There is seldom a brand attached to a certain kind of boat like it is in fact with Alubat of France. When somebody is talking of aluminium yachts it may be most likely an Alubat he is actually talking about. The Ovni Range is one of the most known and most sailed aluminium yachts in the world – the name Alubat derives from “Aluminium” and “Bateau” – boats of aluminium. I was lucky to get Nicolas Moussart on the phone when I happened to be around Les Sables d´Olonne and he instantly agreed to show me around: “Sure, you are welcome, let´s drop by the yard!”
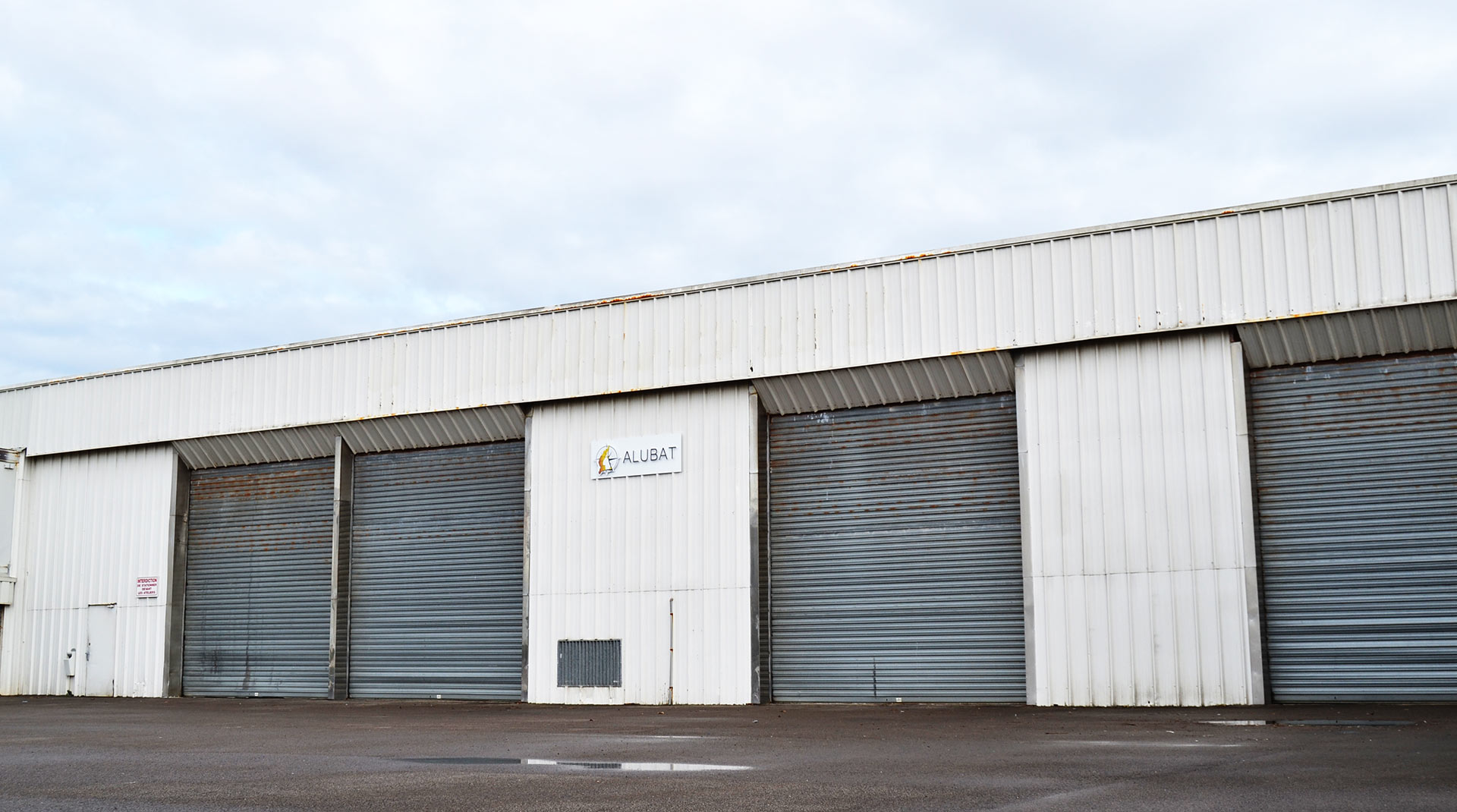
The area around Les Sables (it´s more a suburb of Les Sables to be honest, a village called Chateau d´Olonne) is bristling with smaller and bigger yards, all the way down from Brest to Bordeaux the French Atlantic coast is home to most of the French boat builders like Dufour, Jeanneau and Beneteau and of course smaller yards like Pogo Structures, JPK, RM Yachts (LINK), CNB or – right – Alubat. When I drove to the yard and parked my car I was standing in front of featureless factory buildings, just a small sign, barely visible, announced that in these very shop floors the Alubats are made. Nicolas, Design Office Manager at Alubat, welcomes me and apologizes that the CEO, Christian Picard, couldn´t make the tour with me for he was on a parallel tour with clients. No problem, I thought.
Where real work happens: Making of an aluminium yacht hull
“Let´s start and see the production”, Nicolas said and walked in front of us, pushing aside a number of doors making us finally enter a big hall. The noise was overwhelming, so was the smell: There were metal grinders cutting their way through aluminium plates, sanders were throwing sparks furiously and somewhere people were hammering against some metal plates creating an almost unbearable staccato of noise: Since 90 per cent of the yards I visited do produce GRP boats, I wasn´t aware of the fact that “real” ship building is a matter of joining metal material.
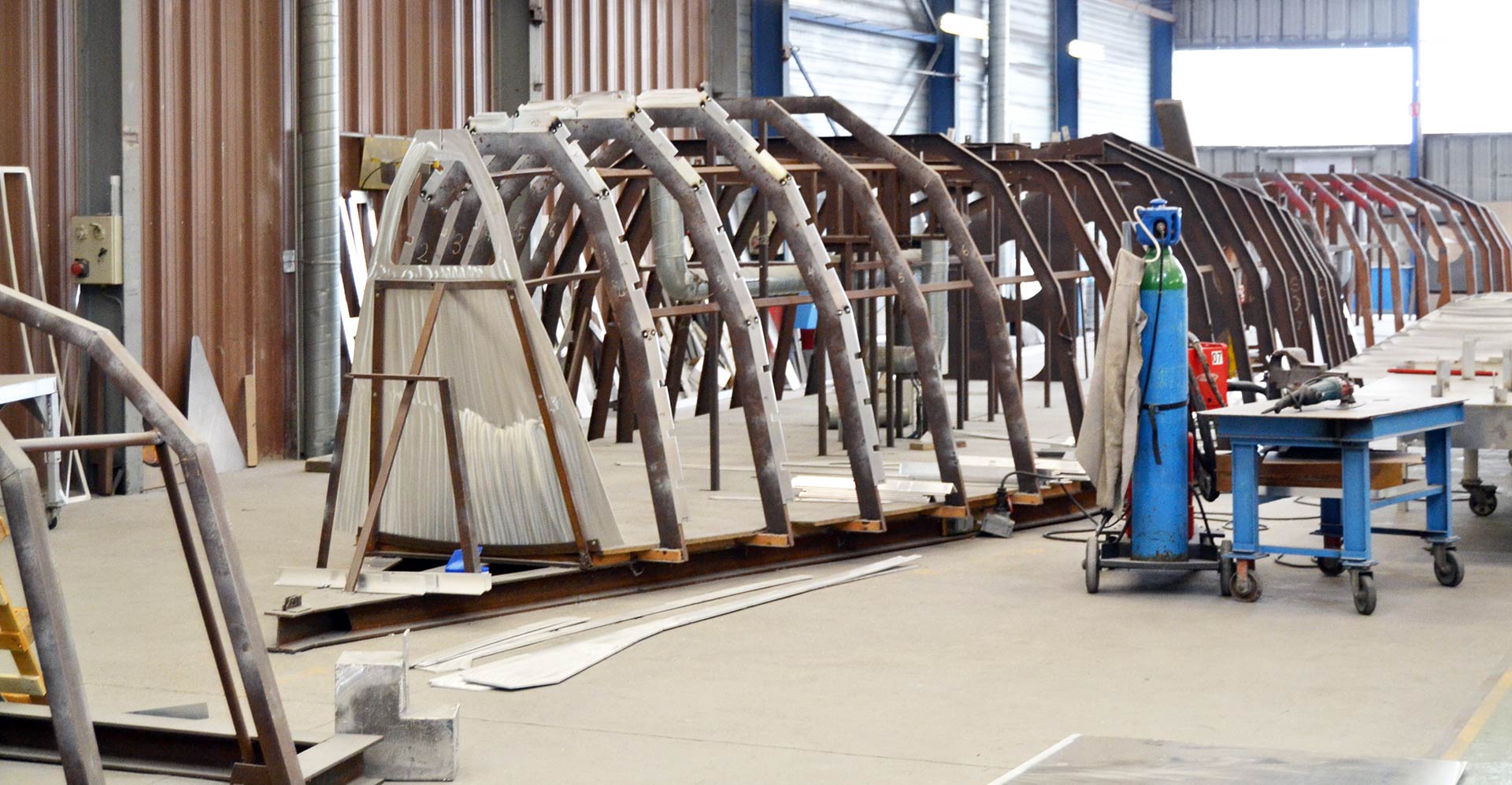
Our first halt was in front of a brown steel frame, a caliper model of the hull structure. “This is where it all begins”, says Nicolas, sometimes raising his voice to near screaming in order to get the message through to me against the noise. “The welders start to put the vertical frame together by attaching the metal to each of these ribs of the model.” I could see frame number 1 with a solid collision bulkhead marking the anchor chain locker and some other frames still attached, yet a lot of others ere missing still: This boat is at her very beginning. “You see the cavities in the vertical frames? This is where in the second step the stringers will be inserted and welded.”
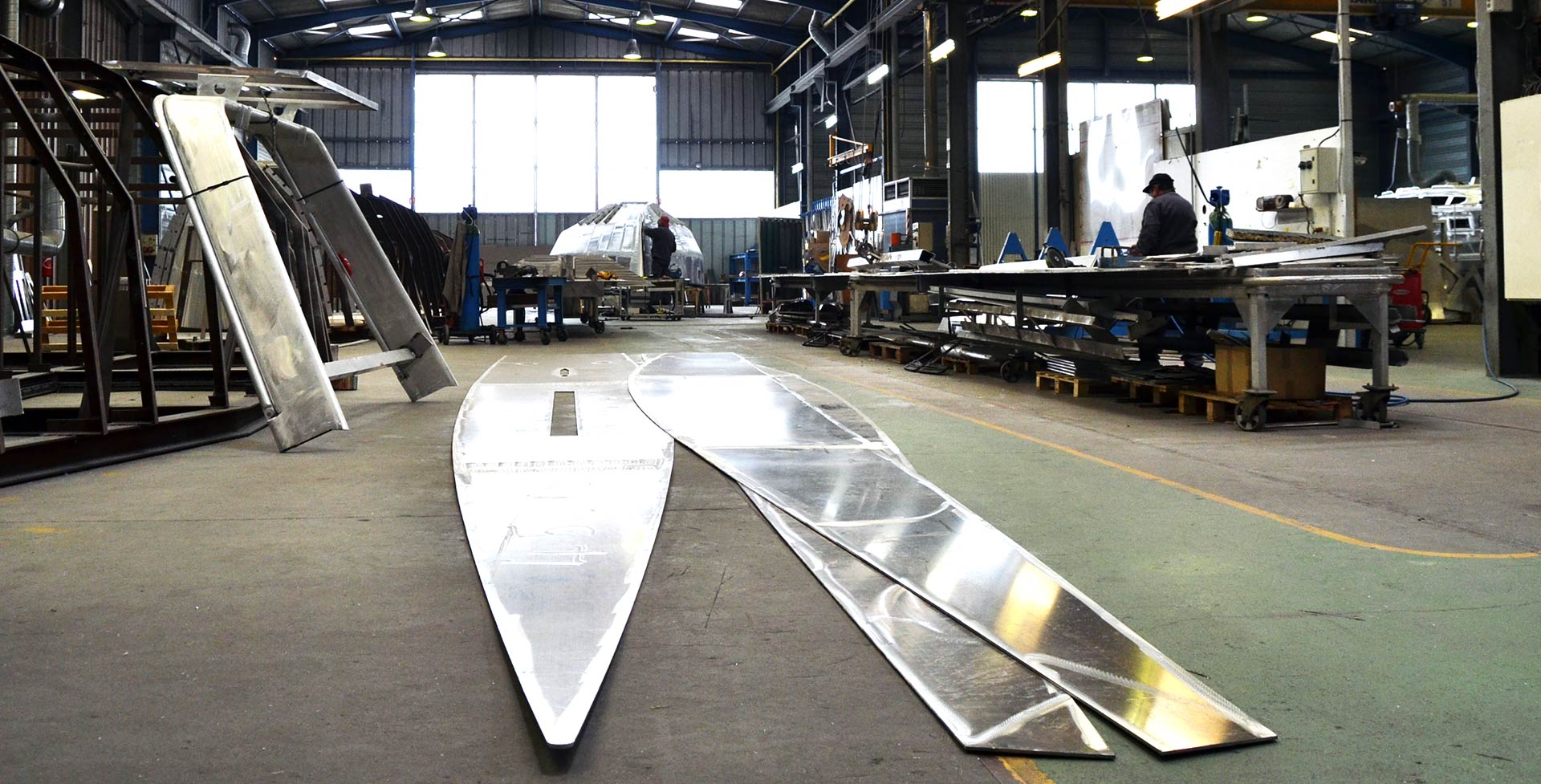
Walking over to the next working station, three 11 or 12 metre long aluminium plates were laying on the floor. Since the Ovni-Range (the most successful series of Alubat boats) is a hard chined boat, almost all of the hull can be done with a handful of larger parts. “You can see here at the left the lowermost part of a new hull, notice the gap for the lifting keel and the blade shaft there.” The metal parts are cut out by laser and prepared by a worker to be welded onto the vertical frame later.
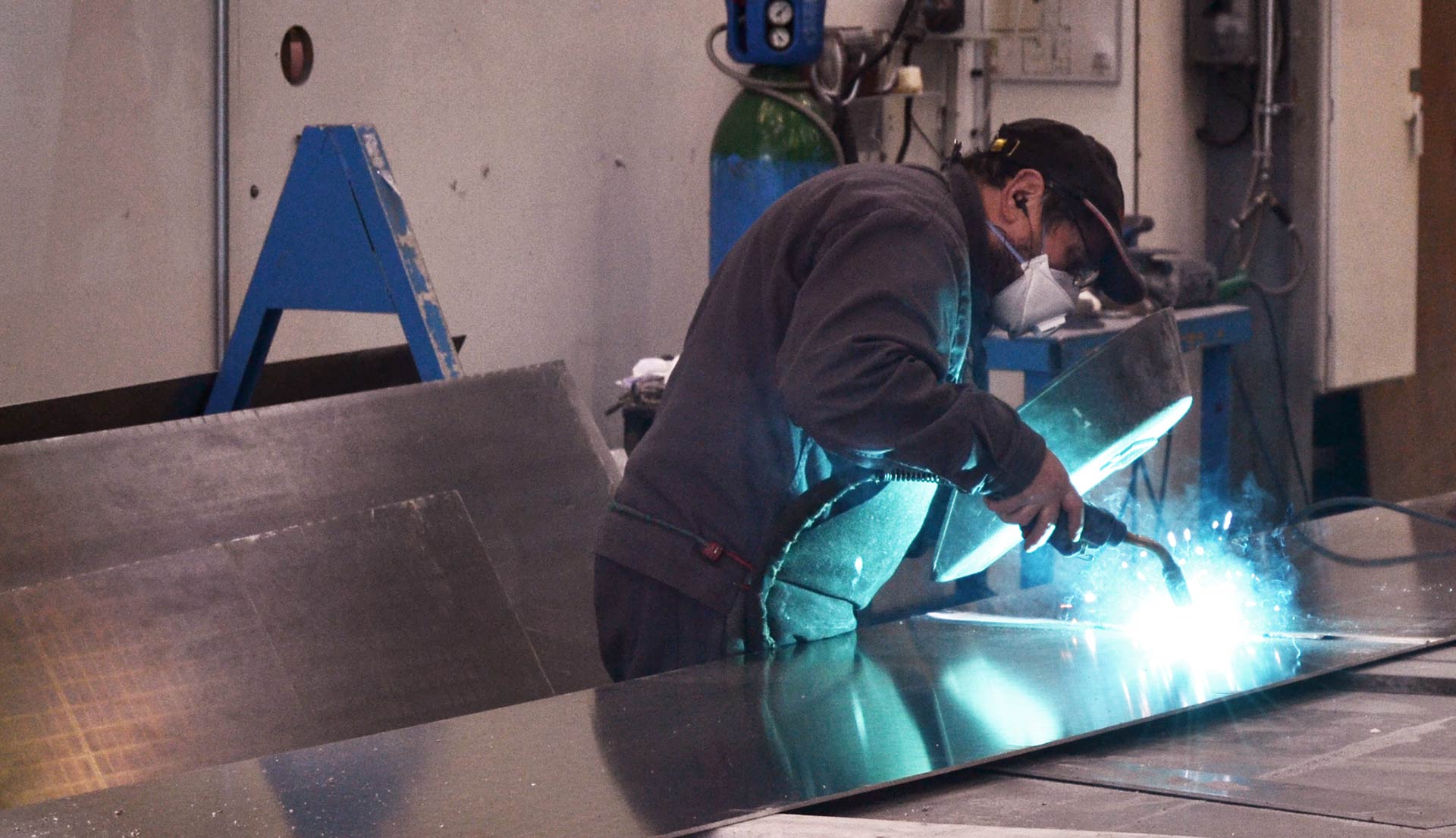
How many people do work here?, I ask Nicolas. He waits until another set of unbelievably loud bangs and clanking was over and said “Some 35 people are working here at the yard.” That isn´t too much, as he told me, but the crisis of 2008 wasn´t really overcome until 2016 when orders went up again. Alubat did have troubled times indeed and it had been a hard time for the whole yard. Now, with 29 employers again the business is recovering eventually: “You see, we launched the new Ovni 450 just 6 months ago – and we are now having 6 orders! This is a great thing!”, says Nicolas and smiles whilst the bing bangs set in again regularly.
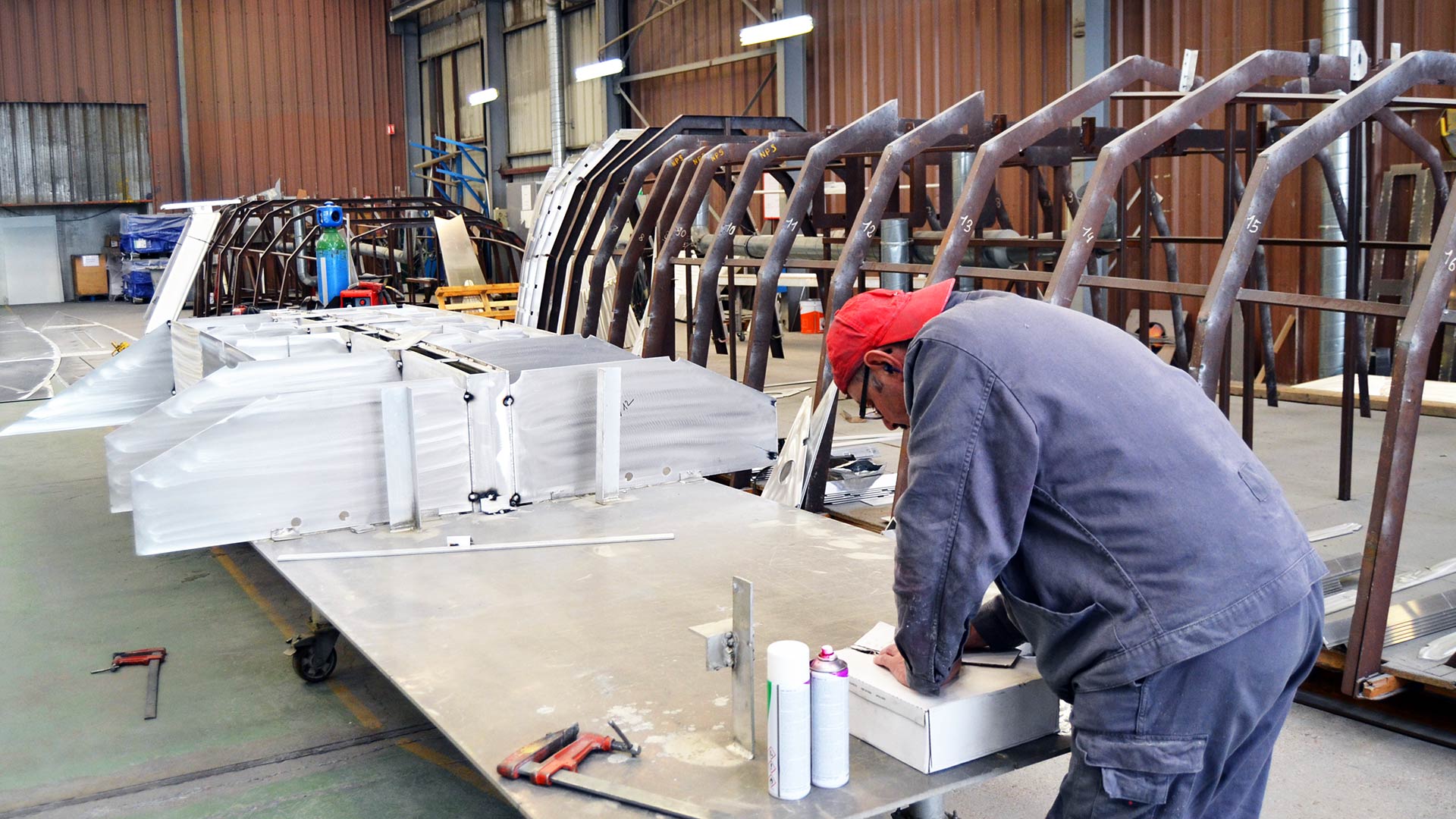
We approach a smaller boat, apparently and Ovni 365. The hull is turned upside down still so work hasn´t been ending here. From the inside somebody is hammering against the metal plates: A worker with a huge rubber mallet is banging against the hull plating: “The worker is meticulously going over all the sheething from bow to stern to look for small imperfections like dents and bulges. He will then graduate the dents with the hammer. But the noise is … terrible!”, he smiles, ducks himself under the hull and some moments later the bang dies out, a smiling worker appears with a “Bonjour Monsieur” and welcomes me to dive under the hull as well to see his work.
Highest demands on quality at Alubat
“You see, every hull is made by one single person at Alubat. In this case … it is this man.” I stumble. Is that true? Like with Rolls Royce? I ask Nicolas if this is correct and he nods. What a great thing this must be, I think by myself: When I order a boat here I will get to know the very man by name who was building my hull from the first small metal parts on the caliper to the very end. I could come here, get to know him, see in his face and be sure that my boat is done in the best way. That´s a cool thing though!
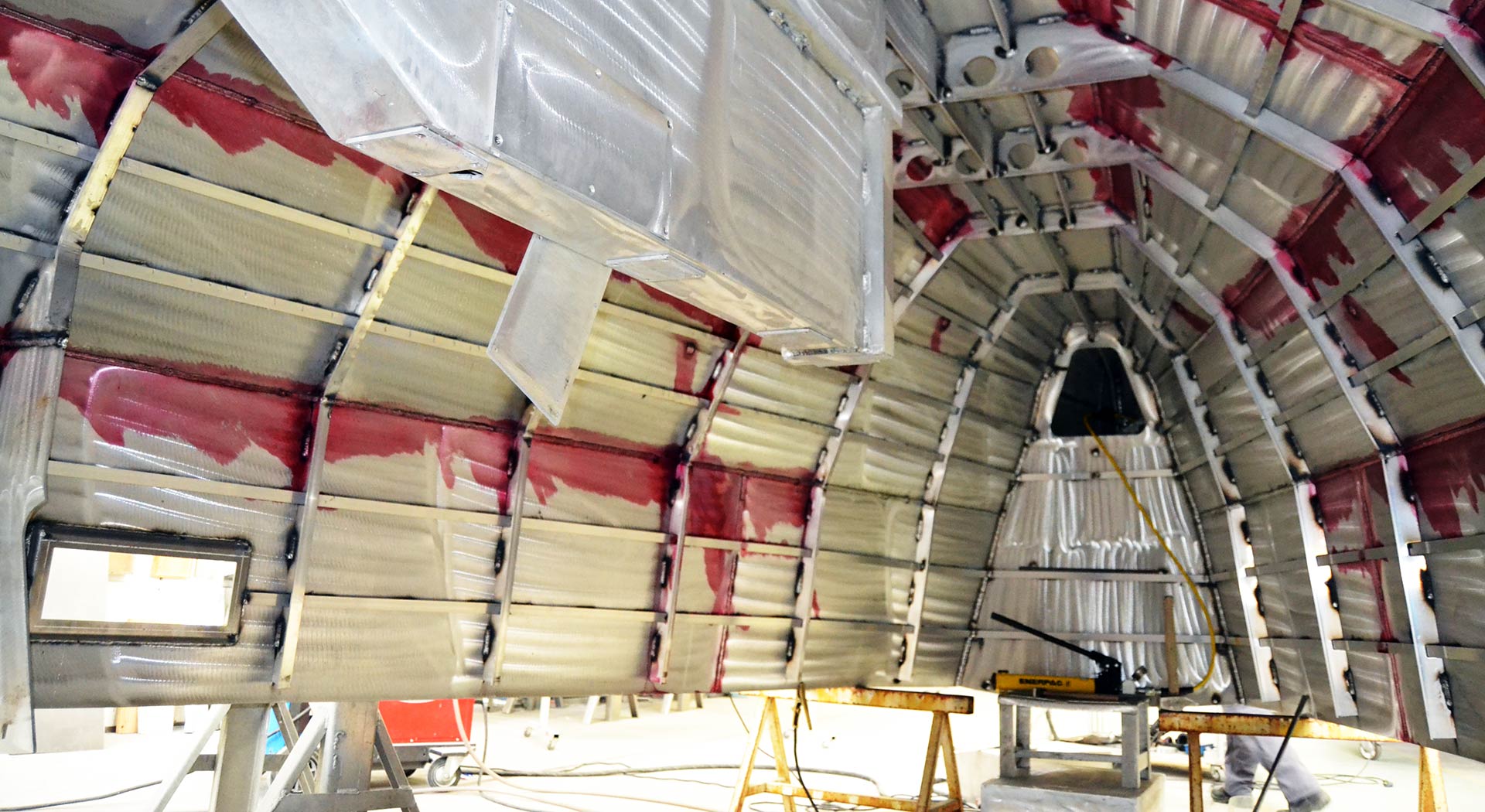
The inside of the Ovni 365 hull was blazing in clear metal colours. The smell was an interesting mixture of metal and a burned sensation. As we were talking, the reverberant sound of our voices were repeated to create an interesting backdrop. I wanted to know what the strange red-violet fluid was that was spilled all over the hull from end to end: “This is a part from our quality checks. The fluid is poured onto the seams where the hull plates are welded together. By a diffusion process the fluid will creep into the tiniest cracks, gaps or holes. When it appears on the outside of the hull we can see that there is a permeable space and can close it.”
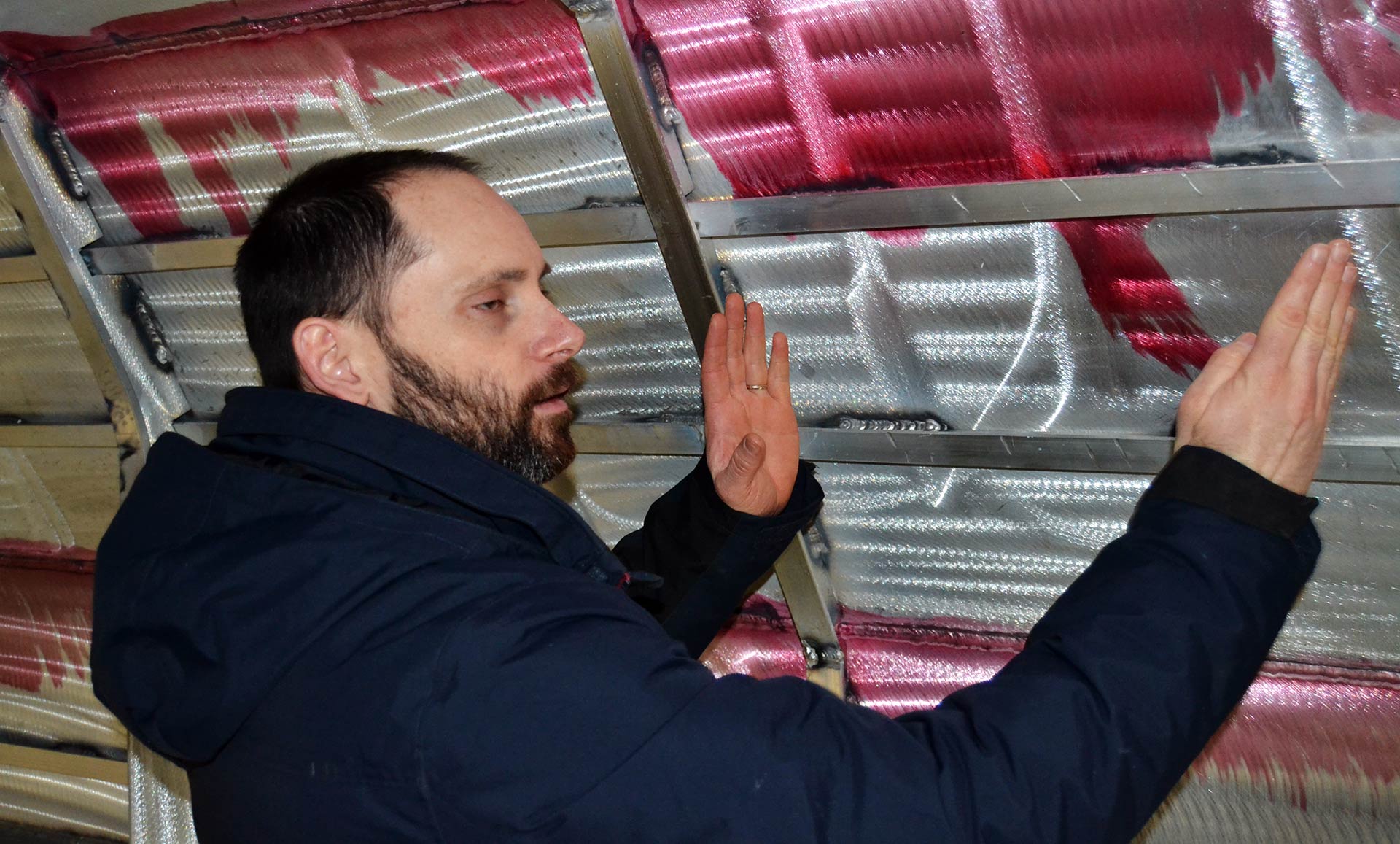
It takes some time to get accustomed to the noise of this large workshop but after some 20 minutes I don´t hear the constant bangs anymore. I feel a nice sensation of being in a “real” shipyard where “real ships” are made. I am attired to the fact that the workers here are welders, metalworkers with grinders, big hammers, electrical wiring equipment and all the “hard” stuff. Sparks are flying around instead of GRP-shreds, an odour of Ozone is in the air instead of Styrol. I like it here very much!
Why an aluminium yacht is superior
“Let´s end the visit to this first part of the production over there”, says Nicolas and draws my attention to a building lot where another big boat is jacked. “This is hull number 3 of our new Ovni 450 in the final stage of the hull production. The hull is nearly finished and then ready to be brought to the next production step.” We say “Hello” to the three workers crawling outside and inside of the boat and enter the yacht.
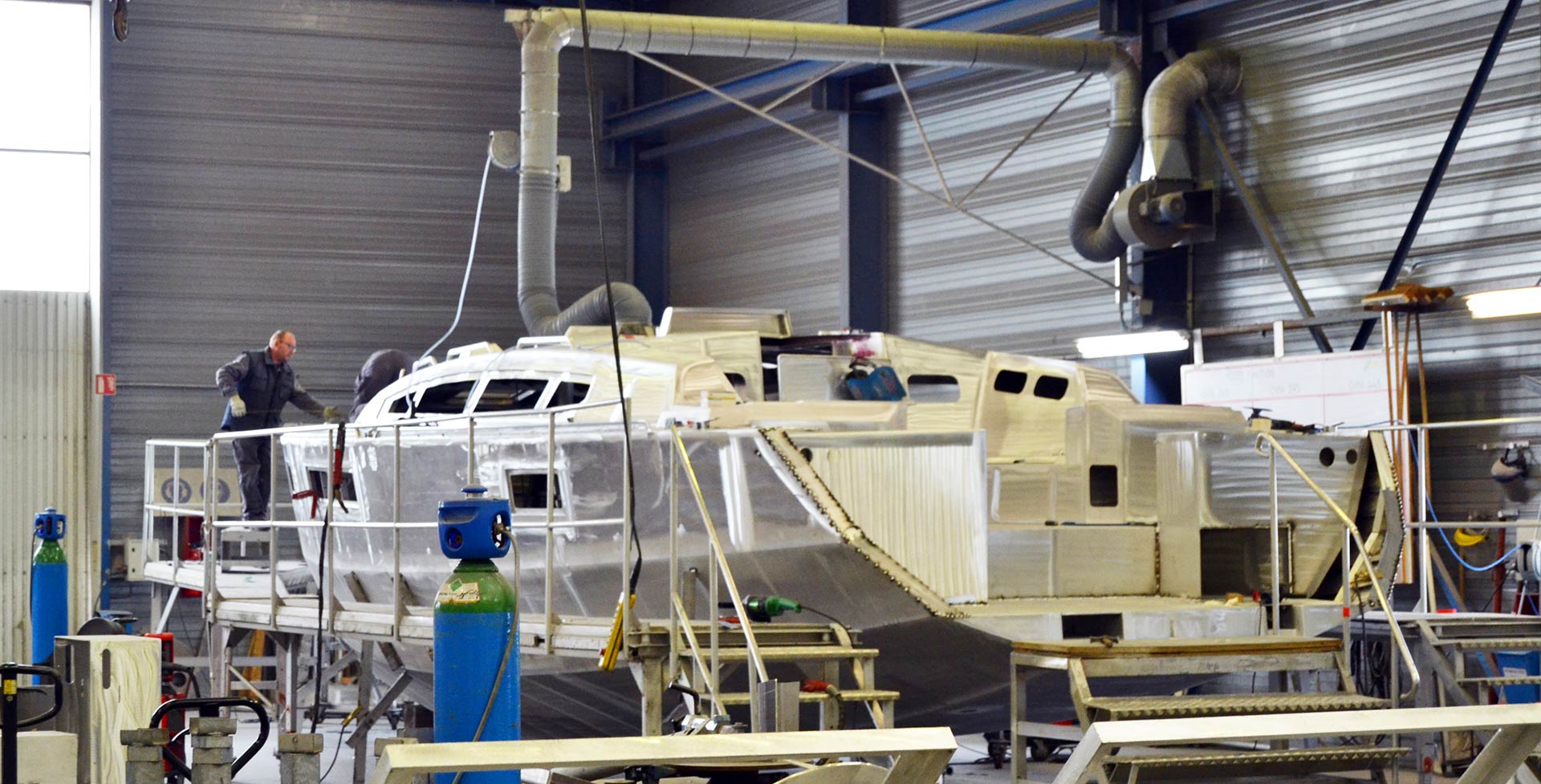
The boat is still completely empty of course but this gives me the chance to have a look at the structure and the bare construction of the hull itself. I notice the integrated fresh water and Diesel-tanks, the massive base mountings for the centreboard keel with an even more massive keel chest as well as some nice details of the stringer/vertical frame construction. As I was witnessing when I was visiting Benjamins Yachtwerft in Emden, where the Berckemeyer yachts are made (read the article here) it´s the same with Alubat: Aluminium is the material of choice when it comes to having a safe, massive, durable yacht capable of going anywhere in the world.
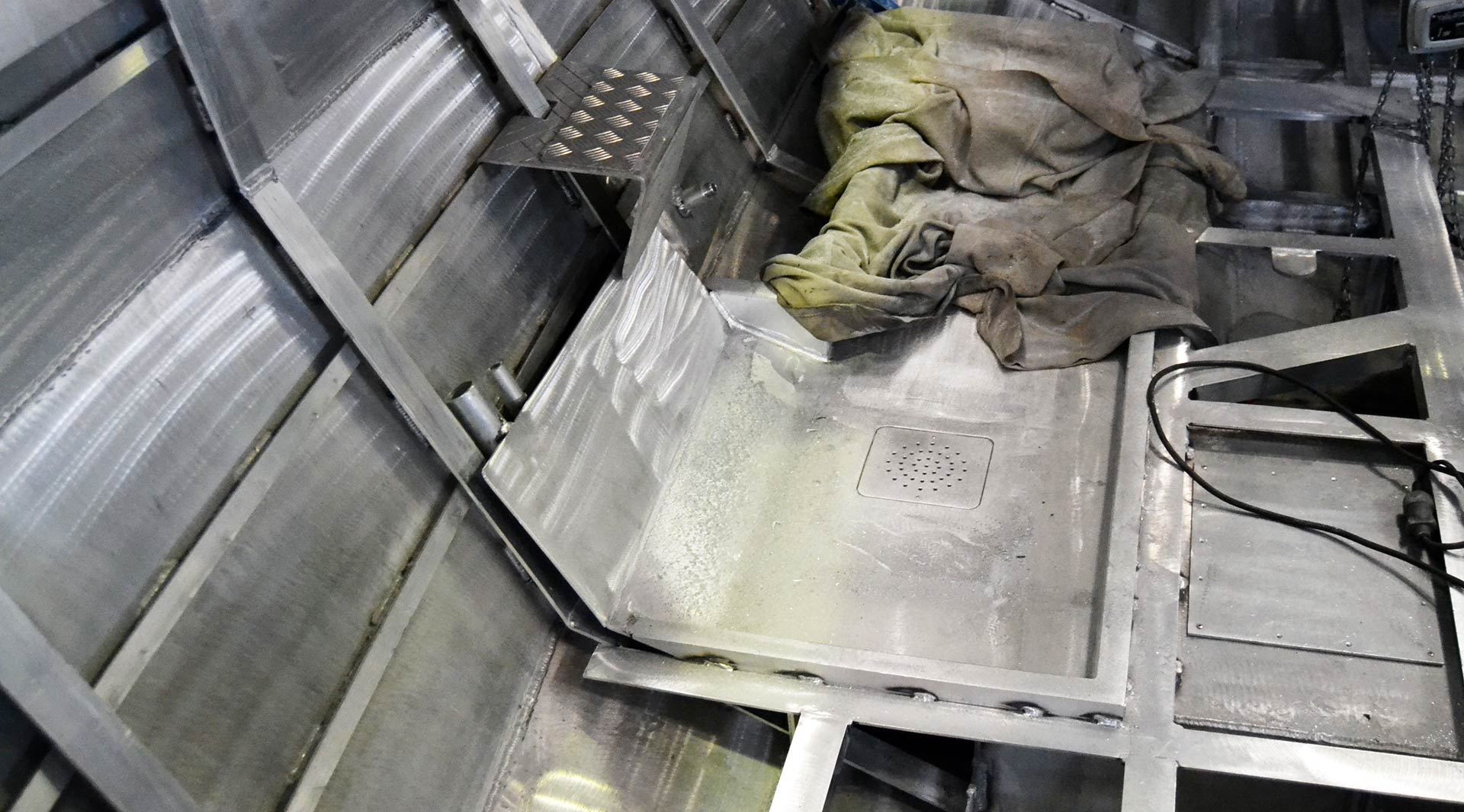
I also liked the detail of the integrated drainage in the heads very much: It shows that at Alubat people with knowledge and experience do indeed design the boats. The Ovni may not be the most appealing boat in the world and she is certainly not a design-award winning state-of-the-art beauty, but these yachts, as I said before, aren´t without reason one of the most chosen yachts for serious long haul sailors.
Alubat´s specialty: Painted aluminium hulls
In contrast to the Berckemeyer-philosophy of preferably not having the aluminium painted, Alubat is also known for their high quality paintjobs done with their yachts. I am very keen on seeing those production steps as well and I was happy that Nicolas agreed to show me around in the paint shop. Besides, I was generally very surprised again by the openness with which I was greeted here: I was open to go anywhere in the halls, take pictures of every single detail I wished and Nicolas willingly and very committedly answered with excitement.
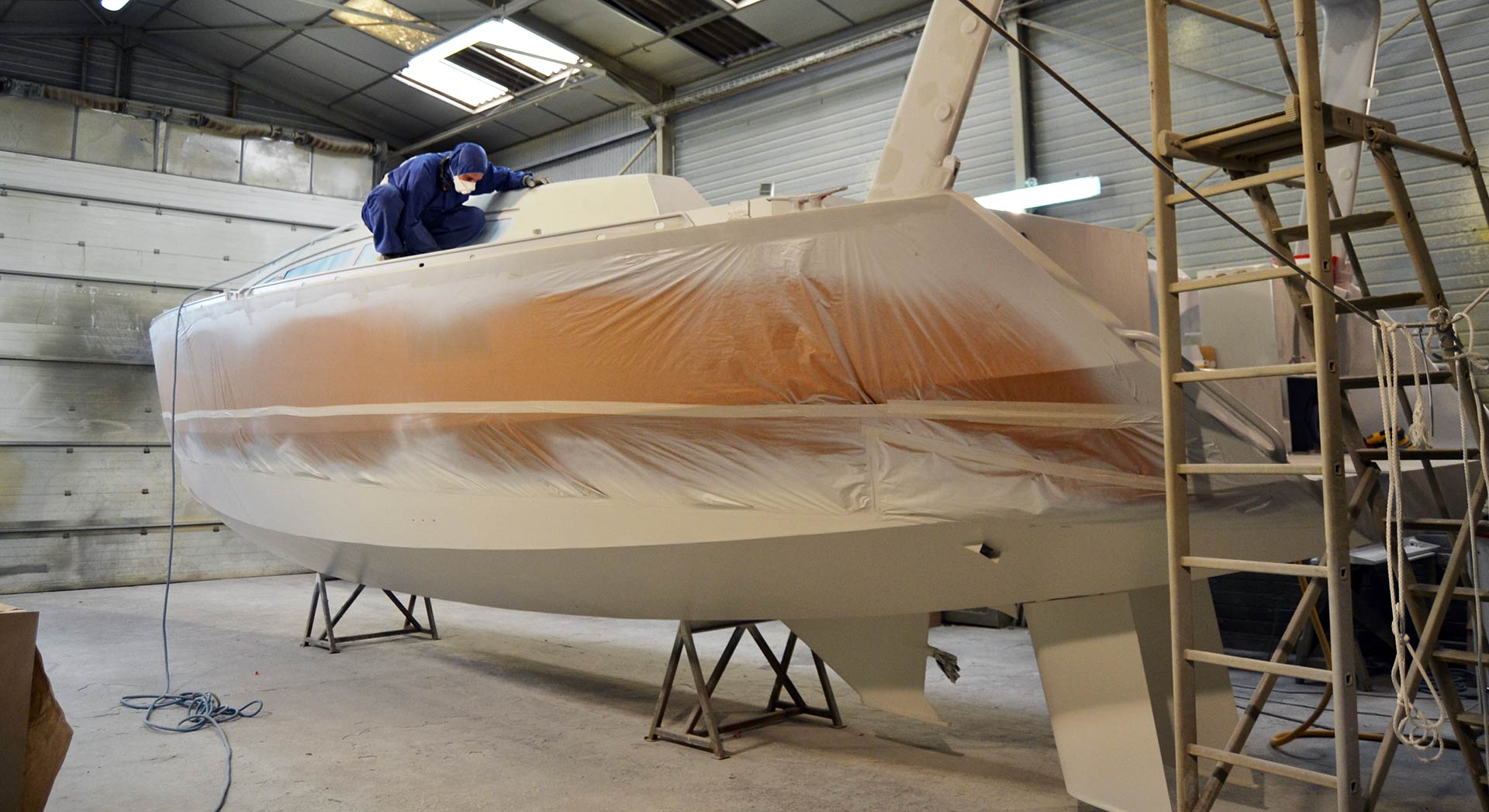
Before an aluminium-made hull can be painted there is a painstakingly elaborate set of steps to be made in order to pretreat the bare hull. Since it takes just a few hours for aluminium to begin oxidation (which creates a thin layer of protective patina) there is a very short time frame for the workers to apply the layers of primer coat to the hull. The hulls will be sanded very cautiously and the treated with a (well, of course, secret) mixture of acids to create a bare aluminium surface without any patina. Then the primer is applied.
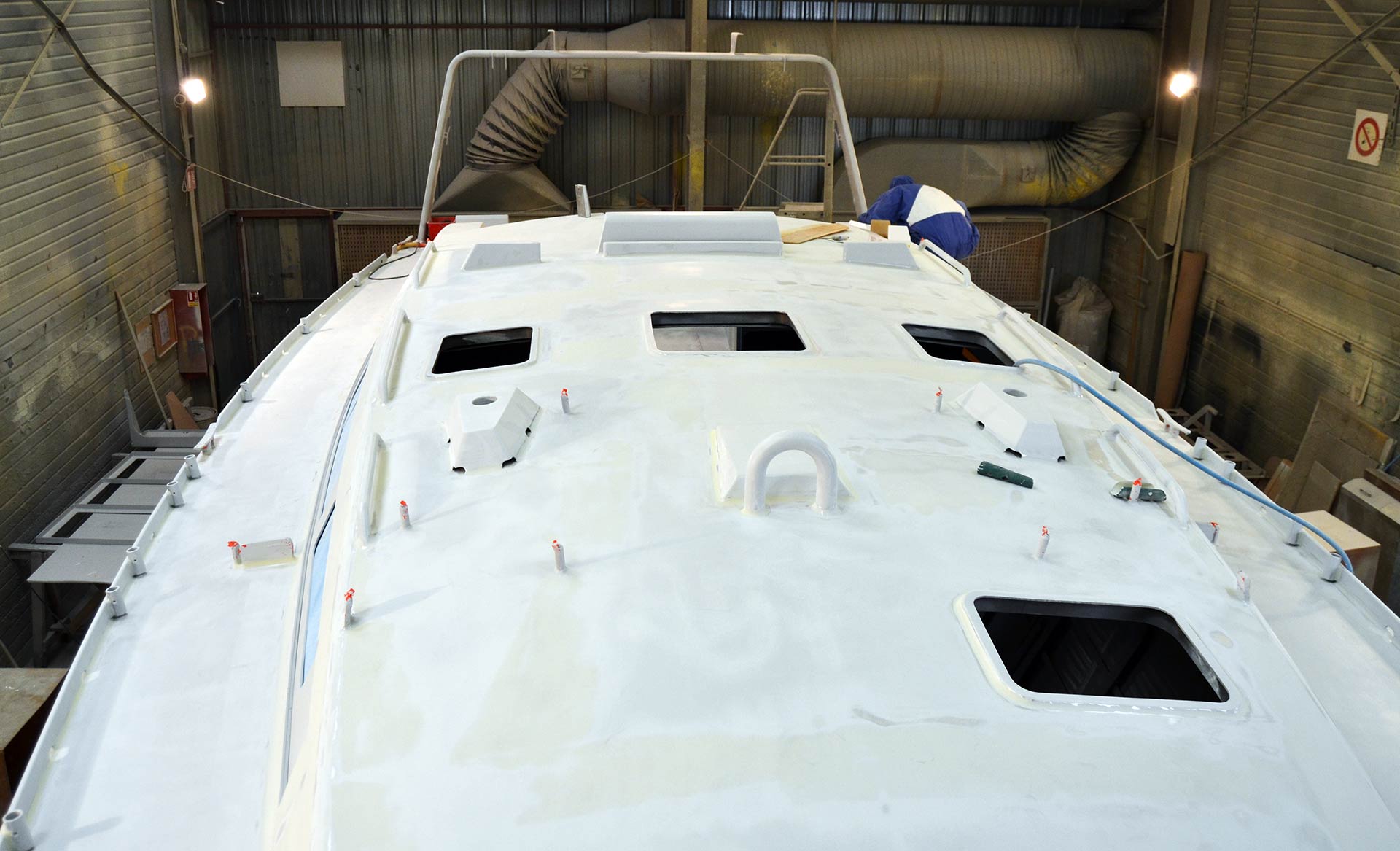
We witnessed the next steps: Sanding down the primer to achieve a perfect surface. This is – I couldn´t believe it but that´s true! – done completely by hand. Here at this smaller Ovni no less than three people were very cautiously sanding down the layers of primer coat on the deck and superstructure: Even in the inaccessible corners, roundings, edges and surfaces the well skilled workers reached with their sandpapers to dexterously give the surface the best possible shapes.
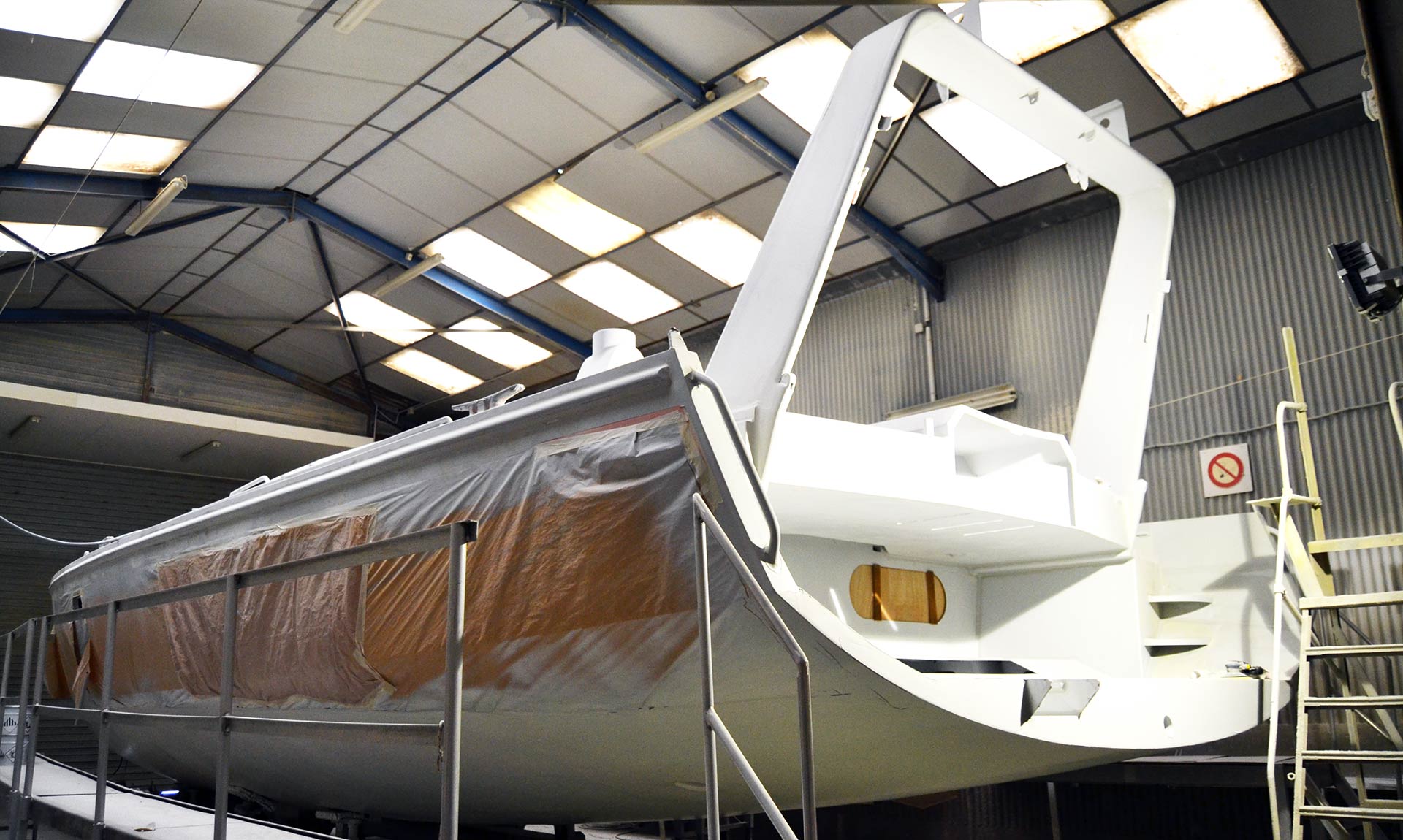
In another hall of the production line an even bigger and more impressive boat was jacked: A Cigale 16, the 2010 by Marc Lombard re-designed successor of the Cigale-range, of which I so dearly love the original Cigale 14 (here´s an article on this fantastic 1997 design by Jean-Marie Finot). I was awed and stunned: What a beautiful boat! This yacht had received her first (or second) layer of the very paint that comes over the primer coat. I loved the yacht-white and looked at her wide stern with growing love. With Alubat – unless clients wish differently – it is customary to have the hull itself above waterline free of paint whatsoever but the deck and the submerged parts of the boat painted accordingly.
Interior design and best craftsmanship
This is what we could see in more detail when we left the paint shop (although I could have spent mere hours here admiring the awesome Cigale 16) and entered the hall were all the boats are jacked stern to a large lifted working terrace. “You see the Ovni in the foreground? Her hull is already painted and works in the internals have begun – but notice the hull above waterline in comparison to the second boat in the background?”, asked Nicolas. I instantly realized the difference in the sanding finish of the two hulls.
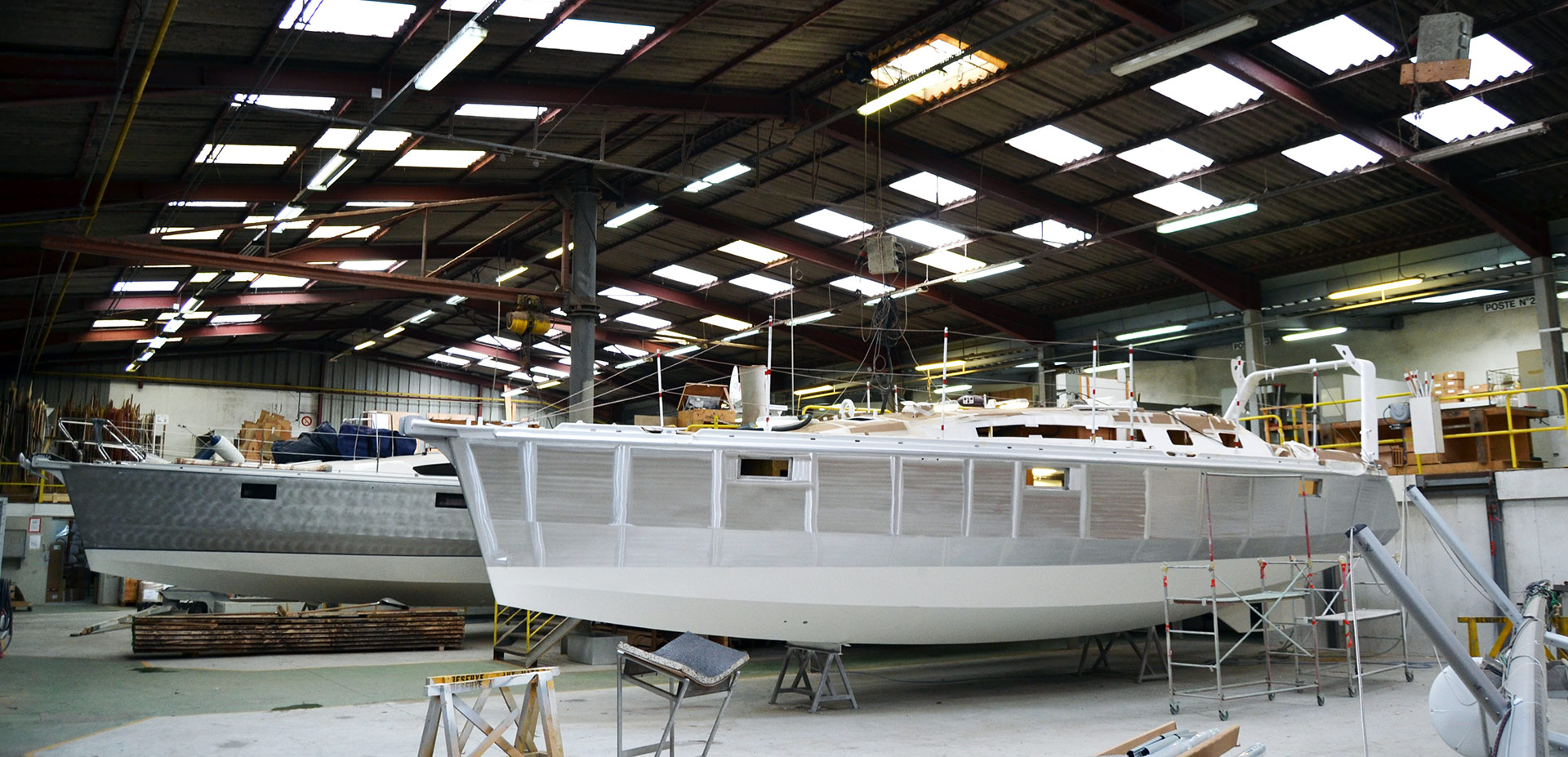
The half-finished Ovni 395 and one ready-to-ship Ovni 365 were open for us to take a look inside. “Here in this hall – and there is another one – the final building process takes place”, Nicolas explained. “We will insert all furniture, electric installations and other fitting here. The boat won´t leave the jack until it is finished here.” The sound-setting of this hall was considerably quieter than that of the metal- and even the paint-shop-halls with their constant loud buzzing ventilation installations.

Alubat went bust some years ago during the economic crisis that had battered so much the boating industry all over the world. It took a vast amount of power, money and will for even the big brands and market leaders to get through the tough years, survive and maybe come out even better prepared, streamlined with better products. “Alubat has been taken over by a pool of private investors who loved the brand and the products and poured their money into the yard”, explains Nicolas. Now, with reduced workforce and refined products Alubat is on its way of recovering. “We kept quality high and invested in further development of our ranges”, says Nicolas. Now the yard produces some 12 to 15 boats annually – trending upwards.
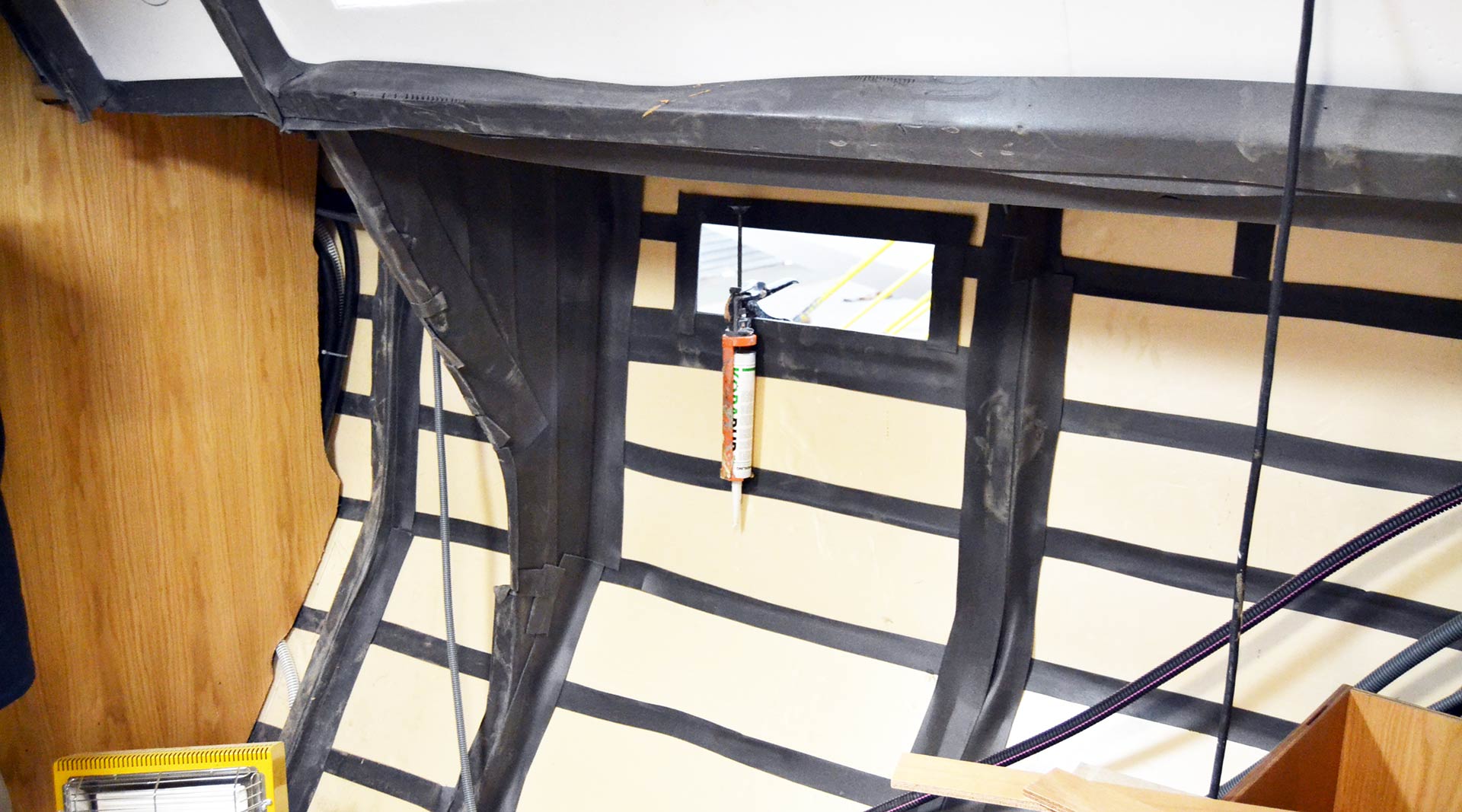
When I took a look into one of the half finished boats I´ve got an idea where the real differences in aluminium yacht-building and big production boat building of GRP-yachts lies: It´s the interior fitting process. Since the hull of a GRP yacht is at first made without the deck structure, all the interior parts can be pre-fabricated as modules and just levied into the place to be screwed or glued to the hull. Here it´s different: And I will soon see by myself why.
Woodworks at Alubat: Amazing!
We leave the final fitting hall to take the tour through the third and last production site of Alubat: The woodworks facilities. “The main difference here”, says Nicolas, “is the fact that we are making all of the carpentry by ourselves. There is – as you may have seen in the metal-workshop – one dedicated person responsible for a certain kind of joinery.” But it all starts with bare trees. Nowadays I would say that most of the new boats are fitted with lighter wood. Oak, to be precise.
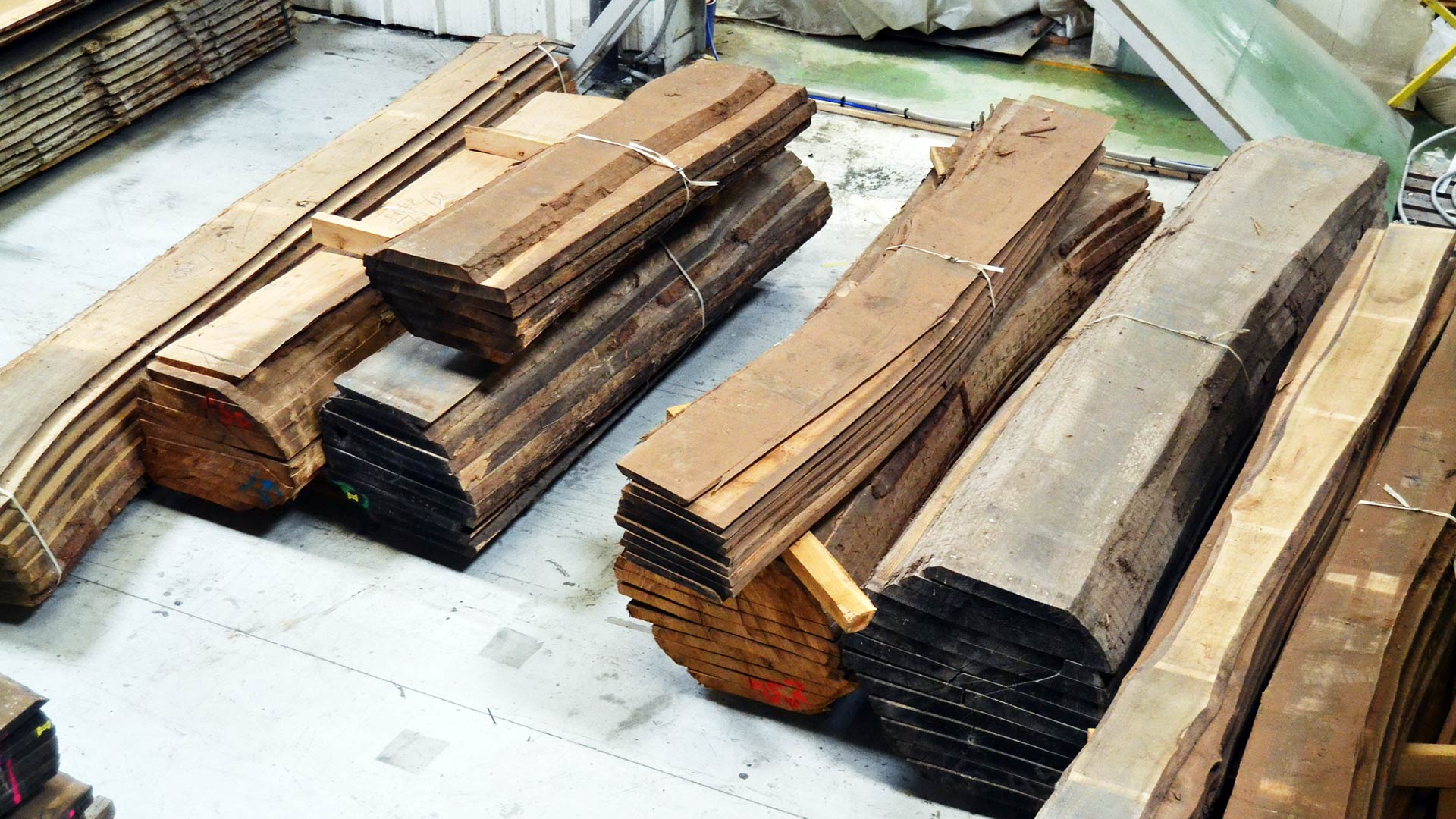
In one corner of the hall large portions of whole trees, roughly cut to thick planks in order to speed up the drying process are piled up next to each other. A very nice odour of forest fills the air. “This is American Oak which makes most of our interior carpentry right now.”, says Nicolas. American Oak is known for the densely grown material and the beautiful grain within. These rough planks will be turned into perfectly crafted galleys, benches and other internal fittings in he process.
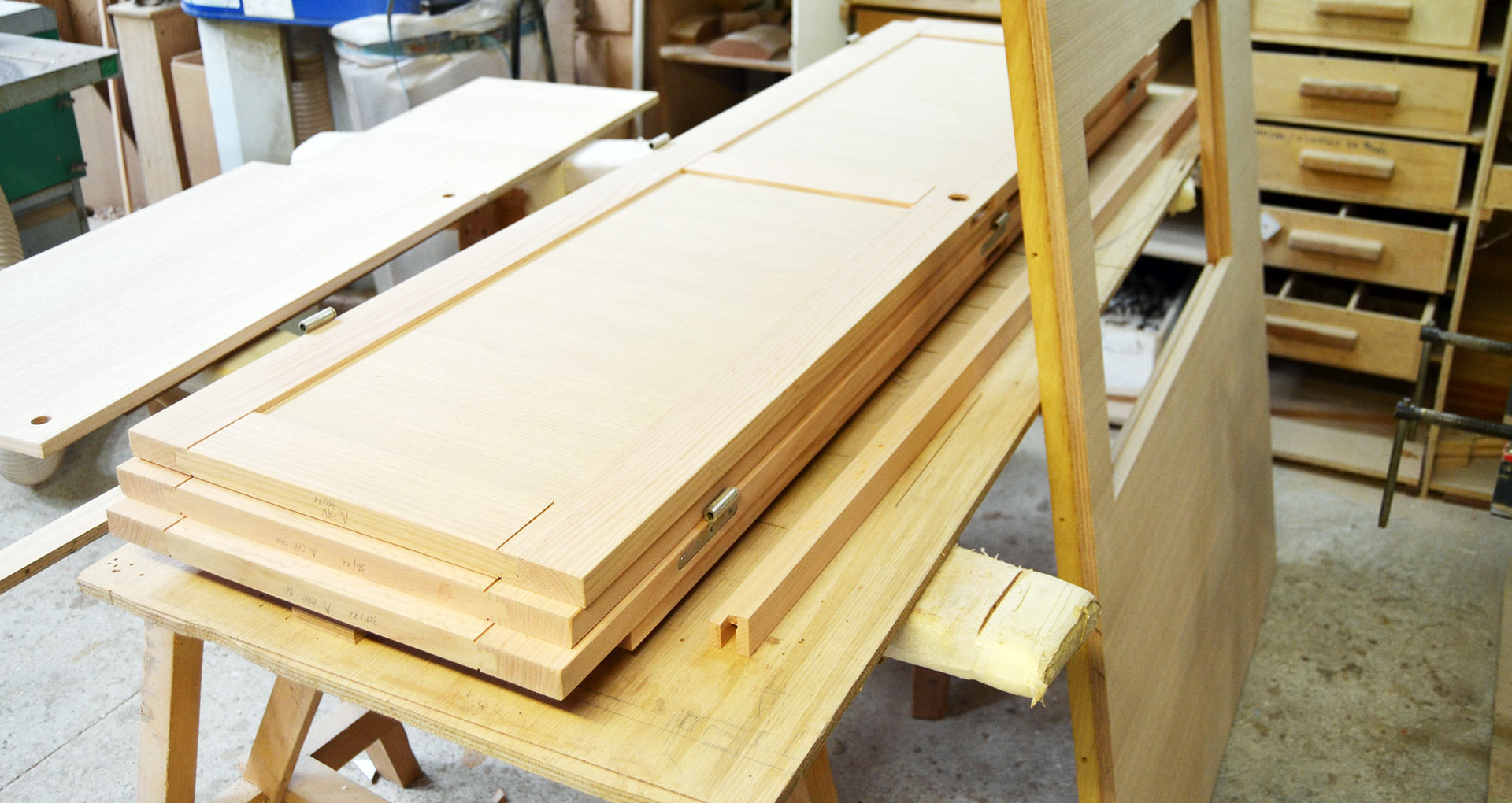
“Take a look at these cabin doors”, says Nicolas and shows a pile of four doors. They have been made from massive wood: No plywood, no veneer, just massive long lasting quality. The doors do not have any marks or scratches. The workshop smells even more intensively and spreads a fragrant of fresh cut wood. Anyway, there is no dust nor any splinters laying around on the floor, I am touched by the cleanliness and the organization of tools. Everything looks just neat and in proper order.
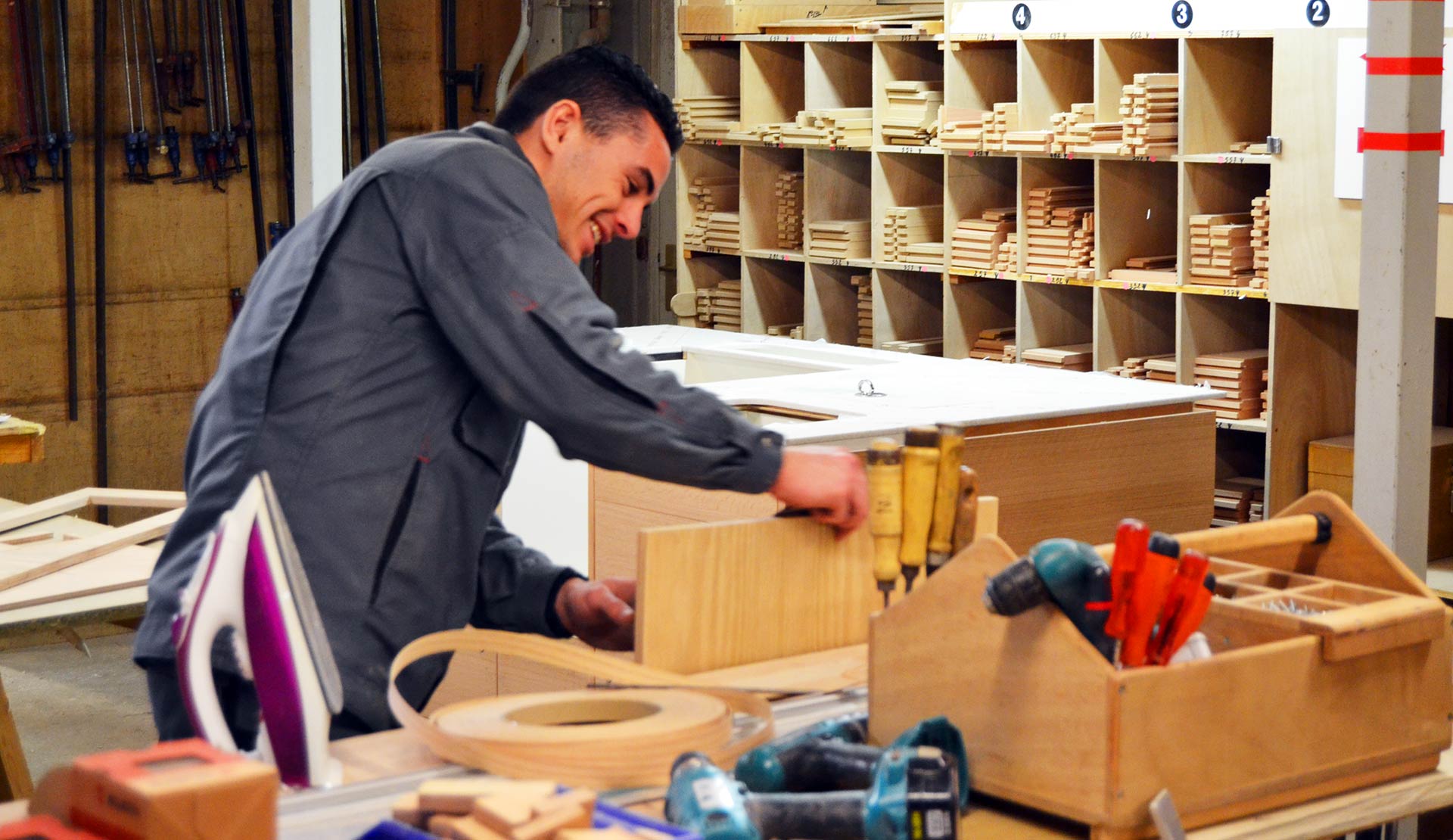
We approach a worker who is treating a piece of wood: “This is the man who is making the galleys for the Ovni boats”, explains Nicolas. One “bonjour” and a question if I could a picture of him later, he agrees and we stand there to observe how he is working. In fact, all the joinery is – not unlike the big GRP production boats – pre-fabricated here in the workshop indeed. The friendly young man welcomes us to take a look at his recent work: A nice Oak-made galley.
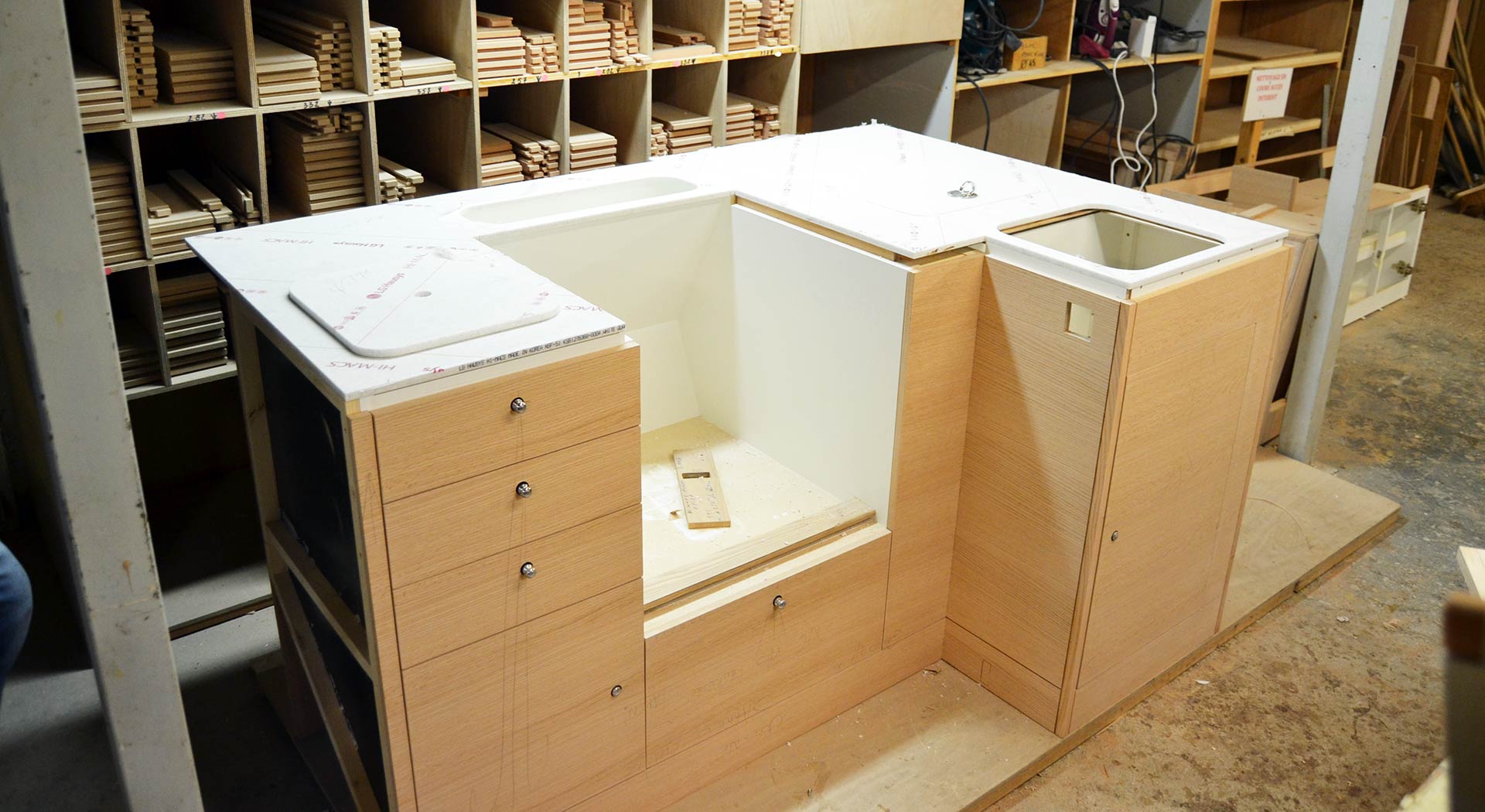
“They do build the galley and all the other things here on a caliper”, says Nicolas: “But then the galley will be disassembled and then brought into the hull. Piece by piece, one by one.” This is why it takes so much longer to make an aluminium boat: The workers have to take down each single part individually. On the other hand, this is what I realised when I looked at one beautifully executed ridge of at the galley, this ensures real quality and best craftsmanship: The people who make the stuff also mount it in the end.
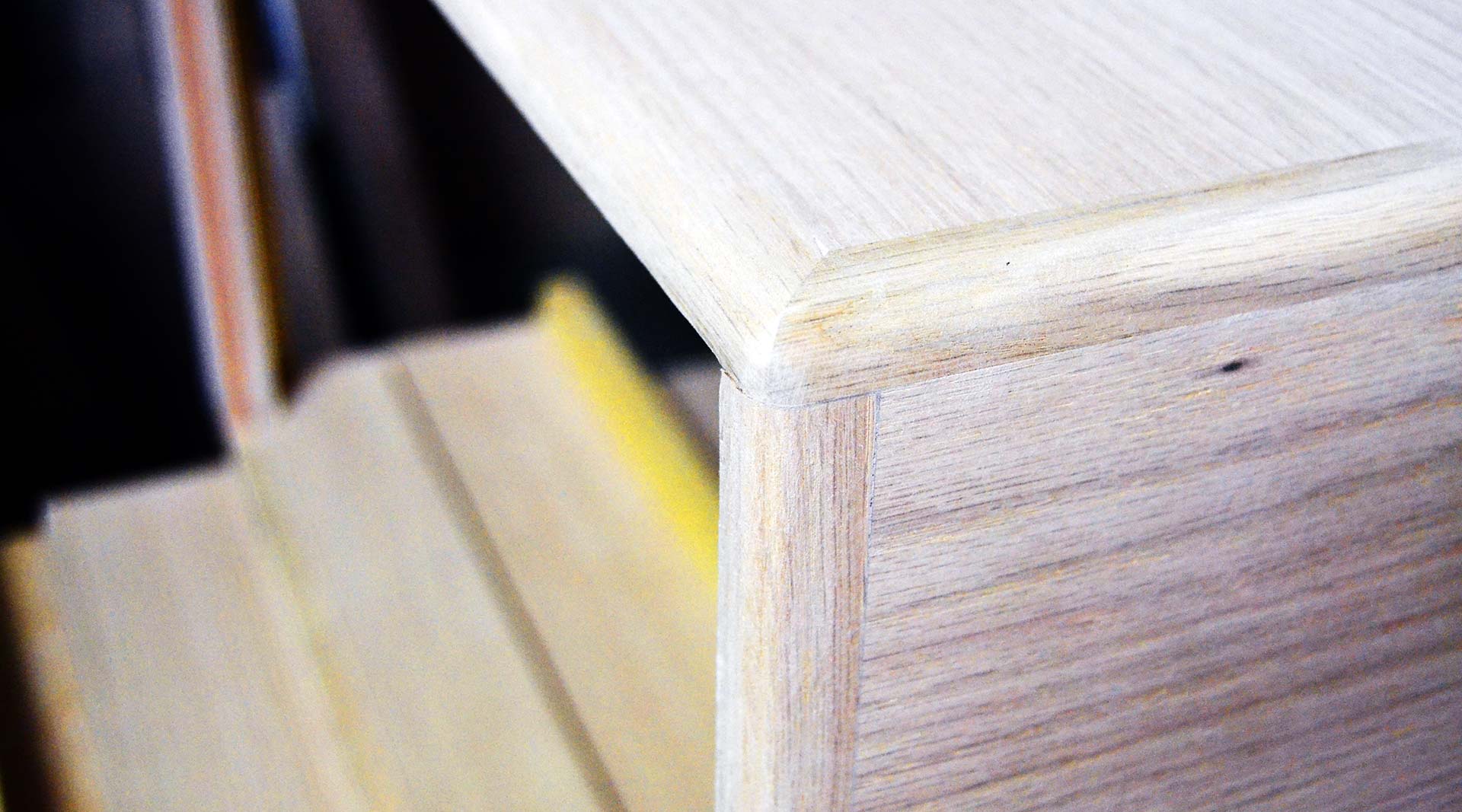
Back aboard an Ovni I see what this in reality means. No less than 4 workers are down below deck to fit their parts of wood to the boats: One is installing the staircases of the entryway, another is doing some panels in the rear cabin, two more are working in the owner´s cabin in the front to get some installations in the fore heads done.
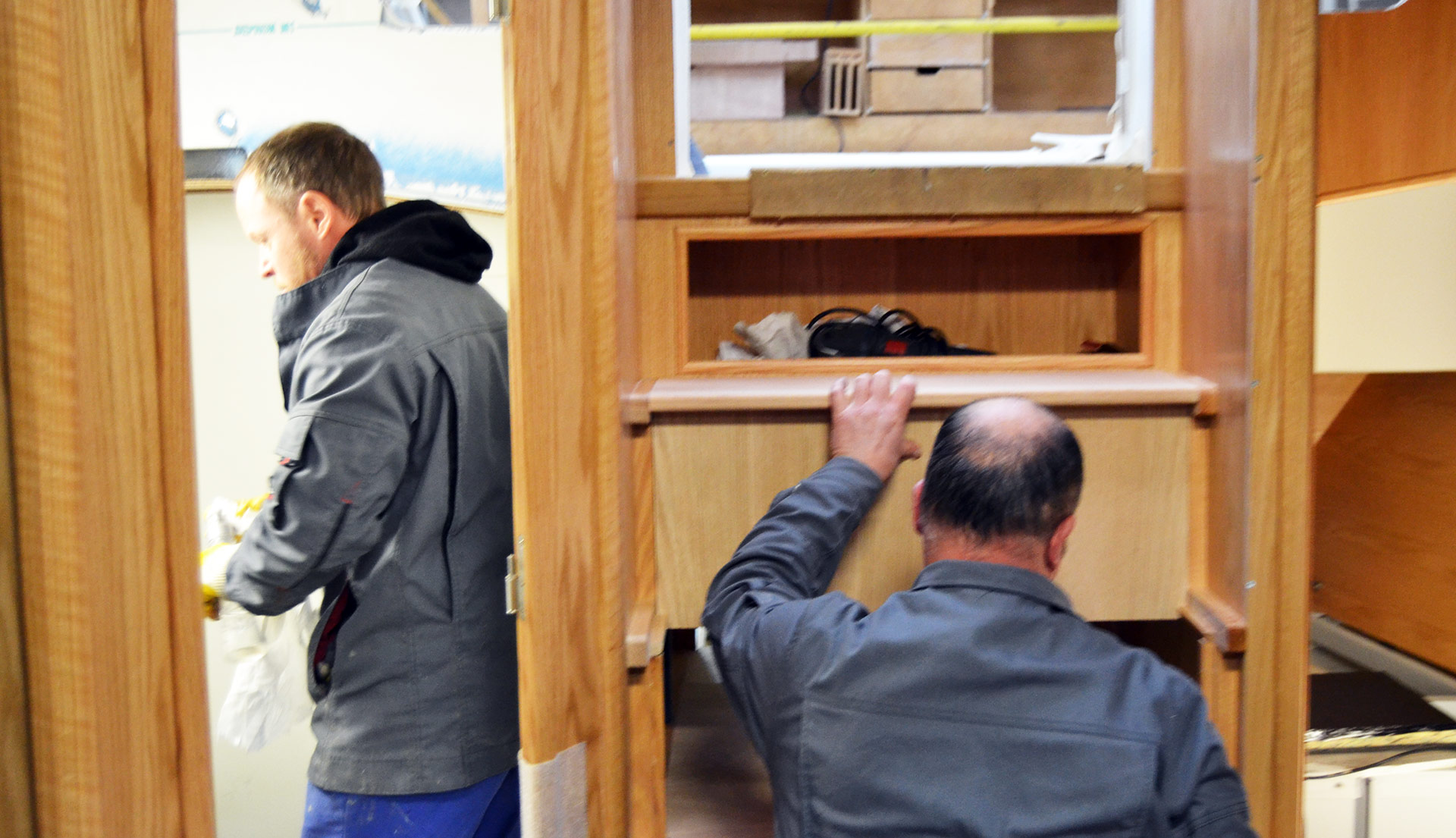
In the end, I think, an owner of such a boat will receive a very individual boat. All the pattern on sawed wood will match each other, the parts are fitted with care and precision and there won´t be any big glitches in the interior fittings. There is also a close monitoring quality-wise ensuring that each day of the building process the outcome of the worker´s efforts are checked and evaluated.
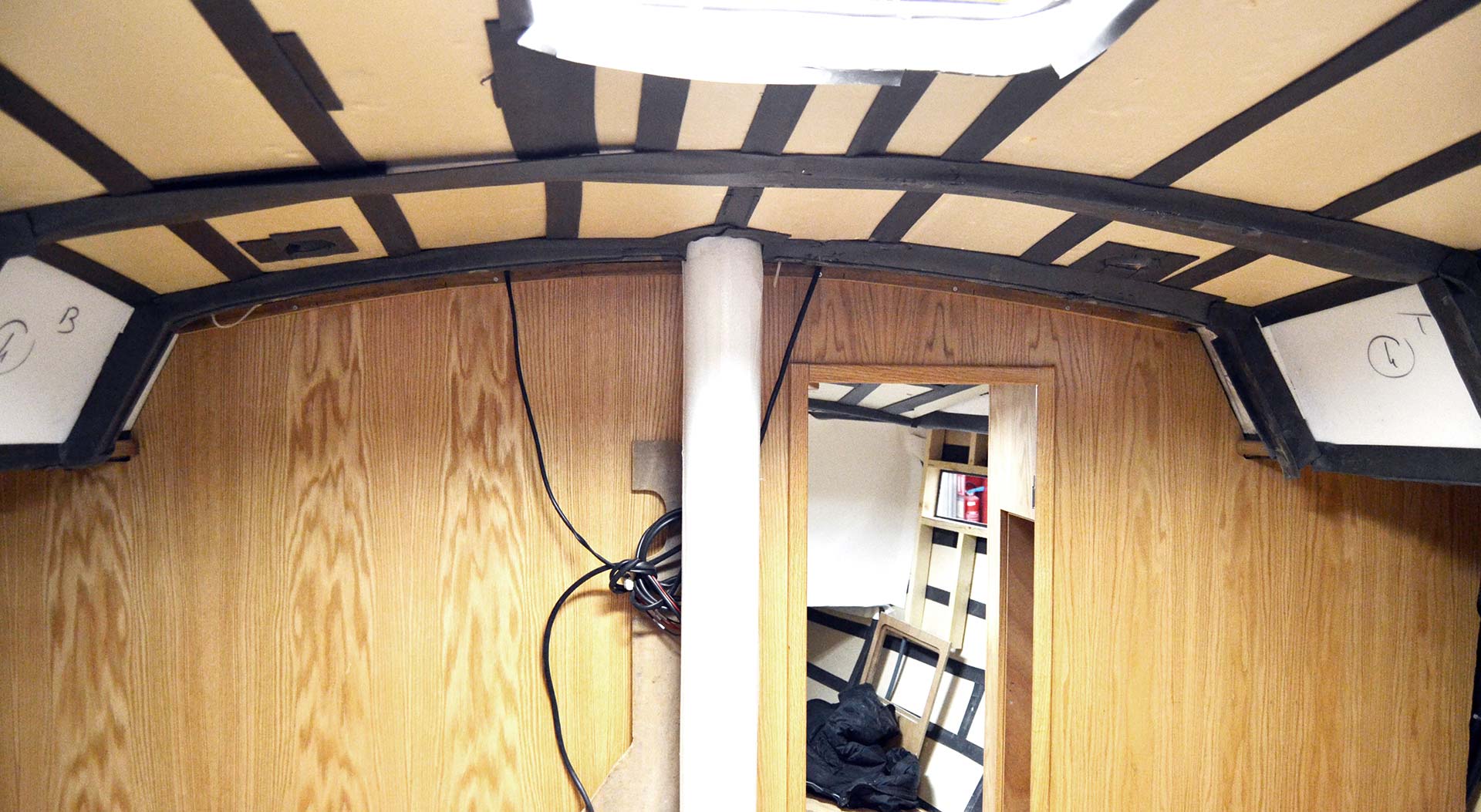
I leave the salon of this Ovni and take a last look back: How adorable the full wooden main bulkhead in American Oak looks! So light, so excitingly patterned. It´s modern and classy at the same time, something that really gives the eyes something to look at. “Now, let´s conclude our tour at the delivery stations where the finished boats are prepared to be handed over to their clients”, suggests Nicolas and we follow him.
Final assembly before delivery: A new Alubat is born
A – not so much finished – Ovni is the first boat we see. The freshly painted surfaces are meticulously covered with strong sheets of corrugated cardboard to protect the surface from the worker´s boots (although everybody wears protection on their feet as well). From the inside I can hear the voices of another 3 to 4 people working on this boat.
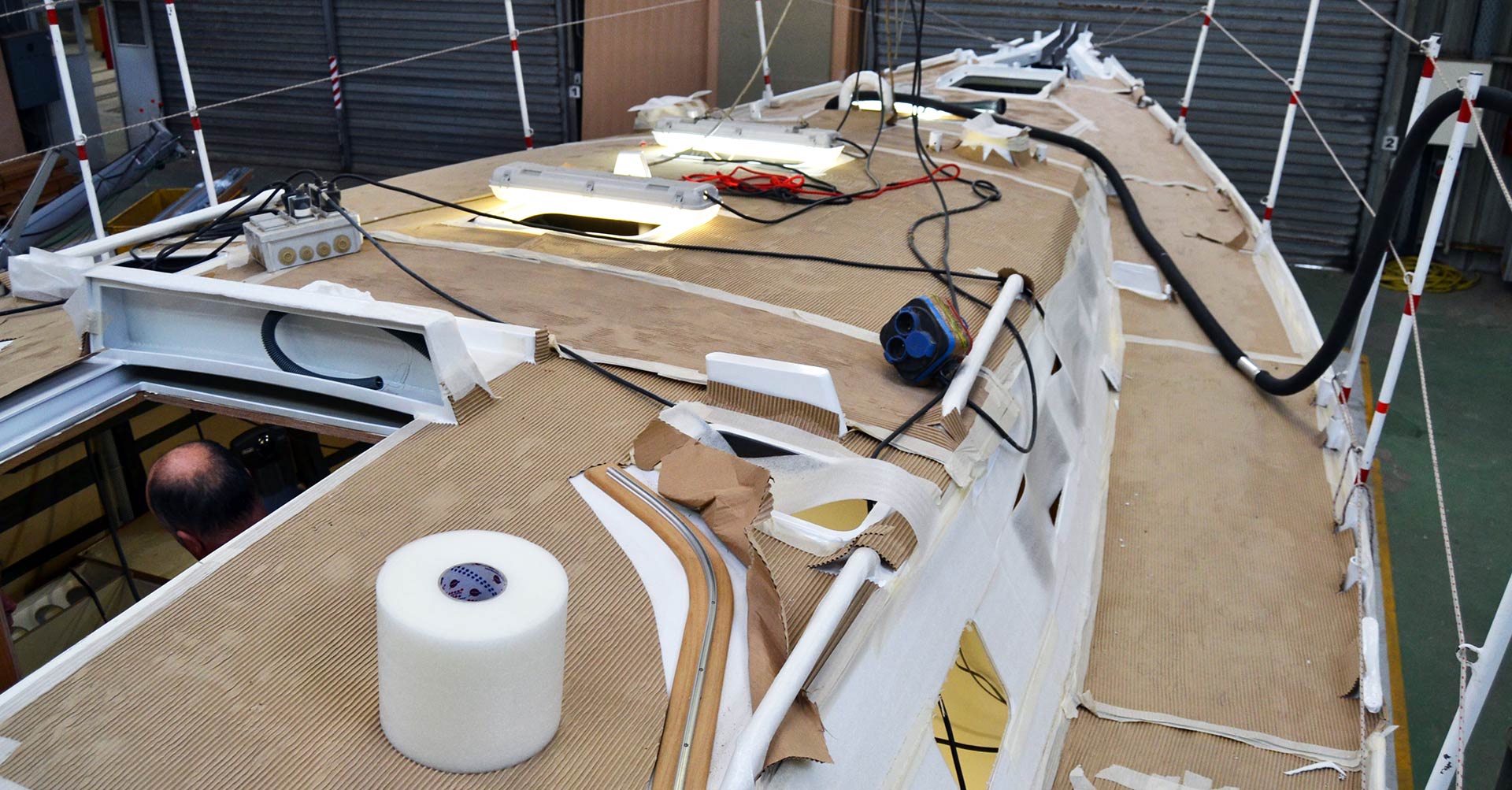
In the cockpit of a finished boat there are some very, very nice details visible: First of all I loved the fact that the benches in the cockpit are not covered with glued Teak panels like it is done with productions yachts. The lids of the lockers are fitted aslope so that water and spray can run off much quicker. To make the benches comforting humans Alubat fits massive Teak battens to create a seating bench. This is very, very nice and should be lasting a long time.
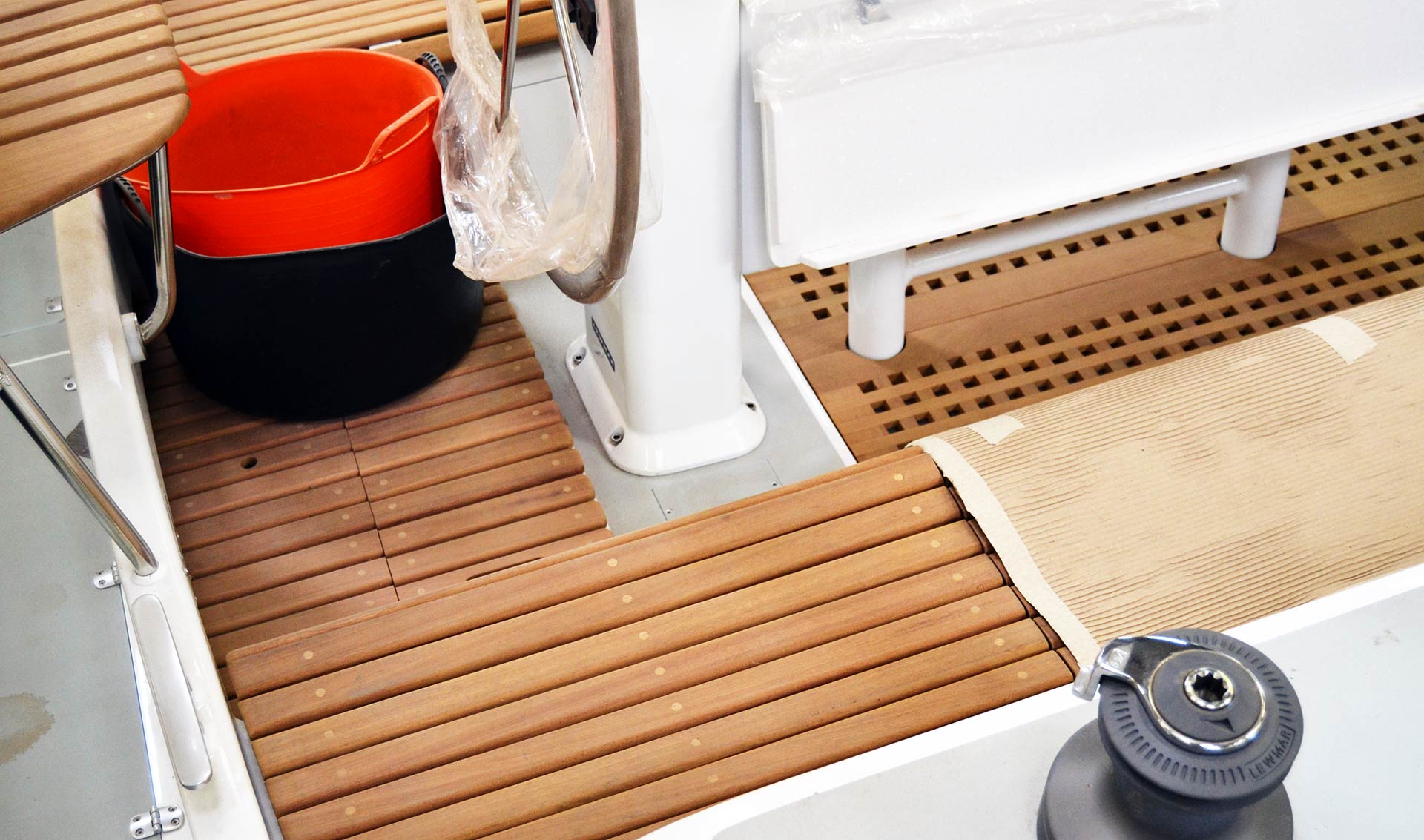
I also loved the massive Teak gratings on the ground floor of the cockpit: When spray or swell should enter the cockpit this classic drainage will empty the cockpit much quicker than ordinary flat cockpits where the water cannot “disappear” underneath a grating. Also, that adds much to the safety of the sailors aboard and furthermore underlines the Alubat-claim to make proper seagoing yachts that can go anywhere.
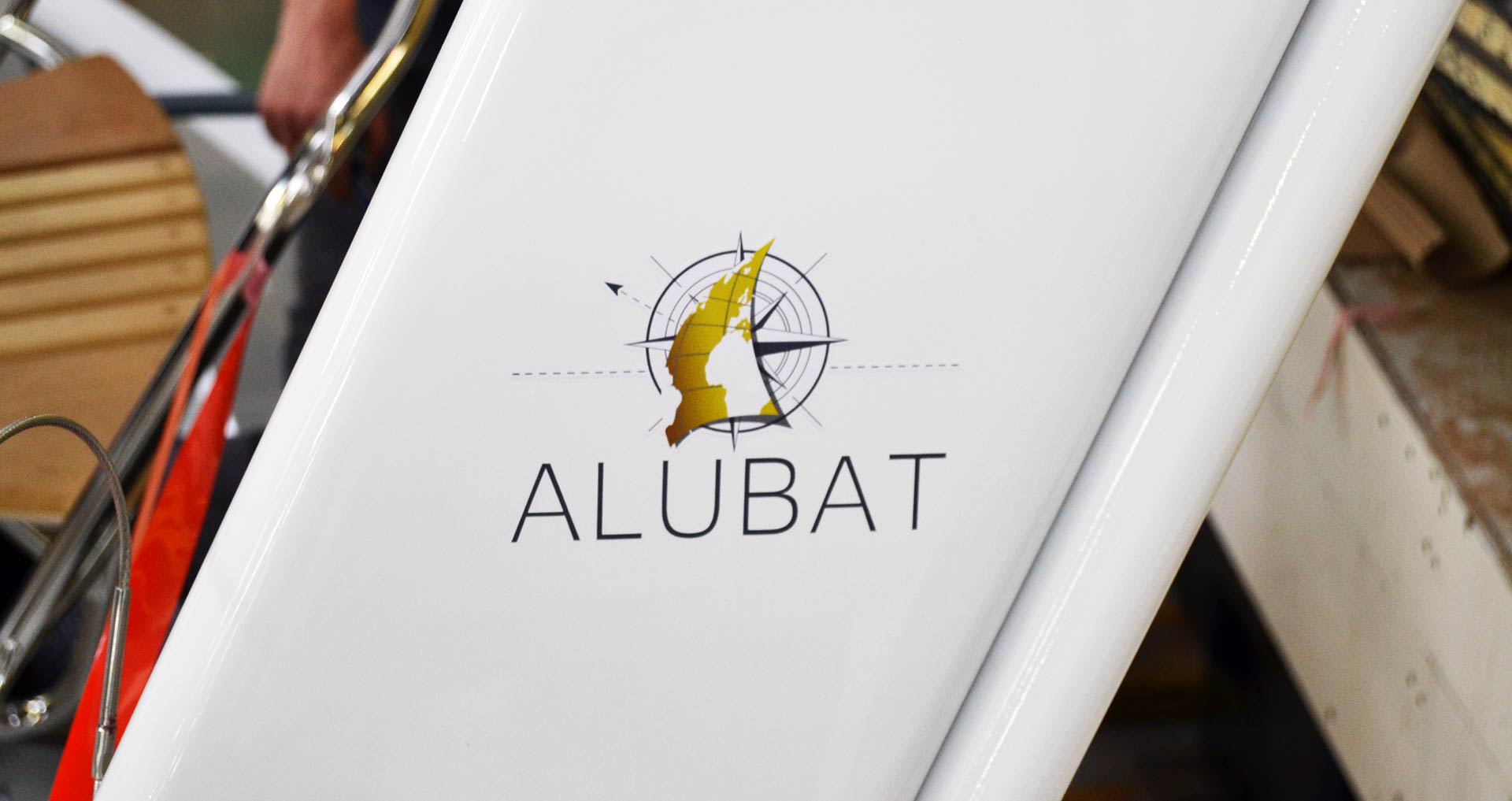
In the end, the boat will be fitted with all the electric and electronic stuff needed, properly tested and all the small parts like cushion, sails, fire extinguishers and alike will be brought aboard. Some protective wrapping added and the boat is ready for delivery. When I was an owner of one of these, I for sure would accept the yard´s offer to have the delivery process be done here at Les Sables because if something goes wrong, the yard is just a stone´s throw away. And be honest: Such a yacht belongs to the high lattitudes and thus into the Atlantic Ocean that is surging its waters just here.
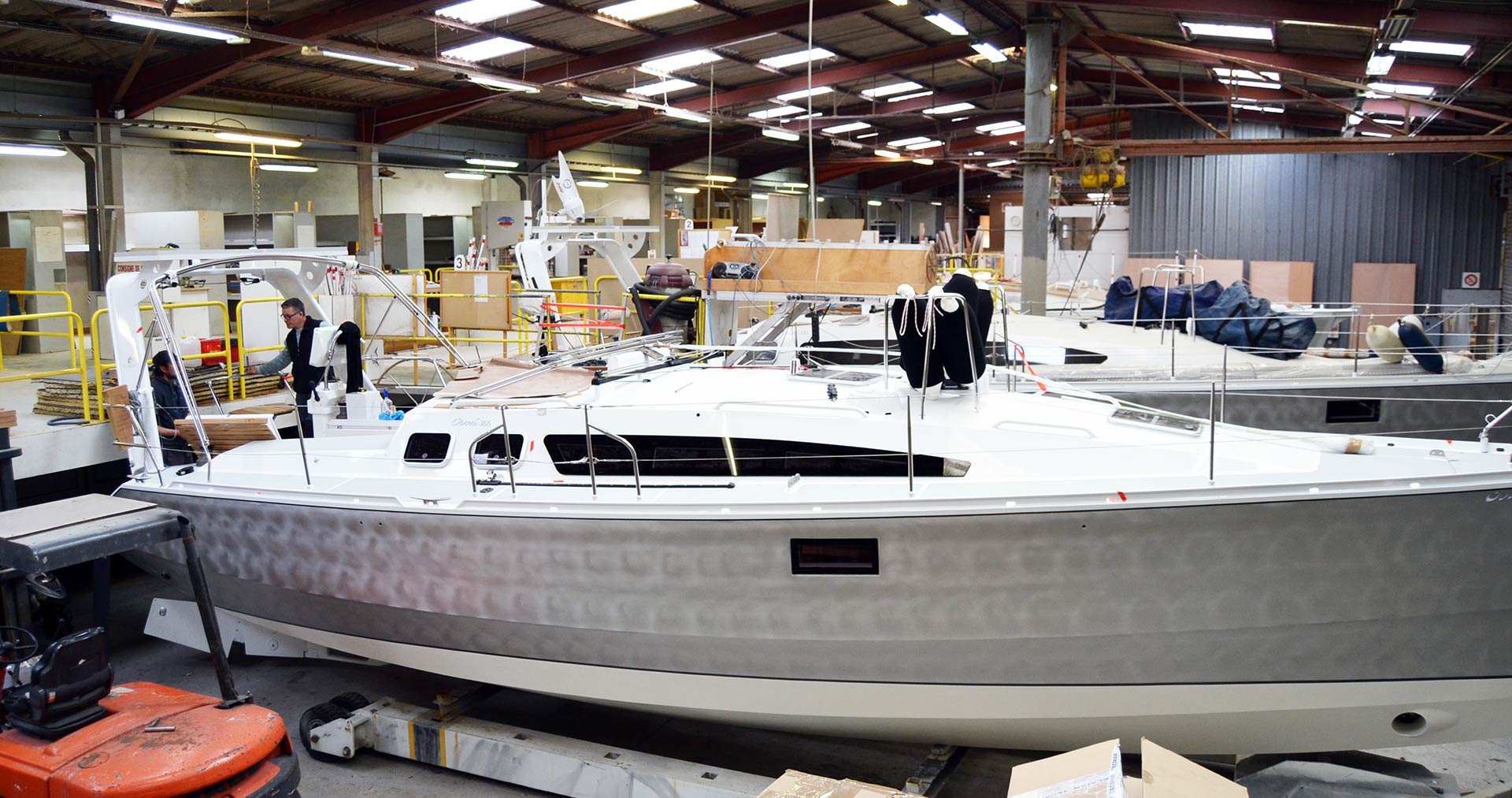
It took me two hours guided by Nicolas to discover what Alubat, this famous French boatbuilder of aluminium yachts, really means: Dedicated people with passion for their products, real handcrafted works from laying a real keel to fitting the last tiny bits of wooden stuff. I thanked Nicolas for granting me this open access to the yard and come home excited and full of joy. But the best thing is … behind one halls I discovered a finished hull of another Cigale 16 which I was free to board and roam, taking dozens of pictures.
So please stay tuned for another upcoming article when I will be talking to Marc Lombard on the very re-design process of this absolutely adorable sailing yacht.
More articles on Alubat and aluminium yachts may be read here:
My favourite aluminium yacht to date: The Alubat Cigale 14
At the Berckemeyer yard in Emden – finest aluminium performance cruisers
What is the perfect yacht for the great loop?