It was indeed close to this year´s Christmas season as I´ve got the chance to take a visit at Beneteau´s brand new Racing Division near Nantes. It was a premiere for both Beneteau and me as we have been only the second people to be allowed into this new venue of the market leader in production boats: Beneteau may be one of the oldest and most successful brands in the market, but even for a company founded in the year 1884 things are new from time to time. It was early November when I parked my car in front of a nondescript industrial building off Nantes – full of joy and pleasant anticipation.
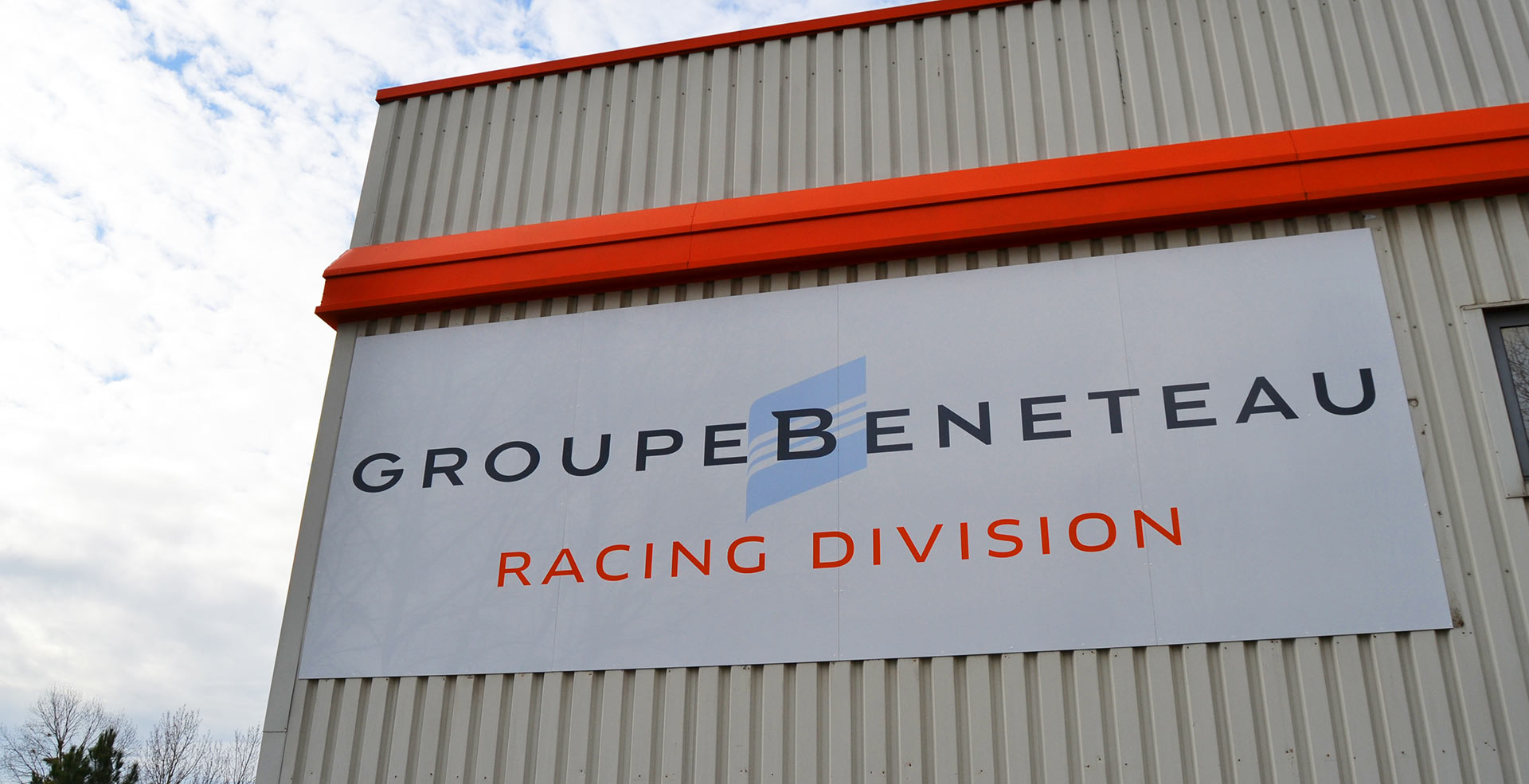
It was nobody less than Gianguido Girotti himself who opened the doors and welcomed us at this holy place: He is not just the General Manager of Beneteau but no less than the mastermind behind the company´s unprecedented reorientation of the whole line of products. Under his supervision more than a dozen new boats entered and will enter the production lines, redefining cruising. And it was thanks to his strive for new horizons that the Figaro 3 project was pushed to the ultimate limits: Creating a new entry level racing yacht with foils. The first ever produced series production boat with foiling technology.
Entering the Holy Halls of Beneteau Racing Division
Gianguido was seemingly interrupting a meeting with his closest staff: “We are designing the future of Beneteau´s sailing yachts in here – and I am talking of projects due in 2020”. This is what they are indeed doing here, defining and anticipating what sailing would be looking like in the coming years. Not just in terms of design and naval architecture, but as well as for the fate of a whole company. He is under pressure to go on with his schedules, but nevertheless is happy – and seemingly proud – to show us around through the whole production process personally. “First I want t show you the beginning of the building process – a GRP-puzzle.”, he says and takes us to a small room.
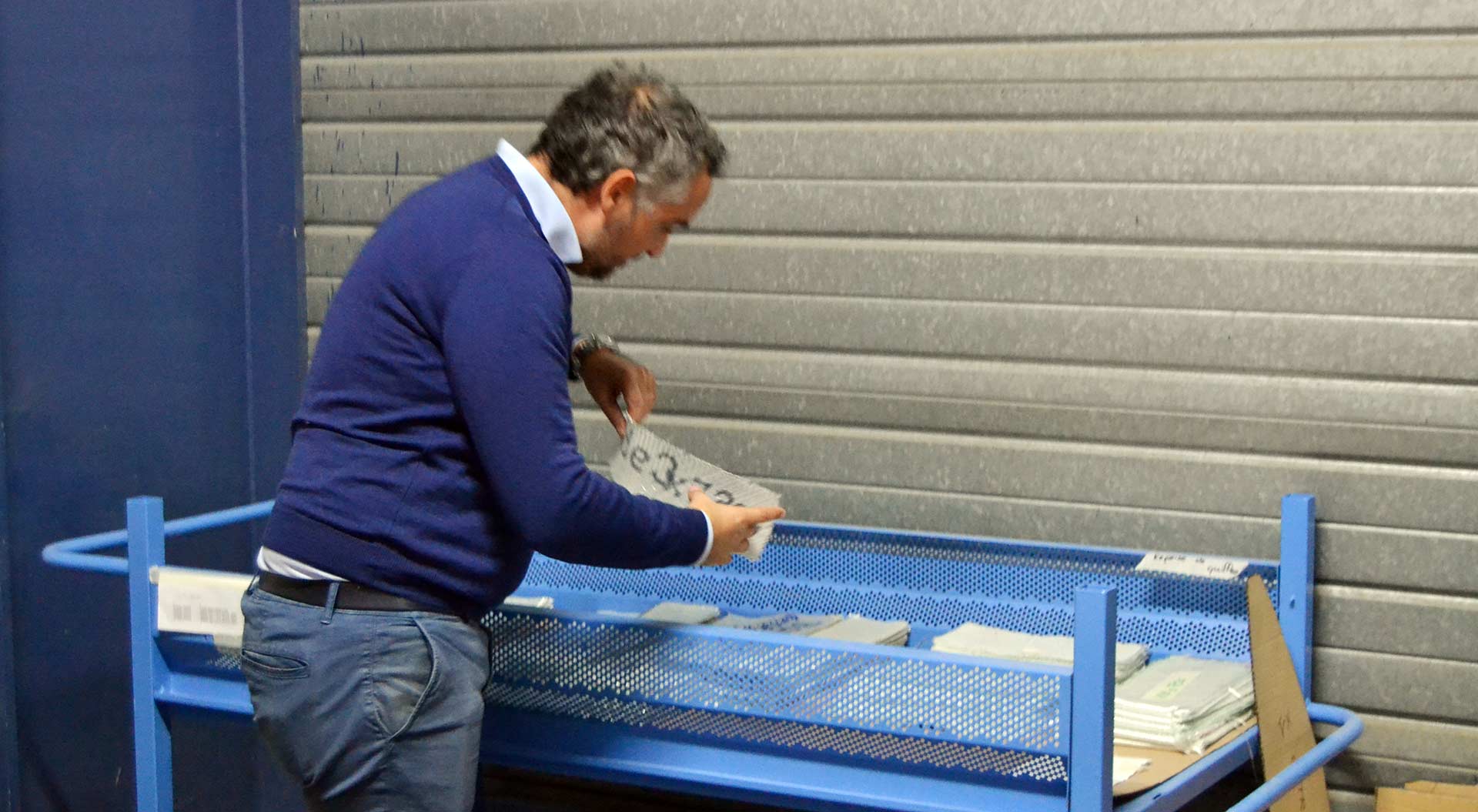
We see a multiple push carts with a couple of shelves. Piled up tiny pieces of silverish twinkling garments: “That´s the GRP matrasses. Laser cut to even the tiniest pieces, as you can see here”, he says and points to a shelf where the weaved raw glassfiber-denim did measure no more than 20 to 30 centimetres. “It is important to understand that in the Figaro 3 everything has it´s place. Everything is thoroughly thought through and you may see it by looking at those tiny bits and pieces”, Gianguido explains. Even the smallest thing has its dedicated and specially designated place aboard the big boat.
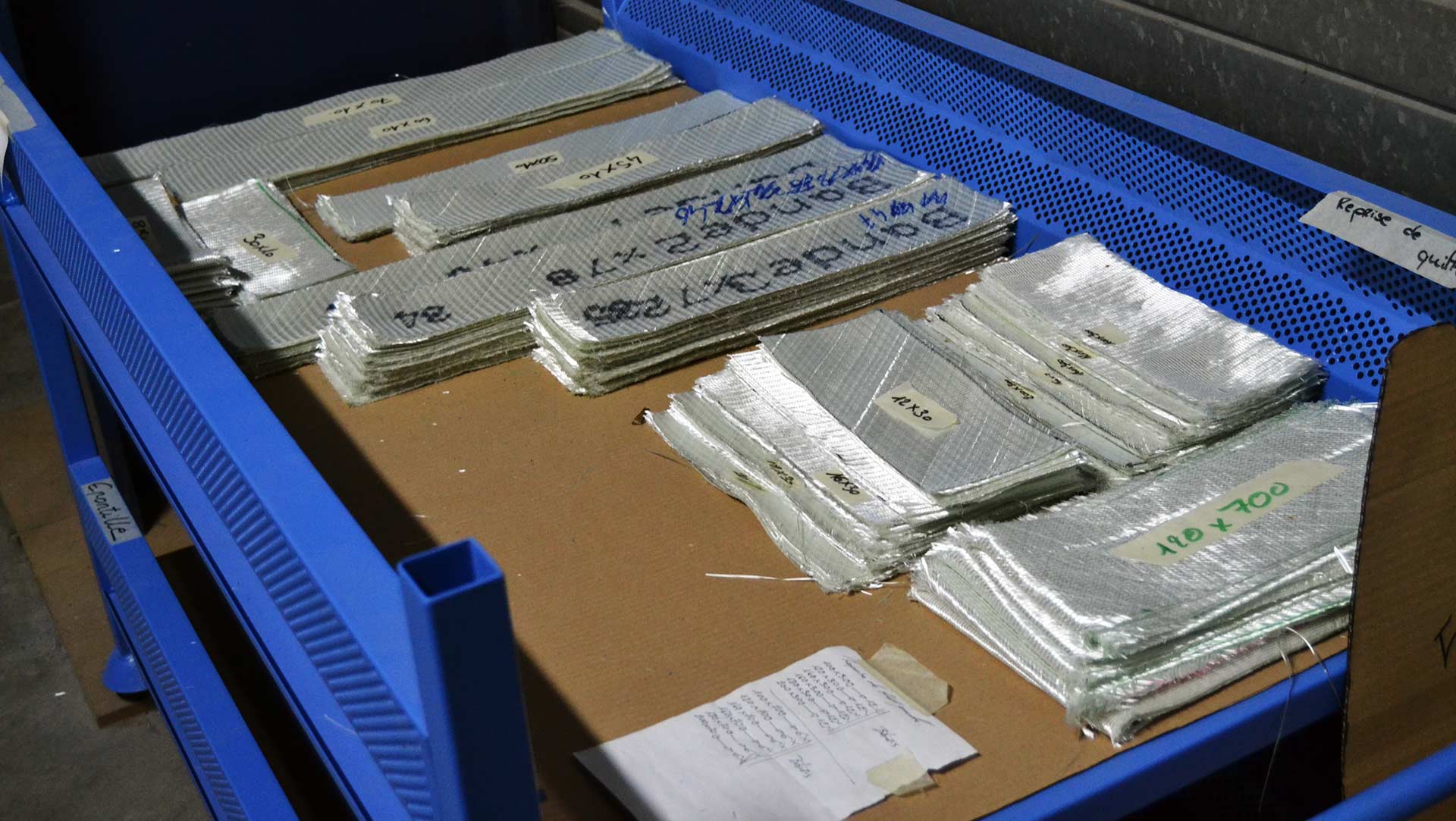
“During the production process, our staff will put each of those garments to a position – placing it exactly where it is needed”, he explains. The garment puzzle will be put together, each one placing to a designated place. The garment itself, by touching it, is sometimes very soft and made of thicker glassfiber-strands, sometimes the weaving is very thin but close-meshed. I can imagine, by looking onto the underside of a deck which is the second production step Gianguido is showing to us, that the meshing degree of the garment is directly defining flexibility, rigidity and therefore the character of a certain area in the construction.
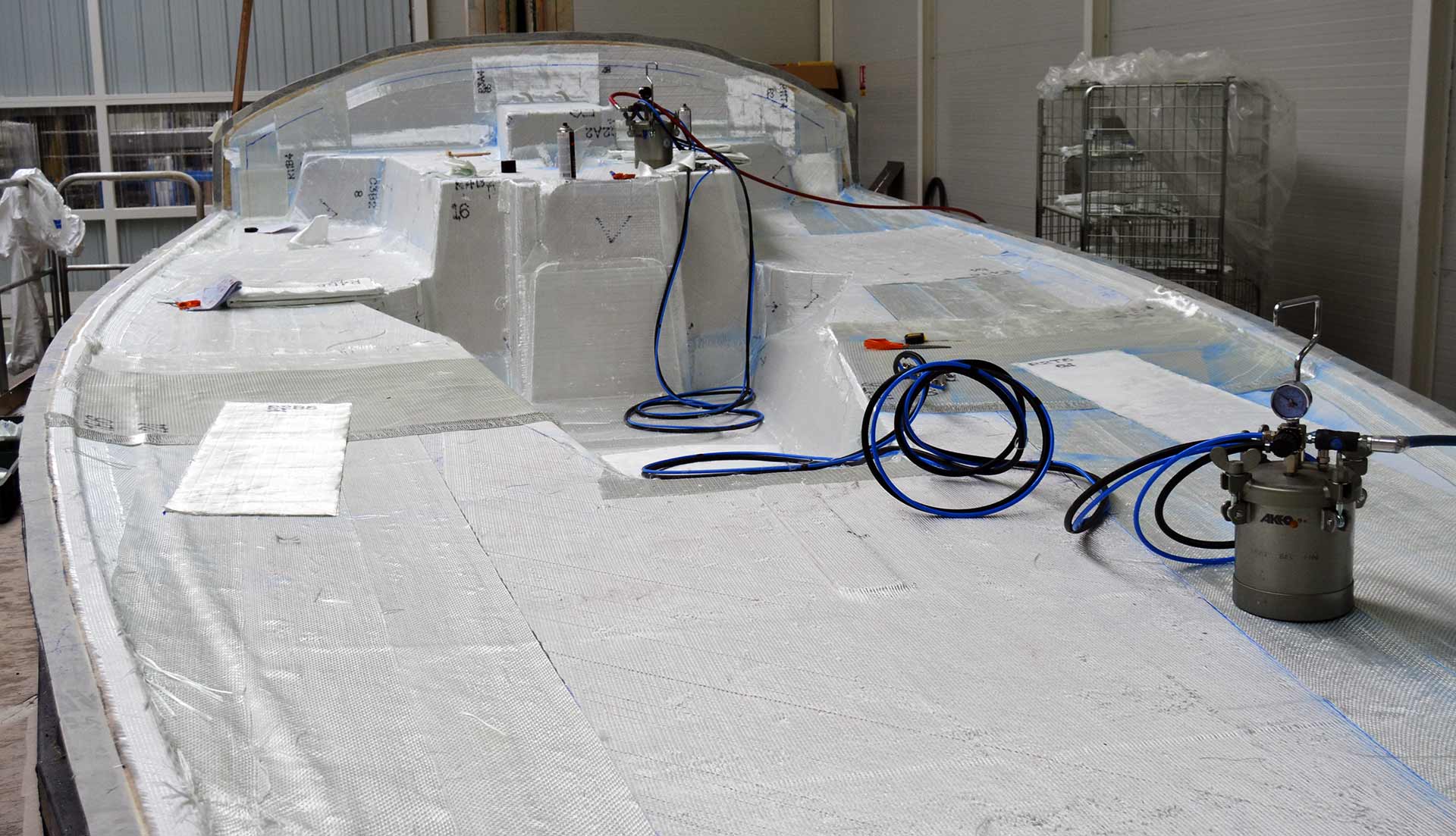
This is achieved in a way, that particularly stressed parts are made especially strong with stronger garments rather than with just more or thicker lamination. “Weight is the key”, Gianguido says: “We want a very lightweight boat to make it as fast as possible. So saving weight by achieving a rigid structure at the same time was the key task in constructing this yacht.” I have seen a lot of yards until now (read here my articles on X-Yachts, Luffe or RM-Yachts) but I have never been looking at making a boat light and stiff by actually puzzling it together.

“You won´t see all the efforts that go into the boat in the end. Like with this deck”, Gianguido says, “but we are sure that this is the only way to come up with a high-tech boat that is worth the name of Figaro.” As a former artist painter, I know perfectly well, what he means: Making a thing by adding stuff (like with painting a picture) is one thing. But making a perfect thing by taking stuff away like in sculpting is a completely different task. And the Figaro 3 – this is what I´ve learned – is like a sculpture the product of a deliberate reduction of the unnecessary to achieve the lightest, but strongest, possible outcome.
Making a strong, reliable, stiff – yet affordable Racing Machine
We proceed to the next production step: The making of the hull. Again, by looking at the actual moulds, it all seemed quite normal. Lamination of GRP-matrasses is a near 60 years old process which hadn´t undergone too many changes. The garments may have been modernized as well as the quality and properties of the resin, but in the end it is hardened resin-soaked glassfibers. But – again – I learned that with Figaro 3 production, there is more to it indeed.
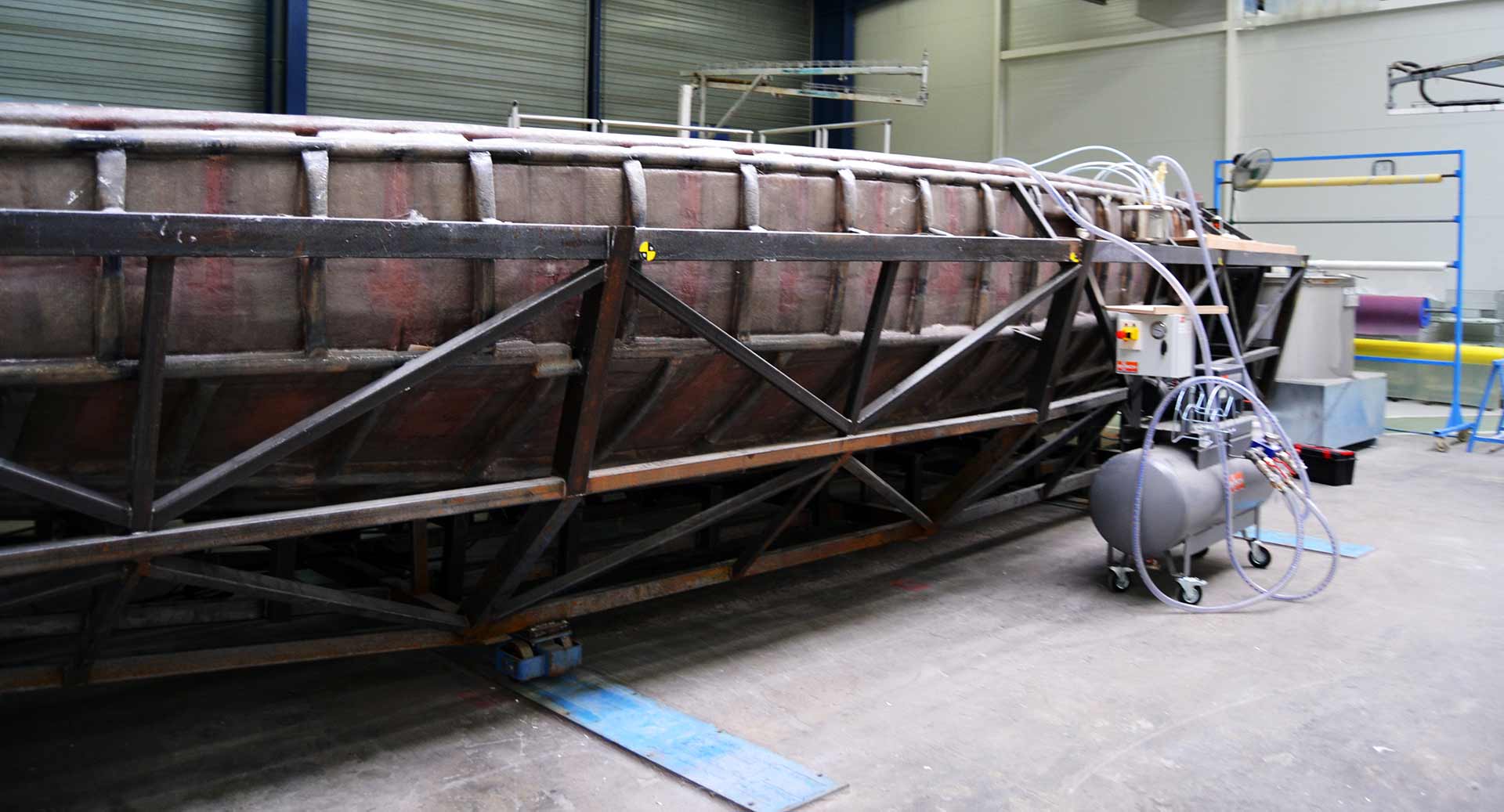
“First you must understand that we spend a fortune to create this environment here”, Gianguido explains: We have merely a chilly 5 degrees Celsius outside and we were freezing the first 10 minutes in our car driving out here, but now I can open up my jacket and take off my hat as in fact the temperatures are well in my comfort zone: “The climate in this halls is manipulated in a way that we have the exact perfect temperatures for the GRP and resin to harden.” I notice that there is zero smell as well in here. There is a big mould in one of the edges of the hall, a kind of oversize cart with a jig. Another unfinished hull is placed on top of it. By inspecting the hulls I can actually feel the first layer of Gelcoat and the hard layers of GRP. Then there is an inch thick layer of hardened foam: “We do not use Balsa as the core material for the Figaro 3”, Gianguido explains: “The sandwich material of choice for this yacht is foam. Again to make sure that we always get the lightest and strongest possible outcome in the end.”
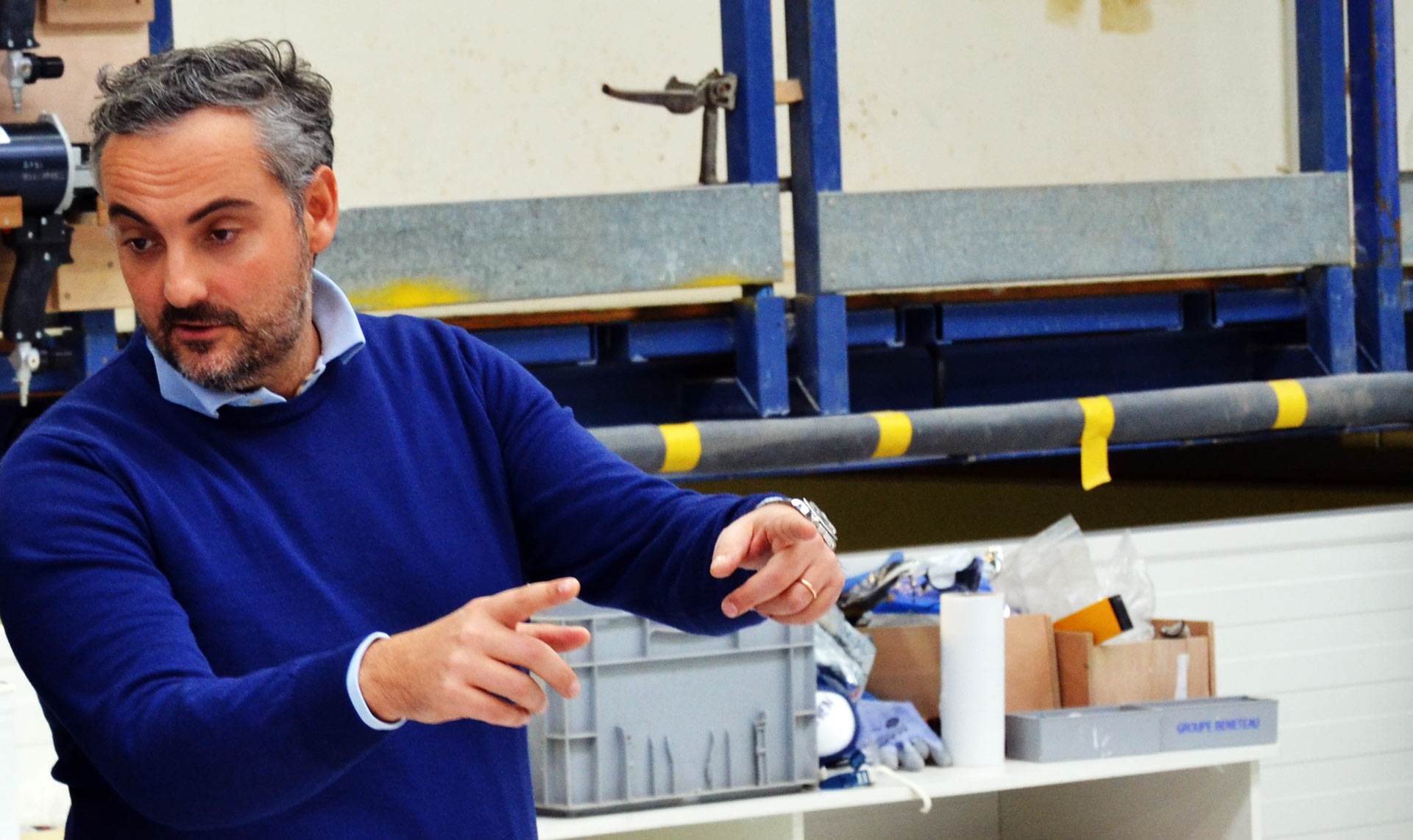
But there is more to it: “The Figaro 3 is not a boat that has to stick to a box rule, like it is the case with Class 40 racing yachts. The Figaro class itself calls for exactly the same boats. So as the supplier of this boats we have to make sure that each and every boat is made exactly alike the others. The boats have to be identical twins. And we must achieve this throughout the whole production life of the boat – for many years to come. You can imagine the effort that went into choosing the right production methods and materials to achieve that goal.”
Vacuum Infusion is the Technique of Choice
One of the measures to achieve that goal is the consistent use of latest vacuum infusion technology in the production process of the Figaro 3. The Figaro 2 was built in sandwich technique as well but utilized Balsa as the principal material for the core. Balsa may be a perfectly suited material but it has several downsides which made the team around Eric Ingouf of Beneteau and VPLP Design switch to foam. I know very well what it means to have Balsa wood soaked with water. On the other hand, Balsa is a natural material and thus one cannot guarantee a 100 per cent product similarity from boat to boat.

We take a halt in front of a hull in the making. “Of course this is a vacuum infusion technology for the hull as well”, Gianguido explains. On top of the multiple layers of glass fiber garments and foam for the sandwich core thicker strings of foam are placed – these will, when hardened, form the longitudinal stringers of the boat adding strength to the whole construction. The thick blue membrane forms an absolutely airtight coat all around the hull. Then a pump constantly evacuates air whilst a dozen or so rubber tubes as thick as a men´s finger inject the resin.
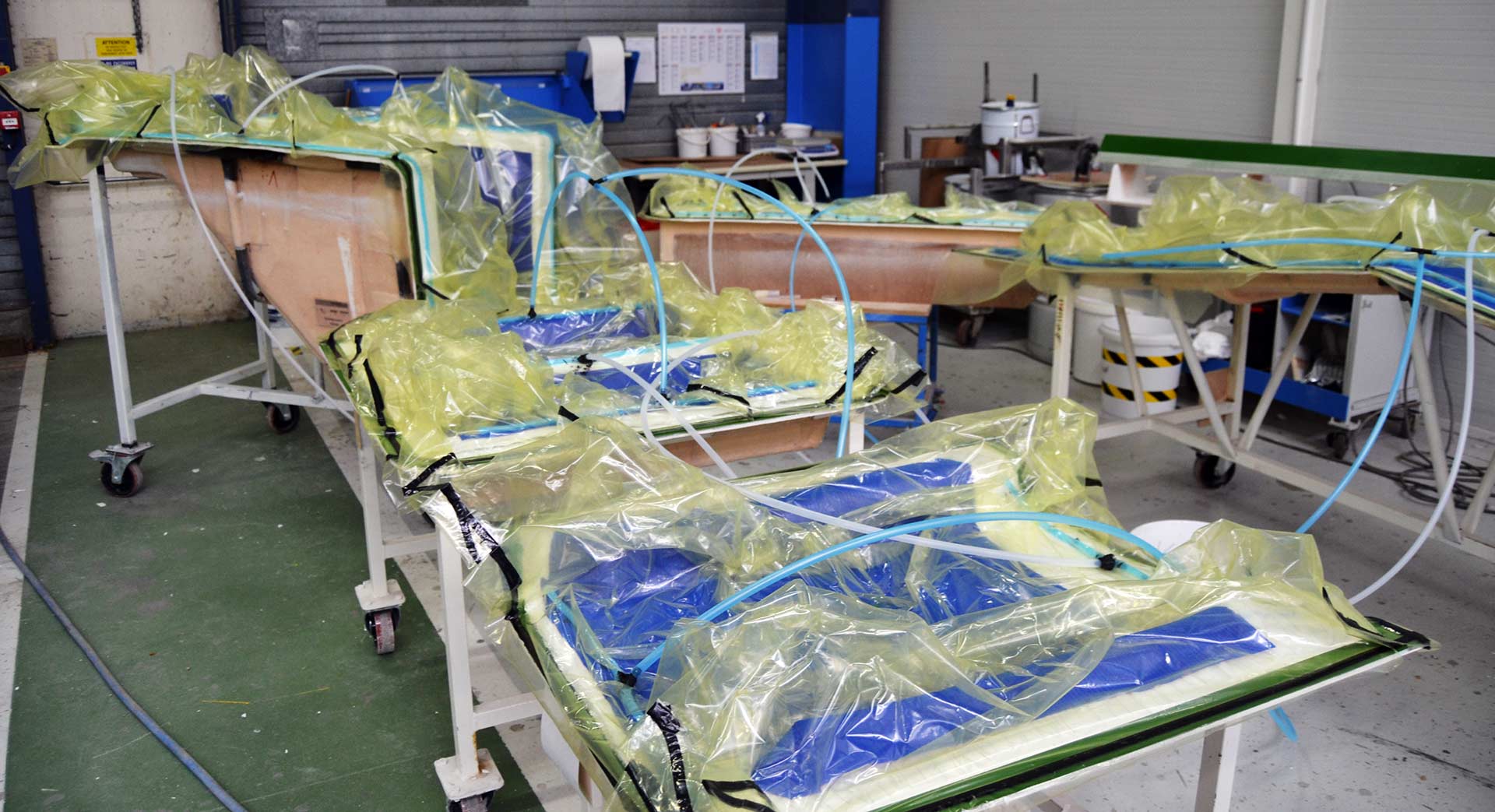
“The vacuum sucks the resin into every little corner of the hull. It will penetrate through the garment layers, soak the foam and finally creep into the last edge of the hull.”, Gianguido explains: “This will in the end harden over time – and will form the stiffest bond you can imagine.” But it does not stop with the hull, the hull is just the beginning: “We are vacuum infusing every single GRP part of the boat.” And indeed, next to hull and deck, the bulkheads and all the smaller parts are produced by utilizing this technology. The fact that the vacuum infusion method doesn´t produce any odours is one rather pleasant side effect – Gianguido further explains that only this method ensures that each single boat is 100 per cent the same as all the other ones: “Remember, we are talking of a one-class boat-design and we have to make sure that every sailor gets a boat equal to the ones his competitors are sailing – just in this way we can provide for the equality of opportunity in the Figaro racing class.”
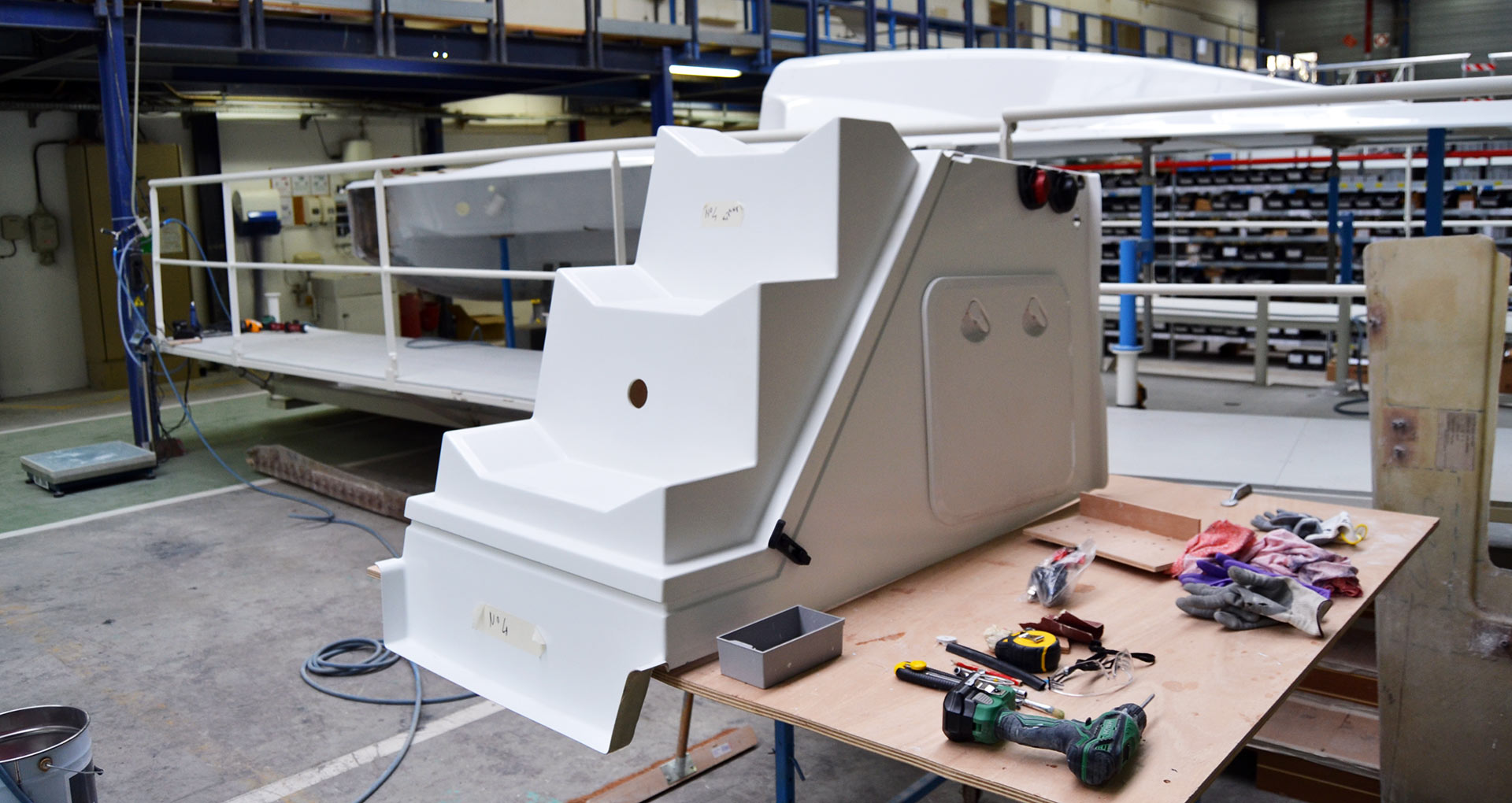
Next stop is a mounting station where the engine compartment is completely fitted. The casing for the engine with all supporting stuff is fitted with the entryway staircase, access hatches to the engine and all fittings needed. Then the whole section will be lowered onto the engine already mounted to the hull. “We tried to improve boat building in every single step of the production process”, Gianguido says: “Even this small thing makes a difference in the end.”
Series Production of Classe Figaro Racing Yachts
Did I say we where lucky? “You are one of very few people to this day to be allowed to enter this hall and even to take pictures. As I remember, you are the first non-French people to see our racing yacht division.” And lucky we are indeed as we enter the big assembly hall. But before I can fully appreciate the three first ever series production Figaro 3 boats, Gianguido points to a deck in the making: “Building a one-design racing yacht is tedious. It even applies to every single bore hole we make.”, sticking his finger into one drilled hole.
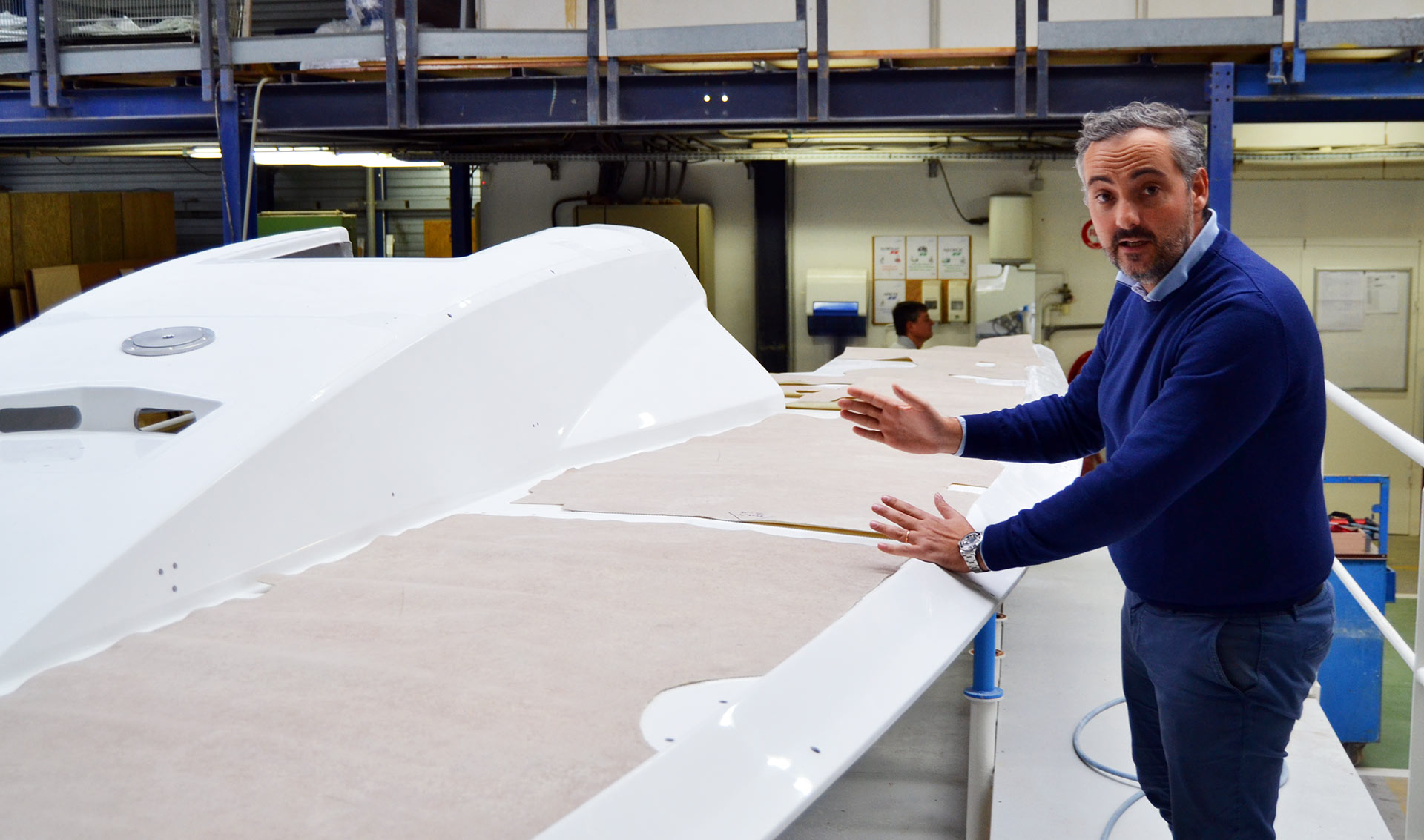
We use patterns and jigs to achieve the needed accuracy. By utilizing the very same jig – for example in placing bore holes – we make sure that the very hole has always the very exact same position in every single boat throughout the hole production life of many years.” Although we saw no Beneteau worker at all during our visit, the building of a Figaro 3 is far from being automated: It is still a man made product mostly done by hand, no matter if vacuum infused or not.
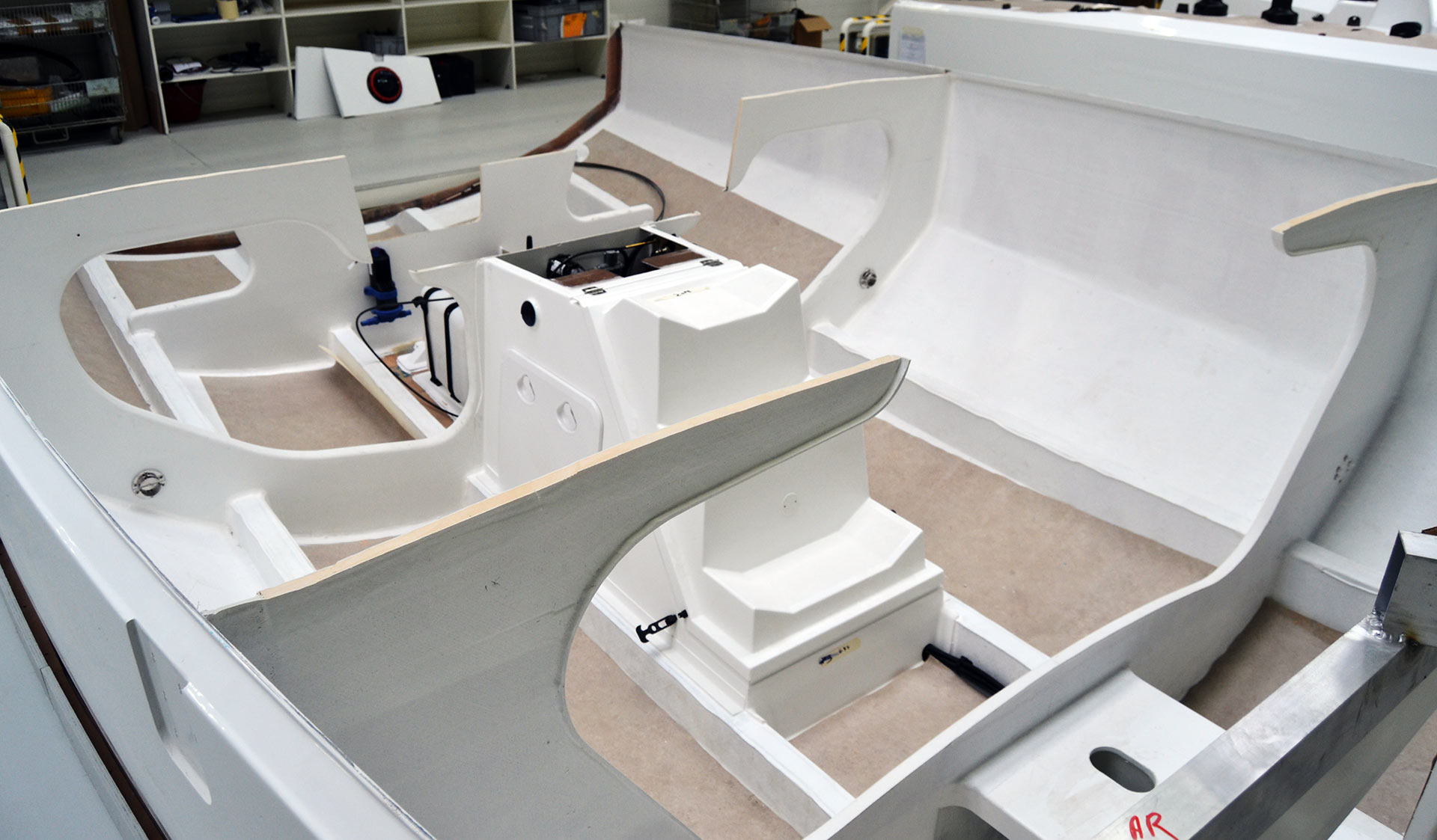
Then we entered the heart of the complex, the assembly line where three hulls had been piled up next to each other: “These are hull numbers one to three, the first ever produced series Figaro 3 yachts”, Gianguido says. I set foot into hull #3 which had no deck yet and took a closer look onto the bulkhead arrangement: There are a handful of them and what struck me instantly was the fact that these bulkheads aren´t closed on their upper sides: Surely a weight saving measure and most surely this won´t have any effect on stability.
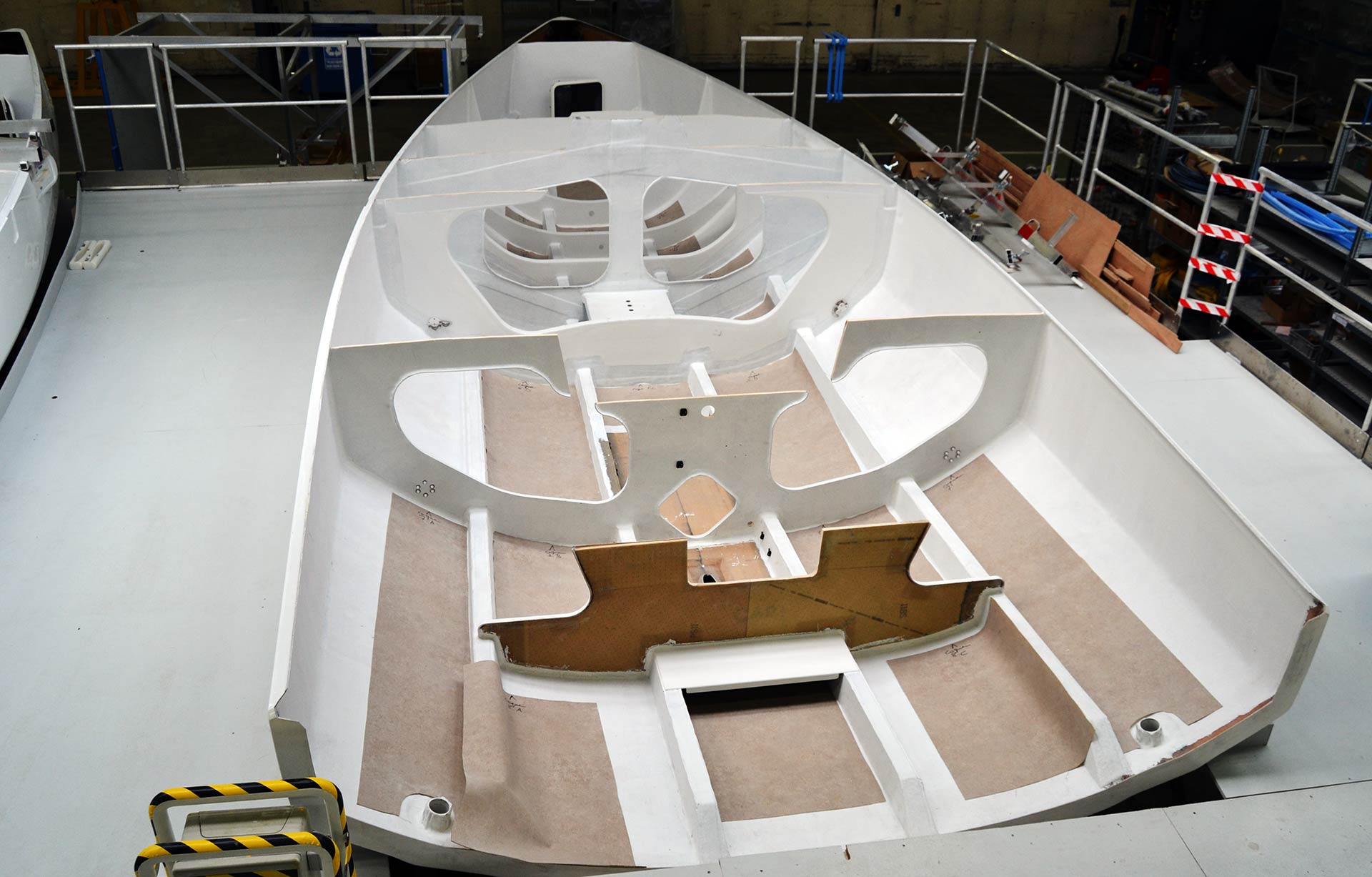
There are three bulkheads in the front section of the boat where the mechanism for the foils and the foils themselves will be housed. I can imagine that a lot of structural integrity of the hull is needed in this section as here in the midst of the boat both loads from the shrouds, the keel and additionally from the foils will enter the structure – no wobbling wanted nor any room for failure can be left here.
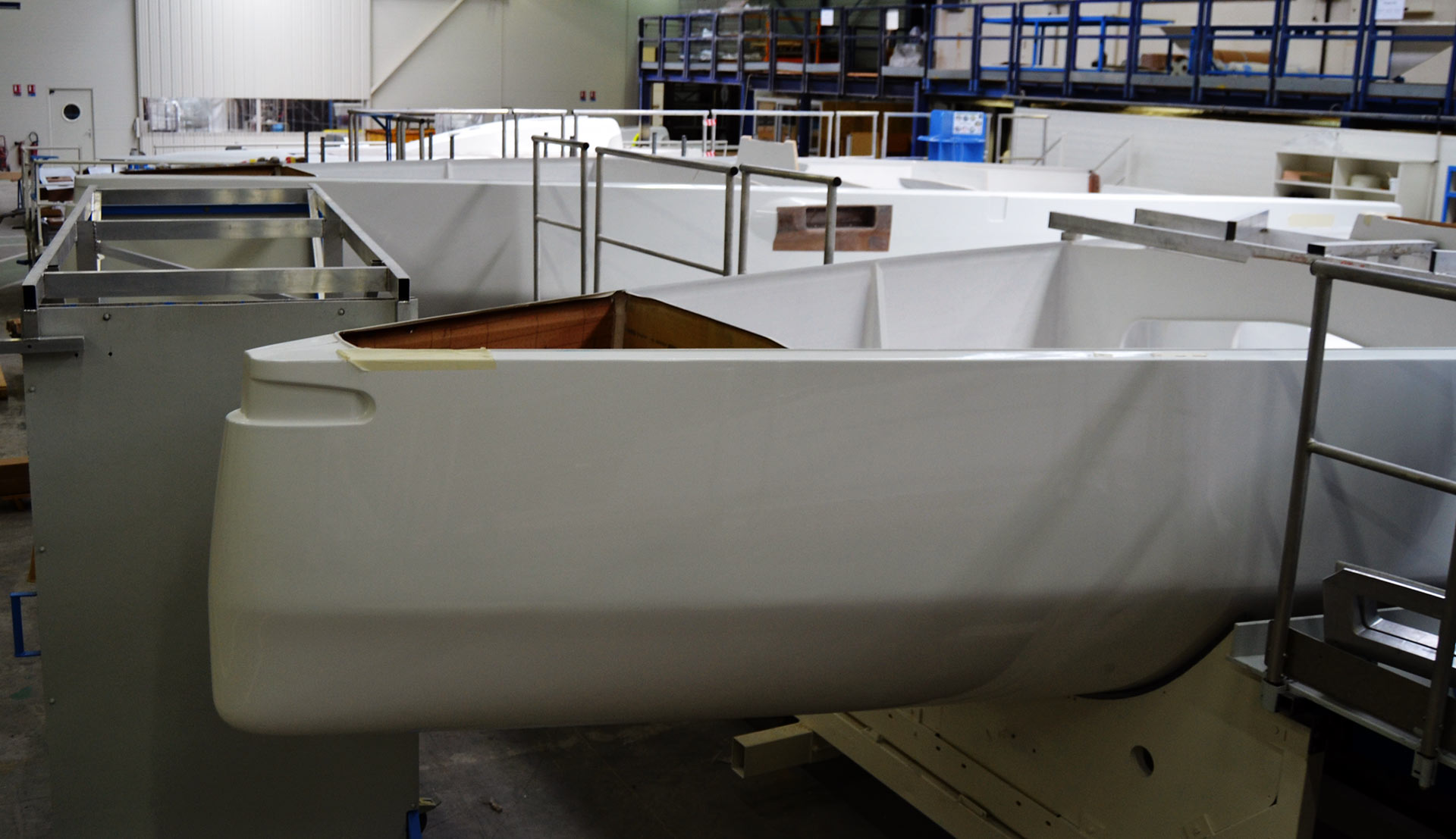
The bow is interesting as well: Judging from the renderings, it seemed that the Figaro 3 will be fitted with a razor-sharp bow but that turns out to be false. Instead, it´s a very rounded, full-bodied almost scow-like bow with chines starting right at the first metre of the waterline of the yacht. There´s a watertight collision bulkhead laminated to the hull and I could assure myself that the reception of the bowsprit was made especially thick and therefore very well capable of taking on the loads of a Gennaker in full speed.
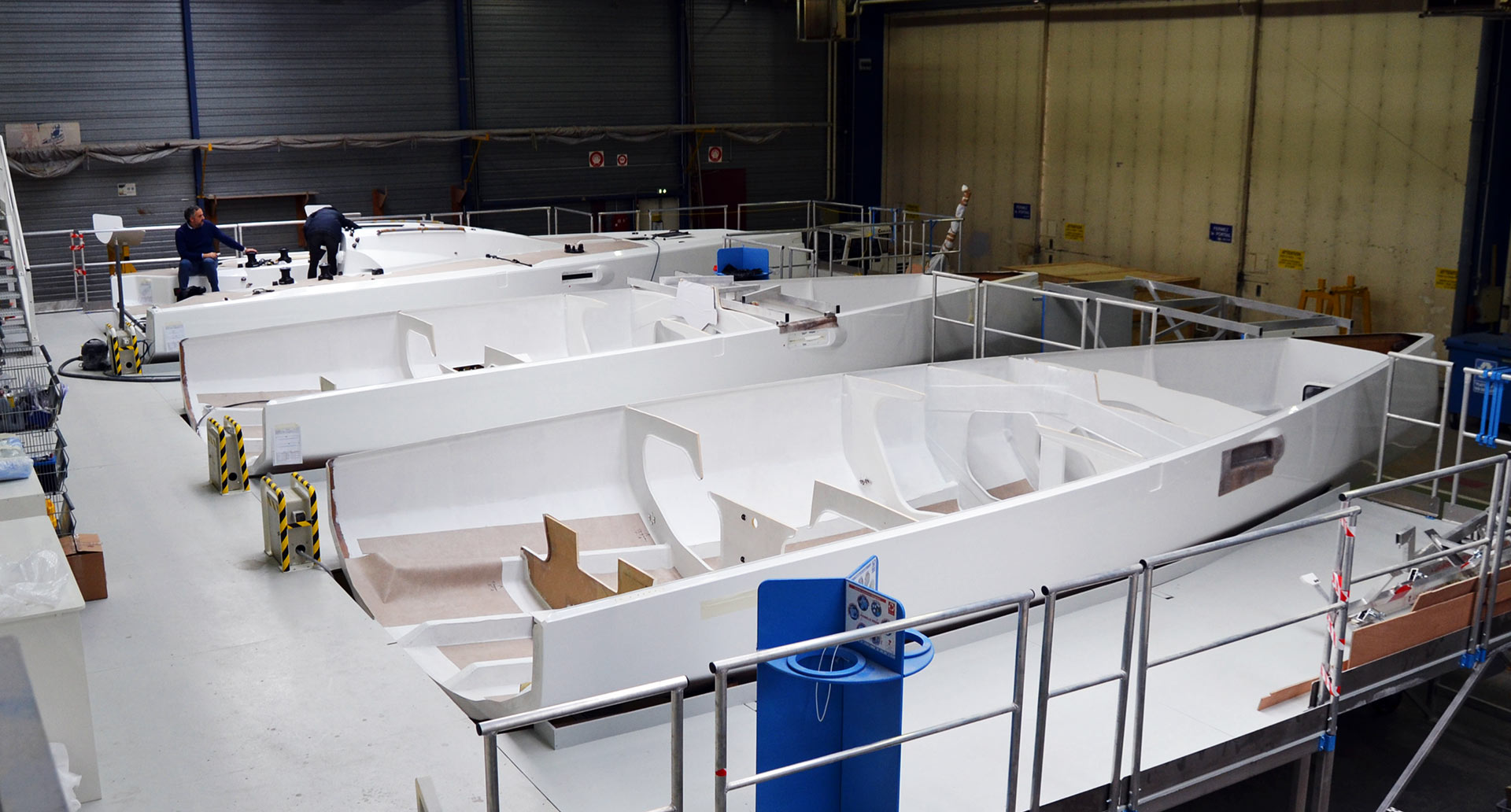
Two of the hulls didn´t received their deck sections yet, one already did. Going from hull to hull it was easy to spot the differences in the progress of the build and this helped to get a feel for the way they do work here. “You see, this racing division isn´t just another part of Beneteau”, Gianguido explains: “It´s like in Formula 1: We try out new production methods, maybe new materials. We strive for saving weight and making fast boats – and finally, the experience we gain here will enter the cruiser production and will influence the way we are making the Oceanis yachts, the Sense yachts and other boats of Beneteau´s product line.” Lucky we were indeed, because …
Meeting Vincent Lauriot-Prevost of VPLP Design
… suddenly Gianguido waves and welcomes another person to our little tour of the production: Vincent Lauriot-Prevost, the principal naval architect of the Figaro 3 briefly joins the tour and welcomes us to this facility: When Marc Lombard is the father of the racing predecessors Figaro 1 and 2, Vincent is the father of the current yacht.
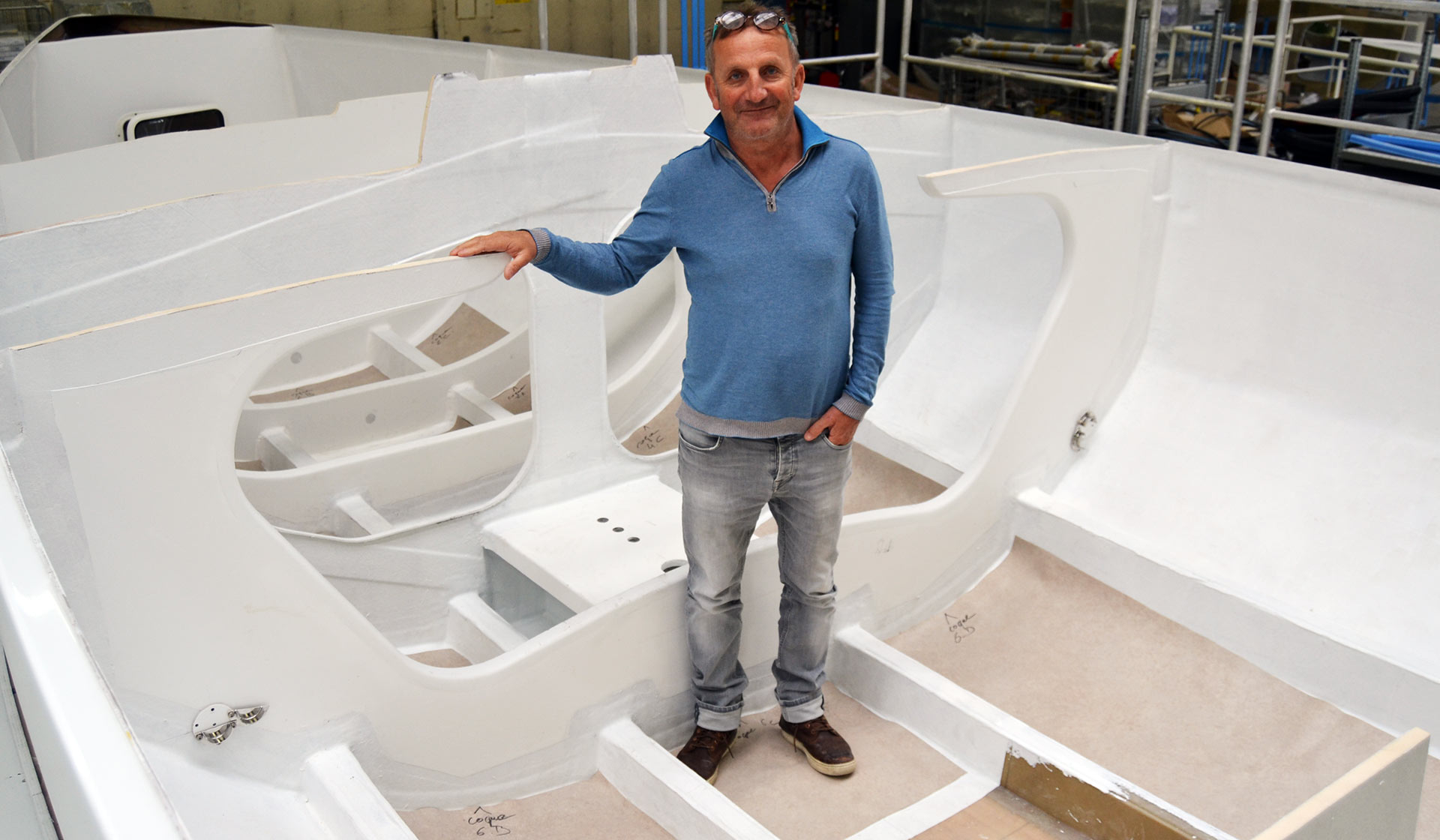
We take some minutes on hull #1 which already got her deck and most of the deck fittings to sit down. Gianguido – although in a hurry because a room full of team members was waiting to resume the meeting – took his time to explain the idea behind the Figaro 3 and why this yacht was so important for both Beneteau and a whole generation of French yachtsmen: “You see, 9 of 10 Vendeé Globe winners are Figaro-sailors. This is the school for pro sailing of France and it is so important to us.” It was more than a product, we understood.
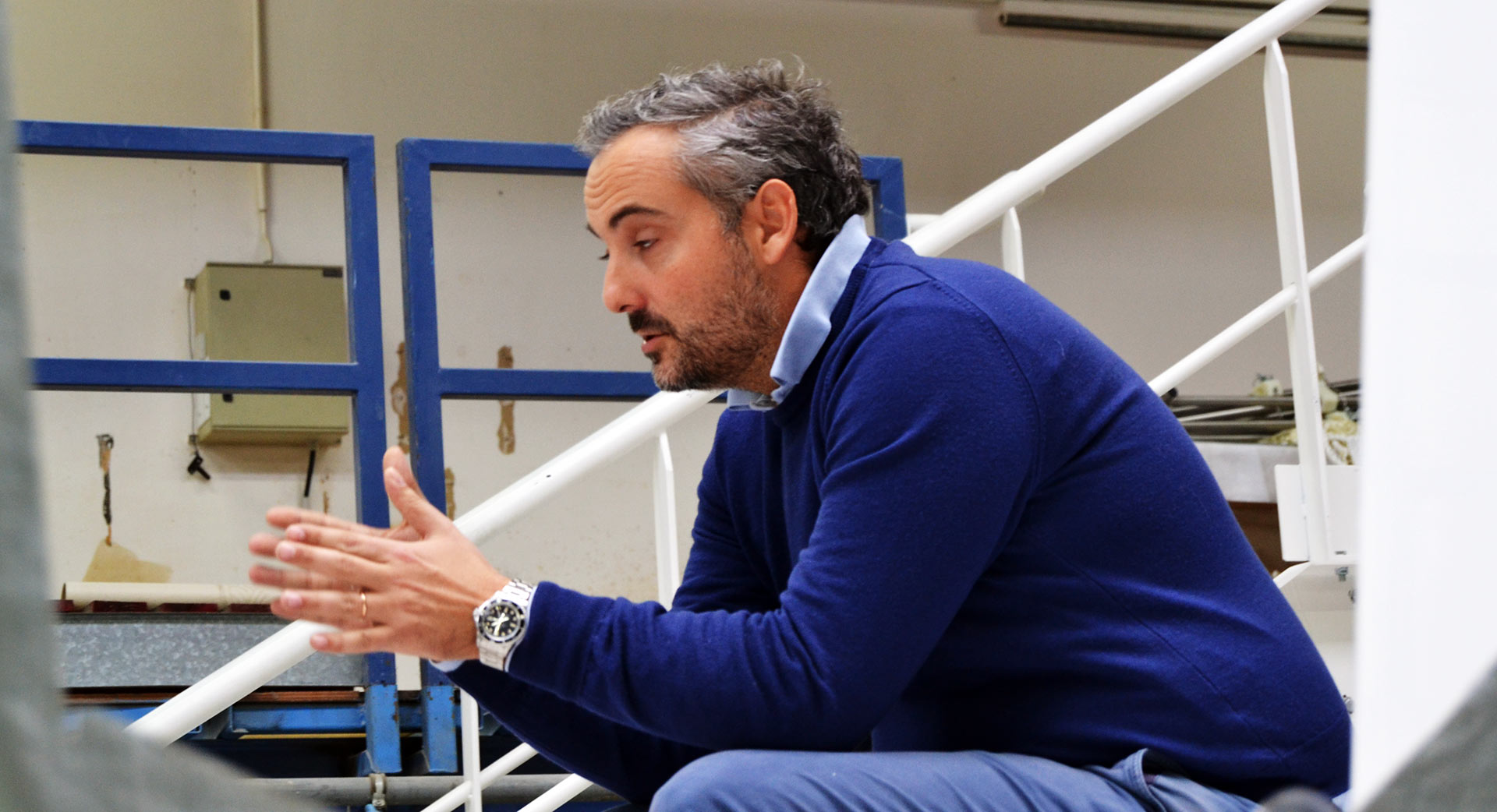
Gianguido may be Italian but his arguments and thoughts had been truly compelling and understandable. He explained every corner of the boat, the steering position, the aspect of single- and double-handed sailing and the fun, the strain and the challenge that this yacht is impersonating. And the more he was talking, the more I felt the need in myself to again set out again and hoist sails. On a Figaro like this?
Imagine to sailing this Speedmachine
I must admit it is a compelling sensation to be standing on a pure racer like this. It is even more radical in every aspect that the Pogo 40 yacht, I love so much sailing (read it here and here). But the more I tried to imagine this boat finished and readily rigged, the more respect and awe mixed with my enthusiasm. That´s a hell lot of canvas for a 32 feet yacht! And a lot, lot more speed potential than in the First 30 R I was sailing recently (read it here and here).
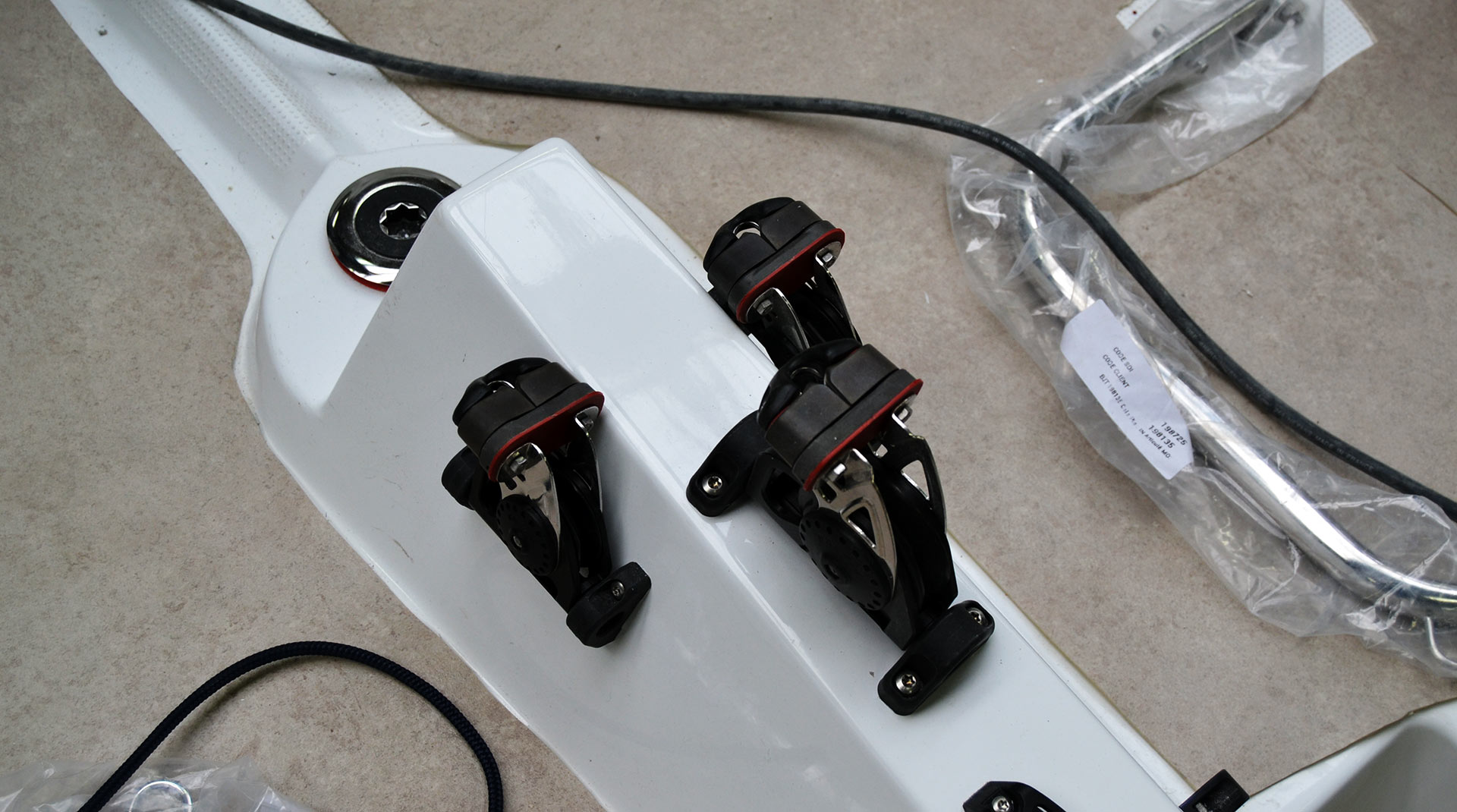
The huge mainsheet traveller right at the end of the yacht implied that a solid Figaro-sailor should be a fine trimmer. The mainsheet controls are made of no less than three clamps: “It´s a big dinghy, if you want.” No steering wheel of course, but a big solid steel framed tiller (not mounted yet). The seating position is just a thin rubber-like pad, possible a tuning element for each Figaro sailor in the future. I noticed a lot more clamps on the cabin roof to either side of the entryway down below deck.
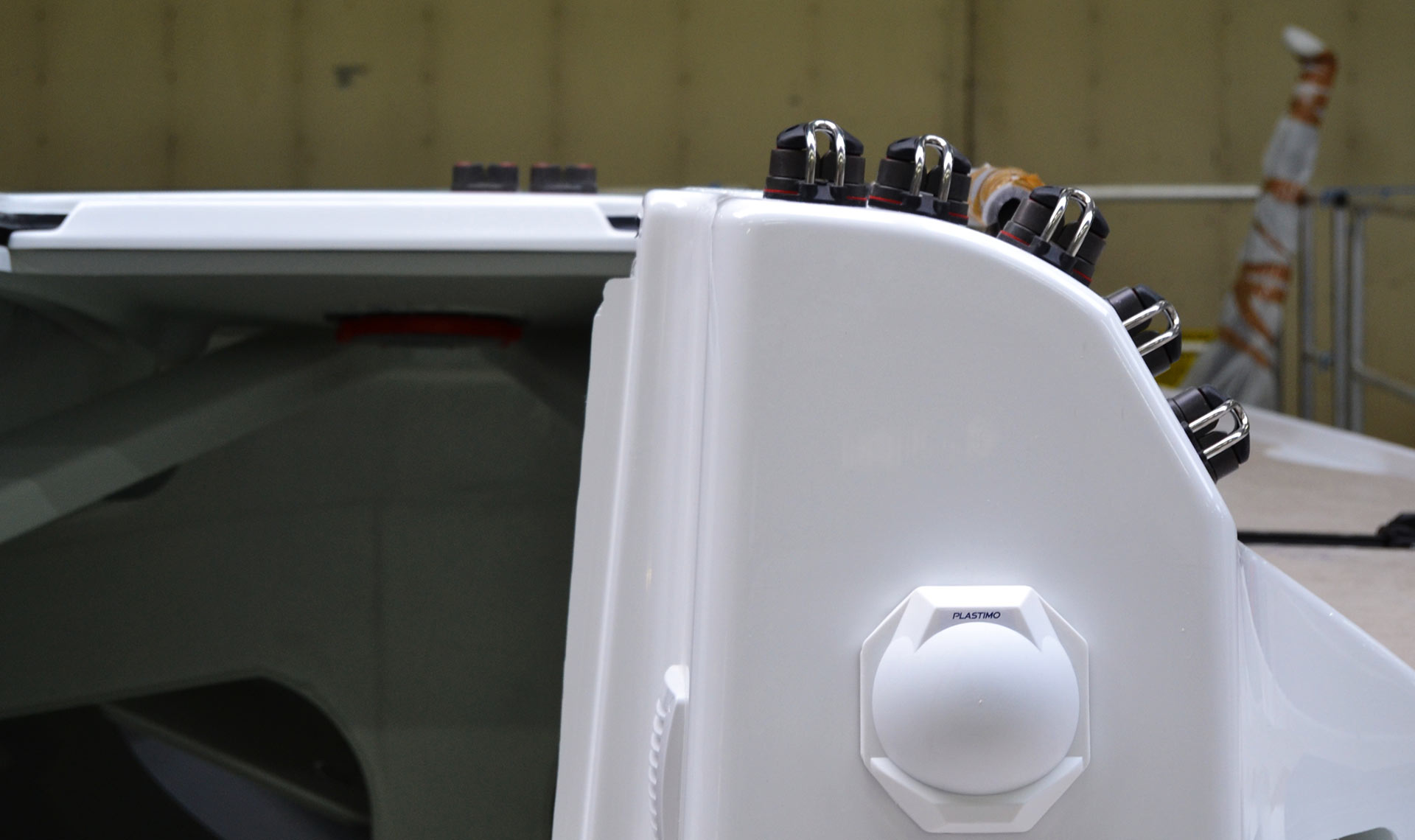
Five clamps for halyards, sheets, outhauls and other lines, two or three more on the roof front. Not the comfortable clamps we got used to on our cruisers, but the “action” hands-on variant – another evidence of the speedy racing this yacht is made for. The whole layout of the cockpit is not really made with safety-related issues in mind for sure: There are several points to get a lifeline locked onto, also some footrests but the whole thing appears very flat, very low, very open. Surely, not a yacht for rookies.
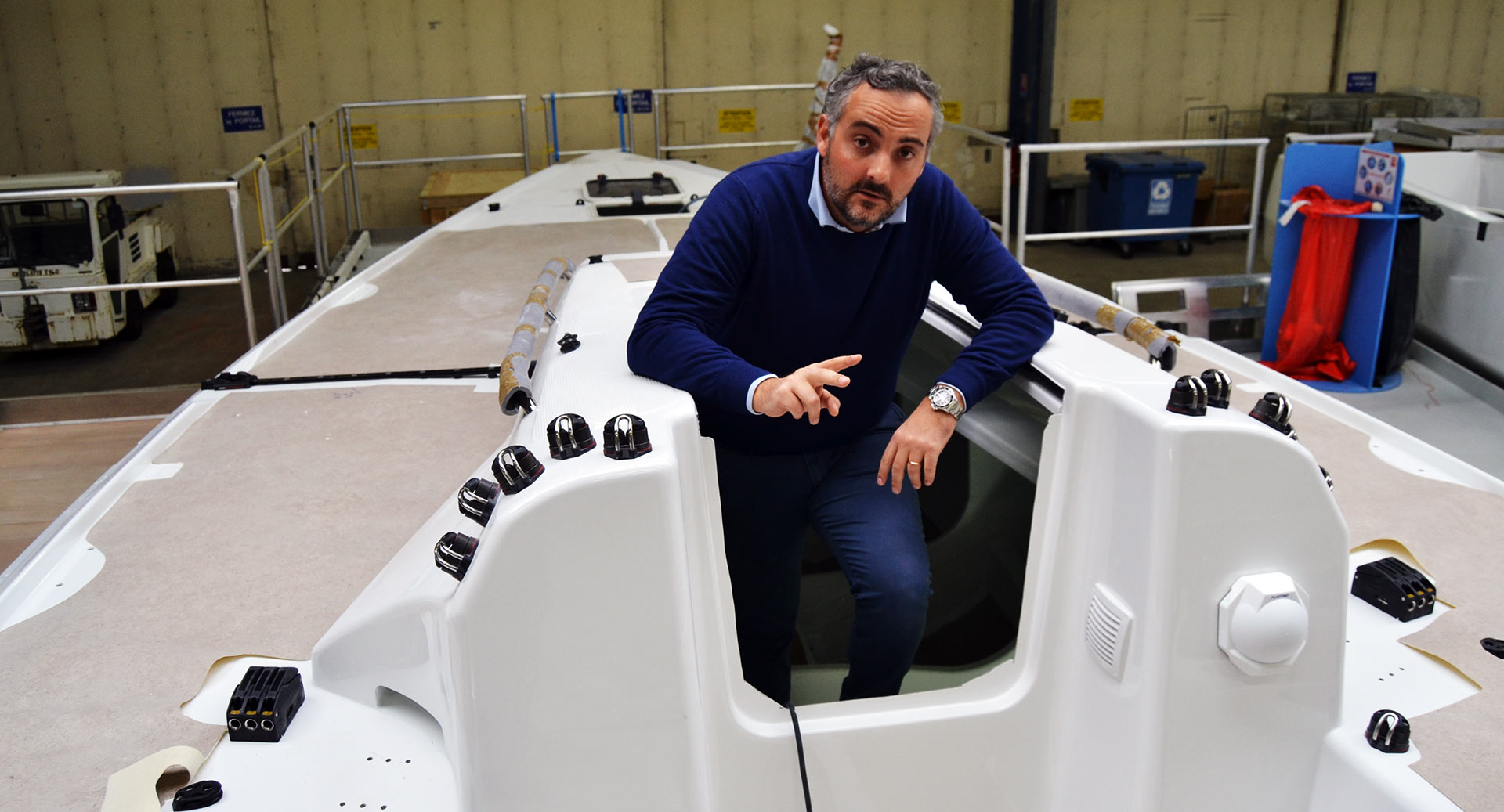
The inside – although I knew that there wasn´t really much to be seen down here – was one of the highlights of the whole tour. Gianguido explained that there won´t we any “nice” things to be found inside: No wood, no panels, no veneers. Just the bare white GRP hull with all structural elements exposed. A navigation station right in front of the entryway and a small folding bunk at the starboard side – that´s all. “The boat won´t have anything fitted inside.”, Gianguido Girotti says: “It´s up to the very sailor to individualize his boat to satisfy the personal needs.” If you want to go fast – let it be as it is, I thought.
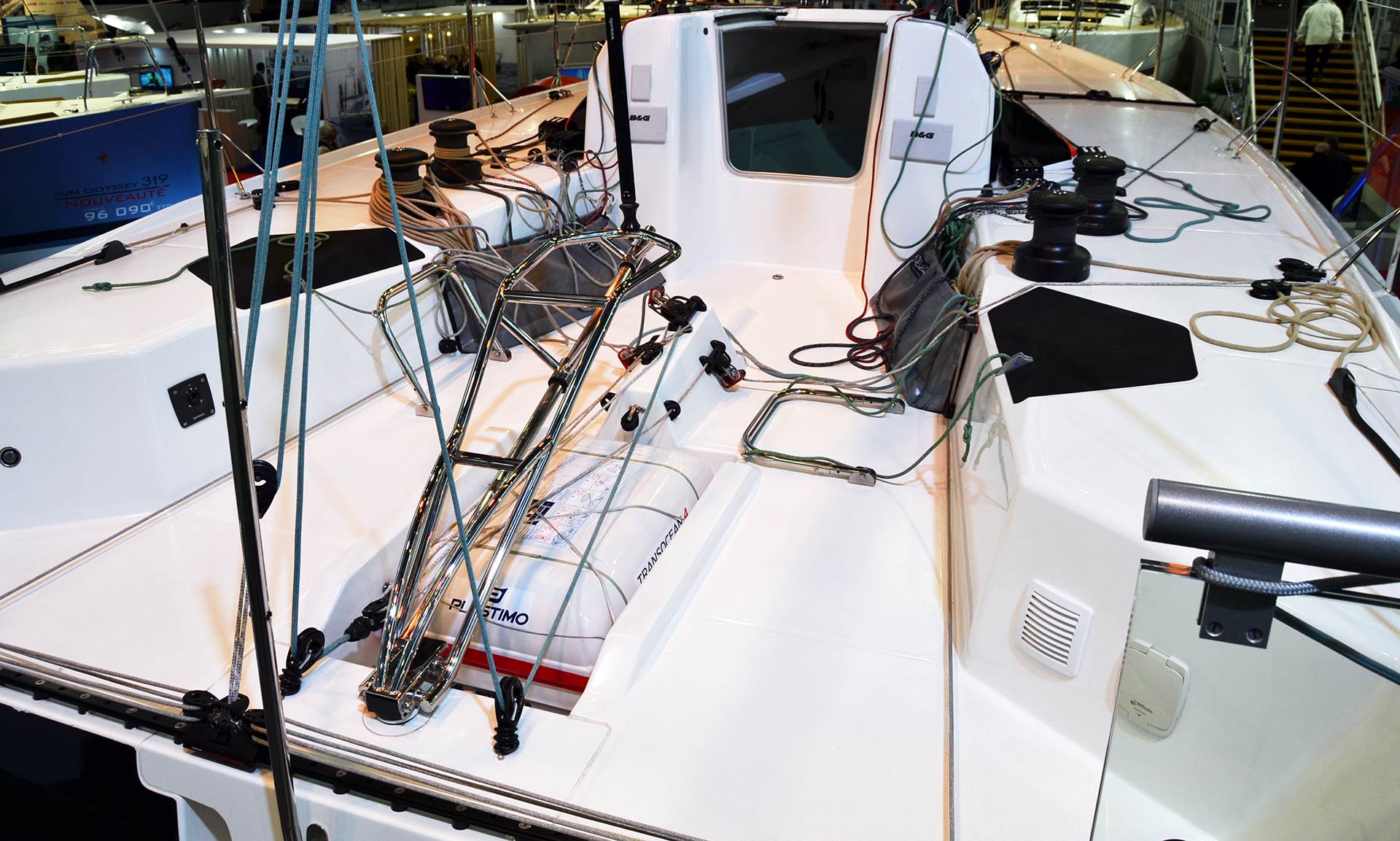
Two days later, on my way back from the Atlantic coast, I made a two-day visit to Salon Nautique, the Paris boat show (which you may read in this article) to take a look onto the Figaro 3 prototype which was on display here. I instantly felt at home in the boat although it was a bit of a shock to see the boat fully rigged with a multitude of lines running all around and across through the cockpit: Imagine this mess in a Force 9 wind at night …
Inspecting the Figaro 3-Prototype during Paris Boat Show
Seeing the finished Figaro 3 in reality was a real blow to my mind! The boat is absolutely gorgeous and amazing to look at from every angle. It´s nonetheless partially owed to the perfect colourscheme and design of the yacht, but the appearance was mind blowing: The full bow, nevertheless appearing aggressive, the short but sharp bowsprit, the very, very long twin rudder blades and the almost skinny and vulnerable appearing needle-thin keel with the short teardrop-like lead bulb.
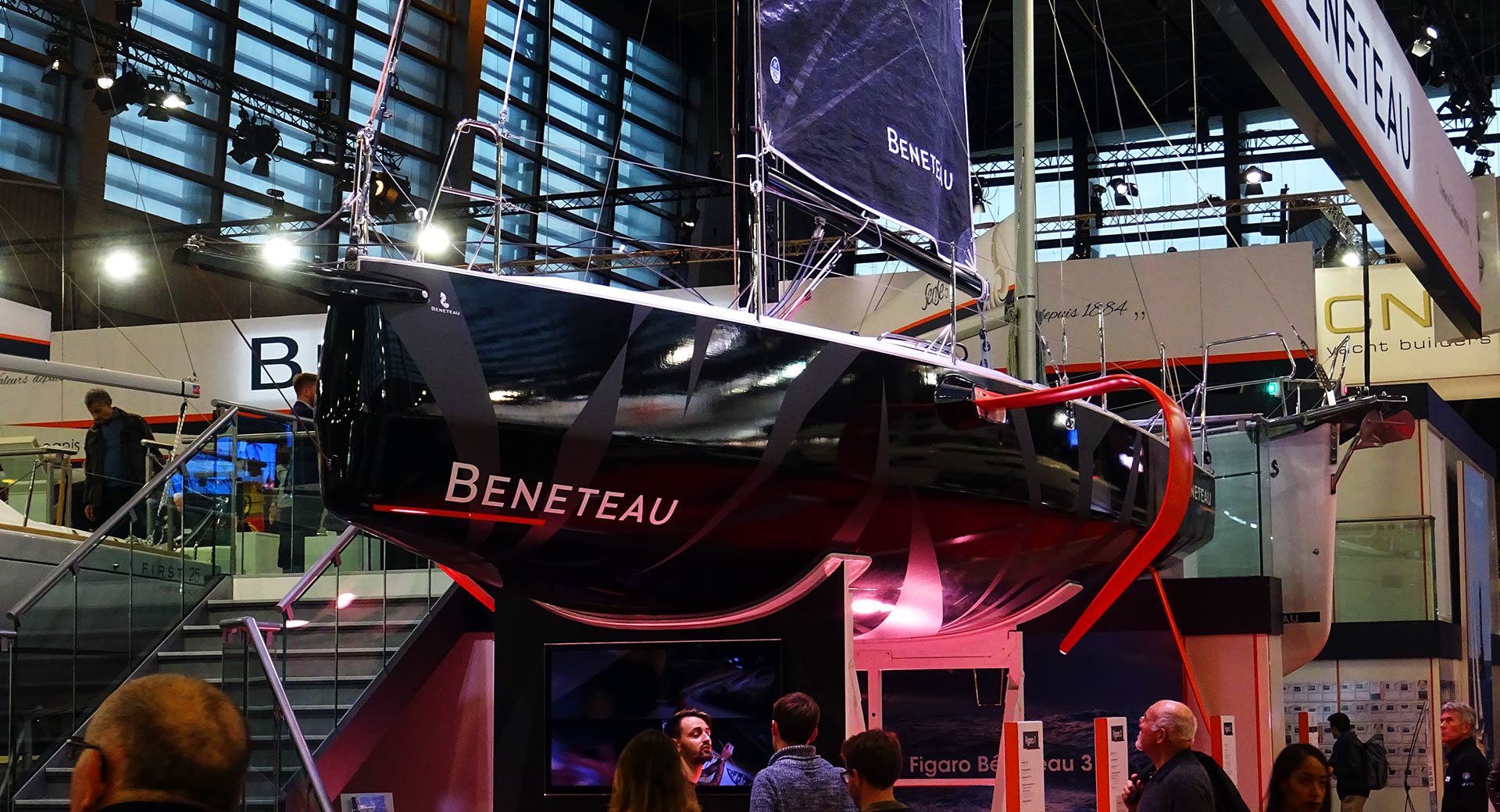
The inside of the boat was – to be honest – shocking. I knew, last told by Gianguido, that there wasn´t much to be expected, but to see it in reality was a blow: There really ISN´T anything at all. The “berth” is a joke. Nobody will ever catch a good night´s sleep in here! I simply can´t believe that any sailor is going to fold out this bunk and take a nap while this wild horse is speeding along?! No way! Even the nice blue coloured lighting couldn´t make up for the fact that this is pure racing. Let go all your romantic dreams about sailing this yacht – it is a beast. Full stop.
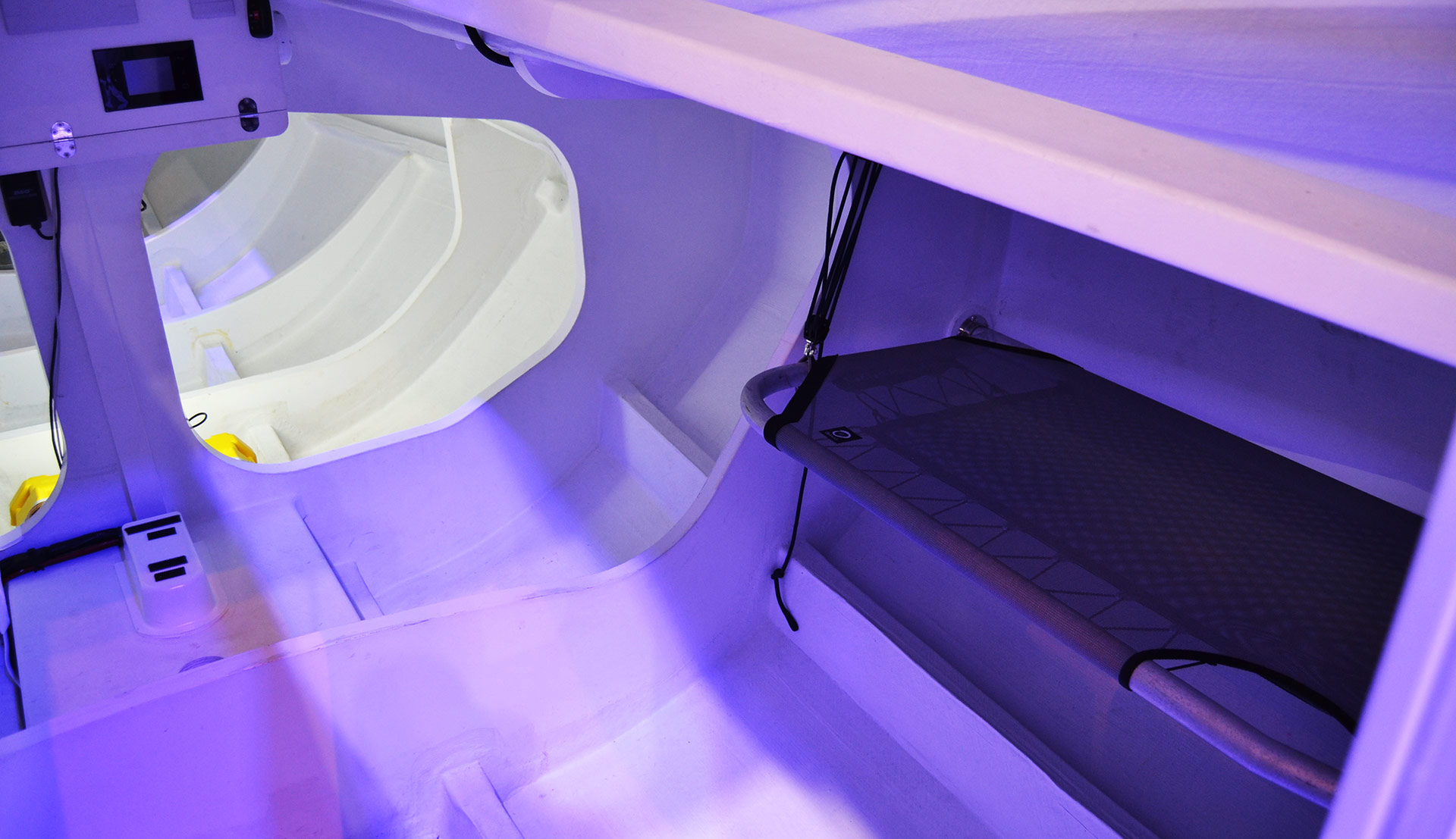
The foils made of composite material are huge! They look so fragile on the renderings and appear so thin in the drawings but they are in fact massive. So are the ducts through which the foils are put out to leeward side by the sailor: Back in the production hall I could inspect the thickness of the hull all around this particular part of the boat and I am absolutely convinced that there won´t be any problems in this part of the boat even if the yacht is hitting an object in the water.
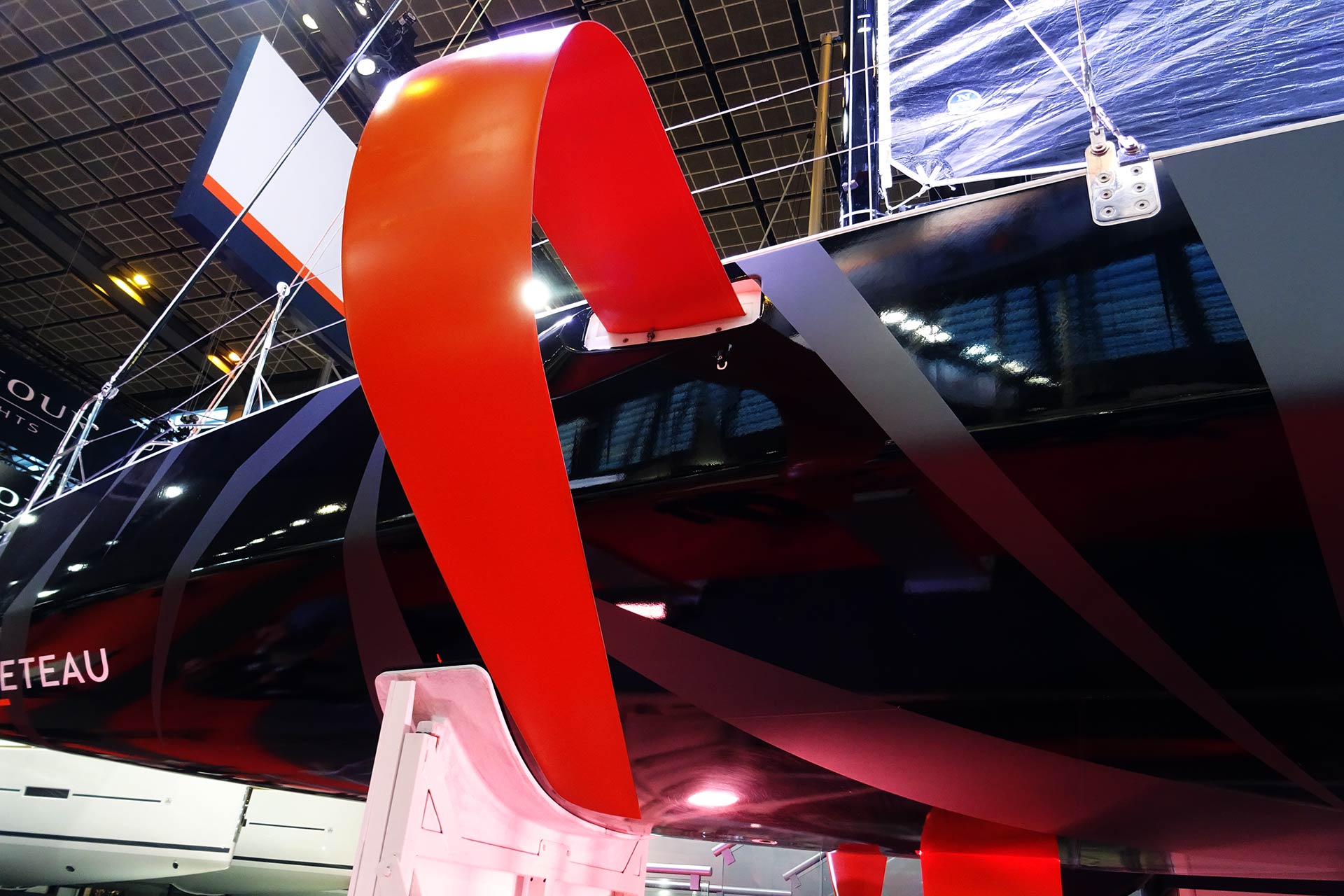
So in the end I spent a full hour on the stand, roaming the Figaro 3 prototype from the outside, crawling underneath her hull, taking closer looks onto all the various aspects of her outer body, creeping over her deck to check the chain plates and all the other fittings. I in the end even try to get myself lying down into the berth which barely could fit my whole body (I am 1.86 metres tall). It´s a truly fascinating yacht for sure – but it´s not a Dehler, it´s not an X-Yacht and it is not a Pogo. This is not a toy. This is serious racing.
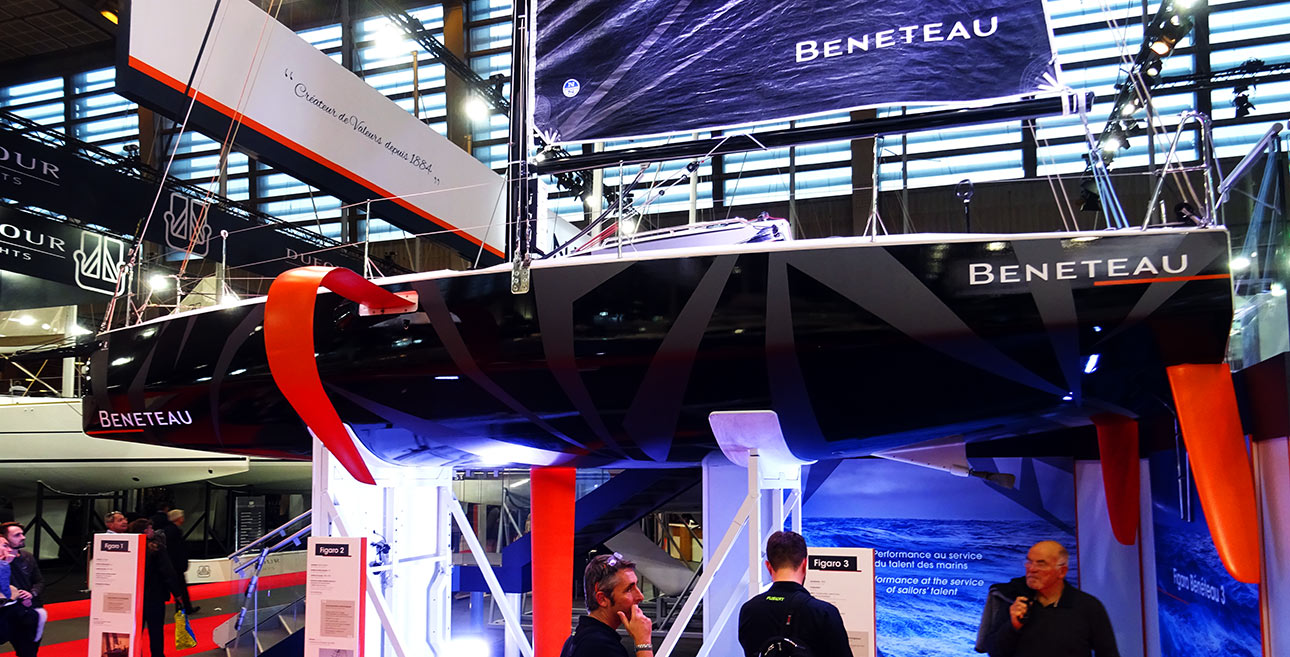
I do thank Gianguido Girotti for opening the Nantes facility of Beneteau to my camera, to showing us around and openly answer all of our questions. I wish the Figaro 3 project, all her sailors and the class all the best and most of fun and joy in sailing these boats starting in 2019 when the class is switched to the third generation yachts. And maybe, only maybe, I will get the chance to at least be a passenger one day – in nice conditions – when the Figaro 3 is casting off to show a tiny bit of her sailing abilities.
Thanks Gianguido, thanks Vincent again. It was a pleasure!
Read more about FIGARO Racing yachts here:
Decoding the Myth of La Solitaire Figaro racing
Eric Ingouf of BENETEAU Racing Division on the new Figaro 3 racing yacht