I do have a special connection to Dufour Yachts of La Rochelle as it appears. When I happened to be in the lovely French town at the coast of the Atlantic Ocean some weeks ago – having visited the yard facilities of Fora Marine, better known as RM Yachts (read it here) I was also knocking at the doors of Dufour Yachts. And as it seems, they let me in as well and welcomed me at their production site. The weather has been perfect that day, some 25 degrees and pure sunshine, so my spirits where high and I was keen on taking a look at Dufour´s style of production.
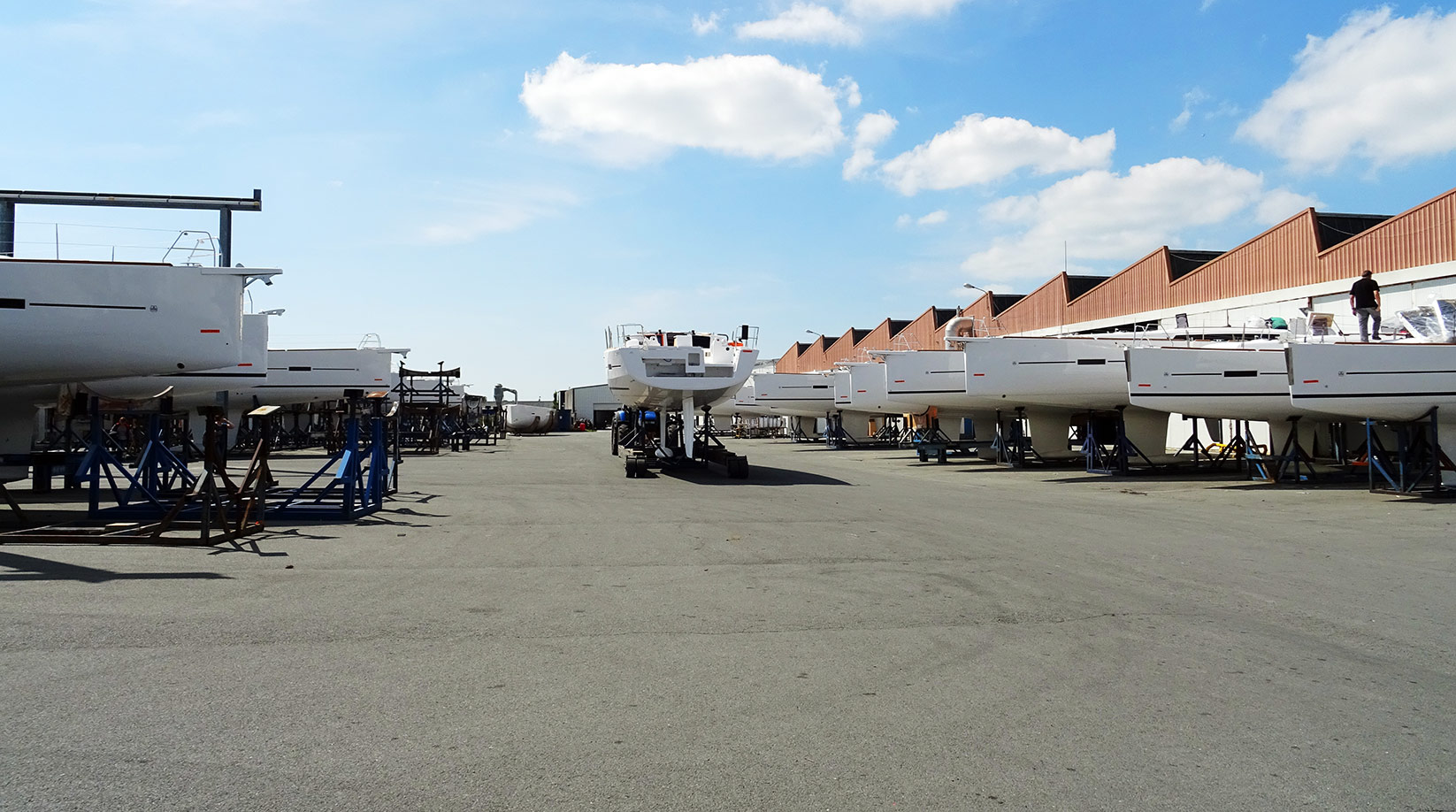
Why? Because Dufour is one of the major leading yards of production boats. As Stephane Villesot, the man who was taking me around, pointed out, Dufour is currently making some 400 boats annually with a little less workforce: Meaning that every man of the yard is kind of making one boat per day. Impressive. Even more impressive when I entered the yard, situated some 15 kilometers away from the shore of the Atlantic Ocean in a commercial zone in Perigny, in the perimeter of La Rochelle. I was greeted by dozens of finished Grandlarge sailing yachts waiting to be delivered. Let´s go inside …
The Invention of Monsieur Michel Dufour
Dufour is an old brand, a brand every Frenchman knows like Coke or Chrysler would be a similar heritage to an American. Michele Dufour, a sailing fanatic and engineer, founded the company some 54 years ago right here in La Rochelle. Michele Dufour is not just the father of the brand and the designer of the first boats, like the Dufour Arpege, but a genius too: His invention kind of paved the way for the breakthrough of GRP in modern boatbuilding.
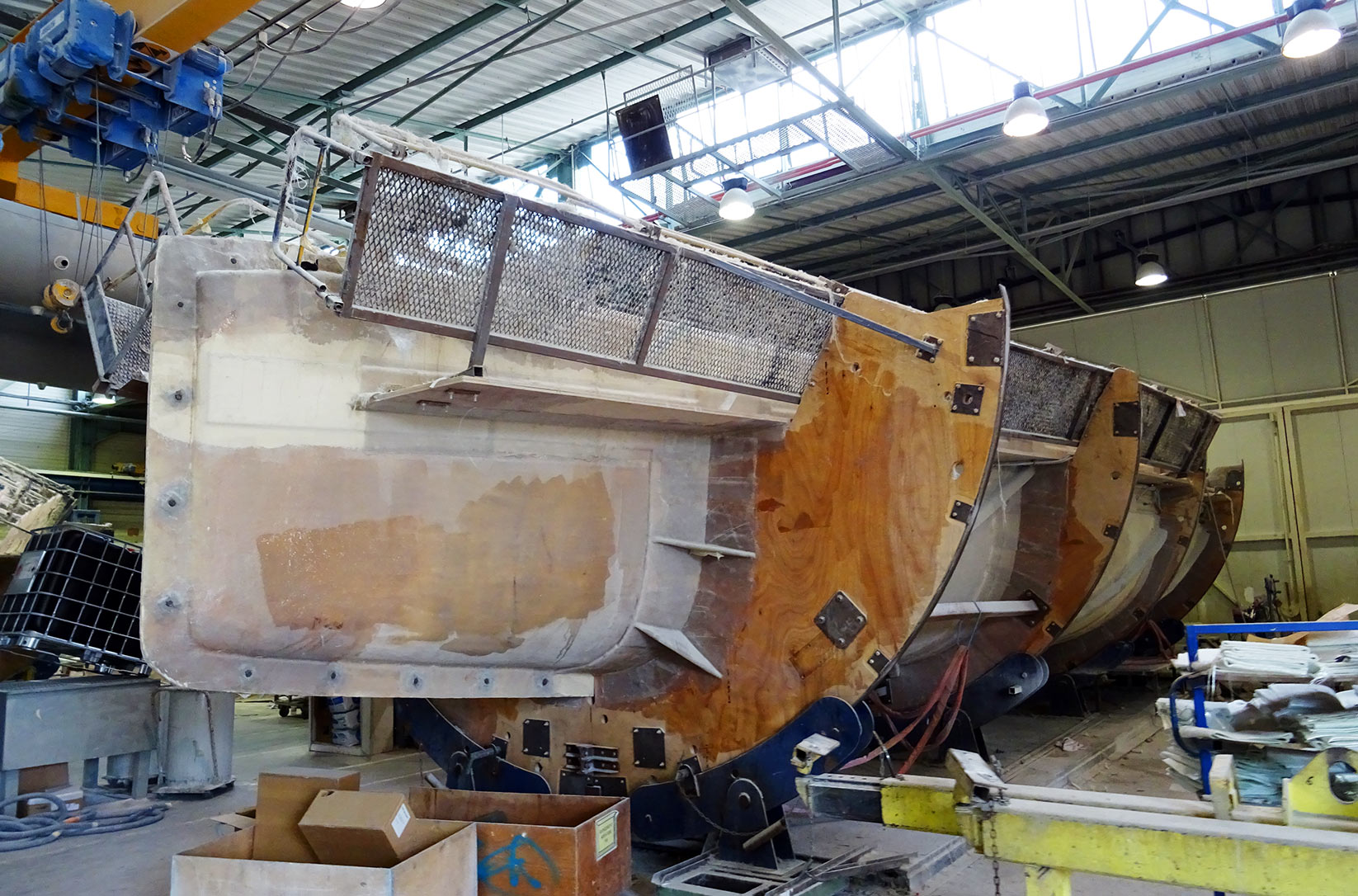
As we enter the hall where the very first step of the production process is carried out, I am standing in front of the molds. It´s a wide known process happening here: The mold is painstakingly cleaned and polished. Then Gelcoat is sprayed into the mold as the first layer. Know a mixture of resin and pre-cut mattes of glass-reinforced fiber (GRP) are laid out inside the mold. Workers will roll out air bubbles with special rollers and lay down even more GRP-layers into the resin, tightly pushing by rollers all the time until the desired thickness of the hull is achieved.
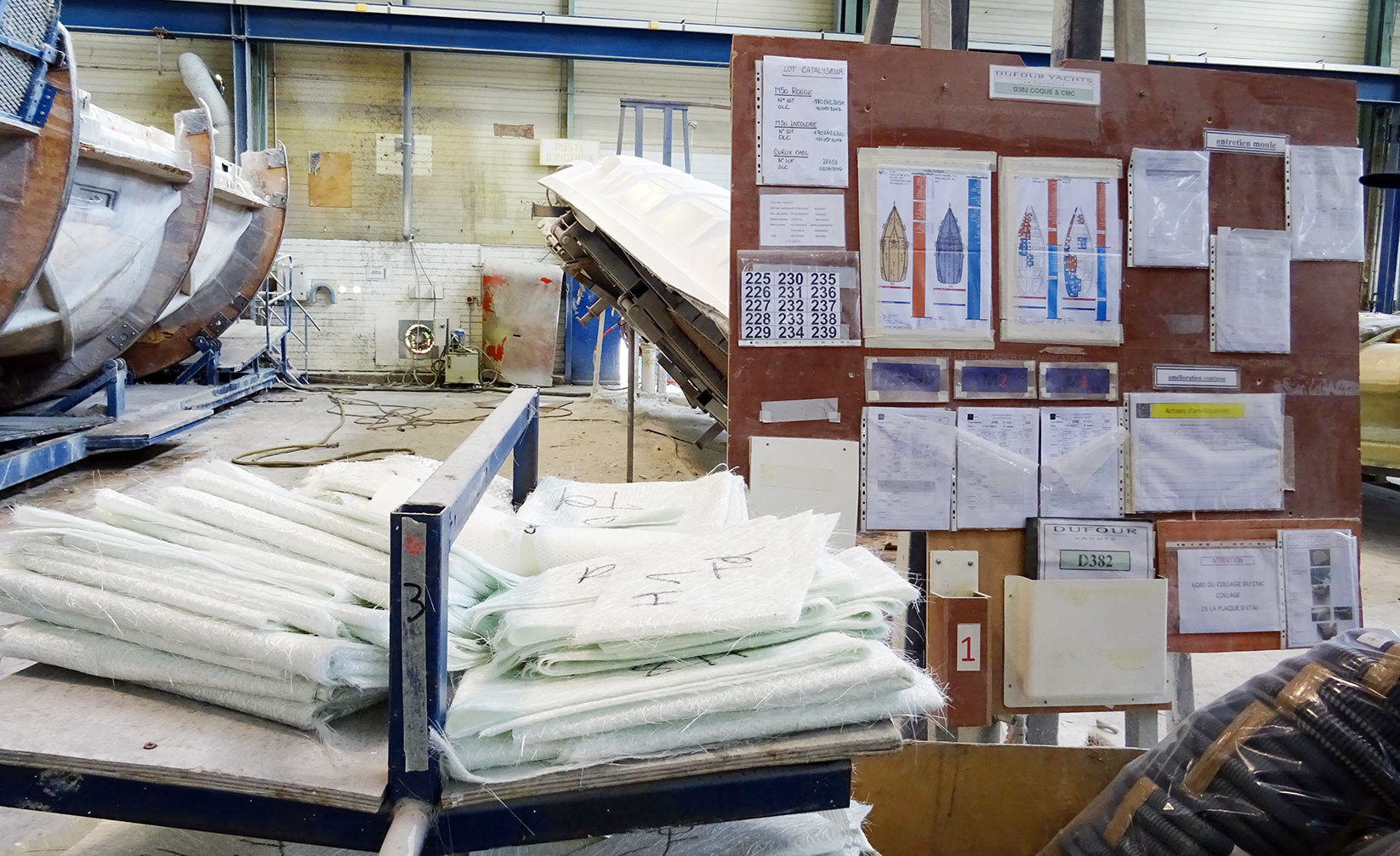
Michel Dufour back in the Sixties was fascinated by this kind of making a boat: It was a fast, convenient process. A process which could be carried out without any special knowledge by a worker (as far as he was doing it thoroughly and placing the pre-cut mattes exactly where they were supposed to be positioned) and – best of all – this way of making a hull could be carried out faster and cheaper compared to classic wooden or metal-made boats. Inside the hull the resin is now allowed to dry and harden thoroughly – the mold will be dispatched.
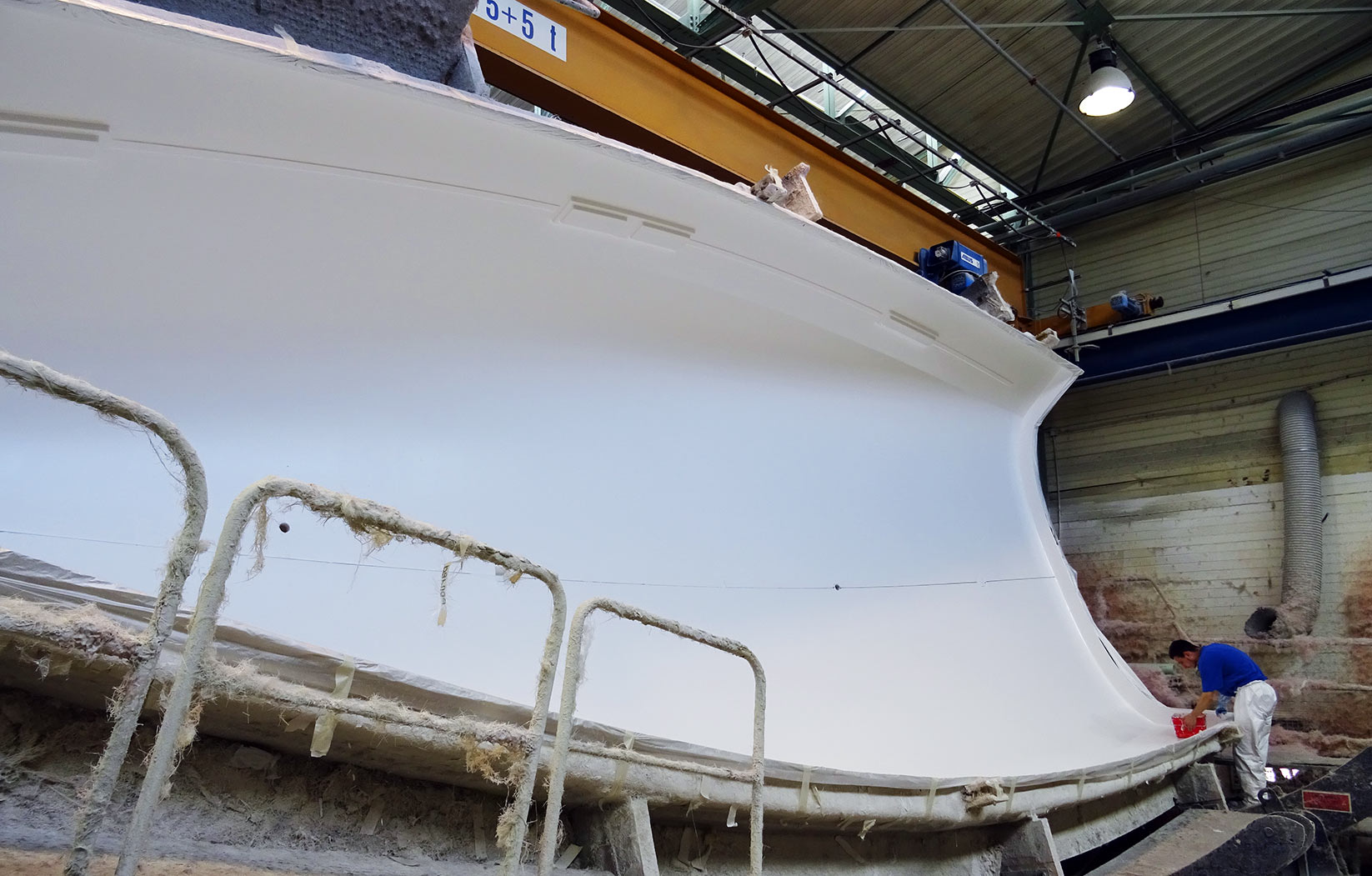
As we stroll along the production line I can see a lot of hulls in different stages of this very process. Of course, in various details the modern Dufour hulls are sufficiently different from Michel Dufour´s first boats but the very process remains the same – and this is what all the other GRP-based yards do all along – copying Michel Dufour´s idea of making fast, comparatively cheap, long lasting yet high quality GRP hulls for yachts. Something, Dufour was bringing up 54 years ago thus shaping a whole industry if you will. The hull is now flipped. Portholes and other openings will be cut out, the hull is checked for quality purposes. Then there comes the second – even more important – invention of Michel Dufour.
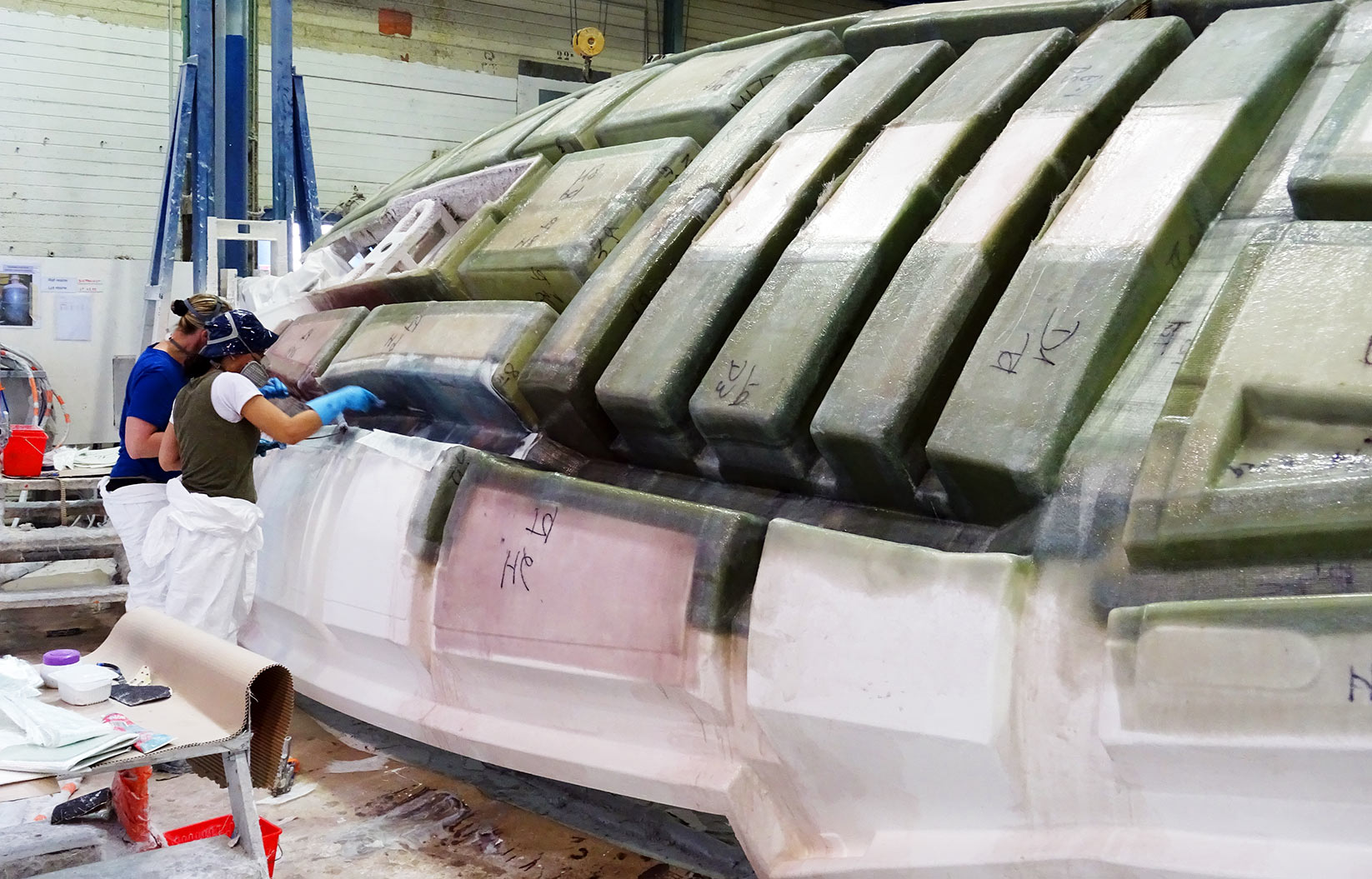
Every naval architect strives to make a hull both lightweight, energy- and material savy on the one hand – yet strong, stiff and reliable on the other. It´s not about the shape of the hull in this case but it´s about how to achieve the best compromise between stiffness and rigidity and while consuming the least possible amount of precious material. Michel, as an engineer, had the idea that would be copied and used by all other producers of yachts in the years to come and still is the standard in hull-making with GRP: The inner shell.
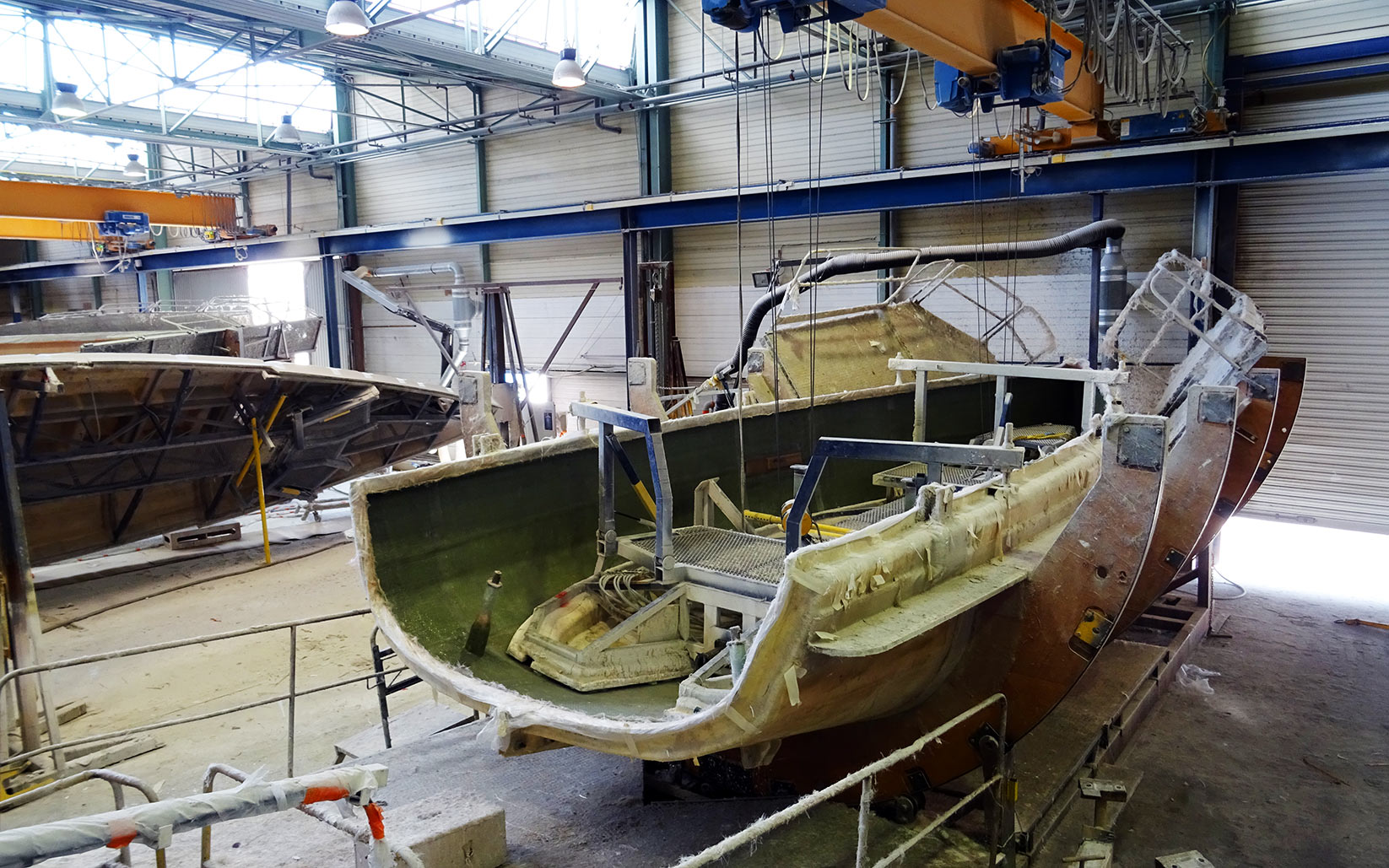
As I came to see, there was the finished outer shell standing on a rig. Inside, there wasn´t really much to see here, but to imagine: A second rig had been placed inside the hull where another, smaller “hull” was fitted to. The rig was pressing the second hull onto the outer hull, thus helping the Epoxy glue to form a thorough bond between them two. And there´s the secret of a stiff yet light hull: The second, inner hull has pre-formed stringers and the vertical frames which – after putting them two hulls together – will provide for the stiffness.

This is one of the really big things Michel Dufour left behind. Today, every yard copies his invention and so, in a way, a part of Dufour still lives in virtually every sailing yacht (and motoryacht). I knew that there is this technique from my own sailing yacht, a King´s Cruiser 33, and I´ve seen the inner shell of my boat and other yachts for sure for multiple times, but I´ve never seen the whole of them two hulls in one piece. Very interesting.
Making the Deck
As we proceed to another part of the large facility, my eyes kind of hurt: So much colour! Some molds of the deck superstructure are being prepared. A worker in perfectly clean clothing is rushing on his knees, diligent cleaning the inside of the mold with cotton tuch. This is because he naturally does not want to have dust, hairs or other particles inside the mold. The next step would be the Gelcoat layer which is sprayed into the mold forming the first layer of the new deck. But why is the mold green?
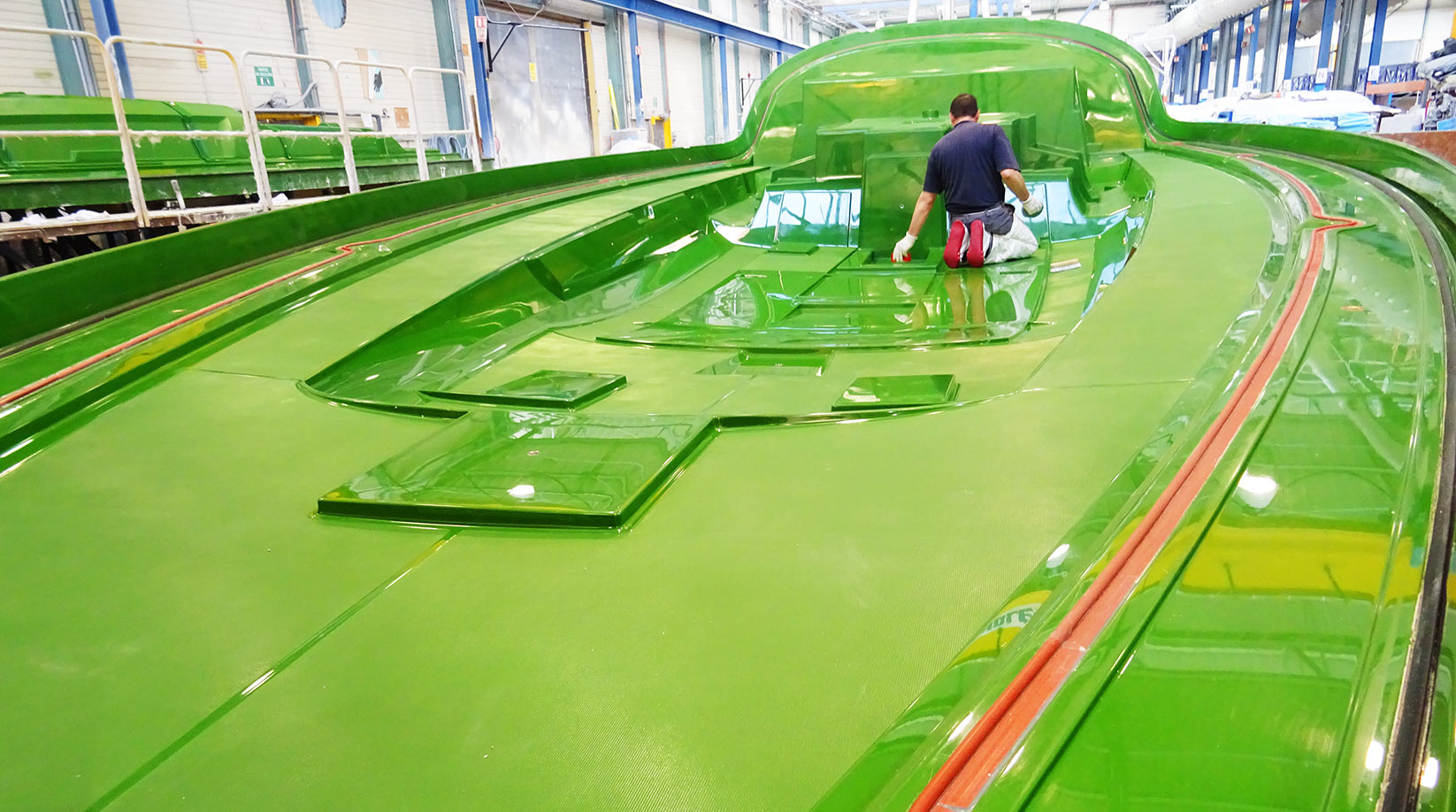
That´s because the workers will get to see where the Gelcoat-layer has a sufficient thickness, and where not. If the mold would be white as well, the distinction between mold and Gelcoat wouldn´t be as easy. As Stephane tells me, they do have blue molds here as well, but green tends to be the best colour. After the Gelcoat-layer has dried thoroughly, the mold will be transported to the next station where an army of women climbs to the flipped deck with virtually hundreds of pre-cut GRP-mats and all kind of sized of foam. The begin to lay the mats and the foam party, all numbered, in a particular manor onto the very positions where they are supposed to be placed.
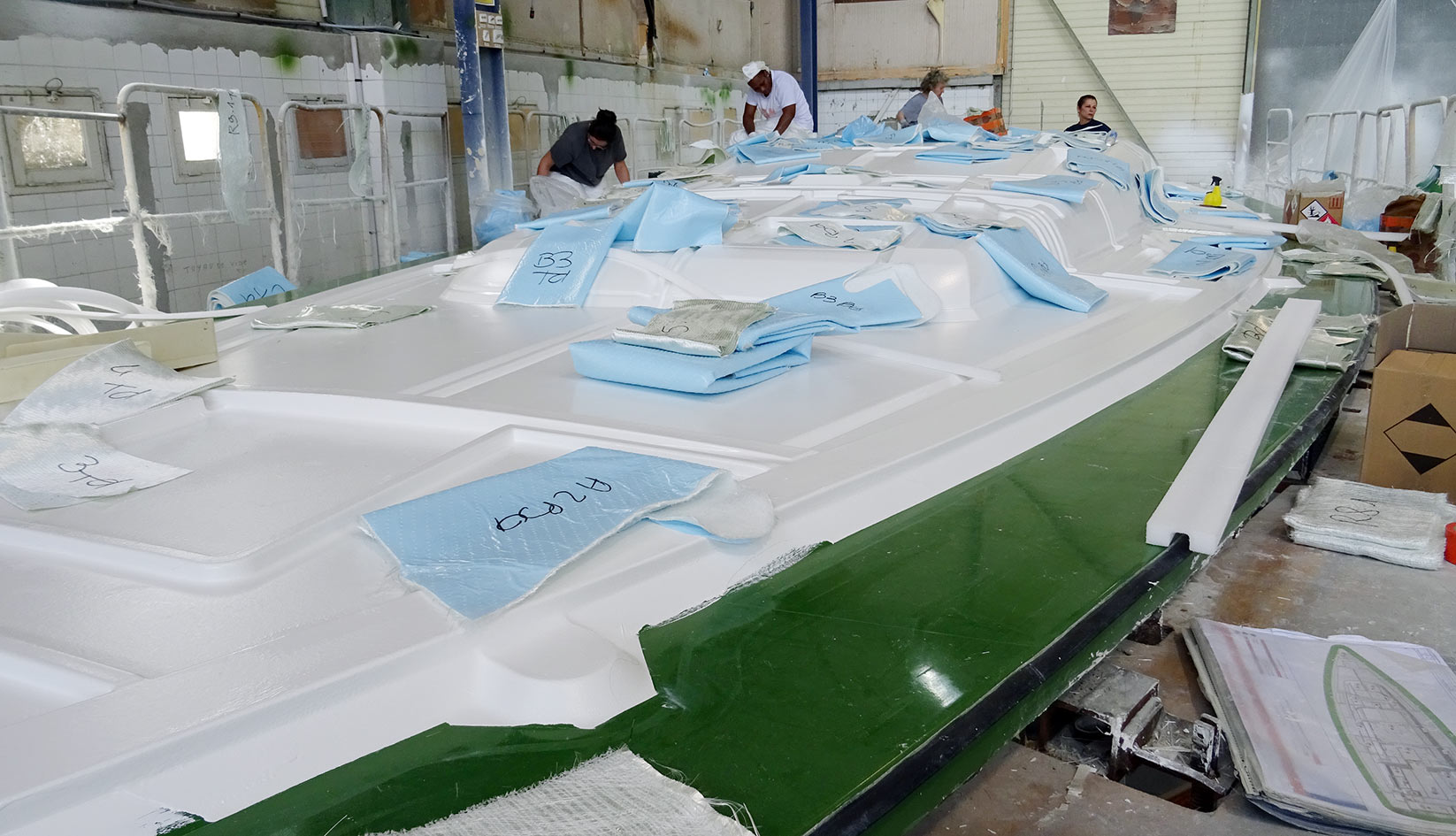
When the decking structure is prepared this way, another mold is put onto this one – the cap, if you want. Now large quantities of resin are pumped into the space between the molds, pumps will create a vacuum thus forcing the resin to creep in every tiny corner of the mold, soaking matts and foam parts, filling every void. This is vacuum infusion. This process takes several hours. Workers regularly check for the quality of the vacuum and after some two days the whole process is done. Then the resin is allowed to dry thoroughly and the molds will be removed: Another deck is born.
The Hull is finished
Whilst the deck is made, the hull will be finished. Because of the fact that all Dufour Yachts are of white hull colour and the colour is “inside” the hull as part of the Gelcoat, there is no need for a paint shop here. The hull will be loaded onto a lorry and carried to the large assembly hall on the Dufour compound. A worker responsible for quality check will have a close look onto the outside and the inside of the hull, every inch is checked for flaws.
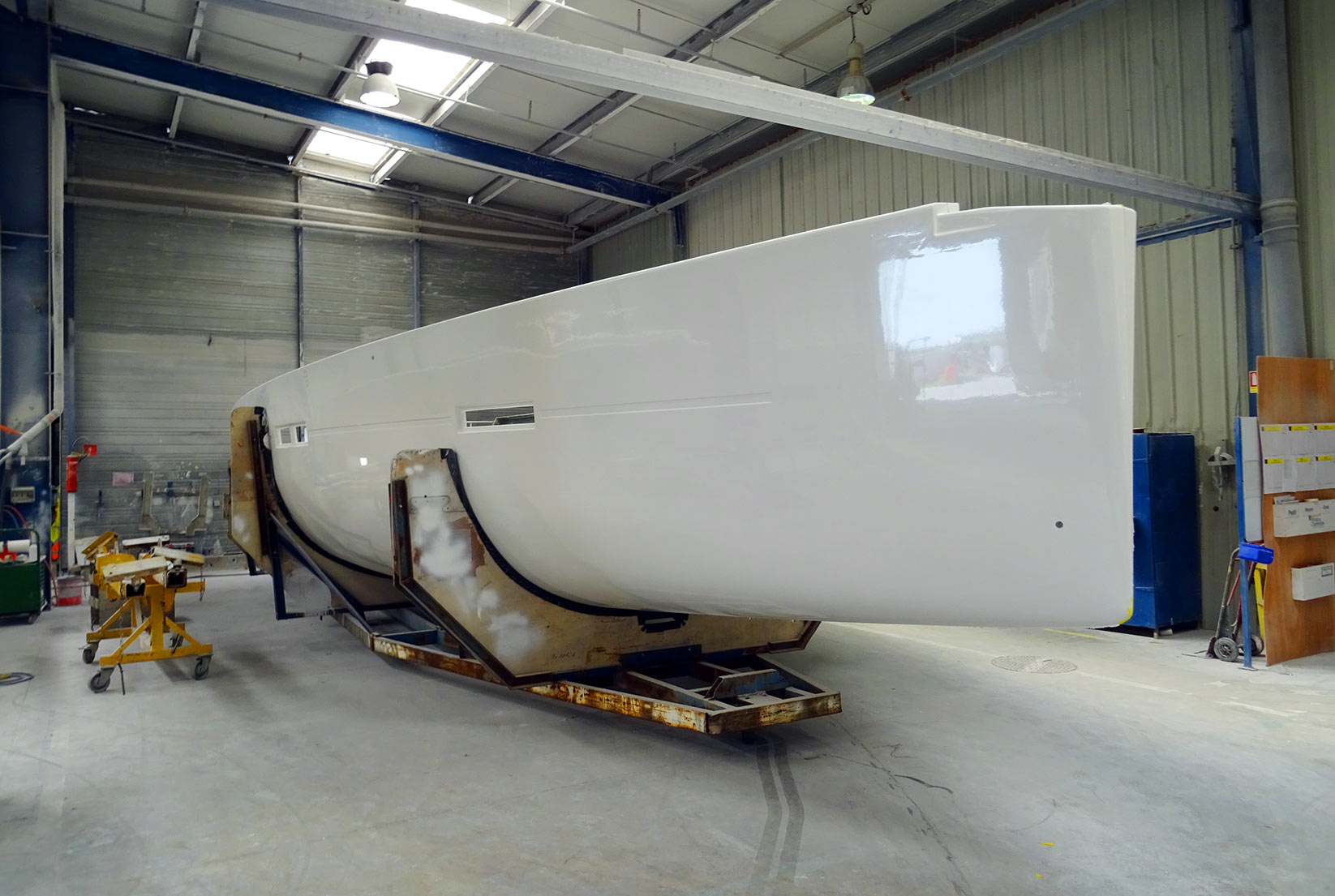
Then the padsaw comes to action as surplus material is removed, the porthole windows and hatches are sawn. Holes for venting, the rudder shafts, the sail drive and the various WC-velves are drilled, minor scratches are redone and the hull be put in place to be fitted.
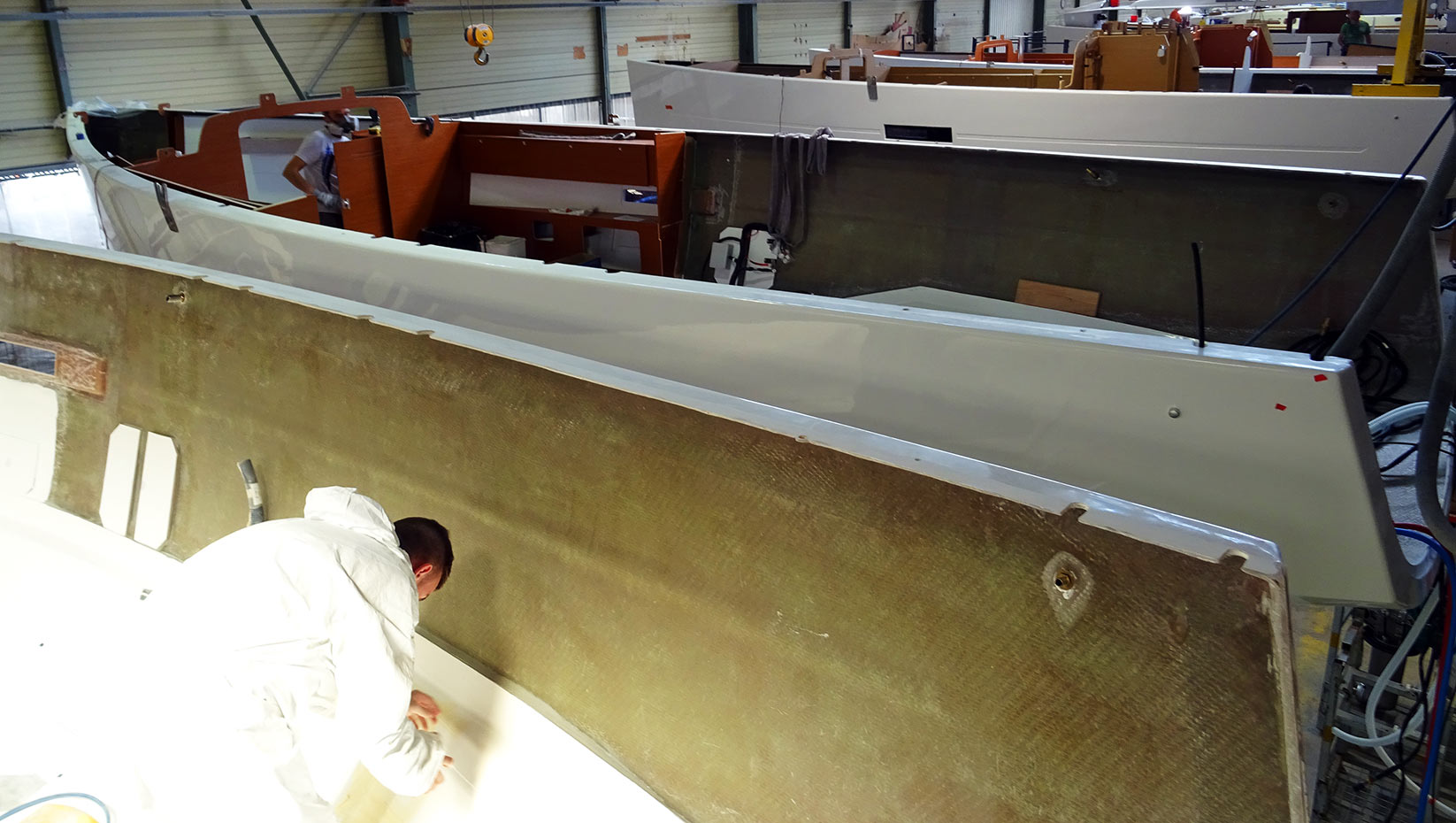
Internal fitting process starts by preparing the hull. Thus, a worker marks with skilfull eyes all the spots inside the hull where the bulkheads are to be placed, where the thick cable harness will e running, generators be put on a stand and all the other parts to be installed. At the same time, every man working on the hull is enganged to keep his or her eyes open for possible faults in the hull as this is naturally very critical: If something has been missed here it will be very hard for the future owner to discover glitches. Constant quality control at work.
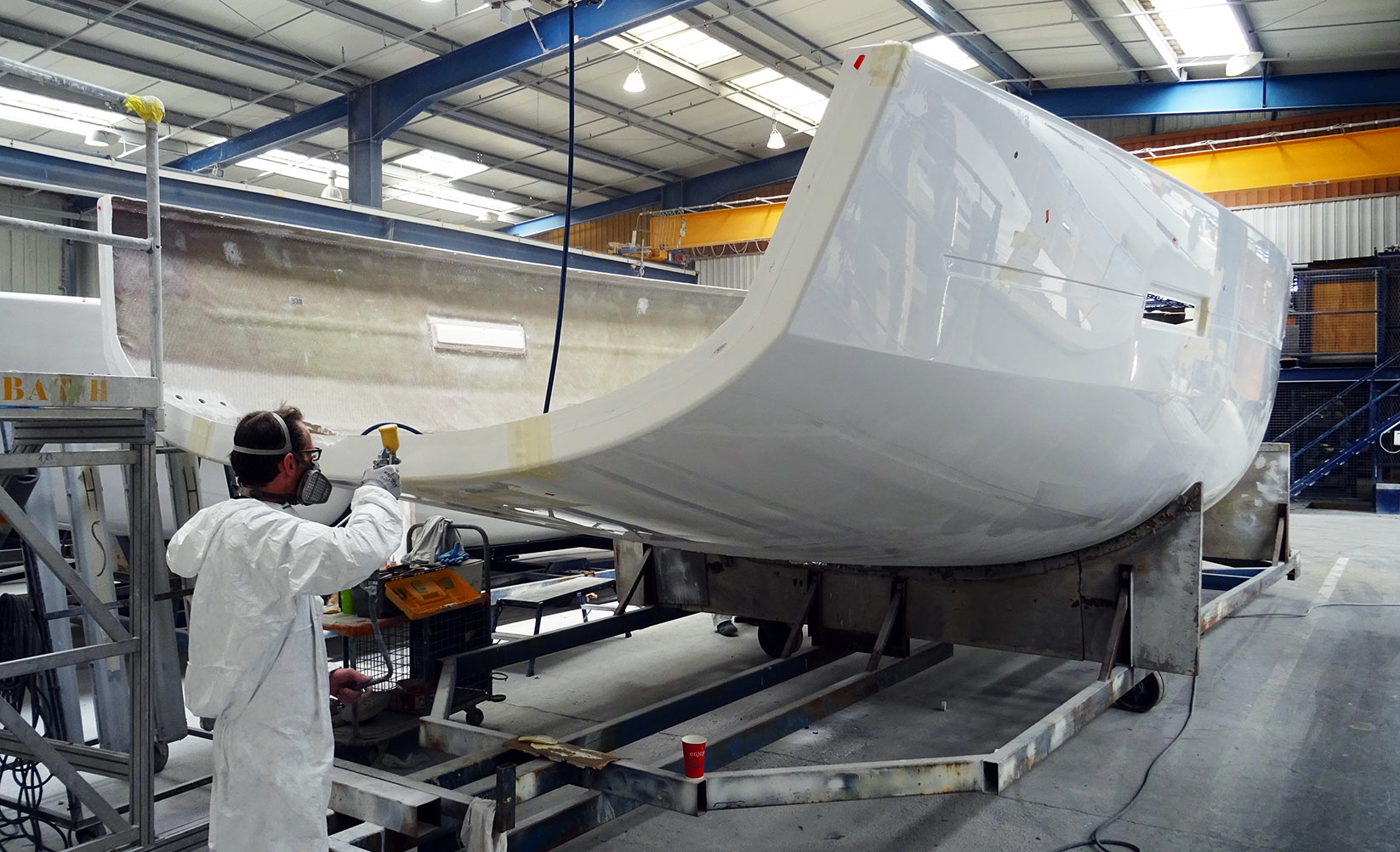
Before the real outfitting process starts, the hull is thoroughly checked a last time. Gelcoat repairs are not rare in this stage. It seems a bit odd because we value our boats as most precious, but I as well had to accept that this is a workshop, a yard where heavy construction takes places. So it´s natural that here and there sometimes things get damaged. Nevertheless, they can repair everything to a state where afterwards nothing will be visible anymore. Good to know.
Fitting of the Interior
Internal fittings always start with the engine, as Stephane tells me. Dufour exclusively offers Volvo Penta engines. As I had learned whilst visiting RM Yachts a day earlier, Volvo Penta does provide for the footings of their engines as well, which was new to me. So after the engine has been mounted all auxiliary machinery is to be installed, including sail drive, generators, batteries and the principal wiring.
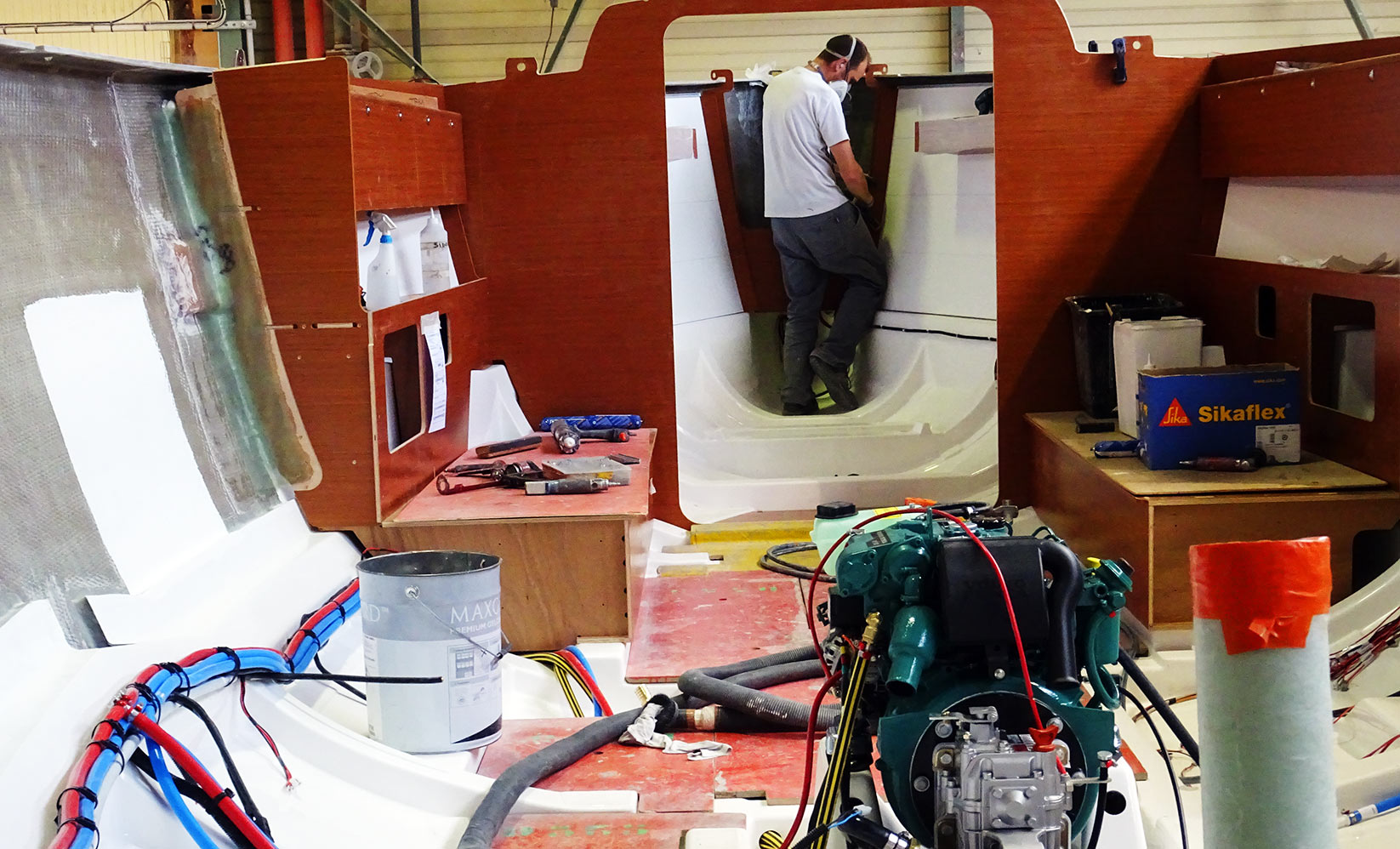
Dufour Yachts offers as the one and only yard in the world the JetThruster-system to be installed as bow (or stern) thruster. That´s a pretty awesome machine: It creates thrust by means of propulsion. A large powerful pump, sitting in the middle of the ship (with the large boats, smaller have the pumping unit in the for peak, read more here), will make water that is sucked into the circle right at the keel to stream through nozzles in the bow – the boat is pushed to either side the Skipper wants. This system is more powerful, less noisy and far less prone to problems than traditional bow thrusting systems. Besides, it can create a constant push of water, making landing a no brainer. When ordered, the JetThruster-system is installed as well now.
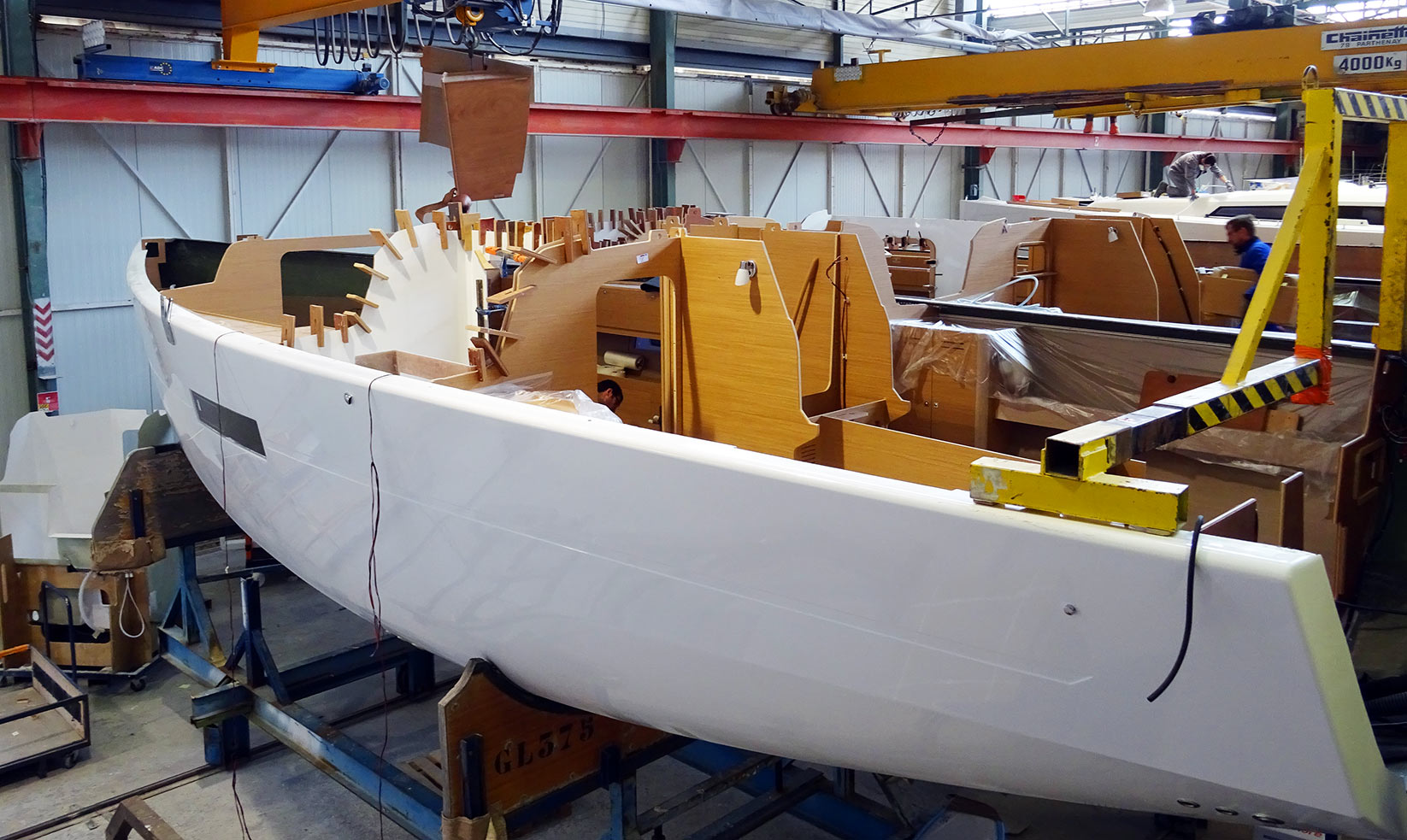
Now all the joinery arrives at the assembly line. From big to small, the bulkheads are the first to be mounted. All bulkheads will be laminated onto the outer shell with multiple layers of GRP and Epoxy resin. Joinery is pre-fab somewhere on the compound and delivered just in time to the hull to be put in place. What I honestly found a bit odd was that – from my point of view – there are no internal enhancements for the shroud-chain plate-combination nor anything in the keel section like seen with Grand Soleil, X-Yachts or RM Yachts. They say they don´t need it as the bare GRP hull is strong enough to take the loads.
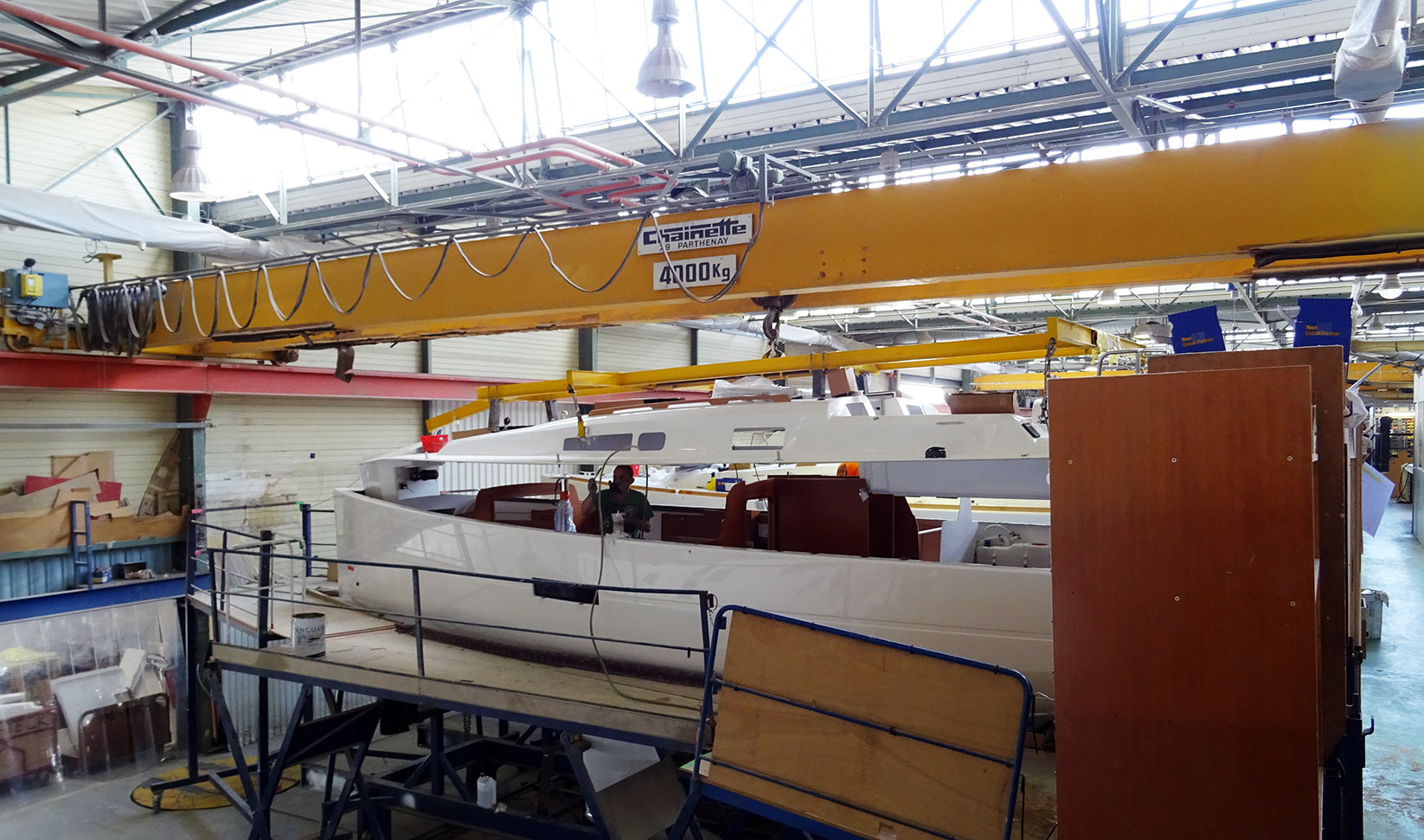
The so-called marriage is a very defining moment for every sailing boat. That´s when the deck-part is lowered onto the hull and finally both are put together. With Dufour, that´s a matter of both putting screws through deck and hull and mounting it tightly my mechanical means plus having strong Epoxy glue forming a firm chemical bond between them two parts. Now with the deck ready mounted, basically, the hull is turned into a boat.
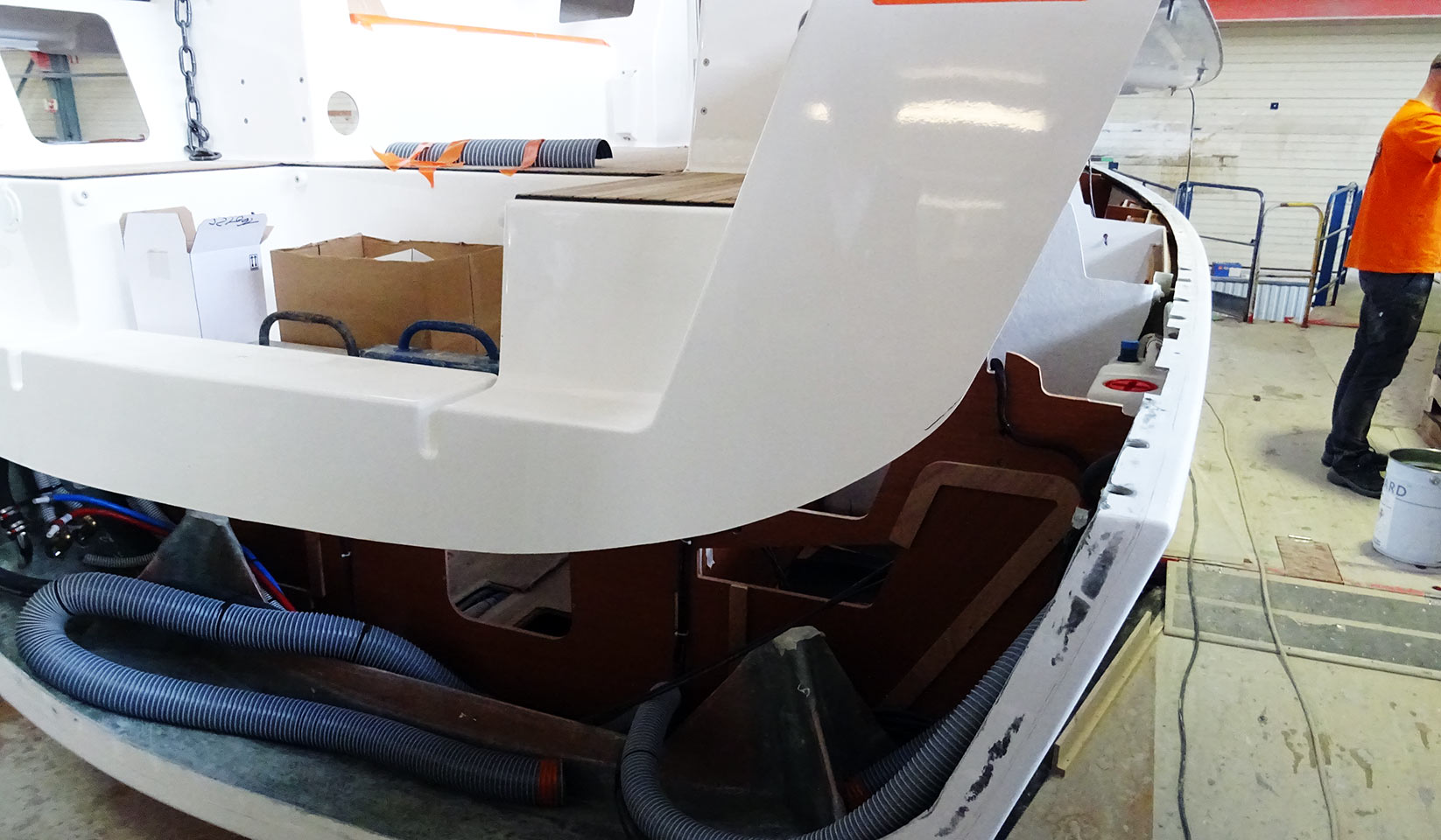
Before closing the gaps of course, everything is checked a last time thoroughly, because if something might have been forgotten to install or has been installed the wrong way, now it´s the time to change it because if the deck has been fitted, naturally, reaching things inside and every take out and fit in new parts will be a pain in the ass as – even with the big boats – it´s a hell of a narrow thing!
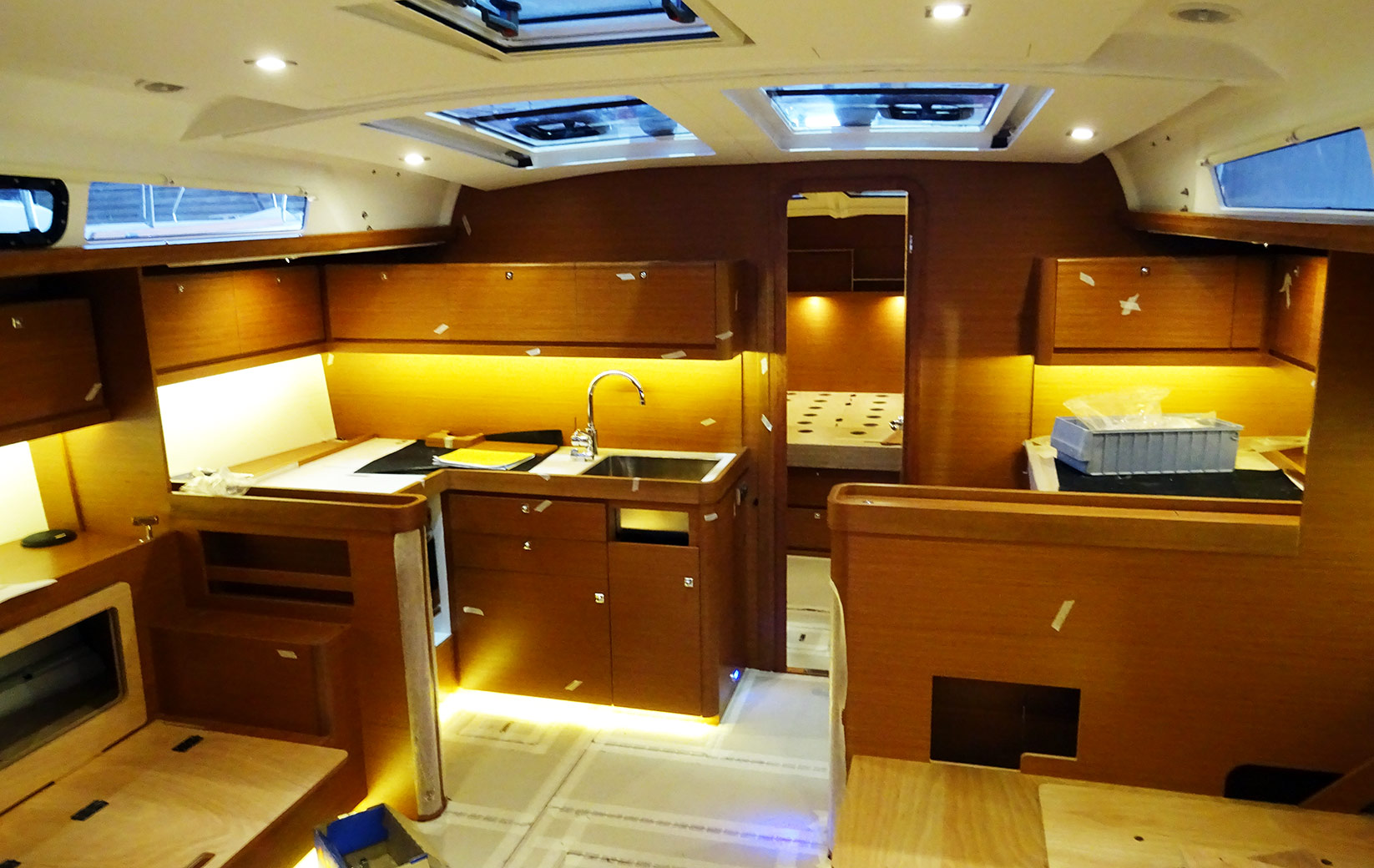
After putting the deck onto the hull, the new yacht basically has everything she needs already installed. Down below deck there´s just some equipment missing like fridges, stoves and stuff like that, but all furniture and LED-lighting has been installed. When I was visiting a Grandlarge 460 I was puzzled by the amount of work that has been done here – it really goes so fast!
Another Grandlarge is ready for the Grand Tour
Stephane takes me to the outside of the large assembly hall: He says, that after some weeks on the stand here the yacht is finished and equipped with everything the client had ordered. We come by an area where new keels have been piled up: Standing next to the massive construction of a keel belonging to a Dufour 412, I can clearly see the thick keel bolds – and there are plenty of them. Good to know.
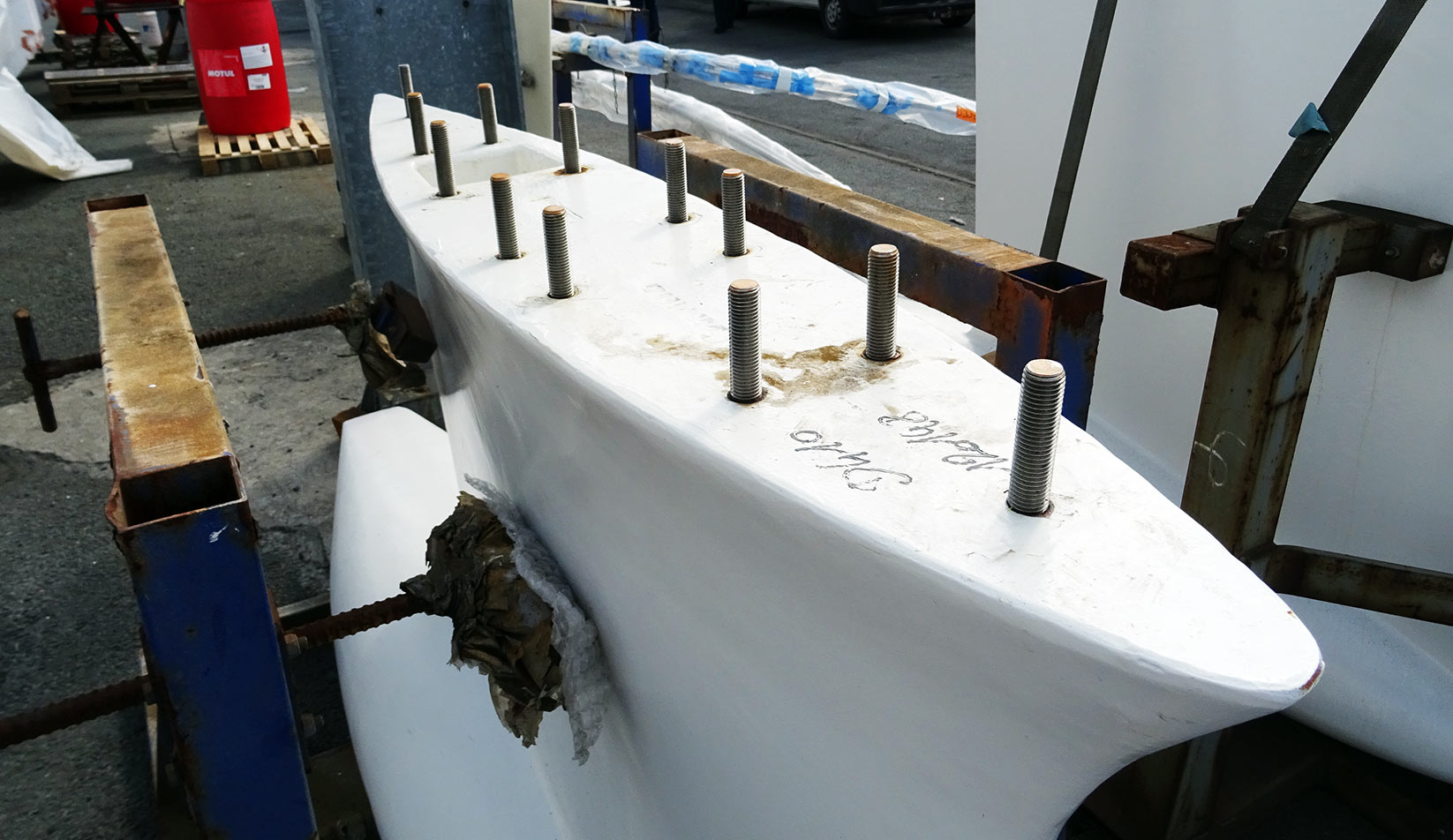
When the boat has passed a “dry quality check”, it is then brought to a large basin. Some four to six yachts fit in this “Dufour Ocean” at once. A large crane lowers the boats and that´s the first time ever the yacht meets her natural element. In this basin, at first, the engine and all connected machines will be tested thoroughly. This is why a brand new yacht´s engine does bear some engine-hours. Rudder, valves and the general tightness of the hull is checked as well.
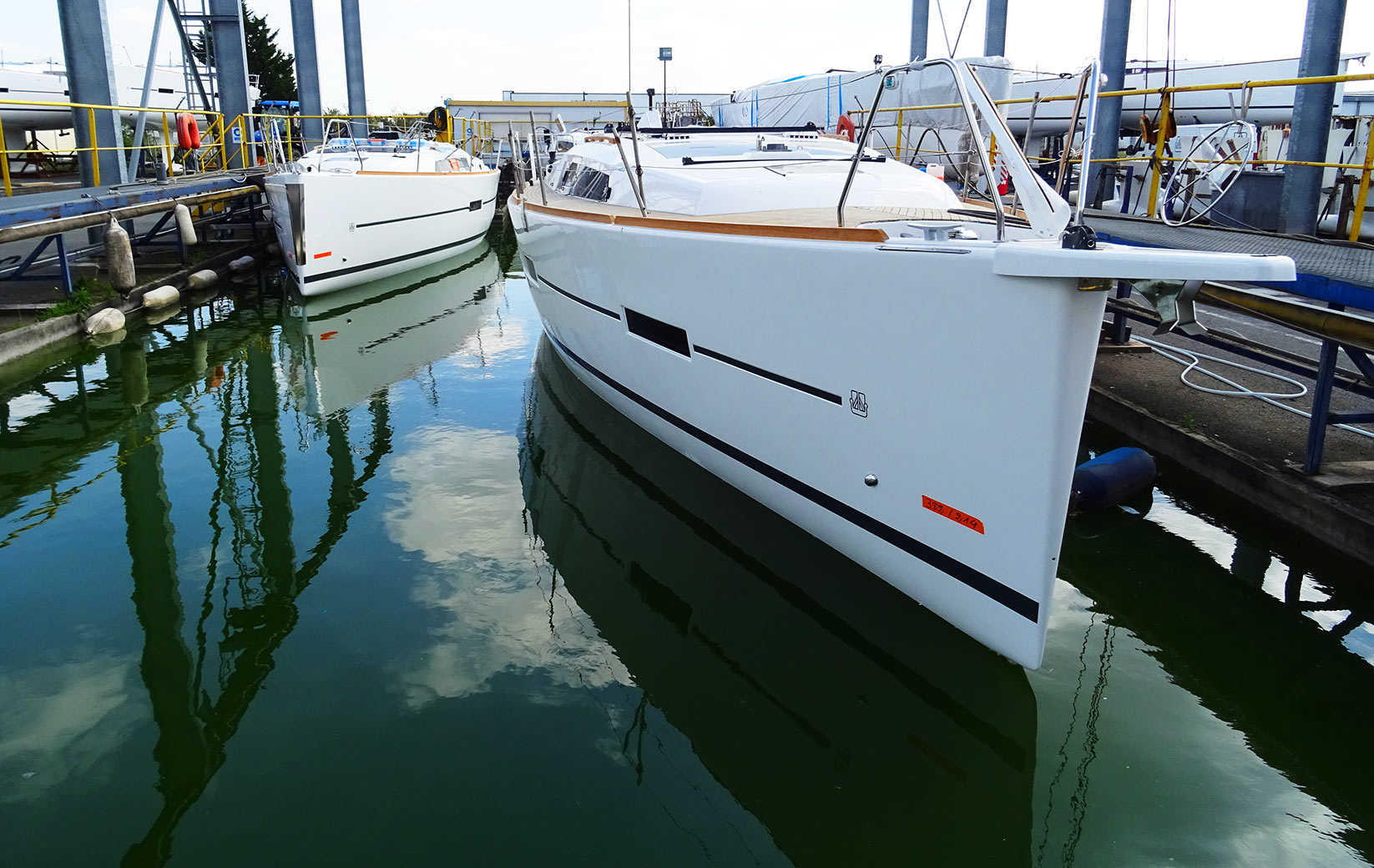
If passed, the upper parts of the boat is checked, because the Dufour-people can make it rain. Thus, simulating Ocean spray and rain, all hatches and seams of the decking structure can be checked if the inside stays nicely dry. A boat will stay for multiple days inside the basin before it is again hoisted out and on a dry stand – put somewhere in queue like dozens of other yachts I can spot on the compound.
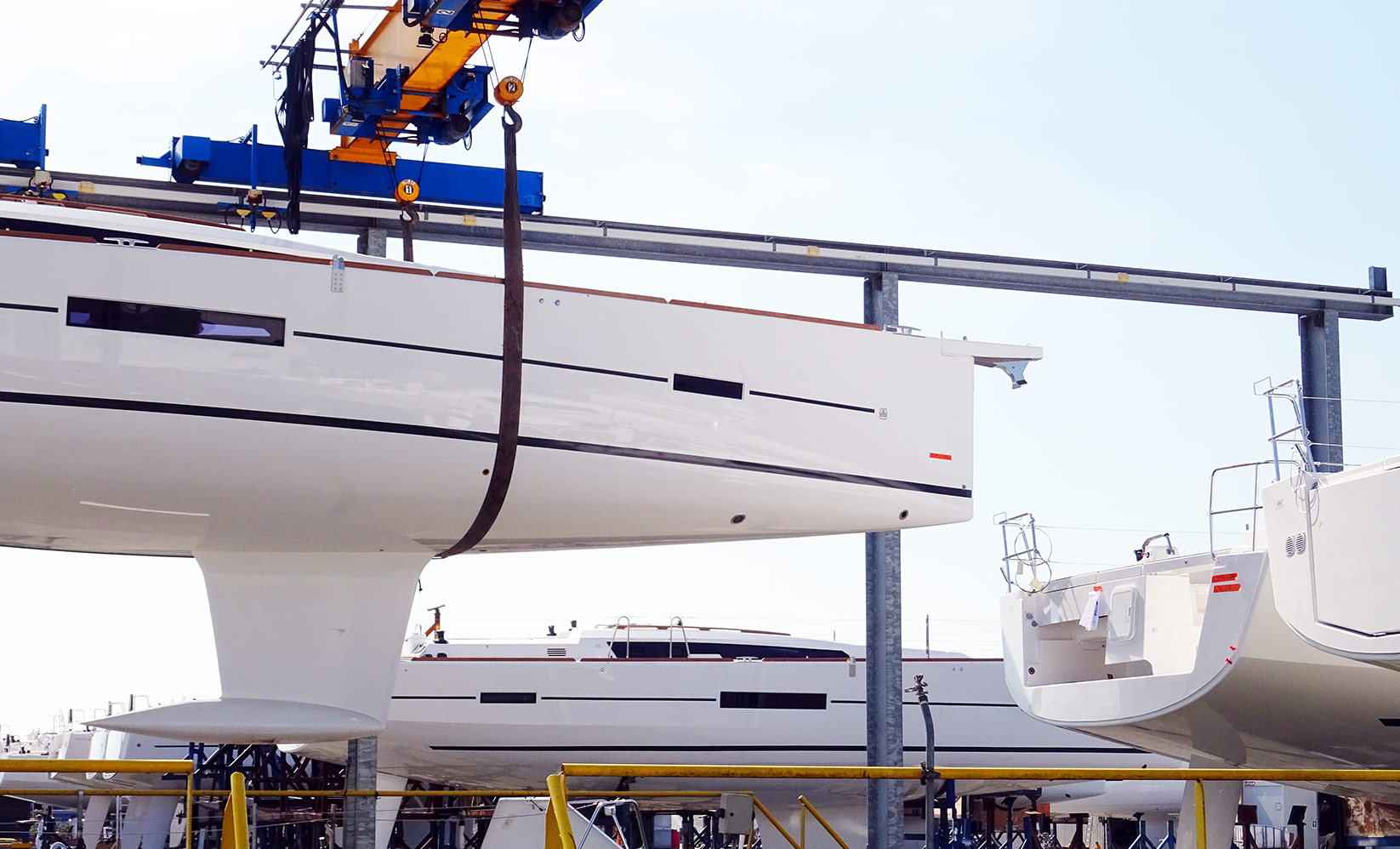
Last but not least is the final acceptance. That´s when a quality managing team roams every corner of the inside and the outside with a lot of check lists to cross off dozens of items from the list: The standard quality check of course, the standard fittings check and the very individual items the very client had ordered are all looked upon to see if everything is completed and made in a perfect fashion. Aftwards, the boat is declared finished and the client (or dealer, to be precise) can arrange the new yacht to be transported.
Building Quality of a Dufour Sailing Yacht
Dufour Yachts is as impressive as every yard I´ve seen, but this takes boat building to a new level. At X-Yachts they barely make 120 boats annually, RM makes 40 and beloved Luffe of Denmark not more than 15 or 20. As being number 4 of the world in terms of the boat output, I know have seen what a large series production of sailing yachts means. It means that this yard is a place bristling with a load of people, a staggering amount of hulls in various states of the process being placed virtually everywhere. I know that Dufour yachts are sailing like hell from my Atlantic Ocean trip on a Grandlarge 460, now I know how these boats are made.
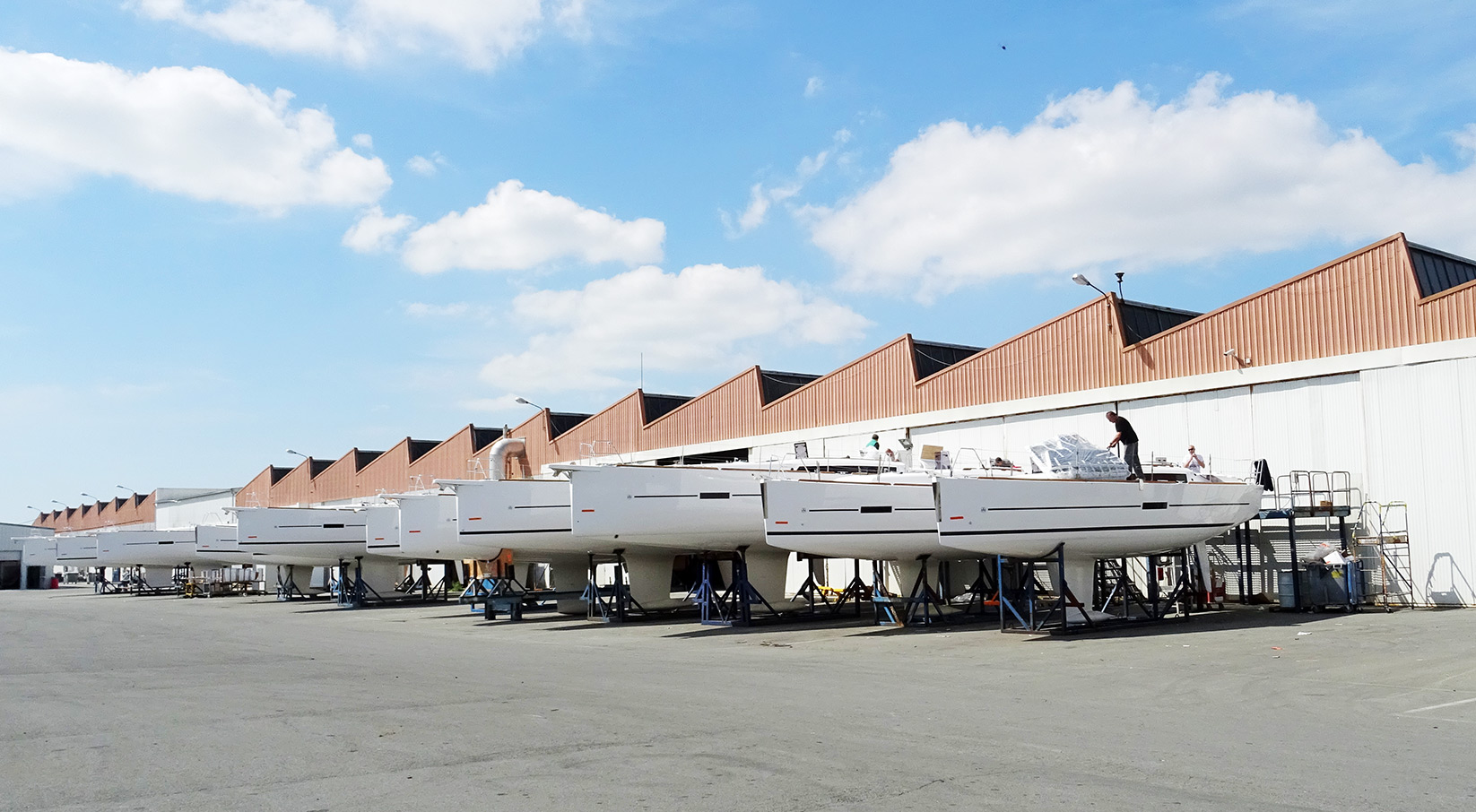
Dufour is of course no small exclusive manufactury. It´s a large production plant putting out huge numbers of boats. One per day in average, as Stephane tells me. If this is number 4, what must it be like to see Beneteau with even double the output? I have seen good people working here, everyone greeting and smiling. Boatbuilding, even in this scale, is still a matter of handcrafted work: Having the time and being encouraged to do their best, a happy workforce and kind of nice surrounding is the key to a good product. Both of which I could see here in Perigny for sure.
Other interesting articles on that topic:
A Day at Luffe Yachts in Denmark
Talking to Dufour´s Naval Architect Umberto Felci on designing a Sailing Yacht
The Dufour 310: So big that small