The French Vendeé is the true heart of sailing for France the least, maybe for the whole world. The big production boat brands have not only their headquarters and shipyards here, but also the smaller brands. Therefore, many other factories and production sites of countless different suppliers, parts manufacturers and bureaus are to be found here, from standard parts to highly specialized high-tech makers. One of these is Seldén mast and spars, renown Swedish rigging producer.
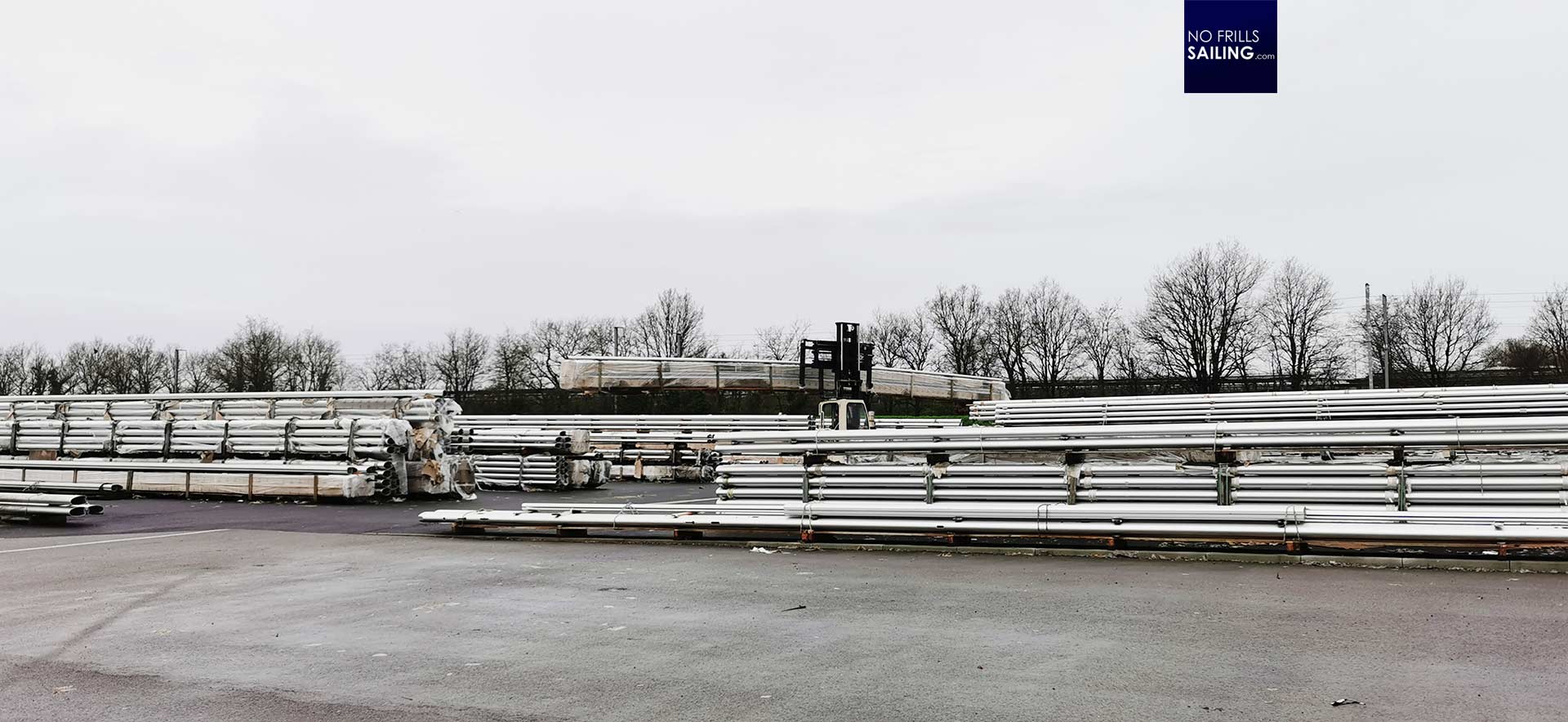
Literally surrounded by Beneteau on three sides, it was only a question of time for me to pay a visit to this site. Meeting the manager of Le Poiré factory during Boot Duesseldorf, endorsed by the German Seldén-representative, we arranged for a meeting since I am regularly around for my customers and prospect clients. It was a rainy, grey morning when I entered the factory site, parked my car and was astonished to see hundreds, if not more, masts neatly arranged in the outer storage area, forklifts bustling around. Avid hustle and bustle, a good sign.
A warm welcome by Leon Lampert
Inside the administration building the manager of the site, Leon Lampert, gave me a warm welcome. The Dutch born specialist is with the brand since more than 30 years now, having managed Seldén production facilities in the UK before being appointed to the then new Vendeé production site some 17 years ago. This guy knows everything about rigging, masts and spars as well as the colorful world of boat builders, from the big names to the small yard, from series production boats to custom one-offs.
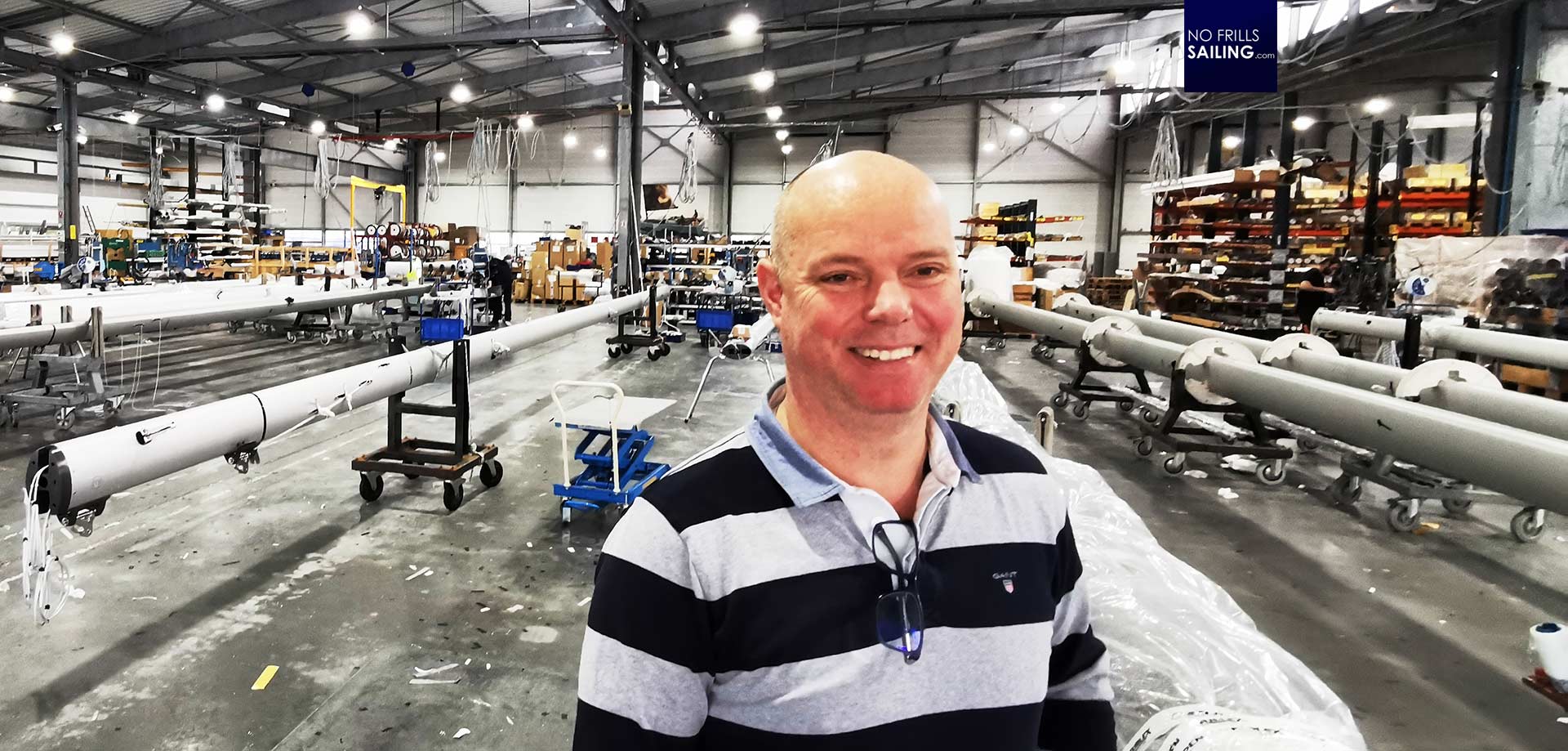
We start the tour by loosely talking about the current situation of the industry, about supplyer´s and buyer´s policies, different brands and projects. Basically, in my world at least, there are two brands of rigging producers, which are Sparcraft and, you guessed it, Seldén. We talk about market share and some trends, challenges of the present day and possible future developments. It is indeed highly interesting to get to know his perspective as a principal supplier. In a nutshell: No crisis at all, high production rates and a good order situation.
The production of a mast
This positive tenor is reflected by the bustling activity in the big production hall we enter after finishing our welcome coffee. Here at the Vendeé production site some many dozens of people are employed. Many of them aren´t around right now as I arrived during coffee break – at last we are in France and some rituals are sacred – but I can see dozens of masts in different stages of production, which is a good thing since Leon is able to show those steps to me in detail.
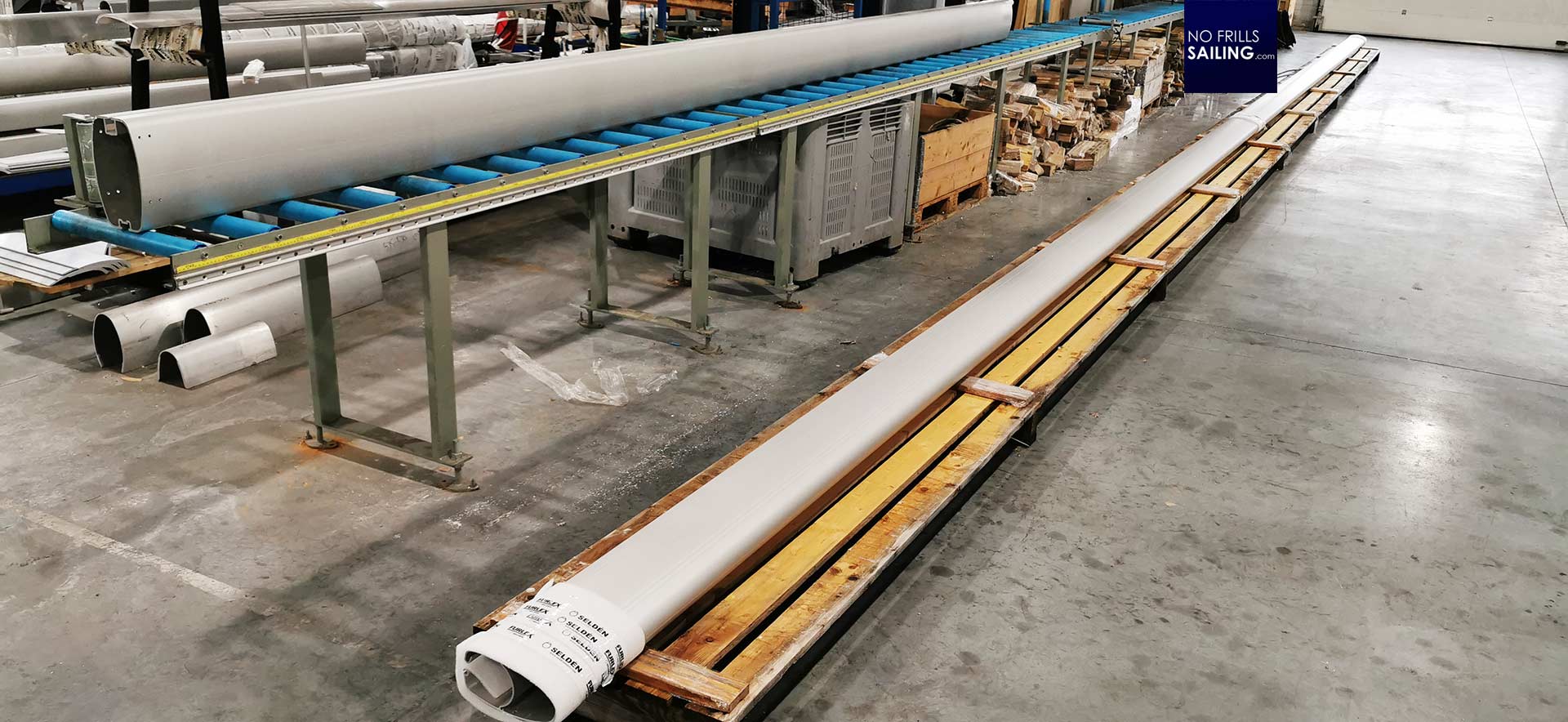
The raw masts, cut to a fitting length according to the sail plan of each boat, first arrive to the CNC-station. This is basically a laser guided computer controlling a 5-axis multi-tool for milling, drilling and sawing. The engineer has to put in the right program containing all the positions, forms and sizes of each hole and opening of the mast and “just” press a button. The machine basically works completely automatic and independent.
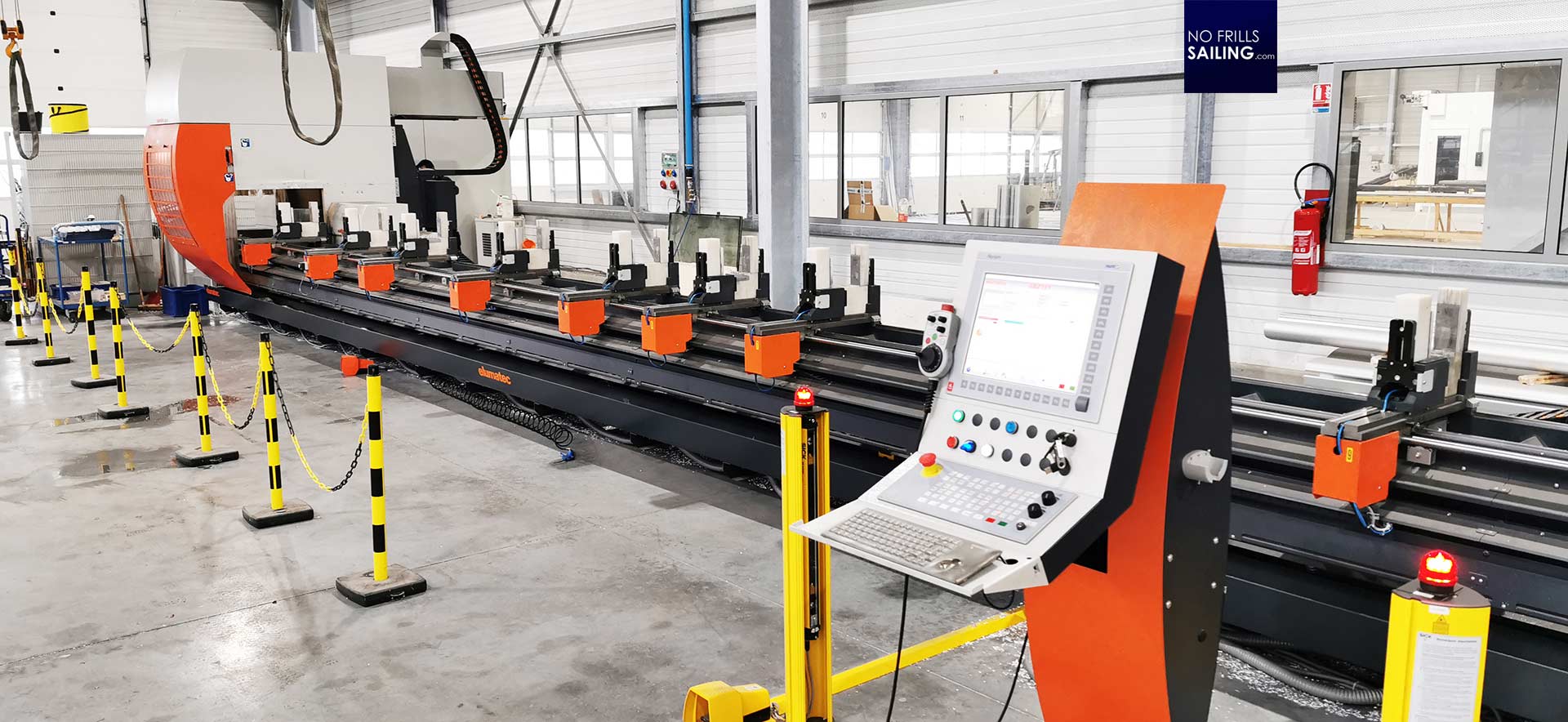
Of course, these programs need to be “written” at first. For many production boats and boat types the rigging is the same. Say for the Sun Odyssey you just have to write the program one single time – and as long as the boat is in production, many dozens and hundreds of masts can be produced with ease. This not only saves labor cost but also insures a constantly high level of finishing quality and precision. The laser-computer-robot has no tolerance, one mast is similar to the other.
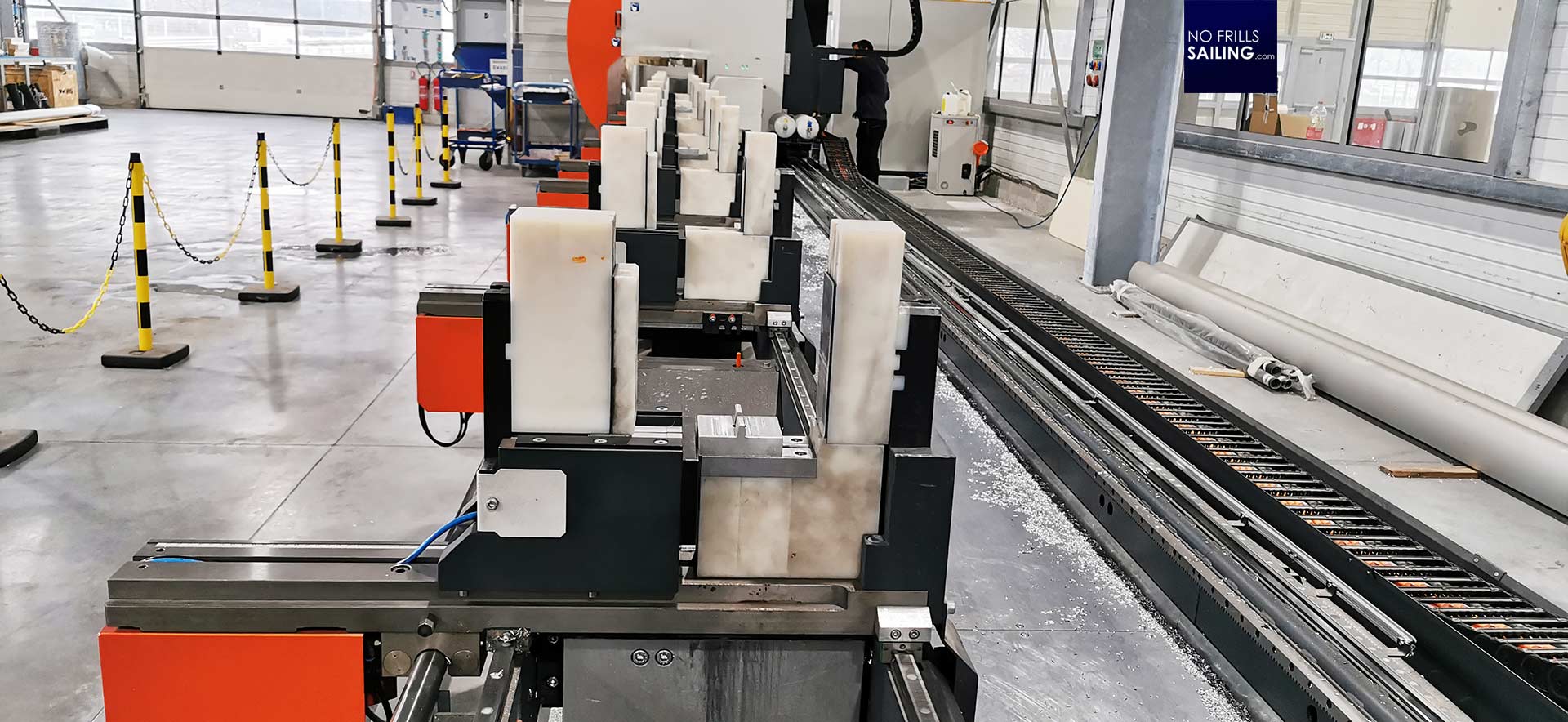
The machine looks like one of these experimental railgun weapons. I ask Leon what the maximum length for a mast is that can be produced here. Masts in one piece of maximum 20 meters can be proceeded here in this factory. If keel-stepped, even longer. The longest mast he remembers was 34 meters, which is awe-inspiring.
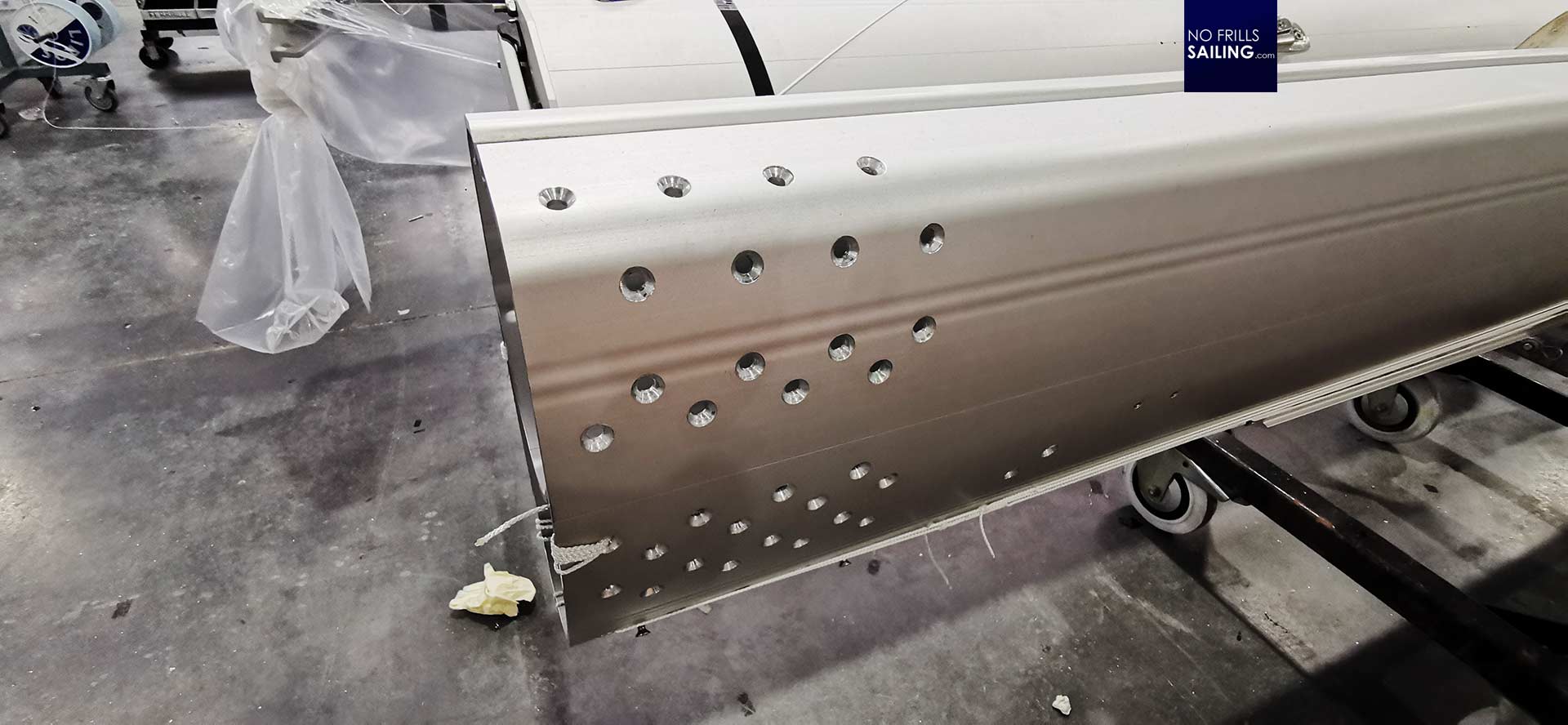
The outcome of the machine´s work is spotless. Done by hand, no matter how good and elaborate the people work, there would surely be some offset at least. As those inaccuracies can lead to deviations, which sum up, it can compromise the rigging as a whole. “Automation where it makes sense is something, Seldén is really interest in implementing”, Leon confirms: “It is surely not about saving money by preferring to employ a computer. We like to “free” our people from strenuous, boring and repetitive work-steps and from tasks that quickly drain the guys´ alertness, accuracy and awareness. This is a perfect example where automation is a win-win.”
Series production – custom one-off
When the raw mast has been drilled, cut and prepared, it enters the next production step, which is the fitting. To be able to do so, the workers need all parts and equipment to be fitted in the first place: If you have read my article about the new Seldén mast for my own new boat, you have seen that the list of pieces to be fitted is literally four pages long!
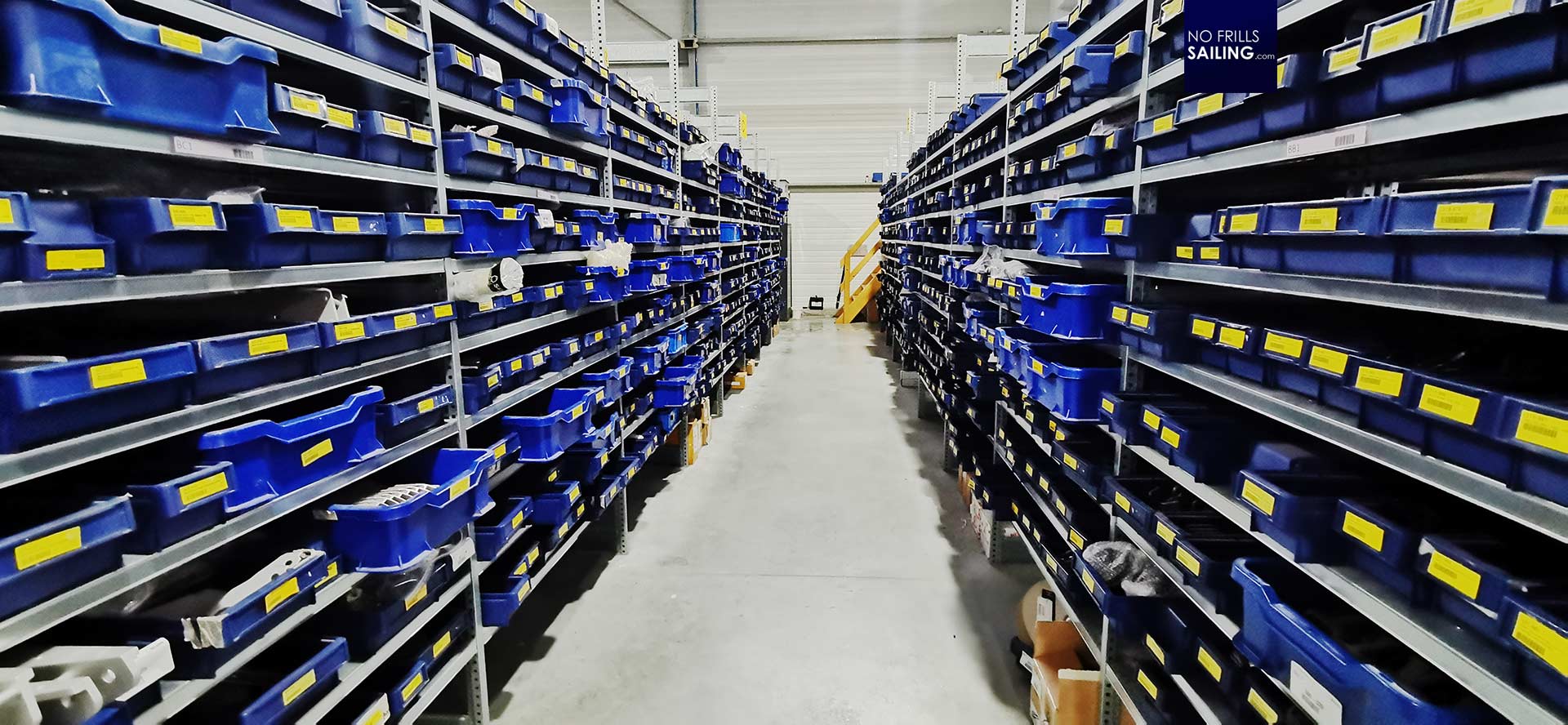
The indoor small parts-storage of the factory contains of a dozen or so rows of racks. Easily 25 meters long and almost three meters high, this is an impressive collection of any part, nut, bolt, stainless-steel fitting, cars and stuff you can imagine. As Leon recalls, the storage contains of no less than 65.000 individual parts. Of which a still staggering number of some 8.000 parts are the currently “active” set of pieces in use for the products. The logistics of this storage must be an art. Or a nightmare, depending on which side you look at it.
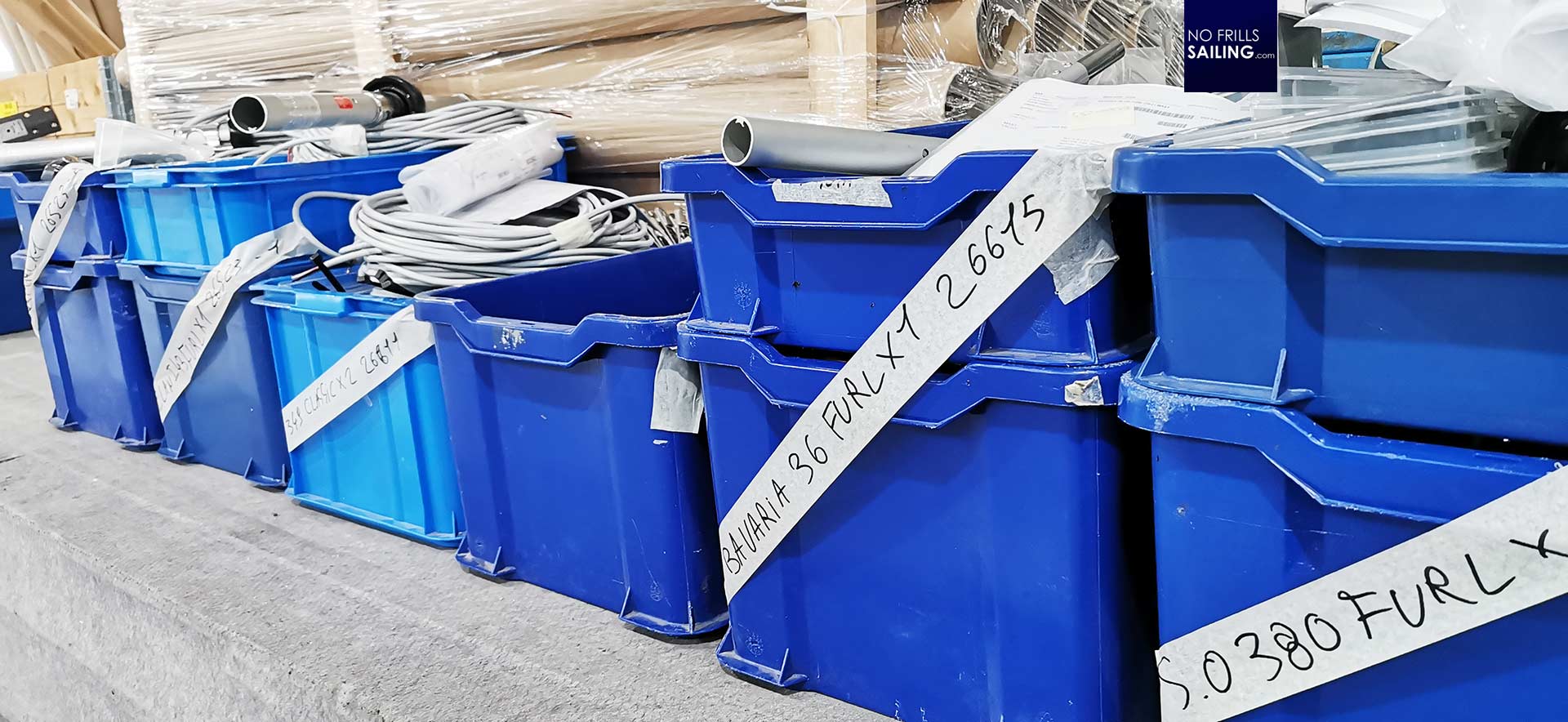
According to a product list, a storage-worker prepares a blue basket that contains all parts needed for the fitters to “build” the mast. Those baskets are labelled with the boat and type and prepared to be taken down the hallway to the mast-fitting area. I read “Bavaria 36”, “Jeanneau Sun Odyssey 380” or “Oceanis 34.1” – the list of brands and clients for Seldén comprises almost all brands and boat builders currently active on the boating market.
Fitting a mast
The fitting area uses to be a place where many people spray around, walking up and down the masts. As I mentioned, it was very quiet that day as the coffee break seems to be a most welcome and holy institution. But that gave me the chance to really come close and ask all question I liked – without bothering the workers and stand in their way.

Eight to ten masts at one time can be fitted in this area. The guys will not just mount all steel-parts, but also put in the electric wire for the navigation lights, VHF coax cables and pilot lines for the running rigging. Also, all steel parts are put on the mast and most of the surplus fittings, if ordered, like deck light or such.
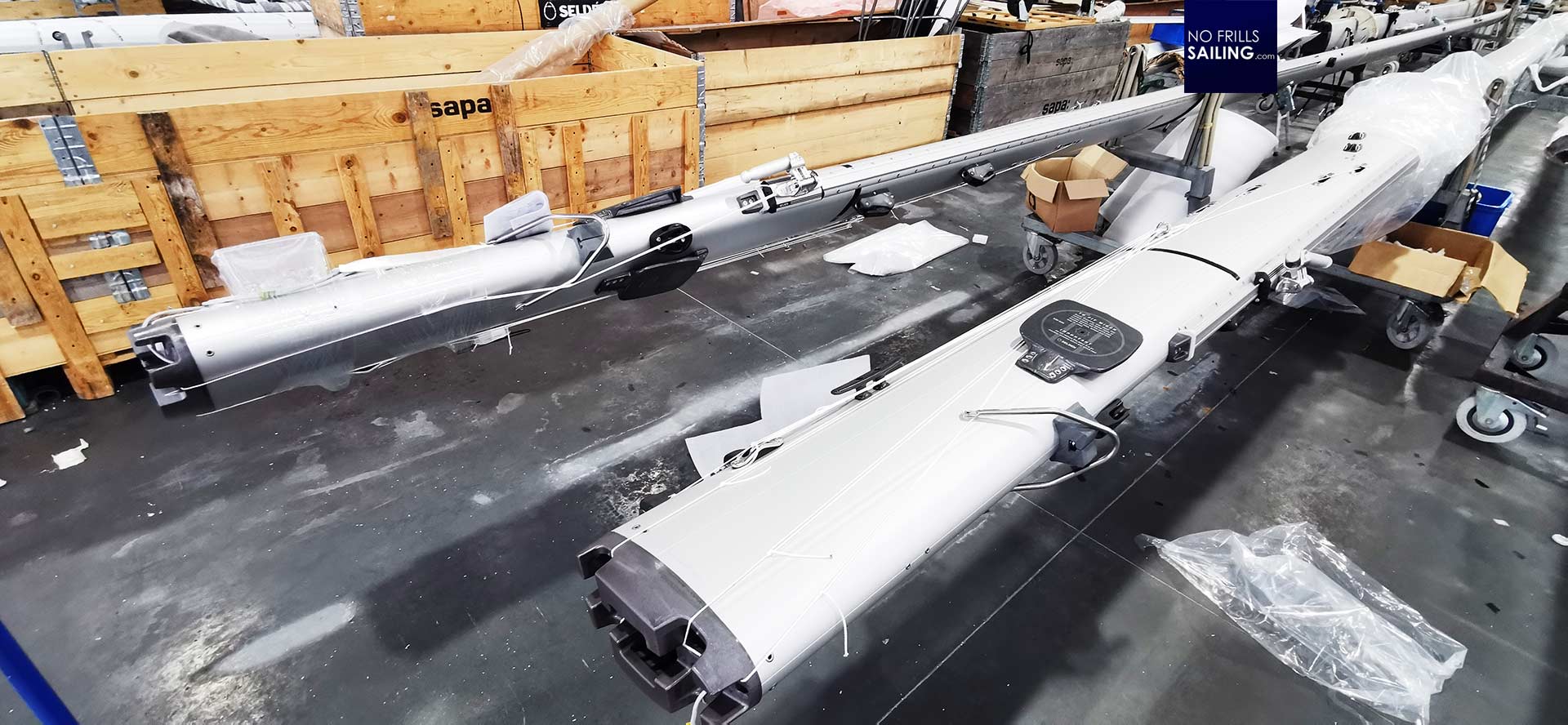
In this, I understand, that each mast still is almost 100 per cent a work of handcraft. This is something I didn´t knew, which partially is a shame since I am a frequent visitor to shipyards in all over Europe. I regularly teach my prospects and clients the lesson, that a boat is made by many, many hands – and almost no robots. Apparently, this is the same for the masts! But Seldén, especially the factory here in France, can do even more.
From standard to sheer artwork
We roam the finished masts and Leon points to a very big piece. This is a masterpiece and true showcase of what is possible nowadays in rigging. It´s a mast for a Kraken 58, consisting of three-parts. This mast in itself is a special one-off with many gadgets which are breathtaking.
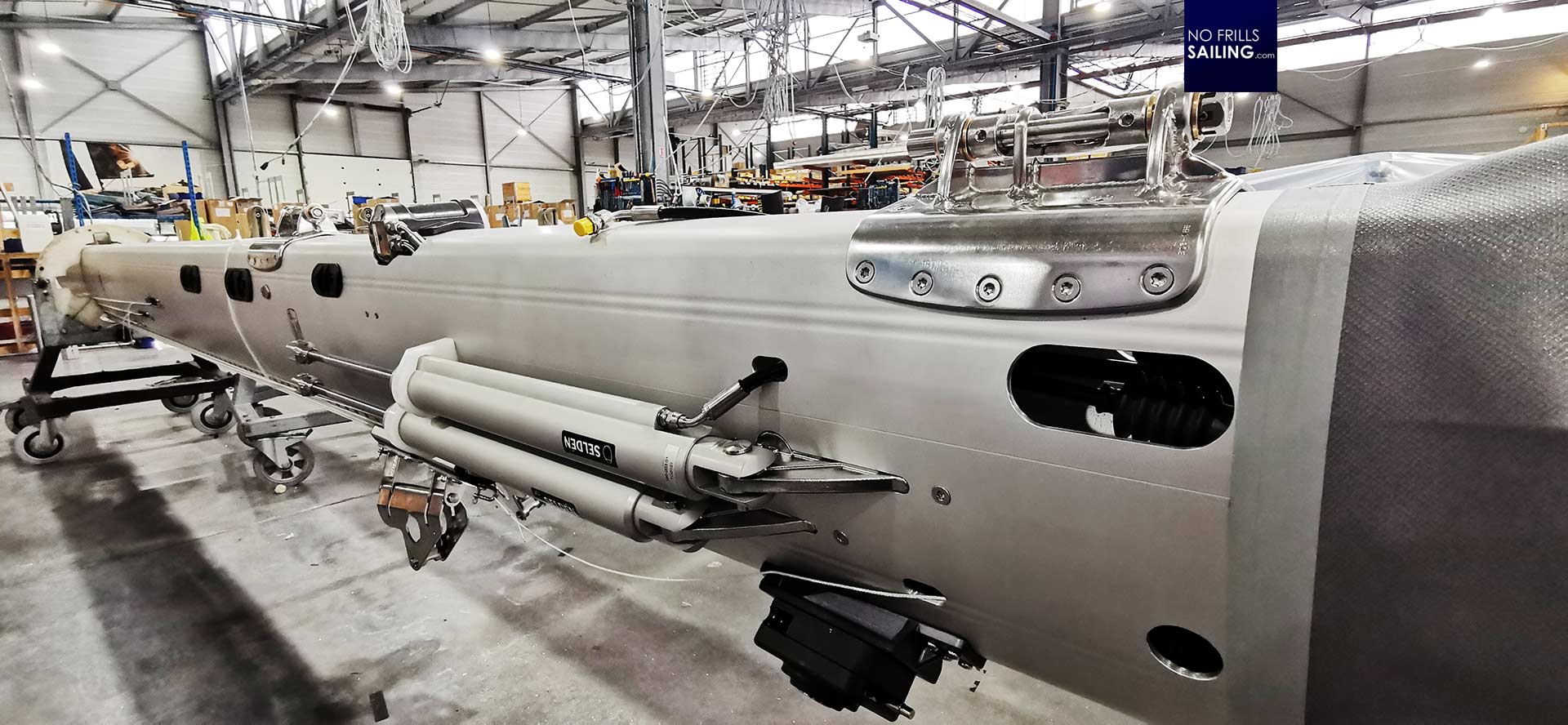
Hydraulic in-mast furling is one feature. Leon shows the thick hydraulic pipes powering the furling mechanism inside the aluminium mast. To either sides, two equally impressive hydraulic pumps are located: Halyard tensioners. It´s truly a wonderful, massive yet somehow fragile machine.
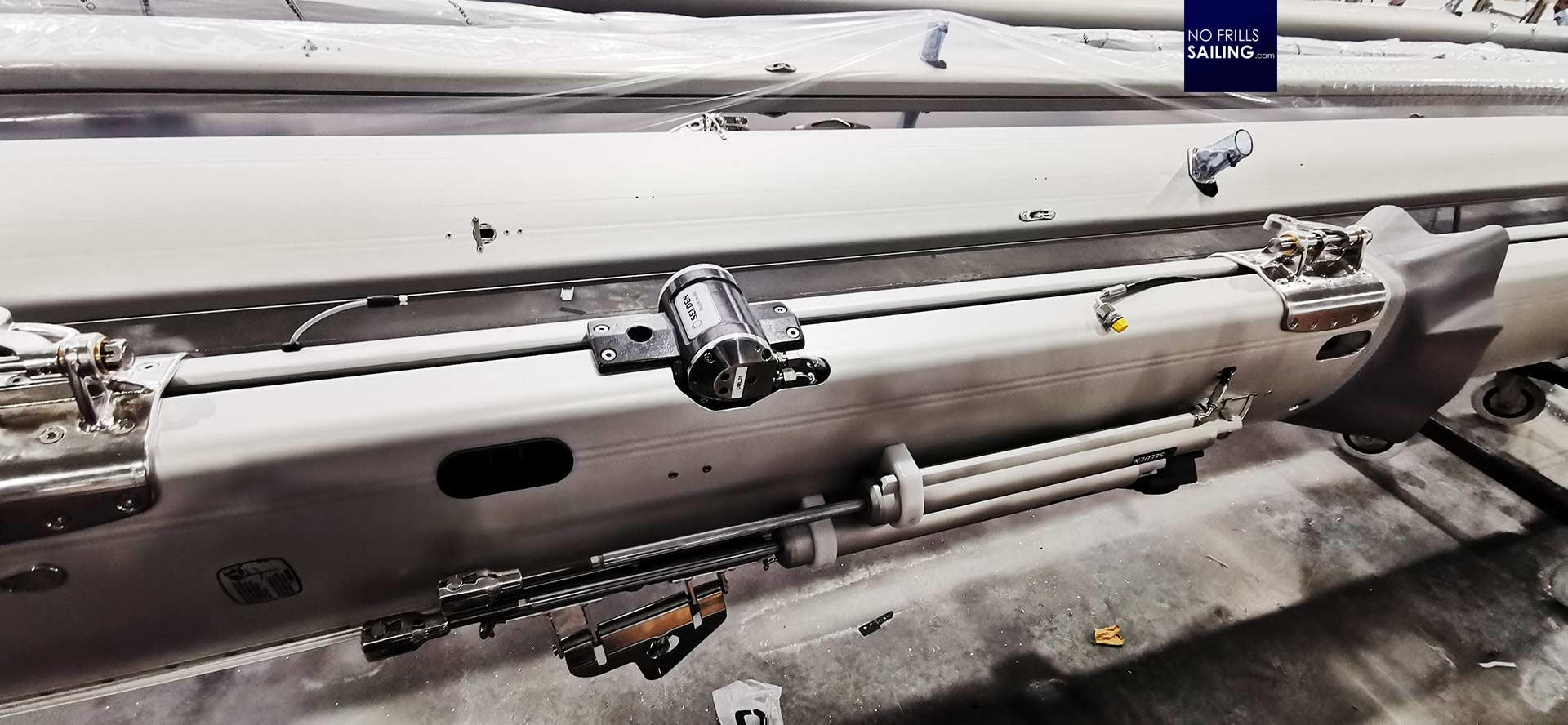
On the front side of the Kraken mast, no less than two Spinnaker boom cars are mounted, this boat certainly is for somebody who wants to go long haul oceanic distances. As Leon points out, the ration between series production masts, like those hundreds of riggings prepared for the big brands like Jeanneau or Hanse, and one-off special orders is nearly 50:50. “In the end, your mast is one of those one-offs too, Lars”, he says.
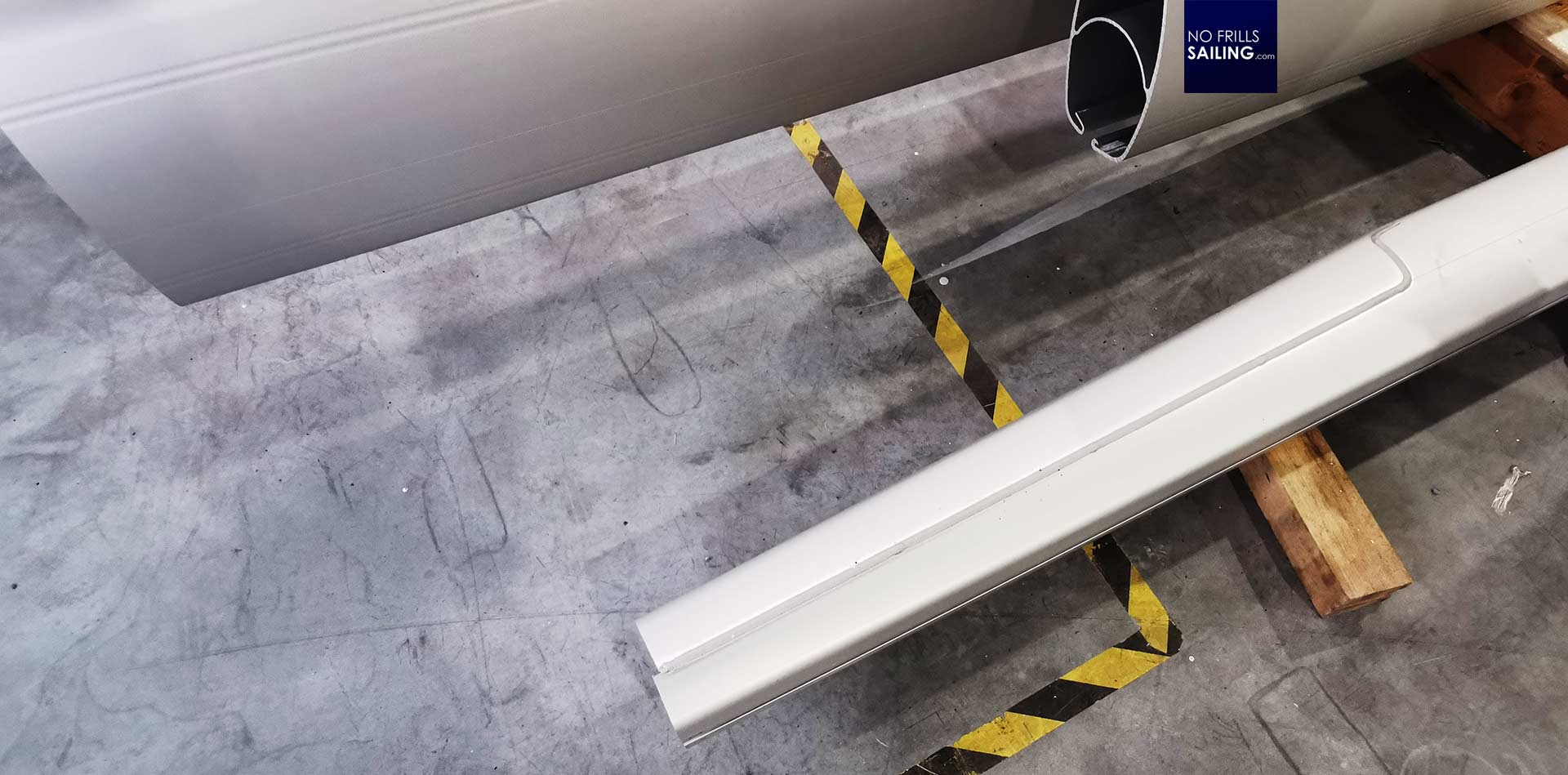
Seldén can realize almost all wishes for the clients: For example the individual style for tapered masts can be adjusted to the wishes and needs of the clients. Usually, the tapered part used to be very long to create a very subtle, long bent shape for the mast. Somehow, in the last years, owners fancy shorter, more aggressive tapered mast tops, Leon explains. Seldén can realize any wish. My Omega 42-mast is also tapered, I shall check it … note to myself.
Different parts, different specialized steps
A mast generally consists of more parts we tend to overlook sometimes. Leon walks me to another area of the big production hall. Another high storage closes off this part from the rest of the production. This is where the spraders are made. Seldén holds all sizes of spreaders as brutes at any time. According to the size of the mast, only a few spreader sizes can then be used.
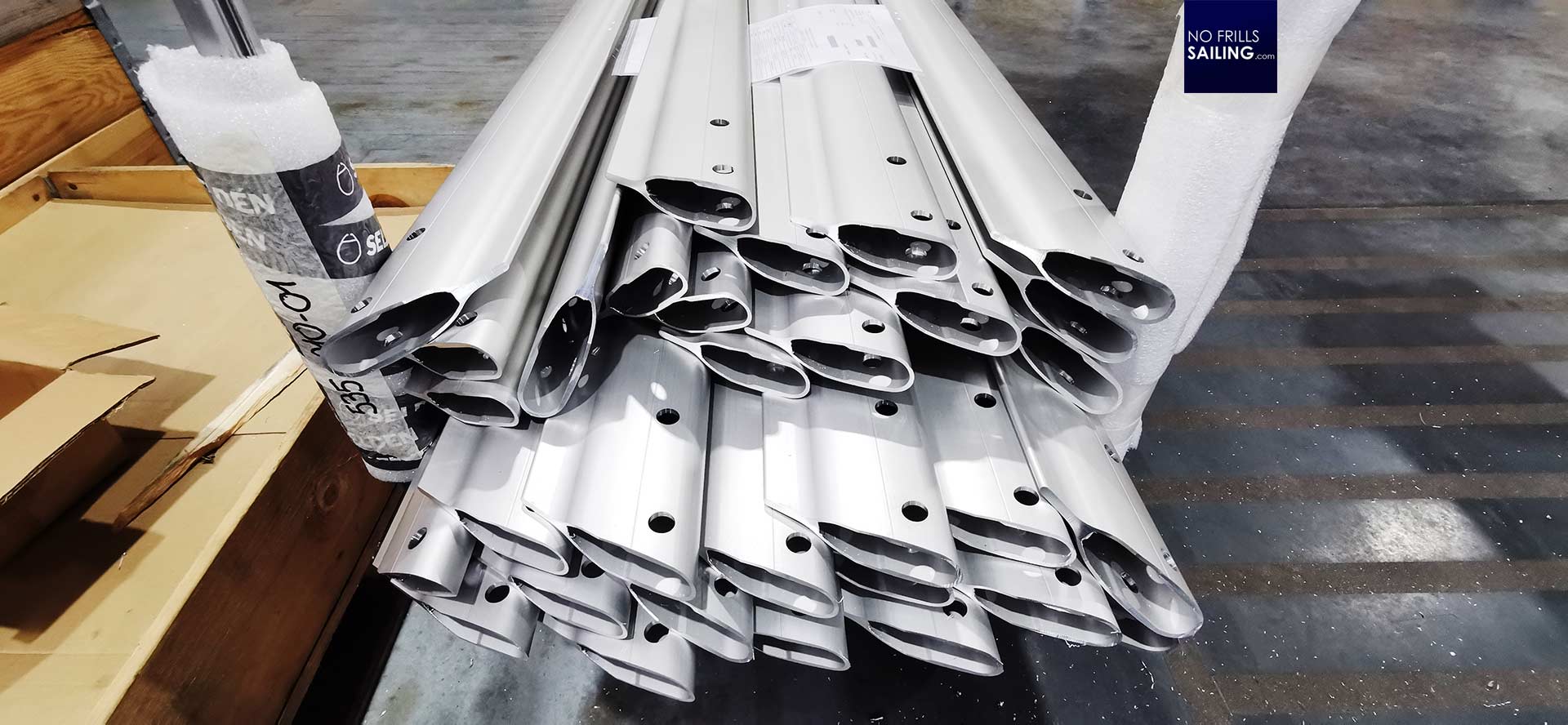
The ends (with caps) and especially the joints of the spreaders to the mast itself need to be individually cut at first. As the spreader´s sweep can be ranging from zero on rather classic boats to relatively extreme 35 degrees, especially on boats without a backstay, the workers need to cut the adjoining areas very accurately. This is done by a swaging machine and gauge models, along which the cut is made.
Fascinating: Shrouds production
The one step in mast-production I was looking forward to see the most comes next. Shrouds. Every time I am aboard a sailboat I am amazed and excited of the simple fact that those tall metal tubes, some as tall as they seem to scratch the undersides of bridges, are held in place by just four, in many cases even only three steel cables: The stays and the shrouds.
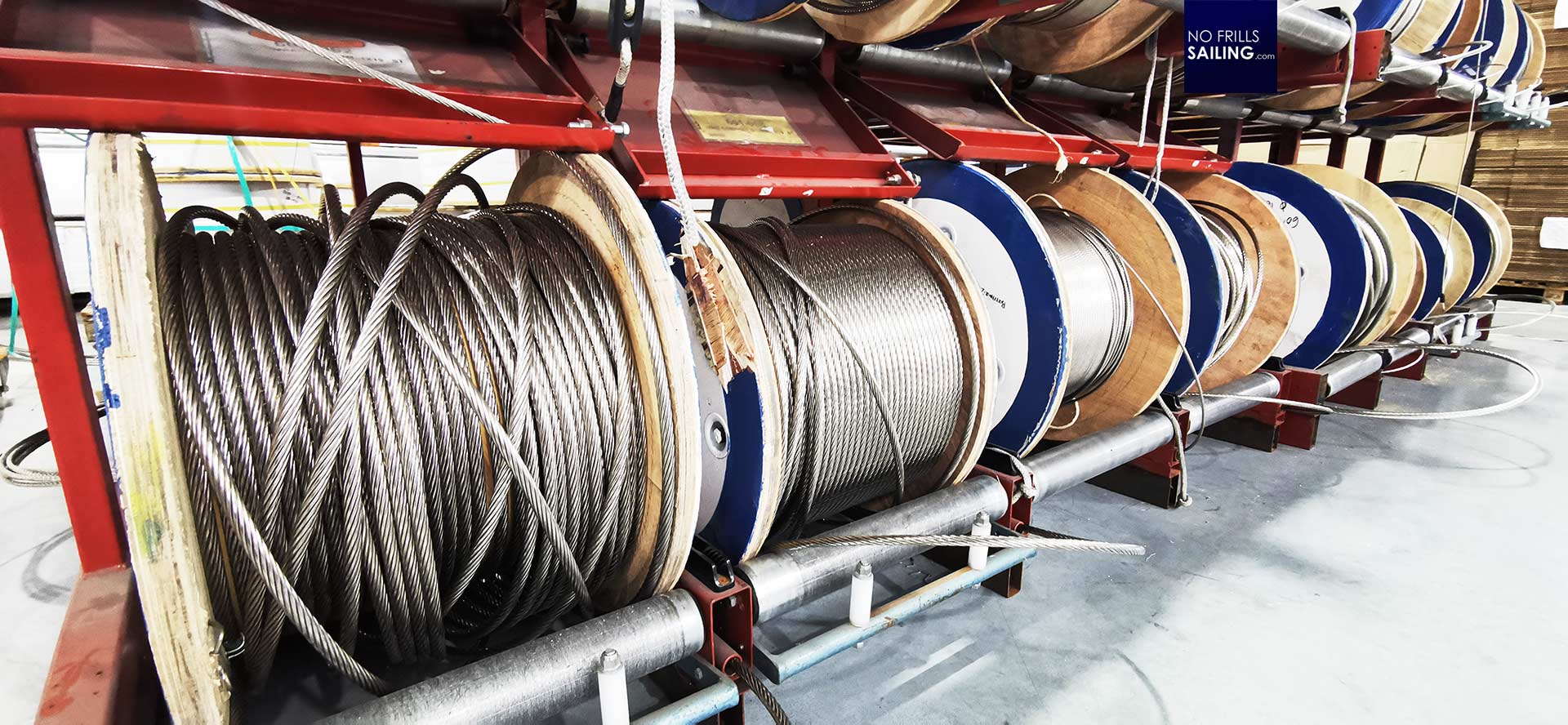
Many newbies think that the mast is somehow bolted, screwed or in any other way firmly fitted and connected to the boat. Which it is not. It just rests on the mast foot. The sheer tension of the steel cables, that are the stays and the shrouds, firmly presses it to the boat´s deck and hence hlding it tight. Even more, those cables are able to not just hold the weight of the mast, but also absorb the stresses put into them by the pressure of the wind or, mind-boggling, by the toughest storms. So how are they made? By hand, again!
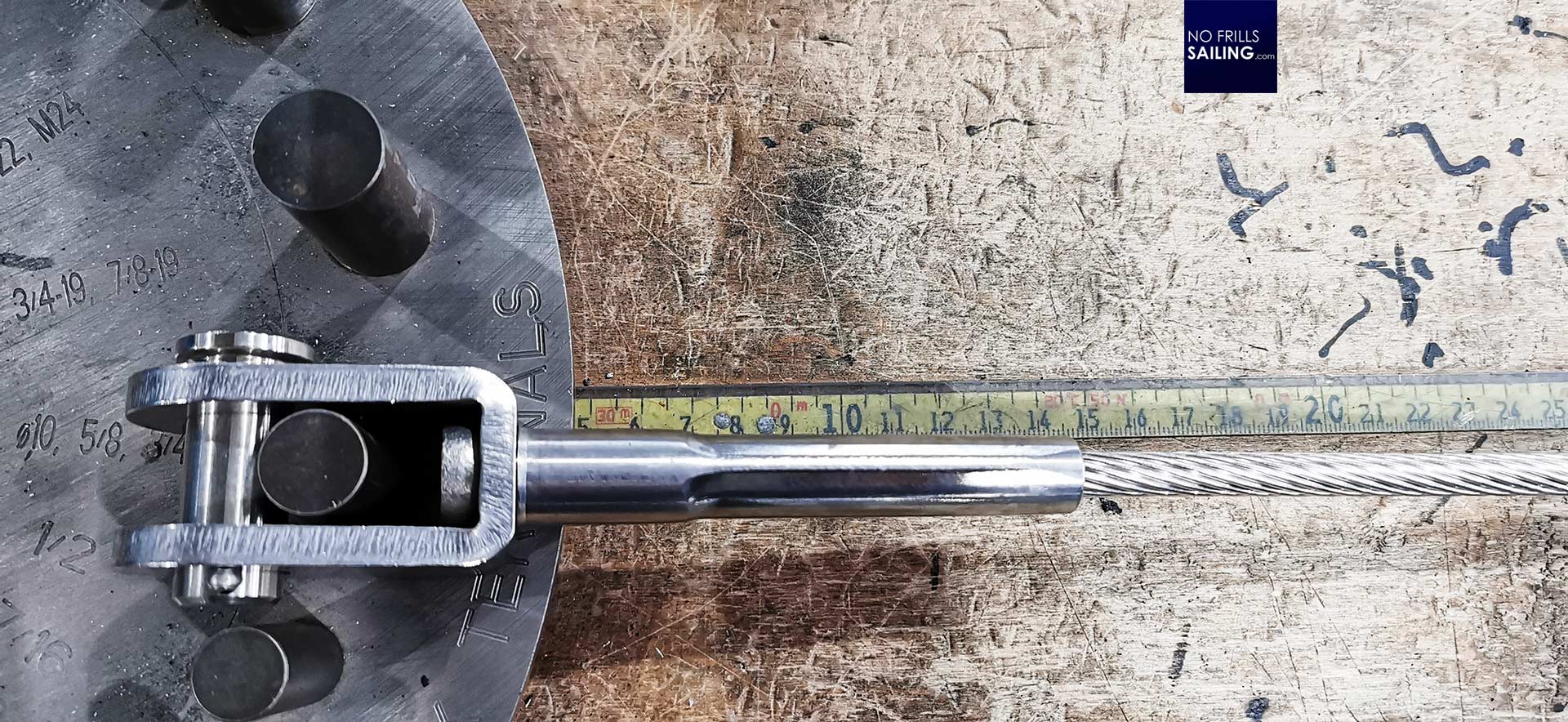
When the lower terminal has been attached (how this is done, is explained a bit later in this text), it is put on a wheel that contains all sizes of terminals. The stainless steel cable is then rolled out over a long, very long wooden worktop. As an inlay, a ruler runs down alongside the cable, enabling the worker to cut the cable to size (again, as a surplus measurement laser-aided) to a mere millimeter accuracy.
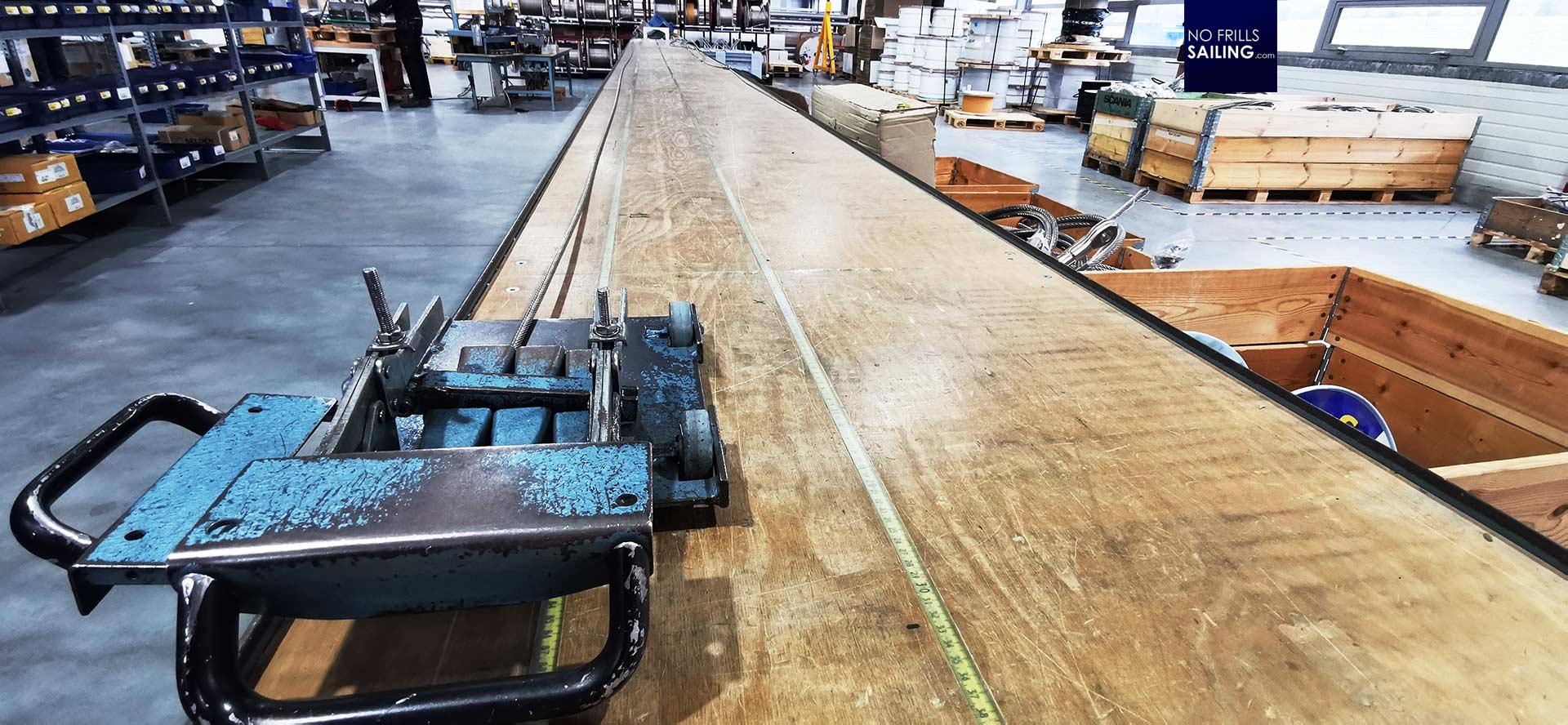
Judging by the wear and tear of this workstation, the sanded wooden surface of the tabletop, the polished bare steel and worn down green paint, this is a place were lots of work happens. A place where – again – humans are actively utilizing their skills to handcraft a part of the product. “This is what I meant”, Leon begins: “We invest in automation where it is saving precious human energy – but we bet on handcraft, creativity, perseverance and real skills where necessary. Making the shrouds is such a step in production. We cannot allow for any bigger tolerance nor – worse – failure. If those terminal aren´t attached the right way, bad things can happen aboard.”
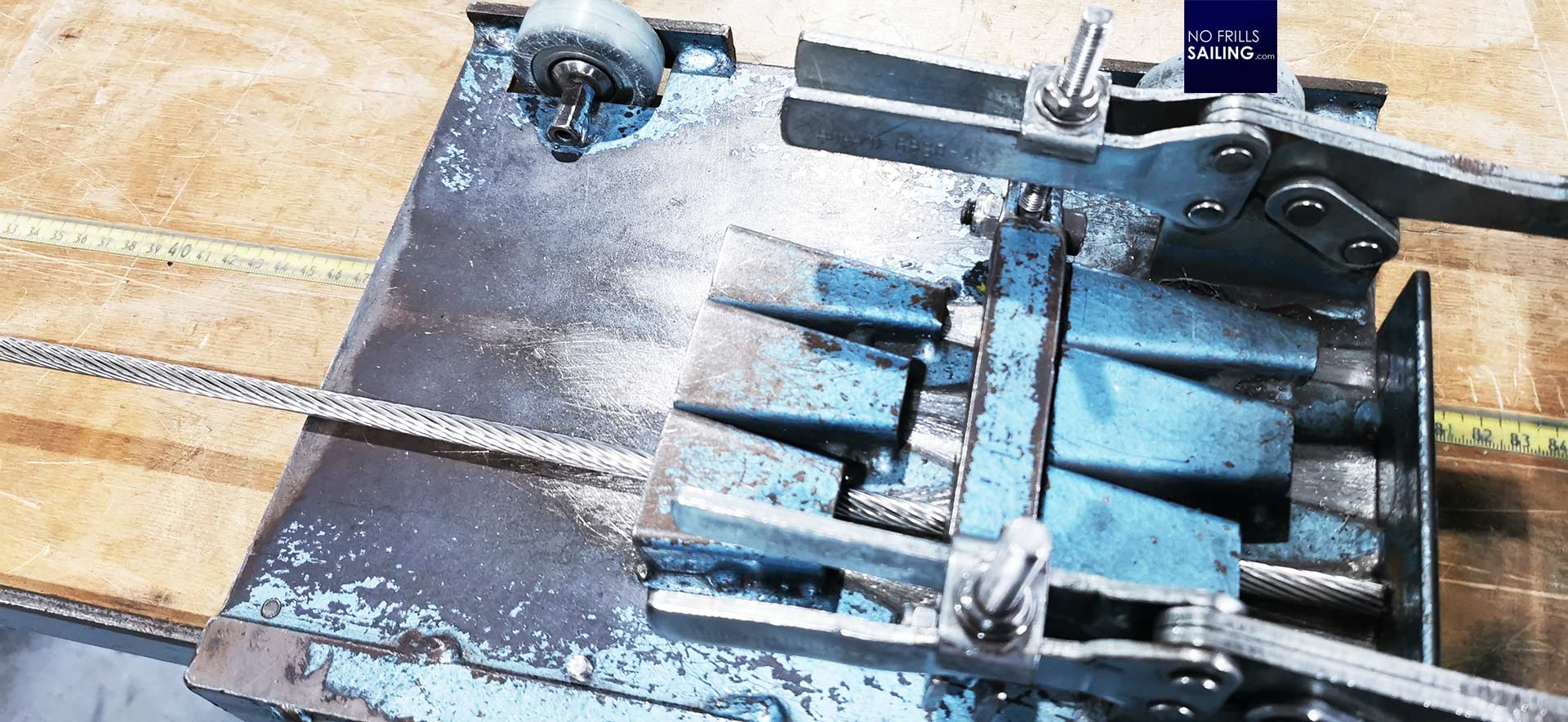
In this, Leon shows a protocol, basically a piece of paper, that belongs to every single mast built by Seldén. This paper, prepared by the office, contains all measurements – in this case the lengths of each cable – on one side and handwritten data on the opposite. The guys working on the shrouds will put in the exact measurements of their shrouds produced and sign with their names for the correct data. “All of these for all masts are archived. Nothing is lost. We can reproduce the production history of every single rigging.”, Leon confirms.
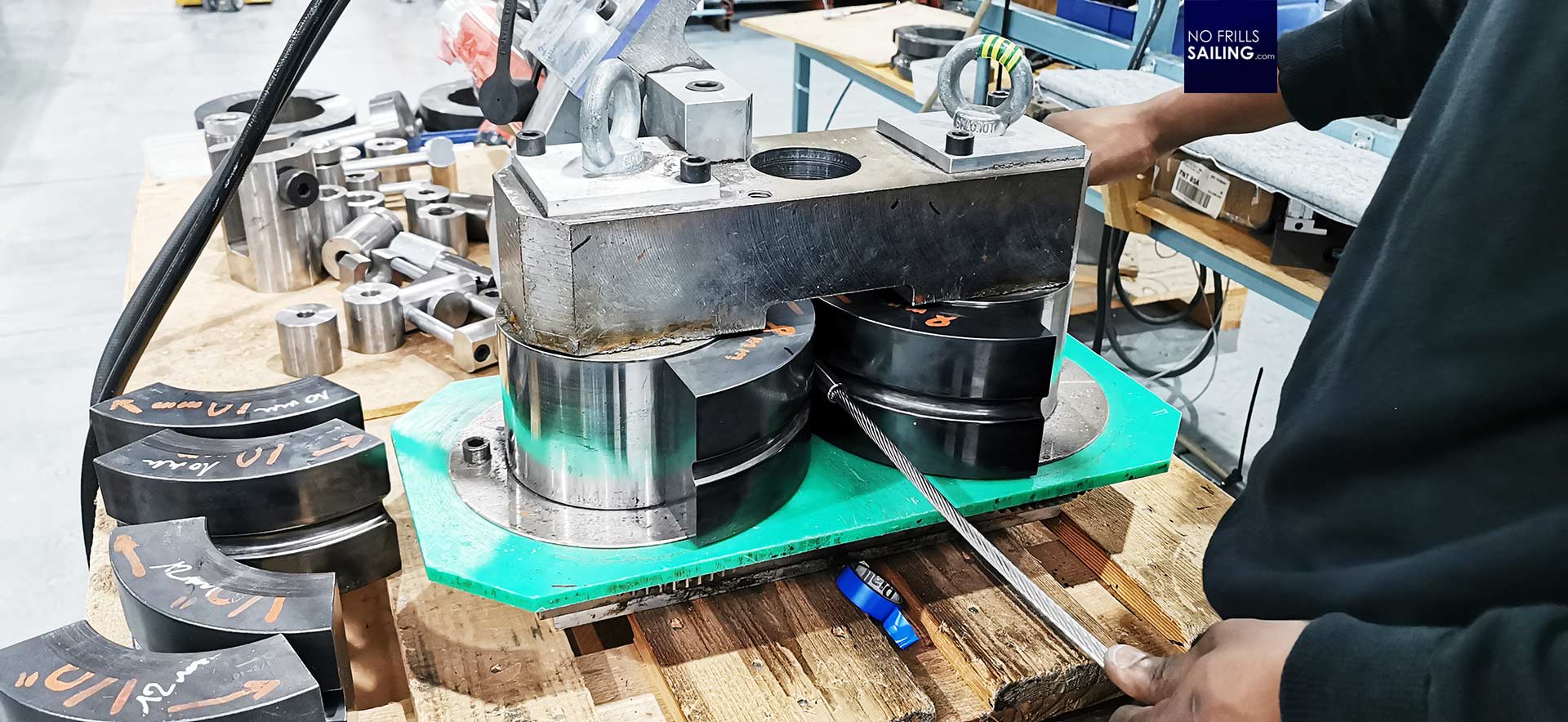
Apparently the coffee break is over and the workers pour into the hall. Sound level increases and we wait for a minute for the guy arriving who is operating the terminal milling machine. Something I wanted to see myself for a long time. The terminal is an integral part of the rigging. Essentially it´s a stainless steel husk into which the ends of the steel cable, that is the shroud, is put. A hydraulic milling machine is then pressing the husk under enormous pressure onto the cable, connecting both in a way that neither the mast´s weight, nor the wind or any other force exerted on the rigging (up until it´s pre-calculated and desired breaking point) can destroy it. Fascinating!
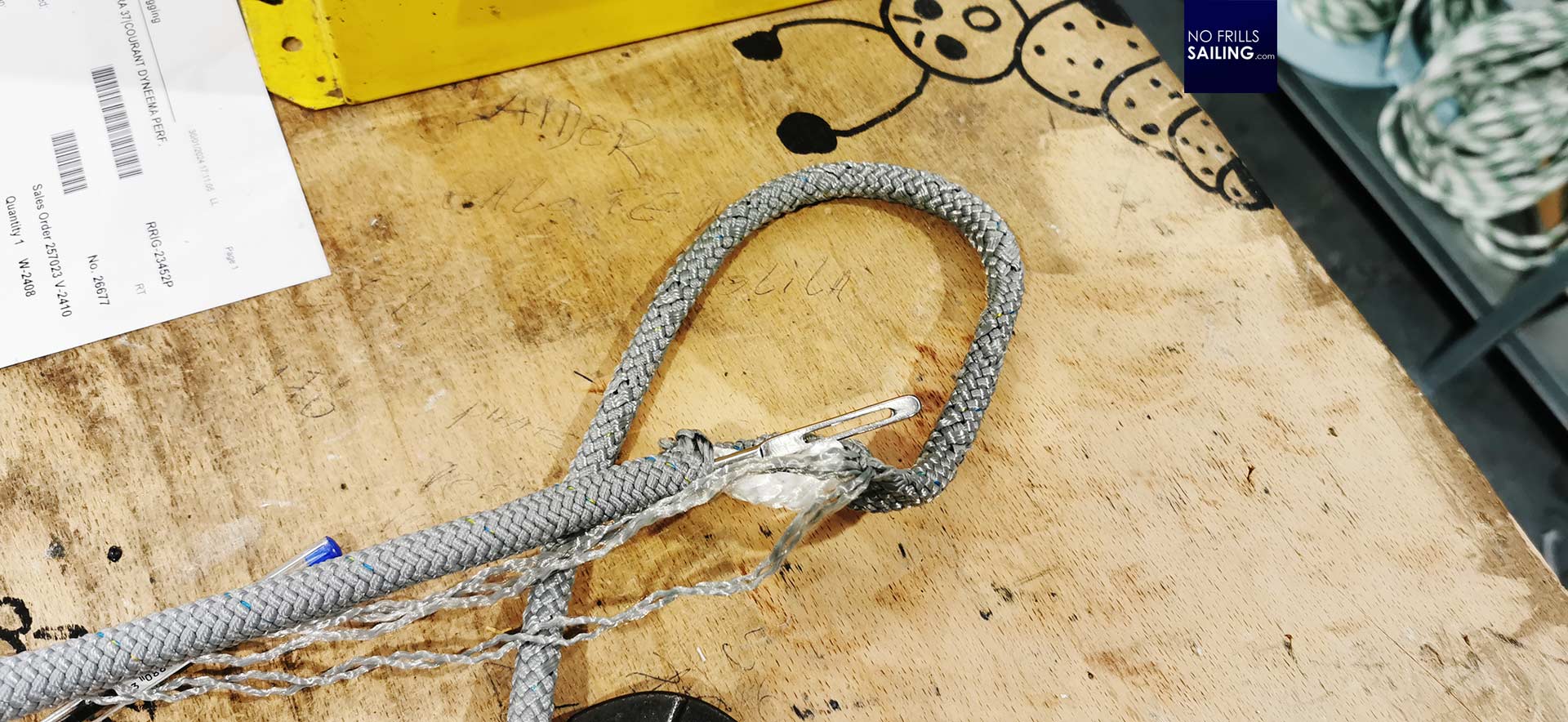
Again, lots of handcrafted working steps by skilled people. Even the splices of Dyneema parts are done by hand, as I can witness on another station. The guys are calmly talking to each other, somewhere in a corner a Bluetooth box is playing some pop music. A nice, kind of lush, atmosphere, in this light suffused hall. As we pass each station, the guys smile and greet, apparently, the team spirit is high. There´s no dirt on the ground, every time someone is unpacking a part, the wrapping and cardboard is immediately placed into the designated bin.
A mast for a lifetime
We arrive at the end of the production of Seldén´s aluminium riggings. After a thorough quality check that looks for the correct assembly of all parts as ordered as well as for the finishing quality, the masts receive a number. “This number is the ID, or DNA of the mast”, Leon explains. “As you have seen, any protocol of every production step is archived. So, if the owner of this mast needs an information about details, needs to replace any part worn down, as maybe an intermediate shroud for example, we can trace and reproduce the exact part at any time – for the whole lifetime of this product.”
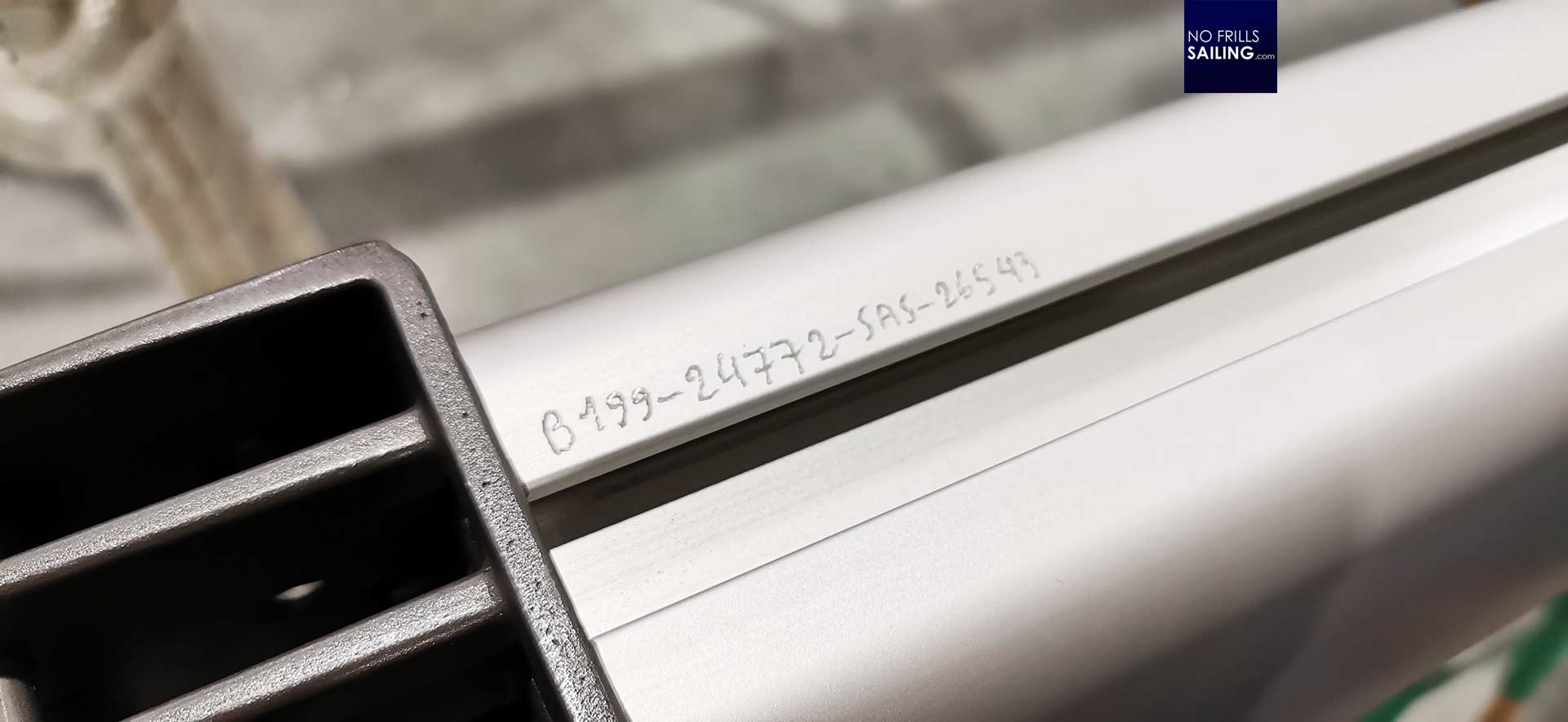
The number is put in by hand, so again, somebody is handcrafting this ID. Sometimes, Leon tells me smiling, the guys are a bit too proud of their work: “On one occasion on a boat show I´ve seen one our masts with a Smiley after the ID number …” I like this idea as it underlines the pride and handcrafted quality by motivated people. Same as I like to know the people who build my own boat back home in Germany, I like the idea that I´ve just met the very guys who will soon start to begin building my mast for the Omega 42 here. “For me, Leon, I hereby authorize your team to put a Smiley on my mast too!”, I say.
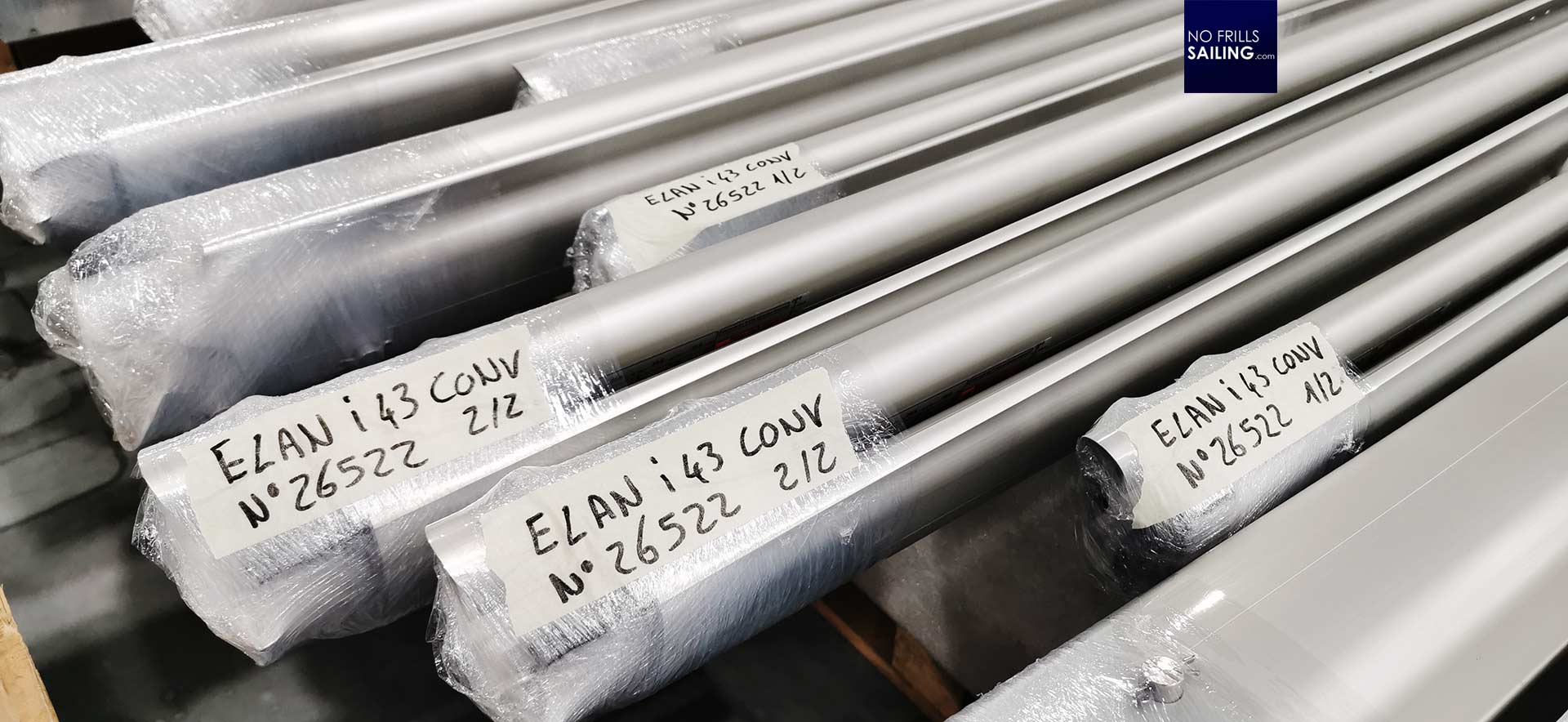
The masts are packed and wrapped to safely being transported at the last station. Now ready for shipping to the yards, I again read the names of the different brands for which this factory produces. Seldén masts and with them the great quality and handcrafted attention are utilized by so many well.-known brands. And I remember myself being happy to see our own boats, the Oceanis 34.1, started to being equipped with rigging made by Seldén. It´s just very impressive.
A huge invest: Carbon masts by Seldén
But we are not finished yet. It´s starting to become even more impressive. Leon leads me through a door into a second production hall. It has almost the same size, but appears a bit less filled with stuff. “We are setting up a Carbon mast production here”, Leon explains. “When fully operational, this will be one of the biggest and most potent facilities for Carbon rigging in Europe.” He is seemingly proud.
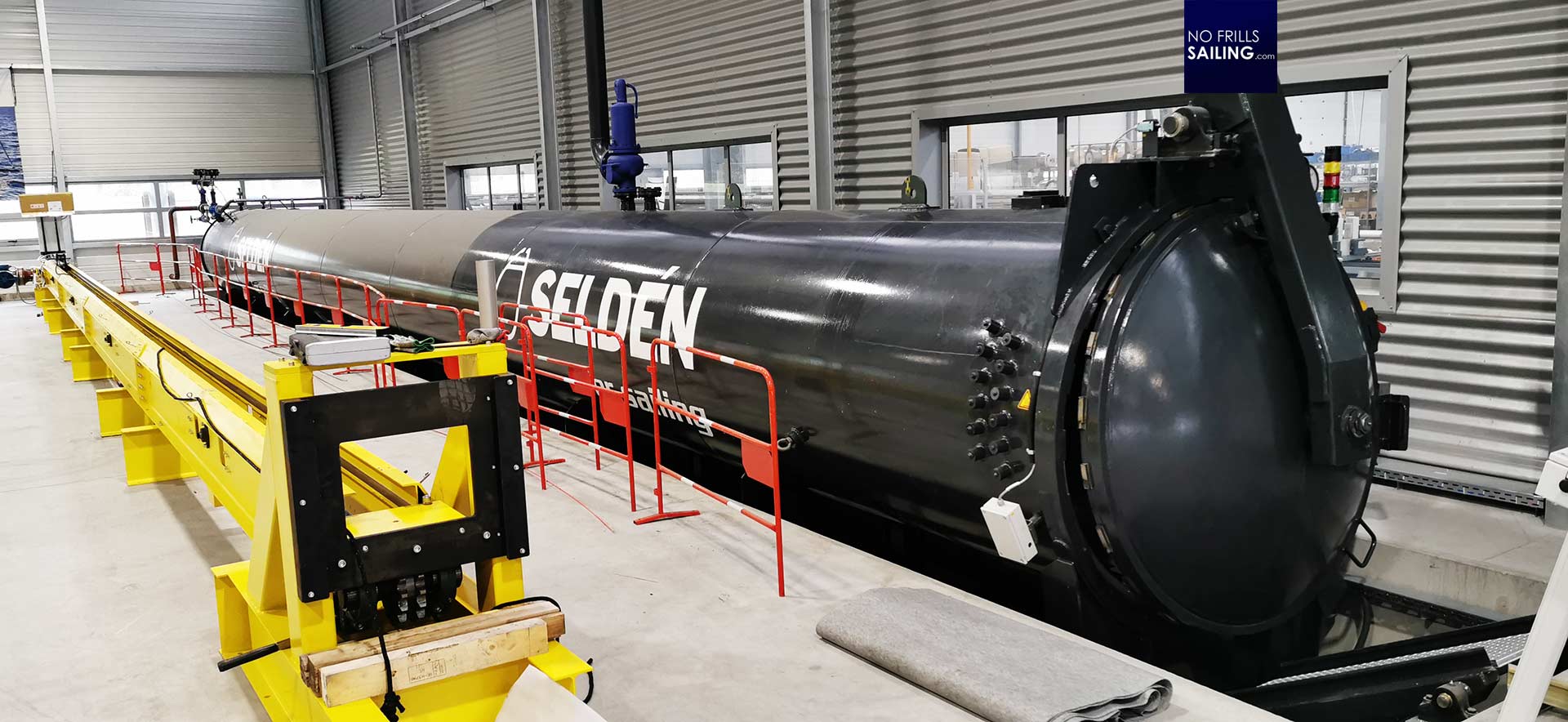
Heart and most impressive part of the hall is a huge black tube. It looks like a steam locomotive from the future, or some part of an oil pipeline. “That is the autoclave.”, he explains the apparent. Carbon parts aren´t laminated like glass fiber reinforced laminate, but it is merely “baked” to a solid form. Apparently, masts are very long, so the “oven” needed for this step must also be very long. I am happy to identify a small type label on the machine: “Made in Germany”.
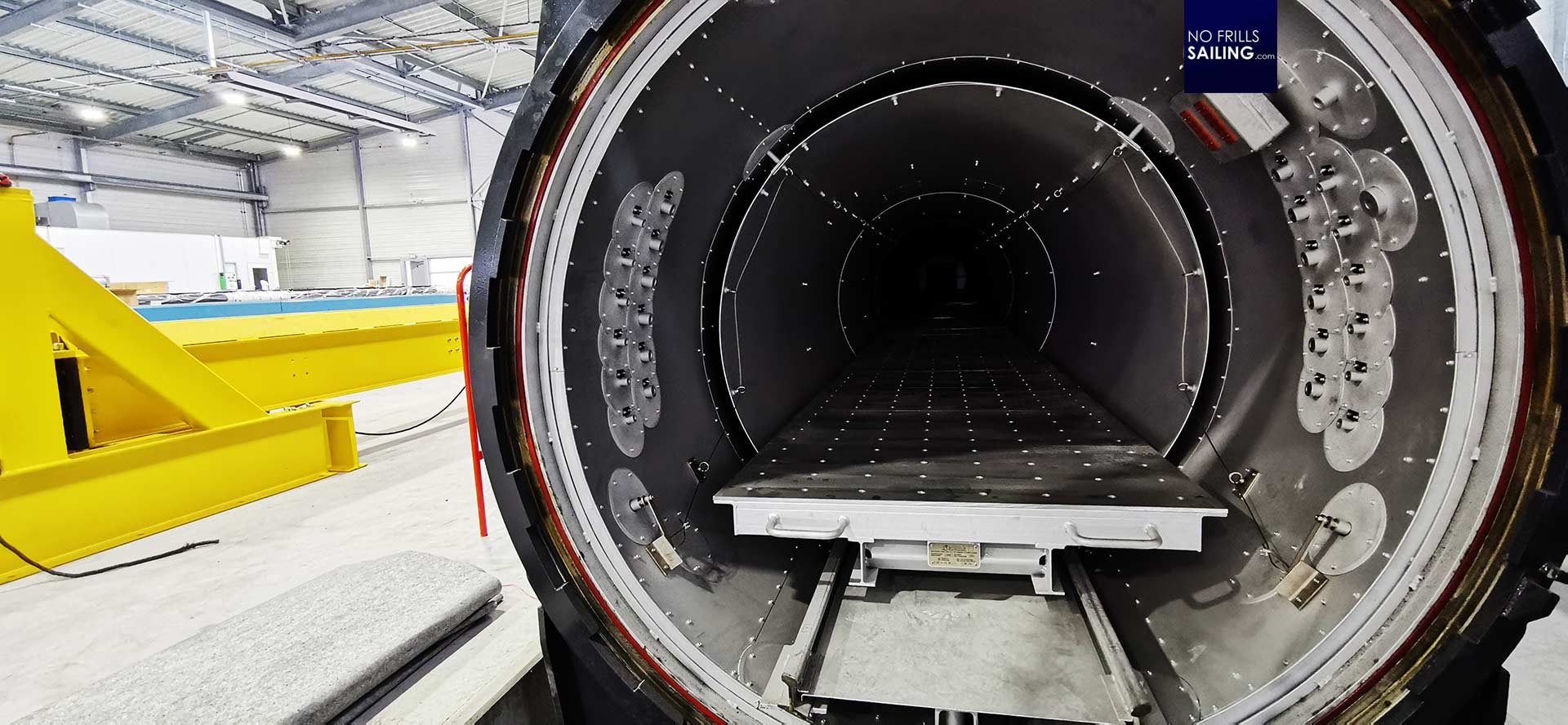
Leon opens the large autoclave so that I can take a look inside. The blanks, when being woven and ready for the baking process, are put together on a stretcher, that can be slid in and out on the tracks. Depending on the diameter of each mast, many masts can be put together and baked in one single process. Looking at the current high energy prices, this is a clever way to save money and work cost-efficient. The baking process is done at a surprisingly low temperature (not more than 140 degrees Celsius) and takes around four to eight hours.
Individual carbon rigging design
The actual baking of the mast may be the most exciting step of the production process, but it´s neither the first nor the last. It all starts with the weaving machine. Again, a high tech piece of computer-aided machinery and huge invest for the company. The weaving machine looks like a giant sewing machine from home.
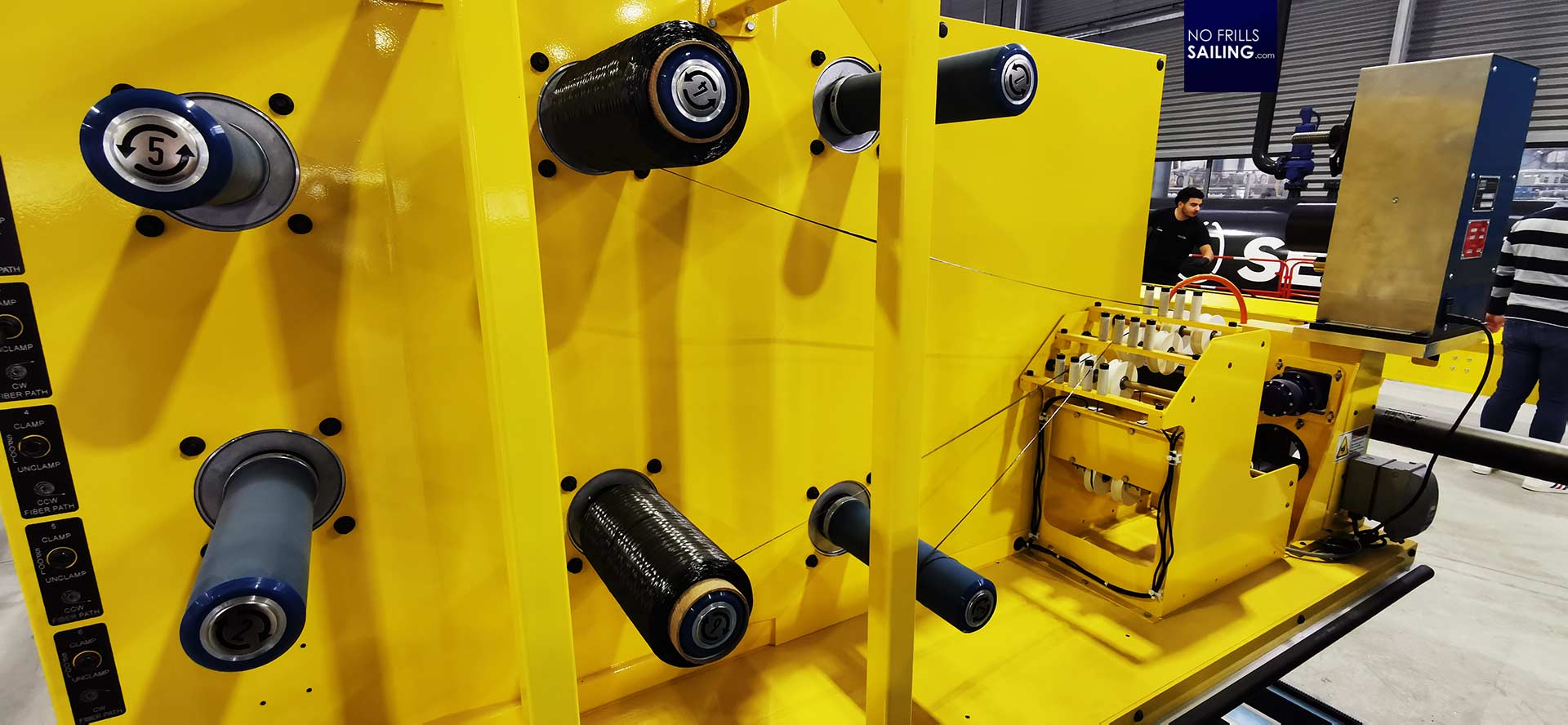
Up to six spndles can be fitted with carbon threads of different thicknesses or diameters. Those carbon threads are fed into one single “nozzle” at the front. This nozzle then – according to the pattern programmed into the machine – goes up and down alongside a rotating brute onto which, layer by layer, the carbon mast is woven. The machine can do different layups, thickness or forms. Depending on the size of the mast, the weaving process can range from a few hours to a full day or more for the biggest masts.
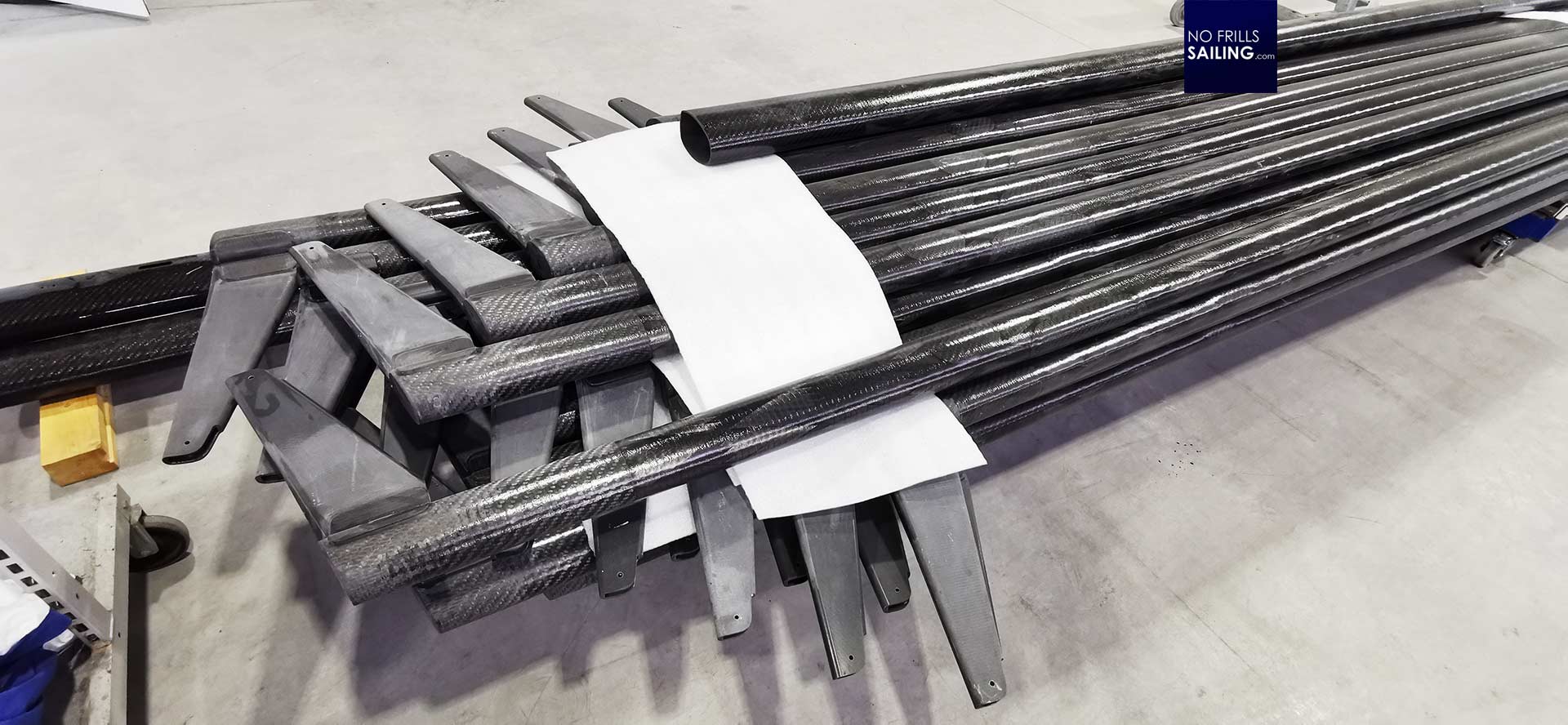
Leon shows me a batch of raw masts as they come out of the autoclave. Some 20 or more masts for J70 sailboats are stacked on each other. The surface is very rough, there are still marks visible by the shrinking wrap into which the slugs are packed before the enter the oven. “The high temperature of the autoclave will make the carbon-garment expand, the vacuum underneath the shrinking wrap exerts a counter force.”, Leon explains. “By that, the carbon layup gets its pressure from both sides, making it bake together, pressing out any trapped air.”
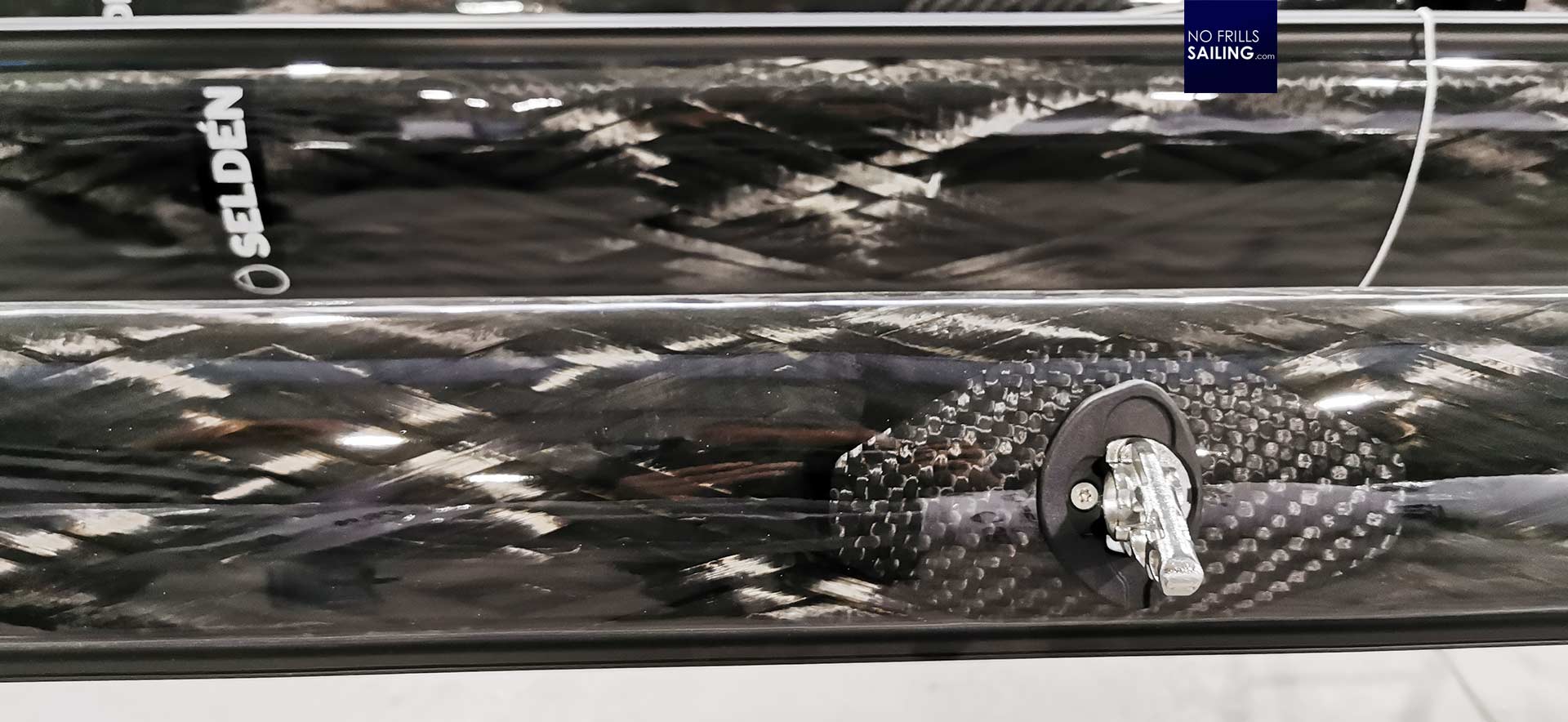
It´s a bit like vacuum infusion, but with heat, I guess. And like vacuum infusion, the shrink-wrap is then pulled off and disposed of, leaving behind a rather blunt, bumpy surface. The raw carbon masts are then sanded in a dedicated, closed off area where the microscopic dust is collected and put into a painting chamber, where the glossy protective paint is applied. “Before that, of course, we are glueing all other fittings, reinforcements and such.”
A production increasing
In a high-price environment like now, people are increasingly putting more focus on quality. Although selling is tougher, this is something that helps the industry: As more emphasis is put on quality, suppliers offering such have an advantage. Even in a market that is consolidating. For Seldén France the sheer numbers are more than good: “Last year we´ve made around 1.000 masts here”, Leon tells me. A staggering number! And it is growing, which is a good thing.
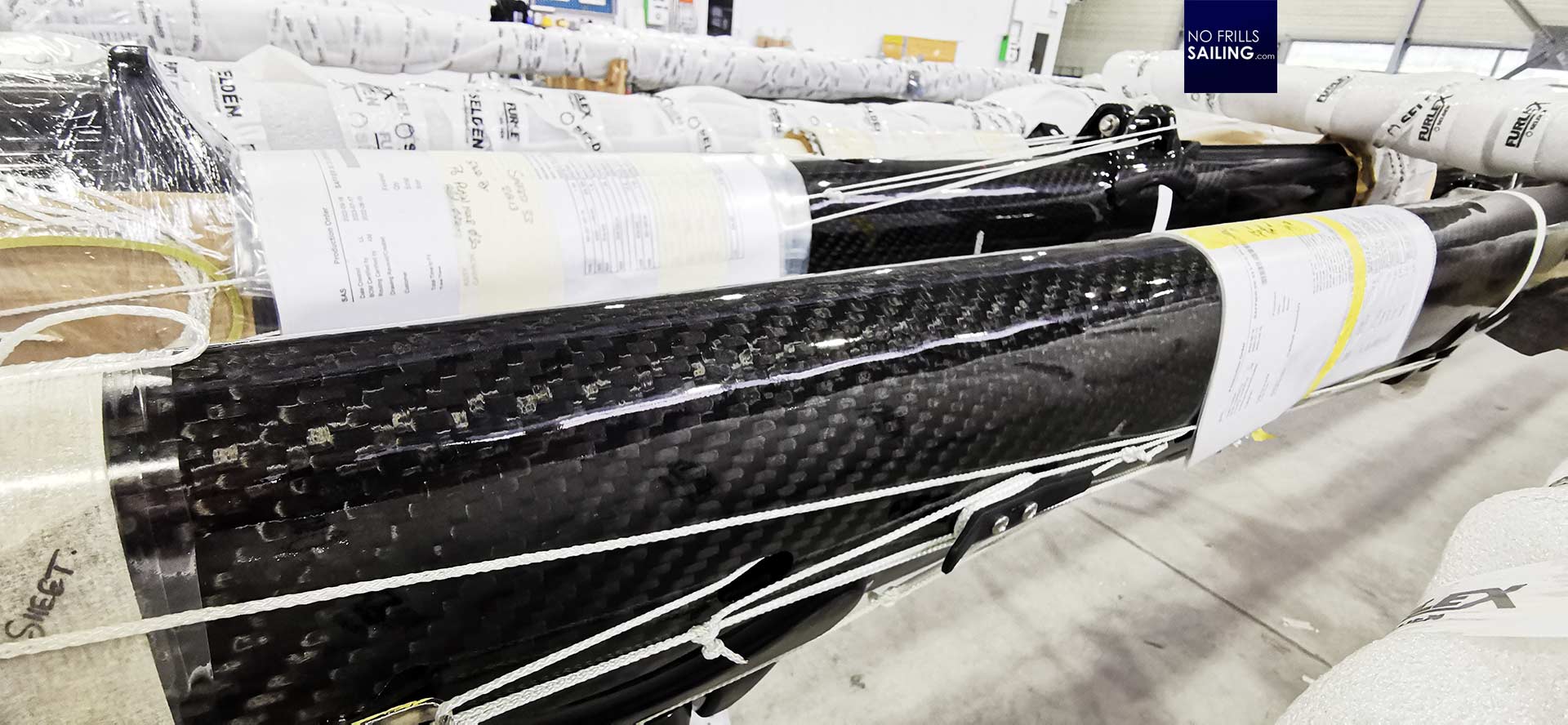
Carbon rigging production is just heating up, but he is very confident that once the setup is in place, Seldén France will be one of the big players in composite rigging production too. What strikes me the most again is the high ratio between series production and one-off special orders, such as mine. “We are constantly looking for new partnerships”, Leon explains, “and in this our location here in the heart of French boatbuilding is perfect. I mean, we are literally surrounded by Beneteau facilities, Jeanneau and many other big and small brands are not so far away. A more than perfect starting position.”
Leaving in confidence
We conclude our little tour by going back through all the halls to the offices. Like a quick rewind I take a look onto each station, wave to the guys working there, smiling at me and wishing a “Bonne journee”. This tour made me learn and understand so many facts, a perfect continuation and addition of knowledge I first gained when I spoke with Seldén Germany about my own mast.
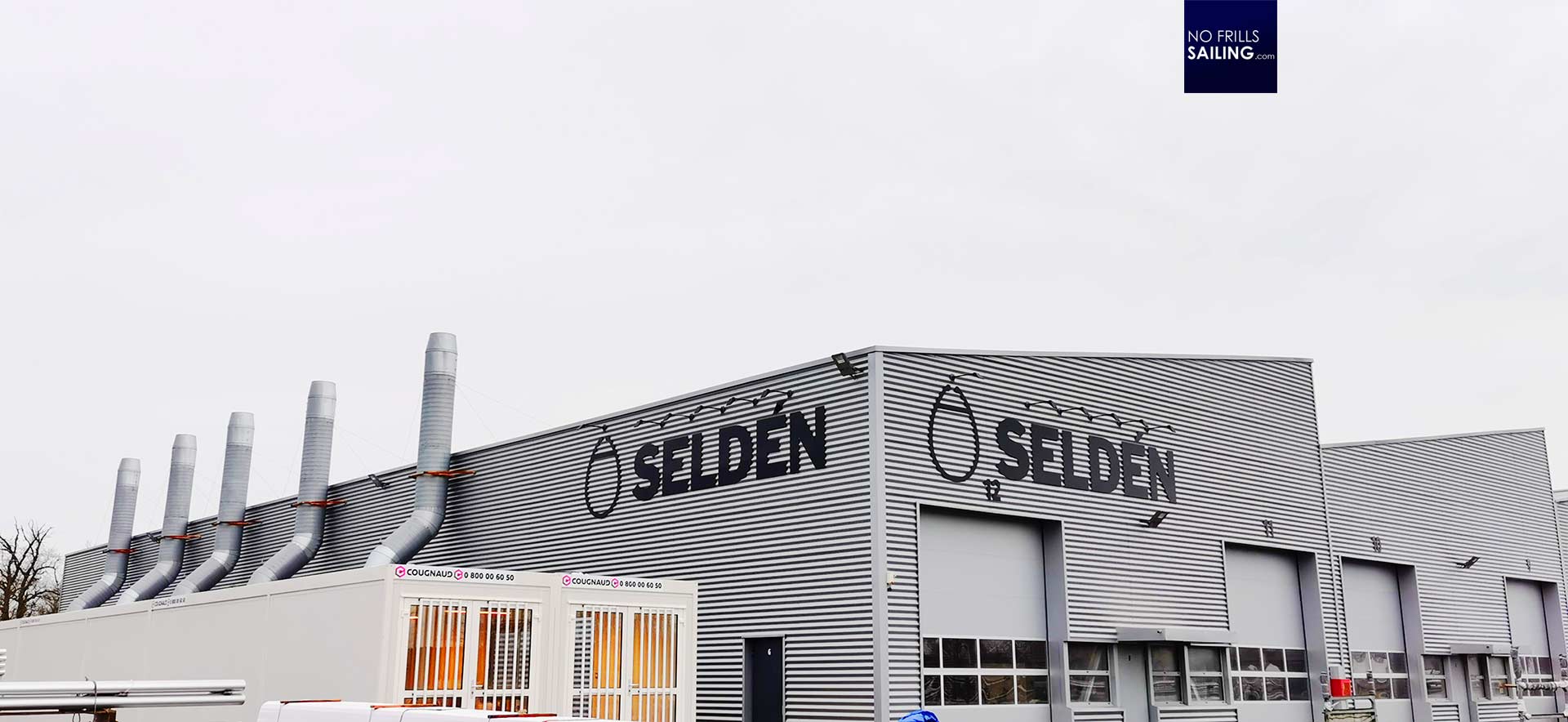
The best thing about this visit is the gain of confidence. Now that I understand how a mast is made, now that I know how high-tech some of the production steps are, now that I have seen the very guys who will utilize their handcraft skills to build my mast, I gain trust in their work. Looking back and waving Goodbye to Leon, I look so much forward to receive the tapered aluminium artwork soon to be put on ALPHA.
Thanks, Leon, for this absolutely interesting and inspiring day at your facility.
Related articles you might find also interesting:
Inmast furling systems: Comparing Seldén and Sparcraft
Talking details: About my custom made mast for the Omega 42
How it´s made – at SPW Propellers