After this exciting racing event aboard the Omega 42 last weekend let´s stay in this beautiful area of Germany. South of Ruegen, Germany´s biggest island, a nice little town with a well-known univrsity is located: Greifswald. It is strange, because somehow after almost nine years of publishing NO FRILL SAILING.com, with visiting almost all shipyards and boatbuilders in Europe and – remarkable enough as I am German myself and not living all-too far away – I´ve never managed to visit Hanse Yachts AG. As one of the “Big 5” production boat companies. Really strange. Although Hanse Yachts AG is a major player and certainly Germany´s powerhouse of pleasure boat production and it was because of a very specific Hanse boat that I started this magazine in 2016, many don´t know this. But that is another story, for now, let´s make up for the sloppiness of the recent years: Here´s my shipyard visit at Hanse Yachts AG in Greifswald.
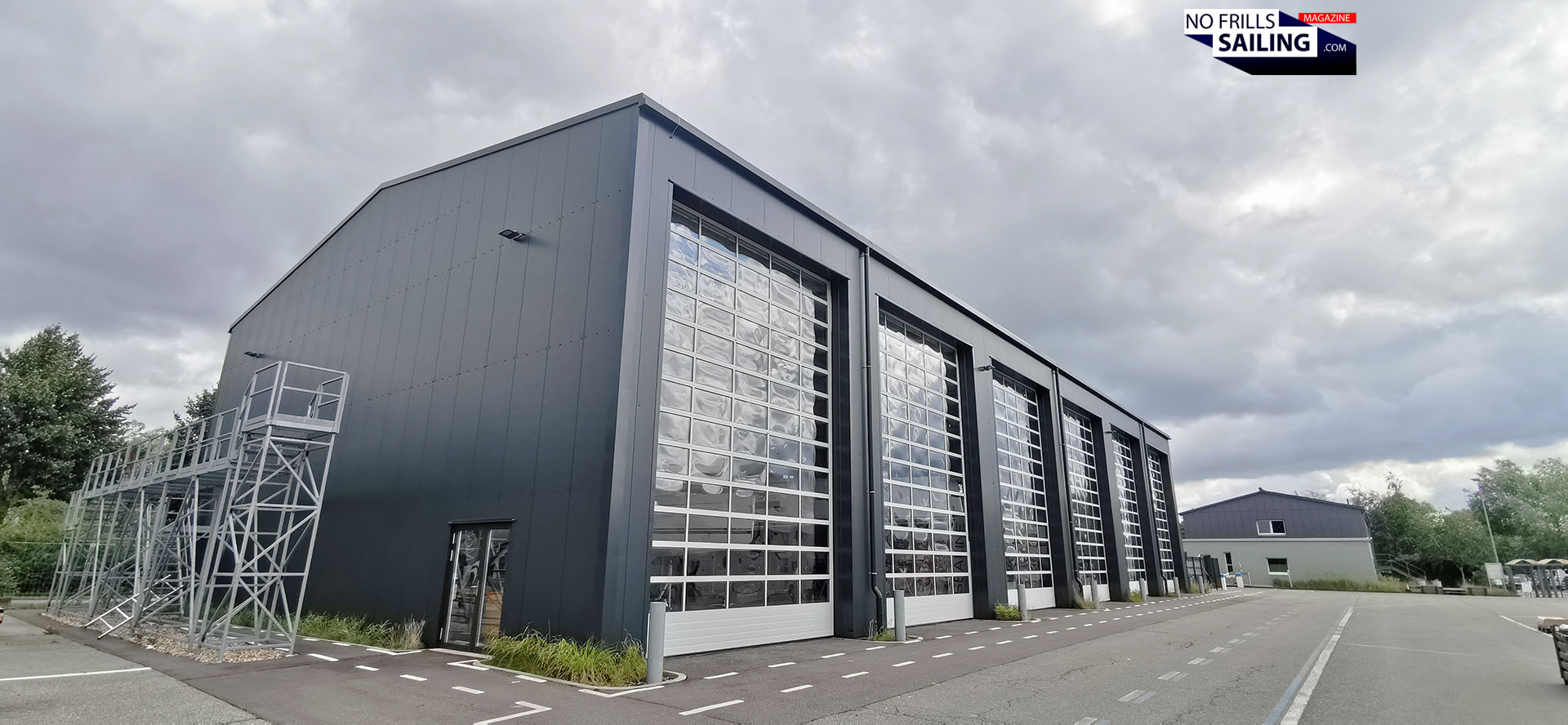
Arriving at the venue (which is merely a one hour-drive from the place where my own new boat is build) I park the car right in front of a big representative building and a humble welcome area. Flags are up in the air, displaying proudly the company´s brand logos. The new big building is Hanse´s famous showroom, a location so interesting and important that I will dedicate a single upcoming article to it. I am welcomed by Maxim Neumann, Vice President of Hanse Yachts AG and Sales Director. We know each other from press boat tests and several boat shows, so the reception is very warm and friendly. Without further waste of (his) precious time, we start the tour – at last I am here because I want to see how they are making their boats, Hanse is one of our top competitors and maybe I can get an impression why …
Utilizing location advantages
A yacht made by Hanse is a German product. Located at the north-eastern shores of the Baltic Sea, Greifswald is right there south of Germany´s biggest Island, Ruegen. You know Ruegen from my sailing trips to Sassnitz or, one of my most beloved places, Lohme, it´s one of the vacation hot spots of Germany. The City of Greifswald has a well known university and some 60.000 inhabitants. It´s location is somewhat pretty far to the East, which is of course a blessing for an otherwise rurally developed region with not all too many big industrial companies settling here. Thus, the company is an important employer in this region. But with Germany being a high wage country, of course, the company needs to implement measures to reduce costs in order to stay competitive. So they cleverly utilize location advantages.
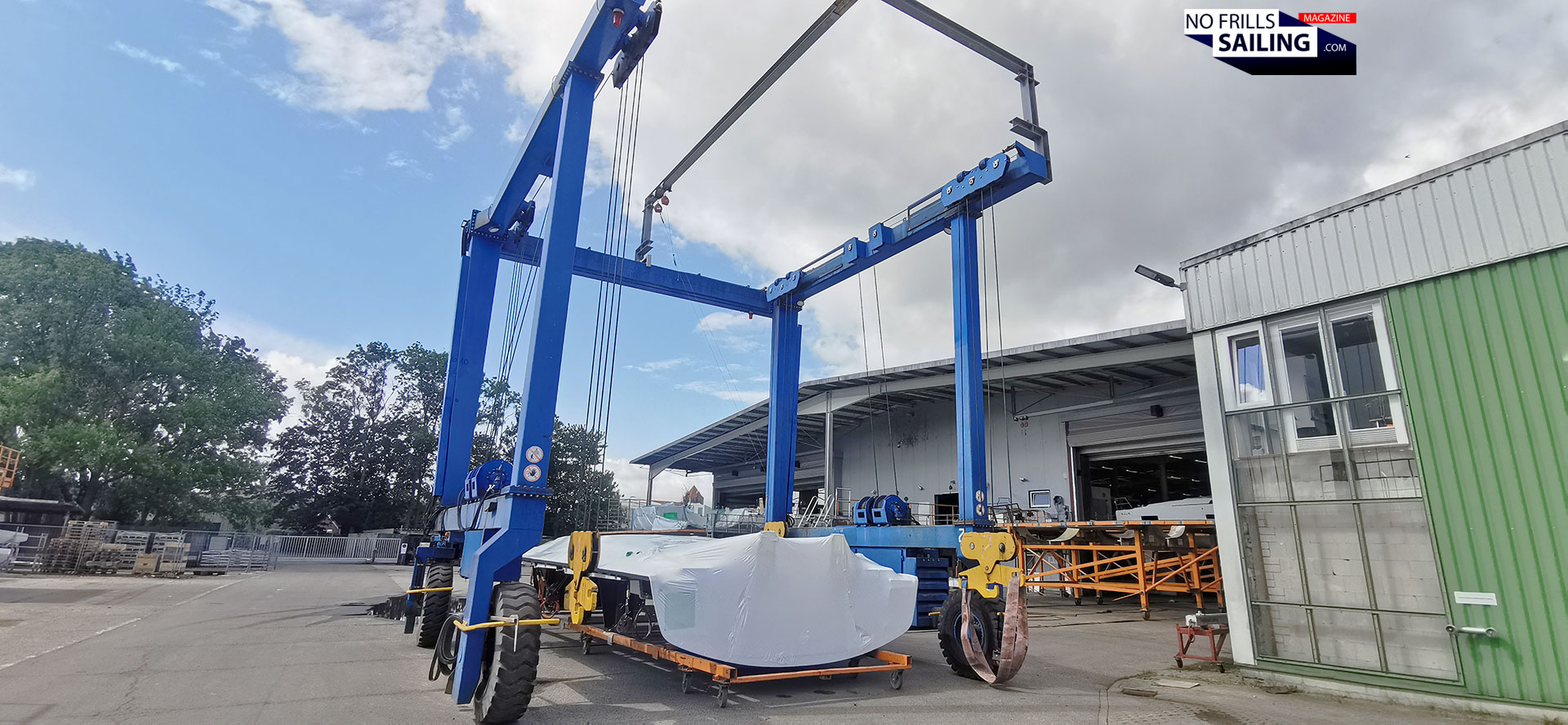
The company is based in two major locations. Greifswald, where we are now, is the production and assembly site. Boats are fitted and finished here, I´d say around 70 or 80 per cent of the work on a boat is done in this factory. Maxim tells me that here in Greifswald around 700 to 800 workers are employed, of which the majority are highly skilled specialists and craftsmen. A second production site is located in Poland. There, near Stettin, most of the lamination work is done: Hulls, decks and other GRP-parts are made there. The factory near Stettin is only 150 kilometers away, roads and the Autobahn are top-notch. Just-in-time production and delivery is therefore possible. Not all of the hulls are made in Poland, Maxim tells me, as the big powerboats and sailboat-units as well as all vacuum infusion-made hulls are also done in Germany.
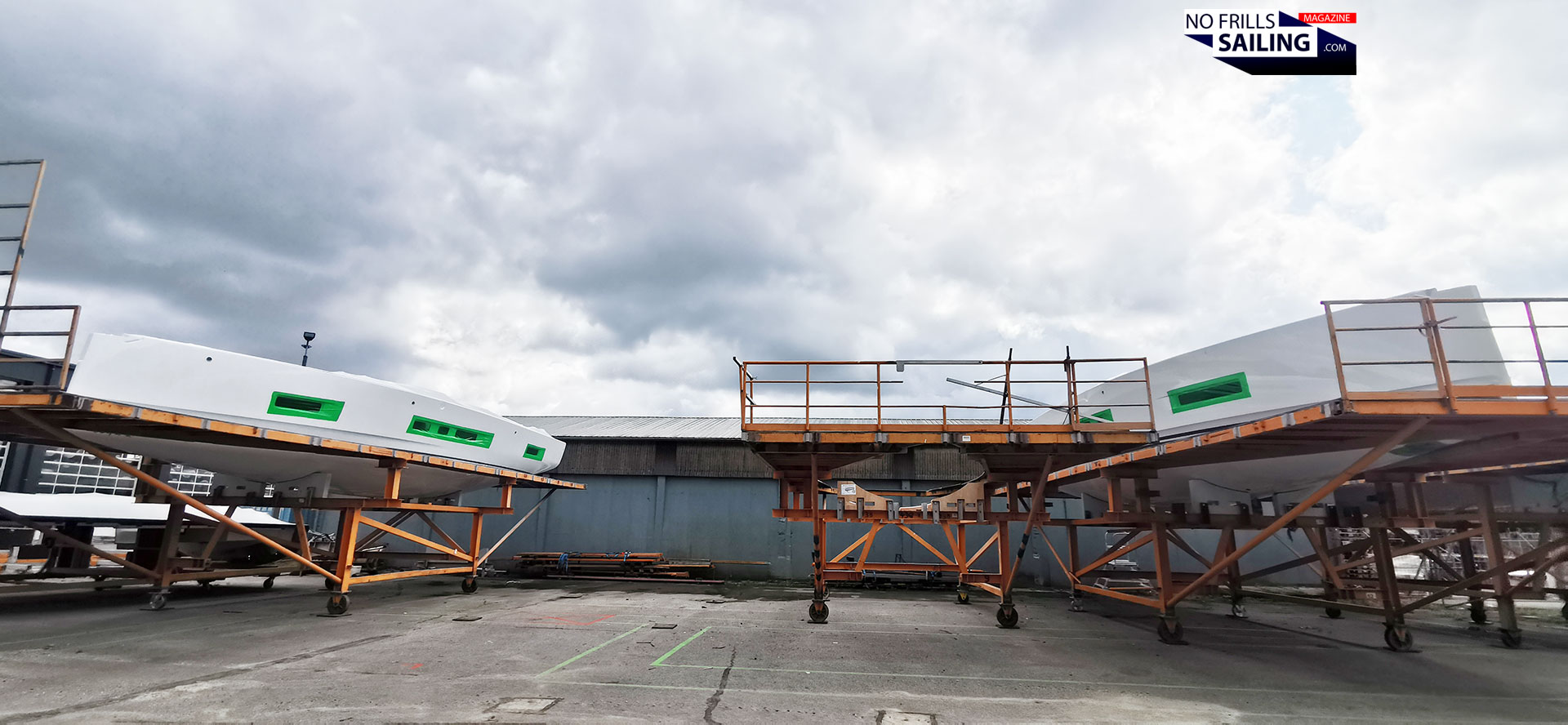
Nevertheless, they´ve perfected the cost-saving production strategy. But it is not only about money. Yes, wages are lower in Poland. But it is also the fact that the Baltic shore of Poland has a long, long standing tradition in ship building, it is a no-brainer to have most of the GRP-parts production based in Poland. A good example of the advantages the European Union provides for companies. Hanse, by the way, is not the only company using this model: Many brands have manufacturing in Poland, ranging from parts-only-production to full boat building. Like Beneteau with their outboard power boats or smaller Oceanis, Hallberg-Rassy or X-Yachts to name just a few. Many don´t know, that the luxury power cat brand Sunreef is infact a Polish company. We walk along and Maxim shows me the logistical area, basically a parking and waiting space for freshly delivery hulls and decks. By the way, in Poland another 700 people are employed, making Hanse´s workforce comprise around 1.600 people, excluding temporary staff that is employed for high season output. Not a small business …
Assembly line manufacturing
Production boat building is almost always done in one form or another on assembly lines. The idea is that the boat “moves” through the different fitting stations along a line through the manufacturing hall. In this, the dedicated assembly areas are specialized in fitting their parts – not the people, the parts and the tools move from boat to boat, but the boats move to them. By that, Hanse has a specialty that I haven´t seen in the other yards so far: Their boat cradles are pretty tall …
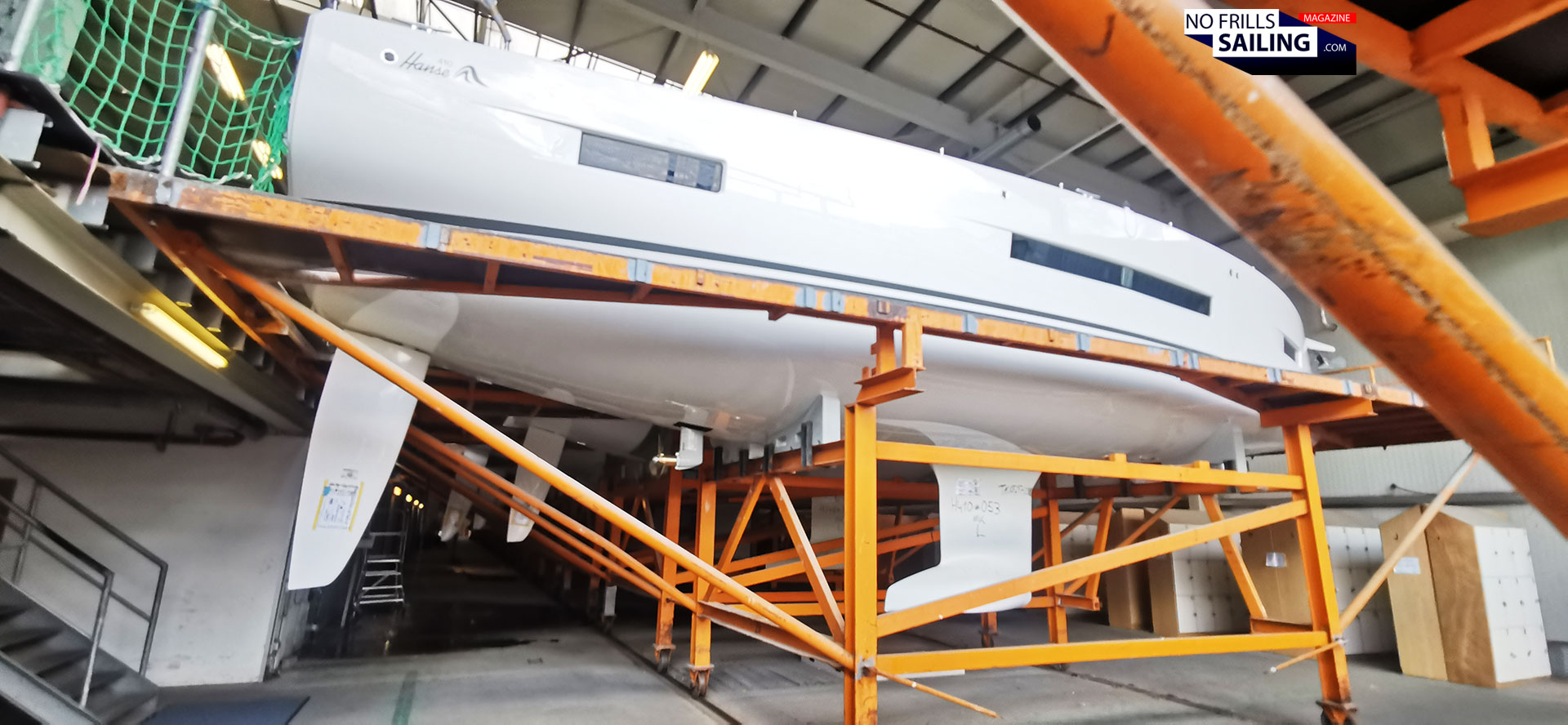
Unlike many other shipyards, at Hanse the yachts are moved along the line with already fitted keels. To compensate for the different draft types and ensuring that “up on deck” all boats have the same height to access, they´ve made special wheeled cradles that can take on any draft of the boats. Along the assembly line, as you may see on the pictures, the racks with the boats are moved sliding in tracks. Underneath one of the boats, a brand new Hanse 460, lots of water is pouring down – another specialty here.
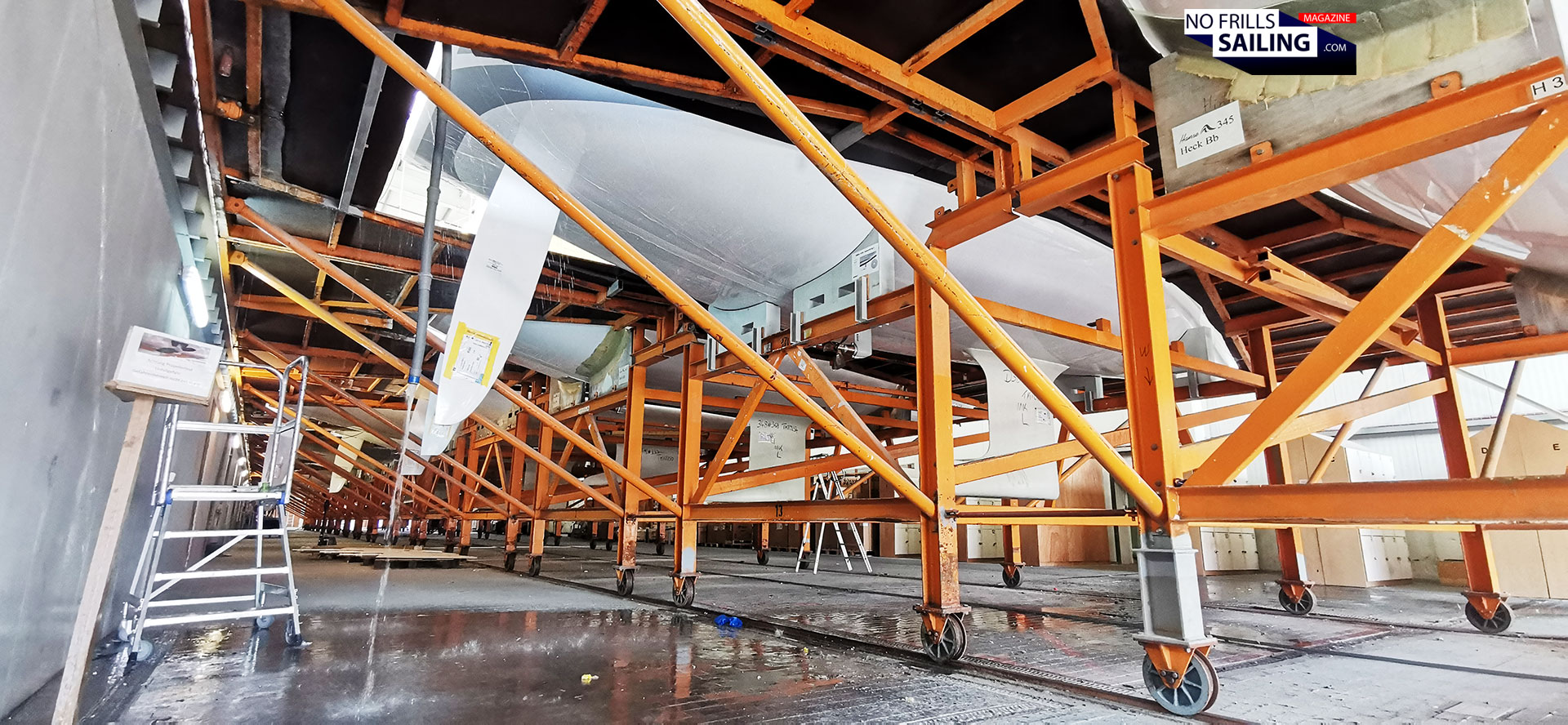
We climb the ladder to the upside of this assembly line where an employer just turns a valve and ends the “rain”. Folding back some tarps, a soaked wet deck and dripping boat is visible. This is the station where the hull-deck-fitting and windows are checked for water leaks. Pretty amazing that they do it at the start of the end-production right after deck and hull had been bonded and not at the very last step before delivery. In this, as he tells me, if a leak is spotted, the boat does not have to move at all as right next to it the specialists responsible for hull-deck-fitting are working.
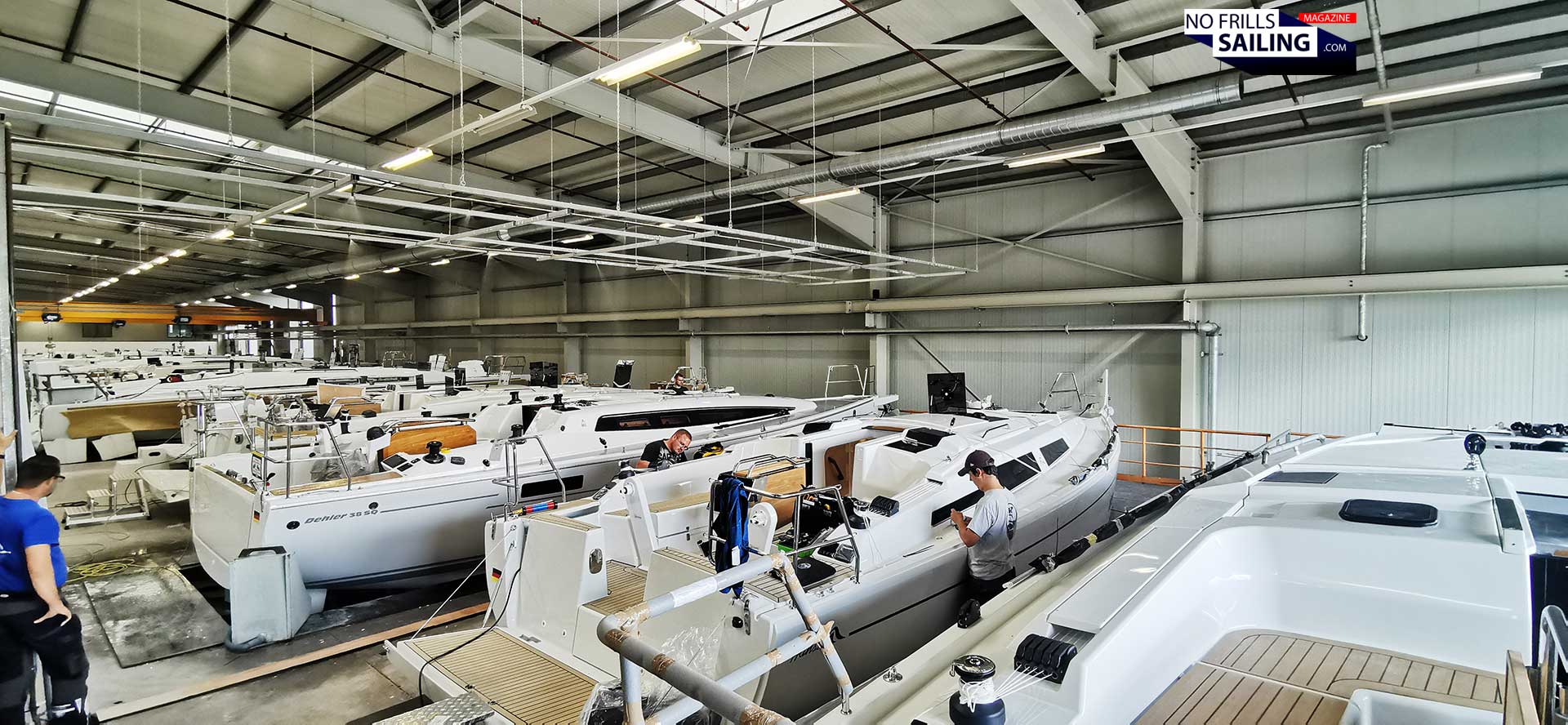
The assembly line itself is dedicated only to sailboats, but it is type-open. Meaning that here at Hanse the teams are trained to build any sailboat of the current line. The different production halls are subdivided into sizes, meaning that they have a small to medium-boat size hall and a hall for the big units. Thus, teams are trained and specialized to do different boats within their size range.
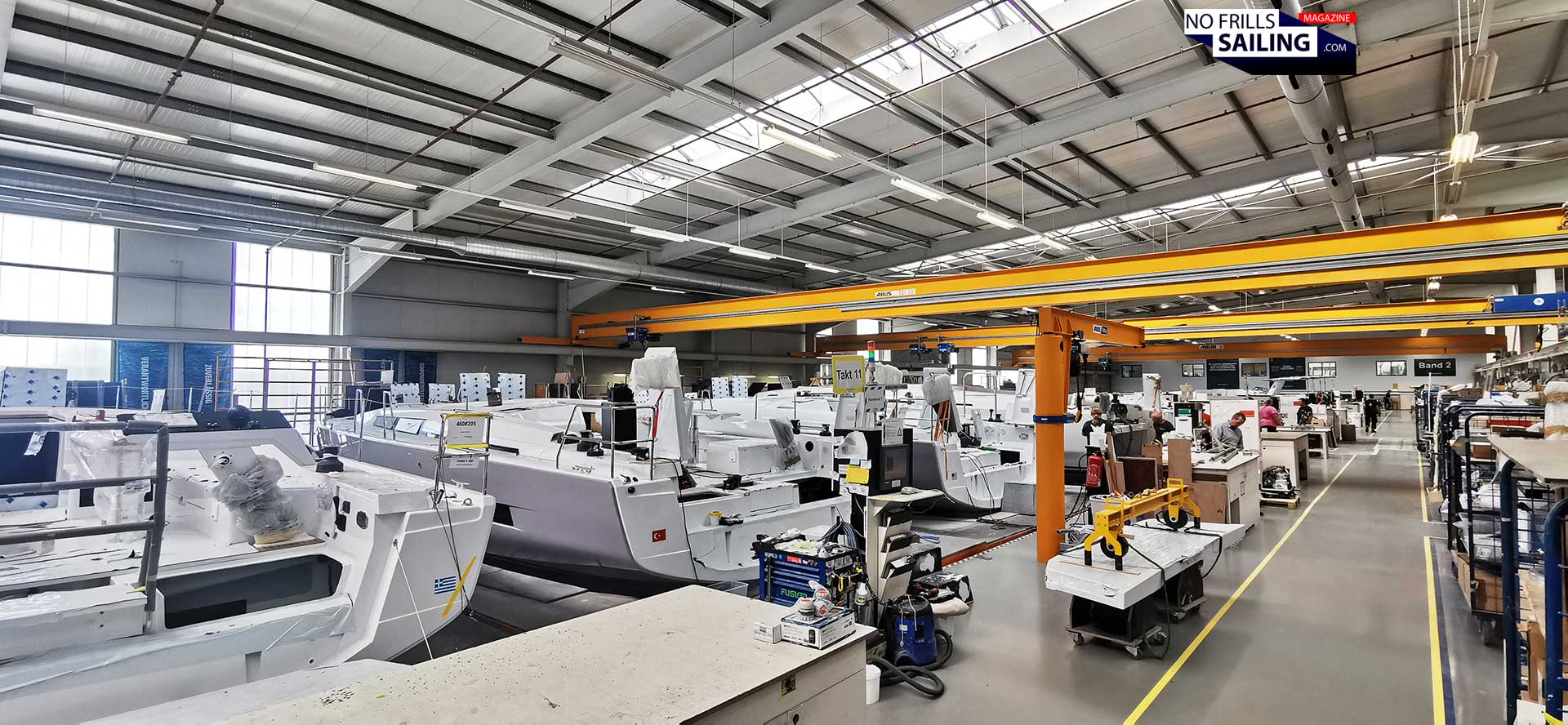
Hanse is a big company putting out several hundreds of units per year. The workshops and halls in Greifswald are pretty new, impressively big and well-maintained. Which is a sign: I´ve visited shipyards with far less nice workshops and surroundings, open roofs with large holes, dark and poorly ventilated sheds. Here, everything seems to be newly built, rigid and well-kept. Within the Hanse Group no less than six brands are housed: Hanse as the cruising sailboat brand, Dehler as their performance sailboat brand, Moody, a former UK-based brand with deck saloon cruising yachts and their power boat brands Fjord, Sealine and Ryck. The luxury catamaran brand Privilege, based in Les Sables d´Olonne has been sold by the company back in 2022. In this, Hanse is the biggest German boat producer, followed by Bavaria Yachts in the South of Germany.
Robots at work!
Beginnings of Hanse are humble – and a great story which I shall tell in more detail on another occasion. Founded back in 1990 by one of the most chatoyant figures of European yachting, no other than famous Michael Schmidt (who is still very active with his luxury sailing brand Y Yachts). Michael Schmidt, by the way, won the 1985 Admiral´s Cup as helmsman. Anyway, Michael Schmidt, from the start, kind of re-invented production boat building by coming up with smart ideas how to further consolidate, simplify and automate production to offer an even more affordable product “for everyone”.
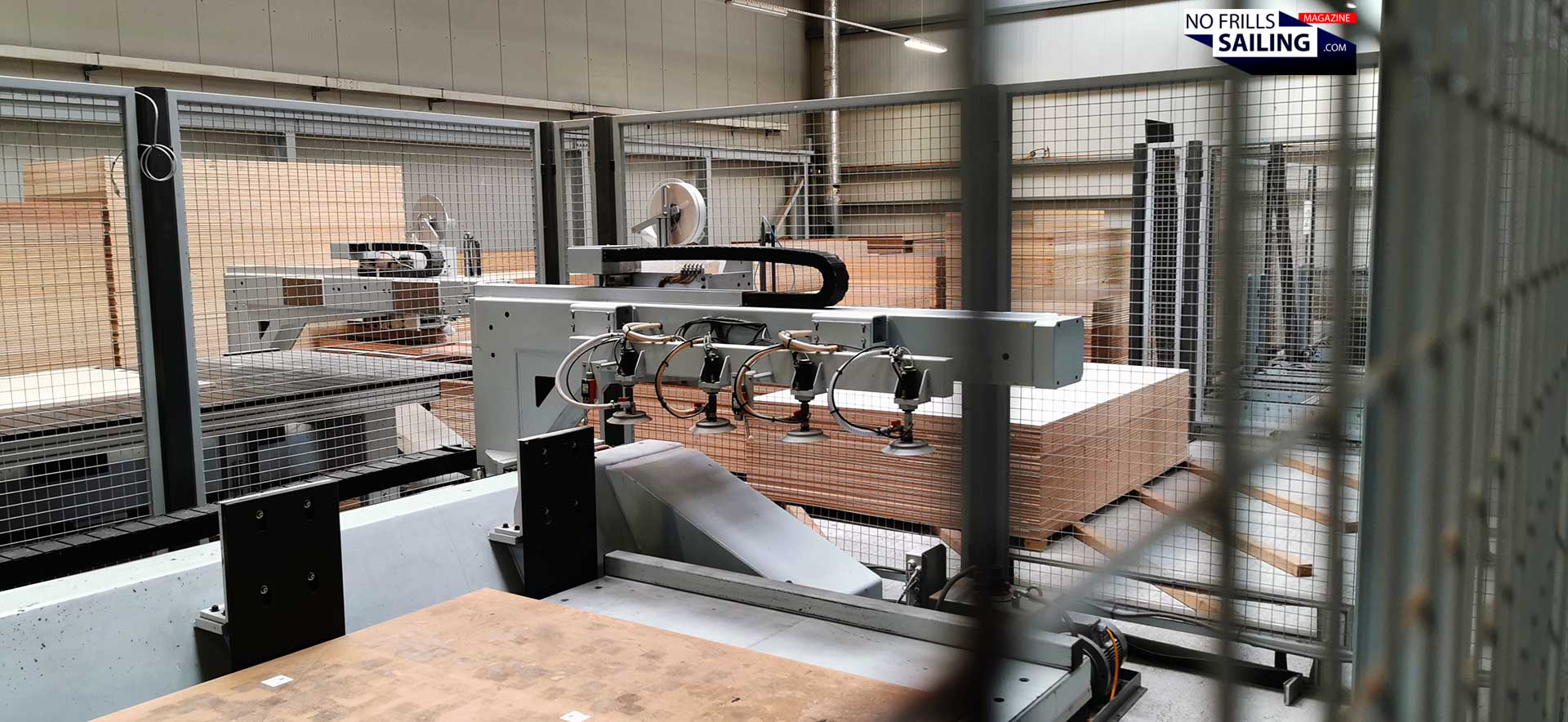
Nowadays his spirit can be seen in the company´s strive to constantly mode forward with this development. Maxim leads me to another production hall, a familiar smell filles my nostrils as we enter: The joinery. One of the few aspects of production boat building where automation is really helpful. Hanse has a full building dedicated to several CNC-robots – a huge invest in technology. But, as Maxim explains, these machines deliver constantly high quality without any margin of error. One machine even sorts not only its own tools needed but also manages raw material logistics on its own: “If we decide to make bulkheads, the robot will over night prepare itself from tooling to raw materials. If the next day we want to do Cherrywood parts, it will make sure that enough Cherrywood raw plates are at hand. Amazing, isn´t it?”
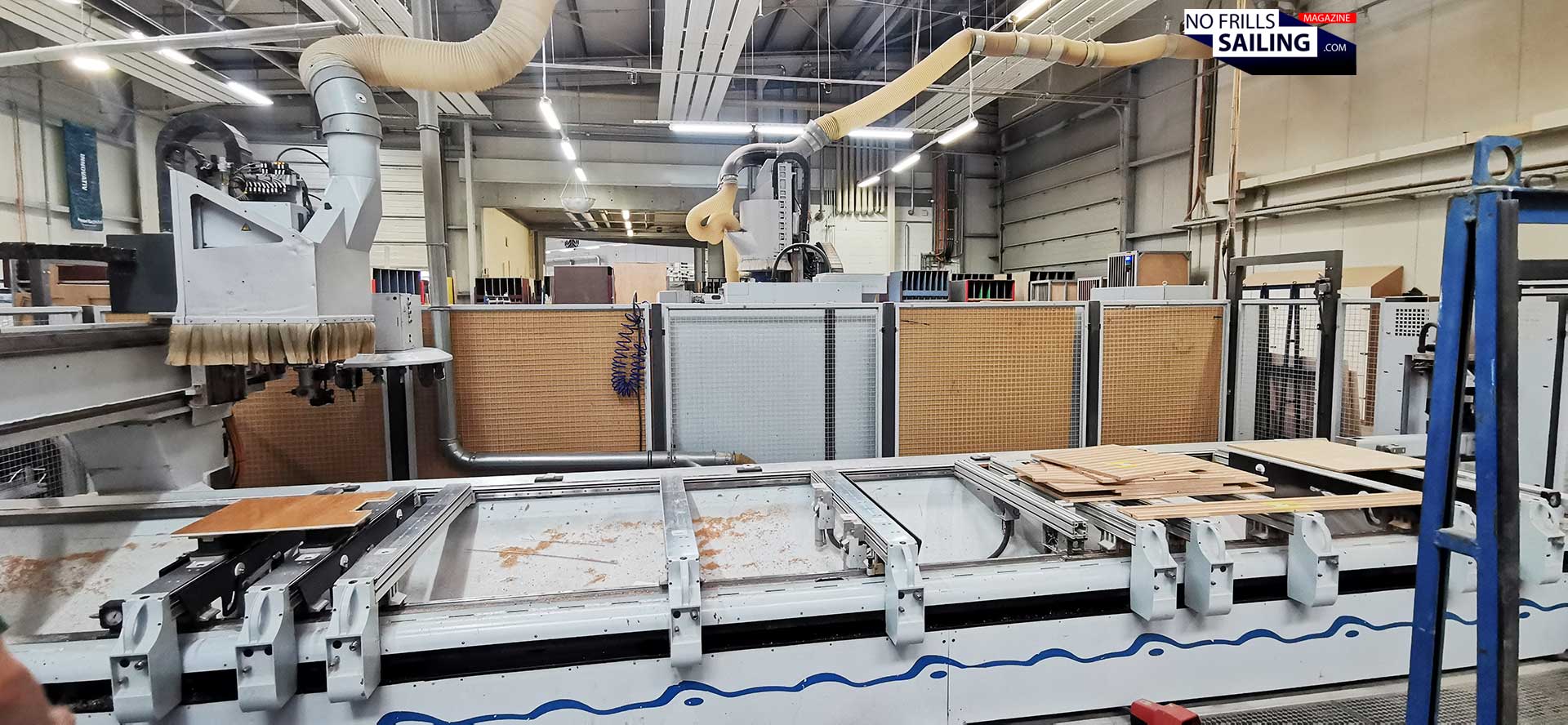
Several CNC-machines are milling, cutting, sanding. Even a state-of-the-art 5-axis robot used to make the really demanding 3D-shapes is humming around a wooden part and will finish delivering a complicated part of the boat that otherwise would have to be made by hand. As for the raw materials, Hanse – like any other shipbuilder – uses marine plywood of different qualities and thicknesses, Alpi veneered surface refinement and as the only “real” timber Cherrywood veneers for their darker boats.
Pre-fabrication of cabin-modules
From the fabrication of the furniture parts we go into another part of the pre-assembly halls where the big “Ikea”-puzzles are brought together by skilled workforce. Maxim tells me that Hanse was among the first production boat companies to adapt modular building techniques from modern cruise shipbuilding into pleasure craft fabrication. Nowadays almost every shipyard, for the big production boat companies all of them, use the modular system – back in the day, this was uncharted territory.
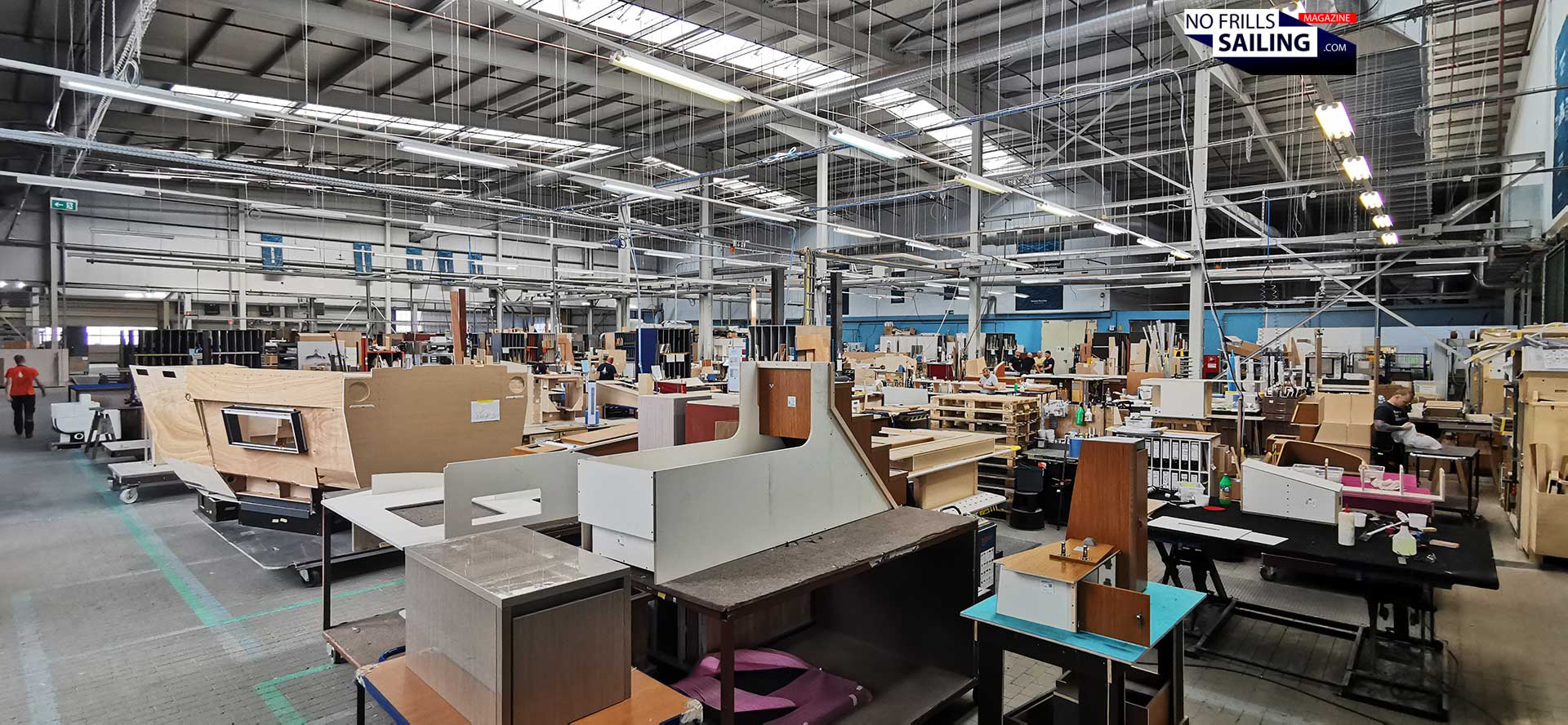
The area is buzzing with people in Hanse-clothing, all of which smile and greet me. Of course, due to personal rights and data privacy, I chose to show pictures here in this article without violating privacy, but make no mistake: These halls aren´t as empty as they seem on these pictures. The hall is divided into several “working islands” specialized to make specific modules.
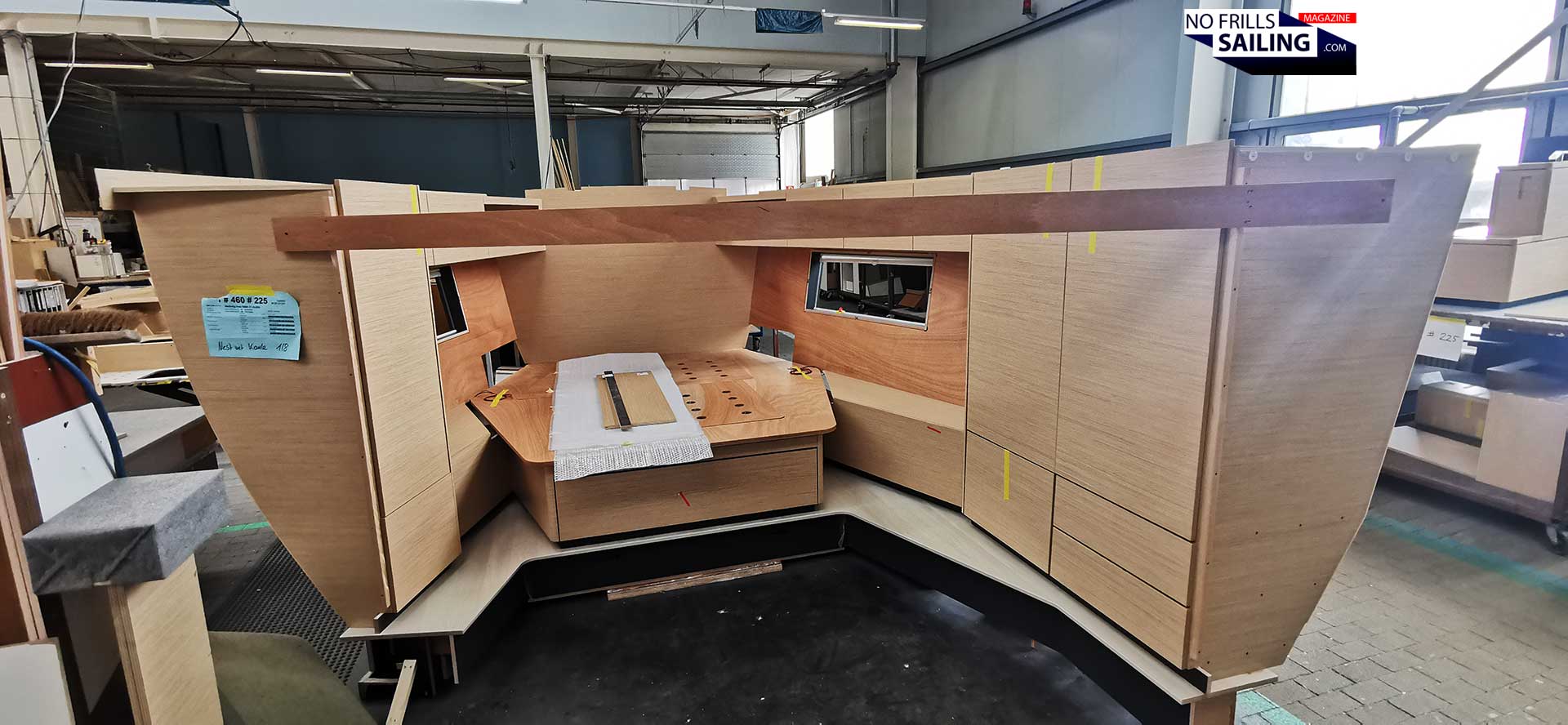
On rolling gauges, bathroom-modules, kitchen modules or, as you can see in the picture above, owner´s cabin modules are pre-fabricated. The whole production is on-demand and just-in-time. A logistical masterpiece: Hull and deck arrive and it is secured that they won´t be parked outside for longer periods of time. Upon entering the assembly line, manufacturing of the parts, delivery of third party equipment (like the Diesel engine for example) and planning of the staff is executed. This owner´s cabin module for example is timed to be pre-assembled right at the time when it is needed to being put aboard – namely, when the corresponding hull arrives at the joinery-fitting location.
Finishing a boat every 4 to 6 hours
This is fascinating – with hundreds of units produced per year, there are several dozens of units at the assembly line in various stages of the fitting process at any time. Thinking about how to organize this beehive of people, literally hundreds of parts and tools needed alone makes my head aching. Maxim tells me that, if production is ramped up at full speed and the shipyard works at maximum capacity, Hanse is able to put out a finished boat every four (!) hours. This is a mind-boggling figure. Right now, as he says, the current output is a boat every six hours, which also is a pretty amazing production speed.
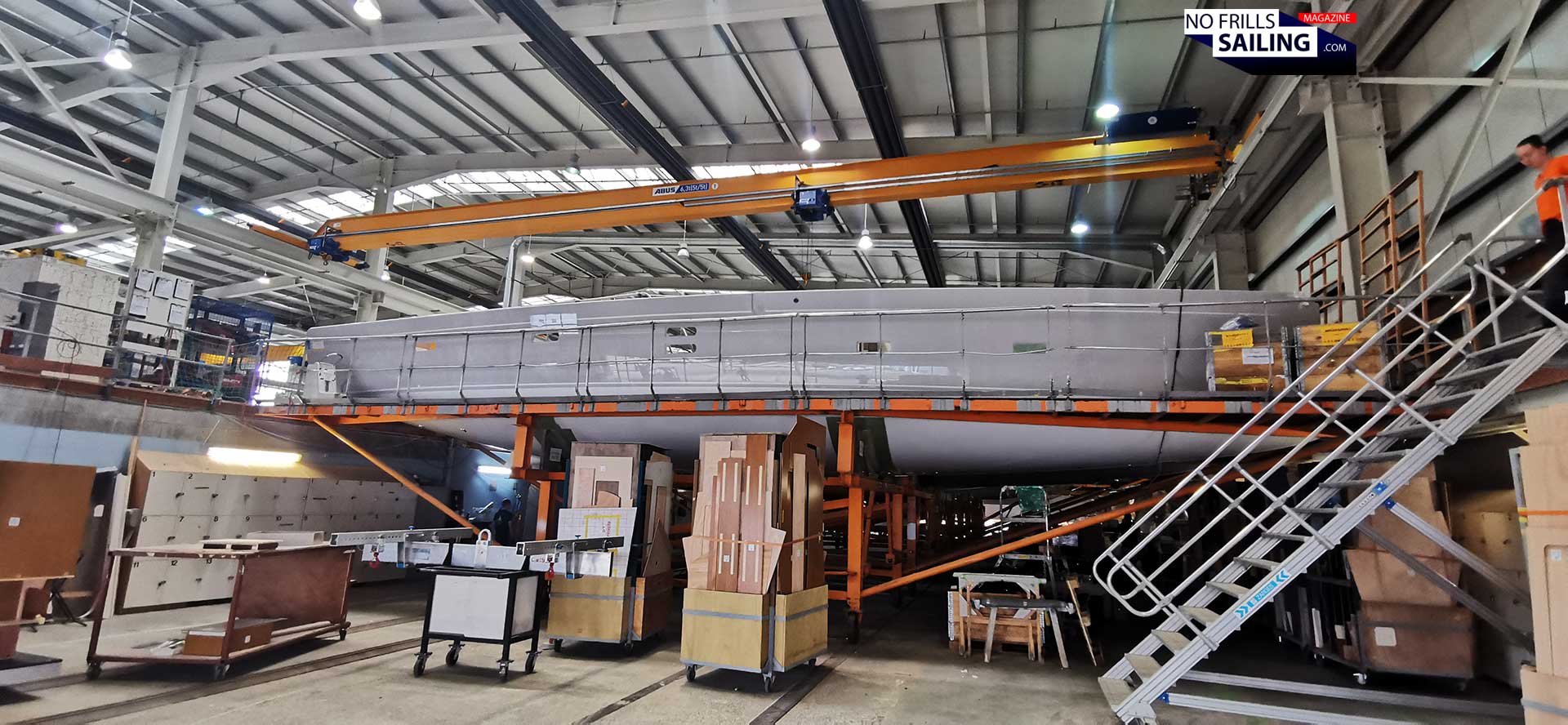
Fitting process itself follows basically the same logic as it is done in all production boat companies: After inner and outer hull are fitted, first bulkheads are installed. Diesel-engine and all related auxiliary machinery is installed, along with tanks (fresh water, fuel and black water), piping and the whole electric system with battery banks, chargers, wires and such.
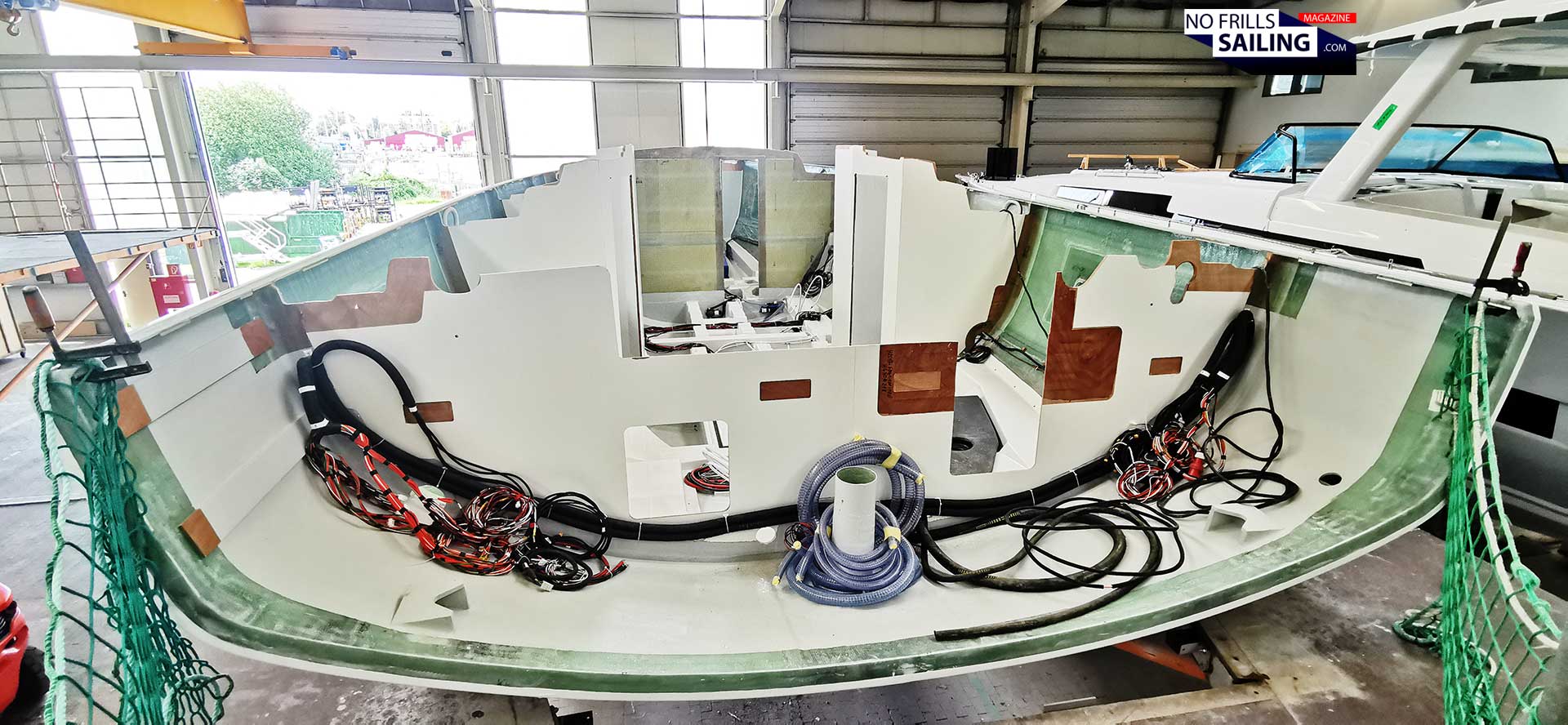
After all of these parts are installed, the boat moves on to the next stations where cabin modules are fitted. Depending on the boat type, a typical cruising yacht has a module for the front cabin, the bathrooms and galley for sure and some also for aft cabins. Along with those modules, mostly, principle electrics like lighting, switches and such are pre-mounted and just need to be connected to the backbone cables and pipes.
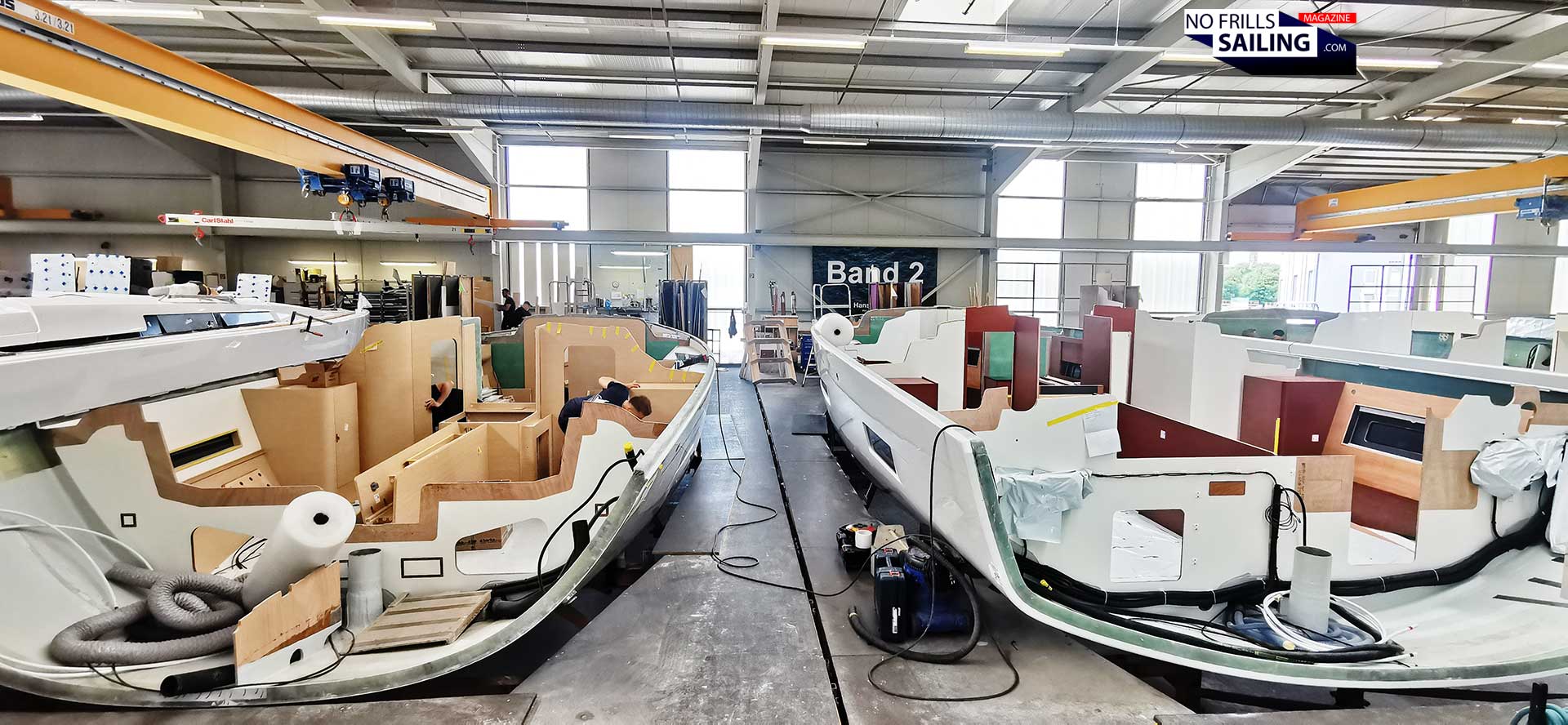
In all this systematic and modular work, that is “industrialized handcraft”, as they put it, with standardized working steps and pretty “simple” ever-repeating procedures, it still looks amazingly confusing. For the untrained eye, it´s just a mess of hundreds of wires and cables, pipes, parts and stuff. So how do they manage all this and keep up the highest possible quality?
The “Quality Gate”-concept
I´ve seen so many shipyards and all of them have systems in place to ensure quality. Hanse´s system is new to me and it is very interesting indeed. They call it “Quality Gate”. The basic production steps, as mentioned above, are subdivided. Between each step such a gate is set up. It is a literal gate, as you may see on the picture below. If a boat is to be crossing that gate – which it is literally by being pulled sideways on her rolling cradle – this means that one crew hands over the yacht to the next. That´s the moment when quality of the boat is thoroughly checked – at a gate. This gate has signals via color codes. They show whether all is right – or if something is wrong.
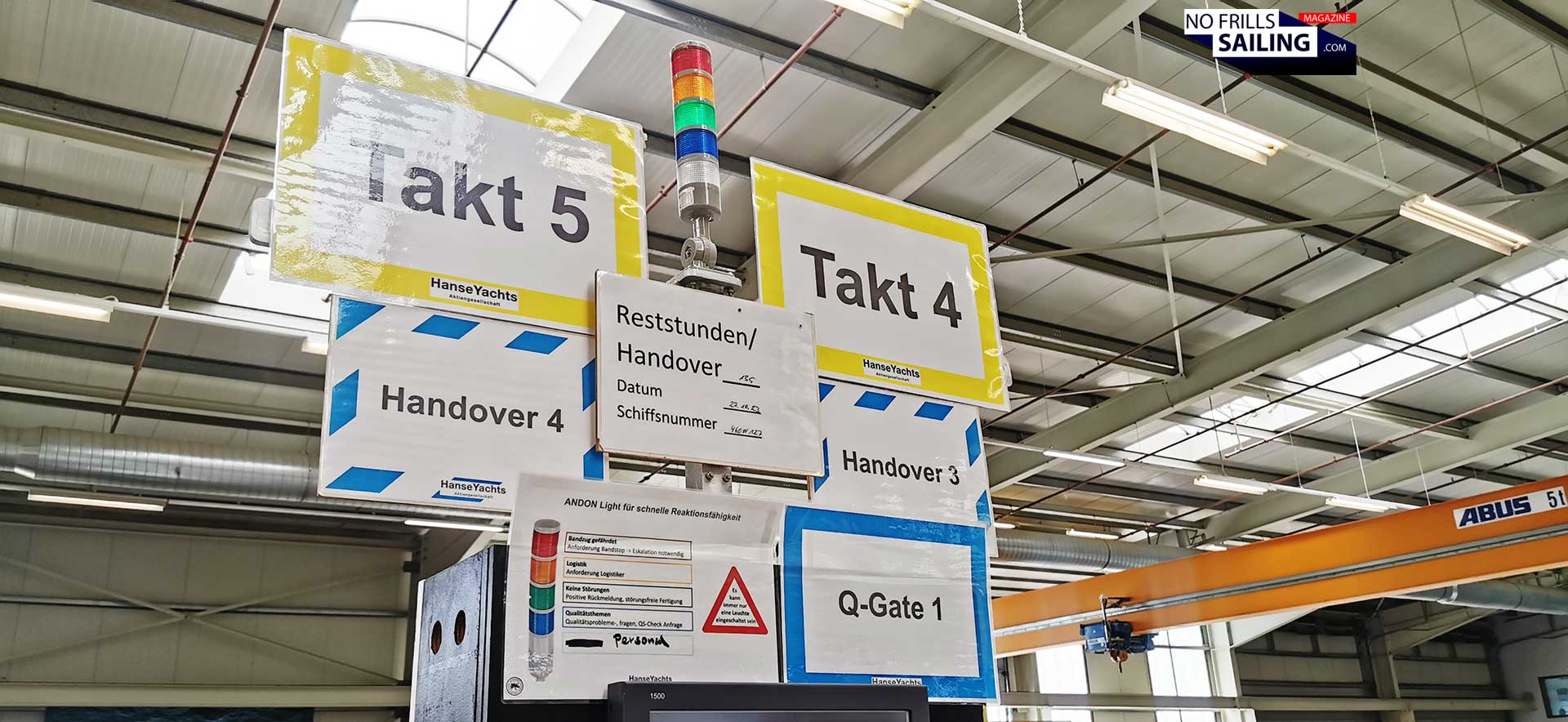
During my visit, all gates had a green light on. Which says “all is good, gate is open”. Reading the color scheme, other lights may be switched on: Yellow for “we need parts – someone from logistics come over!”, blue for “we have a quality issue – QS-manager come over!”, Green means all ok and red, well, of course: “all stop – we have a problem here!” A simple system to signal to all if it is going well according to plan or if somethings wrong. As I said, I only saw green lights.
Yachts made in Germany
Hanse is a German product, a true European product if you count the nearby GRP-manufacturing in Poland. They are proud here, very proud. I mentioned it before: All of the workers greeted me with a smile, I couldn´t spot people mumbling or being grouchy. This tells a lot about work atmosphere and moreover, the team spirit. Another thing I notice is the absolute cleanliness of the whole factory. Just look at this picture:
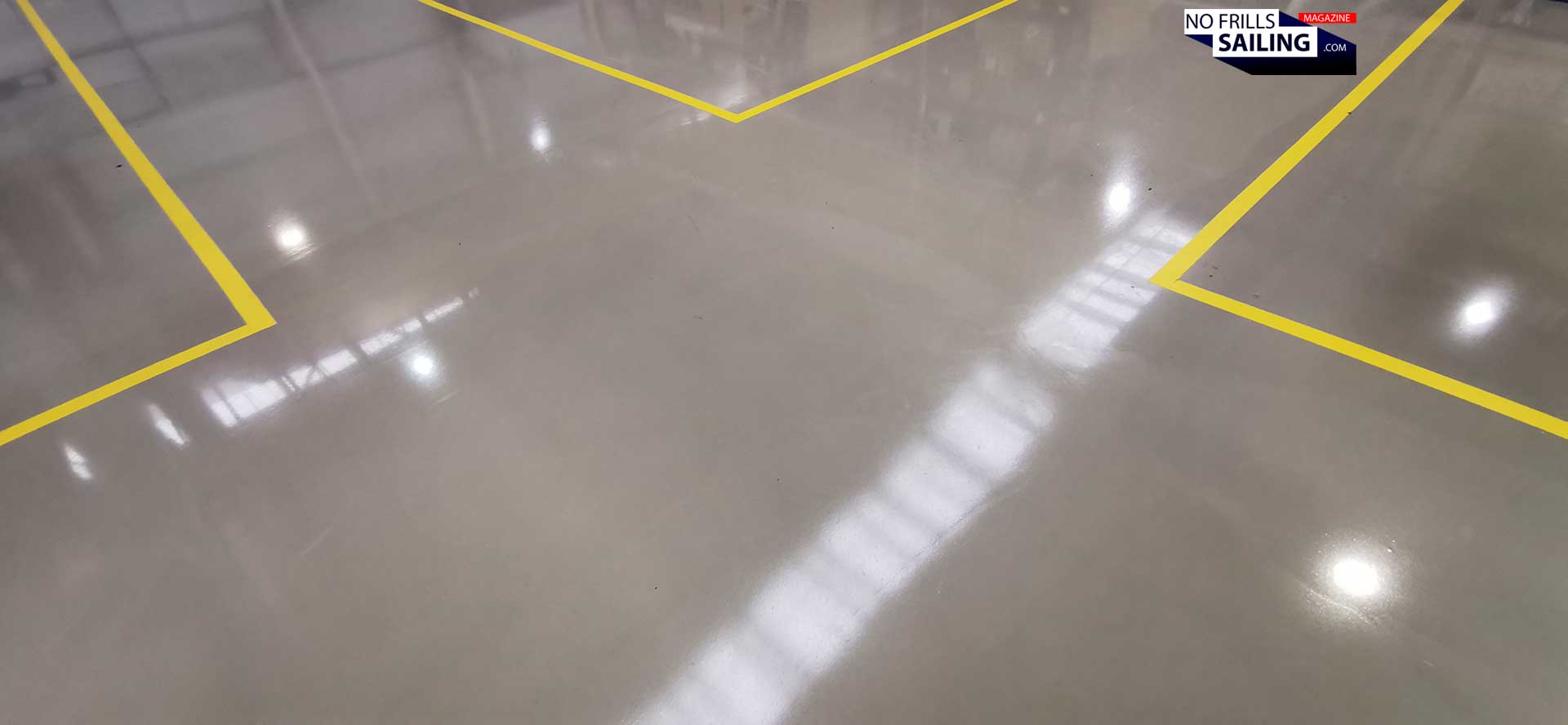
That´s literally a random shot of any floor in any one of the factory-building. I could have taken many more. All the same: It is so clean, you may have lunch on here. I frequently saw little motorized cleaning machines being driven all through the halls, except for the joinery where the CNC-robots are working and lots of offcut dust is accumulating every minute. The whole production area is meticulously kept clean. No parts, no waste, no papers, no screws no nothing. I think this also says a lot.
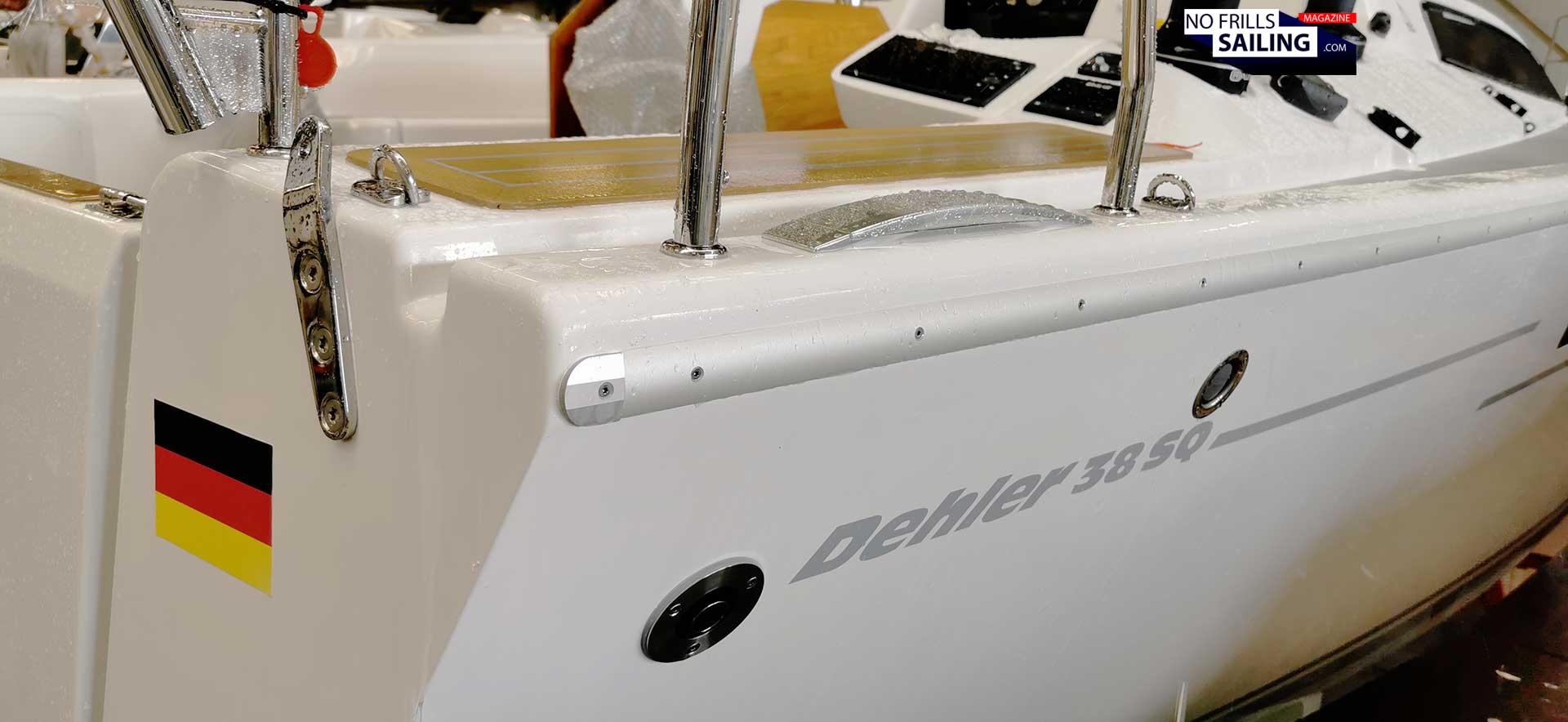
And then there are these little nice details. Flags for example. Each and every single yacht has a sticker at the transom. It marks the nationality of the owner of that particular boat. Of course many German flags, but there are Greek, British, French, Danish and other European countries displayed. There are U.S.-flags and more “exotic” ones: Maxim tells me that for Dehler one of the strongest markets is indeed New Zealand, so I can see some Kiwi flags as well. “We do it so that our staff can really see where the boats are going – and that their work, their craftsmanship is appreciated in so many countries all over the world.” I like this approach very much, much better than the usual dull and unemotional hull number markings.
A new chapter for Hanse sailboats
You may have read my kind of enthusiastic article about the inception of the new Hanse 460 back in late 2022. After many years of not coming up with new boats, Hanse took a bold step into a completely new era. Instead of betting on their long partnership with Judel/Vrolijk for this project they changed to renown French design bureau Berret-Racoupeau. A new era, a well-recognized audacious step. I was exhilarated and still consider the Hanse 460 one of the most attractive production boat cruisers in that class. Pretty tough competition for the Bavaria C46 where I liked the well-made interior pretty much and also the Oceanis 46.1. Certainly a hard choice for future boat owners in this class!
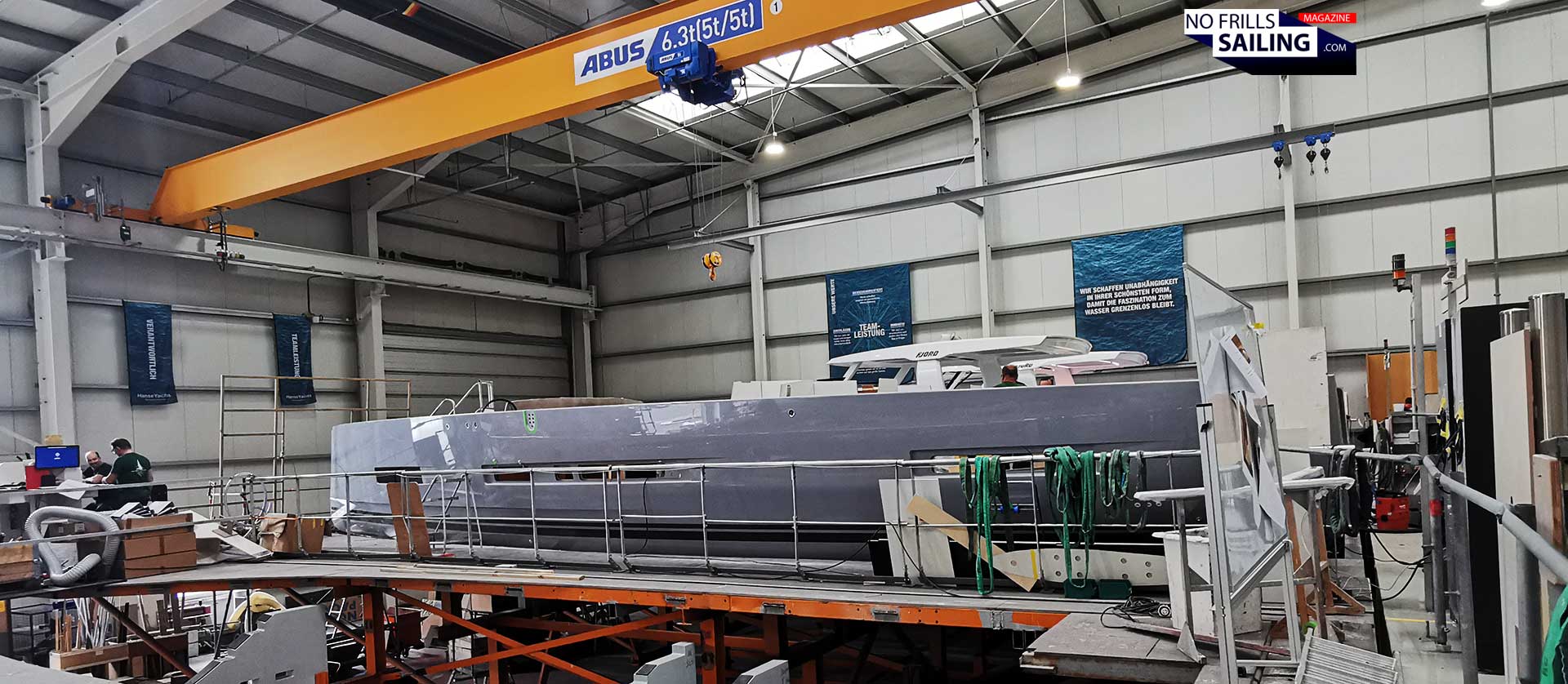
Berret-Recoupeau moves on to step by step, boat by boat renew the current line of yachts. The new Hanse 410 which I´ve seen in Duesseldorf this year (read the walkthrough article here) and the large 510 (walkthrough upcoming) are already available, they recently launched the new Hanse 360, which I am keen to see as well soon. Now, the next one is coming. Maxim shows me a big boat in the distance and smiled: “If you want an exclusive teaser: Here´s our brand new Hanse 60-footer … prototype.” Oh, that´s interesting …
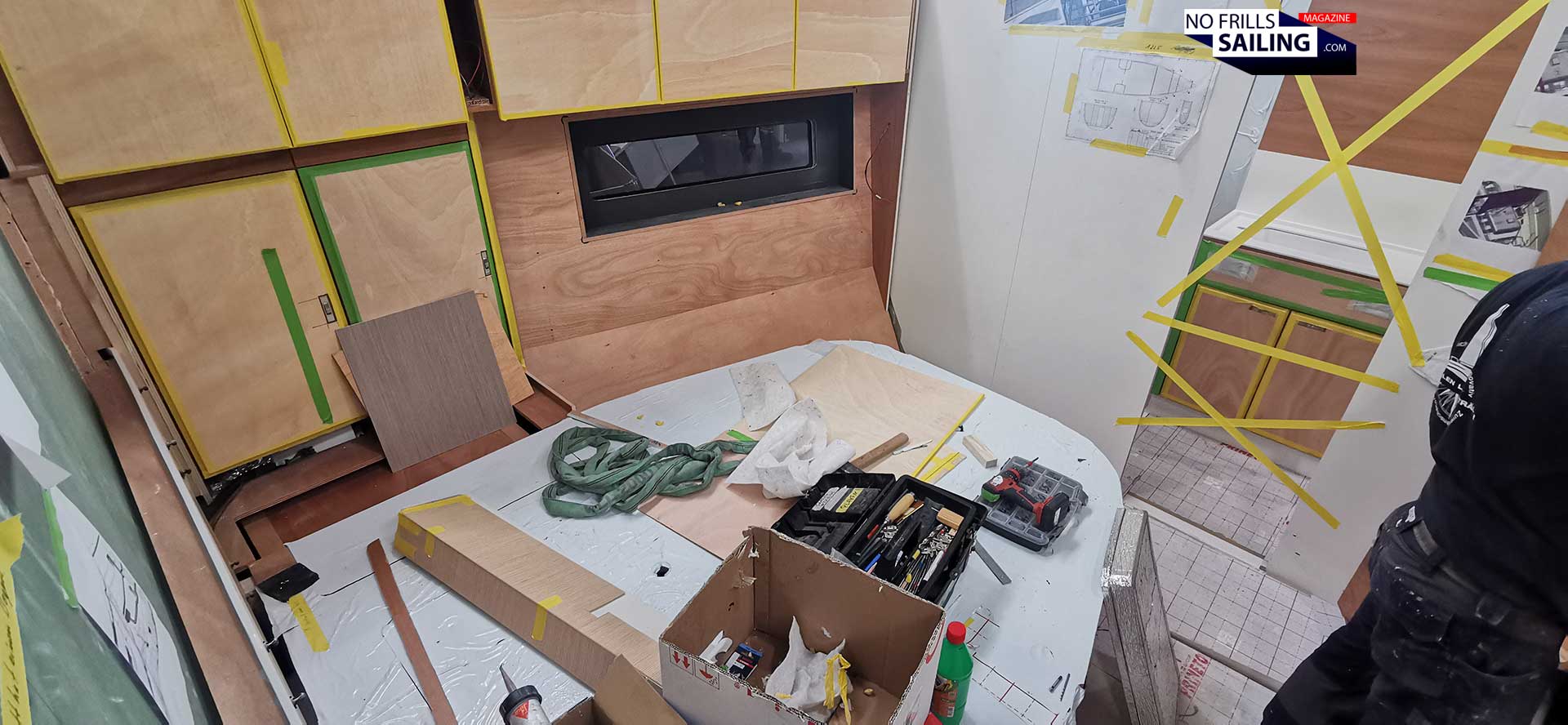
I am not allowed to show the full boat or more details any than this slightly offset island bed in the owner´s cabin with a dedicated bathroom to the front (separating the owners from the skipper cabin), but I can tell you that this yacht will certainly be one of the highlights for upcoming Cannes Yachting Festival in September. I really congratulate Hanse for taking these ambitious steps: Employing a French designer and coming up with beautiful new designs by also retaining the distinct Hanse-style which still makes a Hanse easily distinguishable and identifiable. Something that Bavaria for example maybe did a bit too over-ambitious with their new boats designed by Cossutti, taking kind of too “revolutionary” steps design-wise, repelling some of the loyal customer base.
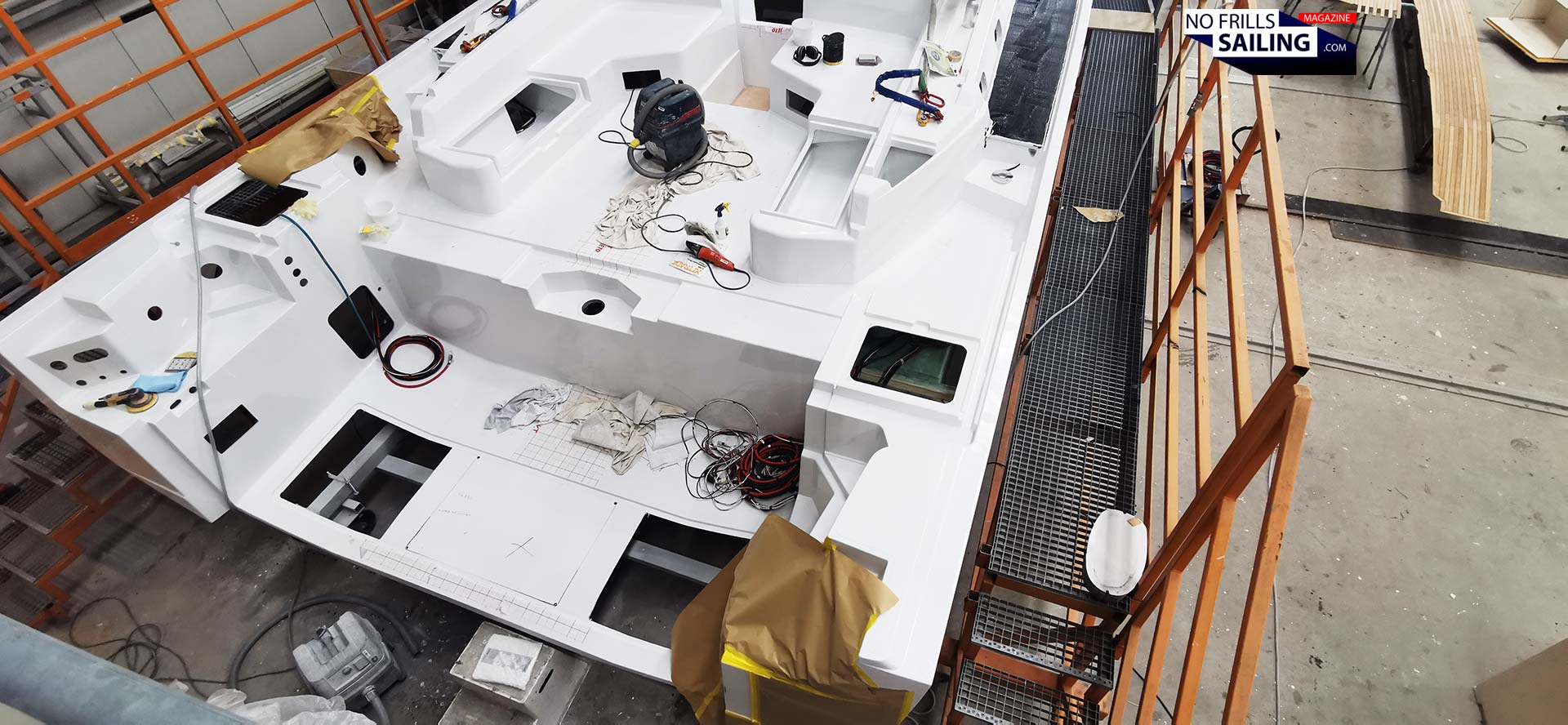
Next to the large hull the deck of the new 60 is pre-assembled. Having just delivered a flagship myself, the Oceanis Yacht 60 to my clients, I notice the particularly interesting detail of the dinghy garage. In this case, the dinghy is stored transverse to the boat´s longitudinal axis. A pivoting arm mounted to the right (I will show in a later article more details) gets the boat in and out. This system allows to save internal volume for the aft cabins – a detail worth looking at later in the finished boat.
A visit worthwhile
My visit here was definitely worth it! I don´t know why I never dared to ask for a tour here in Greifswald before, it´s just “around the corner” from where I live. And there is still so much more to see: As this shipyard is located at the Baltic Sea, clients can literally cast off from the shipyard´s own waterfront. Which is a plus for all North-European clients of course. Making a resume, I´d say that I am surprised about the cleanliness of this whole operation and the kind, friendly and open atmosphere among the people working here – from workers to the administrative staff to Maxim, Vice President of this company. The production process is well-executed and one can clearly see how much effort is put into raising efficiency and effectiveness in every step.
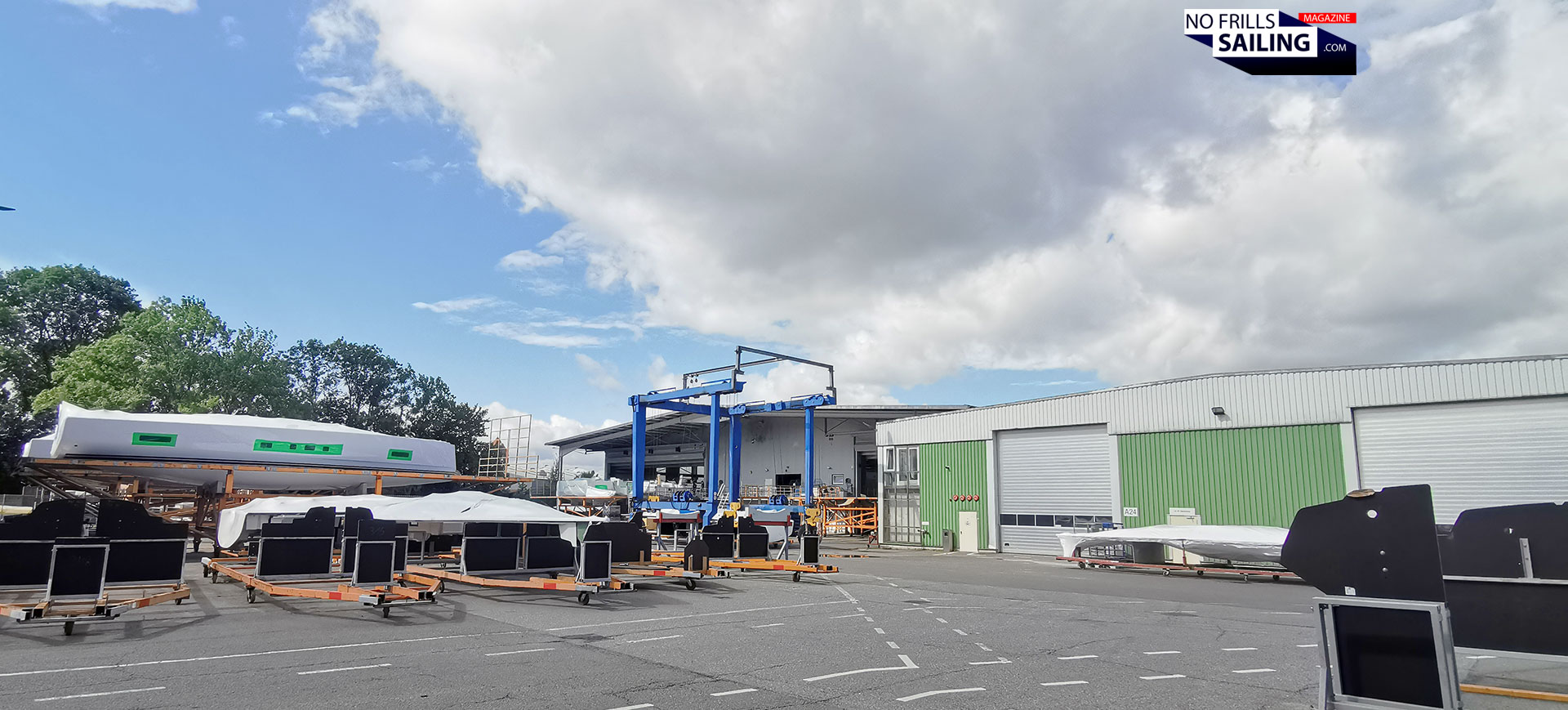
I leave with a pretty positive impression. Hanse Yachts here in Greifswald is certainly not a cheap producing all-out margin focused mass-producer. I did not have the impression that the operation is run on the limits. As every of the “Big 5” has their own specialty and unique character, I´d say the Greifswaldian people try to implement a steady, clean, thoroughly planned and well executed production to make good sailing cruising yachts and boats in general for their clients. They are certainly proud of their work – and I´d say, right so!
Thanks, Maxim, for taking your precious time to show me around.
You may also read these familiar articles:
The “Paukenschlag”-Boat: Meet the new Hanse 460
Exclusive first pictures of the new Hanse 460 in the water
40 feet contrasts – walkthrough in the new Hanse 410 at Duesseldorf