Yard visits are a powerful tool for boat dealers and the brands as well to in the trust of their potential customers, to show their approach to building quality and finally initiate a spark of enthusiasm inside their clients that will eventually turn into a fiery passion. I´ve seen many shipyards, smaller and bigger and always felt this “spark” myself – there is something special about a shipyard, it has some aura or mystical feel to it, it never fails to amaze me seeing the process how a boat is made. Last week, again, I´ve had the pleasure to accompany two couples interested in buying one of our catamarans on such a tour of the very shipyard where the Excess catamaran is made. And this was truly something special!
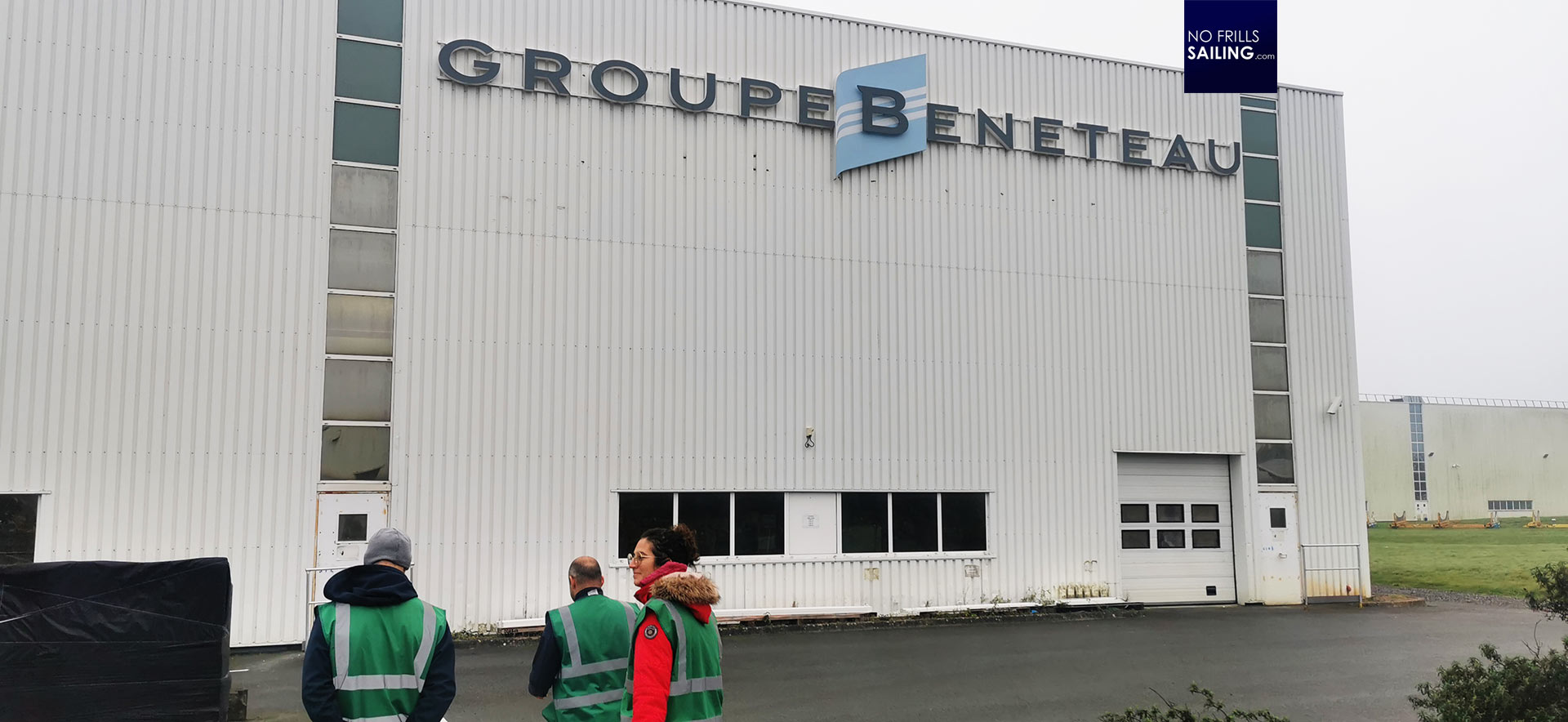
Groupe Beneteau is very open and inviting to its customers and prospects, their “Premium Service” division is there to welcome us dealers with our prospects and clients, they are professionals in showing the production facilities and give the big tour, explaining, showing, and exciting their guests. But as Groupe Beneteau, in our case Excess, is very welcoming and hospitable on the one hand, they are very restrictive and sensitive about taking pictures, let alone publishing them. Of course this is to protect their proprietary knowledge, their special techniques and well-kept secrets on manufacturing details. In this, I feel absolutely humbled and honored that I´ve been allowed to present to you this article with many shots from inside the production facility, personally approved by Hervé Piveteau, “Mr. Excess” I shall call him, the head of products at Excess. So, please follow us into the shipyard …
Everything starts with a push cart
The current line of Excess catamarans comprises the 11 and the 14, both of which are built here in the Vendeé in one of the group´s biggest facilities at Le Poiré. Huge white inornate halls spread out over a vast industrial zone directly connected to the nearby highway. The sharp (but I love it!) odor of fresh resin is in the air, small tractors pushing trolleys with GRP-parts, half hulls or huge moulds around are bustling the streets between the halls. People in safety gear walk around – everyone says “Bonjour” and smiles, something that makes me wonder every time I visit a shipyard: People are always friendly. Maybe this job is a universal happy place? We enter one of the workshops.
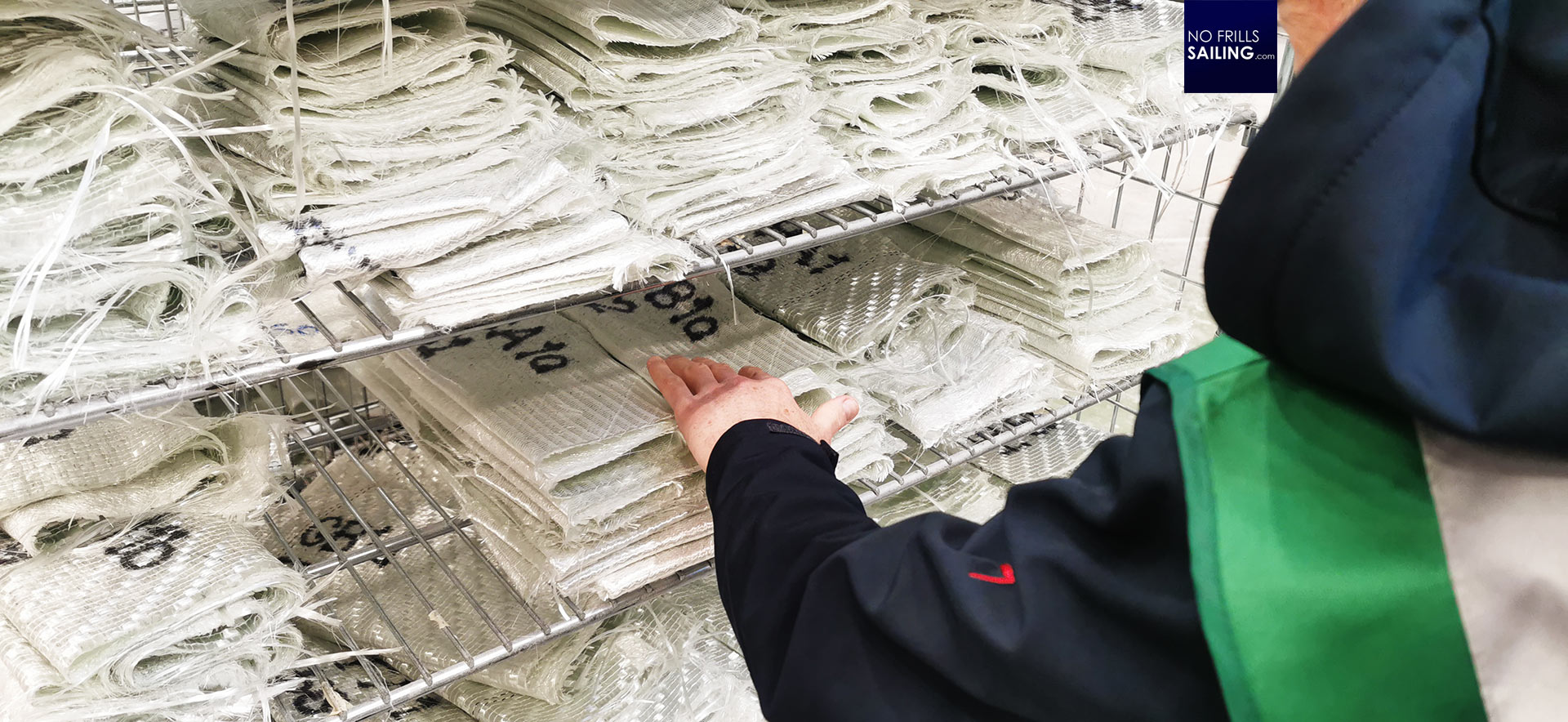
I shall call this place the kindergarten of boats because in essence this is the nucleus of a boat: Dozens of steel push-carts are parked in designated areas, placed in order exactly where they should. Each cart contains maybe 8 or 10 compartments which themselves are filled with GRP-mats. Loose garments of mats, neatly rolled and marked by a computer. This is how it all starts: A cart full of loose matting. My customers behold and think of it: Some time in the future there will be a cart placed right here too, outside a big white paper, stating the type and hull number of the very boat, they will be handed over and sail onto just a few weeks later.
Hand lamination, vacuum infusion and vacuum injection
Next to the kindergarten a woman is making the keel fins. A fascinating process of putting together computer cut hard foam pieces and wrapping a number of those glassfiber mats around, making the fin ready for the lamination. Of course this is one of those sensible processes, so I couldn´t take pictures of it, but it was a great introduction into lamination for our guests because every step could be seen in a comparatively small piece. That changes when we enter another part of the production hall …
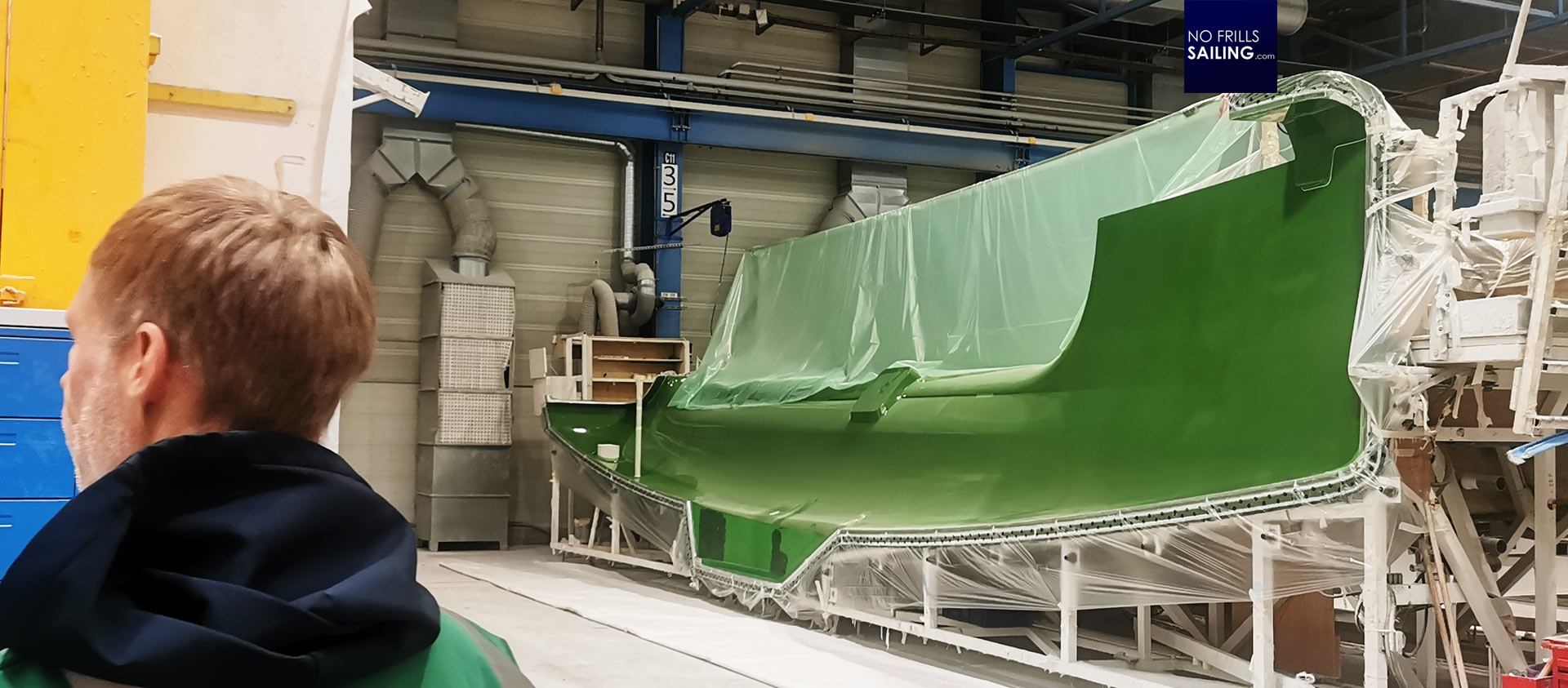
Here is where the big hull parts are laminated. A very sharp stench of resin is definitely something a light-minded visitor cannot bear for a longer period, by my guests are starting to get enthusiastic: In this area I´d say 5 to 7 boats can be laminated at one time. This operation has a high demand for manual labour: It takes up to 8 or 10 people working at the same time, hand in hand, to make a hull. In fact, it feels like watching a well-choreographed theatrical play. There are certain people with certain special handles: One is spraying resin, one is applying the mat (taken out of the kindergarten-push cart) and two are operating big rollers to apply pressure and squeeze out air bubbles. A ballet of skilled workmanship. In this, we notice that in fact most of the workers are females: More sensible, better feel for the material and quality awareness for this kind of work, as our guide explains.
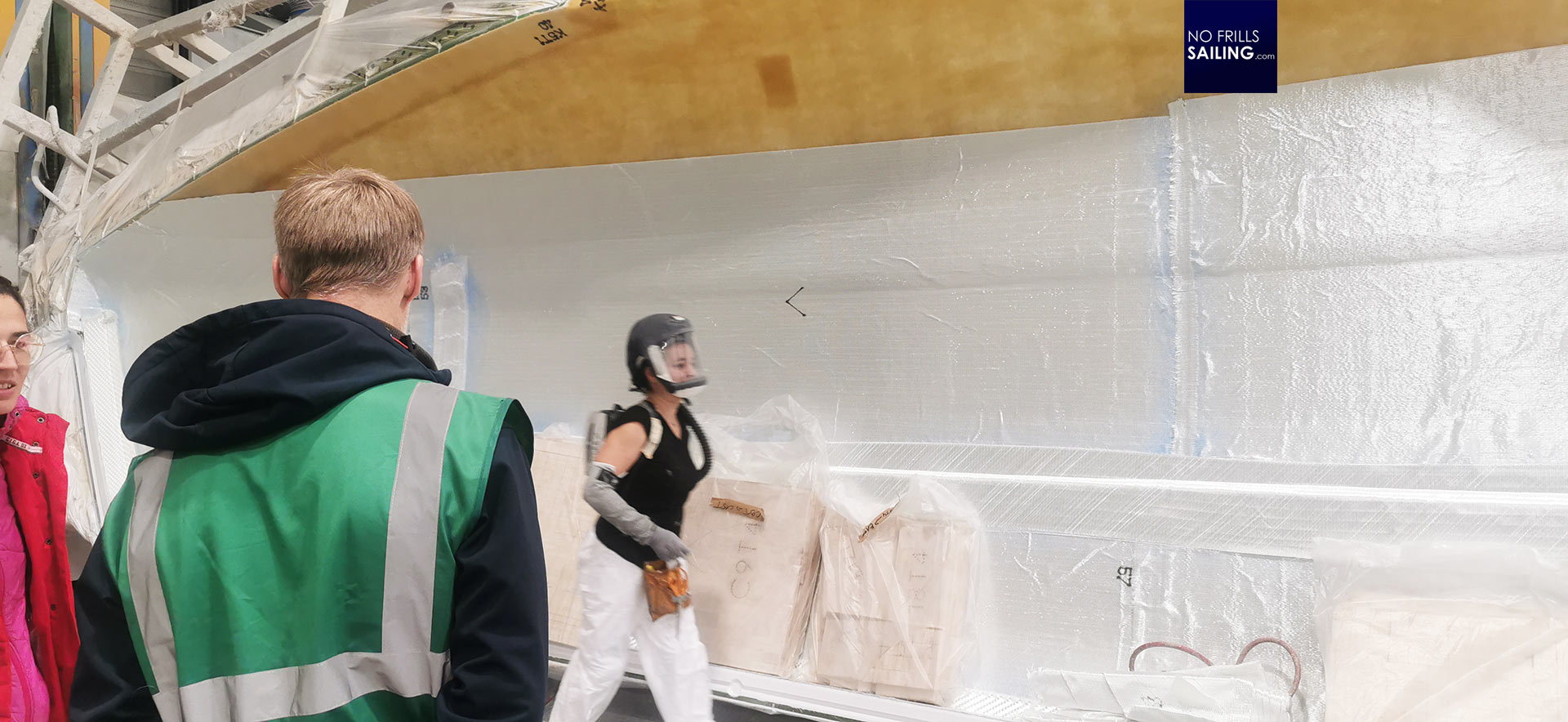
A catamaran hull for the Excess 11 basically consists of four parts: The underside mid-section, two hull-sides port and starboard and the deck with the saloon. Some of them are hand laminated, some are vacuum infused and some are vacuum injected. We get to see all of those different lamination techniques in detail and our guide explains the different approaches and outcomes, yet, you guessed it, as well something I was not allowed to show. Nevertheless, we spend almost a full hour in this area of production as both of the guests were excited and surprised about the “seriousness” of production, let´s say. Most of my visits to shipyards with prospects culminate in their realization: “It´s really definitely not a joghurt cup!”
Balsa sandwich core
Standing in front – or shall I say underneath – one of those huge moulds of an Excess 11 hull, one of the ladies wearing an active filter mask was spraying a blue-marker glue and placing mats. Then she unloaded a set of plastic-bags with all an too familiar material into the mould, starting to unpack and fitting the individual pieces into the mould: She was making the Balsa core. That is a detail I was allowed to document a bit deeper.
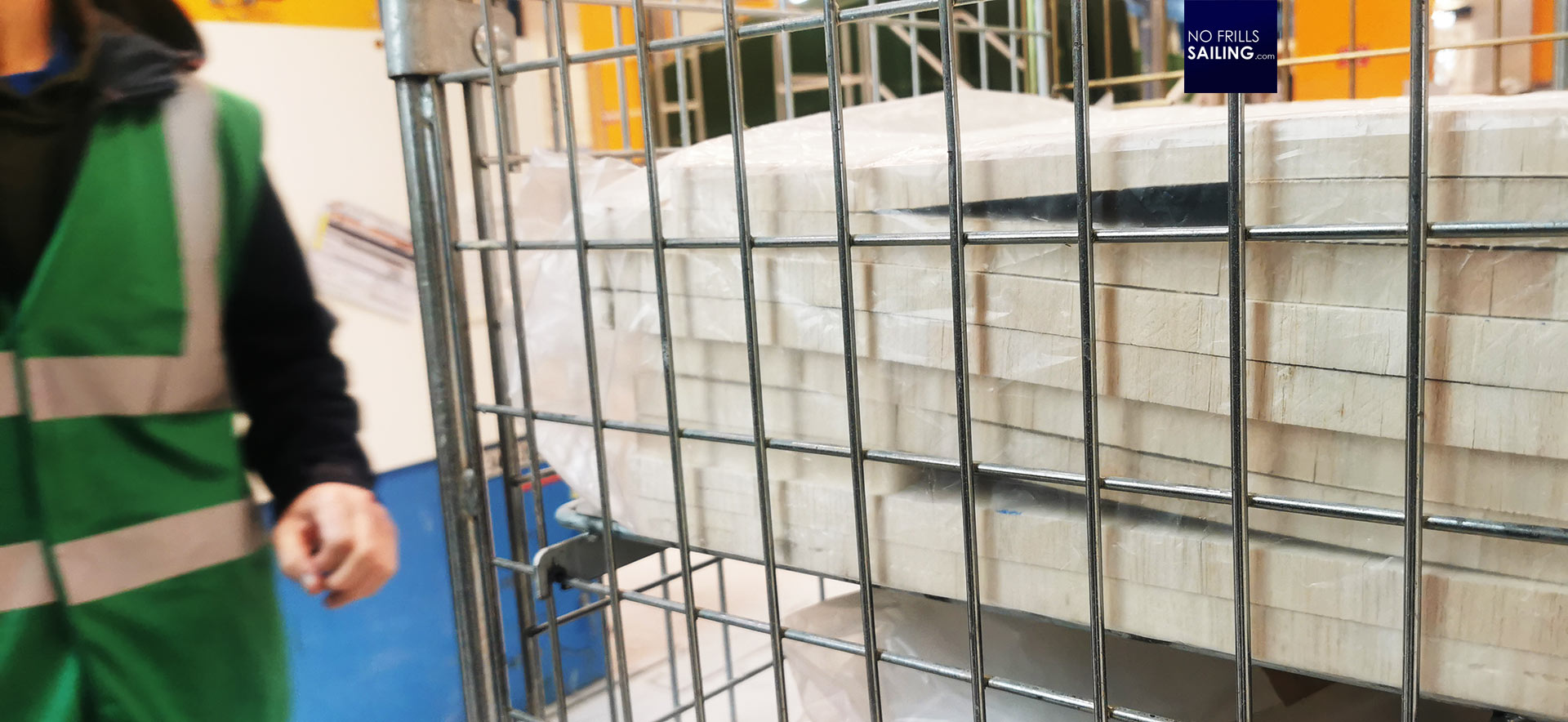
Balsa is a fast growing tree producing a very, very lightweight but dense timber. Balsa is therefore used for a wide variety of products, I know it from my childhood, model planes are still made of this natural material. For decades Balsa is also used in shipbuilding. Balsa alone is brittle and not very stable, but “wrapped” in a few layers of resin-soaked glassfiber the whole structure – now a “sandwich” – becomes very strict and rigid. This, Balsa is a perfect material for making ship´s hulls and decks, a hard structure that can withstand a lot of pressure and stress.
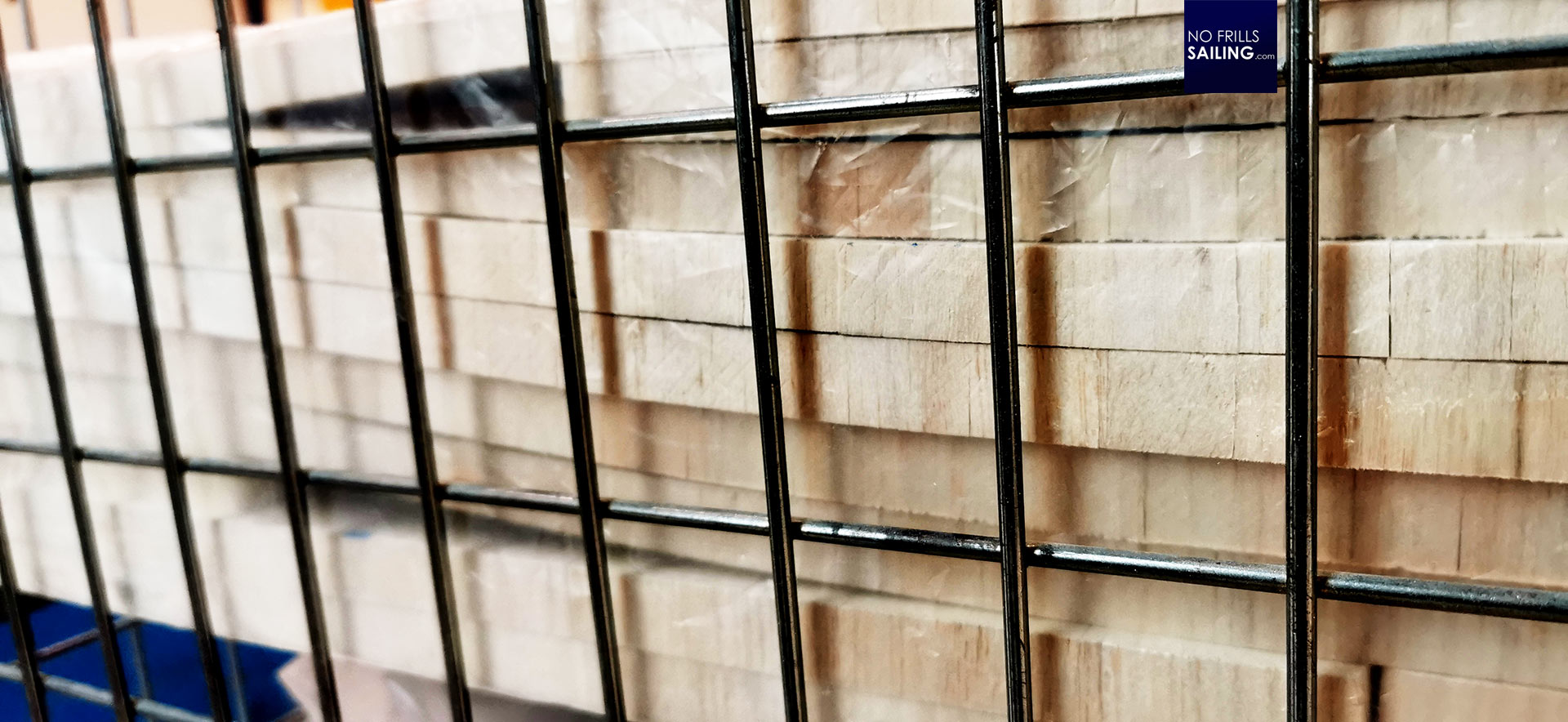
This Balsa material is delivered to the yard in a special form: The wooden parts are cut (I suppose by a laser) into approximately 2 centimeters thick squares of 4 x 4 centimeters. Those are packed densely together and glued to a gossamer. Now, this has two remarkable features: Each mat, precisely cut and numbered, is put by one of the skilled workers at the exactly position within the mould. A huge puzzle, if you will. When the Balsa-matts are placed, another set of multiple GRP-mat-layers are positioned on top. The whole mould is wrapped in plastic foil and through a set of pipes a vacuum is enforced. Another set of pipes sucks in the resin which now creeps in every corner of the layup – including soaking the Balsa-core parts. Dried, this sandwich ensures a lightweight, stress resistant hull. Inbetween the Balsa-squares the hardened resin will then form a watertight “barrier” – when the laminate should be hit and opened, the water will only get so far inside the sandwich (of course destroying the wooden core) as it hits the next square “barrier”.
Modular assembly
We leave the lamination hall after more than one hour: Sadly, many – if to say, most – of the things seen here are secret, containing proprietary production secrets which the shipyard of course wants to protect. Nevertheless, our guests are free to roam the hall and our Excess guide takes his time to willfully explain any details in which they are show their interest in.
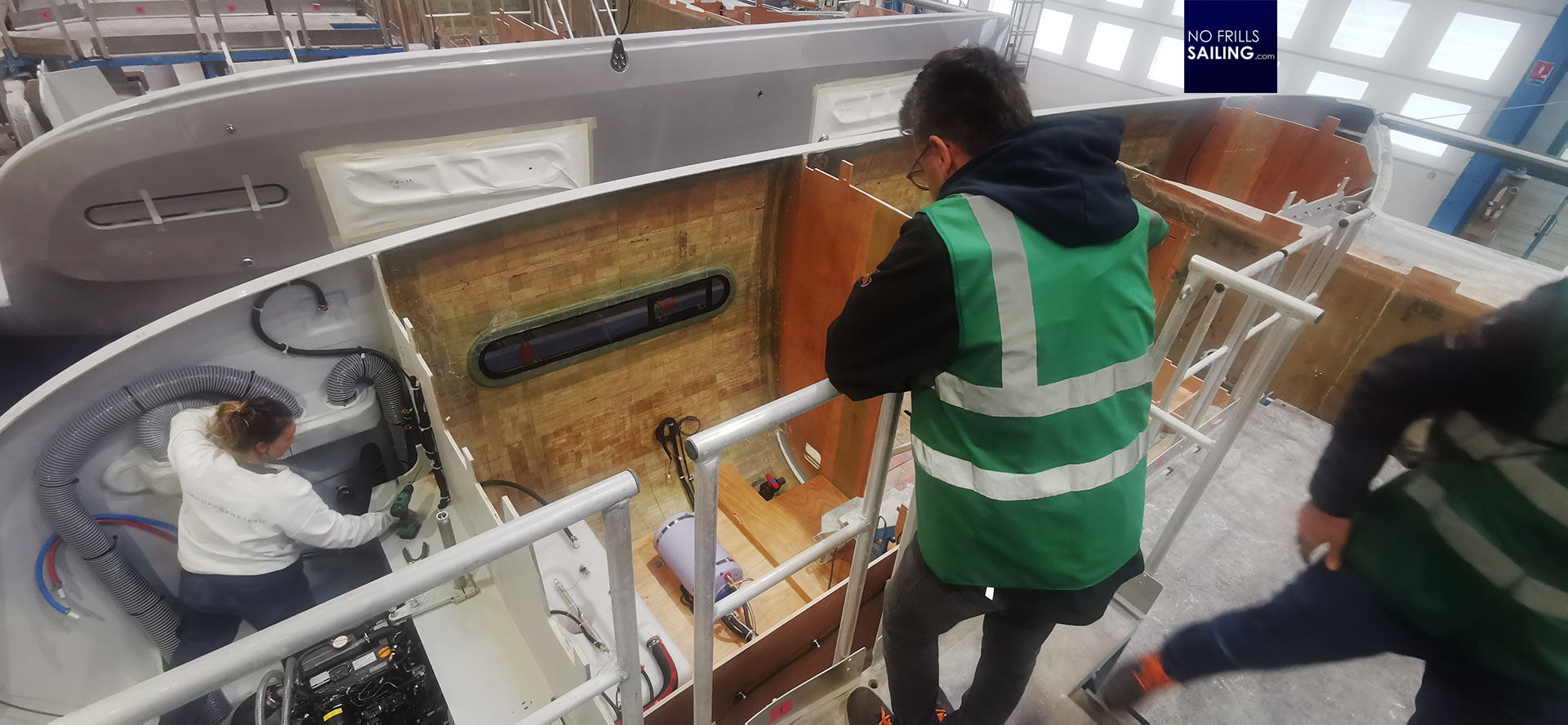
The next hall contains the interior fitting of the bare hulls. After the hull (remember, containing of three bigger parts) is put together and the principle bulkheads are laminated to it, it is transferred into an adjoining hall where it is put on cradles for the fittings. Being production boats, also an Excess catamaran is built in a modular way. This means, that most of the furniture parts or cabins are pre-fabricated modules which will be put onboard by means of a crane.
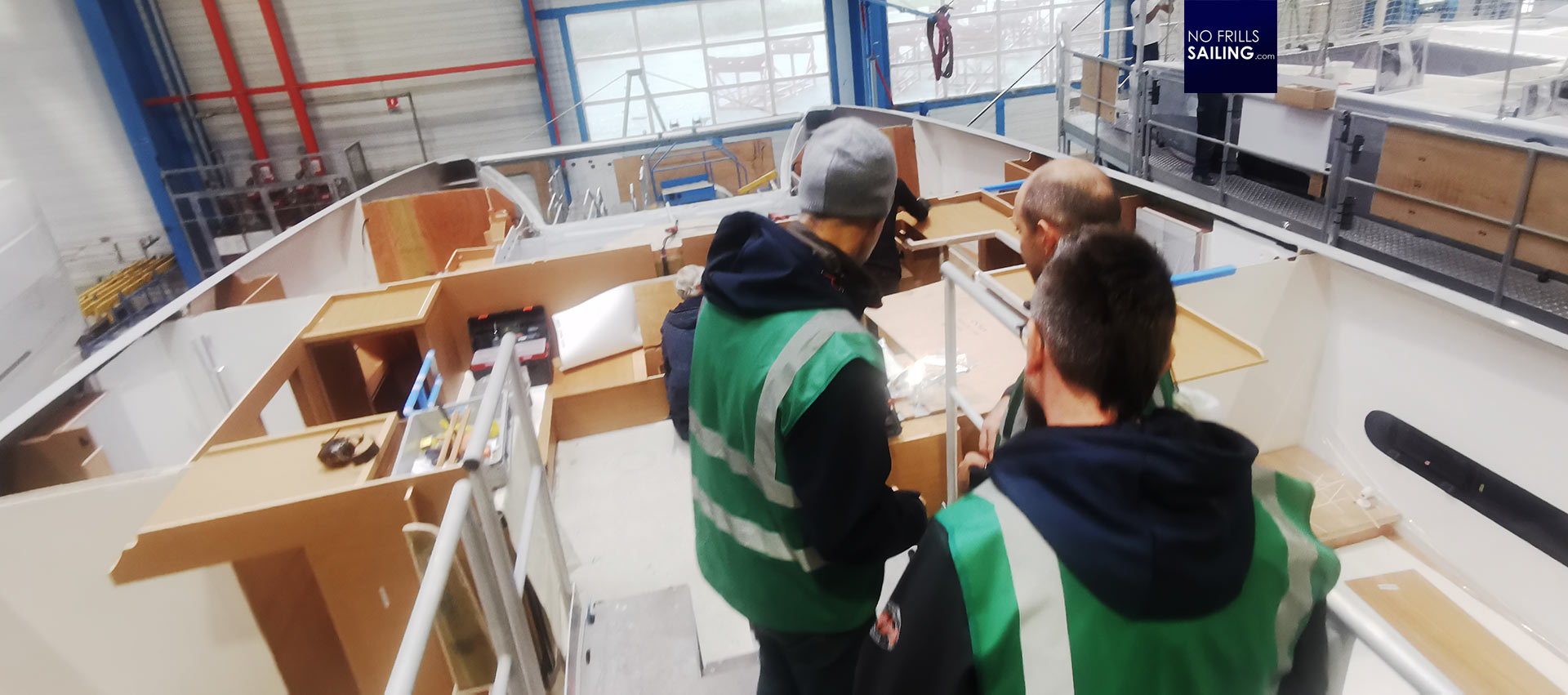
The workers start by the engines, saildrives and the whole gas/exhaust/cooling-systems back in the engine-compartments. Behind the “docking” pontoon the hall is filled with designated areas where the pre-fabricates wooden parts are assembled and fitted with electrics, lighting, plumbing et cetera (not possible to shoot a picture and show) and then transported via crane into the boats to be fitted. This is a process where the people and their actions are interlocking like a clockwork: A very cleverly and well-planned choreography of who is doing what at which time is unwinding.
Final fitting and first watering
It is this “ballet” we are witnessing, which is constantly checked by the supervisors, duration of the working steps, quality and function control, confirmation and clearing for the next people doing their tasks, which is the true power of this shipyard. Lagoon builds catamarans for well half a Century! This is the biggest catamaran builder in the world – know-how and expertise that is 100 per cent transferred to the Excess. I know the guys don´t like it for marketing reasons, but the Excess is the “performance sister” of the Lagoon – built and made by the exact same people (with some exemptions for specialized jobs and also built differently in terms of structure, lamination and so on). But for sure, these 40 years of experience in serious serial shipbuilding is a strong asset! We go on to the final production hall. Again, docked backside to a pontoon, the catamarans inside this “expedition” hall will receive their final fittings and parts. The boat, structurally, is finished. Everything is installed, she is principally ready to go. Here, according to the specification of the owners, the shipyard workers will put on all the details, small parts and individual installations.
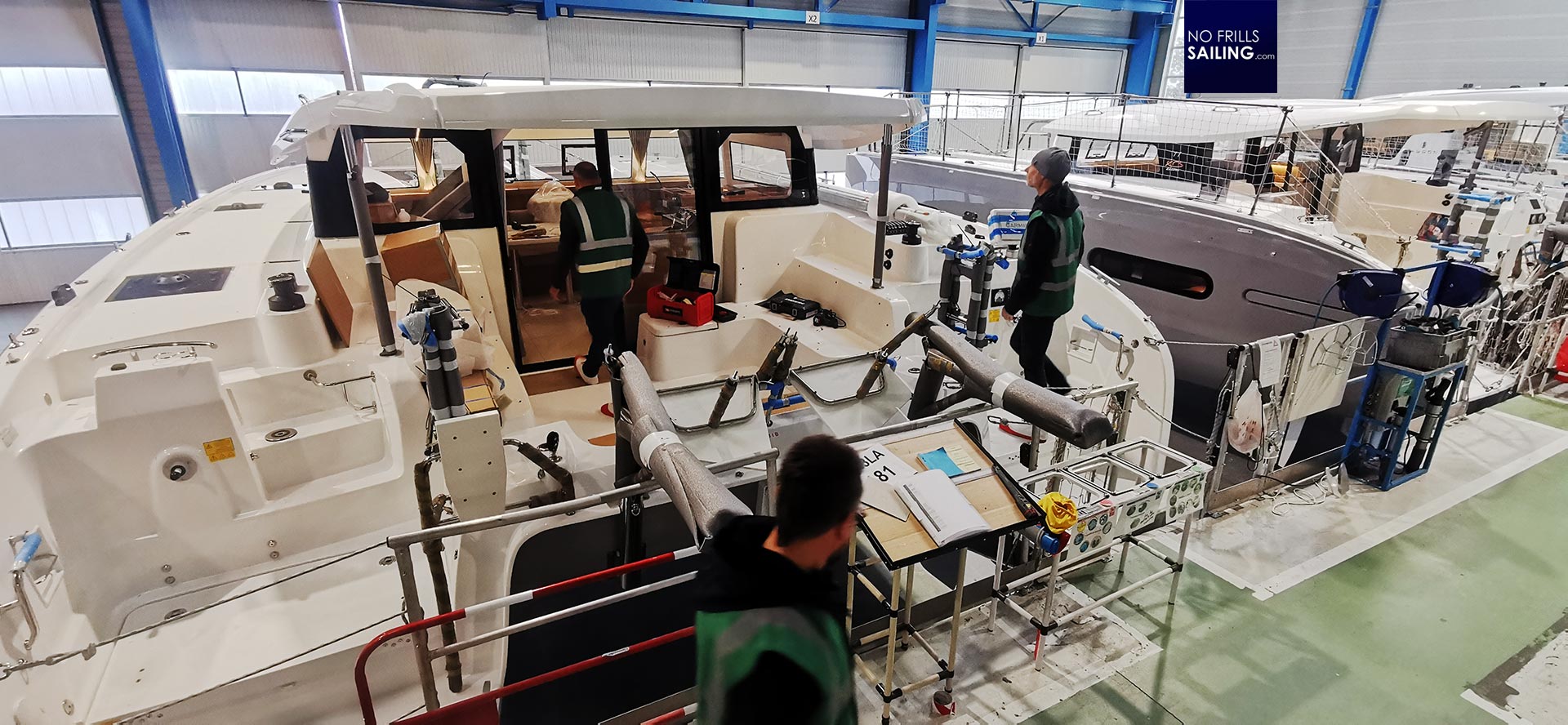
This can be the cushions in their different colors, the installation of davits, solar panels and of course all the dozens of boxes we as a dealer will have to unpack and install. Like the sails, the lines and ropes, anchor, chain, blocks and cleats. The bits and pieces which turn a “product” into a boat our customers can sail away with. Also, of course – and I could not photograph it – each and every catamaran is put to a last thorough quality check and into the water. Therefore, they have a huge pool fitting two cats at a time. Engine will run for 3, 4 hours, the boat is soaked in water sprays, simulating rain, to check if she is watertight. After more than 3 absolutely interesting hours we conclude our shipyard visit.
Back at the pier: Our catamaran is commissioned
Saying a warm and heartfelt Goodbye to our guide at the yard, we drive back to Les Sables d´Olonne. I have a little “bonus”, let´s say, for my guests. To round up our yard visit and connecting to the last step they have seen in the shipyard, my guests can now witness what is happening after the catamaran has left the holy halls of Excess: The commissioning.

We roam the premises of Yacht Care Services, one of the two big subcontractors of Excess and Lagoon, specialized in pre-commissioning the cats. Applying a hull paint, unpacking, rigging and getting the boat into the water, that´s their job. For us, around 80 per cent of the work needed to get a newly built boat ready for handover to the clients is done by our friends in Les Sables. All we have to do as dealers, is to come and check and add the last 20 per cent, like calibration of the network, last fixes, individual settings like onboard-WiFi or else, cleaning and preparing for the handover.
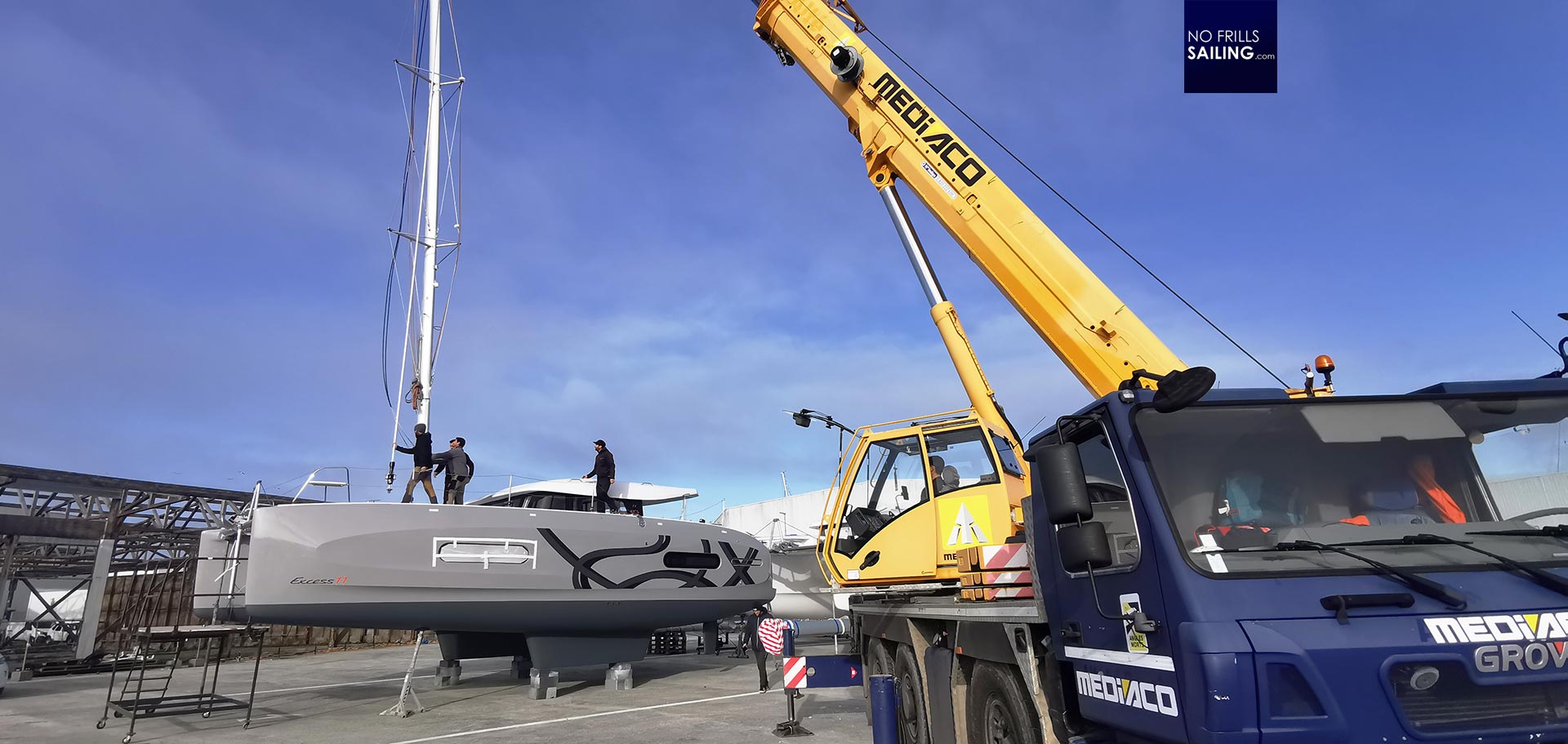
So, which adventure will this very catamaran go through with her owners? I cannot say for now, but surely this boat has been made by a lot hands and people working together to form this outstanding and fascinating product. Seeing the shipyard in all its details (even if I couldn´t show them all here), is very re-assuring and builds trust. Apart from that, I find most impressive to realize that those are real people, lots of friendly smiling and waving women back there in the yard, lots of young people and experienced “old timers”. It´s a boat made in the Vendeé, breathing the character of this fascinating and unique part of France. Maybe that´s the true and biggest message, and every time I come here with my clients and prospects, it never fails to amaze and excite me.
You might as well find interesting:
Catamaran boost: My first deliver through the Biscay in an Excess 11
How to escape a capsized catamaran and testing the emergency hatch
Sea trial of the all-new Excess 14 catamaran