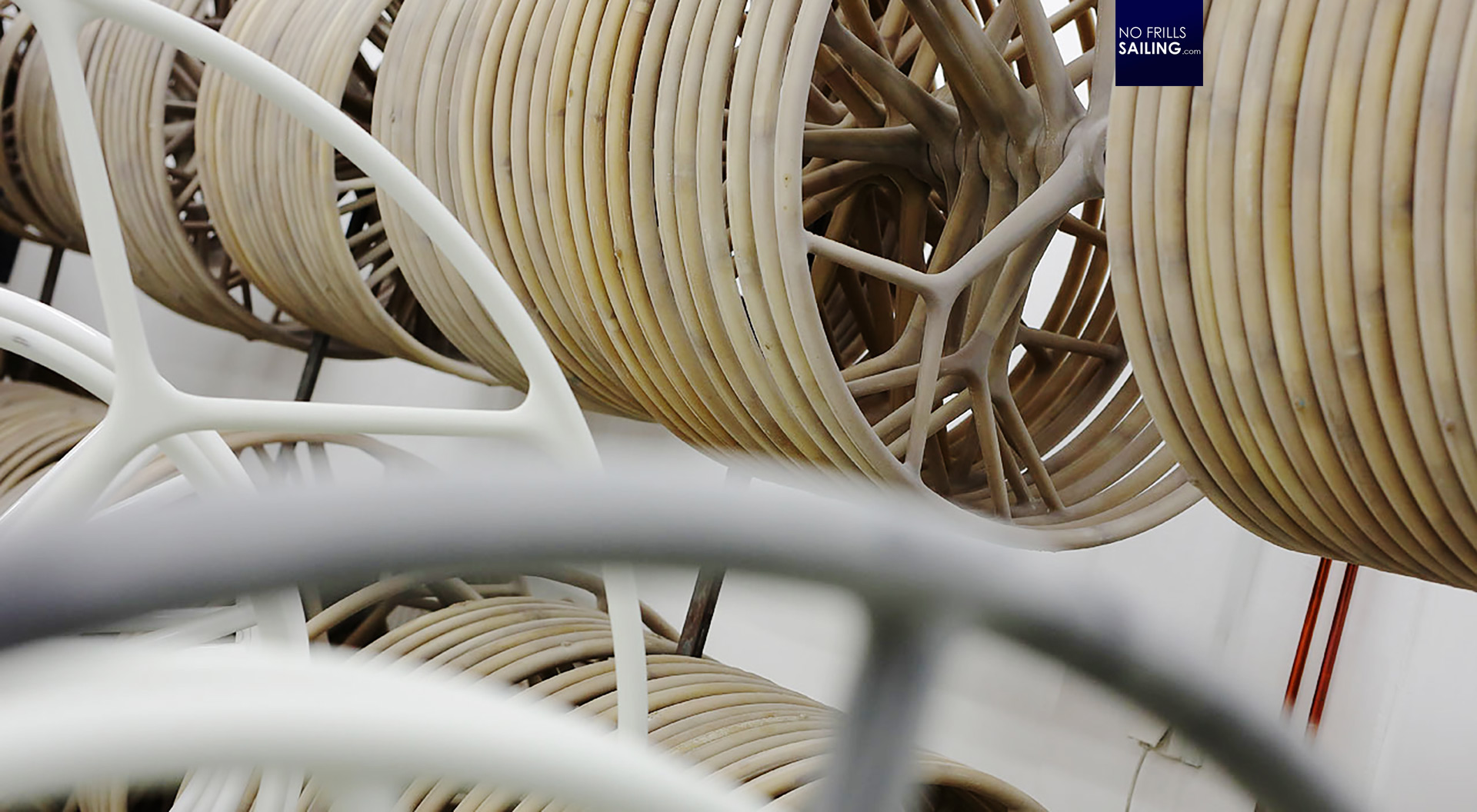
I also noticed that composite wheels feel much better when grabbed with bare hands. The material takes only a few seconds to get to hand-temperature, which is especially in colder times a real plus. Steel will keep its cold, freezing temperatures much longer and kind of radiate the minus-degrees into your fingers. I´d say a composite wheel thus combines beauty and real practicality.
Why I chose a composite steering wheel
So, you might ask, if the First 36 comes with a composite steering wheel already, why order them anyway? You might try to check out the article about how I found the name of my new boat to understand better. The new boat will be named LIMÓN. As such, the main “theme” of the boat, the spirit, will be the juicy, tasty, fresh lemon. (I know, many have notified me about the rather unluck connotation of “receiving a lemon” in American and UK-English, but that is why the name is written in Spanish). Anyway, back to LIMÓN …
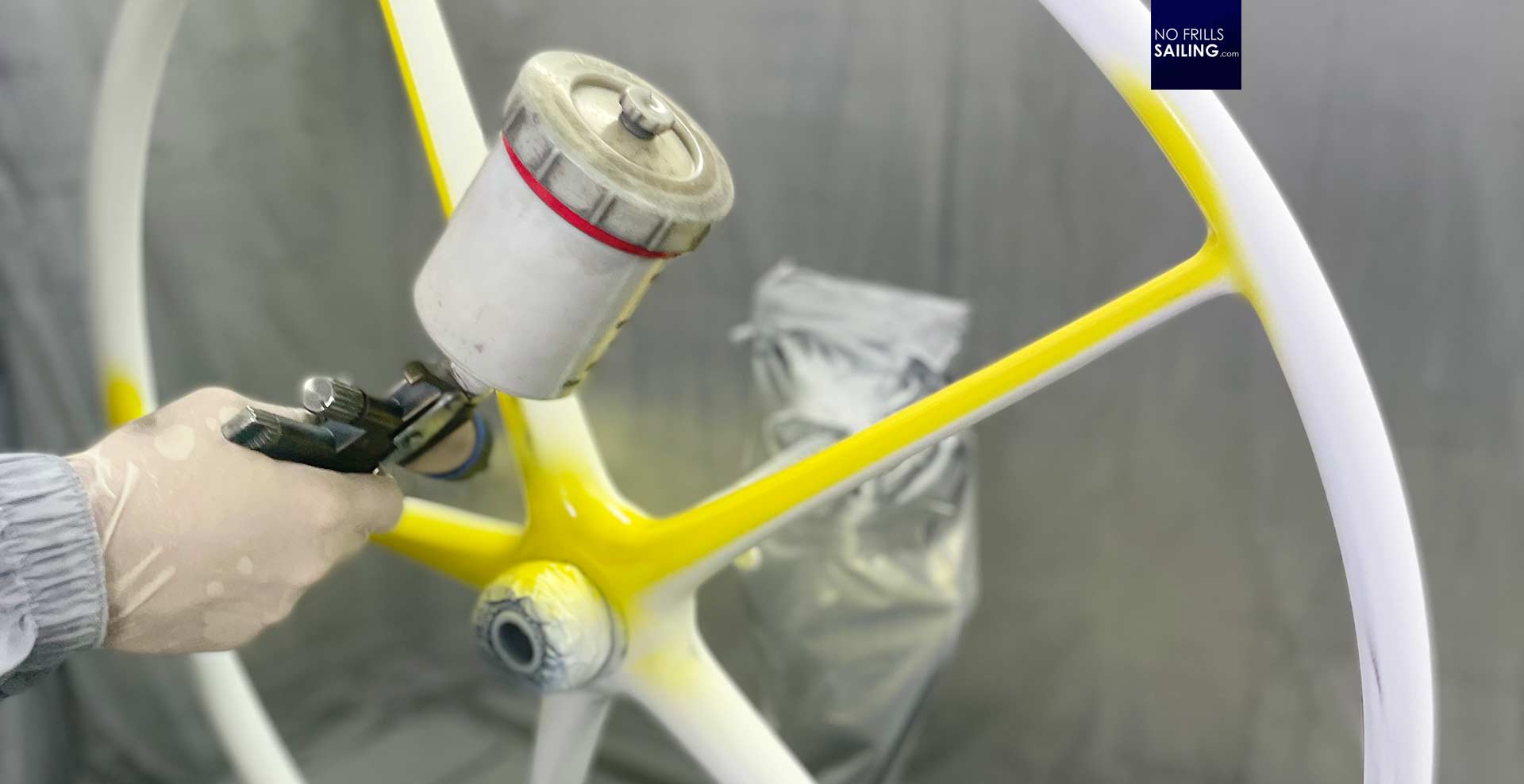
Seascape will go for the sporty 3-spoke Y-joint wheels in black. Those look awesome, for sure and are great on the boat. But for LIMÓN I thought if I could get the 5-spoke straight classic wheel and have s custom painted in LIMÓN-yellow, those could be looking like a two slices of lemon. Combined with the nicely done name on the transom and the yellow waterline stripes, this would add to the overall-design idea.
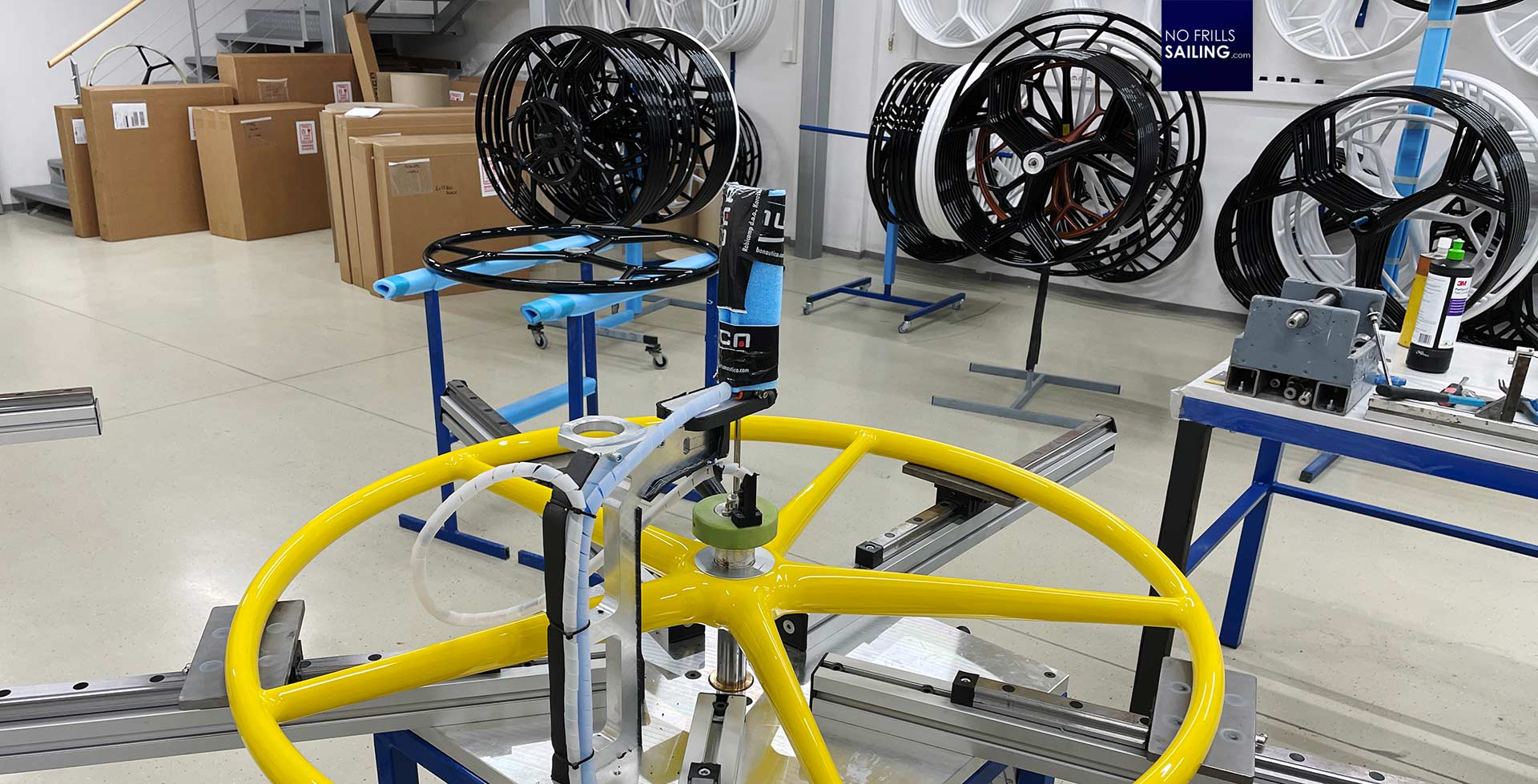
And this is how I ended up contacting Carbonautica, who instantly agreed on taking on the job. I was to send the RAL-code of the yellow that I chose and only a few days later I received not just the fantastic looking steering wheels but also pictures taken in the production from the guy who diligently spray painted the wheels and covered them in a shiny glossy-paint layer. Those wheels are now the center of my living-room decoration back in Luebeck – and you bet, I count the days I could back them back into the big box to take them to Slovenia, putting them on to the boat itself.
A nice selection of related interesting articles:
Hooray to Slovenia!
At Seascape yard in Slovenia
How it´s made: A life jacket