Things are getting serious with my new boat now. Last week I went to Hamburg for a meeting with the guys who are responsible for the rigging of my Omega 42 sailboat. Gotthardt, a Swedish wholesaler with a wide range of brands providing equipment for sailing yachts, is the exclusive dealer for Seldén masts. Their Hamburg office is a large warehouse with the HQ offices on top. Here I had an appointment with Sören Matthiessen, Sales Manager and passionate sailor (and kiter) himself.
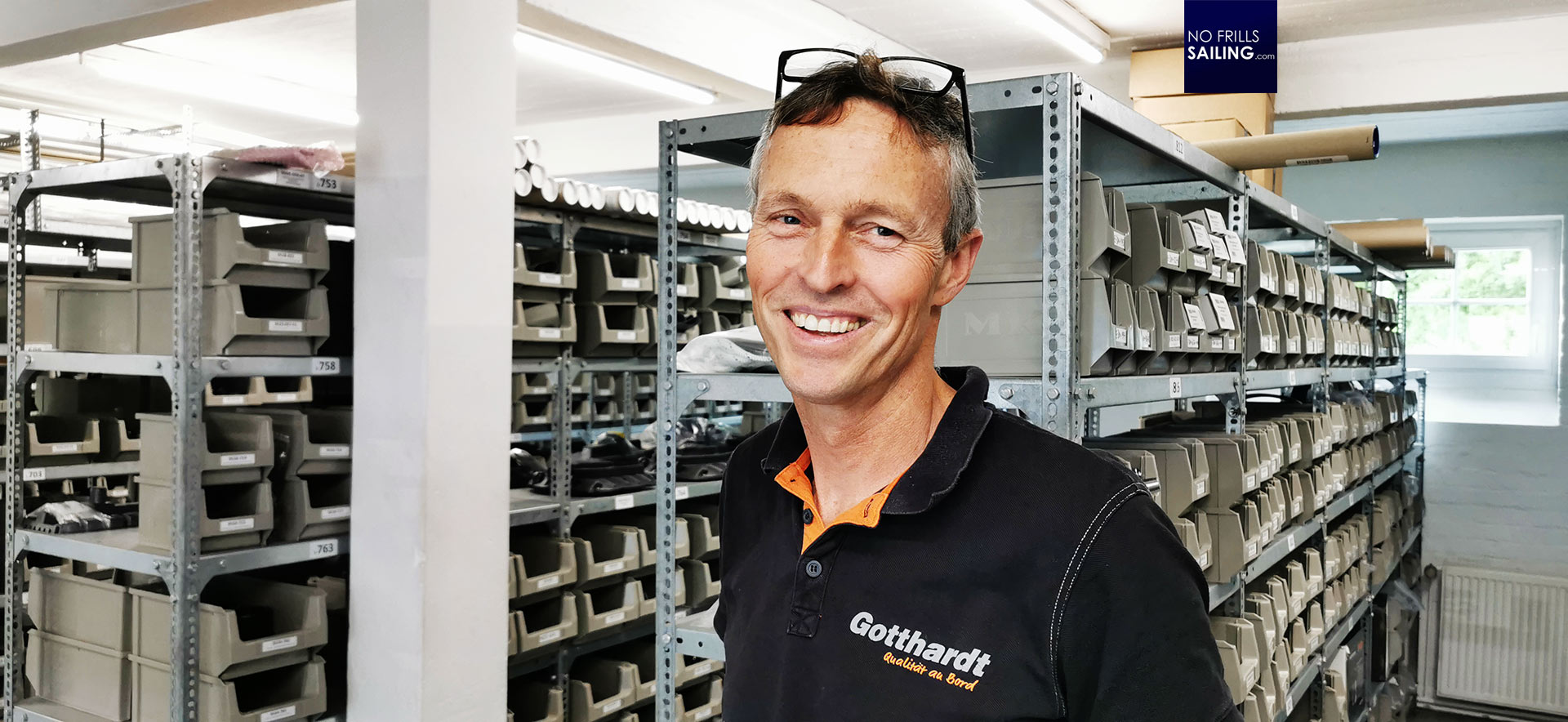
Sören is kind of a well known name in Germany when it comes to Seldén and Gotthardt-featured products. Working for many boatbuilders, Gotthardt has a specialty in providing custom solutions for one-off projects and, let´s say, unusual yachts where very special demands by the builders or owners have to be met. In this, Gotthardt and Sören have earned themselves a quite remarkable reputation. I got to know him personally some two years ago when we asked Gotthardt to come up with a special custom made rigg for one of our catamarans.
Talking about my sailboat´s mast
Sören welcomes me on a hot midday in front of the brownstone warehouse. We climb the stairs to reach the third floor where the offices are located. After a short reception and showing me around, we sit down in his office and start talking business right away. After re-animating the Omega 42 in 2017 the shipyard asked Seldén to come up with a new rigg. As the story goes, all original plans of Peter Norlin were unattainable by the yard, the family didn´t respond and therefore the mast and rigging had to be completely designed from scratch.
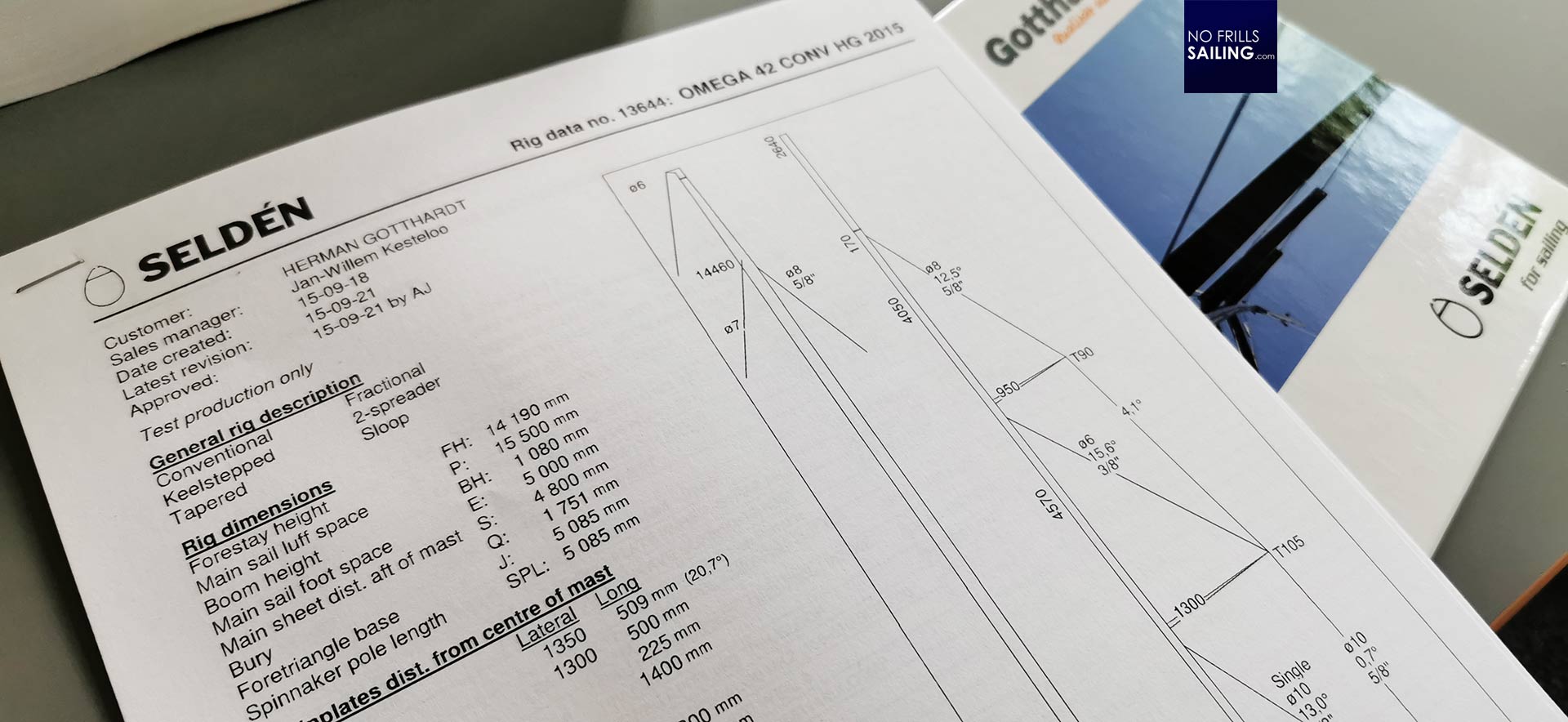
Sören pulls out a stapled stack of closely printed papers: “That´s your mast”, he says. Back then the shipyard had to deliver a set of numbers of the boat´s hull. This was the basis of the calculations of te rigg-designers back in Sweden at Seldén. As Sören tells me, the most important numbers for a rigg-designer to come up with a solution for the mast is not – as one might initially think – the sails area. In contrary, what matters most for the design of the mast is the righting moment!
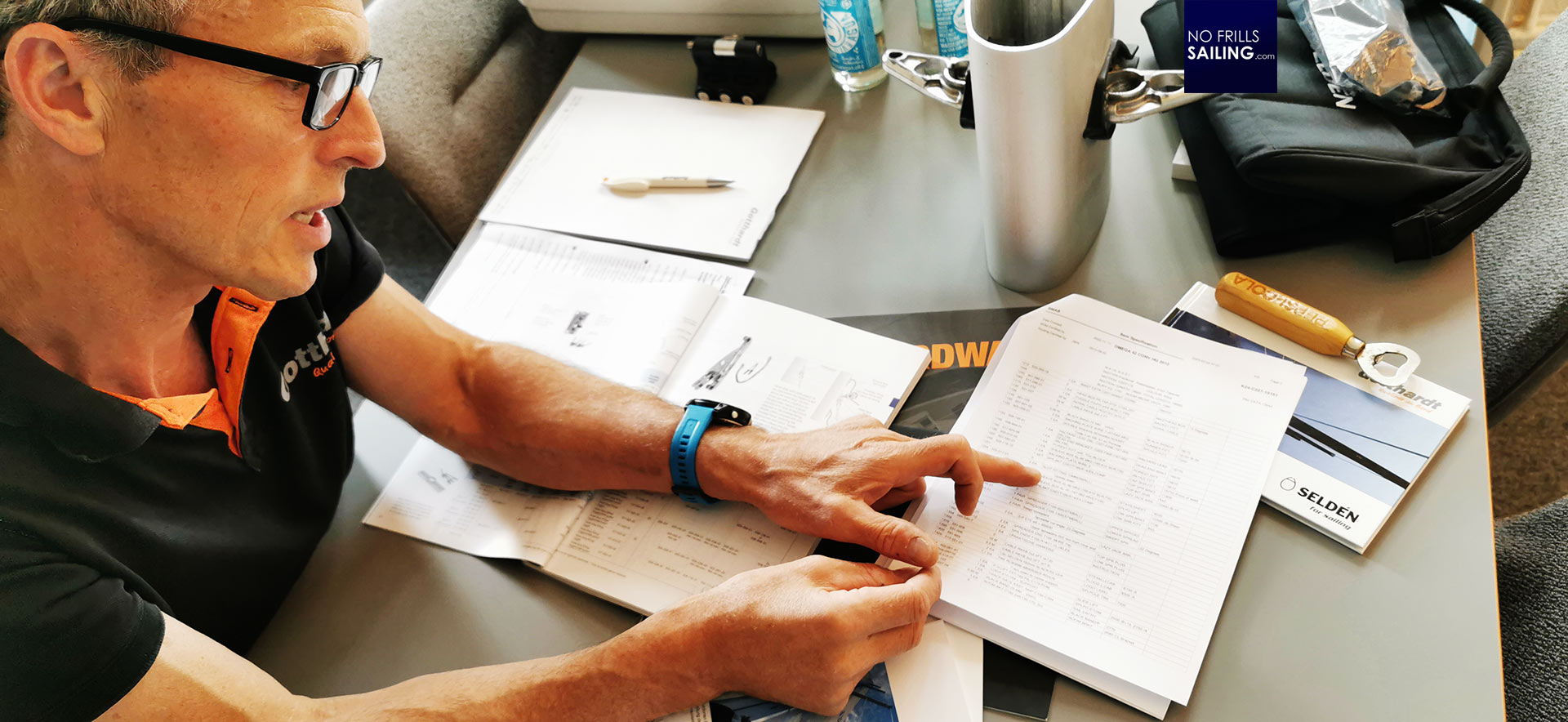
Sören explains that after collecting exact measurements like forestay height, mainsail luff space, boom height, foretriangle base or distance of the chainplates from mast center and of course all hull measurements like length, beam, draft or displacement, it´s this one number, the “RM” or righting moment, that defines the mast most. As for my Omega 42, the RM is 42.2 kilo Newton meters at a 30 degrees heel. Something learned here, I always thought the pressure generated by the sails defines the strength of the mast. Well, it does not so much, apparently.
Walking down the mast from top to foot
This pile of stapled papers, five A4 papers in total, is a very interesting document. “In general, this document walks down the complete length of the mast from the mast top to the mast foot”, Sören explains. With a font size smaller than 8 the papers are densely printed and describing the mast and all fittings in detail. These are more than 300 different individual parts used for my mast, which is blasting my mind. Up to know, for me, a mast was just … well, a mast. Standard. Not much thoughts went into it. They always come almost readily assembled. Again, it´s not that easy.
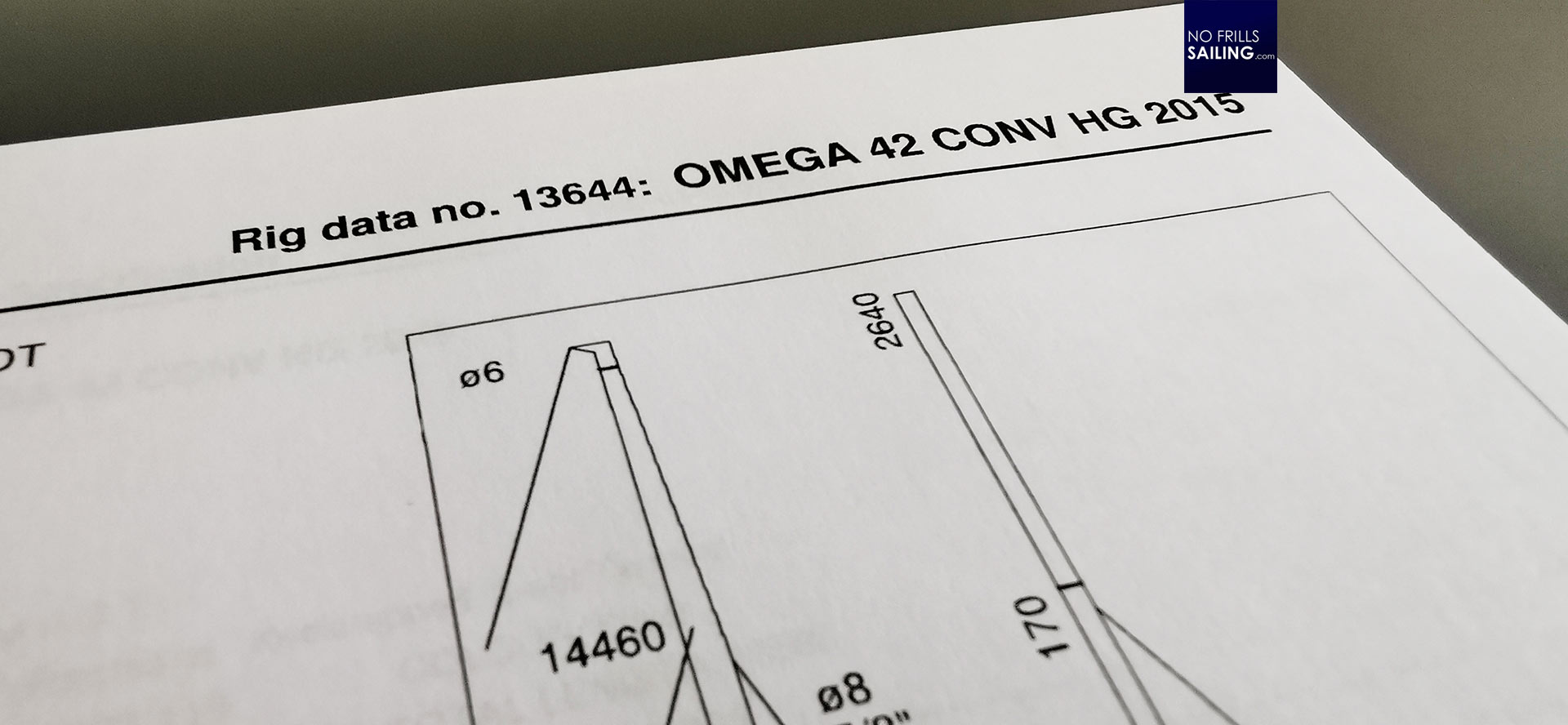
Starting from the top, Sören explains that the mast of my Omega 42 is fractional keel stepped two spreader tapered mast. The upper end of the mast is tapered, meaning it gets thinner to the top. This not only looks much better but makes the mast more sensible to trimming with the backstay. “The raw mast is cut for the top. To both sides long triangles will be cut out and the rest is welded together again. By that we achieve the tapering”, he tells me. We go down the list furthermore.
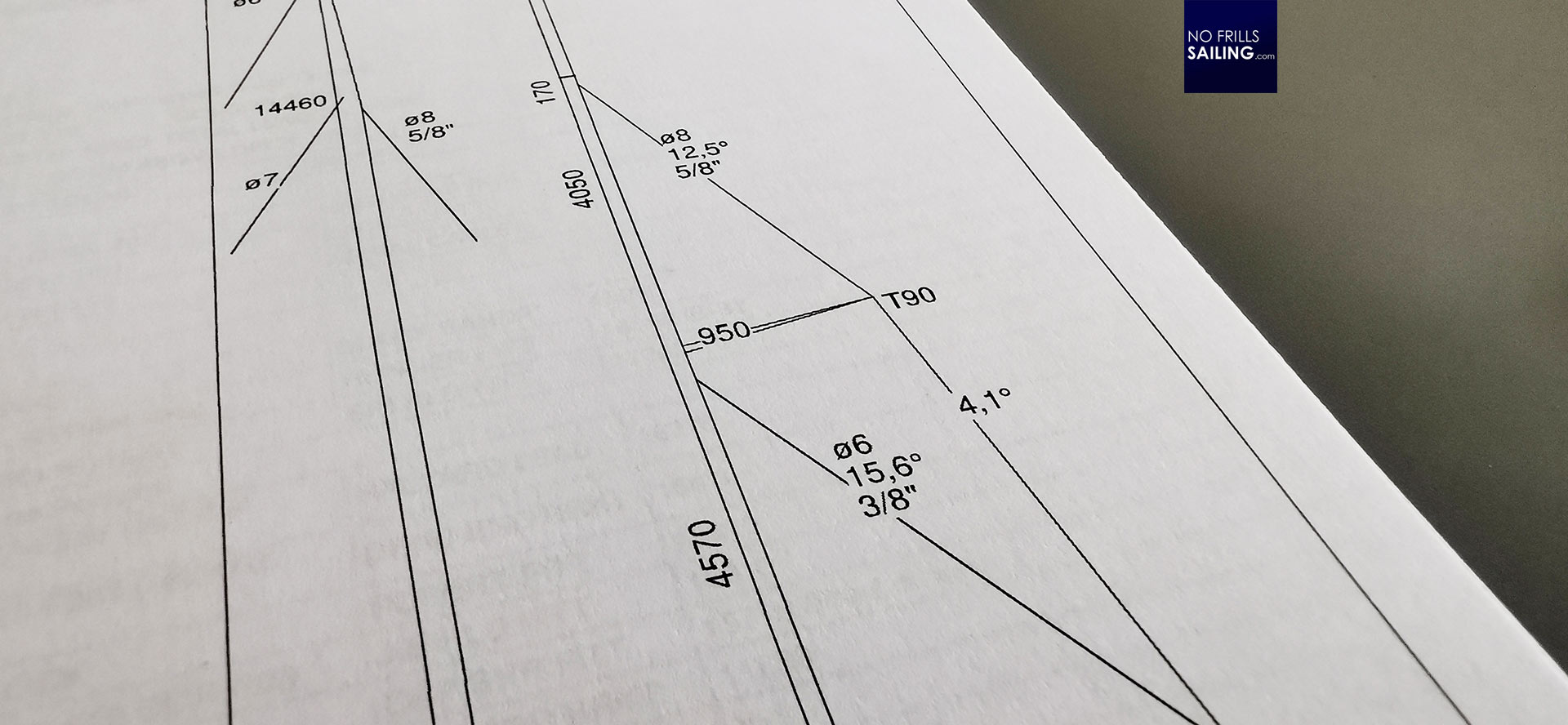
This document apparently not only consists of the complete list of all fittings to my mast but also definers their exact position on the mast itself. This is fascinating. The mast has kind of its own coordinate system. By that, the designers specify the position for each toggle, inlet/outlet, backing plate or support so that the actual craftsman preparing the blank mast accordingly.
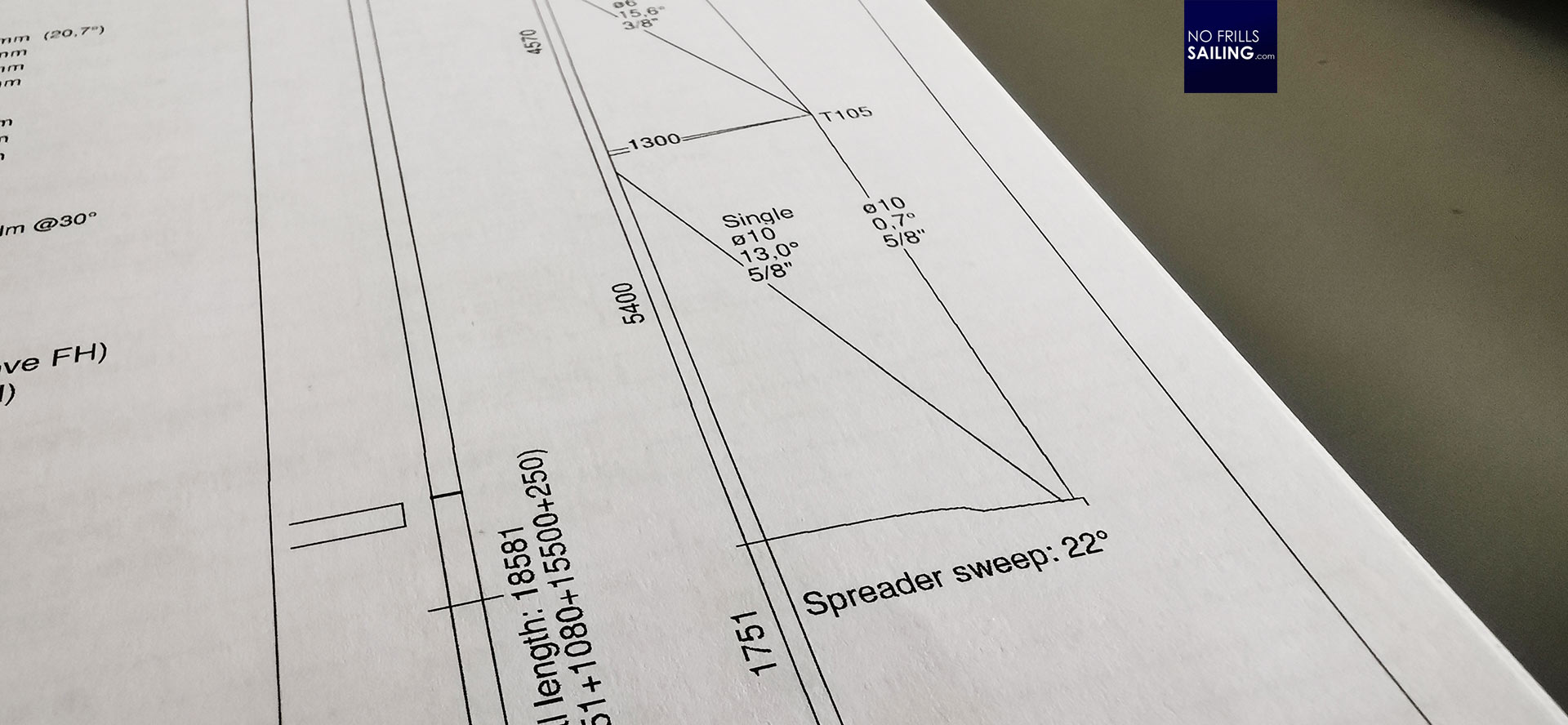
As we “arrive” at the boom, we decide to have a one-line-reefing system with two reefs in the mainsail. The third reef will have a reefing line at the leech to get it down and a conventional old-school hook taking on the eye in the luff. Going down the list item by item, Sören explains the mast in detail and both my admiration and respect for the work and effort that goes into conceiving and constructing such a product grows. It is indeed much, much more than just a piece of metal stepped onto your boat!
What Pasta and masts have in common
Sören shows me a small “slice” cutout from the exact mast profile that is used to build the mast for my Omega. I look closely onto the metal from all sides and suddenly realize that again I had a complete misconception of how a mast is made. Apparently, this is a one-piece part! I always thought that aluminium masts are kind of welded together or “rolled” and “milled” to achieve the complex form. They´re not.
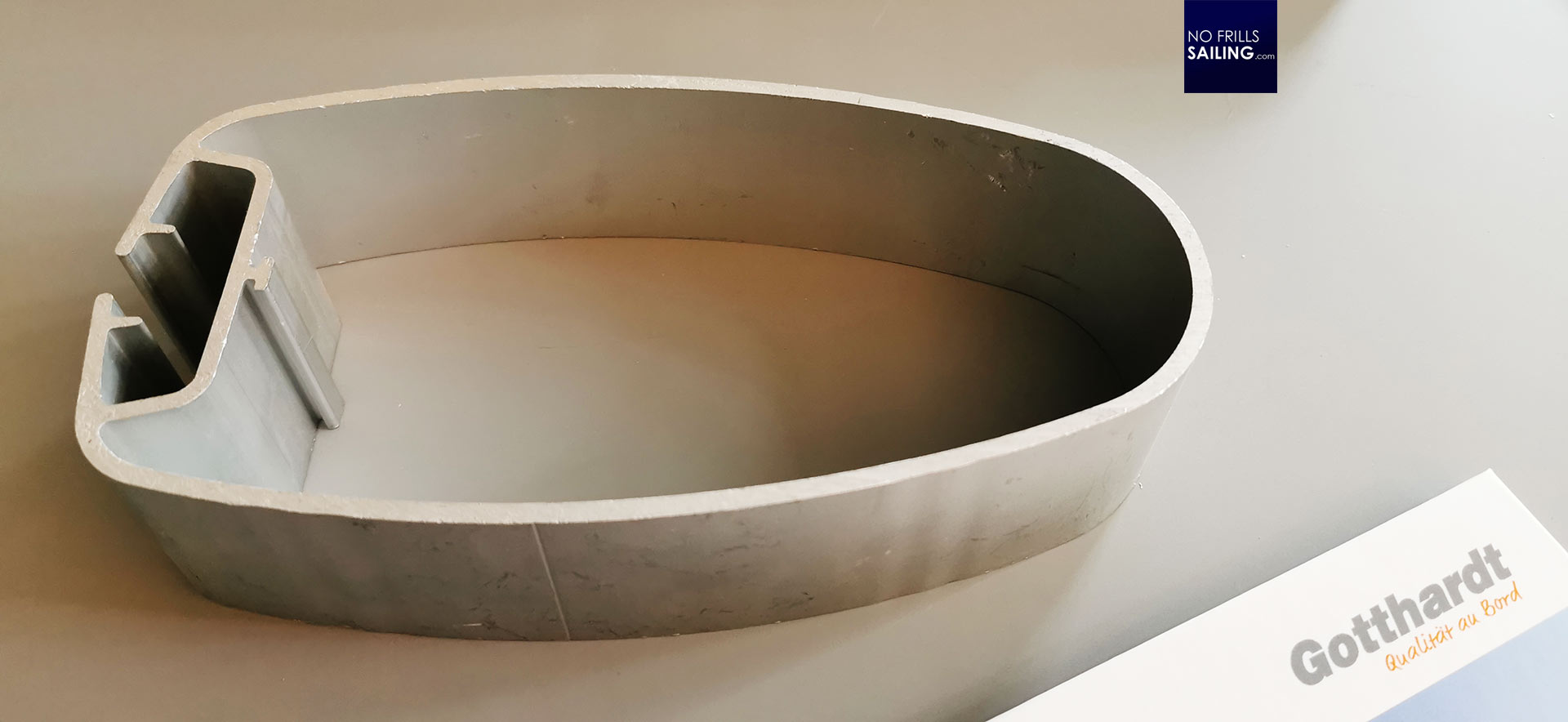
„In principle“, Sören explains, „the raw mast profile is made like Italian Pasta.” He smiles. Our Seldén masts are produced by a huge aluminium factory in Norway, Norsk Hydro. Imagine a tank full of molten aluminium. Seldén provides Norsk Hydro with a “nozzle” that has the shape of the mast profile.” A kind of negative, a sieve. “Through this the raw mast – in form of molten alloy – is “pulled out” and this is the way how a mast is made in one single coherent piece.” Pull casing like Pasta.
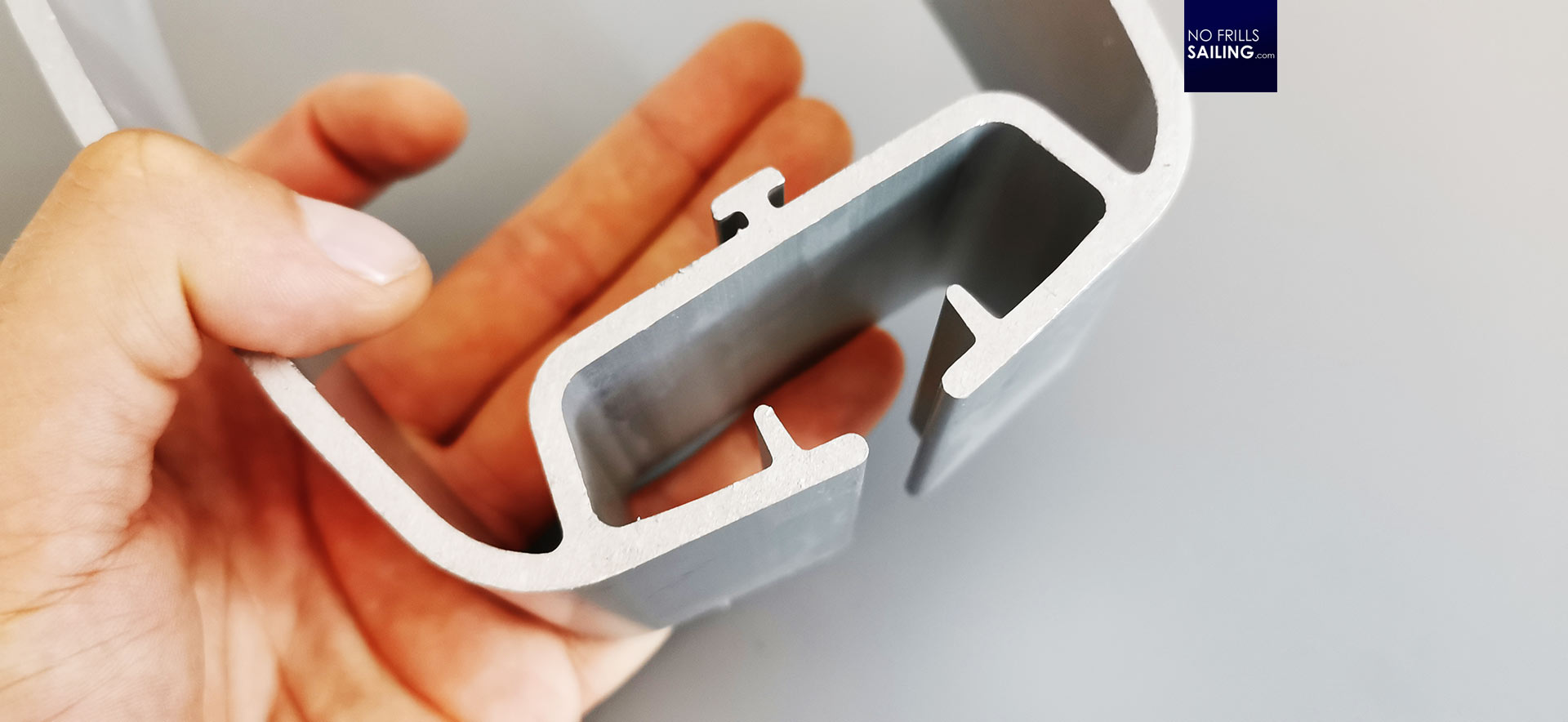
With big eyes and raised eyebrows, I tell Sören, putting my finger to a “seam” that runs all along the mast, that I always thought that this was the cut where the two halves of the mast had been welded together. He smiles, apparently, many think this way. “This seam of yours is a marking. We call it the “B-line”. It´s one of the reference lines on the mast from which the measurements are taken – the coordinate system for positioning the fittings.” He shows me a detail on my list: “See here: This slot fitting is positioned B +10.” Again, very enlightening.
Seldén´s proprietary mast sliders
Holding the mast profile in my hand, I ask for another detail. This time, for me personally, a very deciding detail indeed. Seeing the “duct” for the mast sliders, I ask Sören about Seldén´s solution here. Why? Because mainsail sliders can be a true pain in the ass when those cheap plastic sliders are used. But when high quality sliders on rollers are used, operating the mainsail is not just much, much easier and convenient but also enhances the safety of usage multifold.
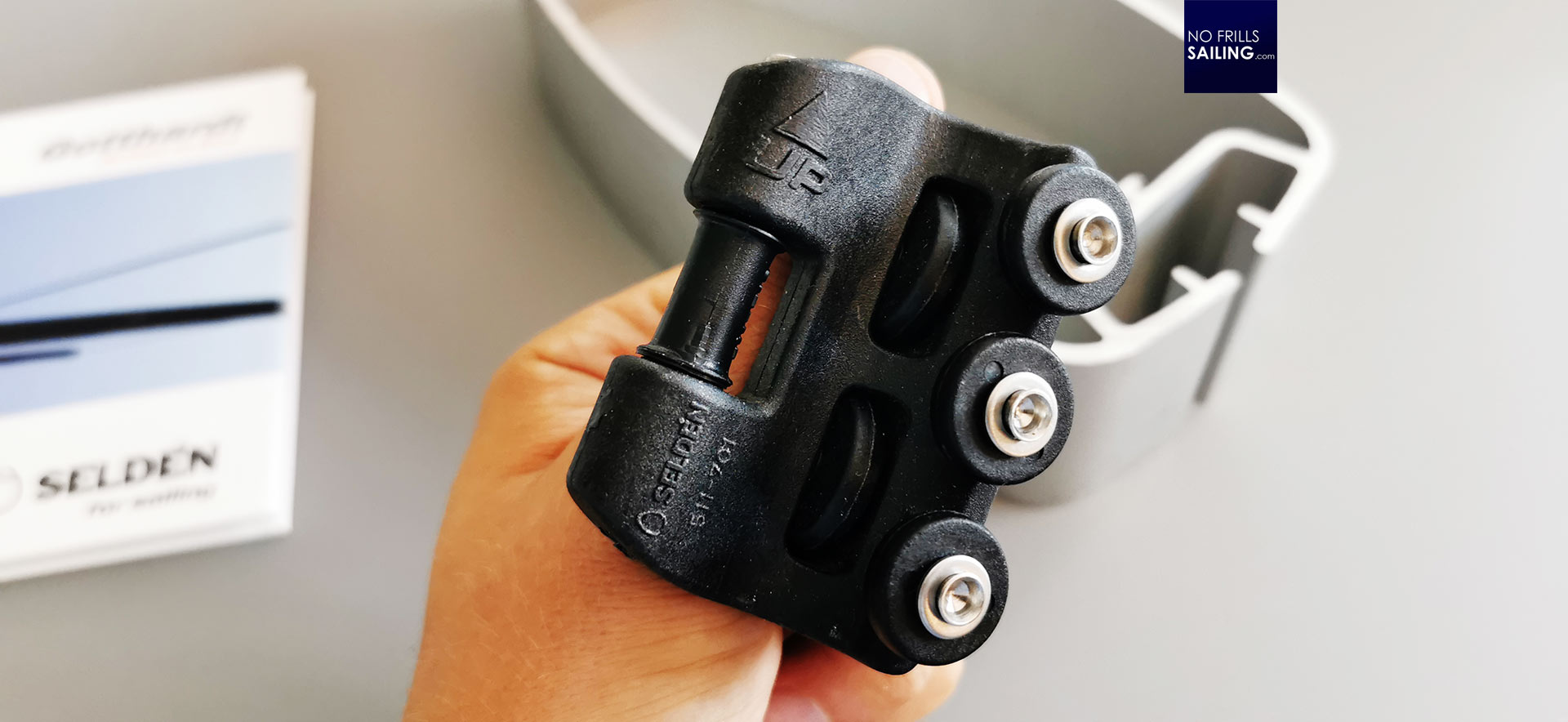
“For Seldén masts we have a proprietary system with our own slider cars for the mainsail”, he explains. The cars have ball bearings and double axis. Therefore, the glide up and down within the mast duct with ease. As there is just a minimum slit open to the elements, the inside is pretty protected against flying sand, dust and salt. The cars can easily be taken out and maintained. Lowest possible friction, highest possible duarability.
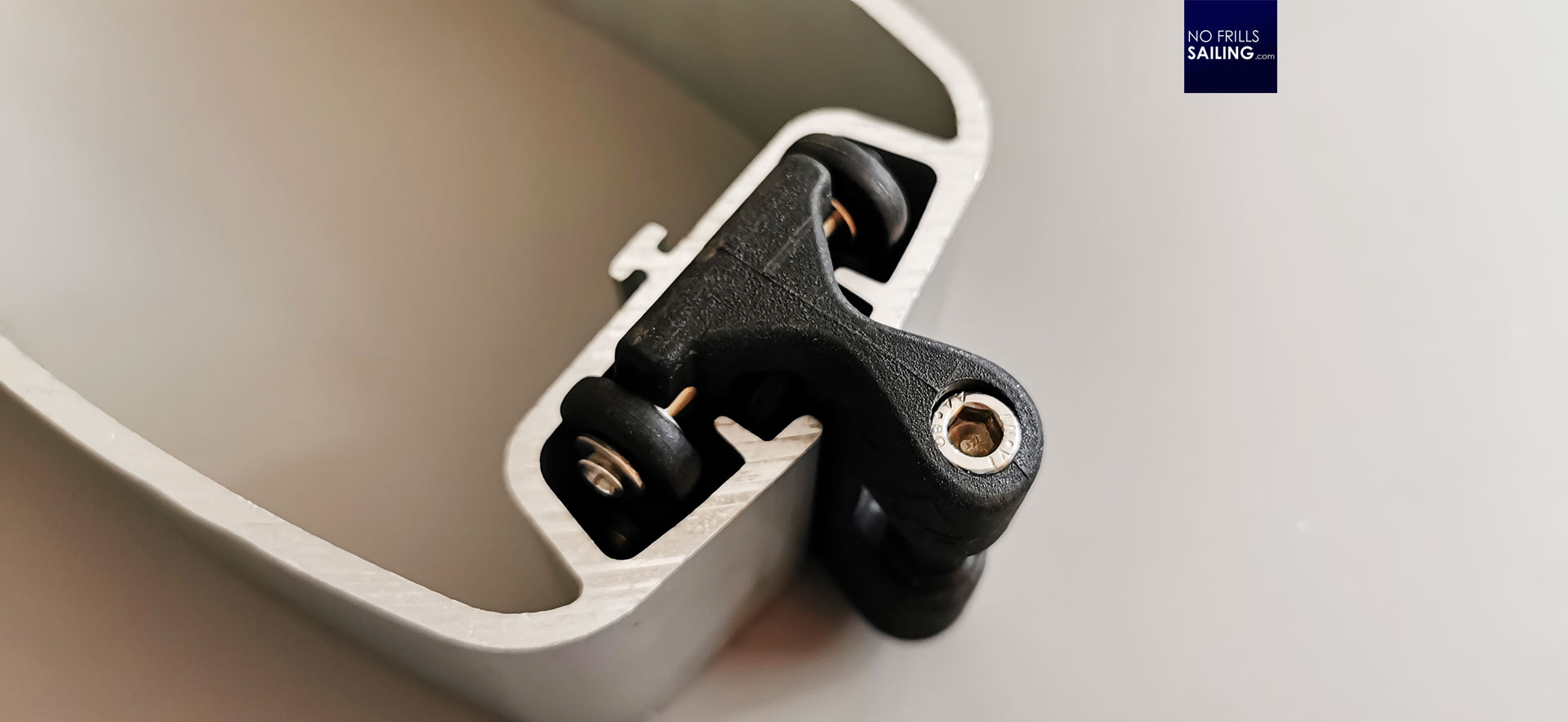
Why do I insist to have high quality sliders? Well, most of the time I will be sailing single handed. Oprating such a large mainsail, hoisting, getting it down and reefing, requires muscle effort. Of course I want to minimize this. Also, imagining foul weather and high seas, I under all circumstances want to avoide leaving the cockpit and working the mainsail from the mast. But you will have to on cheap riggs when the plastic sliders won´t come down. Sören adds: “For this system, no further fittings are needed. Normally you would have to attach a track to the mast if you want Harken cars, for example. This system is fully integrated, kind of “invisible”.”
The new rigg of the Omega 42
Although Norlin considered the Omega 42 to being his crown jewel out of all designs he ever made (and this is true), the classic Omega 42 had a birth defect. The original one-spreader rigg tended to get pumped up when sailed in a strong breeze and there are not few cases of broken masts. This, of course, is unacceptable in a new boat and it really had become one of the main premises when designing the new mast. In the end, Seldén came up with a two spreader rigg, a strong back stay to the top and two running back stays fitted at forestay height.
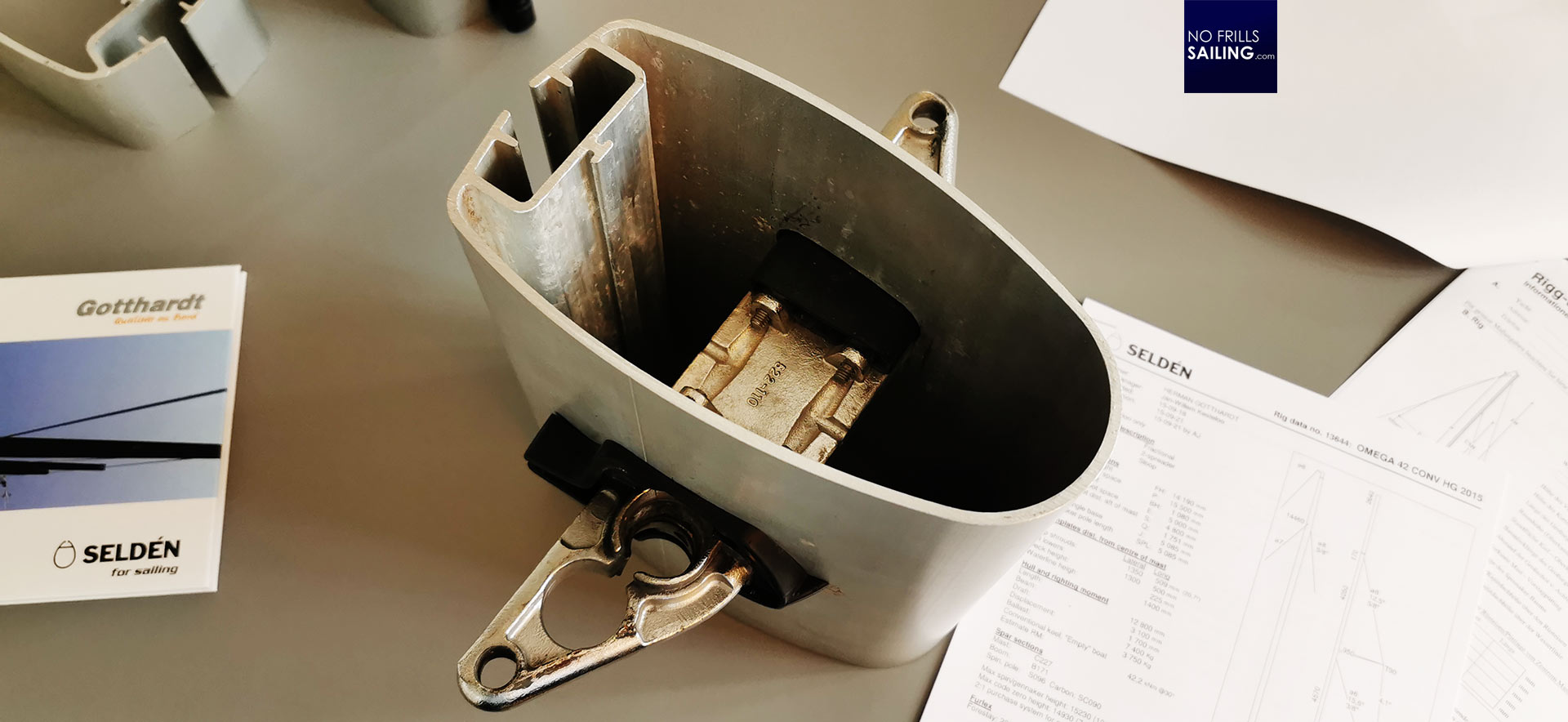
The two spreaders increase safety to a maximum so that this newly designed rigg lives up to modern safety standards in sailing. How much safety margin is built in? Shrouds and stays, for example, are fitted to a maximum of 20 per cent of the rupture load. “How much margin there really is I cannot state exactly”, Sören tells me, “but it takes a lot before a boat dismasts, for sure!” Back to the shrouds – something new to learn here too.
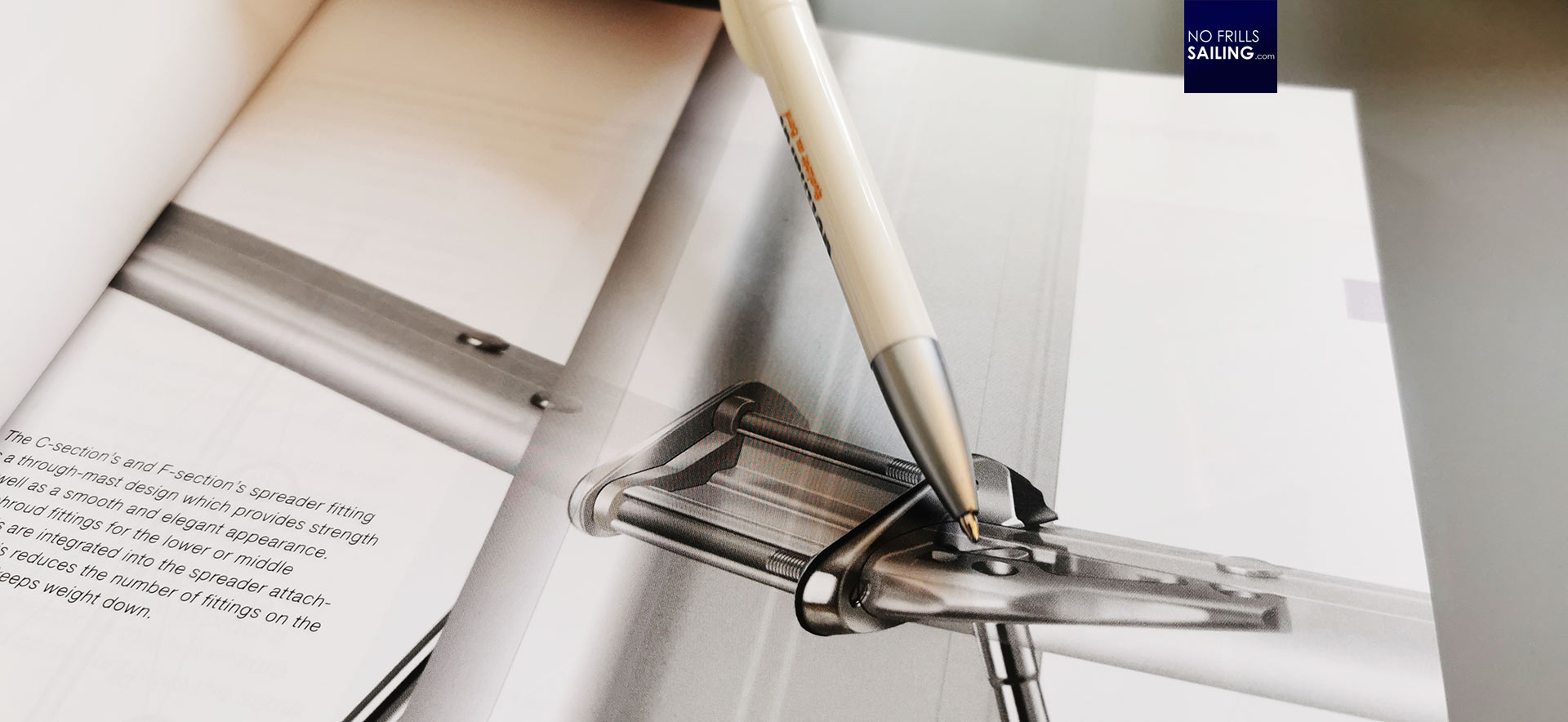
Up until now I thought that the spreaders are just put on massive pins which are welded to the mast. But that´s not the case. In reality, the spreaders are hold by a massive piece of machine milled stainless steel which, in case of Seldén masts, also holds the inner shrouds and thus takes on much more load than just that from the outer shrouds. I am fascinated how many little details come with such a barely noticed and spoken about fitting.
Nice details …
Speaking of details, there are a ton of “hidden” things to talk about. For example the wire ducts. For these, meaning the wires to run the mast top light, deck floodlight and other installations in the mast, like Radar for example or VHF, Seldén has a proprietary two-chambered plastic duct system that is running along mast attached to the sliders-duct. Much easier to maintain and run new wires.
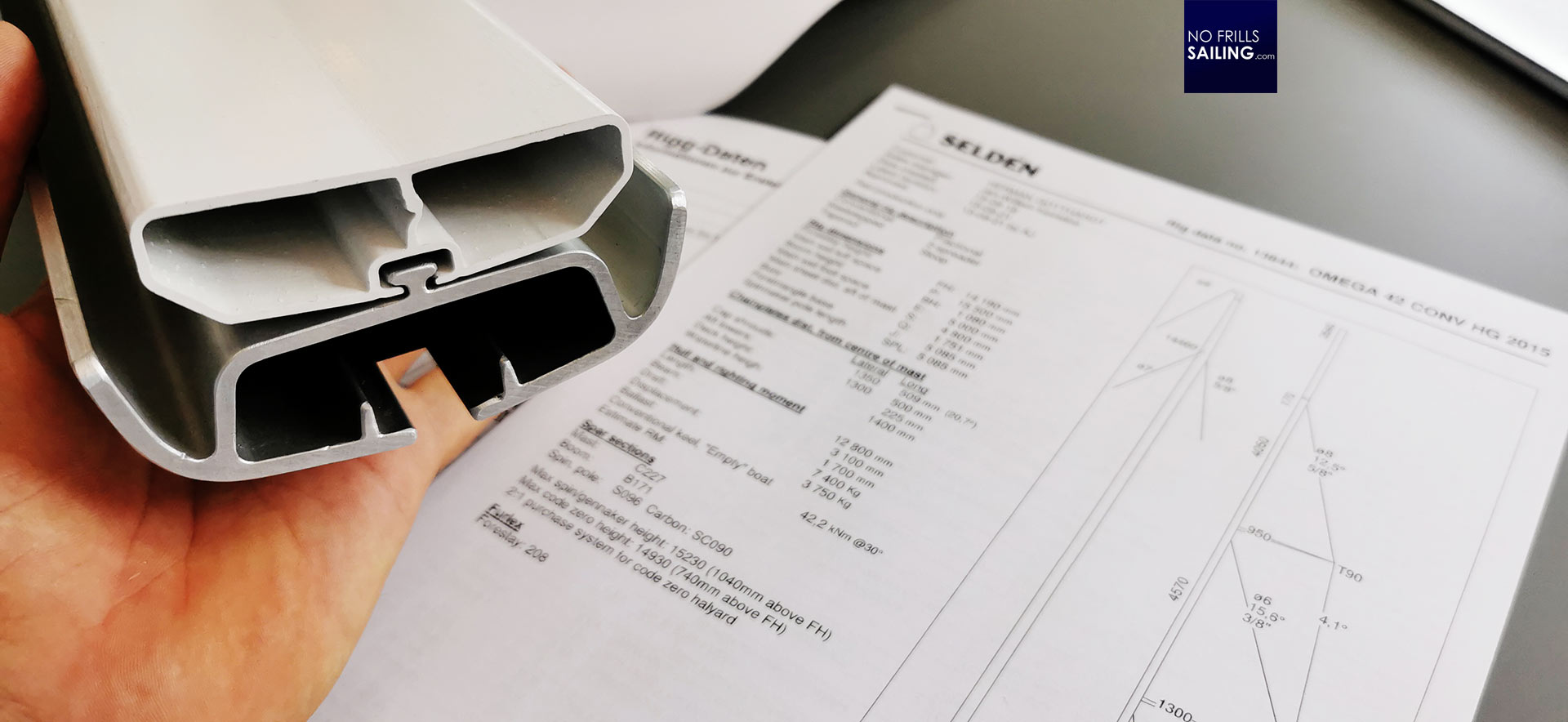
We also talk about „nice to have”-things, like hidden lazy jacks. I have seen this on WINDFAENGER, hull 001 of the Omega 42 evo-boat when we sailed here some weeks ago. It has no practical effect but is rather beautiful, to have the lines run inside the mast. Sören insists: “Au contraire, Lars. It is also very practical as you can eliminate one of the sources of annoying rattling and cluttering of the lines in the wind.” Well, it depends on the price, I´d say …
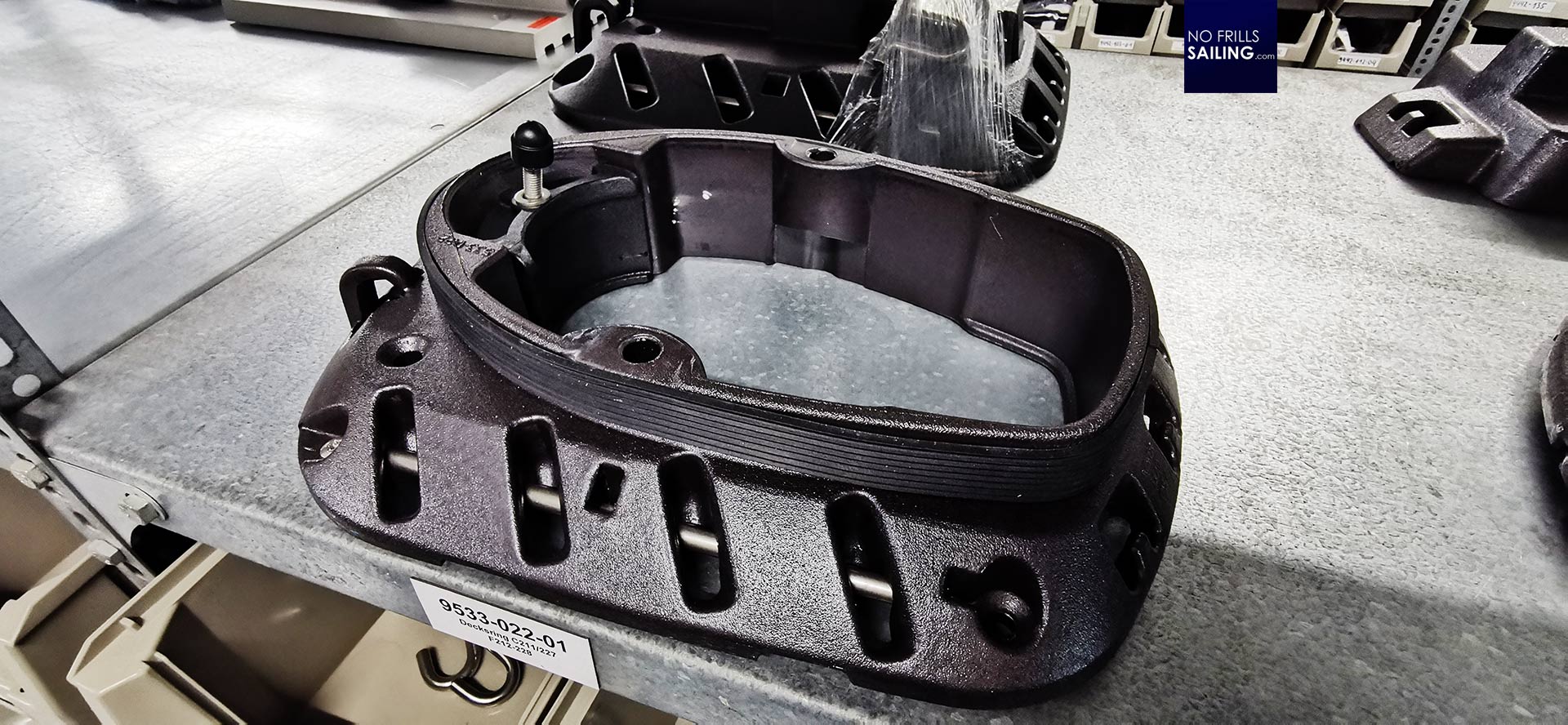
I also loved the Seldén mast collar. This is a massive steel part that is sitting on the deck holding the mast in place, securing it and make for a watertight connection. The mast of the Omega 42 is stepped on the keel. What I loved was a simple yet so practical solution to attach the blocks to the collar which are diverting the lines back to the cockpit. Where on ordinary boats you have to open and secure the shackle of each single block – making it up to 10 shackles – on the Seldén collar you unscrew a nut, pull out a long shaft, put in the shackles of the blocks in the designated positions and push in the shaft again. This will easily save so much time when rigging the boat.
Working with absolute accuracy
Sören insists that we´d try to have all terminals done by the factory. For WINDFAENGER, the shrouds had not been trimmed to length and the end caps hadn´t been fitted by the factory. This can be done by a skilled sailmaker/rigger but I agree that on the standing rigging as much as possible should be done ex works. For that, of course, exact measurements are essential. “What we can do, Lars, is, that once deck and hull are “married”, we meet in the shipyard to make these measurements on spot.” He takes out two large rugged cases.
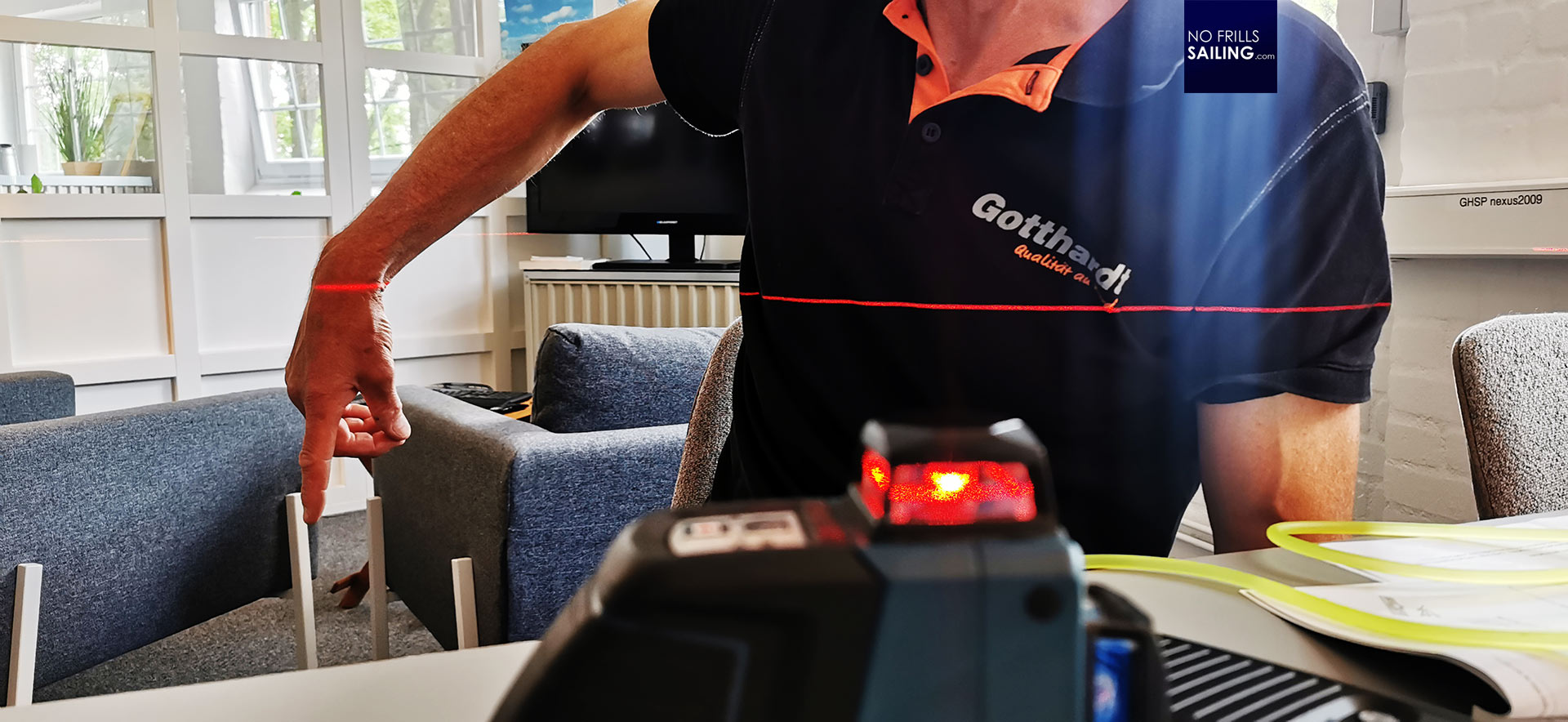
One case has a laser-device that is used to accurately find measurement-points relative to a certain source. The second one is even more fascinating: A barometric level that works by measuring the tiny, tiny, tiny fractions of difference in air pressure. To being able to cut the shrouds to their exact length and have the terminals attached those measurements are necessary. So, I can look forward to another article showing this in detail.
Accessories, fittings … an endless list
After we finish talking about the mast and how elaborate this crucial piece of a sailboat is made, Sören invites me to follow him downstairs. Gotthardt Hamburg is one of the big warehouses from which Germany and several other countries are delivered with parts. The store is a Mekka for sailing aficionados though.
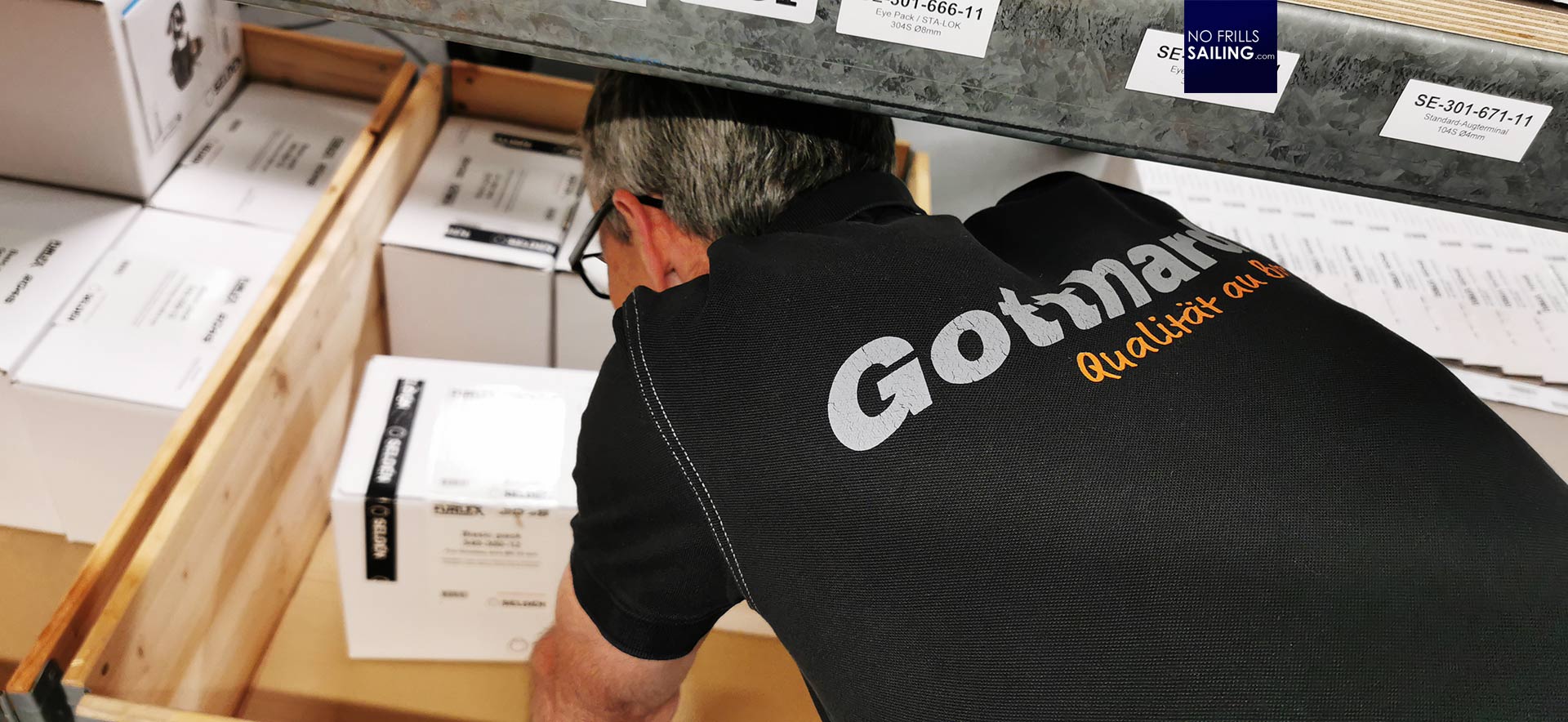
For my Omega 42 I – for now – chose to sail the boat in Peter Norlin´s original sails set up. That will be a huge mainsail with 39 square meters sails area and the self-tacking Jib. I am normally not a huge fan of self-tacking Jibs but in the case of the Omega 42 this is how the boat is supposed to be fitted. The huge mainsail (huge and also high up over ground) was intended to catch the wind inside the Swedish Archipelago, therefore the Jib is used primarily to optimize airstream onto the main.
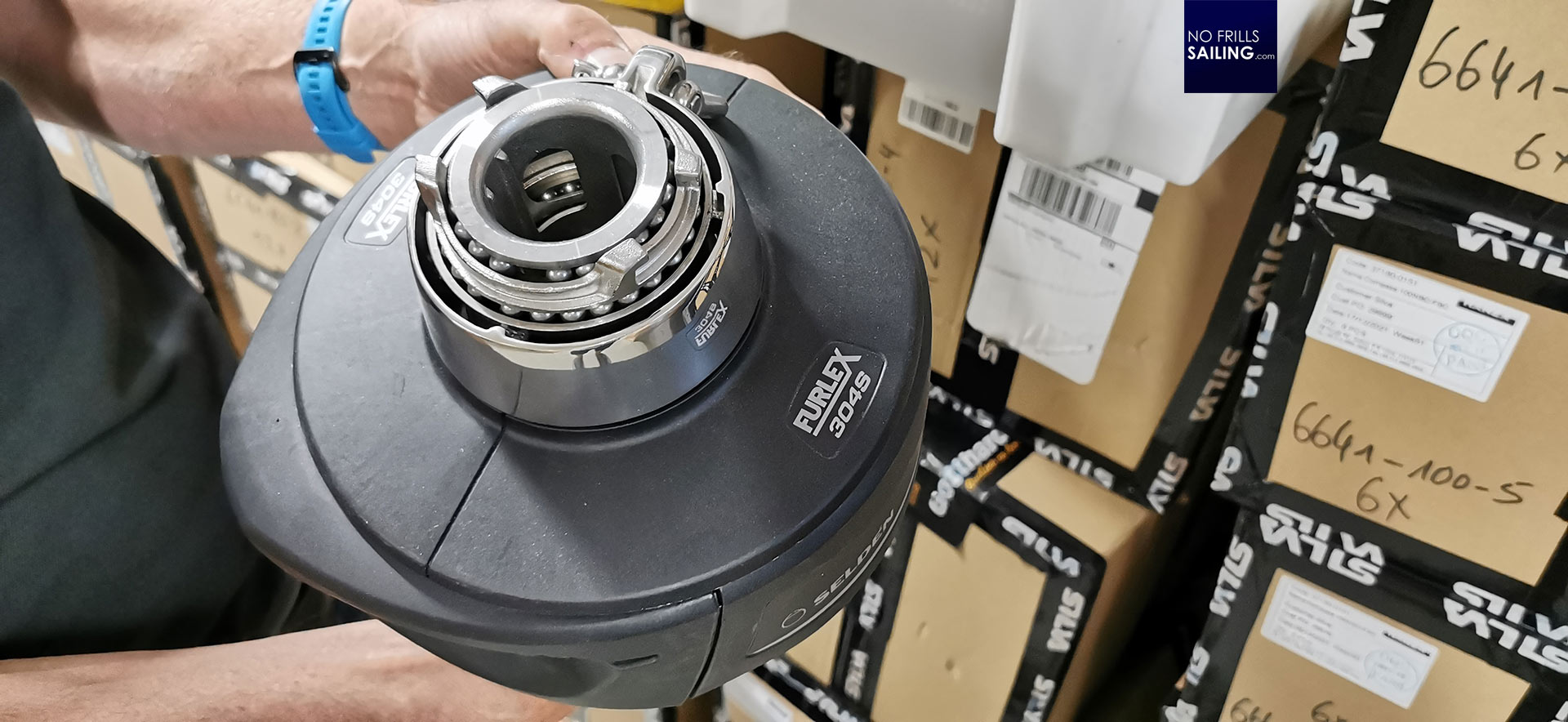
To get it in and out, a furler is needed. Gotthardt is traditionally bound to Furlex. I don´t know if this is true, but I´ve heard that the original invention of the furling-box is indeed credited to Furlex. What I know for sure is that their product is around for some 30 years now and they hold some patents which make it special. Sören shows me the very type I will be working with on my boat: I am impressed by the double roller bearings.
Let´s go!
What started as a “just drop by when you happen to be in Hamburg and we´ll have a little chat about your mast” ended up being a so much interesting, surprising and detailed crash course of how a mast is made and how many different tiny but deciding details have to be taken care of to have sail hoisted and driven safely in the end. Sören openend the doors to a world rarely spoken about but so essential to having fun on the water and do it safely. I am grateful for these three intensive hours, thanks so much!
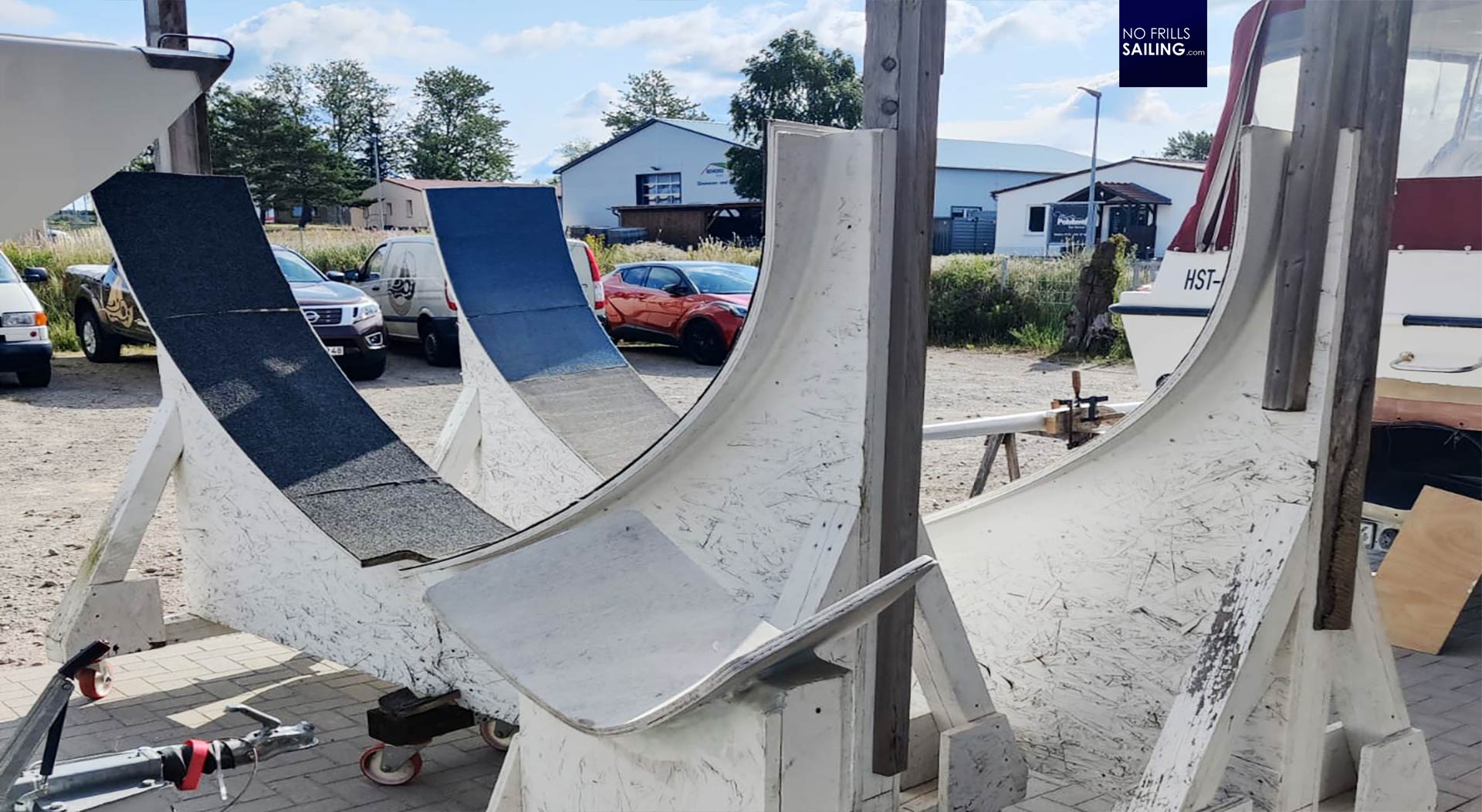
The same day, returning home, I receive a whatsapp-message. It´s Heiner Francke, owner of the shipyard that is building the Omega 42: “Hello Lars. We have prepared the assembly racks. We will put your boat onto these end of this week. This will be the official start of the works on your Omega.” Smiley. Good news in a row – how exciting!
You might also find interesting to read:
Seldén or Sparcraft? Comparing the two inmast-furling systems
Performance sails for inmast furling