You may have read my article about the Bavaria C46 as seen during the boat show Duesseldorf 2024. After the boat was awarded the renown title “European Yacht of the Year” I was keen on taking a look. Little had I done research beforehand, mostly because I was biased and honestly did not expect too much of a surprise, but I was puzzled setting foot on a truly well-built boat. To be specific: Her well-built interiors.
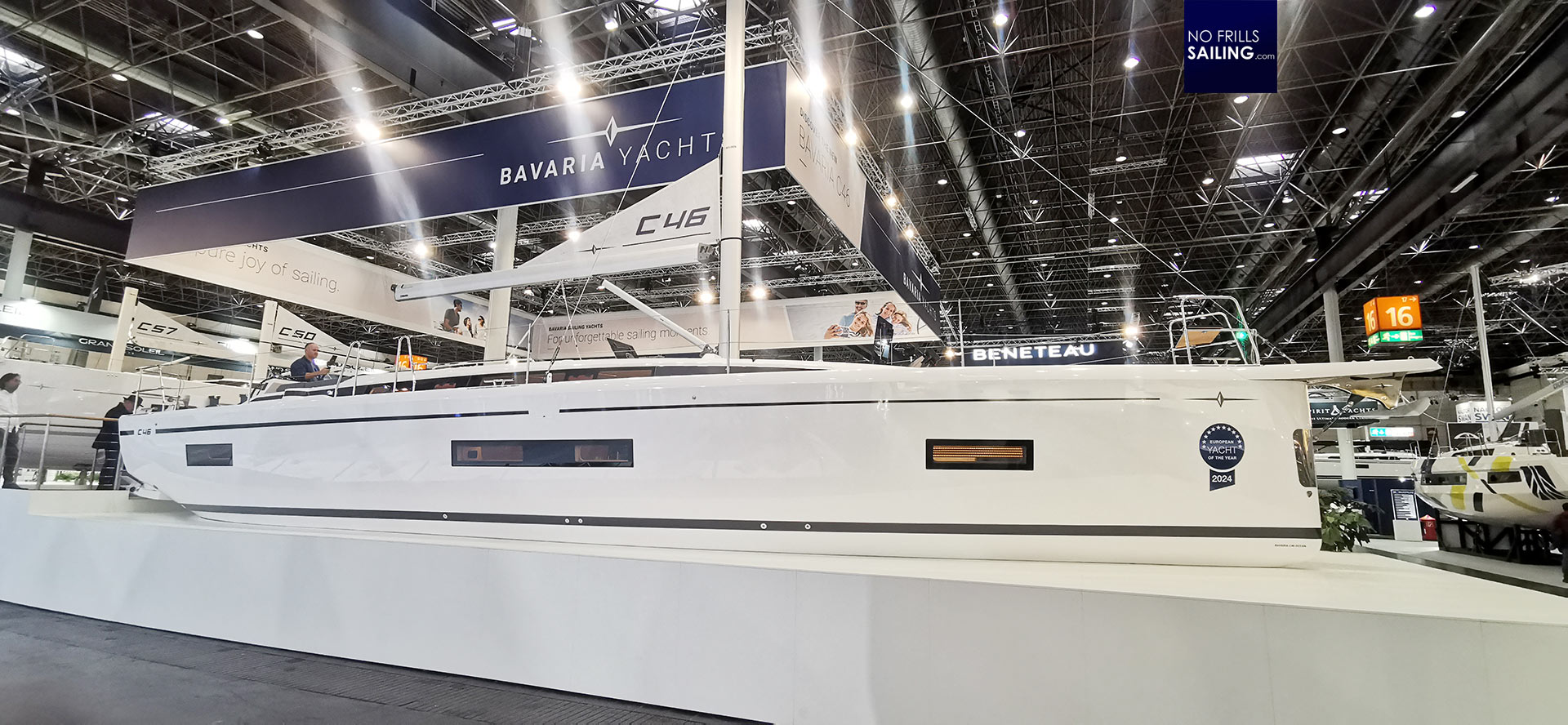
I was astonished how nicely the interior had been done, the joinery was not just beautifully designed by also had a high quality feel to it. Nothing squeaked or groaned. The fittings – like the grab handles – had a nice touch and I was astonished about the veneer quality, especially the thickness and robust quality of the edge bands. I asked Marcus Schlichting, Head of Marketing at Bavaria, if I could come and visit the shipyard: “Yes, of course!”, he agreed surprisingly openly. Now, roughly five weeks after the show, I dropped by at the Bavaria Yachts headquarter.
Somewhere in the nowhere
It was a cold early morning, the sun barely risen over a misty, half frozen landscape. The shipyard is situated in a small village called Giebelstadt. Where are we? Well, some of you may have heard the name Wuerzburg, the nearest city. Giebelstadt has nearly 6.000 inhabitants, it´s not a “Stadt”, meaning “town” in German, it´s a bigger village. Bavaria Yachts is apparently the business around. The large white halls are easily recognizable from afar.
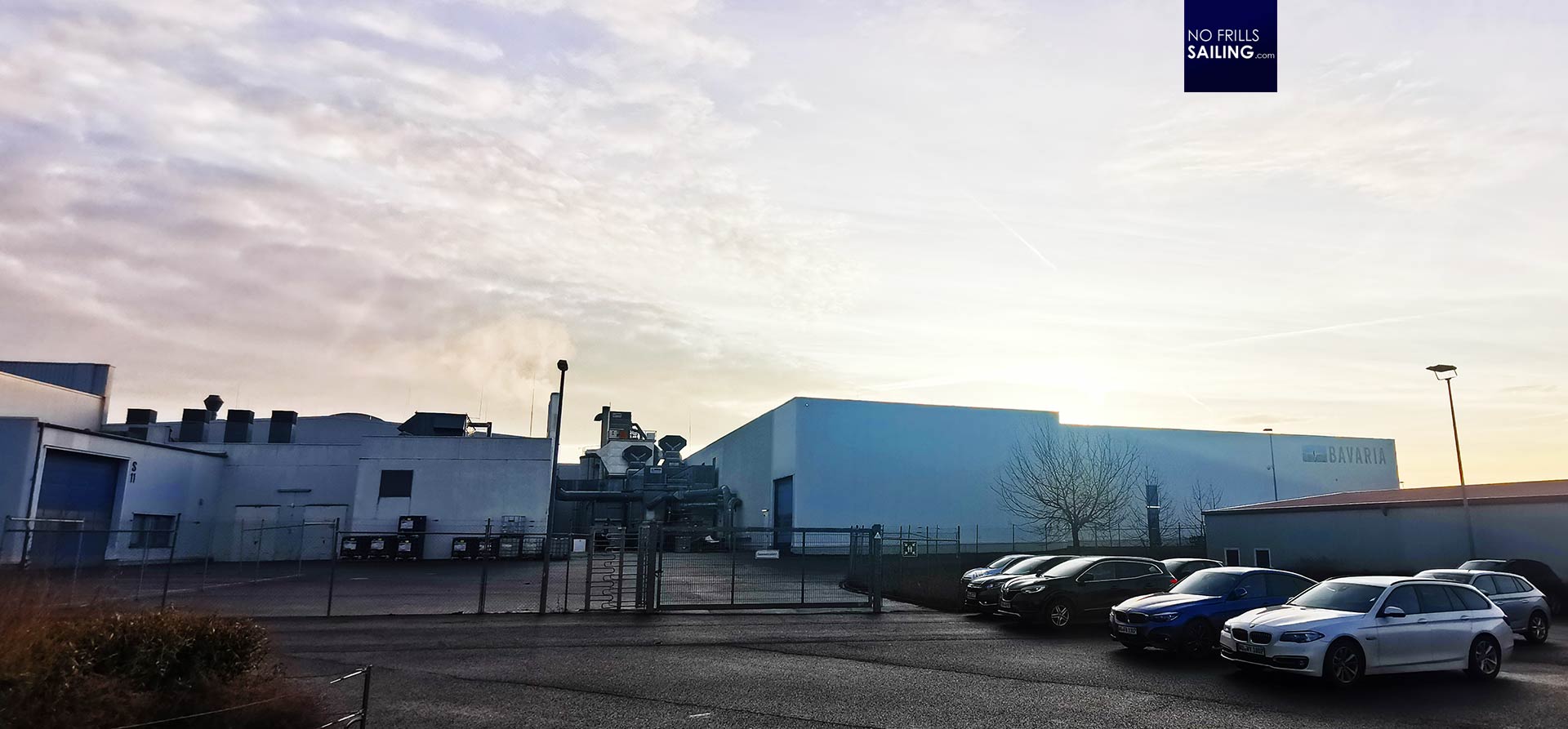
It´s a strange location: In the southern part of Germany (it´s Lower Franconia, not Bavaria, as the inhabitants would proudly persist to make clear) with hundreds of kilometers to the next shore. Nevertheless, since the company was founded back in 1979 as a joint business from the then window-maker Winfried Herrmann and a charter fleet broker, Josef Meltl, this brand has seen a some impressive growth but it also had some serious setbacks, the one we all have in mind is the insolvency back in 2018. Since then, they are on their hard way back onto the market, fighting for their customer´s loyalty and trust. You can literally see this history by looking at the large white workshops, the big Bavaria-logo, multi layered painted on the walls and in the eyes of their proud workers walking by.
A German success story
Marcus knows that I am especially interested in getting to see the joinery of Bavaria. The quality of the furniture I have seen inside the C46 was really good. But Marcus, a PR pro, said that we would take the whole tour. This was a good decision: Although I have been to so many shipyards since I´ve started blogging – big ones, small ones, industrialized ones and small workshops for one-offs – each shipyard is a bit different in how the work is done and organized. And so I was keen on getting the whole tour.
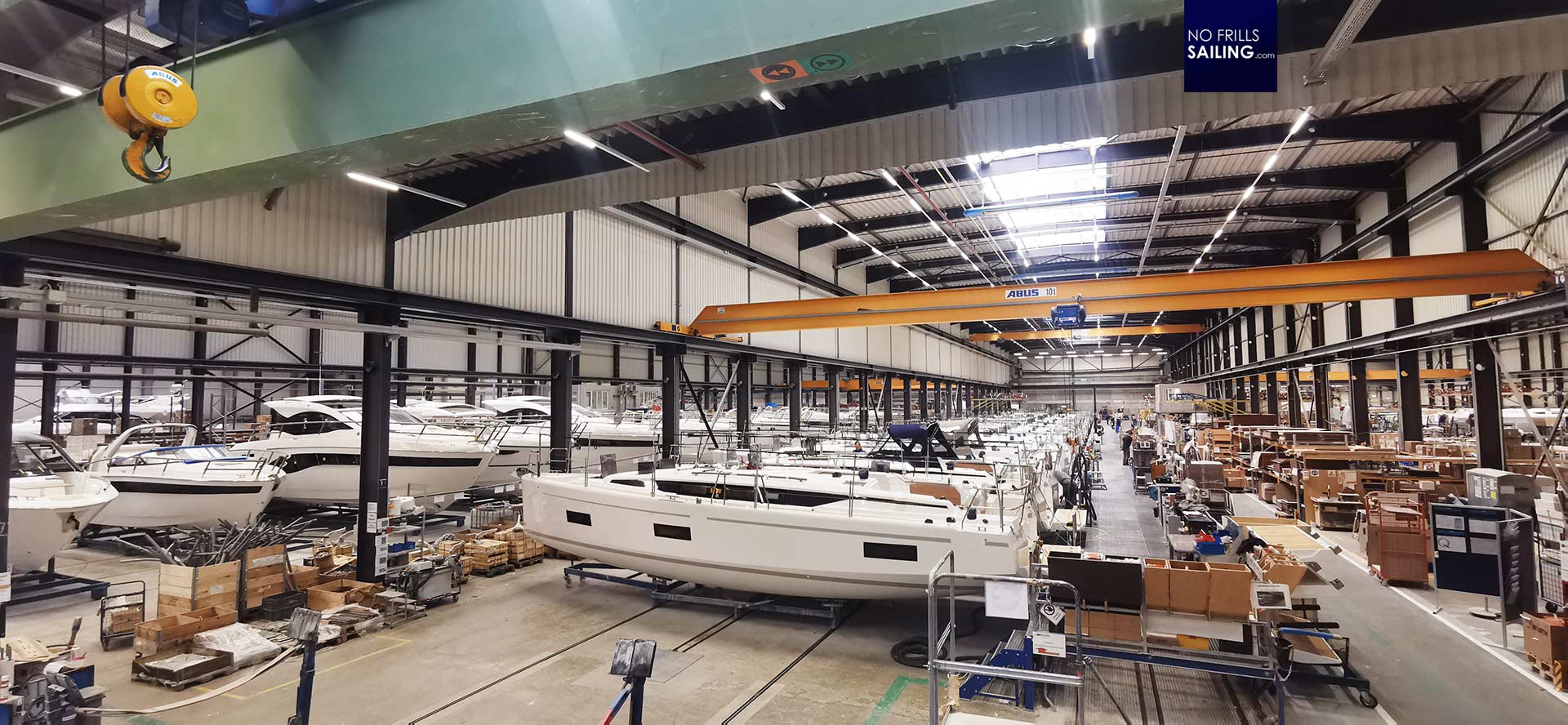
After the big bang in 2018 the shipyard is back into pretty secure waterways securing its place among the four big brands of series production boats. I see bustling activity in the halls, literally every square meter of the production is occupied, boats of all sorts, sizes and types are built in a sheer endless queue. Bavaria employees are working, walking around, carrying parts or moving hulls, decks and equipment. It´s reassuring to see such a hustle and bustle, because it means that apparently there are enough orders.
The Bavaria shipyard
The process of making a GRP boat is the same since many decades. Bavaria manufactures most of their yachts in classic hand-lamination. “We can do vacuum infusion of course”, Marcus explains, “but for our market, client base and the use-case for the majority of our boats, the advantages of vacuum infusion are miniscule.” It all starts with the application of the first layer, the Gelcoat. A huge hull mold is “flying” past us, from behind I can see freshly prepared hulls in line waiting to take on their white coating.

The lamination at Bavaria is organized in a way I have never seen in any other shipyard. There is no dedicated line for a specific type, but rather everybody here works on every type and form of boat. No matter if it´s a power boat or sailing yacht, no matter if it is a small sized boat or the flagship, the C57. “Well, it is all the same, isn´t it?”, Marcus explains. This goes for the Gelcoat, but when the molds enter the next hall for lamination, things get a bit complicated.
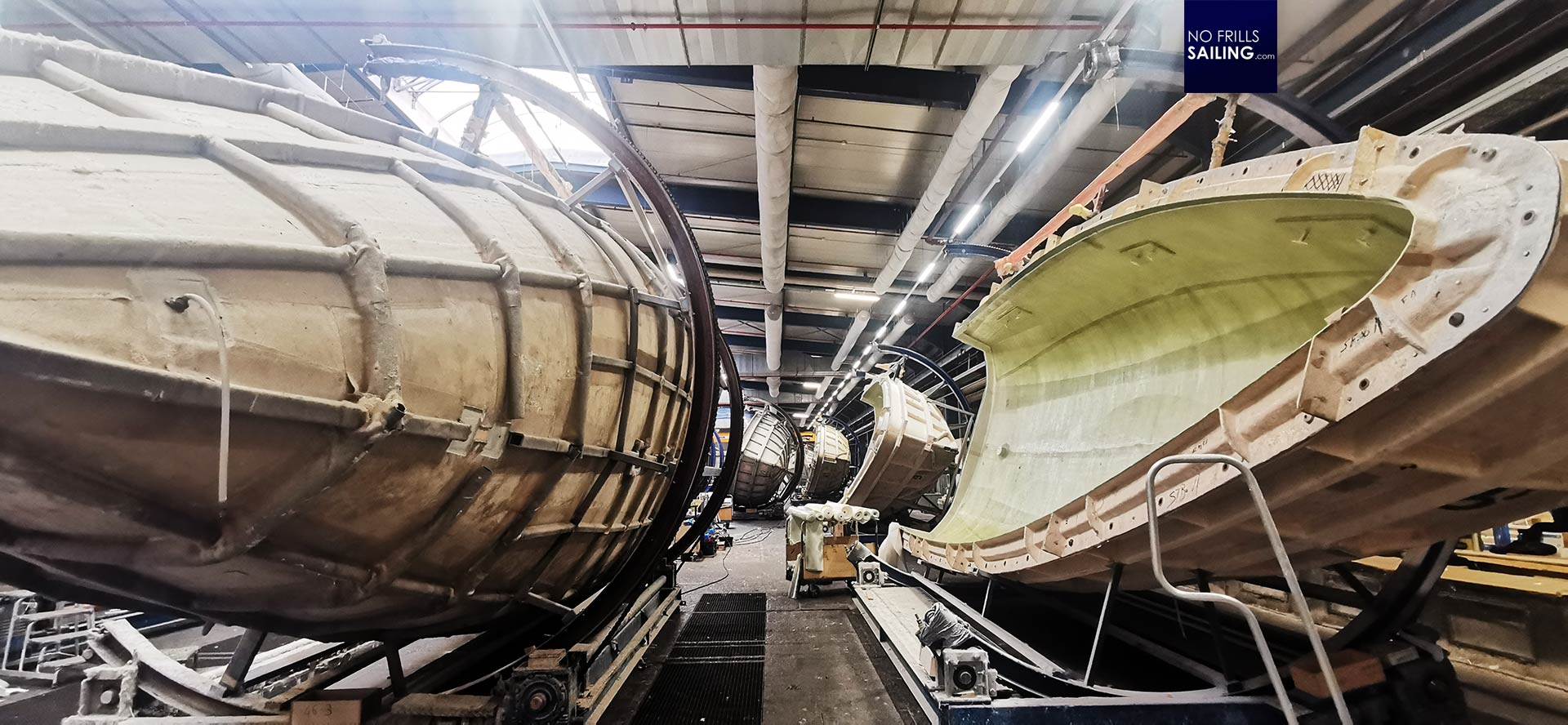
Each team on each mold must recap the layup specifications when laminating. This is important because the guidelines by the naval architect and structural engineers must be followed to insure the maximum stiffness, least twist and distortion. As in every GRP-shipyard, the air is filled with biting odors of the resin, we keep our distance from the freshest of them laminated molds to protect our lungs.
Handcraft meets High-Tech
So far, so good. I recognize many similarities to the shipyards I have seen so far, but there are also specialties. For example, I´ve never visited a yard before that employs autoclaves, essentially big “ovens”. There are two of those in which they heat-dry the freshly laminated parts. As we pass by, a deck was parked inside one of those.
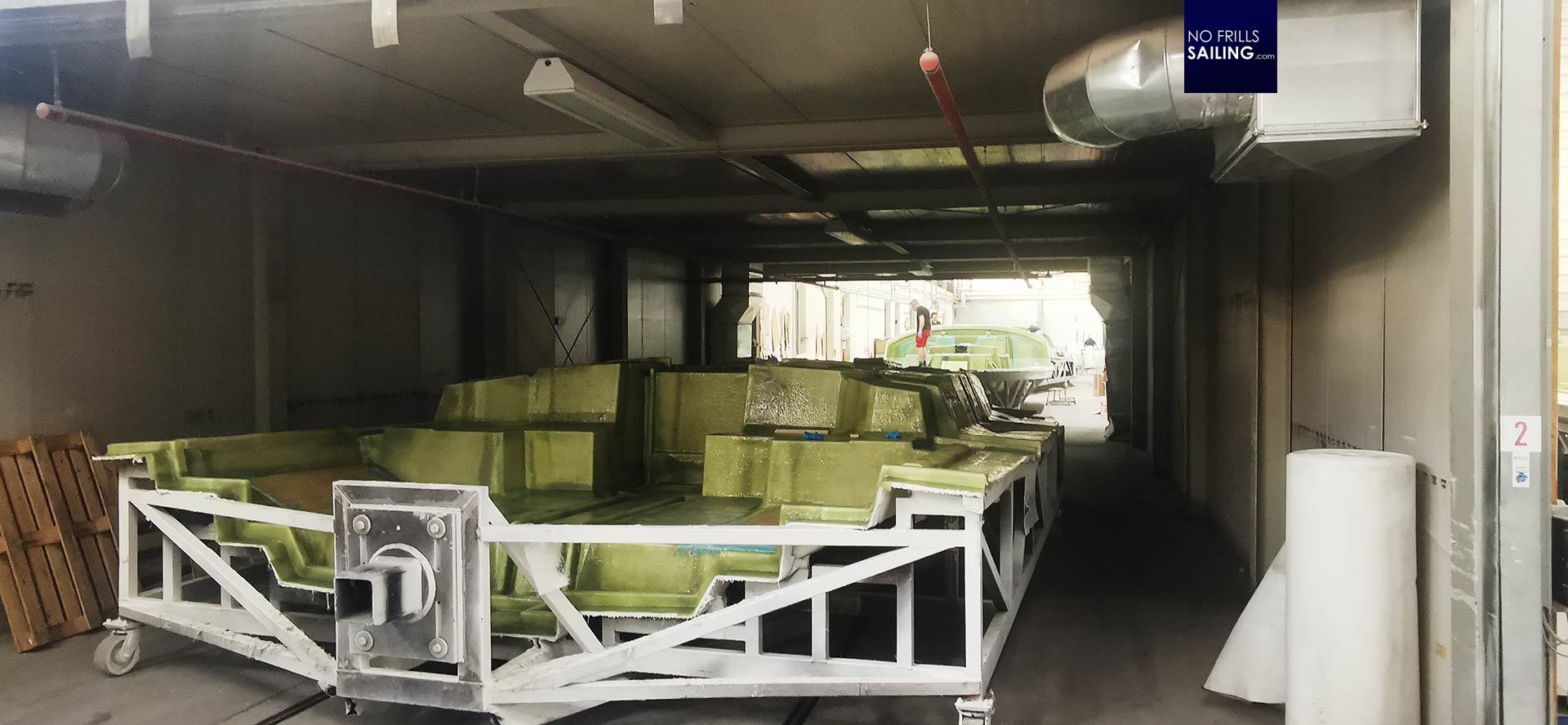
The temperature isn´t that high, I mean, you couldn´t bake a Pizza in here, but they say they can significantly reduce the drying time of the laminates by applying heat and thus speeding up the overall production time of a boat. Another highlight is to be found in one adjacent hall: The CNC machine.
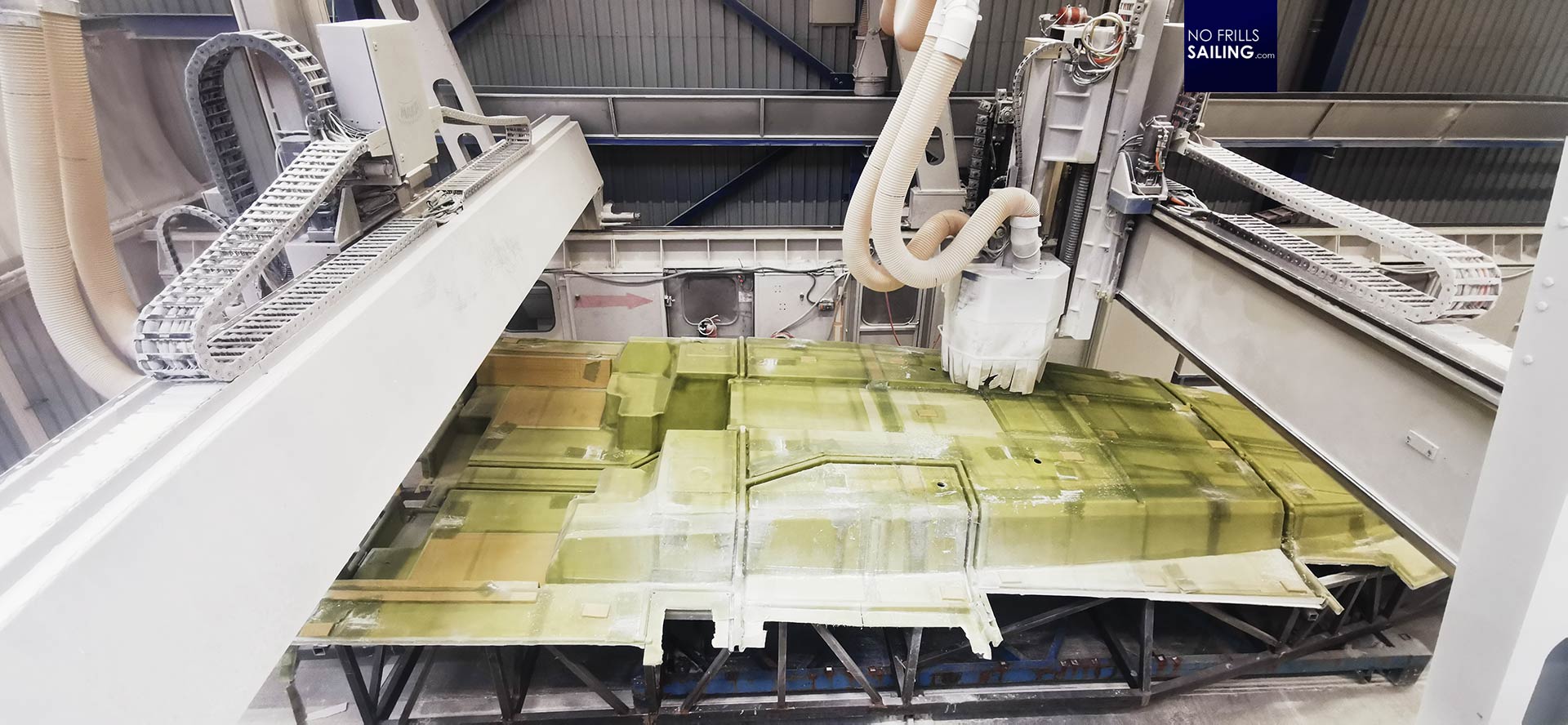
I´ve seen many of them in many shipyards, yet this one is special. Whereas on the machines I am familiar with one single robot is milling, cutting, drilling and sanding the boats and decks. This particular machine has two robots which are operating on one boat at the same time: It again reduces building time. Marcus tells the story of a fire, a cutting device had caught, lighting up the boat inside and having the machine standing still for a couple of months. “We had to organize this work to be done by hand again”, he says: “It took us many weeks to just make gauge models for each boat so that our guys would be able to make their cuts and drill their holes at exactly the right positions.” Making a boat is a lot of handcraft work – but you also need at least some degree of automation, especially when putting out large numbers of units.
Finally: The Joinery of the shipyard!
After seeing the hull and deck production, we finally enter another workshop. The smell of wood, Teak and plywood, a scent of slightly burned chips – indicator of wood-cutting and sanding going on – fills my nostrils. I am familiar with this odor, during the refit of my King´s Cruiser 33 this was what I was smelling for four years …
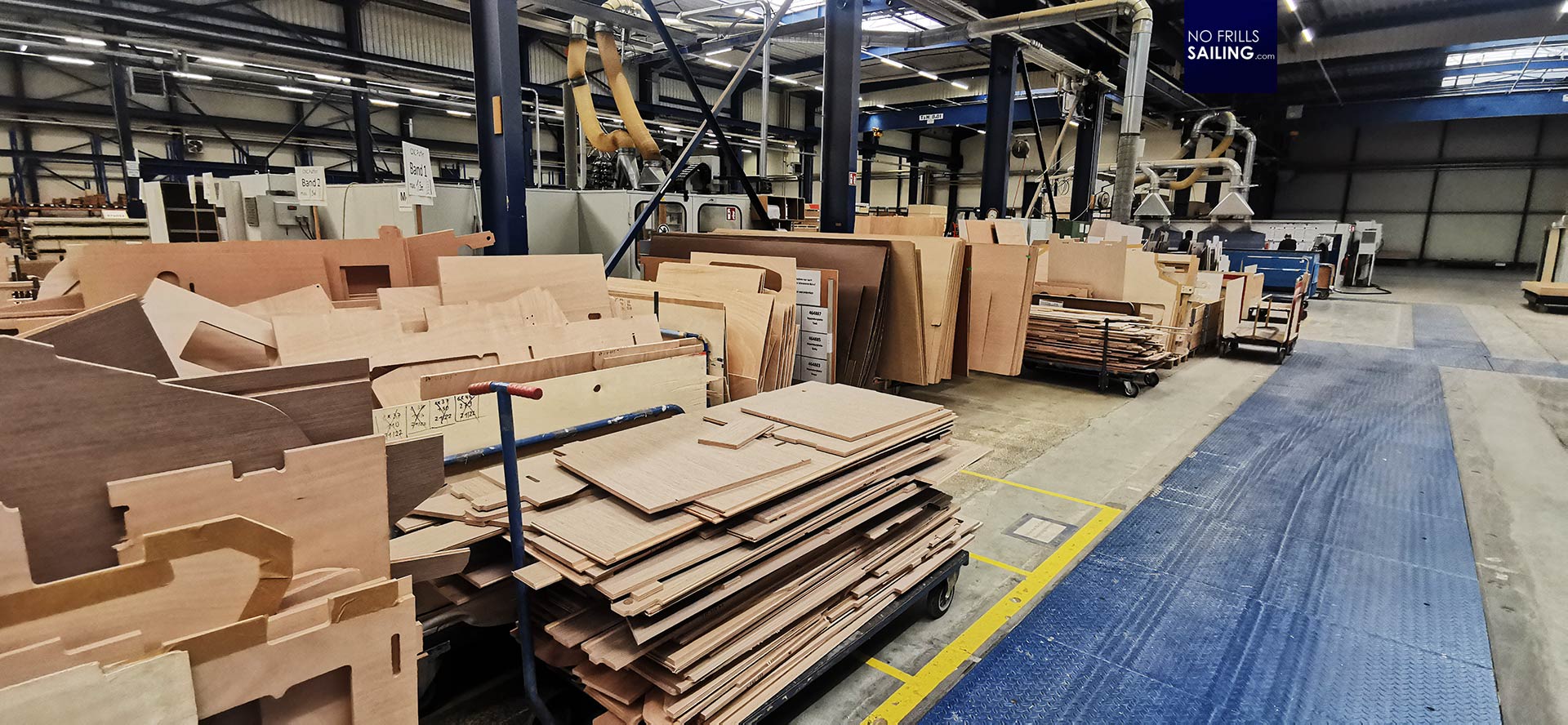
The material storage is arranged in “islands”. Push carts and large trolleys containing wooden parts, thin sheets of plywood and thick boards of massive wood. Handwritten notes, route cards and barcodes make it possible to track each sheet through production. “In the early days the joinery was much bigger.”, Marcus says: “We received whole trees which had been treated to become veneers, battens or furniture. This was the DNA of the company back from the windows production.” Nowadays, such an in-house production wouldn´t be financially sufficient. But there´s still something to this place …
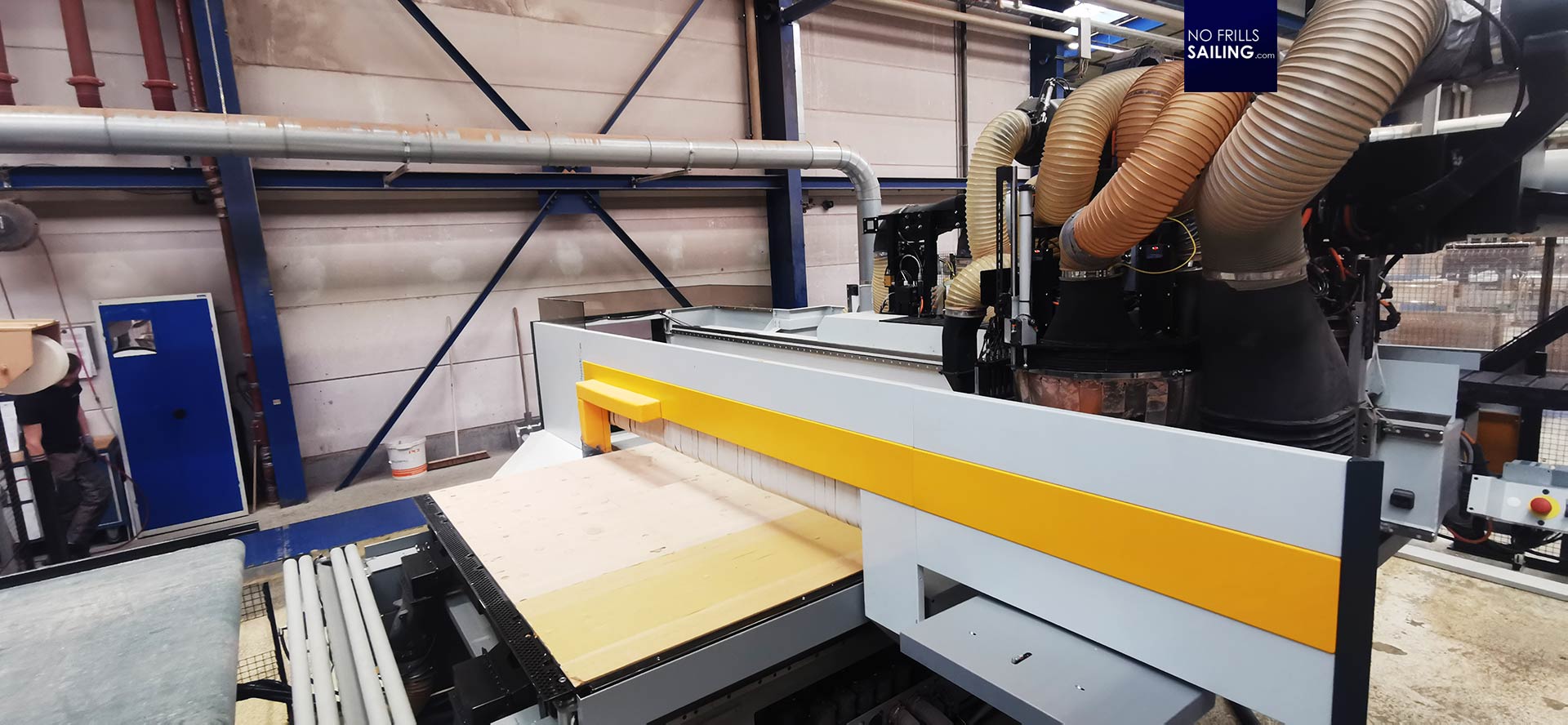
The sheets and boards are cut by huge CNC-robots, of which I observe for some minutes. After cleaning the machine from the previous operation, the worker places a large wooden plywood board on the “table”. A program is entered, the robot starts to cut out the parts. This process is surprisingly quiet – I had thought we would be wearing ear protection, but there is literally no noise in here although huge machines are working around us all over the place.
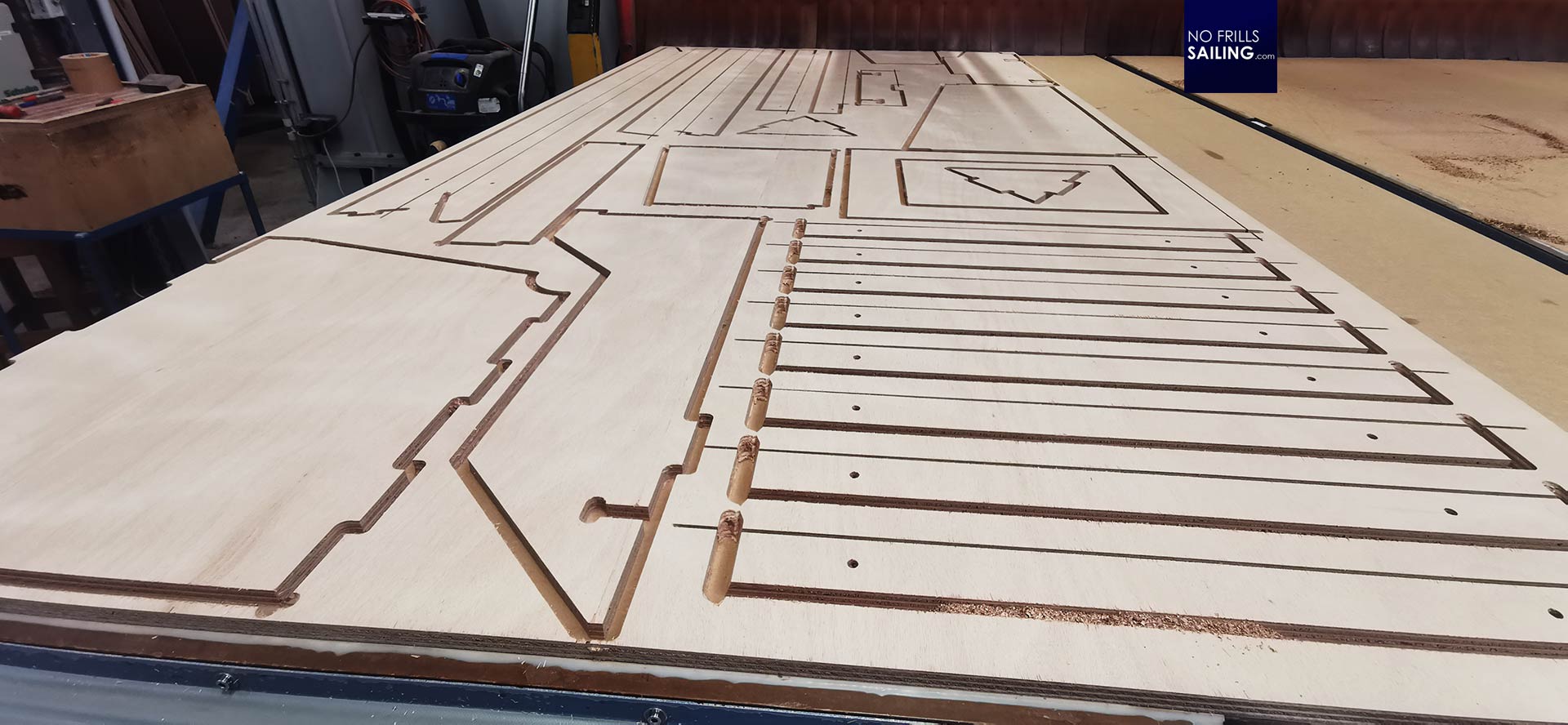
On the opposite side, another big table, the wooden part is slowly re-appearing after having entered the machine. I cannot identify what exactly the robot has cut, but I can see a spotless work. “All parts are precision cut here”, Marcus tells me. “Basically a huge puzzle that is put together later on.” At the opposite side of the hall, another impressive machine is located. We head towards it.
Automation: Wooden parts coating
On our way through the production Marcus and I greet the workers. Many are smiling, some seem to be are a bit grumpy, which is just the way they are here in the deep South of Germany. Listening to the heavy Bavarian (or Lower Franconian, I am sorry!) accent quickly reminds me of this very special and kind of weird fact, that we are here in the middle of nowhere. Arriving at another big machine, a very un-grumpy and funnily joking specimen of Lower Franconian worker, greets us: “This is our painting machine”, Marcus says.
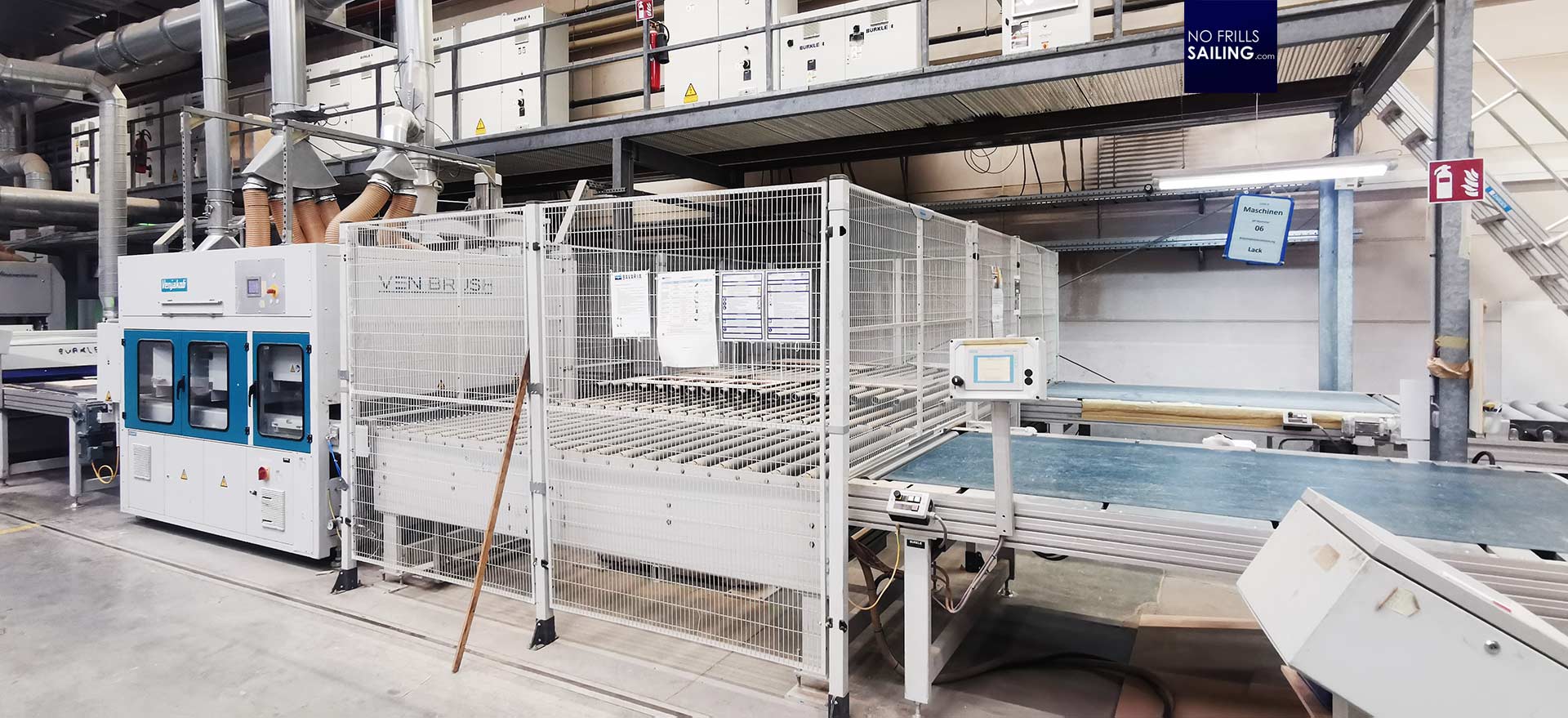
This machine can spray-paint the wooden parts as wished. Glossy paint, matt paint, impregnation: Depending on the program put in. “It is able to apply no less than six layers of paint and have them dried as well”, Marcus explains, as the worker puts a number of wooden parts in a conveyor that is slowly but surely transporting the parts into the protected inner of the machine.
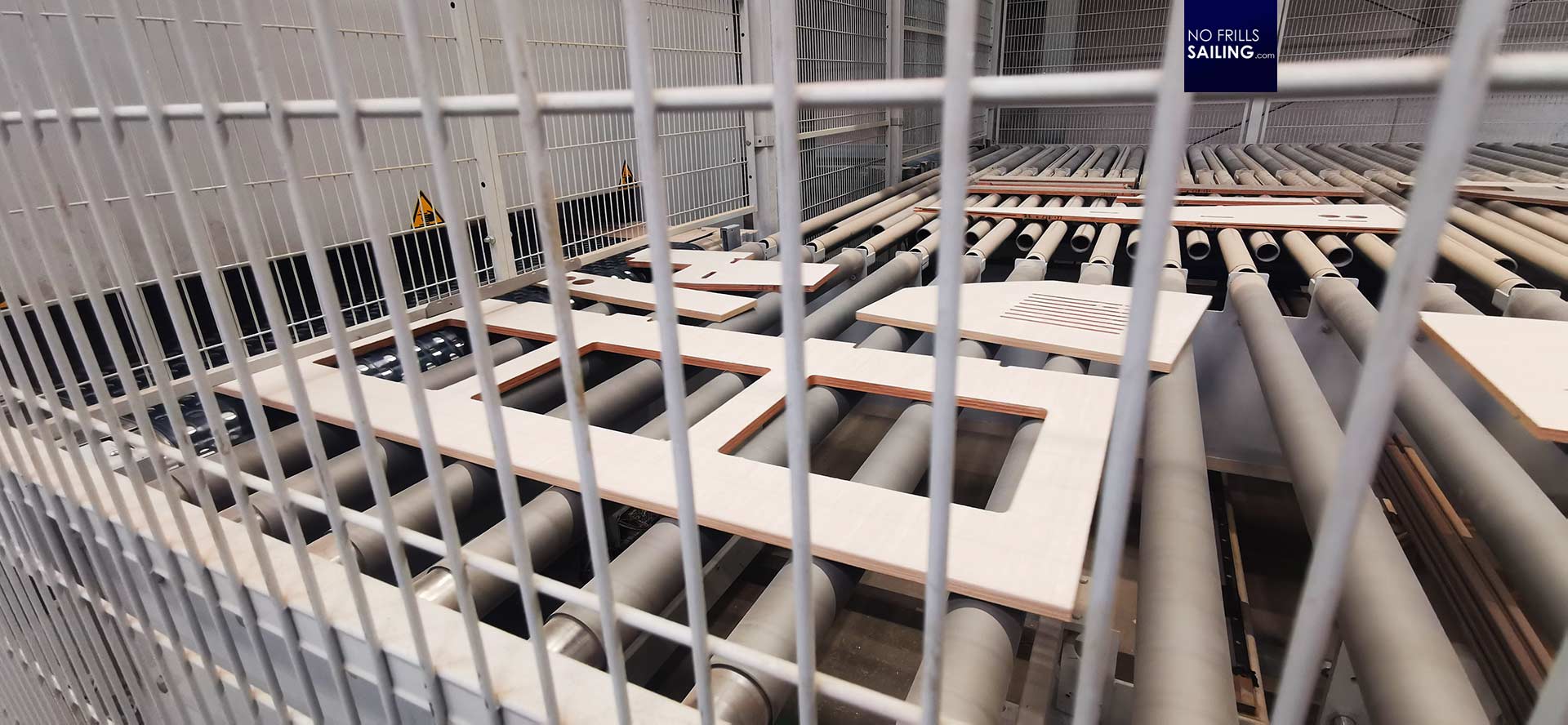
Two of those chambers have glass fronts so that I can look inside. Two spray-arms with two nozzles each are constantly hovering back and forth over the wooden parts which are rolling underneath them. A camera is “watching”, probably a quality checking device. Passing through the paint chamber roughly takes a minute.
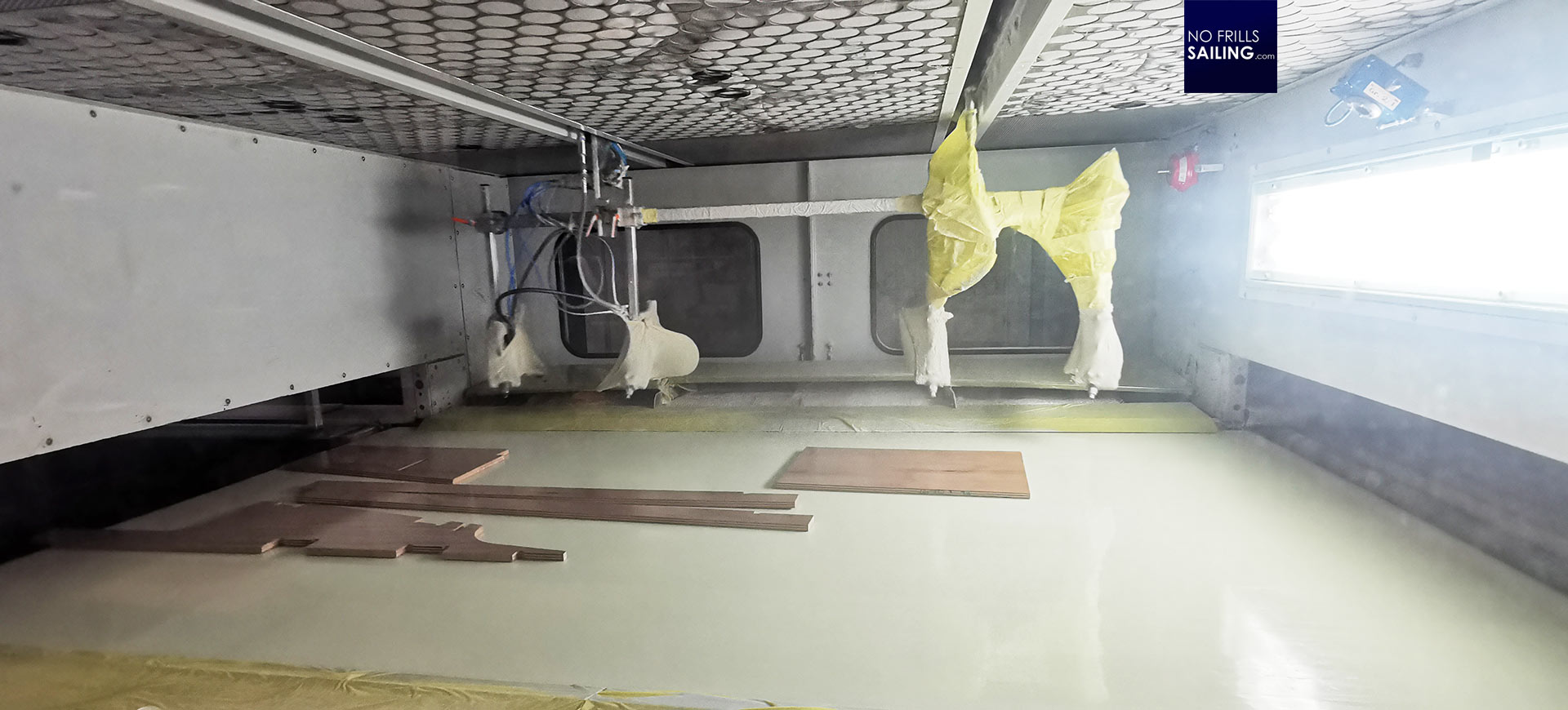
Again, to speed up drying process, the freshly painted parts are funneled through a heavy UV-light exposure. This process is kind of soothing. A never-ending stream of blunt wood enters. And eventually re-appears after some time, coated in gloriously shiny gloss-paint. Again, no noise and, what surprises me most, no smell.
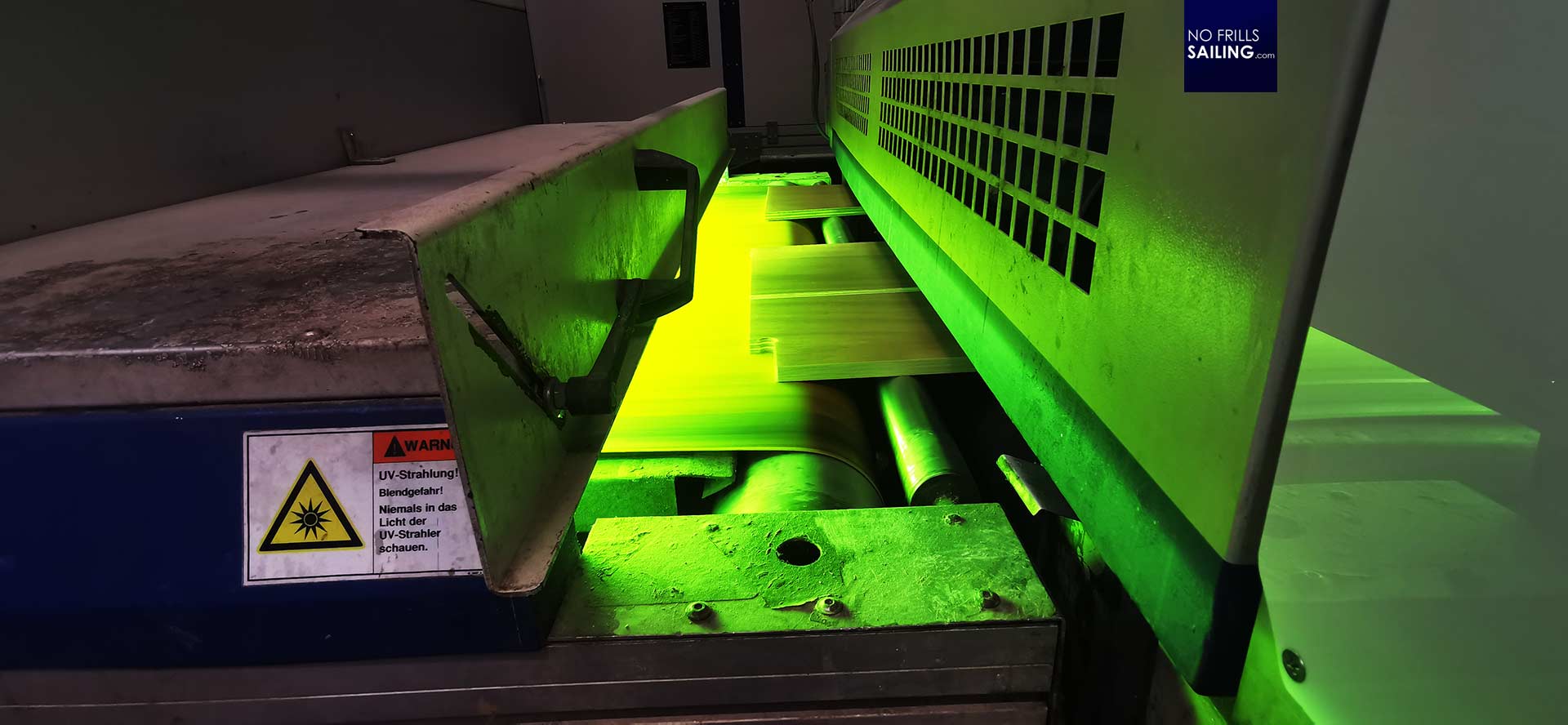
As impressive as it looks, so far I cannot see any bigger differences to other yards. The fine joinery I´ve witnessed during Duesseldorf is made with the same machines and processes others employ. But why did the Bavaria C46 make such an impression on me? Maybe because I was biased by our “own” products and I lost a bit the sight for our competitors? Maybe …
The secret of their massive bandings
Most apparent in furniture quality on production boats are the edge bandings. Why? Because of the fact that massive wooden joinery parts are too cost-intensive for production boats, manufacturers use those thin wooden “framings” that run around floorboards, tabletops, cabinets or flaps. Of course, when in use, those edge-bands are the “neuralgic points” in every boat´s furniture, so I am especially keen on checking how Bavaria does it.
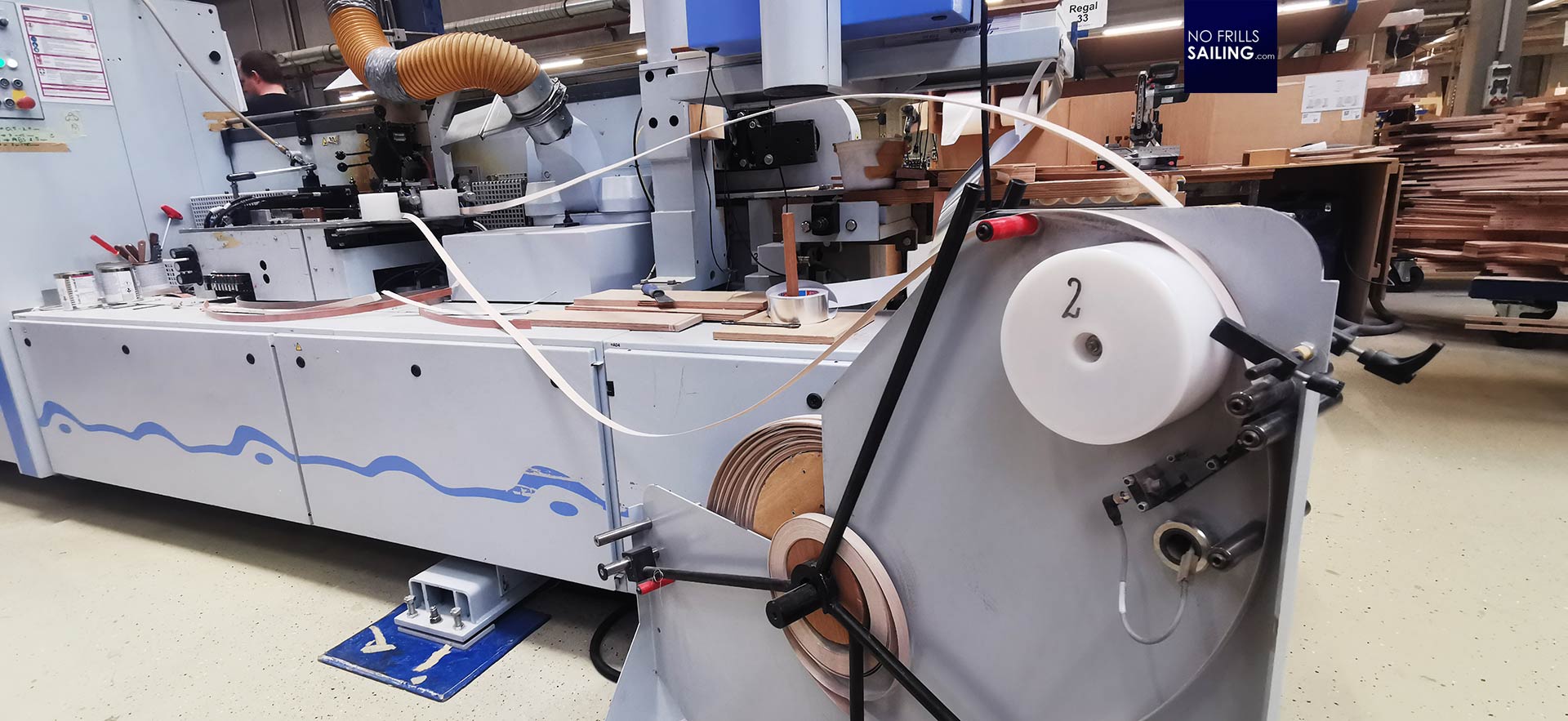
The banding machine is operated by another very friendly guy. He shows me how to do it – which in the end isn´t that spectacular. At the backside of the machine two large coils of wooden banding are put. They run over many rollers fed into the machine´s inside. The worker is on the other side, putting – for example in this case – raw cut and painted floorboards onto a track.
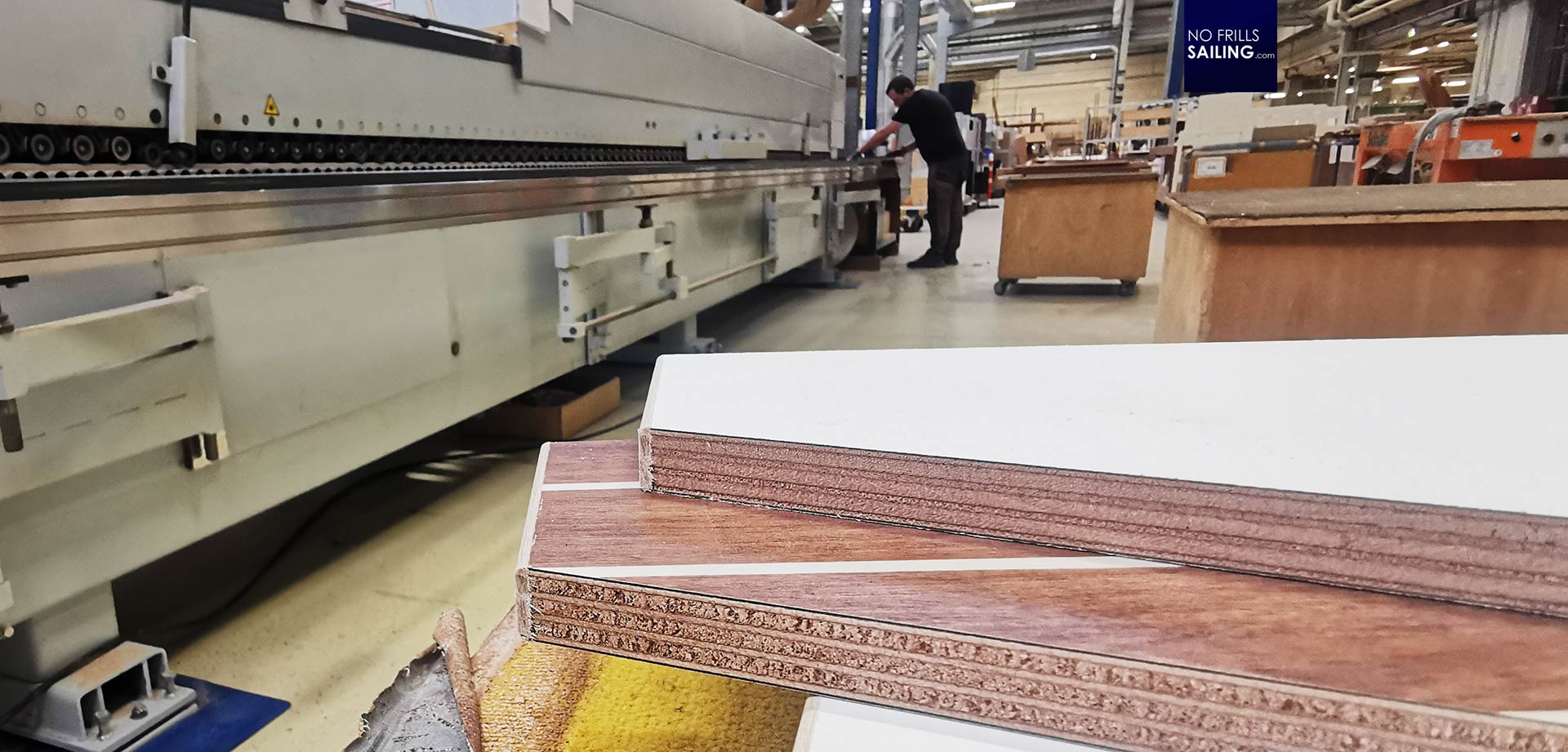
The floorboard is fed through the machine that heat-glues (some call it “ironing”) the banding onto the edge of the piece. The end product is a firmly attached, thick banding that has a real quality. It not just has to look nice, it is expected to be standing the test of time and rough handling (mostly by charter crews).
The big wooden puzzle
After all parts have been made that way, they are put on another pushcart and being brought to one of the nearby assembly “islands”. There, as we know it from so many big industrialized shipyards, the furniture is put together in modules. I see large parts which I can quickly identify.
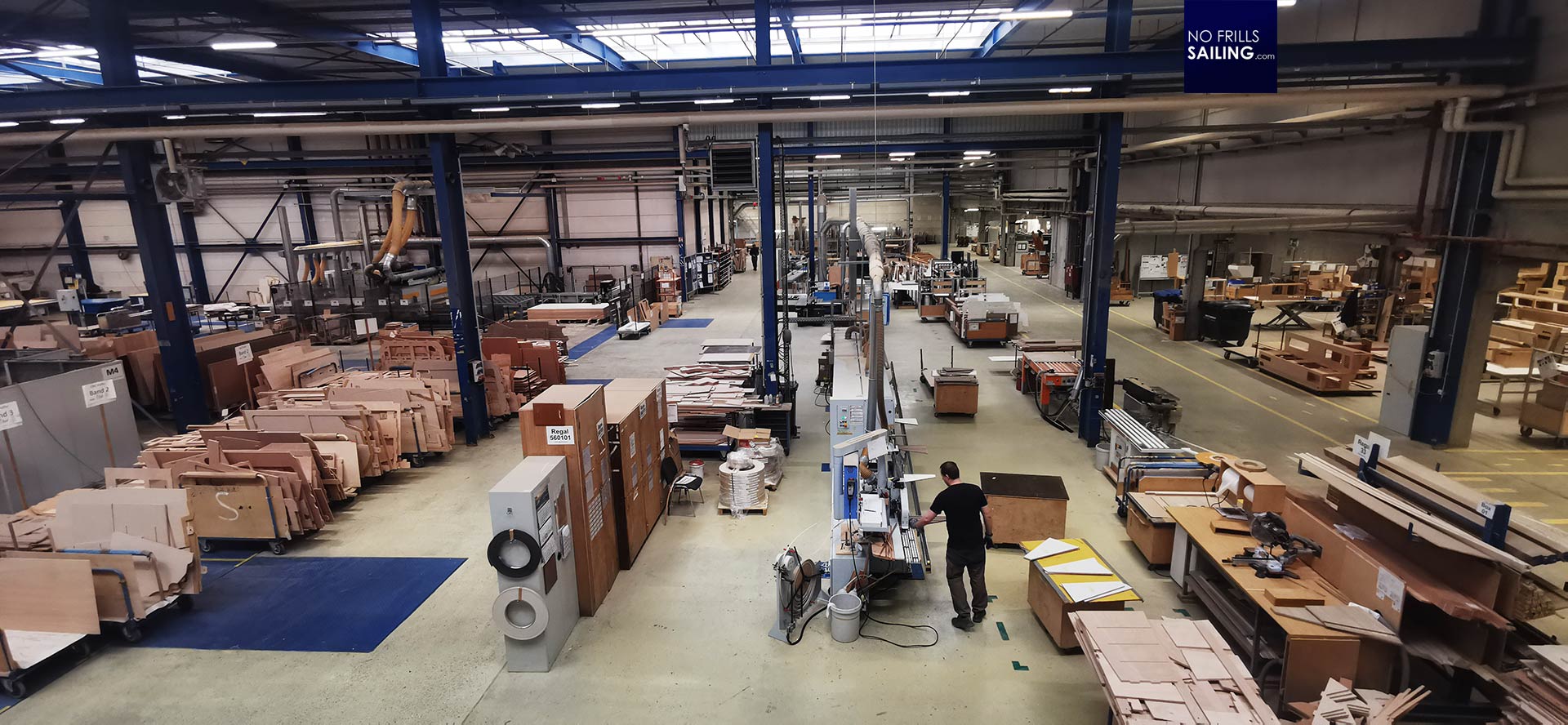
There is much space inbetween so that people and their materials can pass by quickly without hitting into somebody or something. Some of these “islands” are used to store raw materials, some are a kind of hold for pre-fabricated parts and some are used as fitting areas where whole modules are fitted. We walk towards this area so that I can have a look onto them.
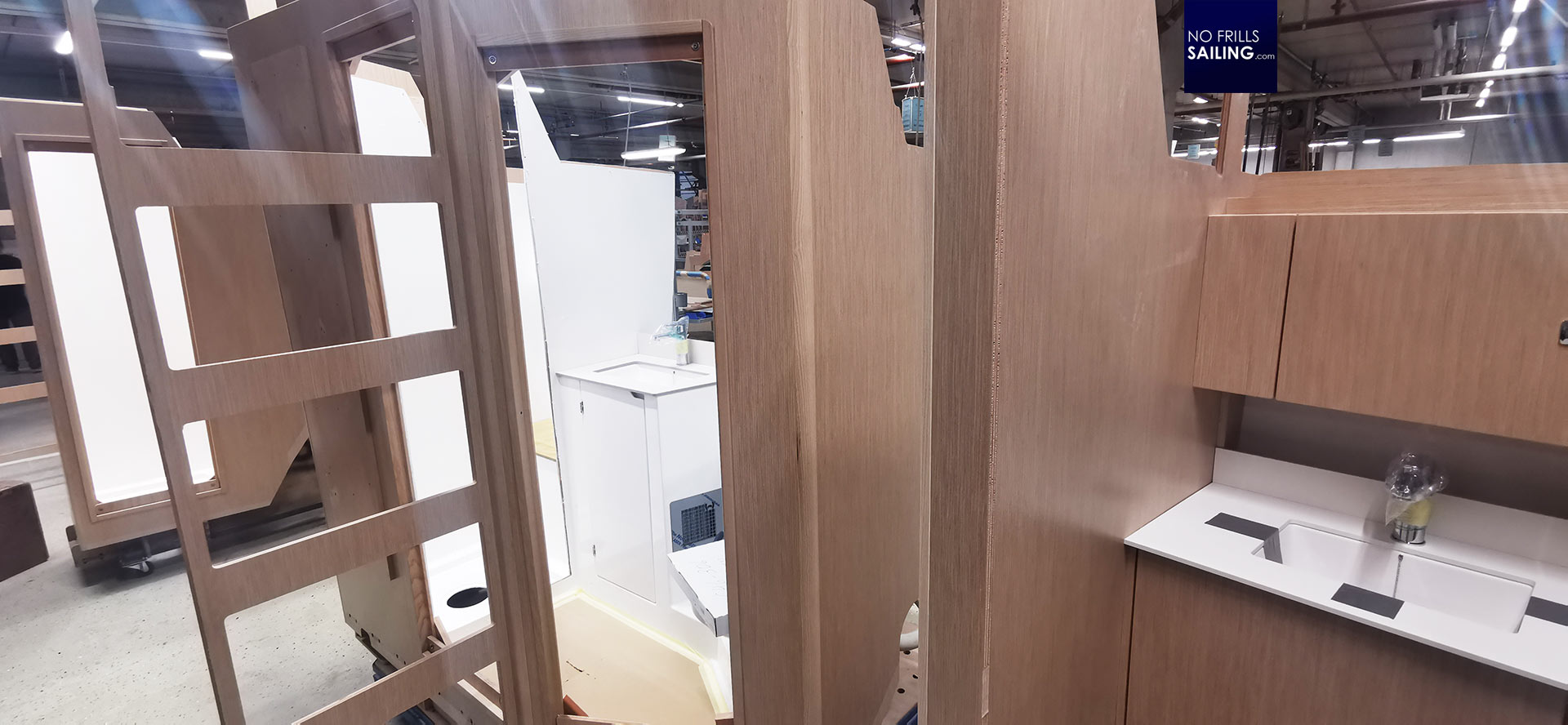
One of these is dedicated to galley modules. There is much space for the workers to access both the front and the backsides of each module. Making those is not just bringing together the joinery parts but also to already install all electrical and mechanical parts needed. For example here where the galleys are made, the complete fresh water supply and drainage is already in place, just along with the equipment, LED-lighting and such.
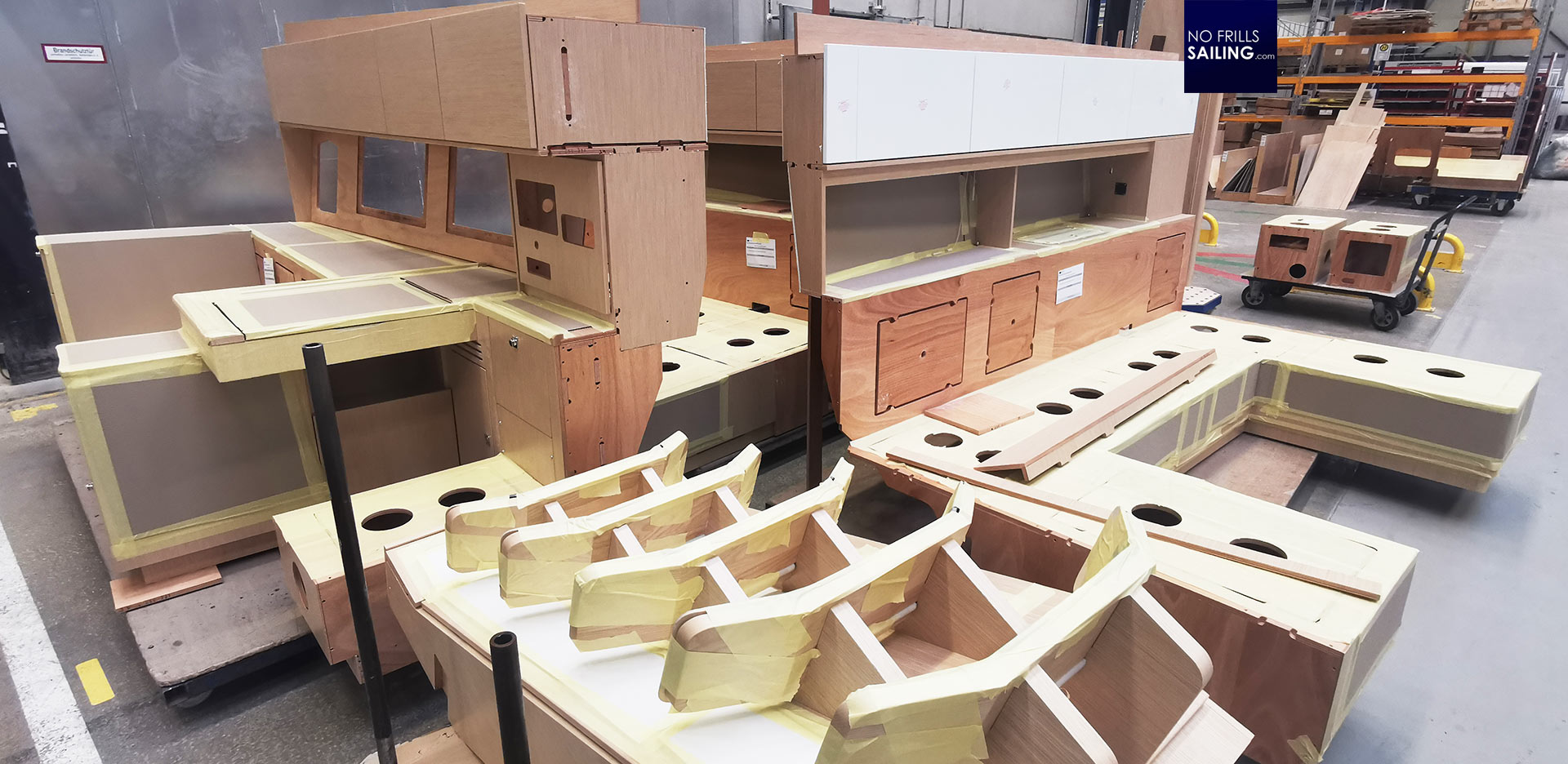
After a quality check, the modules are set up with some protection for the most exposed areas and deemed ready for installation into the boats. In designated “waiting areas” the modules – completely pre-fabricated and pre-installed with all wiring – are awaiting the fitting crew to be brought into the big halls where the boats are finalized.
Worth being proud of: The end product
The modules arrive one by one after each other just in time. These are also build in a way that the wooden modules come with built-in lift-eyes which accept either a crane or a special-purpose built gantry. Attached to it, the module is lifted and placed into the hull at the designated location. Held tight by the gantry, the module cannot shift much so that a precise fit during glueing, lamination or screwing of the very module is ensured.
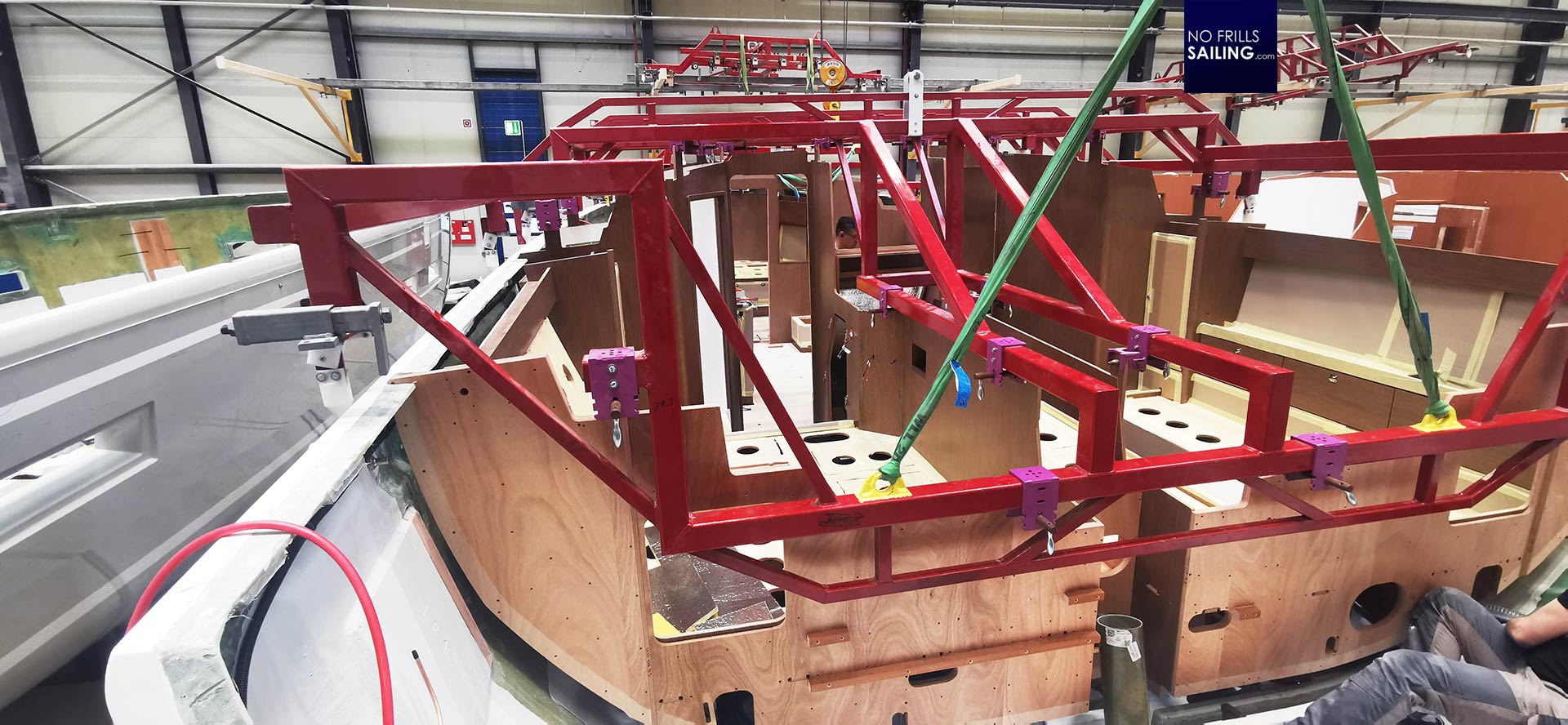
Piece by piece the modules are fitted, just after the bulkheads, technical parts like engine, tanks and piping have been installed. Inside, nothing will be visible for the owners and guests. A nice wooden interior, just as I have seen in Duesseldorf. “Now you have seen the complete production here in Giebelstadt”, Marcus concludes our tour. And just as if it was pre-arranged, a brand new Bavaria C46 is there with some stickers on it for last works before delivery. This is how my voyage began, some weeks ago on a boat like this with an appealing interior.
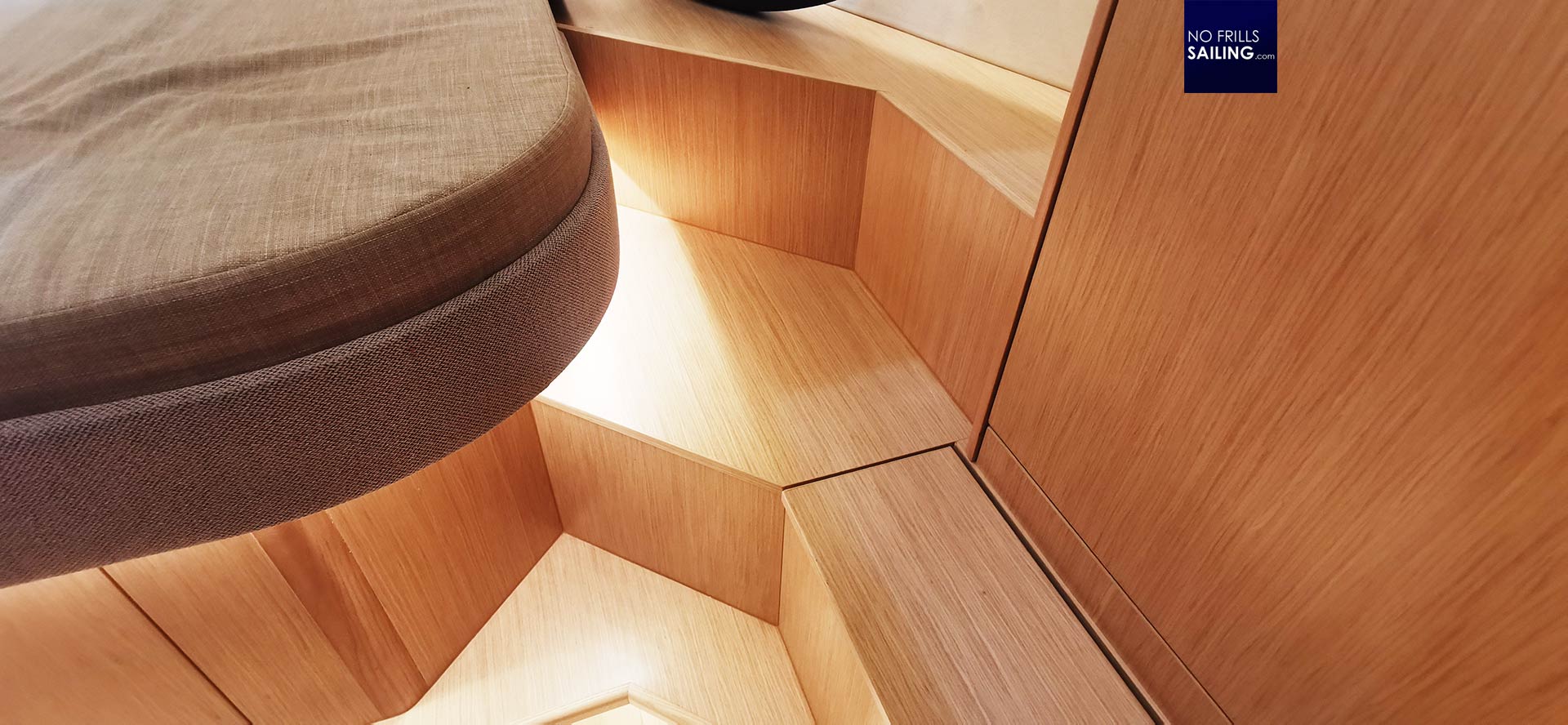
In the end, it´s neither magic nor something special. I´d say that Bavaria utilizes the same machines, techniques and materials like any other shipyard does. Maybe, because of their historical origins, there is a kind of special emphasis on the joinery, much like for example Beneteau taking their pride in seaworthiness and performance of their hulls or Pogo, who build fast boats, not really focusing on interiors. It´s a bit like cars, I think to myself as I drive away, waving Marcus a Goodbye: Each brand has its specialties, its strength and individual touch. Which is a good thing for the customers who – in all the similarities especially for production boats – have a real choice to decide for the one boat that fits their needs and dreams best.
Thanks so much Marcus for the tour and the time taken!
You might as well be interested in these articles:
Walkthrough of the Bavaria C46 cruising yacht
At the Beneteau shipyard
RM Yachts of La Rochelle: How a boat is build from plywood