Christmas time is coming nearer and thus I am sure that just a few weeks later and the guys probably would have fitted a red gift ribbon around this thing. I am so excited to see another big item being finished, ready to being crossed off the „to do“-list for my Omega 42. Finally, the massive three tons lead keel has been cast! Look at this beauty:
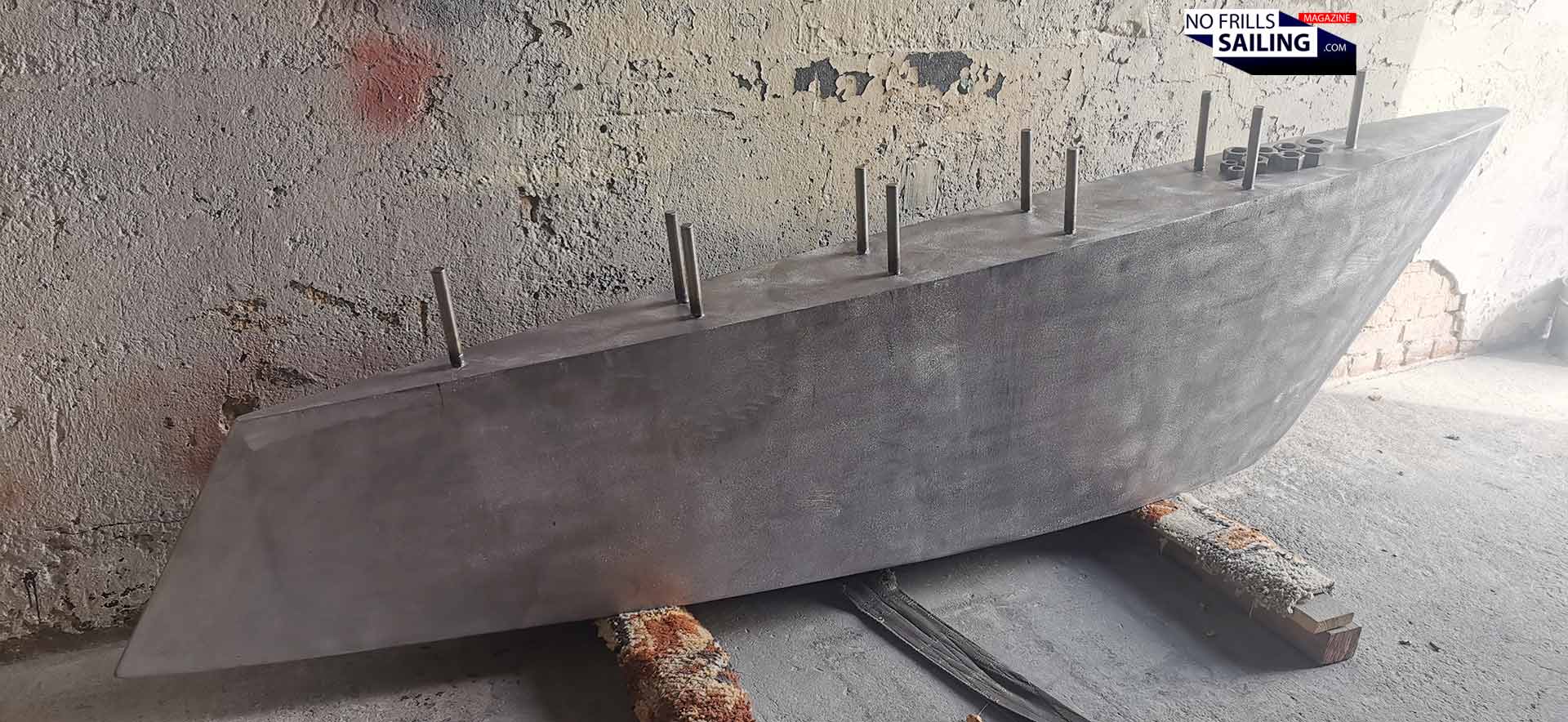
I received an email from my shipyard, with a bit of surprise and astonishment, that the foundry had notified them of the completion of the task. We were a bit thrown off guard by that message because we thought that we could witness the casting process itself, but, apparently, they pulled it off without us. Well. Here we are: ALPHAs keel is born.
Norlin´s ingenious construction
In fact, Peter Norlin´s construction of the Omega 42 in terms of her ballast is very, very interesting and worth taking a closer look at. It´s not the amazing ballast/displacement ratio of the Omega I want to refer to here now. You might already know the backstory of this boat or heard it: Norlin wanted a fast, high performing boat with a very high rigging to catch wind flowing over the small islands of the Swedish Archipelago but also a minimum draft so that he could sail nearest possible to the stones, cutting corners and win races. No, it´s not about that.
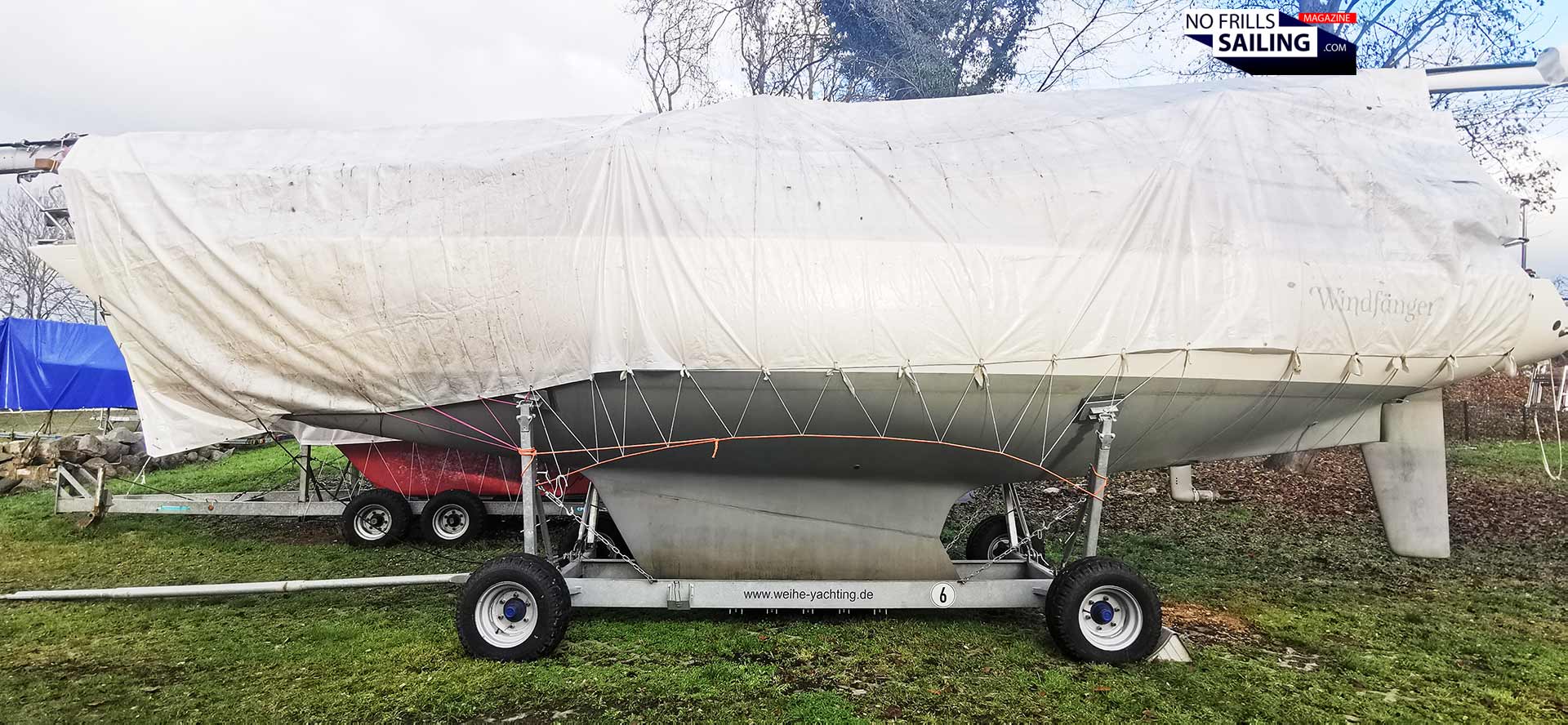
If you look at the picture above, showing ALPHAs sister ship, #001 WINDFAENGER, you might clearly see the thin line marking the border between the GRP hull and the full lead keel. This flange, also shown in the picture of my boat below, is sloped. The flange itself inclines from abaft to the front. This has two reasons. First, yer less important, in this the flange´s surface area is increased in comparison to a flat horizontal flange. By this, the number of keel bolts can be increase and therefore each single bolt a bit relieved from the amount of tension or the weight it has to carry. Much more interesting is the second, most important reason for a sloped flange.
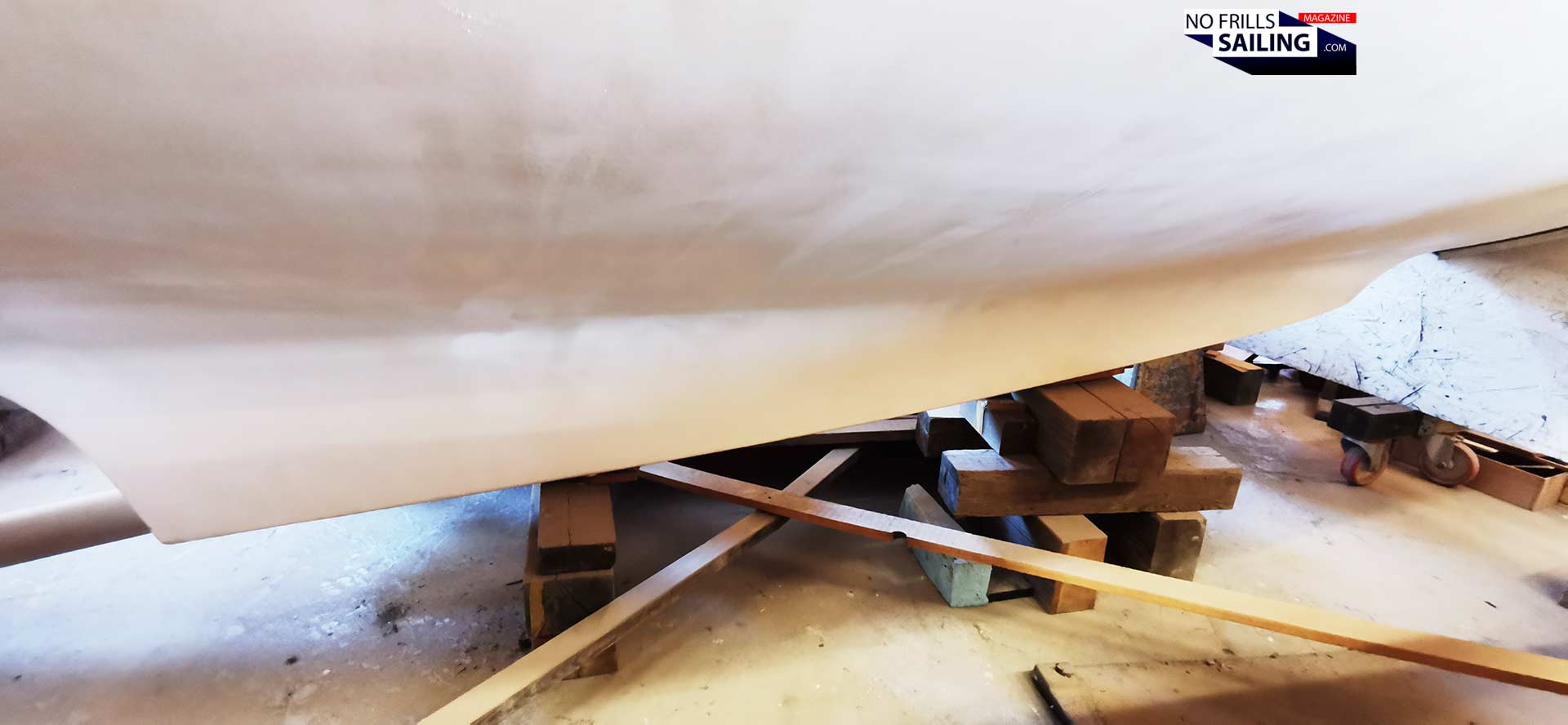
Imagine a grounding or collision with an underwater rock. A sloped flange can take the compression forced from a head-on collision much better and pass the flow of energy on into the flange than a harizontally mounted keel would. Those keels usually snap and bend backwards, ripping off at the front and compressing into the hull at the back. Not so with the Omega 42 – the forces will be distributed evenly into the massive GRP flange and the risk of snapping or, worse, ripping out keel bolts is minimized.
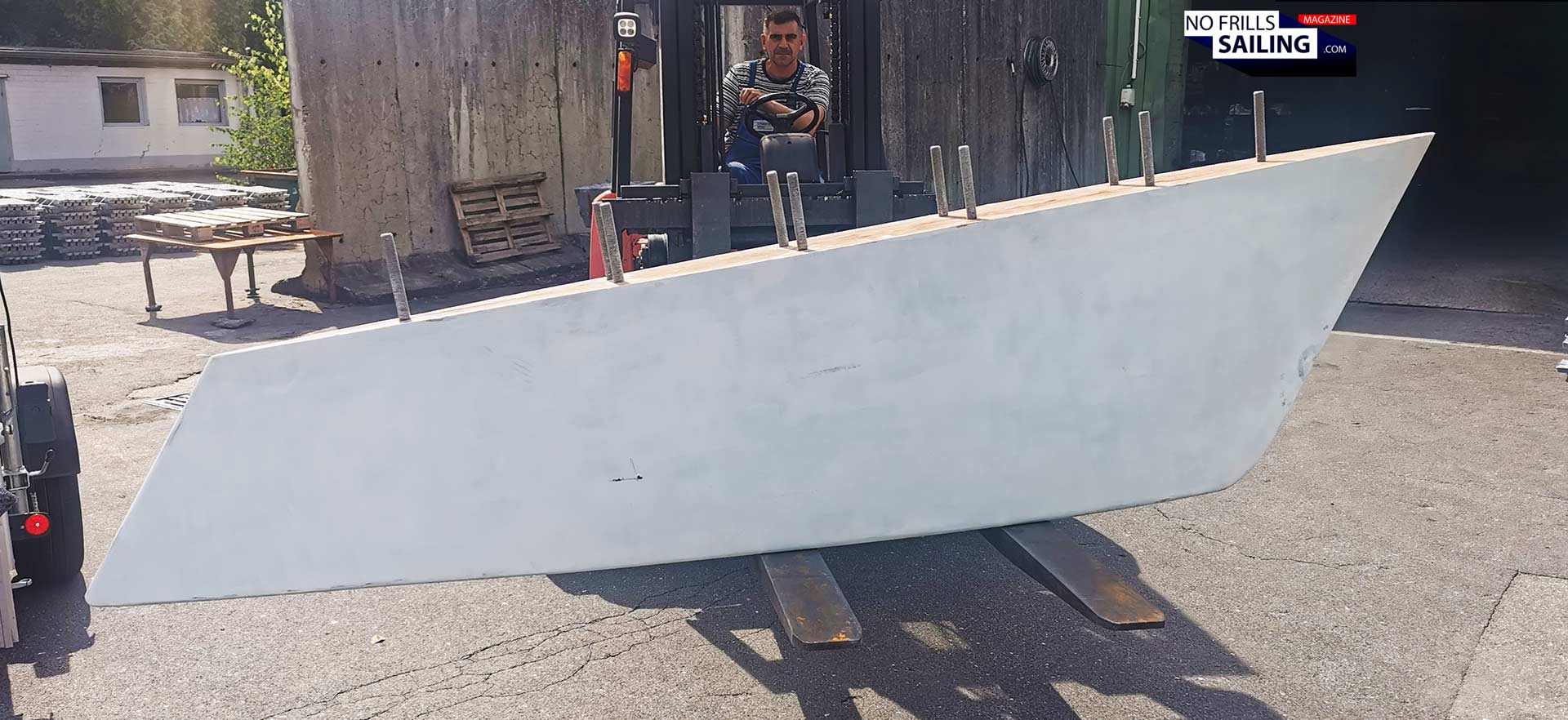
I witnessed a grounding in the Omega 42 a few months ago during the fun and adventurous regatta. Right after the start our skipper miscalculated a bit his distance to the shore – in the midts of a tacking maneuver we glided onto the rising seabed resulting in an abrupt halt. Luckily, it wasn´t a rocky seafloor, instead, some nice grainy sand, but nevertheless – with a fin keel maybe, with a thin performance T-bomb keel, damage would potentially have been much, much worse!
What´s inside a massive lead yacht keel?
So, as I wrote at the start, my idea was to be present when the keel would be cast. I was also keen on showing how the casting mould is made from a special sand. I´ve watched some very interesting documentaries about this ancient handcraft, when huge church bells are being cast. Well, not this time apparently. But as I receive two more images from the foundry, another interesting detail is revealed: The inner life of a keel.

Up to this point I had thought that a „full solid lead keel“ like mine would be … well … full and solid filled with nothing else but lead. This isn´t the case. A meticulously constructed and calculated „keel cage frame“ made of high grade stainless steel. This cage alone is a major item on the invoice for this keel – and a very interesting detail to look at. So, why is there a „cage“ inside the keel? The answer is quite simple: Because of the lead. Lead indeed is one of the heaviest non-radioactive „cheap“ materials on earth and as such predistined to be used for creating heavy leverages, for example in keels. It has a density of 11.3 grams per cubic-centimeter, iron on the other hand „only“ 7.8. One could say that my 3 ton lead keel made of cast iron would weigh in much more, maybe around 3.5 tons. Not good for a boat built to win races, so we stick to lead.

But of course, as with everything, lead has some downsides too. One of these is the relatively low melting temperature of just 327.5 degrees Celsius: It might be good for the foundry´s electricity bill (which is quite through the roof anyway) but having such a „soft“ material means that – just as any steel-concrete structure – the keel needs an inner reinforcement armor, which is this cage. Cast iron keels don´t have such an elaborate construction: With a melting temperature of 1.540 degrees Celsius any steel cage would bend and suffer. Keel bolts in cast iron keels are mostly drilled into the fin, just like a huge screw anchor. Well, this beautiful steel cage is now holding firmly together the precious lead for my boat.
Keel bolts & Co
Everything that is visible now from this cage are the massive bolts. There are four rows of two bolts ovr the complete length of the keel, flanked by one single bolt to either end of the fin itself. You can clearly see that even the bolts are angular relatively to the horizon, bend „backwards“. This will also help to minimize collision damage and make for better force distribution into the hull.
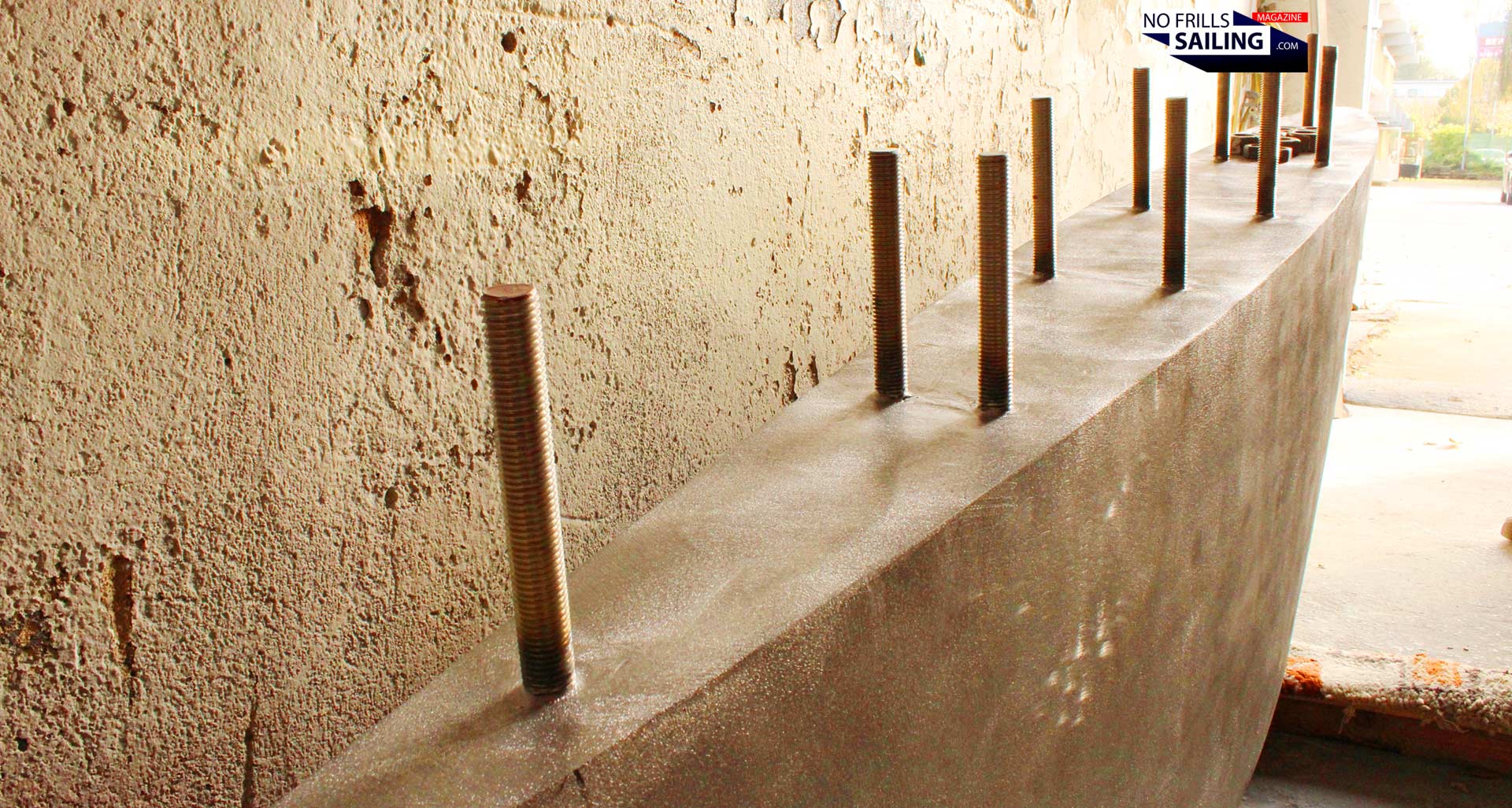
The keel bolts will be secured with massive counterplates and huge nuts, some of which are already laying on top of the keel. Later, when this monster will be mounted to the hull, I promise to be there in person to do a thorough documentation of this venture. I´ve had the pleasure once to observe a keel mounting to a small First 27, but as my shipyard told me, it will be a bit different for my Omega 42.
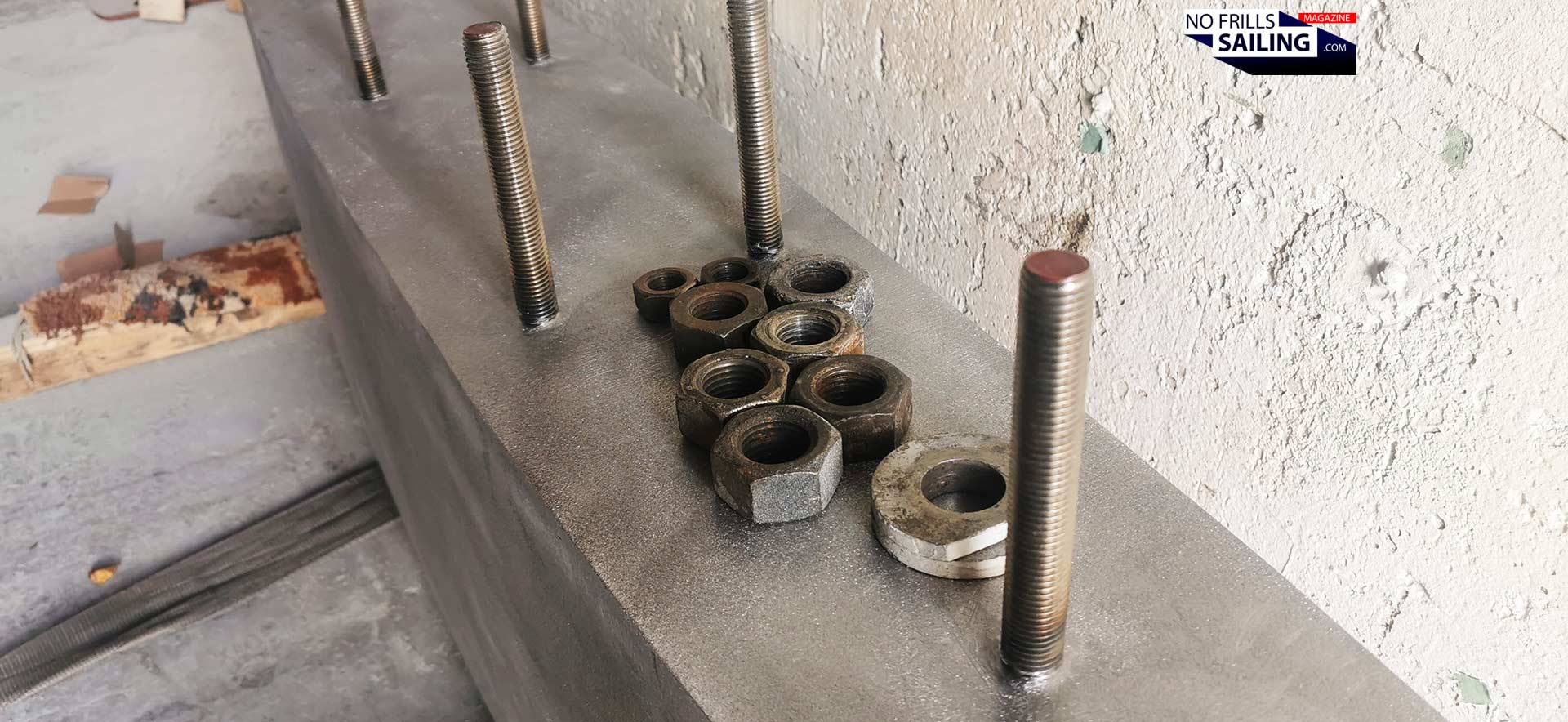
After the raw lead keel will have been delivered to the shipyard, the guys will prepare it: Sanding it to smooth out some dents with filler, the keel will receive a full coat of epoxy resin. In fact, being made of massive, pure lead, corrosion won´t be a thing for the keel, but lead is a heavy metal and thus toxic. According to boatbuilding regulations and also some ecologically sound common sense, we want to close off this toxicity from the living environment of the ocean. After „sealing“ of the keel, it will be kind of glued to the hull in a single, exciting moment. You can´t imagine how I look forward to seeing this!
A bit of sadness …
So, here we are. The keel had been cast and awaits ist transport to the Baltic Sea. I am indeed a bid saddened and also kind of dissappointed about the missed chance to record and document the very casting process, the making and finally crushing of the mould, the heat, the sparks, the smudgy black dusted craftsmen pouring three tons of molten lead … it would have been a truly medieval, deeply touching and moving moment!
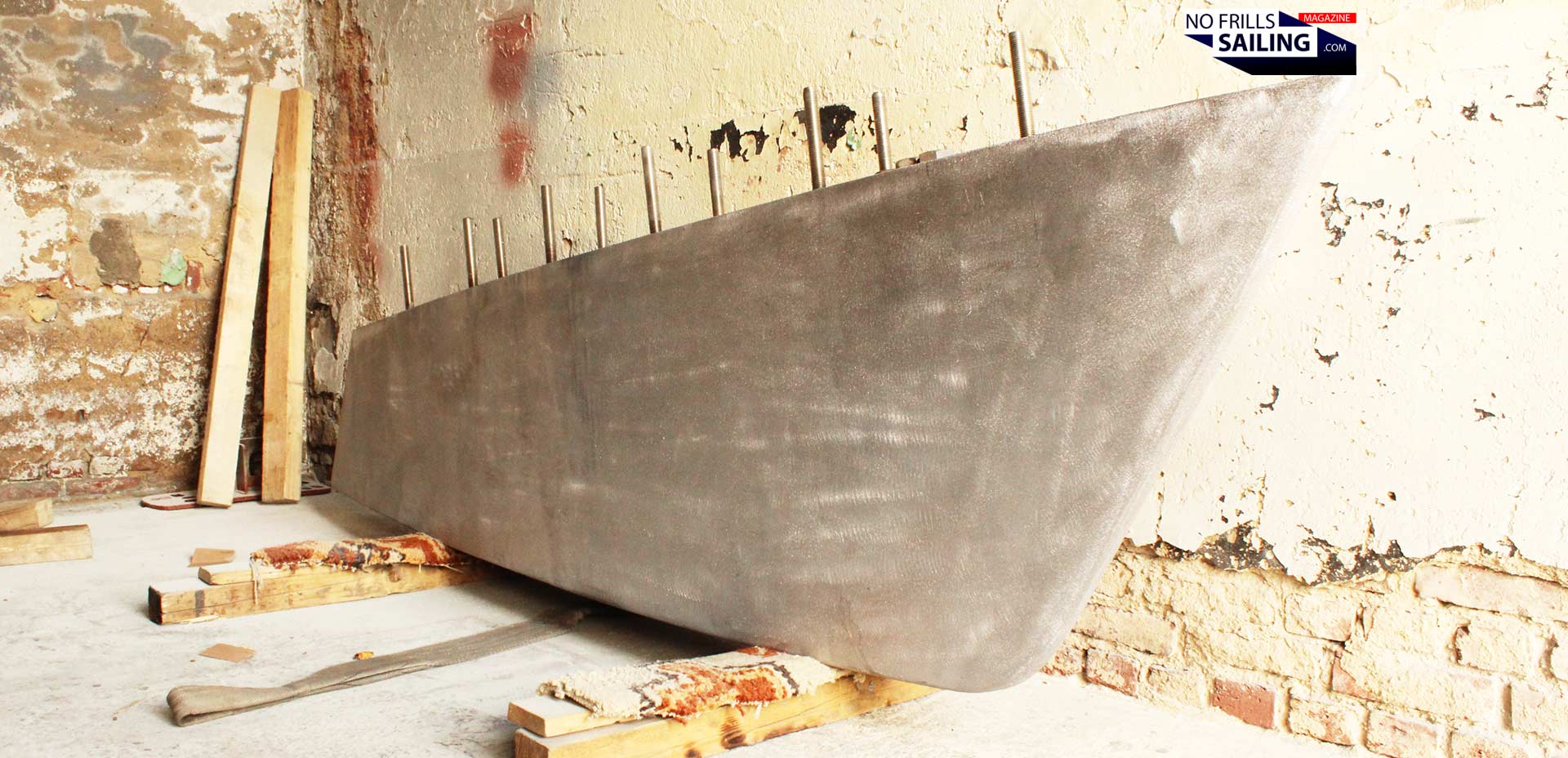
But I also see the reality: Toxic fumes, sparks and maybe splashes of molten metal flying around. Heavy work safety regulations – in the end, we are in over-regulated Germany – and the risk of a crazy fascinated and absolutely freaked out guy like me getting hurt or injured is a pretty darn realistic one. And there´s another thing to keep in mind: Company secrets. Although casting and the principle function of a foundry is pretty clear, I am sure that there are deciding details these people don´t want to get busted by a stupid sailing blog …
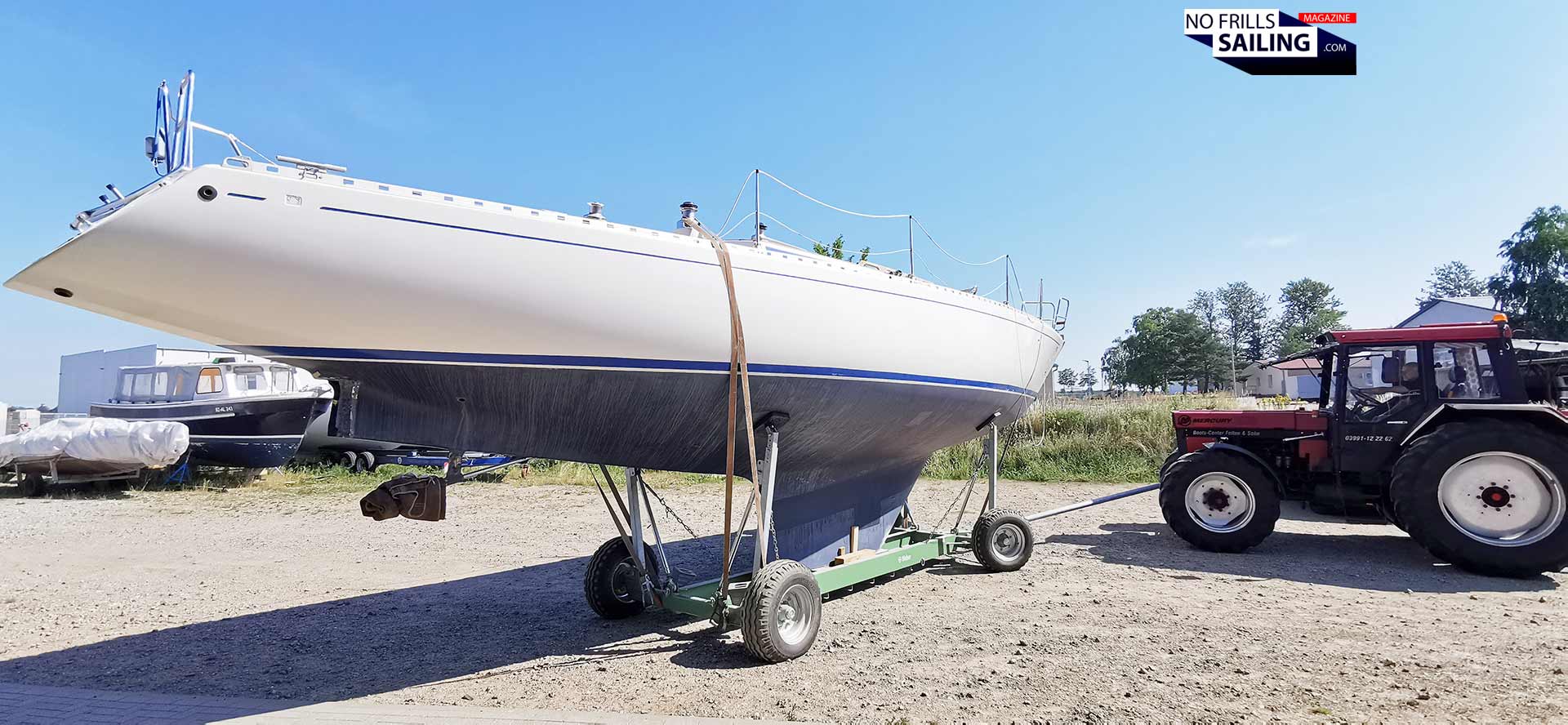
And so I am happy about the biggest pre-Christmas present I´ve ever received in my life. Finally, one of the single biggest spendings of the boat is done, about to being crossed off the list. I can´t wait to see it attached to the hull so that my ALPHA will look like this wonderful classic Omega 42 as seen above: One of the most stunningly beautiful classic sailboats ever to be constructed, with its wonderfully shaped keel as a dominant visual signature.
You might also like to read these related articles:
All building progress-articles
My first sailboat race in the Omega 42, parts 1 and 2
Zero risko of keel failure? Kraken Yacht´s approach.