I am increasing the rating on a daily basis when it comes to commissioning my new boat. More and more parts for the sailing equipment arrive regularly, the application for an MMSI and call sign is being worked through by the authorities and slowly but surely my home flat fills up with various parts from A to Z. Same happens in the big showroom of our company where GEKKO is currently situated. After receiving her antifouling she is ready for the next steps.
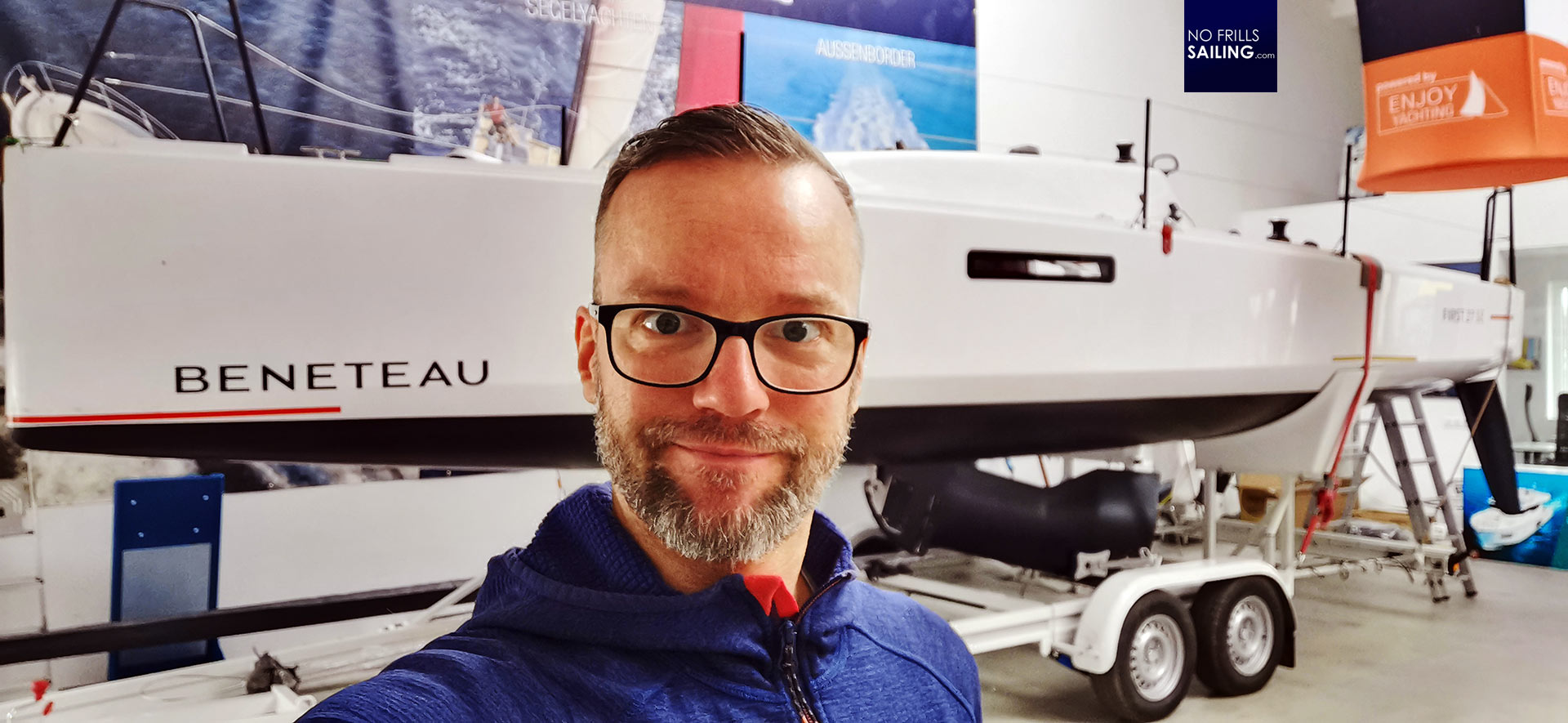
Last week I took a day off and “hired” our master-rigger to pre-commission the while boat. The idea was to have everything rigged and readied for her big day when she will see water for the first time (which is an appointment within the coming two weeks) and to exercise all steps of readying the boat under professional supervision “on the dry”. Also, to check for any possible glitches and receive answers for any upcoming questions.
Carbon mast transport of a First 27 SE
But before that I encountered another big task I´d have to tackle the coming days: Mast transport. There are numerous ways to safely have the big mast lashed to the boat on the trailer. First I must admit that I failed to tick the box for a mast stand for the trailer. If your supplier offers that: Use it, it will spare you some of the trouble I am going through now.
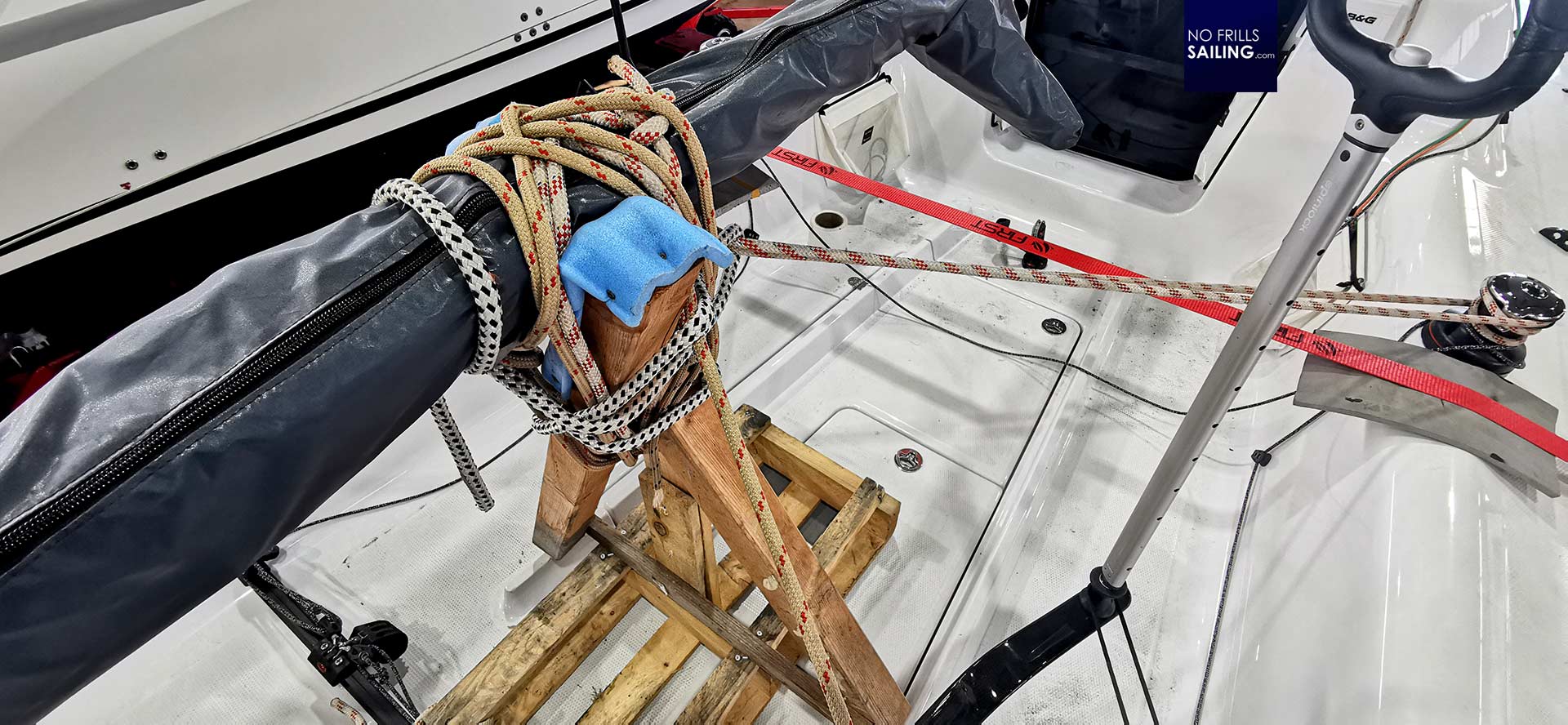
Nevertheless, I am used to manufacture wooden mast stands as I had to do it for my first boat as well. For her first two or so kilometres from our yard to the showroom we timbered a rather short-lived makeshift mast support for the rear end, fitted an old fender in the middle to prevent the carbon from bending too much and secured the mast top on the pulpit with a thick wooden lug.
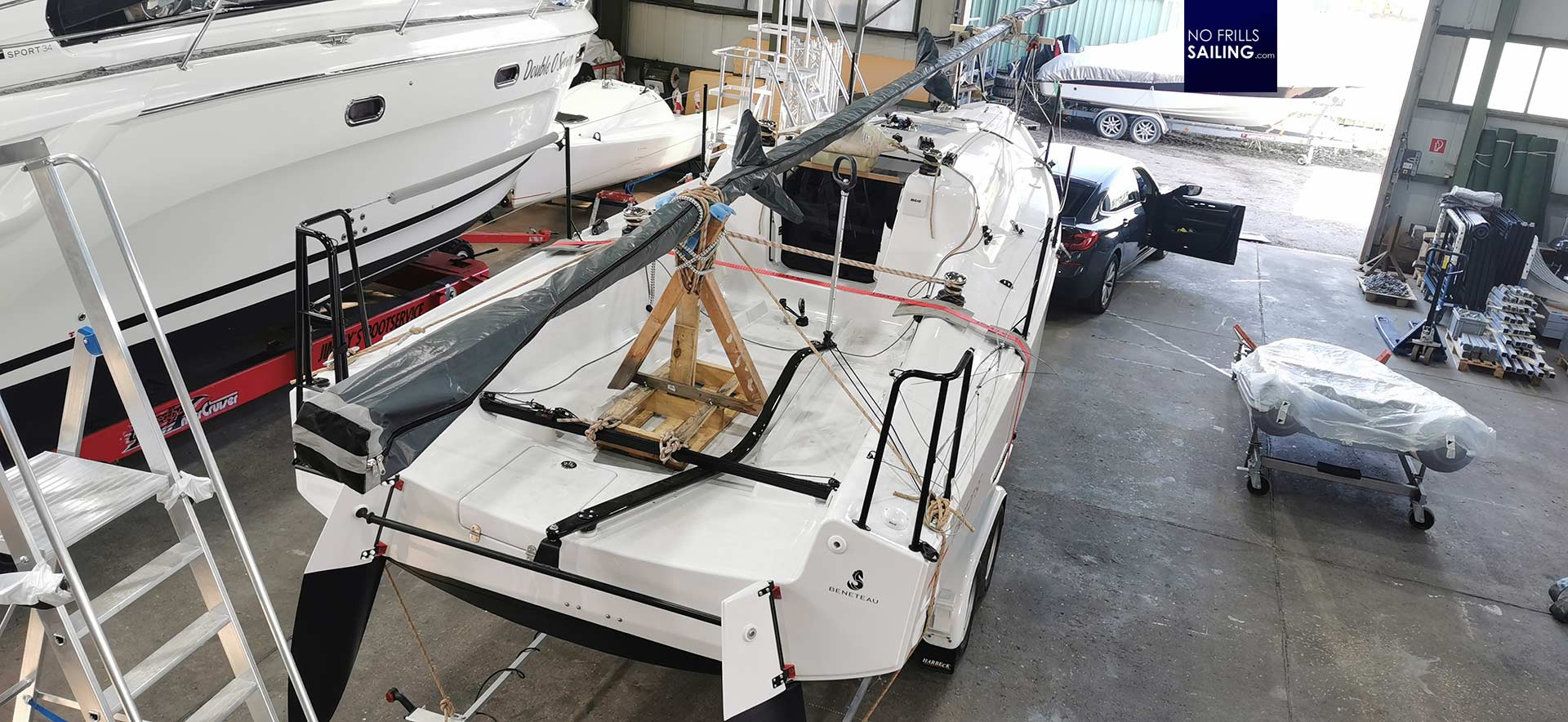
Unloading the mast in our showroom I took elaborate measurements and will start to make a really good engineered mast stand for the boat next week. That is for me a crucial part which will not just have to make sure that the carbon parts arrives in one piece and intact but also to last for many, many more transports in the future: Being mobile is a key feature of this boat and was a big pro on the “which boat to buy”-list.
Checking all parts of the Torqeedo electric engine upgrade
The biggest item still open on the to-do-list for the boat is the integration of the main engine. After having visited a number of smaller First 24 boats sailed by our clients I refrained from ordering the Tohatsu internal combustion engine for my own boat. I decided to opt for the electric option. That is – honestly – almost ten times (!) more expensive than a simple outboard engine, but bears only advantages.
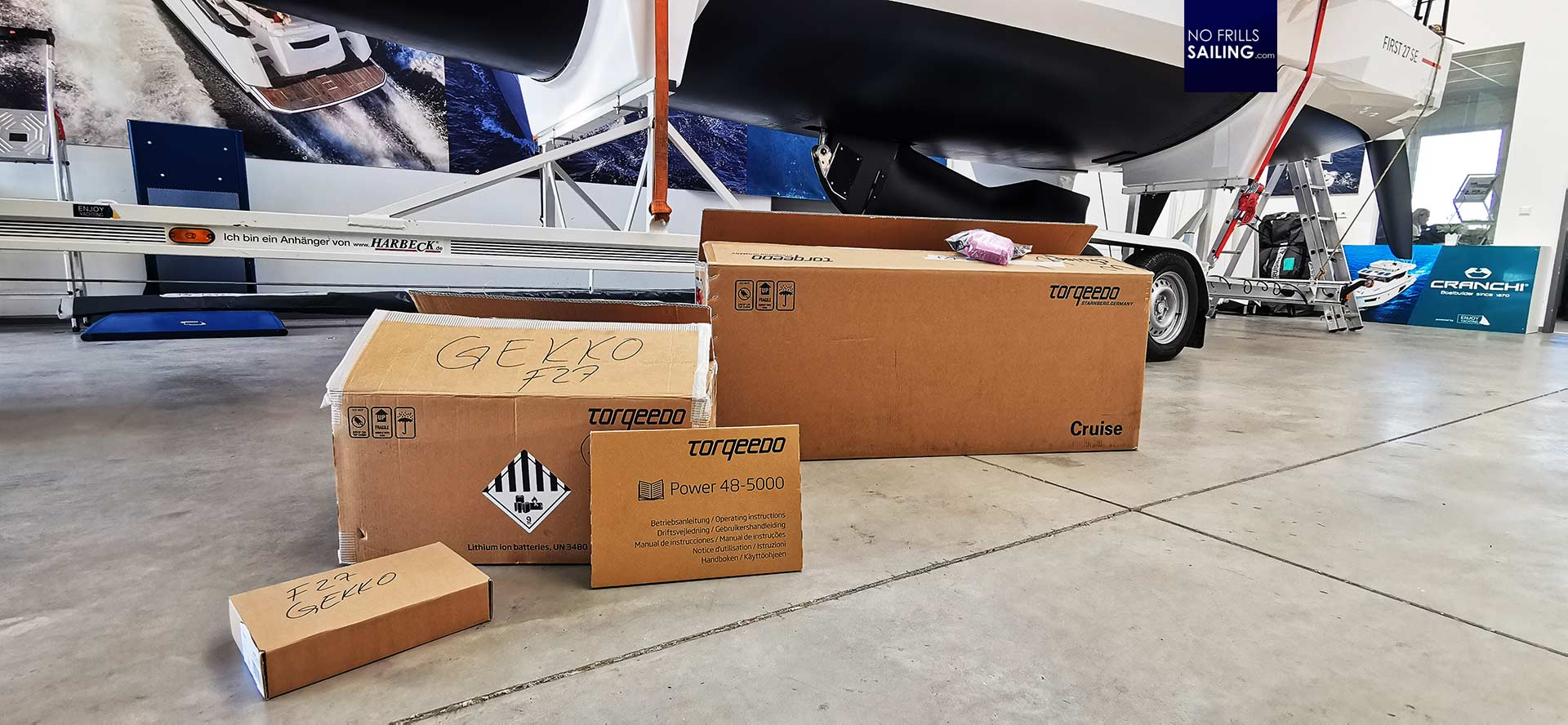
No smelly, dangerous fumes from the gasoline. That was the biggest point for me to order the Torqeedo. As you may already know, I do have two small kids which I do not want to expose to this carcinogenic agents. A gas driven boat will always start to adapt this awful smell in a short time. Secondly, I hate the crackle and loud sound of the outboard engine and don´t find that these engines aren´t all too reliable, especially when the boat sailed kind of wet over a period of time.
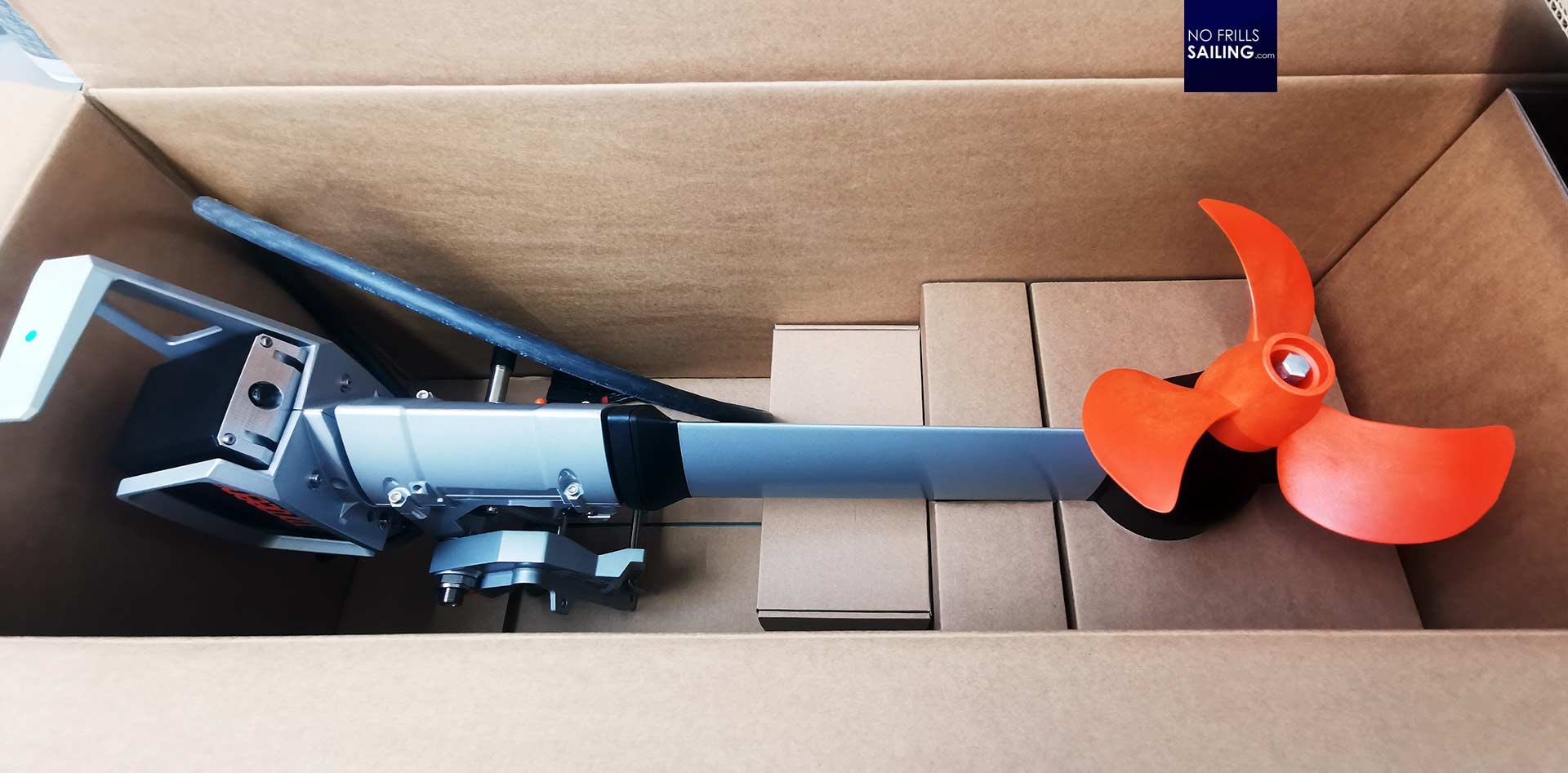
The Torqeedo may be installed by the yard but we wanted to receive the full experience and decided to have the installation done inhouse for exercising purposes and getting to know the material. It´s honestly a very impressive set of big, heavy cardboard boxes arriving to our showroom. The Cruise 4.0 equals a combustion engine of up to 10 horse power, more than sufficient for propelling the 1.6 tons weight of GEKKO I´d say.
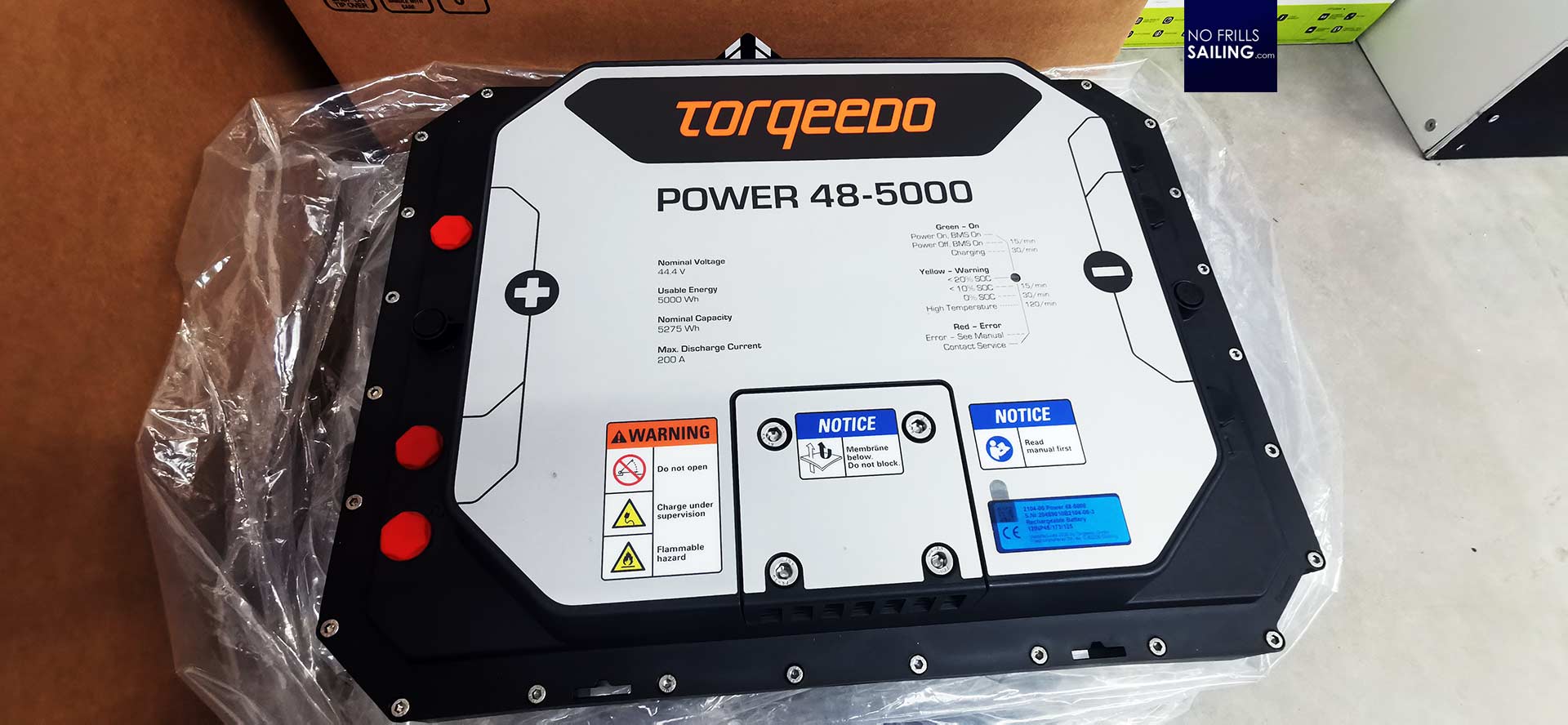
Most impressive part of the set is the heavy duty WH 50-4800 Lithium-Ion-Battery which weighs in at some 36 kilograms. It´s a fascinating piece of engineering, software and product design. I am going to cover the installation of this setup extensively in upcoming posts as well as noting all relevant data of the Torqeedo electric engine setup when installed and in the water. Not to mention the interaction of the ensemble with the later to be installed custom solar-panels which are currently being manufactured.
Mast, standing and running rigging of the First 27 SE
We prepared the mast by laying it down. I am lucky as the main part of the job been had already performed in Slovenia by the guys from the yard. They had used my boat for an extensive shooting for the new line-up in 2021 and thus all halyards and other lines and almost all of the blocks had been fitted to the mast.
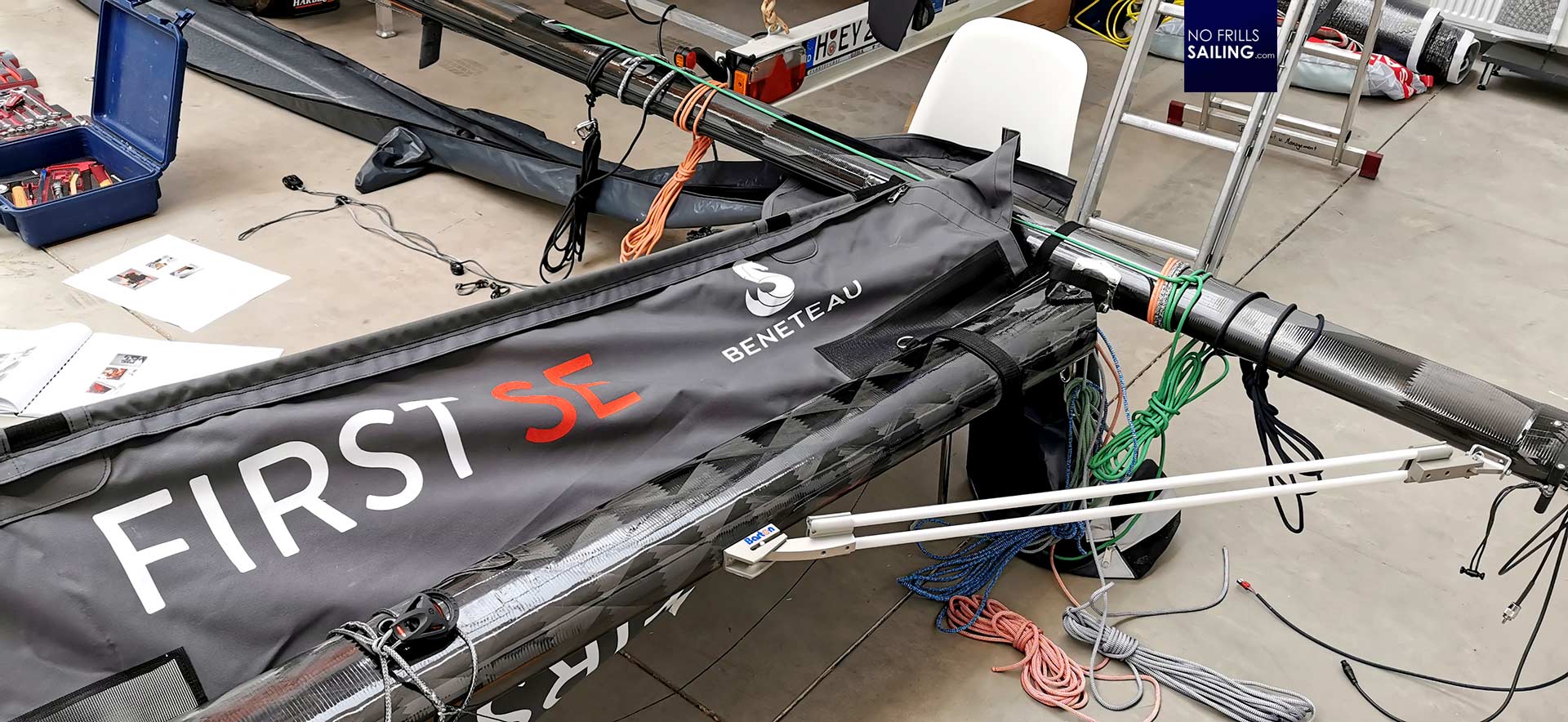
I opted to order my boat both with rodkicker option (I hate it when the boom is in the cockpit) and with Lazy Jack/Lazy Bag-option: Taking down the mainsail is a pain in the ass on the First 24 SE already, this big-ass sail on the 27 is nothing I´d like to take off the rigging completely in sailing mode. So we fitted the Lazy Jacks (which is a no-brainer) and the bag. I was very relieved seeing this working out so nice and smoothly.
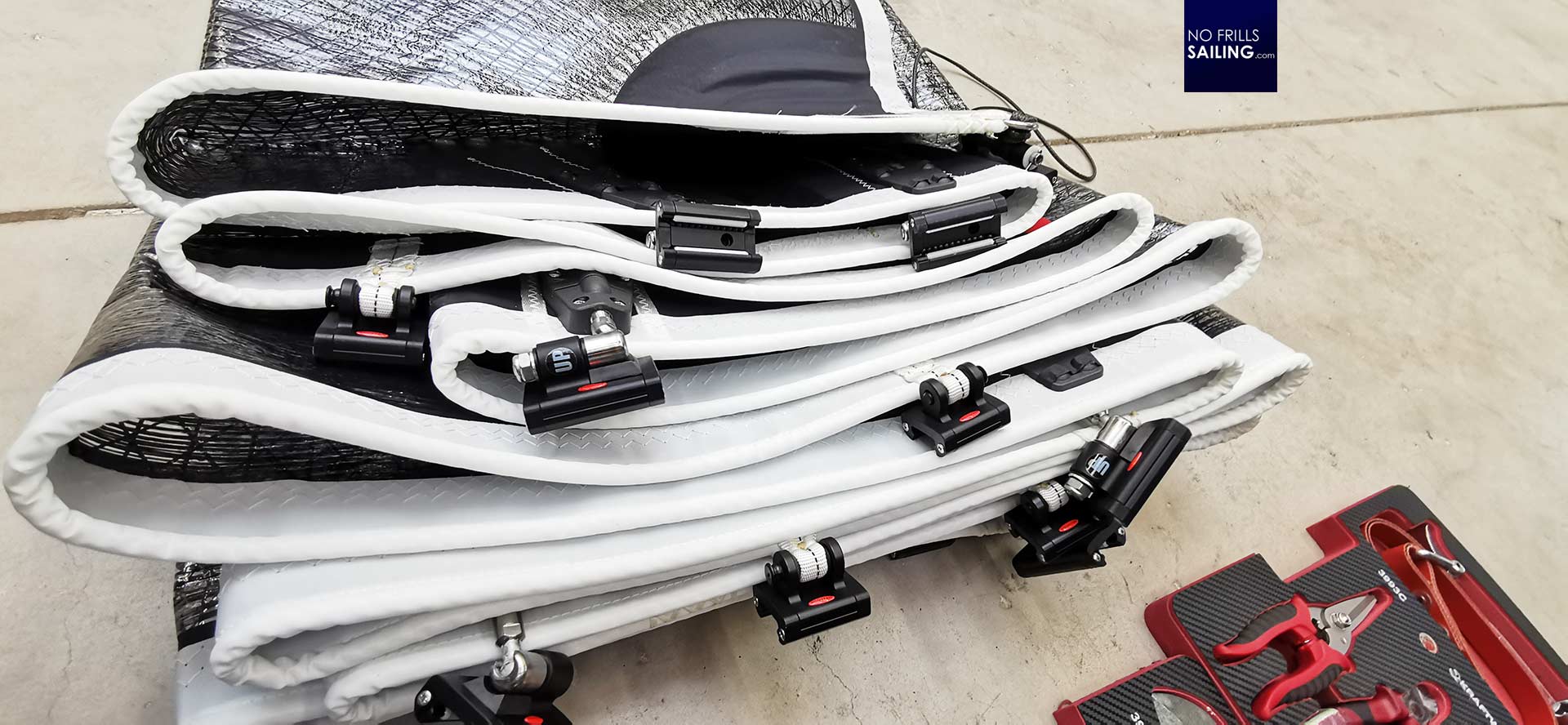
The whole point of this day for pre-commissioning was to learn as much about readying the boat as possible. Normally, when you arrive in the marina for crane-action, there´s lots of action going on. The crane operating crew has a day packed full of boats they need to be putting to the water and having their masts stepped as quickly as possible. So there normally isn´t all too much time for newbies to figure out their new boats: As the queue behind them is long and people quickly get frustrated. In this, it took us a full 8 hour day to “dry-train” on the boat how to set it up the right manner.
The last boat to fly One Sails cloth
Now, let´s check the sails. In fact, the First 27 SE – originally conceived as Seascape 27 by Sam Manuard and the crew around Andraz Mihelin of Seascape – have had a contract with One Sails. Now, after joining the Beneteau Group, somebody somehow made the decision to have all boats from 14 to 27 feet – now re-branded as “First” – fitted with North Sails. In fact, my boat, hull number #122 is the last one to receive the sail cloth from One Sails.
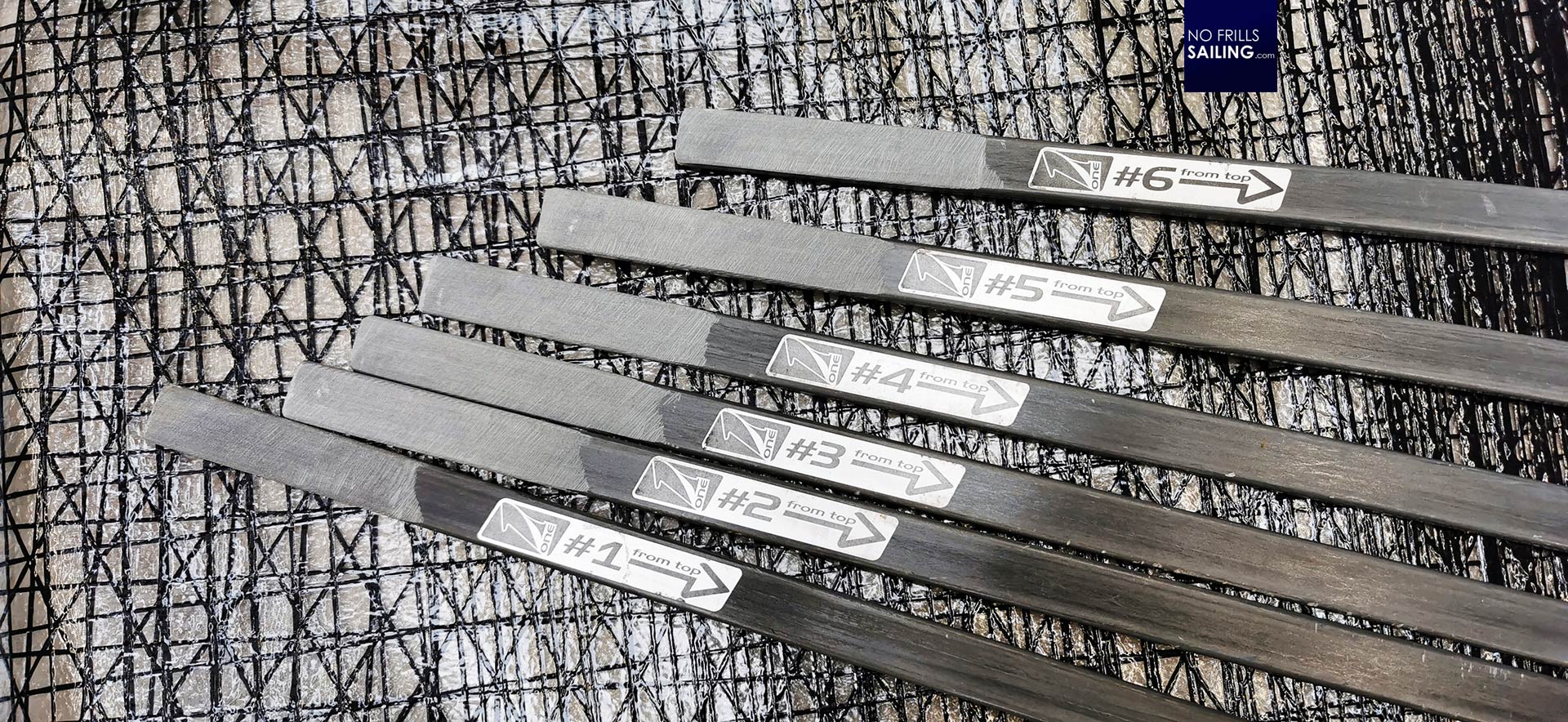
I must say that I like this fact. One Sails as an Italian company has a well-known represaentative situated not far from where I live and it feels kind of “special” to have the sails on GEKKO. Everybody has Elvström, Quantum – honestly – is too expensive for me right now and by checking the quality of One Sails after unboxing the sails I must say it looks awesome!
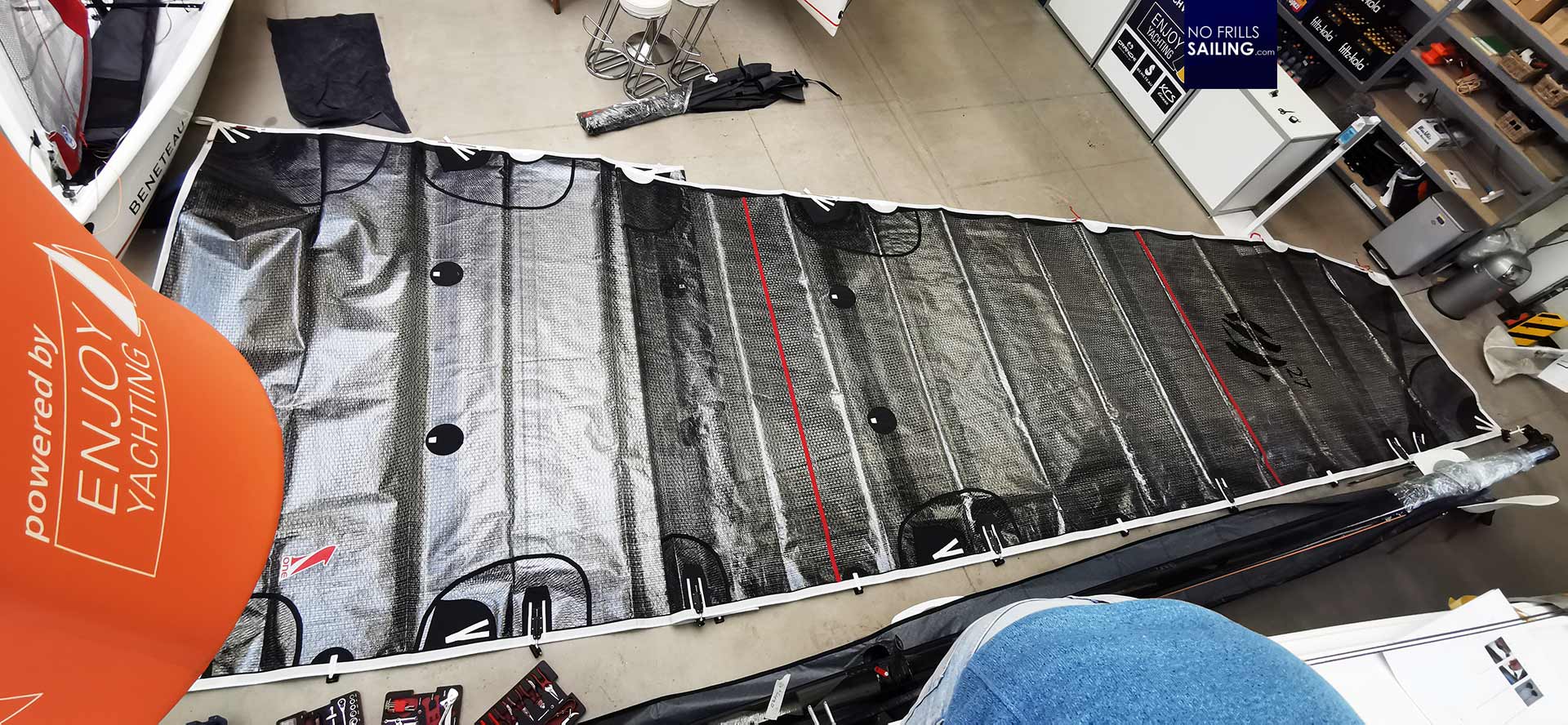
The main sails is a big bastard, the Genoa even more impressive. For the mainsail I fitted the batten which I must say I have never seen better manufactured mainsail batten than these by One Sails: Their front side was sanded down a bit to better fit into the batten bag, the quality of the fiber is of such a kind that you do not get any splinters into your hand skin when working with them. There are numbers imprinted: Just a very small service but so nice, making fitting even quicker. The garment and quality of the laminate of the sails is impressive, a dense and thick quality that I guess will last a couple of years.
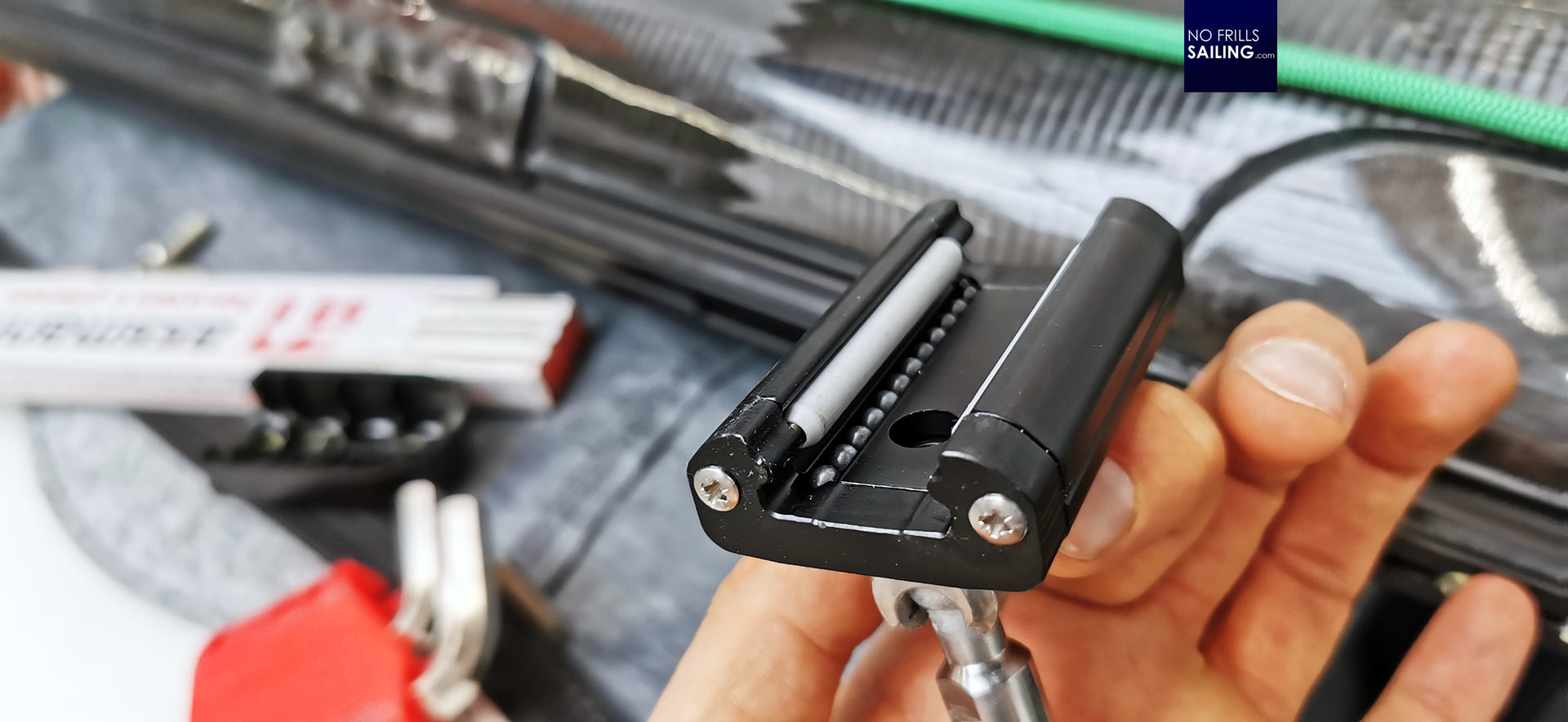
I also was very, very happy having invested a surplus budget on the option for ball bearing mast sliders. The standard sails will be hoisted with simple sliders in a track, made from plastic. Apart from the fact that these will give way to wear and tear much faster, I don´t like their “gruff” behaviour, especially when wet. Now, looking at these massive sliders and checking how easy they slide up and down (well, side to side on this day) the mast, I am looking so much forward to having lessened potential trouble hoisting and most of all taking down the main.
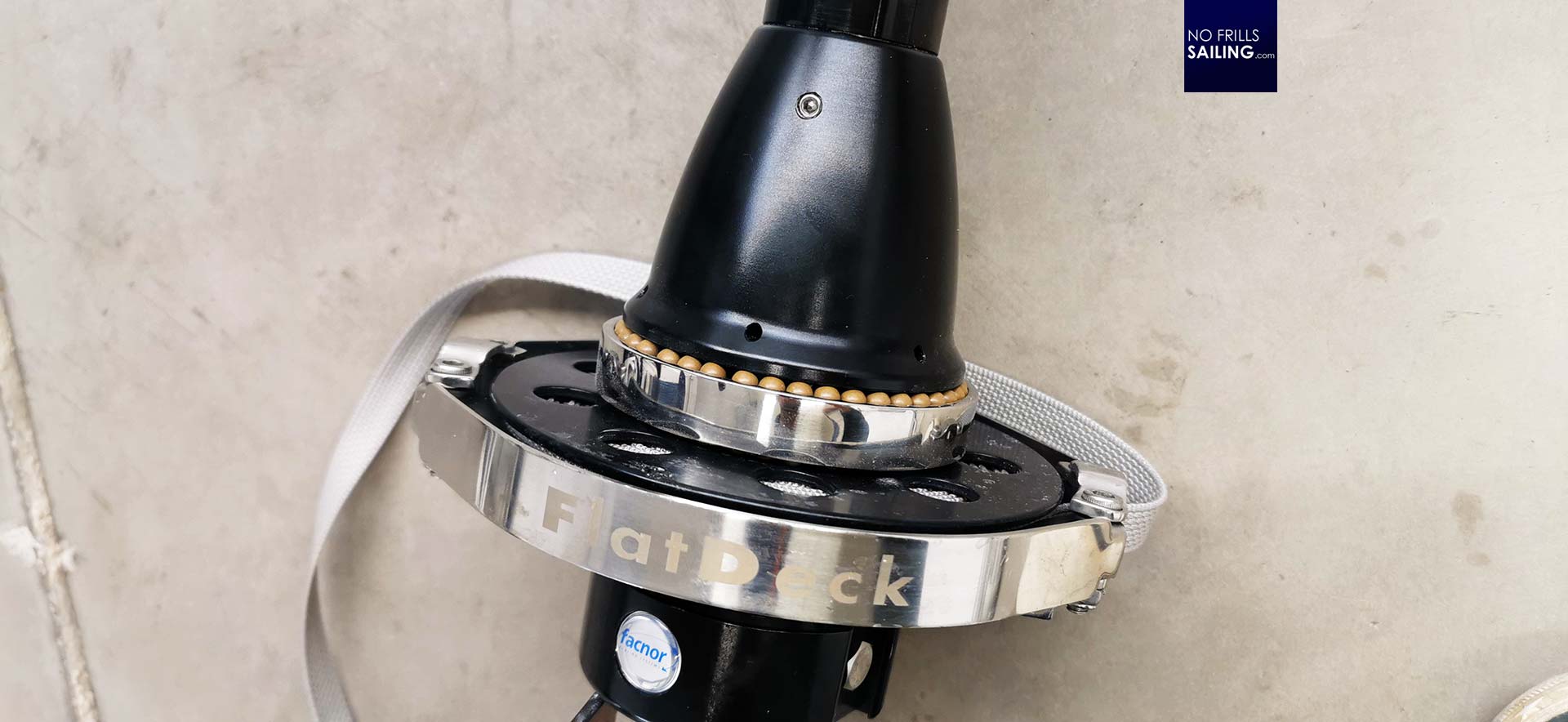
Another upgrade was the Facnor FlatFurl for the Genoa. This not just slightly increases sail area but also improves the performance of the sail as the area around the foot of the sail is the one producing most of the uplift. The Facnor furler is a massive and impressive piece of engineering as well. We pre-fitted the aluminium forestay and exercised how we´d set it up prior to putting the boat to the water.
Pre-commissioning the boat on dry
All in all it was a very successful day. I drove home and spoke to myself that I was now relieved and happy. Much better feeling now, as this boat will be the first ever I will be rigging without utilizing help by a professional. Well, I of course will invest in 2 hours to hire a pro-rigger to fine-tune the tension of the standing rigging, but the bulk of the work will be done by ourselves alone. Relieved, I am truly relieved! Talking to my colleagues and pros in the company, taking hundreds of pictures and doing some films of details, writing down notes into the owner´s manual and – most important of it all – sucking up all of the special knowledge of my mates. It´s 10 days from now and I have the best feeling that bringing GEKKO to the water will finally turn out smooth and easy. I hope …
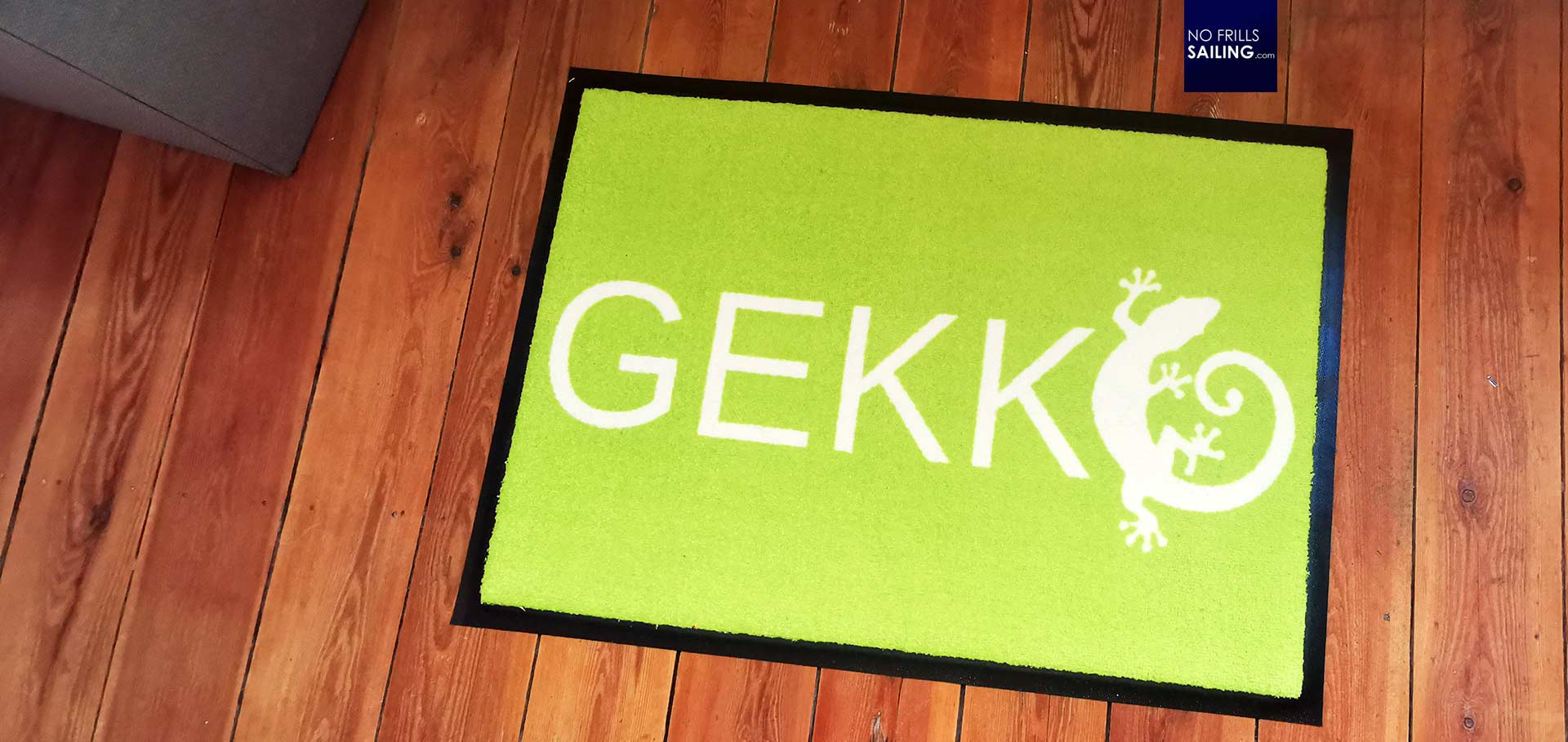
Now, let´s hope for the best. Next week the GEKKO-custom design will be brought on by the pros from the foliation company and this is the time when the boat will finally receive her image. In the time being, more and more details for the equipment arrive – more or less useful stuff. It´s just the best part of it all: Pleasant anticipation and this ever increasing great, great feeling of finally being able to set sail in my own boat. No matter what, it will be an unforgettable summer for sure!
You may also like to read these articles:
All Seascape-related articles on First-boats and GEKKO by clicking on the hashtag #thinkseascape
Delivery of a big sailing yacht
Winter deliveries & Corona trouble