Sustainability, ecological awareness, the reduction of footprints or the new „green“ and „blue“ technologies are huge topics in the boatbuilding industry. I´ve covered some efforts, may they big or small already. It´s not only a matter of political and societal pressure, but a matter of consent that the reduction of waste, the use of energy and precious resources should be common practice nowadays. Trying to separate pure greenwashing from serious approaches and real game-changers is not easy: The marketing industry is as busy as usual to cover up for all too lazy of half-hearted projects, helping their clients to paint a nice picture. Anyway, there indeed are cool projects everywhere, as I found out a few days ago.
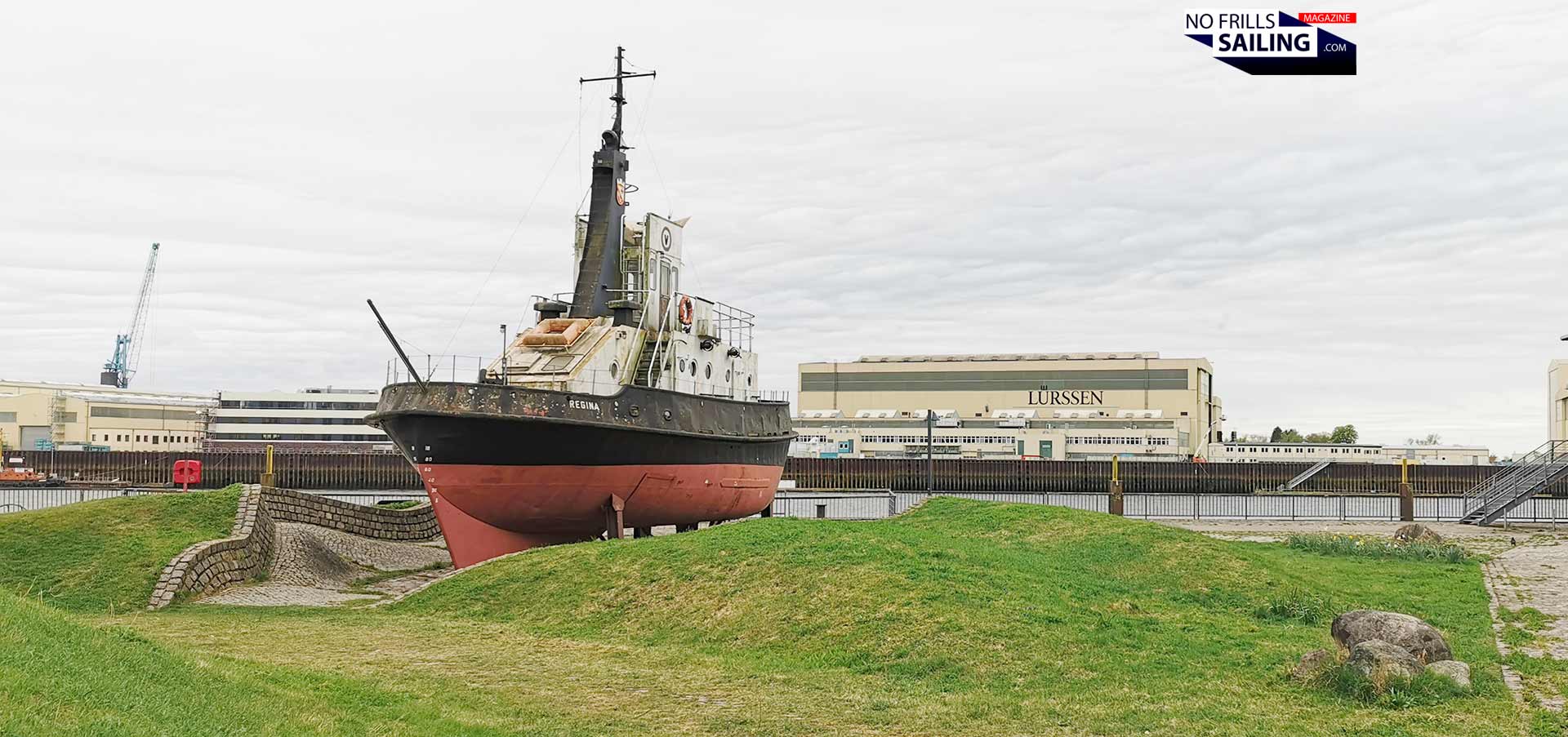
Bremen is one of Germany´s top addresses for maritime industry. Together with its sister-town of Bremerhaven it operates one of the busiest deep water ports of Germany, is a major hub for heavy industry products, especially wind turbines, and still has a vivid scene of commercial shipyards. One of the prime addresses of Bremen is the world famous Lürssen shipyards which has its headquarter here at the river Weser. Directly vis-a-vis, on the premises of former Vulcan shipyards (where during World War 2 U-Boats had been built), a relatively young company found perfect conditions to start something that could change boatbuilding for good. Tesumo promises no less than a full replacement of Teak as deck material.
From patent to full scale production: Tesumo´s rise
Supplanting teak in boatbuilding is a big thing. Many materials are proposed, ranging from synthetic PVC-based „plastic“ decks to real wood (like Iroko or alternative natural materials, like Cork. Utilizing teak from Myanmar– although the best material for being utilized in the harsh maritime environment on boats – is forbidden and under sanctions since years. Tesumo, the young company in Bremen, has found a way to offer a completely similar looking, similar behaving, similar feeling product that could substitute teak once and for all. As I arrive at the production facility in Bremen, I am greeted by the company´s Managing Director, Arne Petersen.
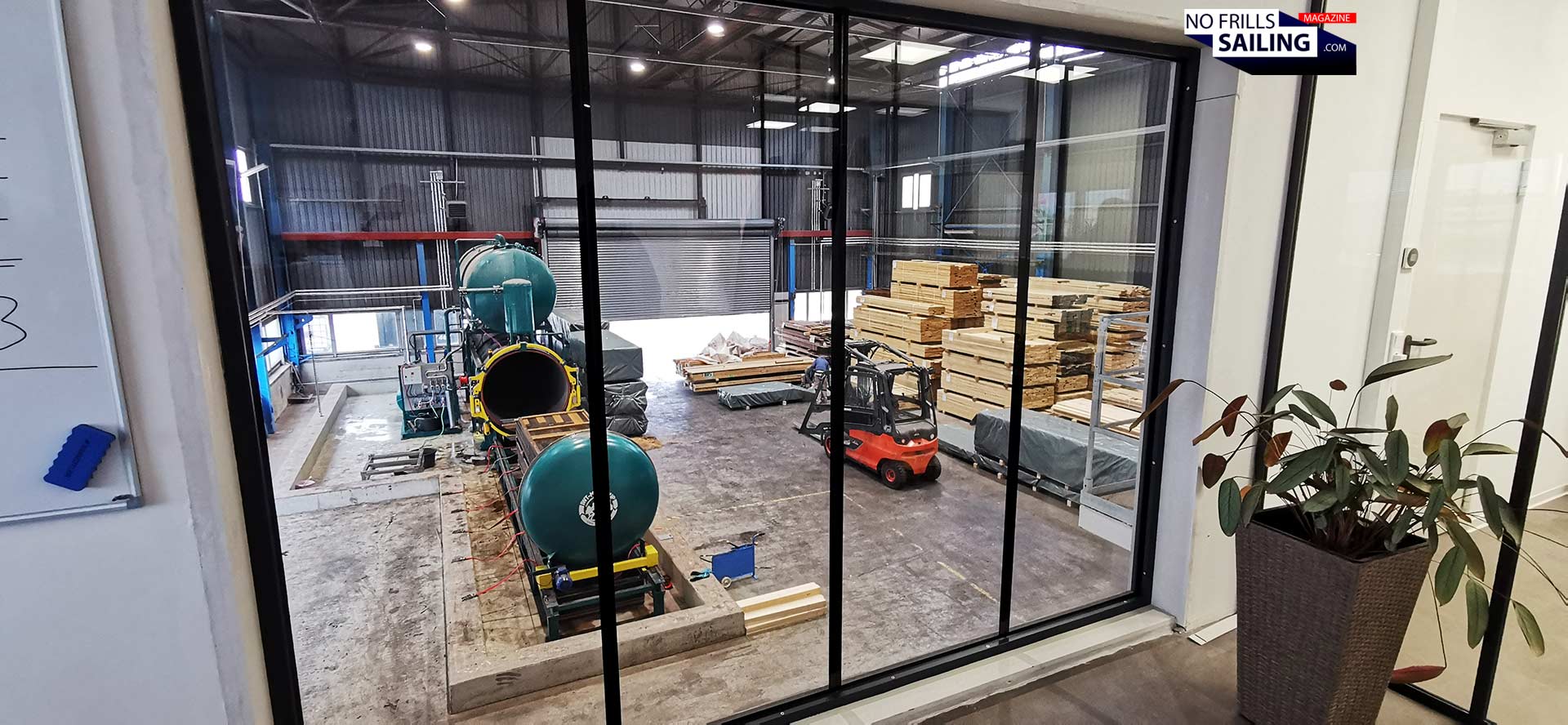
We enter a steep staircase to the office level, and I can see through a large panoramic glass window into the hall. It´s a repurposed construction hall of the former Vulcan shipyard, elaborately refurbished, insulated and fireproofed to adhere to modern-day safety regulations. Down there I can see huge piles of timber. People are bustling, a heavy forklift drives around, carrying palettes of wooden planks from A to B. I sit down with Arne to get a proper briefing on what´s happening here.
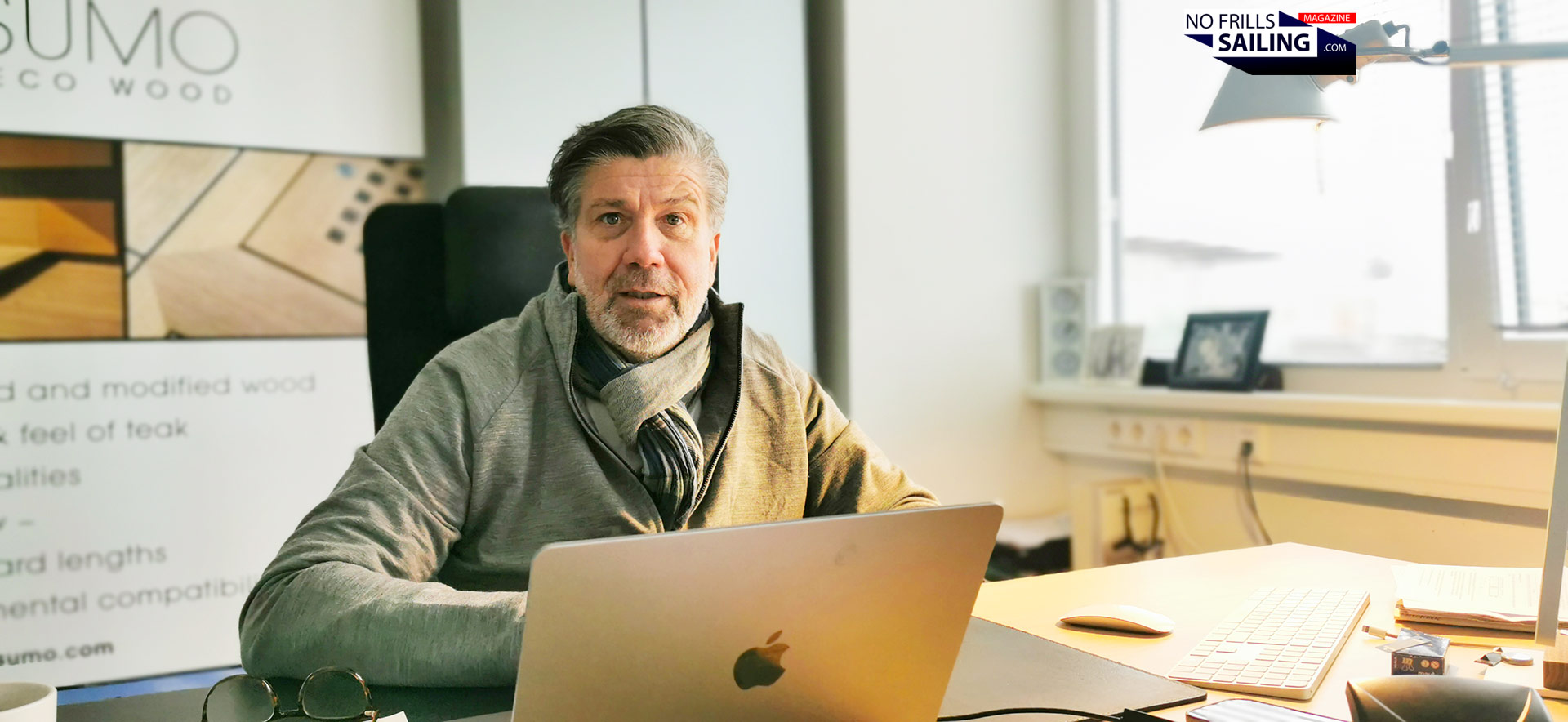
Arne Petersen had joined the company only a few months earlier. He is indeed no stranger to the boating business: Having worked in the boating industry for the past 24 years, he had run his own yacht dealership up until he joined Tesumo. Arne is a keen sailor as well: Having won the last „real“ X-99 World Championship or the second place in the Worlds for the 3/4 ton class, he knows what it is all about. Being a licensed dealer for renown Swedish brand Arcona Yachts, selling luxury goods is in his blood. You have to know this to understand the following: Introducing a new product to the boating business is not an easy task, having someone that experienced at the helm surely a plus for the 1.5 years old company Tesumo. So, what´s their thing?
What is Tesumo?
Basically, the name „Tesumo“ is derived from „Terminalia superba“, the scientific name for limba wood. As the company had found out, the timber of this Central African tree is perfect for their patented process that turns it into „teak“. Limba, as we call it in Europe, grows naturally in professionally managed and, as he ascertains, OLB-certified forests mainly in Ghana and the Ivory Coast. This may raise some concern, and rightly so. But Arne assures me that his company only sources legally cut, officially certified timber, like FSC. As there is an embargo to import roundwood (mainly to keep a higher margin of the value-chain in the producing countries), Tesumo works closely together with a Belgian importer, making sure that the arriving planks are not only „clean“, but also of the highest quality.
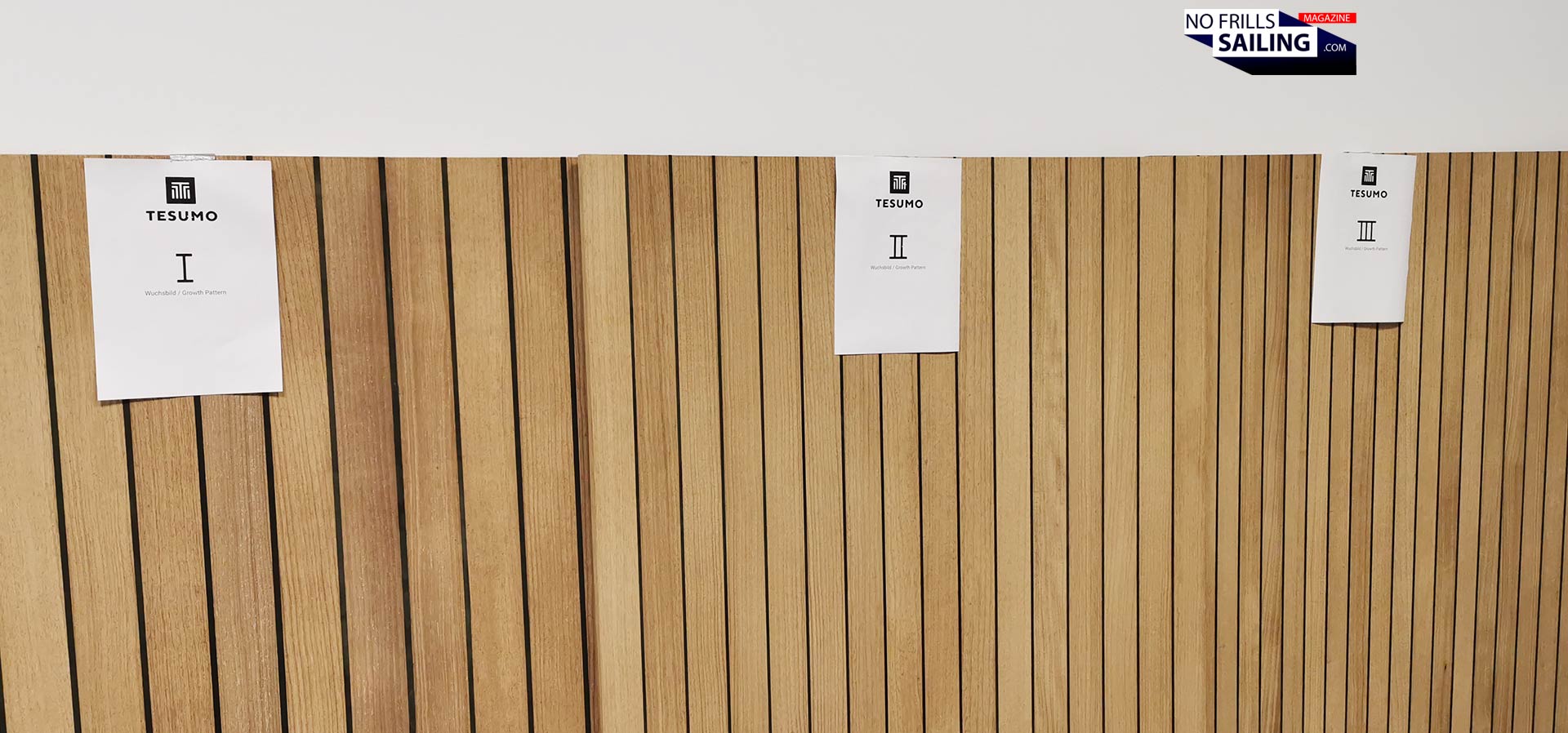
Speaking of which: Tesumo is offered in three such quality levels. First level, the prime cut if you will, is absolutely spotless. This is what is later turned into the spotless yacht decks. Second and third quality levels could have minor to bigger irregularities or small growth-damage. These planks may be used on places aboard where no immediate or direct sight is granted, heavy-wear- or „hidden“ areas. Then there is a fourth category which bears bigger irregularities, major differences in grain, colors and growth damage. Although perfectly fine from a material standpoint, these planks cannot be used on yachts as no owner would accept them: They are perfect for natural facades and facings of houses. As Arne tells me, architects love Tesumo: Like Teak, it´s very durable, doesn´t rot and is perfectly fine to be used in buildings.
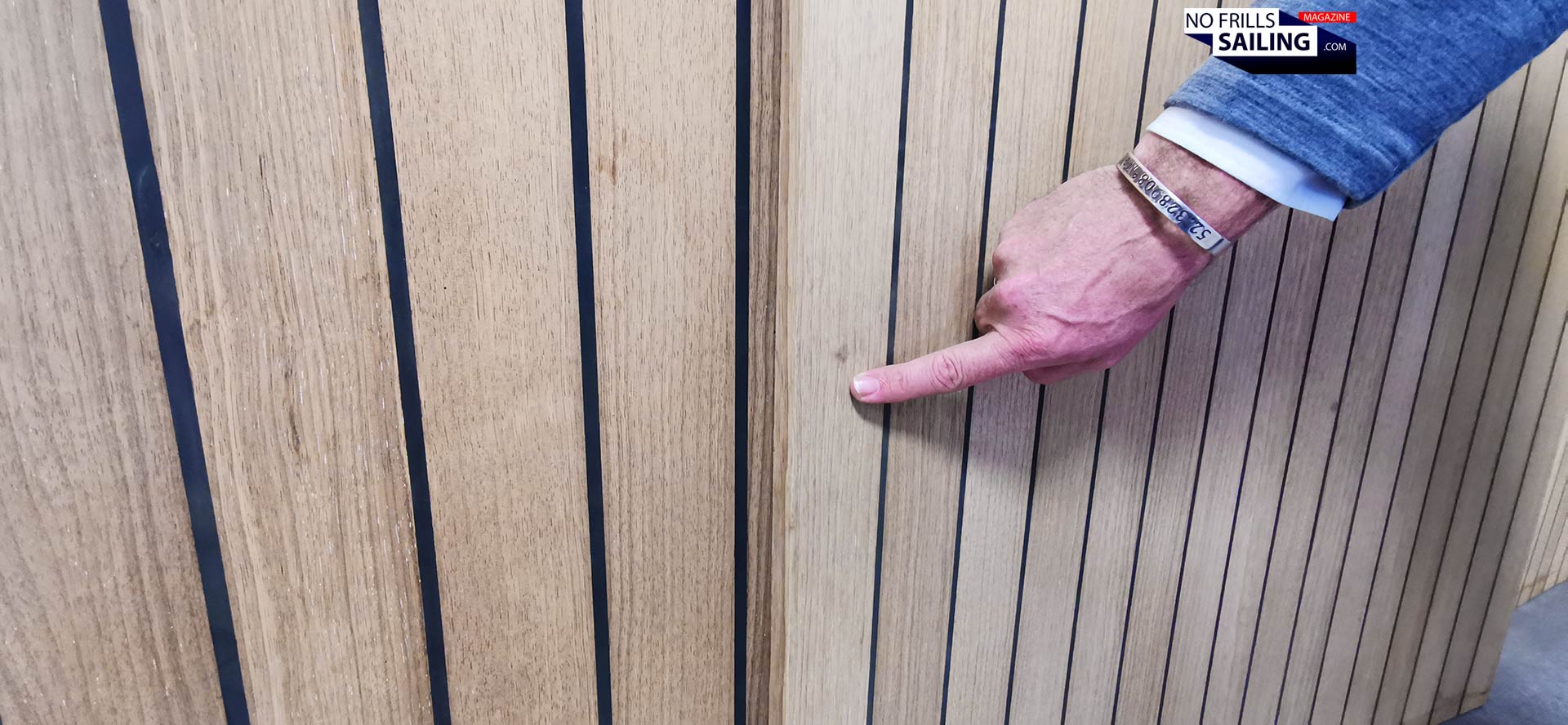
As I look very closely onto this material, hold t in my hands, even check the smell of it, honestly, I cannot find any difference from teak. Although the intense smell of fresh cut teak is indeed something very hard to copy, everything else, like the haptics, just feels like … well, teak. I can certainly spot the „irregularities“, now that Arne points out where to find them, but honestly: Even grade 3 Tesumo looks just as fine to me. It´s a very beautiful material. Where artificial plastic-based fake teak will always keep its synthetic looks, kind of an uncanny valley, having natural rain and the feel of the real is certainly a big plus for Tesumo. Now that I have seen the end product and know where the base material comes from, I am ready to see the production. Exciting!
From Limba to Tesumo
Tesumo is the result of the meticulous research by University of Göttingen, which still holds the patent on this material for all non-marine applications. Lürssen (and here the circle closes) financed part of the research and holds the marine patent for Tesumo. So, how is this new „Wonder-Teak“ made? Arriving by cargo ships in Belgium, the raw cut limba planks are thoroughly pre-checked. Only the best of them are shipped to Bremen. Arriving here at this huge hall, the skilled eyes of specially trained surveyors will put the planks under another scrutiny: A first assignment to different projects follows. Tesumo´s own joinery will do a first planing of each plank so that all potential irregularities can be seen.
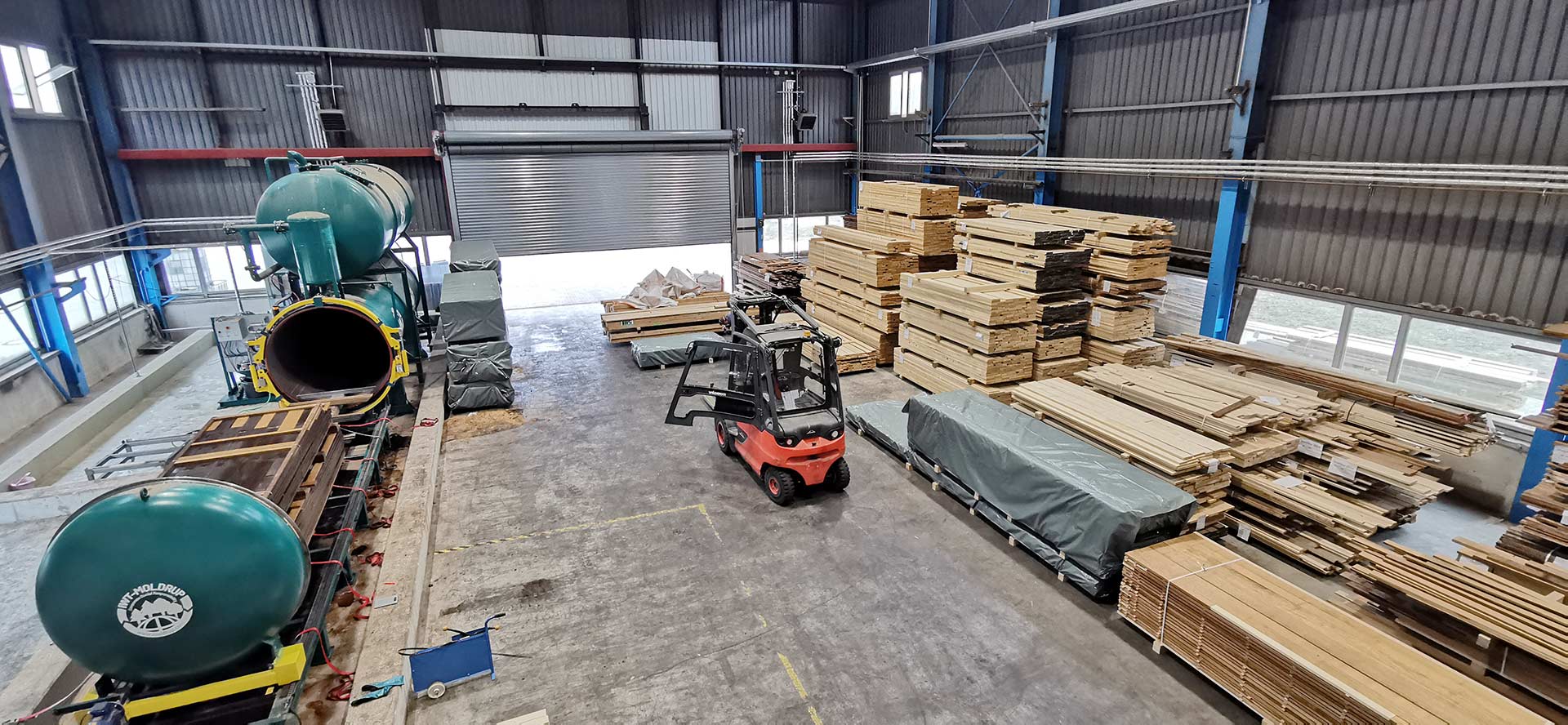
The planks will be sorted to so-called „process batches“, where each boat-project has its own batch or batches. Arne explains to me that each client orders a dedicated number of material, just to fit the area of the deck that needs to be covered. This could be just a small number of square meters for a mid-sized yacht or several batches for superyachts. Lürssen shipyards is one of the few world´s renown shipbuilders capable of constructing very, very large vessels. Dutch luxury boatbuilder Vitters is another client utilizing Tesumo. As a first step of the production, the planed raw limba undergoes a thermal processing.
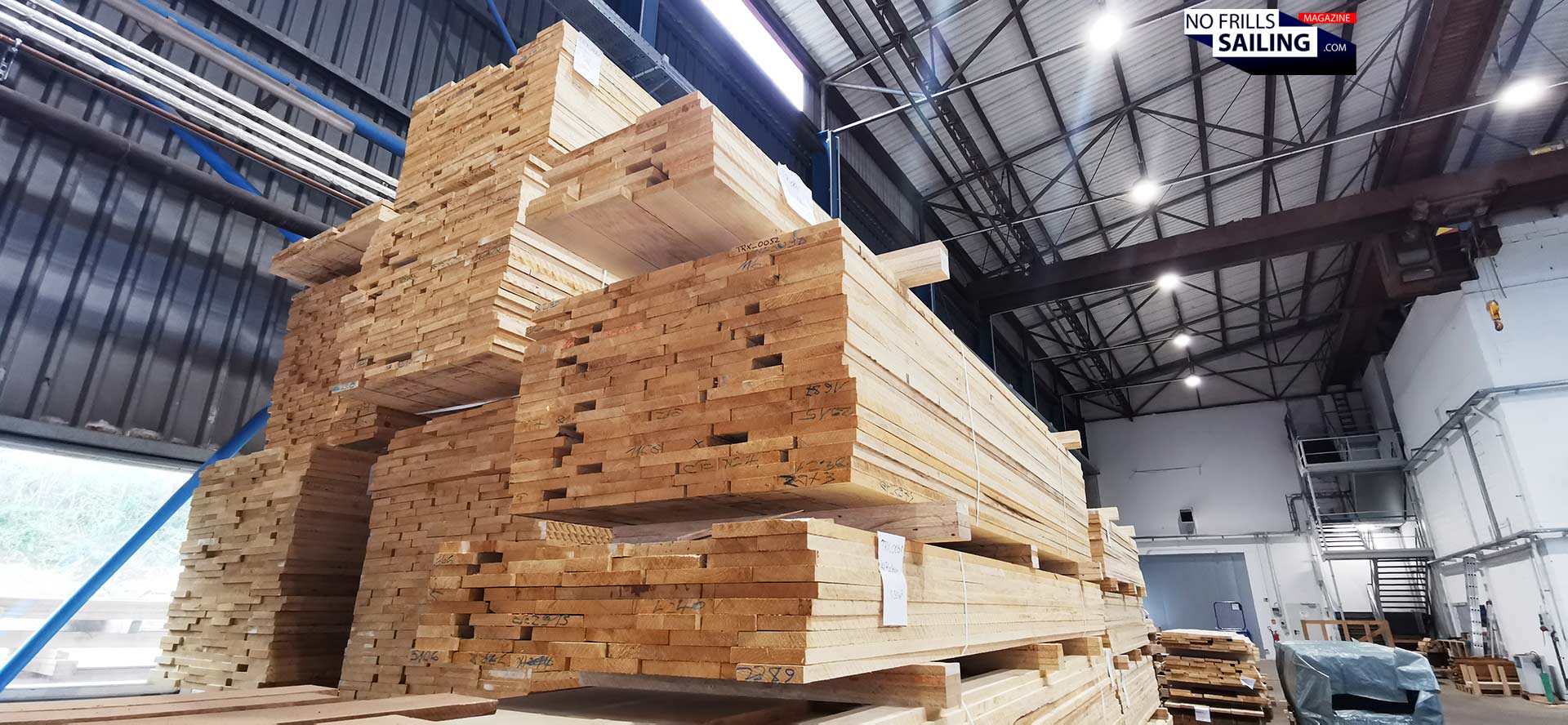
Where naturally dried timber often retains a 12 to 15 percent residual moisture. Arne says that this is too much for Tesumo productions and this is why the first thermal processing is done. In large autoclave the process batches are subjected to a specific, patent-protected process. Vacuum, temperatures of over 160 degrees Celsius and varying atmospheric pressures the batches remain in the autoclave for 2 to 3 days: Depending on many factors. After this first process, it´s called „Thermo-Limba“. Up until now it´s not really breaking news: Thermal modified timber is already a widely used material in house construction, especially in Finland and the Scandinavian countries.
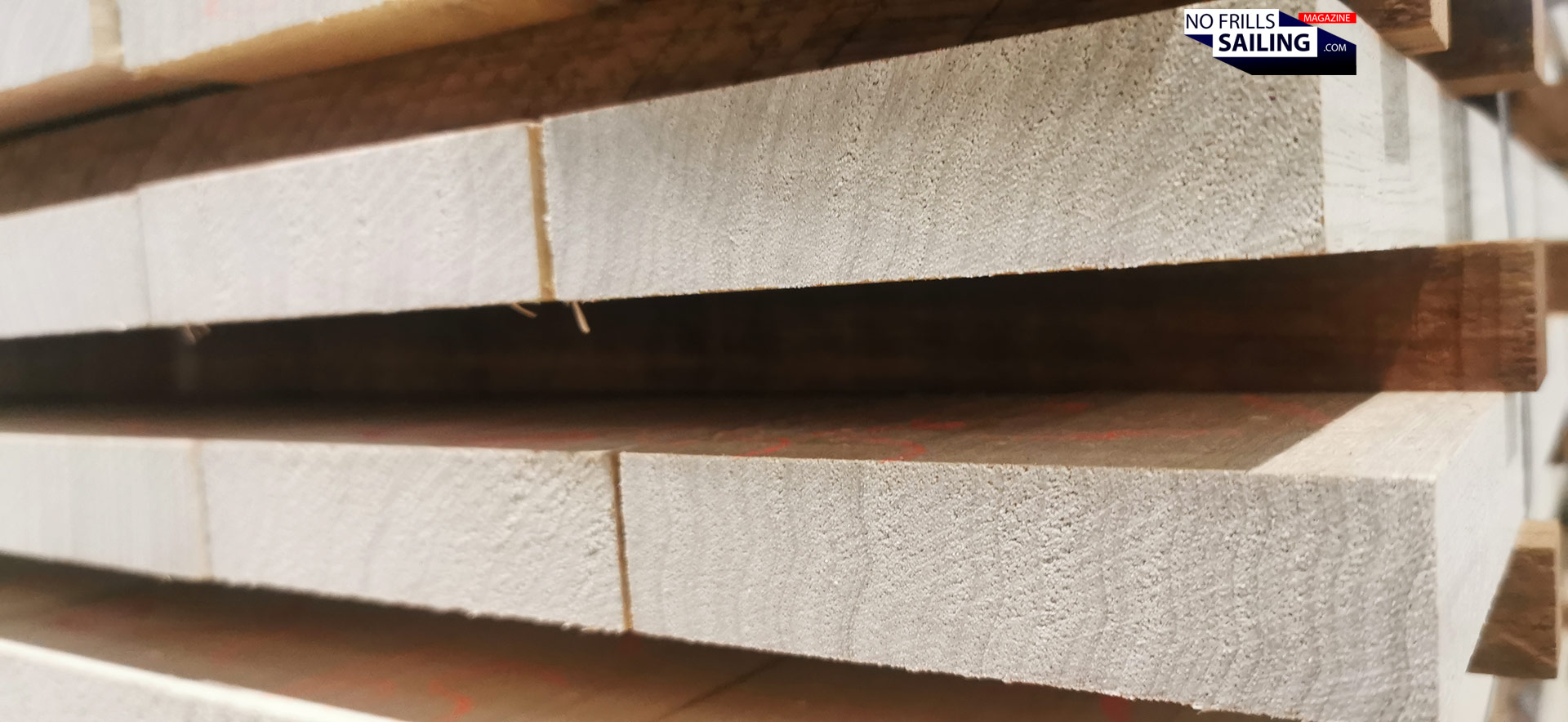
The batches are taken apart. Plank by plank. You guessed it already: Another quality check. As it is still a natural material and thus contains a wide variety of differences, each plank may or may not react slightly differently to the thermal treatment. The job of Tesumo´s surveyors is to sort out the worst and mark minor damages. Quality control is absolutely non-negotiable at Tesumo: No owner of a Lürssen built superyacht would accept a knothole in his deck!
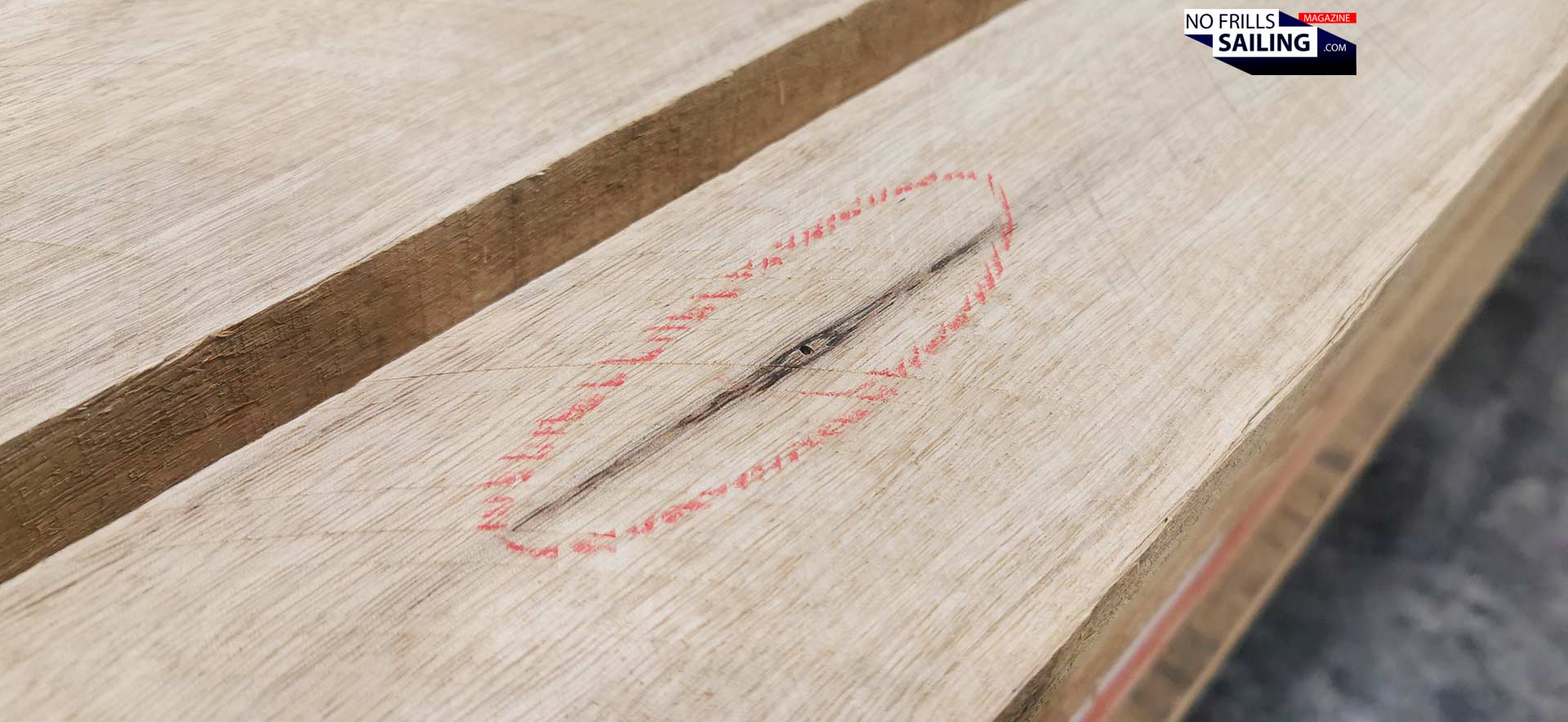
All planks, for example, must be cut in a specific way. This of course is done back in the producing country where the logs are treated in large lumber mills. Arne points out that the first sign of good quality is a „standing grain“. This means that the tree rings must have an upright direction in the cross-section of each plank. This hasn´t only aesthetical reasons: Standing grain ensures much of the rigidity and durability of a plank. Here I detect a very interesting detail in Tesumo´s code of conduct: The „control plank“.
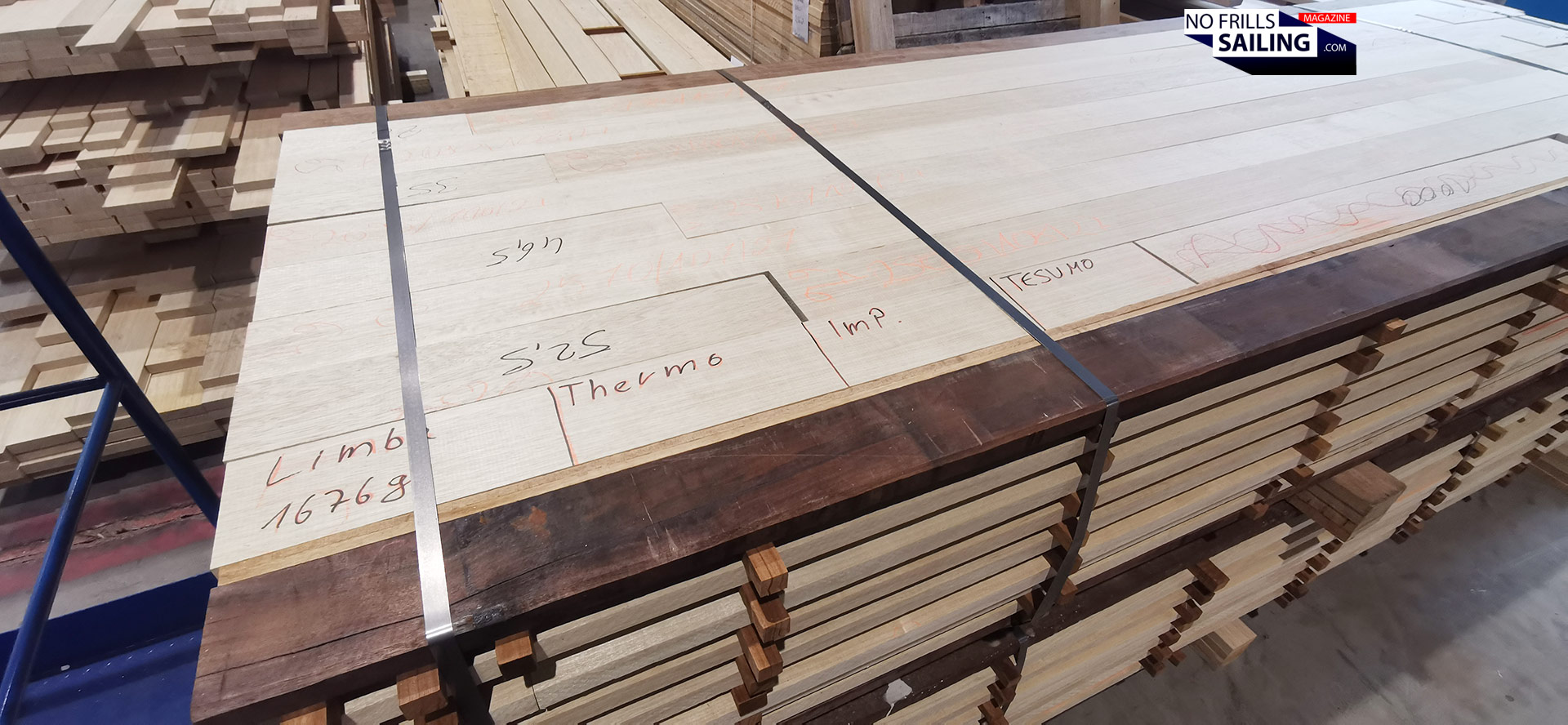
On top of a complete process batch an approximately one meter long plank is clearly marked. As Arne explains, this control plank goes through the whole production process of the complete batch. It is devided into four distinct areas: „Limba“, the raw planed timber; „Thermo“, after the first production step; „Imp“ for impregnated and „Tesumo“, after the process is fully completed. Keep this in mind, the control plank will surface now from time to time … for now, it is time for some awesome engineering!
Meet the „boiler“!
Upon arrival, when standing in front of the panoramic window overseeing the production hall, the defining element of Tesumo´s hall was this huge, green, double-tank monster. A purpose-made machine that will ultimately turn Limba into Tesumo. I am lucky to being able to witness this. Arne suggests not to breathe too much of the odors and stay away at a safe distance from the green monster: The workers put on breathing masks. A yellow caution light is switched on – we open the boiler!
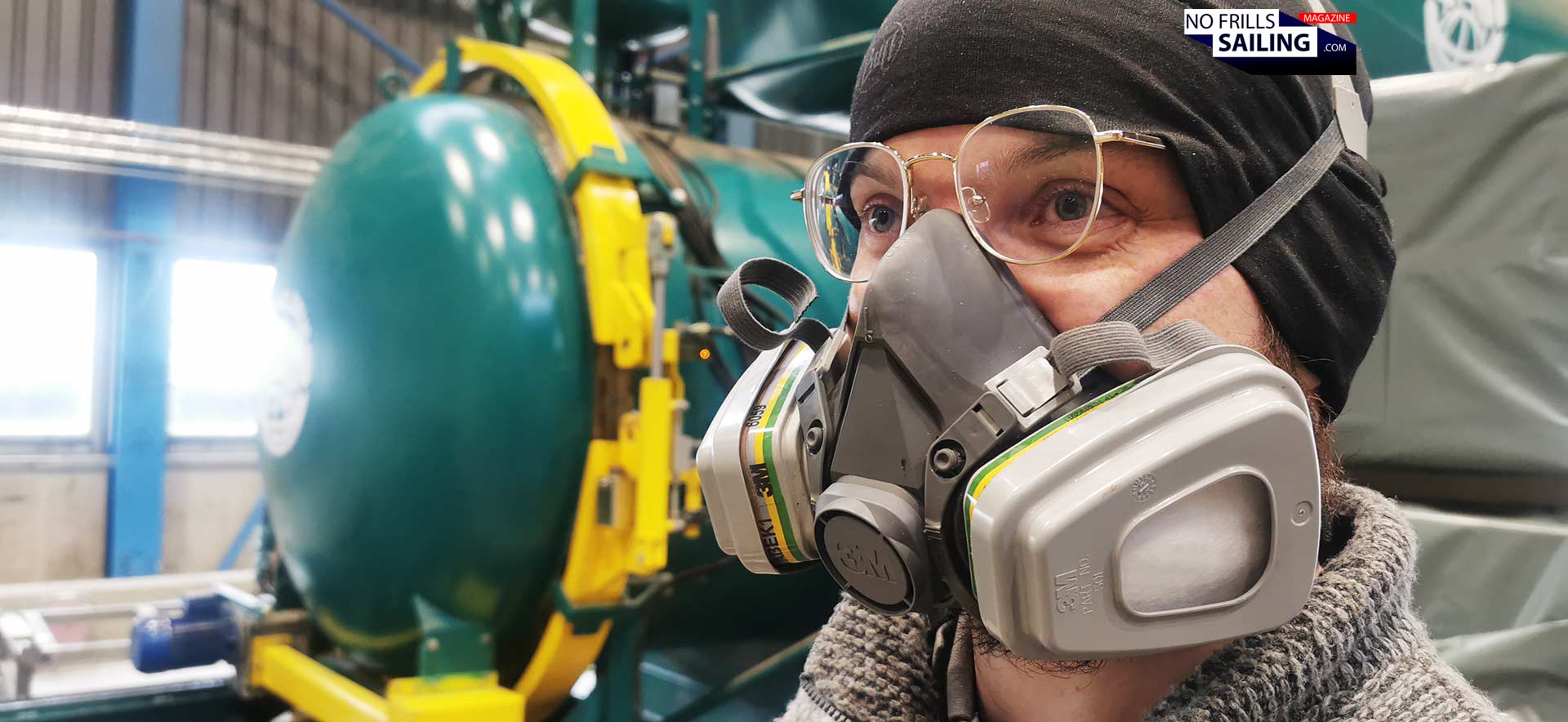
It is basically an airtight pressure chamber connected to a huge tank. This tank contains what the guys here call „the soup“. That´s the liquid that is used, together with pressure to process the timber. The huge round pressure door swings open, a cloud of odor oozes out, rolls up to the high ceiling. Although I keep a respectful distance to the dark gaping hole of the boiler, I cannot hold back my curiosity: Holding my breath, I walk up to peek inside.
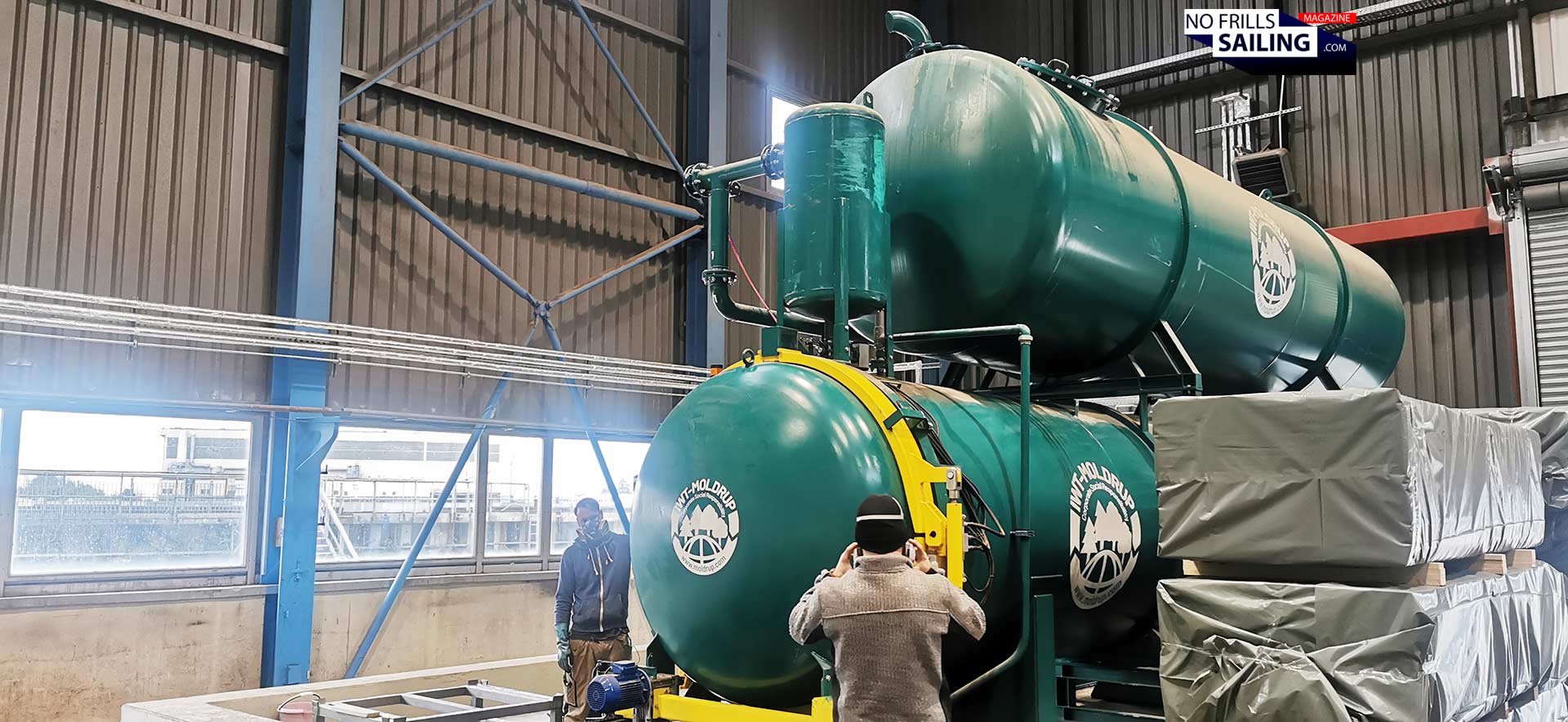
Of course I am not a freediver. The door is swinging open so slowly that I have to breathe. The smell is not as bad as I had thought: I resembles the smell of my brother´s football shoes after a long game in the rain, it instantly strikes me. A mixture of sweat and a not too unpleasant „earthy“ odor. Yet, if inhaled with a too deep sniff, it makes for a very strange feeling in my lungs. Arne resassures me that the finished Tesumo won’t be toxic at all – yet, breathing the soup´s odors is not recommended. So I wait in a respectful distance. The large factory gates are open, creating a nice airflow, venting the steam almost instantly. Behind me, a forklifter rolls up.
Tesumo´s secret: The „soup“
The secret mixture used together with applied pressure, temperature and time, turns Limba into Tesumo. It´s a Cappucchino-colored liquid that to a great extend contains fresh water. The soup´s small percentage of chemicals are responsible for impregnating the cell structure of the limba wood. Thus, making it dimensionally stable, weather resistant and durable. Of course the recipe of the soup is patented as well. The process batches remain 8 to 10 hours inside the soup-induced high pressure-environment of this autoclave.
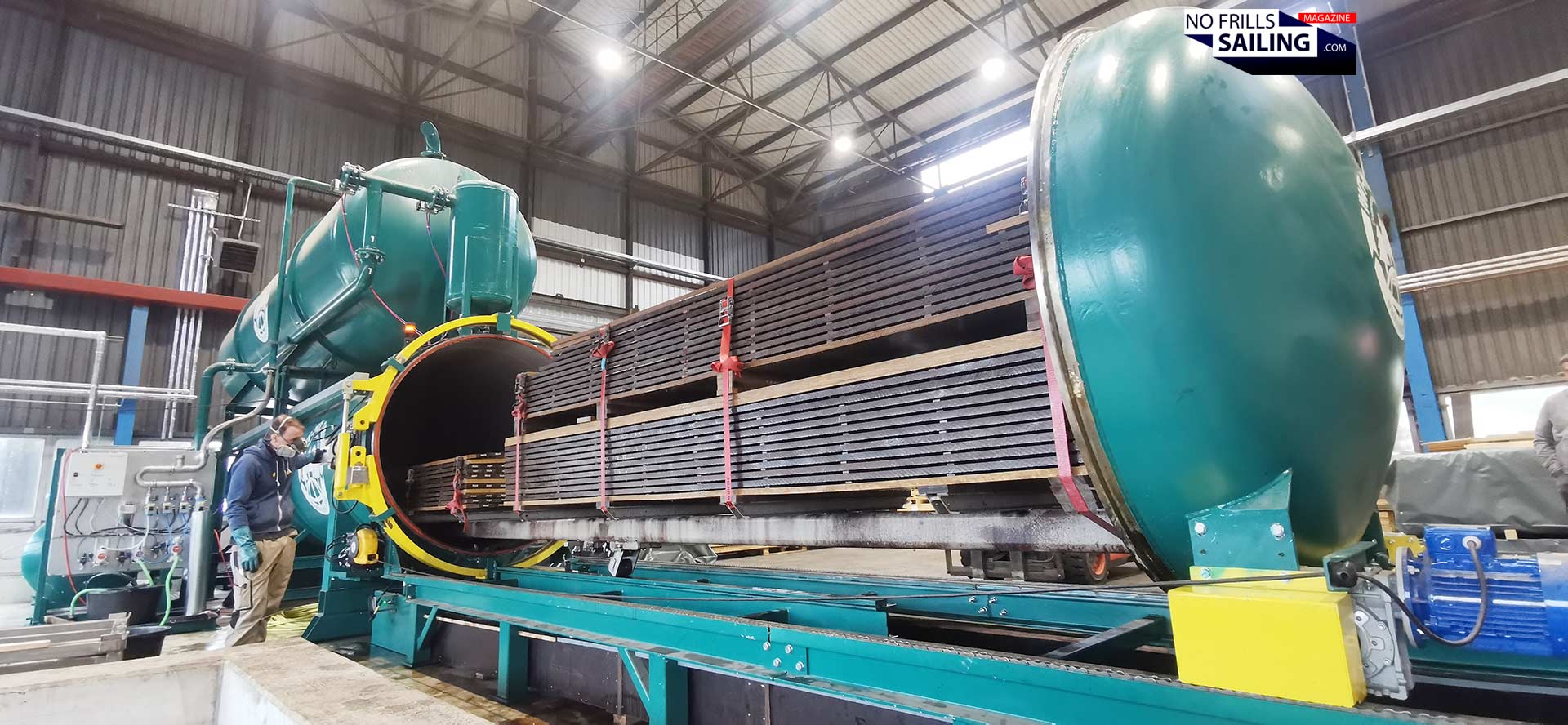
On a sledge the badges slowly glide out of the stainless-steel chamber. I try to sense a change of temperature or something, but there is none. Between the piled up planks, streams of soup sare pouring out and down into the holding basin at the foot of the boiler and will be reused in the next process. A large, almost half a meter high concrete surrounding is set up here: One of the environmental requirements needed for being allowed to setting up and running the production at this location.
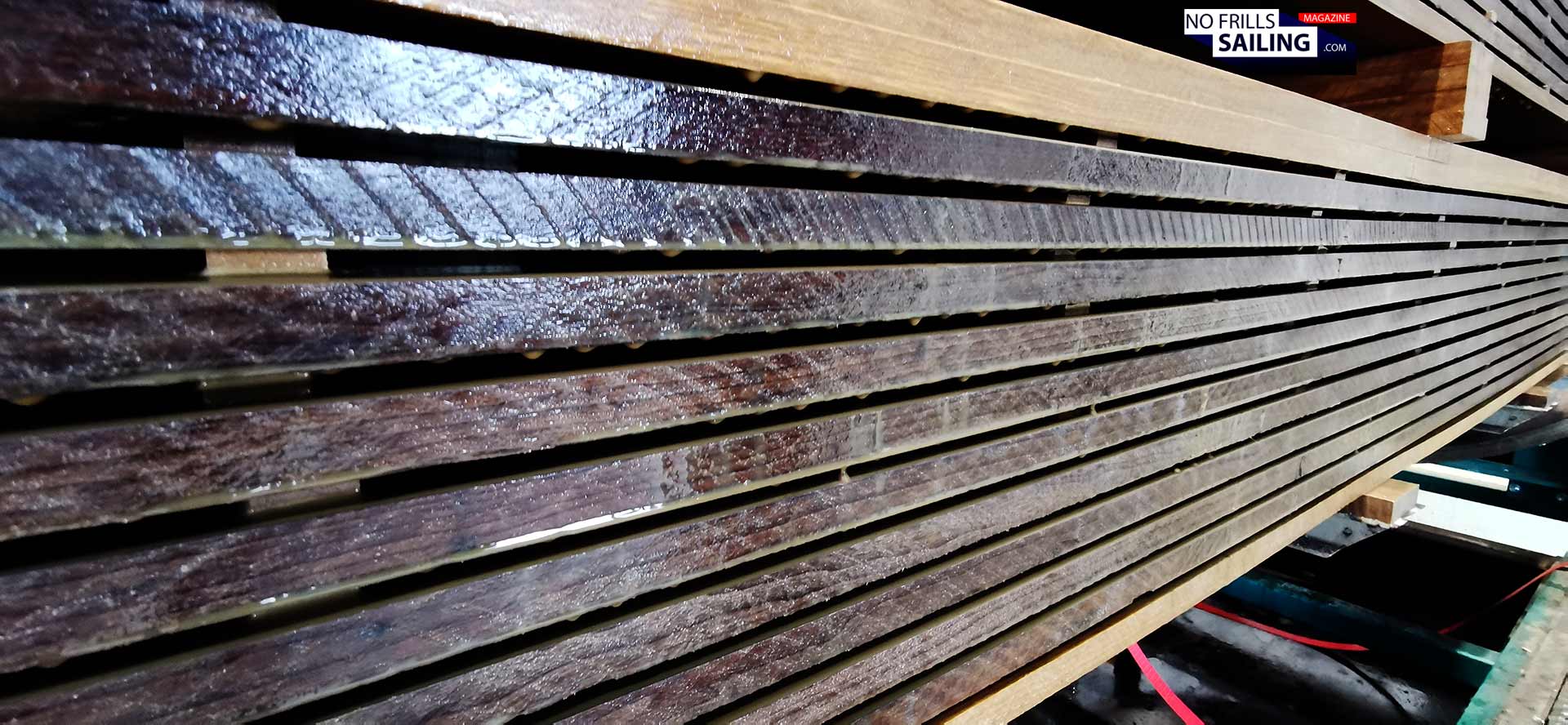
The planks have turned very dark now. Soaked with soup, the cell structure of the limba wood is now fully loaded with this rich broth. The soup can be re-used multiple times, Arne explains. Although a totally different process and not comparable to this one, I am kind of reminded of the „Body Worlds“ exhibition back in the day: Corpses of real humans, „plasticized“ and opened up, cut and re-arranged to show how a human body looks like in reality. The process of making these exhibits everlasting is different, but not unlike Tesumo´s invention. At least for me as a non-scientist it feels like this. Certainly, the finished product is way more attractive …
Quality control is not just a word here
While one of the workers checks the batch and prepares it for the next step, the other one takes the control plank off the pile. He puts it on a precision scale. I peer over his shoulder. The plank´s first note „Limba“ states that it brought some 1.759 grams to the scale. After the first thermal treatment it became lighter, of course: The note on the plank states 945 grams. Significantly lighter because it lost so much of the residual moisture for example.
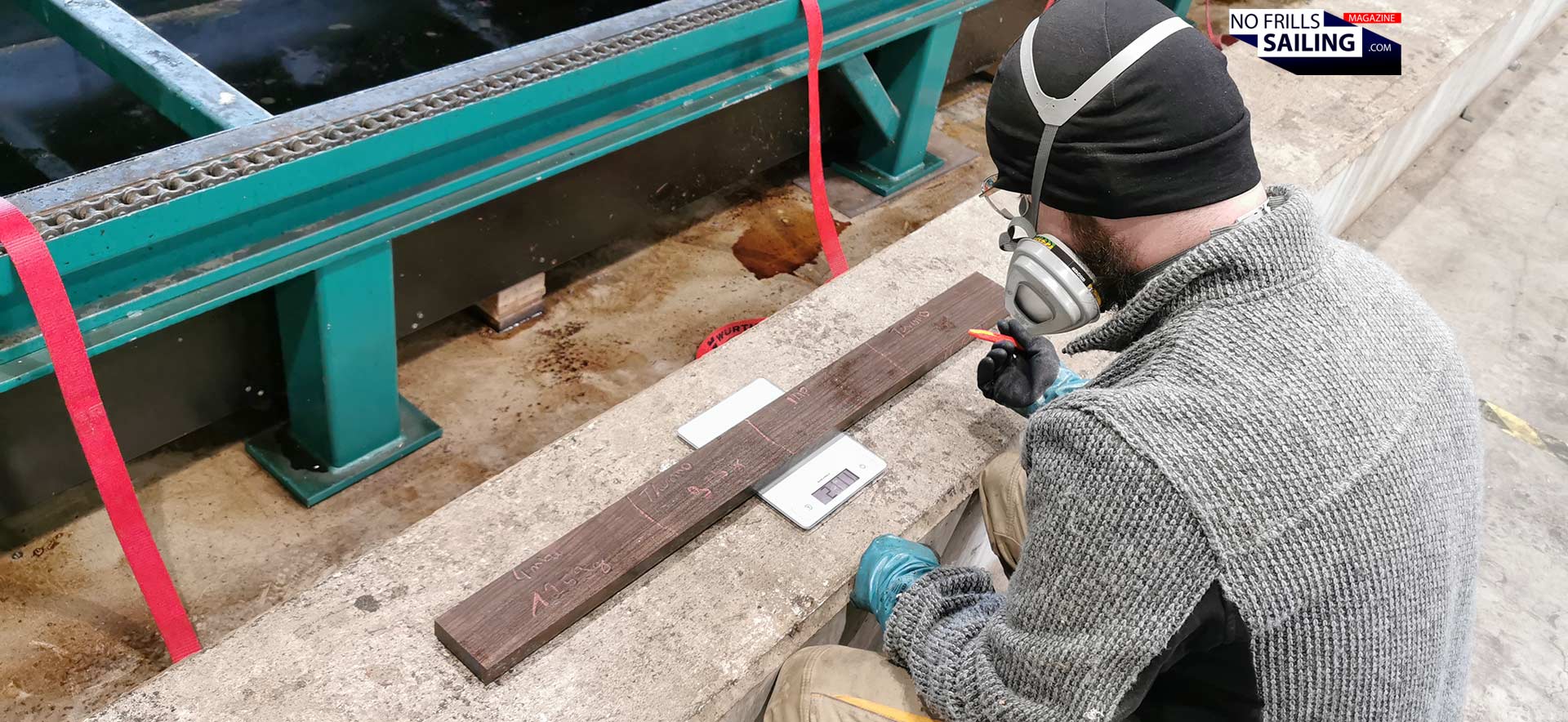
Now, after the treatment in the „boiler“, the plank is pumped up and soaken with soup. It should be much heavier now. And it indeed is! The scales reads 2.111 grams. The numbers are noted onto the control plank and it is put bank onto the process batch. The worker sends the details into the system: Tesumo keeps track of every process batch all along the complete production process. By comparing the numbers and the weight decrease or increase after each step, the company´s quality controllers can decide whether the treatment was successful or not. If the timber hasn´t lost a certain amount of weight, drying is incomplete. Hasn´t it gained a specified percentage, the impregnation is.
It takes time. Like a good wine.
Just as it is on a vineyard, Tesumo production cannot be rushed. Arne explains that good stuff takes time. Absolutely natural. The freshly treated batches are instantly packed in thick plastic wrap. Still dripping with soup, the aim is that the planks are now allowed to „chill“. The process of maturation and drying is prolonged by this measure – just as you would do with a Steak, taking it off the grill you want it to relax a bit. Same here.
Ready for some chillingThe guys put each of the three batches on a free space to start working. It´s easier that way to wrap around the plastic foil. Here´s the one downside of this process: Making Tesumo is admittedly a very energy-intensive and waste producing thing. You may have read my articles on plastic waste in yachtbuilding, reduction and even complete abandonment of single-use plastics is one of the „quick wins“ and comparatively easy goals of the industry in becoming more sustainable. Arne agrees: Something they are working on right now.
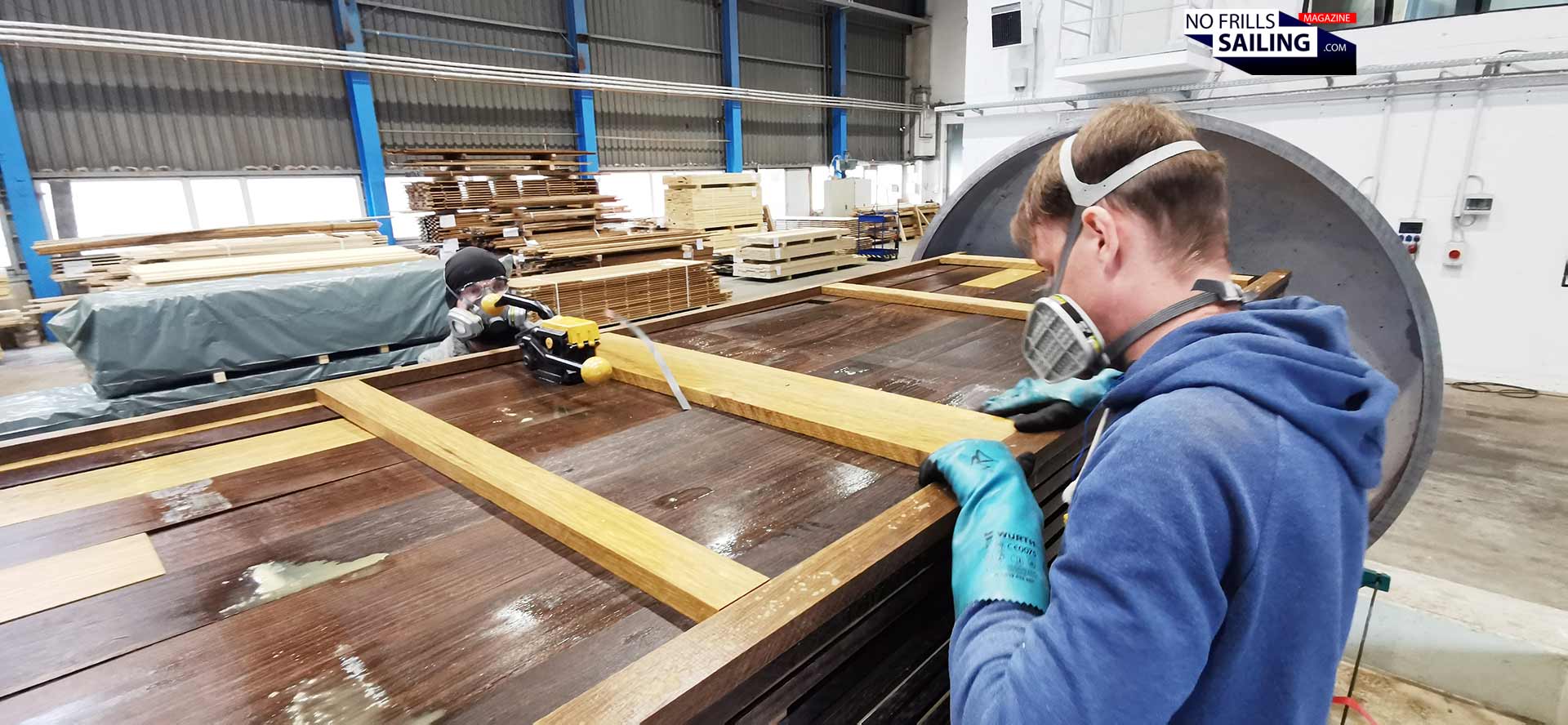
Maybe replacing this green single use plastic wrap with multi-use materials is one step Tesumo´s engineers can undertake in the near future. The skilled team is fast. No 30 minutes does it take to wrap the batches and put them aside. Here the Tesumo planks will now be given 10 to 14 days to chill out. Arne explains that the company wants a slow process of maturation. This is to achieve a evenly saturated, homogenous product.
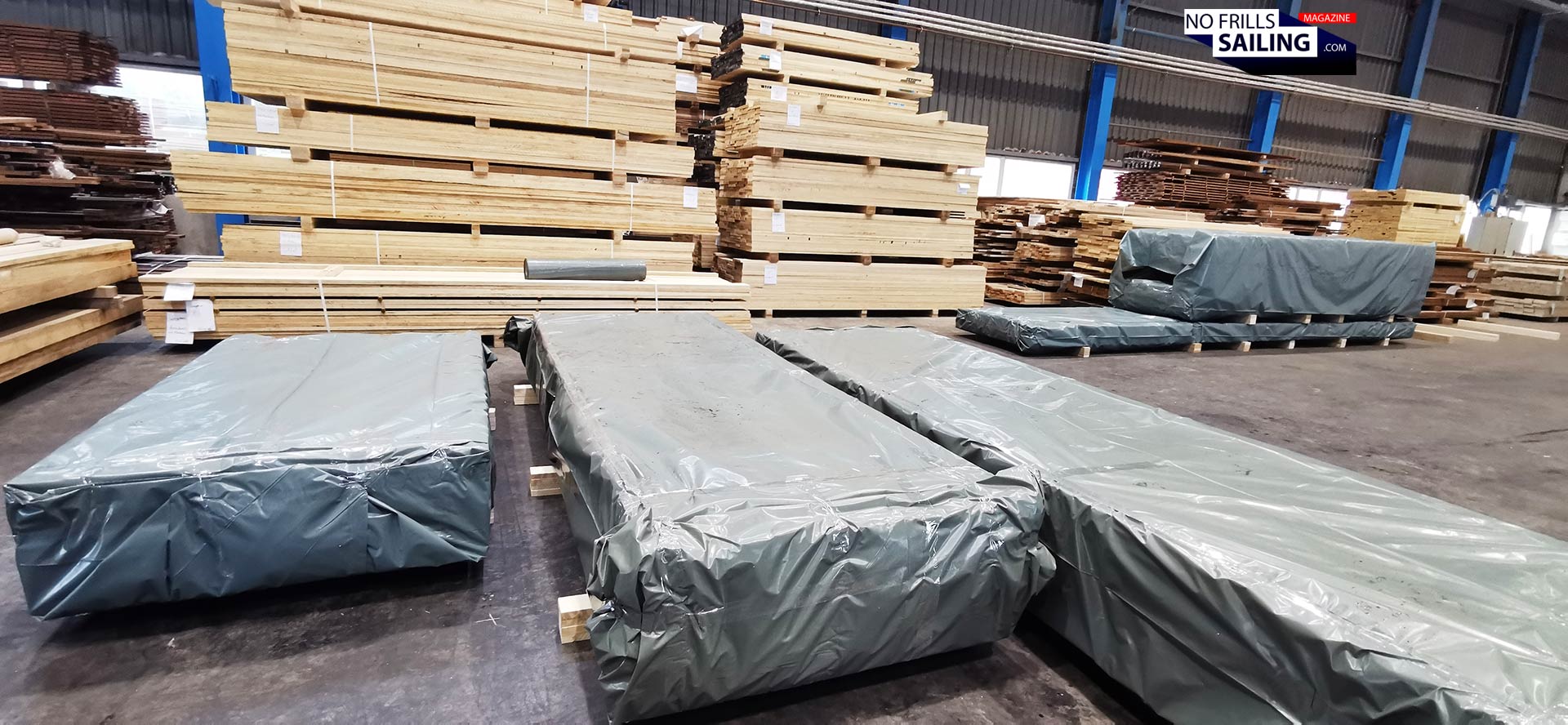
The factory gates are closed by now as the soup´s odors are completely gone. The temperature goes up again. We walk between the piles of timber. Raw limba that has just arrived from Africa, batches with thermo-treated limba awaiting their bath in the soup, a number of green packages with tesumo „chilling out“ and batches ready for shipment to the clients. How much cubic meters of limber are present in this hall, I ask myself. And how much is this amount of wood worth? Arne asks me to put on my jacket.
A last thermal treatment of the future yacht deck
To see the last step of Tesumo production we have to leave the building. After chilling out, the process batches are subjected to a final production step to become the finished product: Yet another thermo-treatment. In a safe distance to the huge ex-shipyard factory, a two-story silverish machine has been set up directly next to the levy protecting the area from the river Weser´s spring floods. This location is on purpose: The last step involves a lot of heat: Fire hazard!
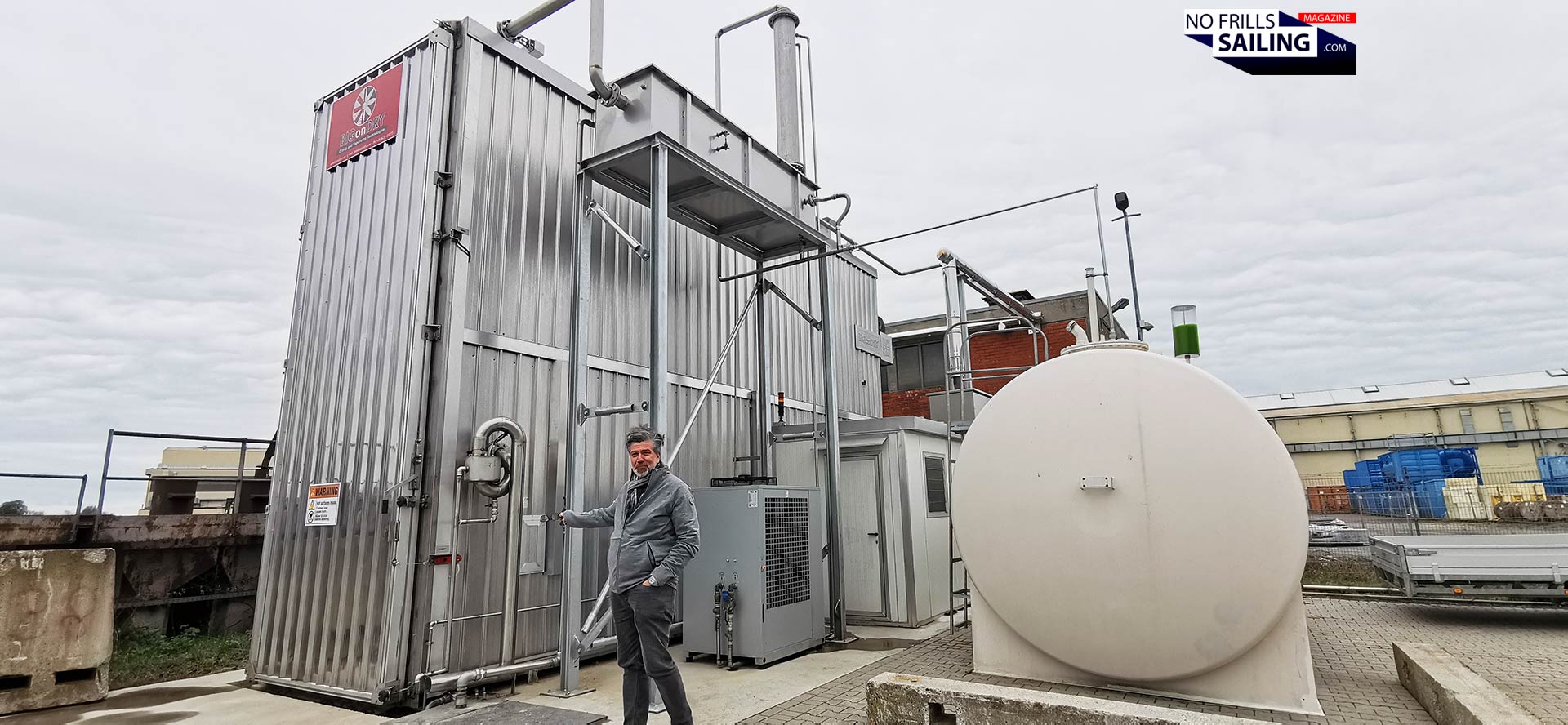
This oven – has the size of two standard 40 foot containers stacked on top of each other. Again, a rather secretive amount of heat and a special atmosphere is applied. A delicate matter, as Arne tells me: This last process needs a close motitoring as well. Too much or too little and a whole batch can be rendered useless. To ensure a complete monitoring, multiple sensors are installed within the batch, delivering digital real-time data to the operations center.
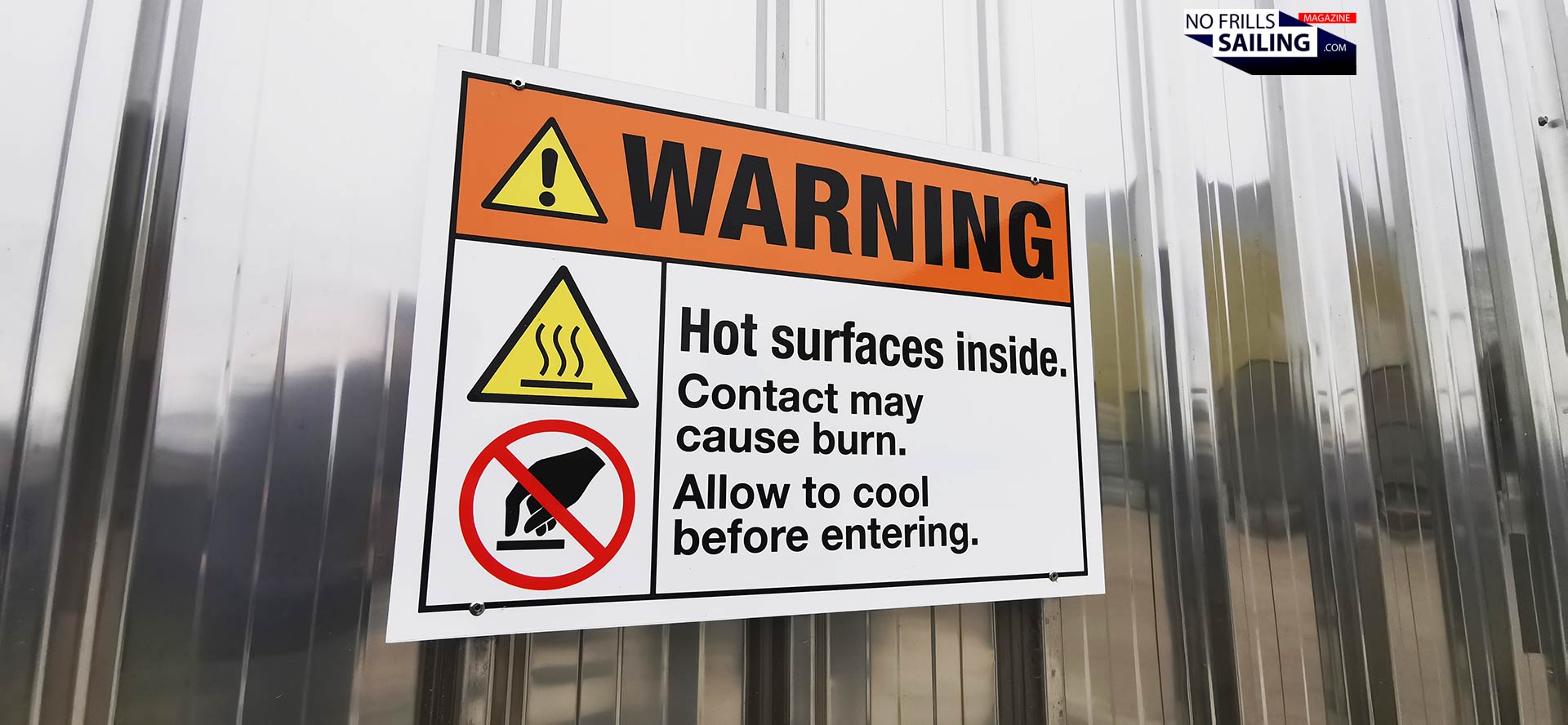
Taking the analogy of a cook, constantly checking the food he is cooking, so do the engineers upstairs. The final process of drying and curing can take between 8 and 10 days. Depending on the saturation of the planks, their size and thicknesses and other factors. After completing this final and last step, practically, Tesumo is now finished. The same way I had been lucky to be present to witness the opening of the „boiler“, I was rather unlucky because the oven was currently still in use, no opening for me.
Processing the raw product
But that´s no problem as the company has a lot of Tesumo in all steps of the production in use. Going back inside, Arne takes me to the inhouse joinery. Here the skilled craftsmen operate large industry-size planing machines, impressive saws and other tools. Some of these joiners are trained to act as quality checkers and production surveyors, constantly checking if the product adheres to Tesumo´s quality promise.
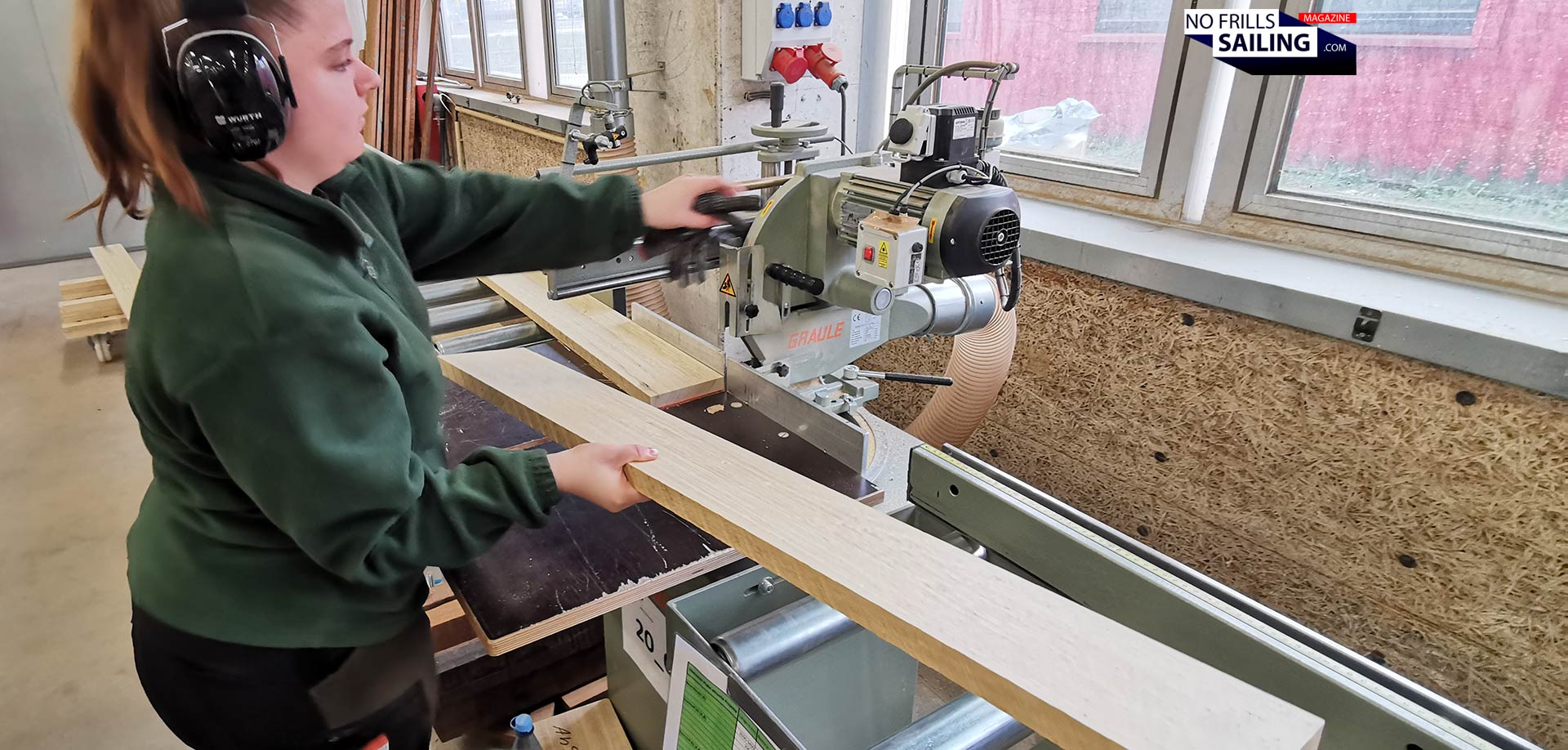
The raw limba is raw planed and shaped here, as well as the finished Tesumo planks after completion of the whole process. Now, the dark color of the soaken Tesumo-planks I´ve seen coming out of the impregnation chamber is completely gone after thermo-drying. The wood received its nice, warm and light color. The grain is accentuated and pretty. I take one plank and check the smell: The „soup“ is completely gone.
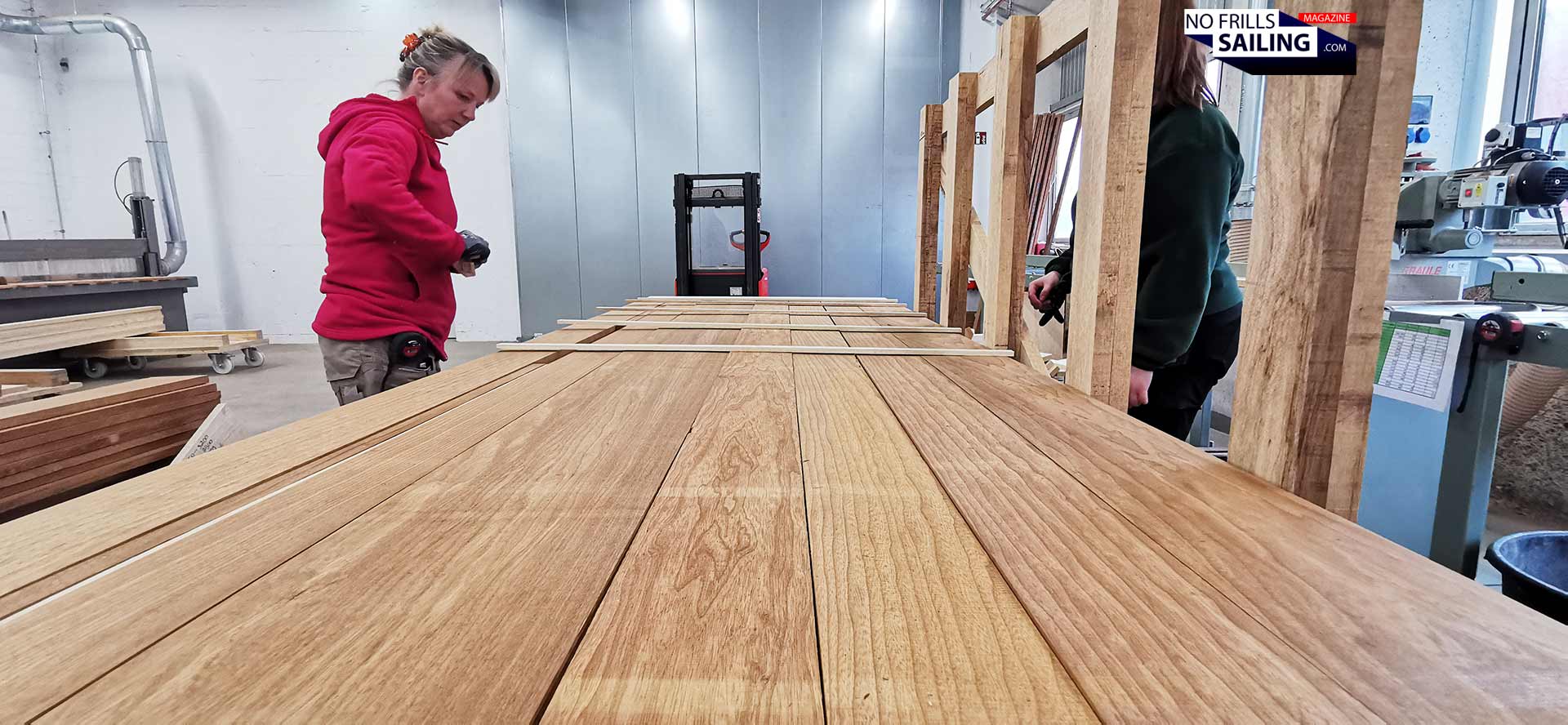
The joiners – most of them women, which is a fact that I like very much – apply a last planing to each plank. This goes along with the end-check. If the workers detect planks with irregularities or damage, these would be sorted out or downgraded to a lower quality level. The ladies pile the end product up on new stacks. Spacing battens and protection planks on the edges are set up before the stack is bound together with lashing strapes: Ready for shipment to Tesumo´s clients!
Backtracking every single Tesumo plank
What I notice is a little aluminium label with a barcode. It’s put to each single plank´s side. This barcode is the tracing for every Tesumo-plank ever produced. By scanning it, every single information connected to its production can thus be traced back: Origin of raw limba, the project batch number, the dates of the production cycle and all data of each production step.
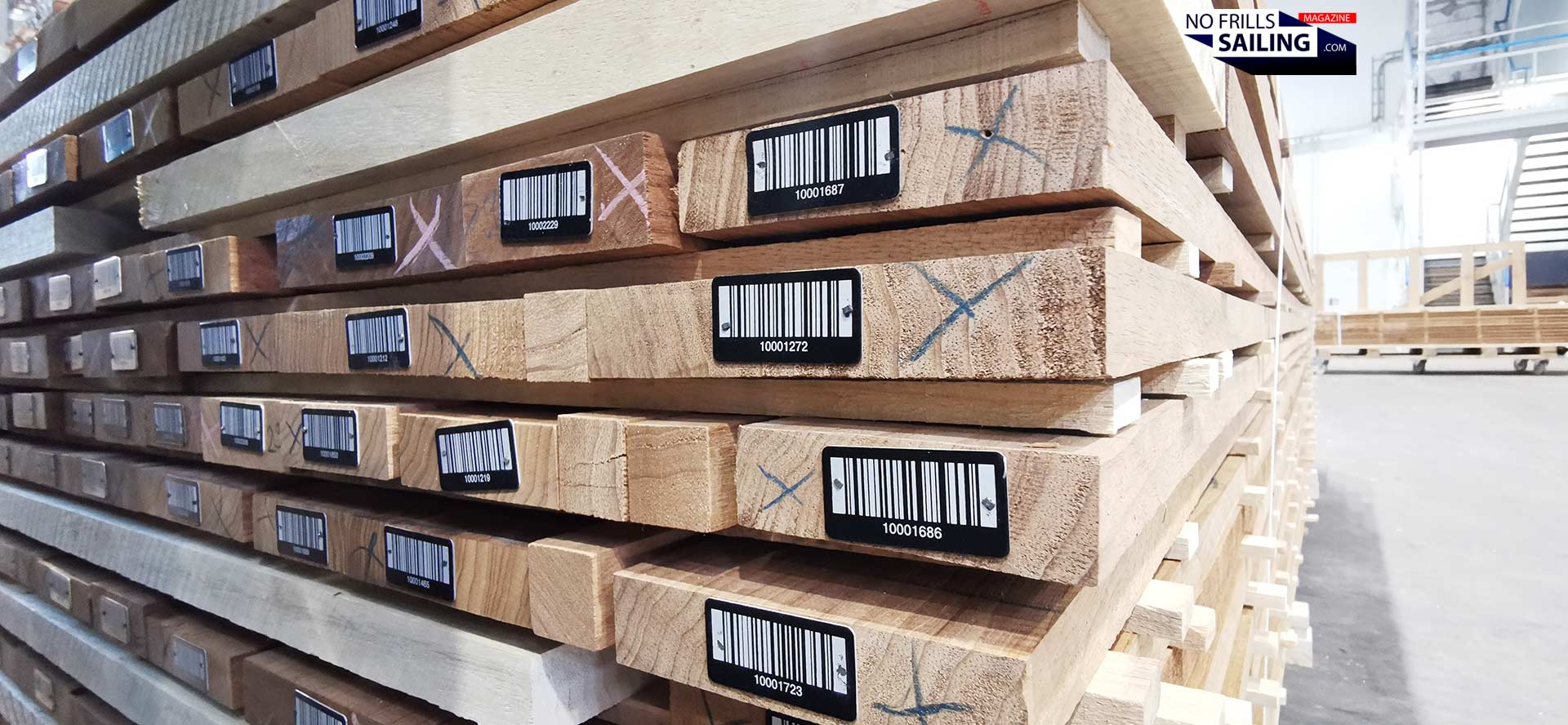
In this, not only in theory but also in practice, Tesumo would be able to give detailed information on every single piece of deck used in the later yacht. Something, a client like Lürssen or Vitters appreciates very much. And what about the control planks? Arne takes me to a special room. The „archive“, as he tells me. It´s in a rough shape as the company is currently finishing the style of this room, but in essence that´s the “library” of Tesumo.
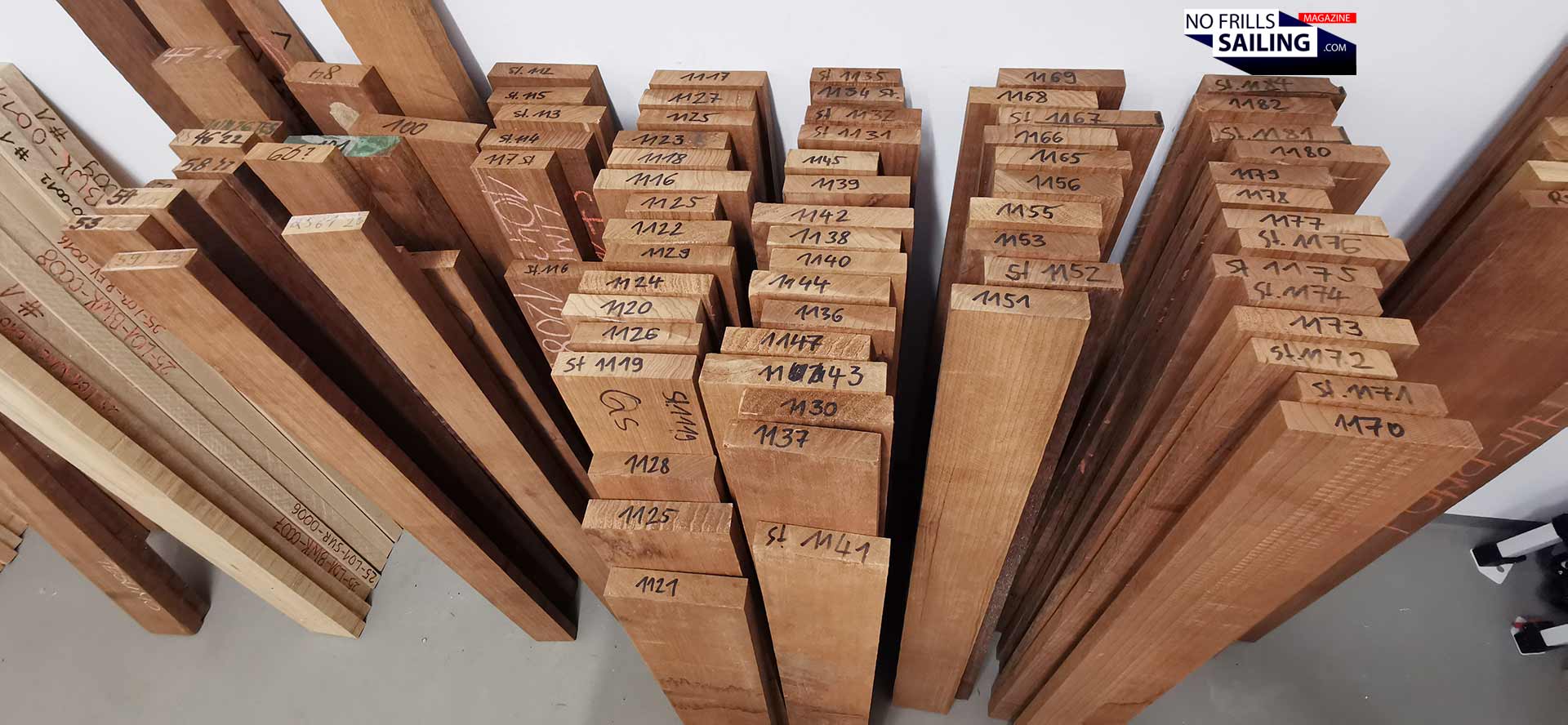
Here I can see every single control plank of every single production cycle of every single process batch that this plant has ever produced. This means that Tesumo is not just able to confirm the history of every single plank used in any boat but can also reproduce proof of the overall quality of each process batch. This is impressive: It reminds me of some scientific research labs in Antarctica where the drill cores are stored.
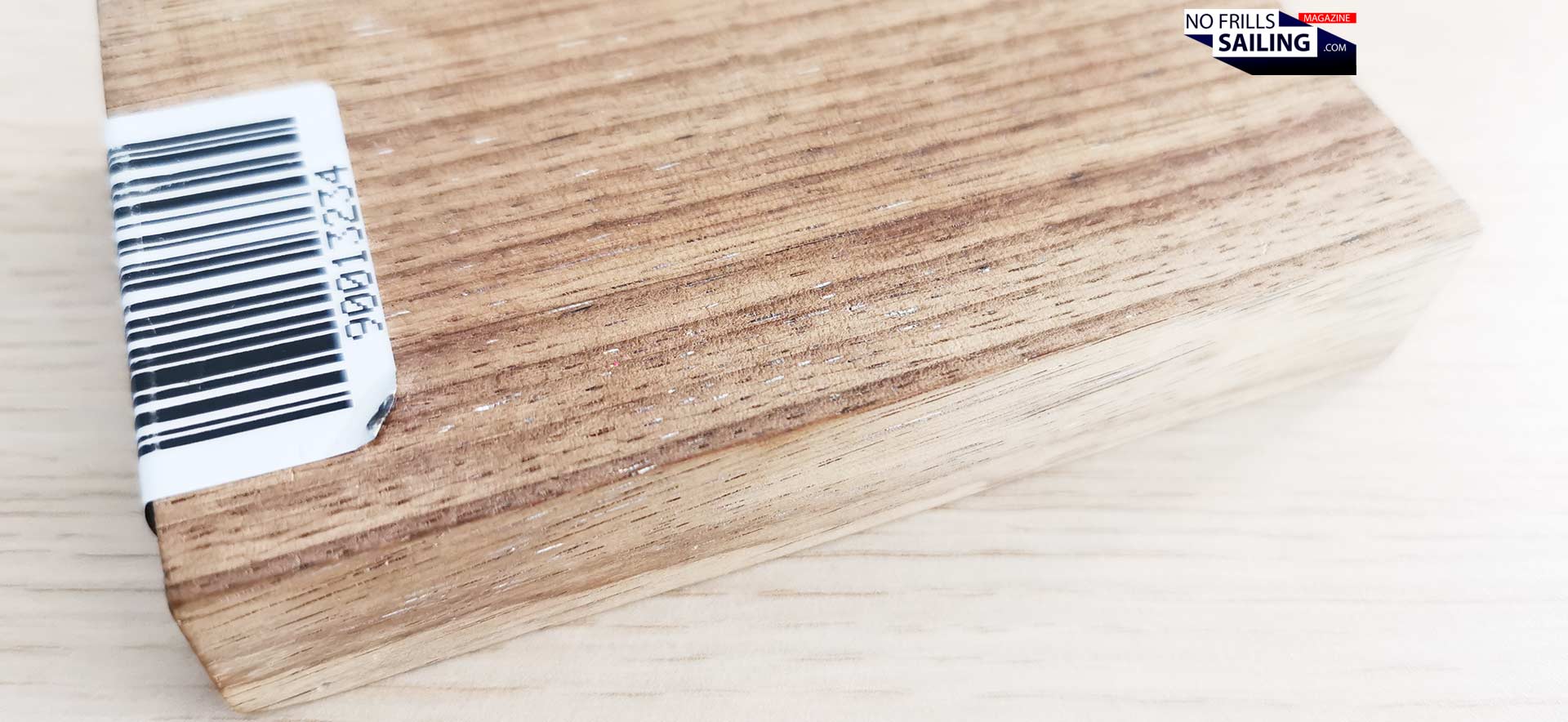
This archive also functions as a lab in itself. Here, as well as on specific rooftops at selected locations, Tesumo planks are subjected to nature´s elements. Although a thorough test phase that had incorporated extreme weathering of this material had been commenced during the start development of Tesumo´s production process and patents, the company still keeps records and conducts a specific testing program of their products. There´s always room for improvement, as Arne says. Tesumo is currently in the 45th production cycle. That´s roughly 2.5 cycles per month. Many had been test cycles: Setting up this factory to work seamlessly, calibrating the machines, fine-tune the soup or the training the staff. It all took time.
A standardized process – but á la carte
Now Tesumo in Bremen is ramping up production. Arne says proudly that up until now some 10 projects had been completed or are underway. That may not sound like much, but it is: Their main client up to now is their „mother company“ Lürssen shipyards. Here, superyachts of 70 to 150 meters length are built: Imagine the sheer amount of timber needed for just one of their multi-store decks! The first aim was to set up the production and have it running smoothly. This goal has been achieved.
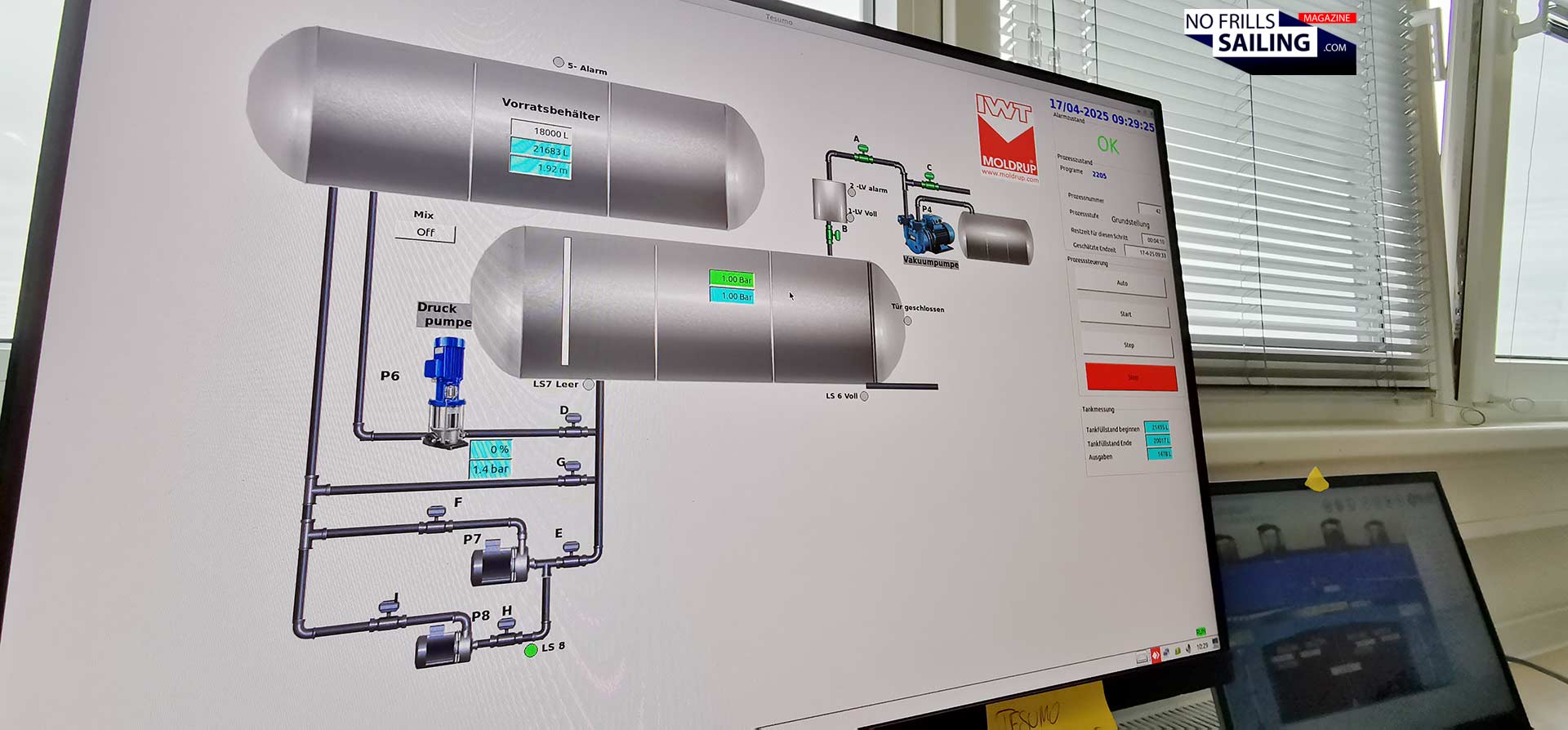
Almost all steps of the process steering are digitally aided and controlled. Back again upstairs, overseeing the production, computer displays show the factory´s machines, temperatures, pressure and liquid flows. A highly standardized process that is largely automatic, yet, it still needs the expertise of skilled and trained people who can spot irregularities and have a certain feeling for the wood. In the end, as Arne puts it, it´s still a natural product they are working with here.
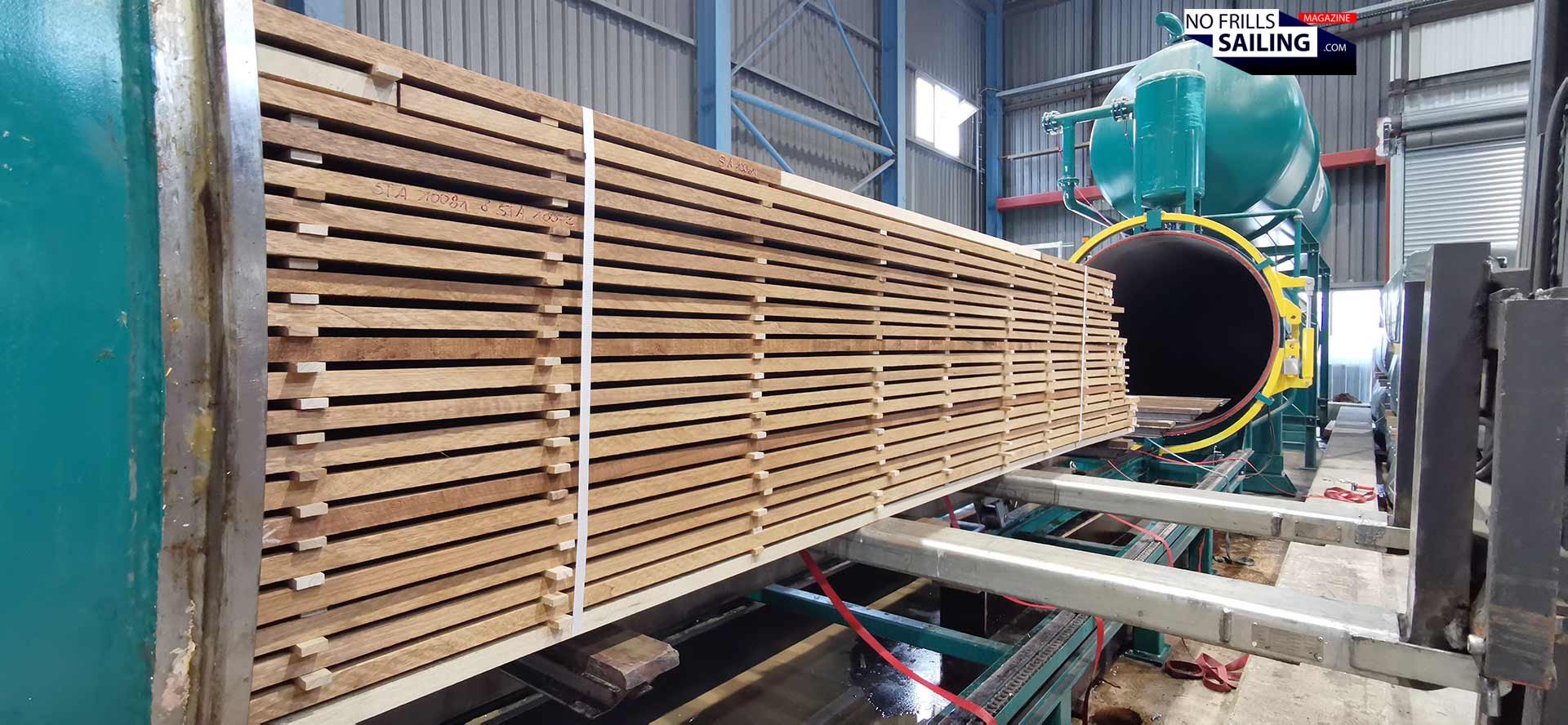
As this most interesting tour of the Tesumo production draws to an end now, I say Goodbye to Arne. These have been two most exciting hours. As I wave to the guys, they are busy in preparing yet a new process batch to go into the gaping dark hole of the „boiler“. Thick planks of 24 to 21 millimeters, certainly the size suitable for use on yet another superyacht. Now that I´ve seen the whole production process from A to Z, I am asking myself: Who are the clients, where is Tesumo used and could I see a yacht fitted with this new deck material?
Tesumo deck for your yacht?
Naturally, this is a sensitive thing. Superyachts are owned by people mostly not very interested in creating a buzz. Even more owners of power boats. Of course, a photo session on the other river side at Lürssen would be absolutely exciting, that´s a request even Arne cannot satisfy. But there´s light at the end of the tunnel: Arne is convinced that Tesumo will see a „trickle down effect“. As more and more of his product will be utilized by more and more shipyards, production size will grow – thus, the price for Tesumo will certainly go down, making this material accessible for „normal“ yachts as well. Just as it happened with Tesla: Rich early adopters paid high prices to pave the way for more income, more re-investment and growing production sizes.
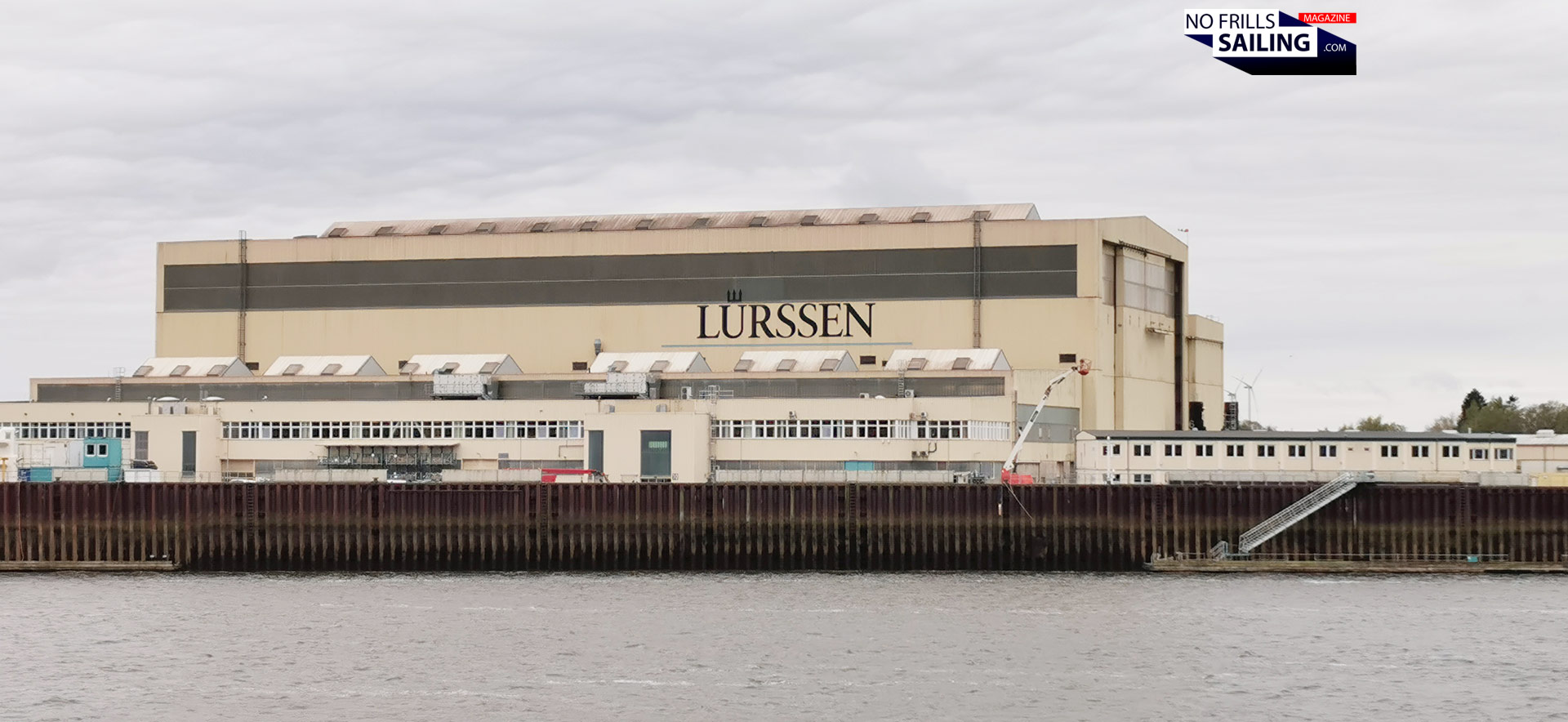
And rightly so: Only a few days later I read the news that a Knierim built carbon fiber 31-footer by one of my most favourite naval architects, Martin Menzner of Berckemeyer Yacht Design, had been launched – sporting a deck with Tesumo. All in all, an exciting day with a most interesting product. I don´t think that giants like Lürssen or Vitters would invest in a product that is unsafe or cannot live up to their highest quality expectations. Arne says, the problem is not to find shipyards wanting to use their prime grade Tesumo deck, his challenge is to find architects and companies wanting to incorporate second and third grade Tesumo into their houses. So: Why ordering the corresponding boathouse for your new daysailer in Tesumo as well?
Also interesting articles, connected to this topic:
An Imoca 60 for the Vendée Globe – made of wood?!?
Wooden boatbuilding masterclass: Woy 26