I thought, since I am driving to the shipyard every two weeks or so anyway, to open up a new hashtag for the Omega 42-project which is called #buildingreport. This will be part one. The shipyard is located in the Northern part of Mecklenburg-Pommerania at the lake Mueritz, just a 2 hour drive from Luebeck and one hour away from the Baltic shores. I arrived quite early in the morning just after the guys had have their coffee, about to start working today´s list.
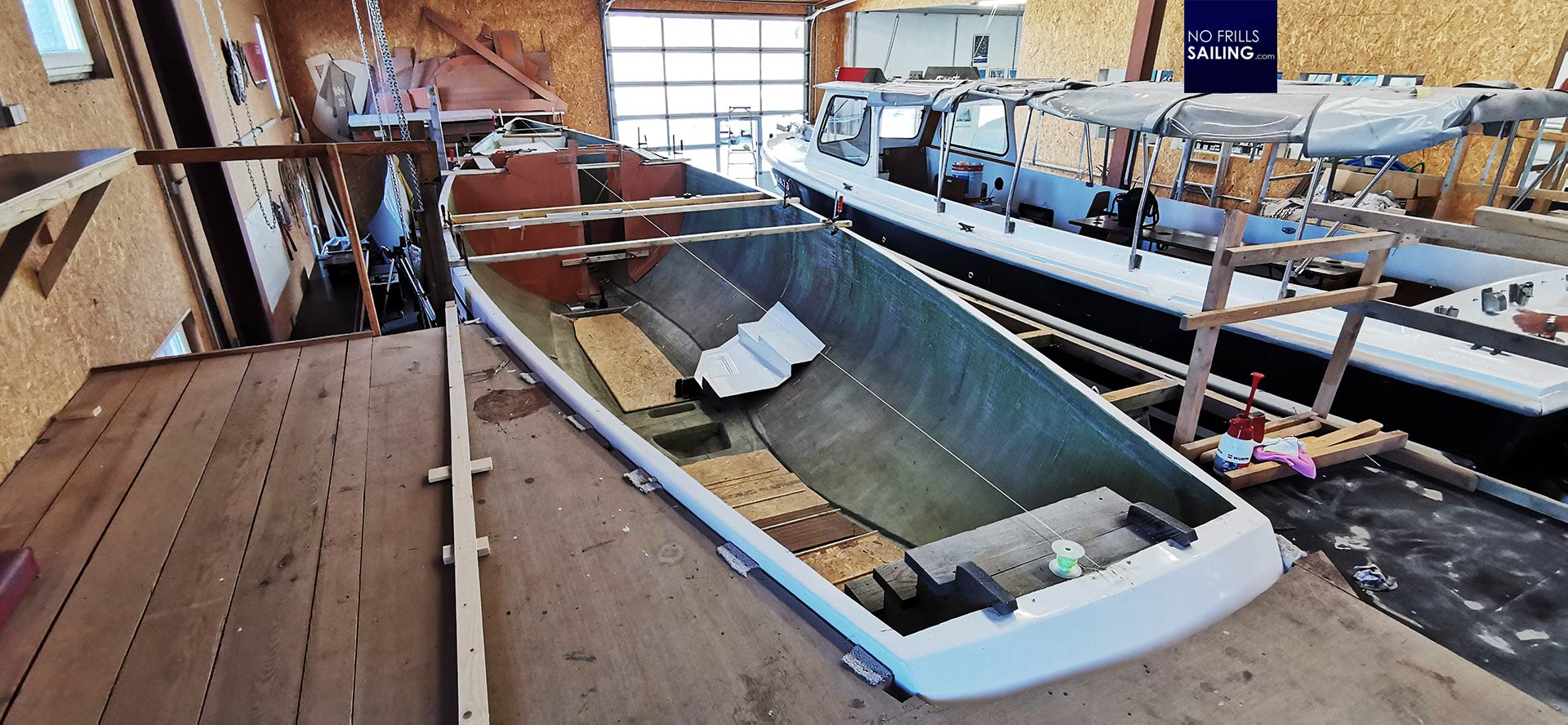
Since building commenced a few weeks ago, looking superficially, nothing really big happened, you might think. But this is not the case: On the contrary: setting up the boat on its building lot is quite a job. A job that literally calls for the skills and patience of a watchmaker. I´ve been to a lot of shipyards but never really paid much attention to this detail, which is a shame. The guys had cleaned the boat after five years on the open air storage and one of the apprentices immediately took a buffing machine and started to polish the Gelcoat of the hull. I went on the building rack to get a better overview.
De-bending the hull
For the past few days and certainly for some days more the chief boatbuilder has the task to de-bend the hull. Jonas, that´s the name of the skilled craftsman, explains to me that no hull comes out of a mold the same. Depending on drying time, temperature and other factors, like how the two halves of the mold are put together, each hull has a certain aberration. Laterally, longitudinally and in relation to the symmetry.
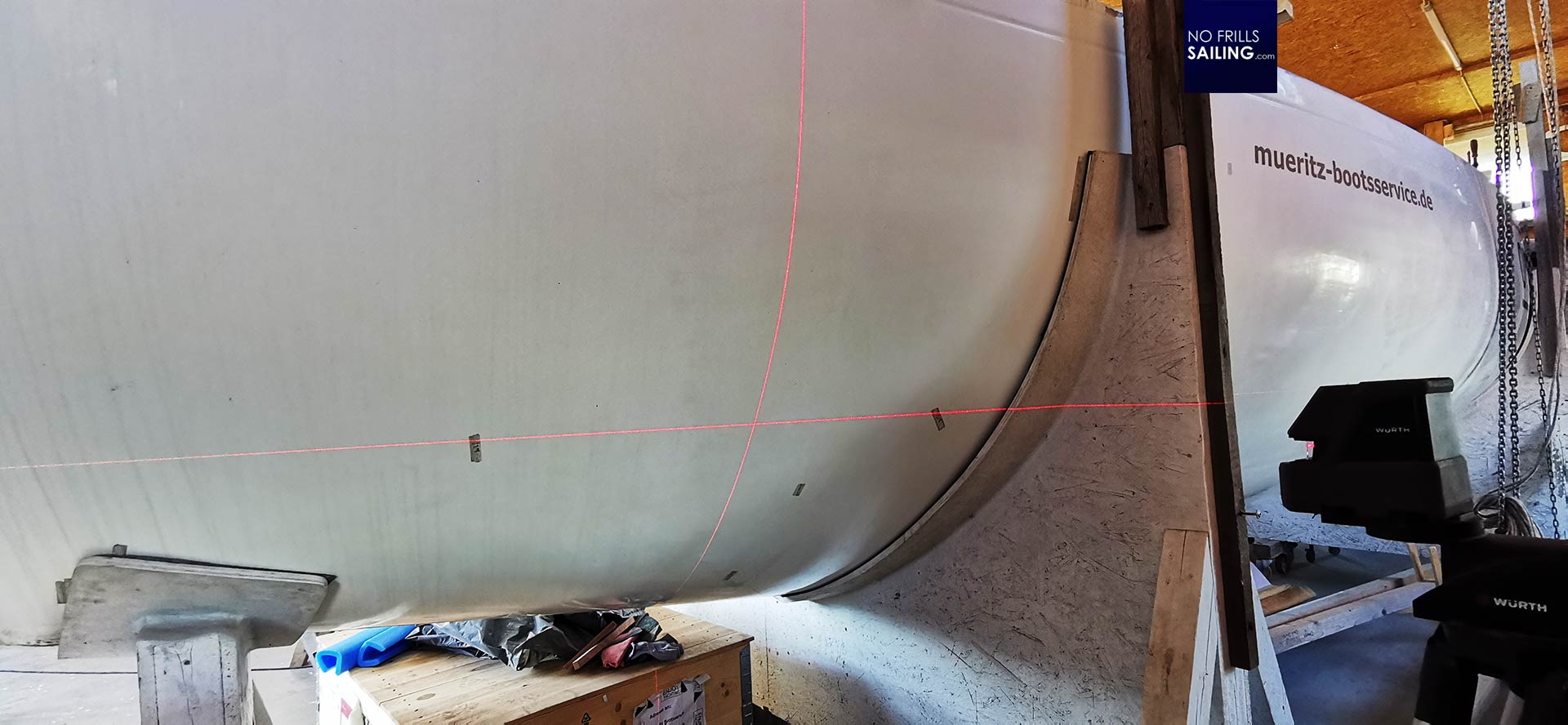
Laser-levels are positioned around the hull, adjusted to display the thin red line exactly where the waterline of the hull should be. Stickers on the hull, set by the Swedish shipyard that had produced it some five years ago, mark the approximate waterline, judging by the laser, there are indeed divergences. For a boat that long, Jonas says, even a deviation by a few millimeters can produce quite an ugly outcome.
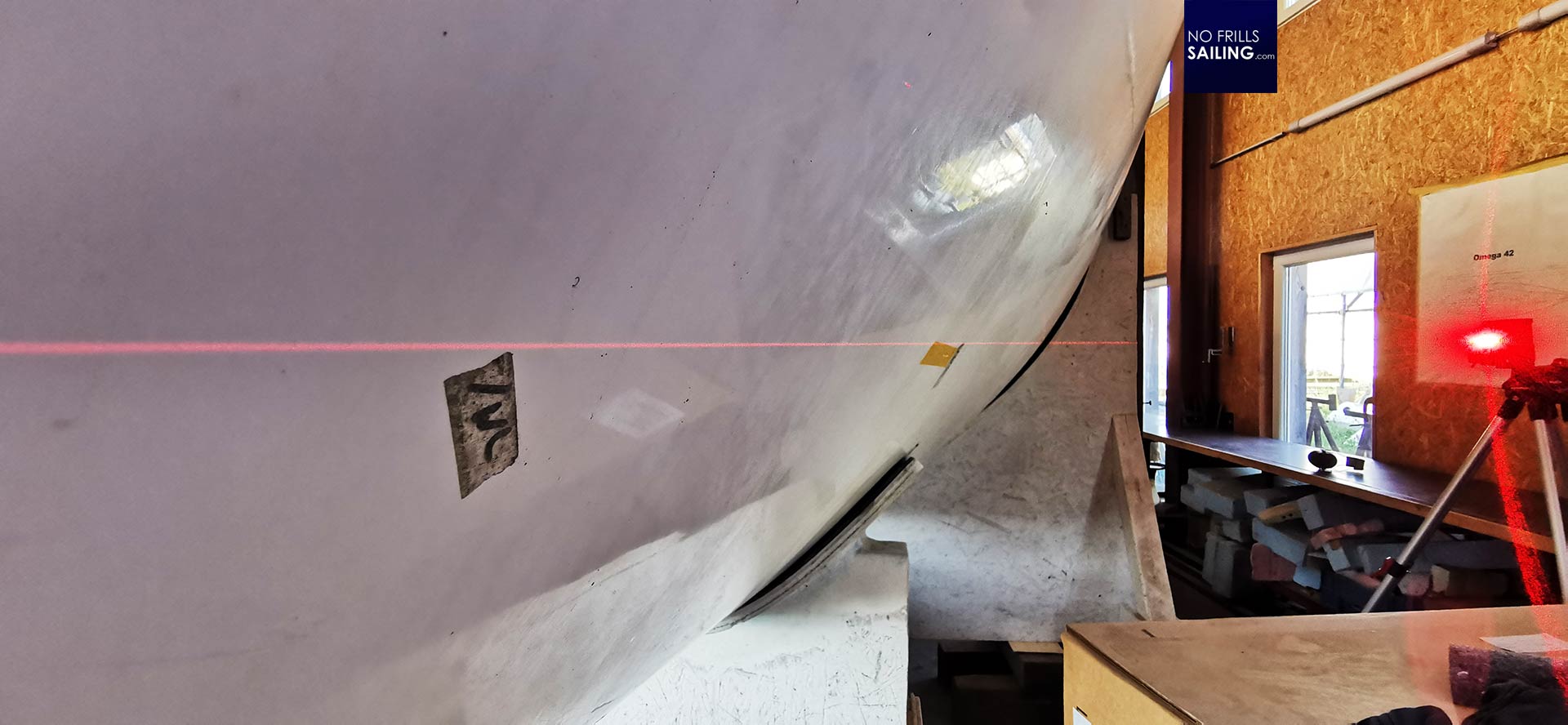
Ignoring those imperfections don´t make a boat sink, but a longitudinal bend, for example, can make it appearing heeled all the time, even in her berth. A boat that is not leveled sends uneven strain into her keel and could even make her sail constantly as if the rudders were making her turn. Also, when a hull is not leveled exactly, the joints with the deck will come under stress, producing a constant pressure. That is why the team around Jonas is putting so much efforts into this first step: Meter by meter.
Trimming the imperfections
Standing on the side of the boat and looking down into her empty hull, I notice wooden slaths bolted to her hull. The slaths are connected either by screws or by big screw clamps. I understand: piece by piece and meter by meter Jonas can adjust the hull – either by widening the hull´s connection to the slath or by shortening it.
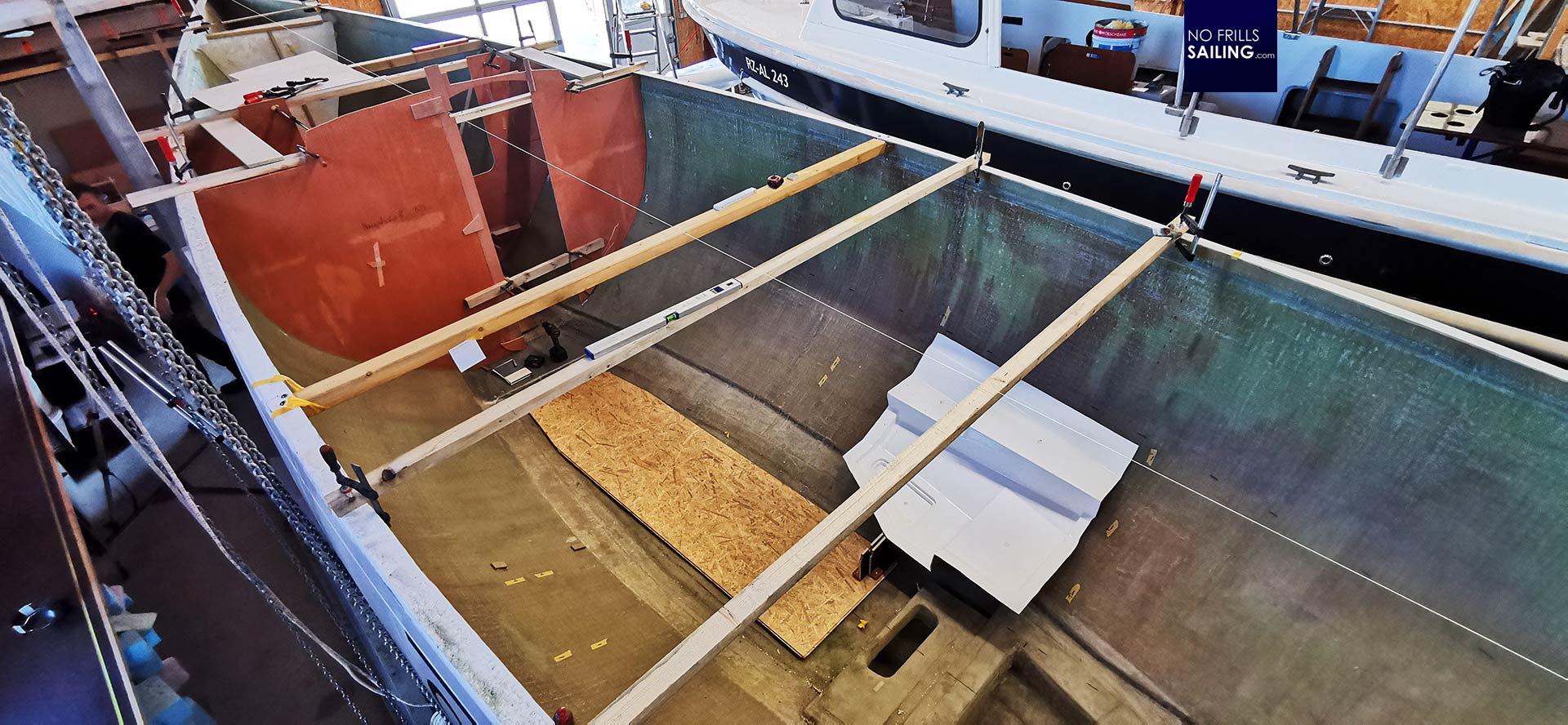
In this, with each change, he climbs out of the hull, switches on the laser levels and checks for the outcome. From bow to stern, step by step, the boat will be then put into a perfect level. The changes are subtle and the efforts to achieve them are big: For each change someone must climb into the boat, adjust the connection points in the slaths, climb out, check, control and repeat. Five slaths have already been set – at least five more will have to be set before it´s done.
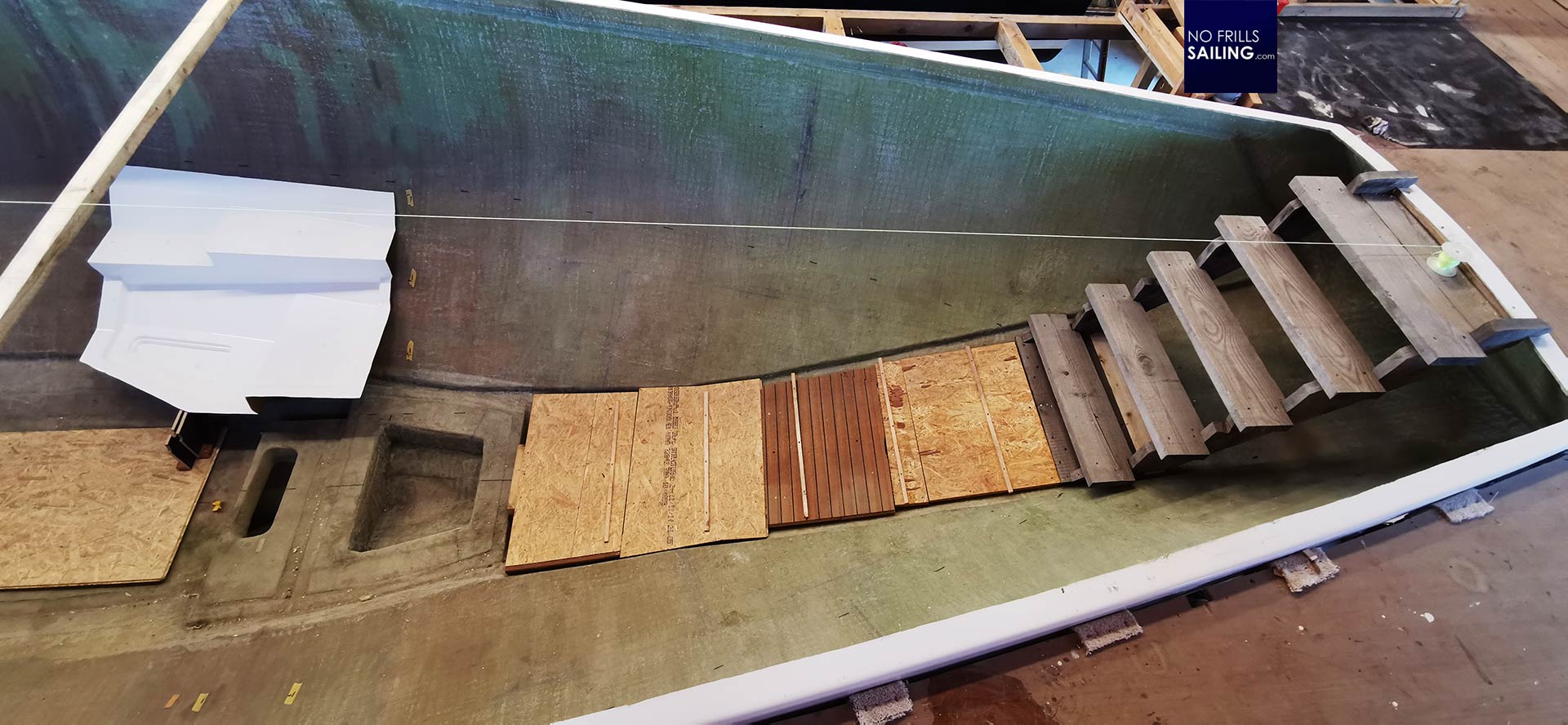
But it is not just the de-bending or checking of the perfect curvature of the boat´s cross section to achieve symmetry, it´s also the longitudinal axis. Instead of a laser, Jonas uses a good old fluorescent thick thread. The cord is attached to screws at the bow´s tip and the stern´s exact mid-point. Tautly tight, the guys can measure the distance from the cord to either side on the slaths to check symmetry. I am puzzled by the calm and strictly controlled, steady but progressive work efforts here. Jonas says that for a boat like the Omega 42, any imperfection in the hull would later be felt in poor sailing qualities.
First fittings
Alongside the leveling and de-bending of the hull, the guys already have fitted the first bulkheads. Just the working mockups to check the correct size and position, nevertheless, seeing the boat partially partitioned is exciting. I climb inside over the roughly timbered stairway at the stern and walk down to where later the saloon will be placed. A big white GRP part is drawing in my attention.
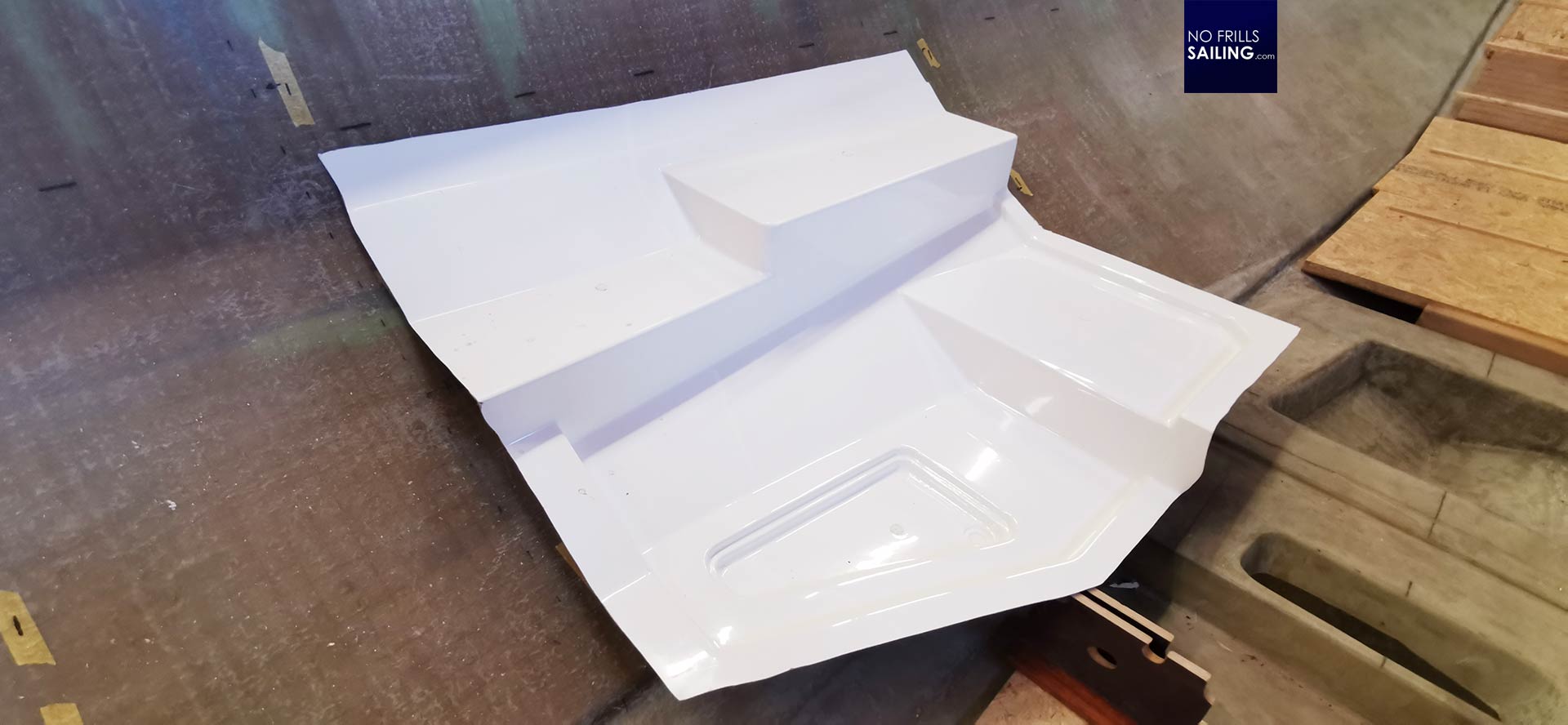
This is one of the few molded GRP parts made in Sweden as well. That particular part is the floor of the later bathroom. I can clearly see the raised base for mounting the toilet (which I also delivered on that day) and the collecting pond for draining the shower water. (Apart from the fact that my boat won´t have a shower). But I will surely fit one of our great CNC-milled Teak gratings which I fancy so much.
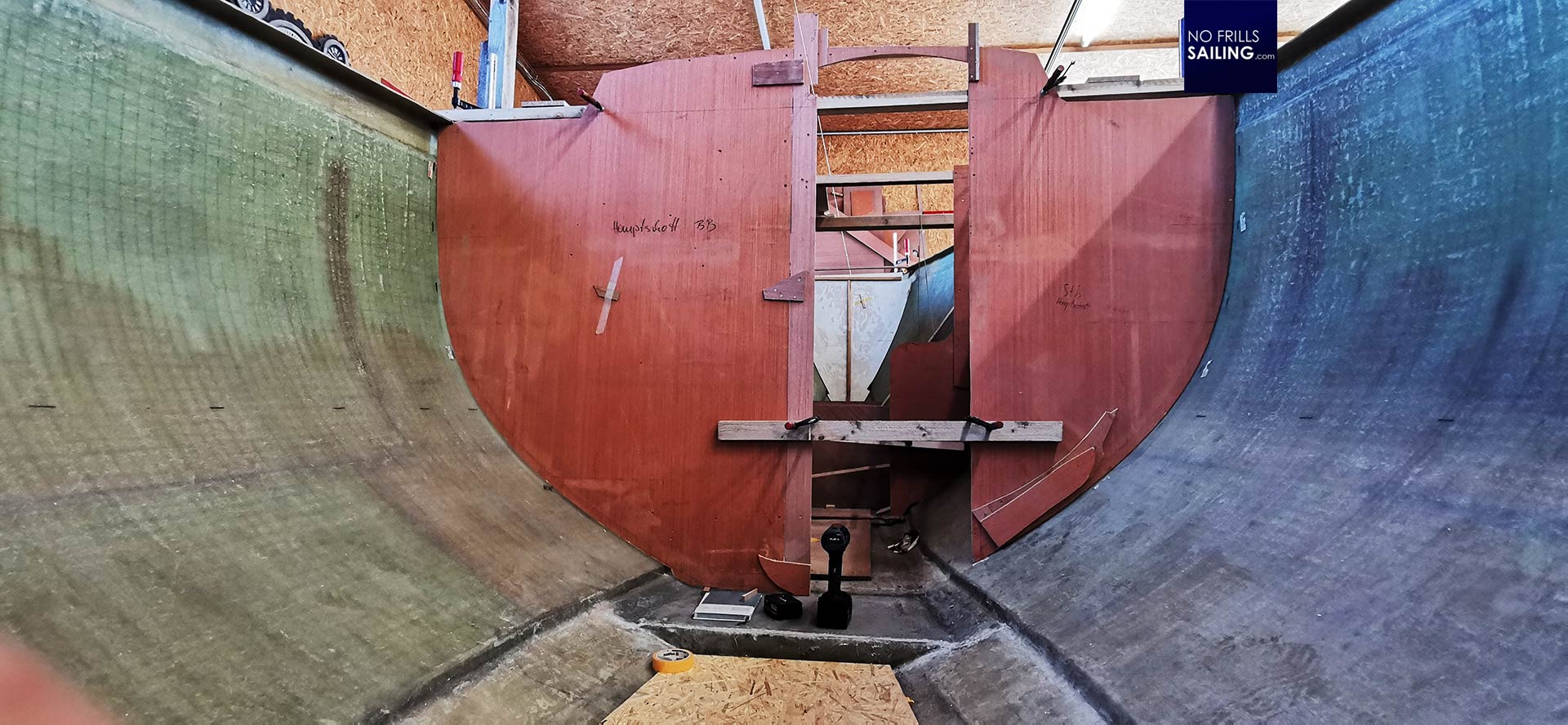
I walk down furthermore through the saloon, over the massive base for the stepped mast and end at the main front bulkhead. It´s a mockup, nevertheless, one that coveys a feeling how the boat will look like in a few months. There is the door that won´t receive an actual door and a nice wall that could feature the classic barographic instruments or a nice decorative element, like for example my Oyster half model or something else.
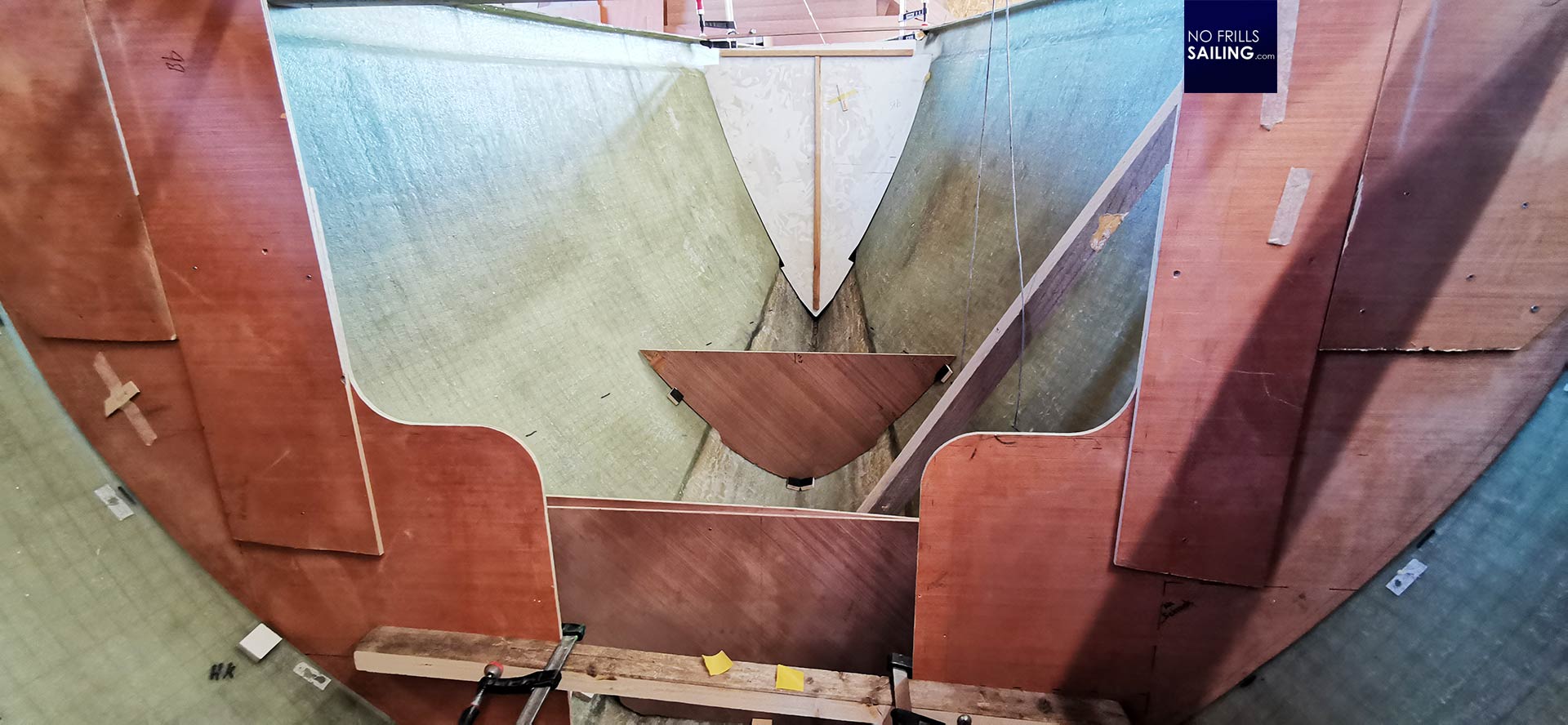
I also take a peek into what will become the fore cabin of my boat with the long V-berths where I will later hopefully find a good night´s sleep. Nothing really exciting to see here, I admit, but a first step for sure. This all will be much more revealing when the stern bulkheads are set and the walls of the bathroom are fitted so that the boat reveals what we have principally planned to be her layout.
Every day brings something new
Sitting on one of the bottom mounted slaths I look abaft. The whole length of the boat is just breathtaking. A view I suck in and try to memorize because this is something I won´t get to see at least in this boat never again. The gracious lines of Peter Norlin revealed in her spacious inside: The sleek, hydrodynamic shape of the ship, especially the huge volume in her rear end that will be forever hidden when engine room and pilot berth cabin are fitted.
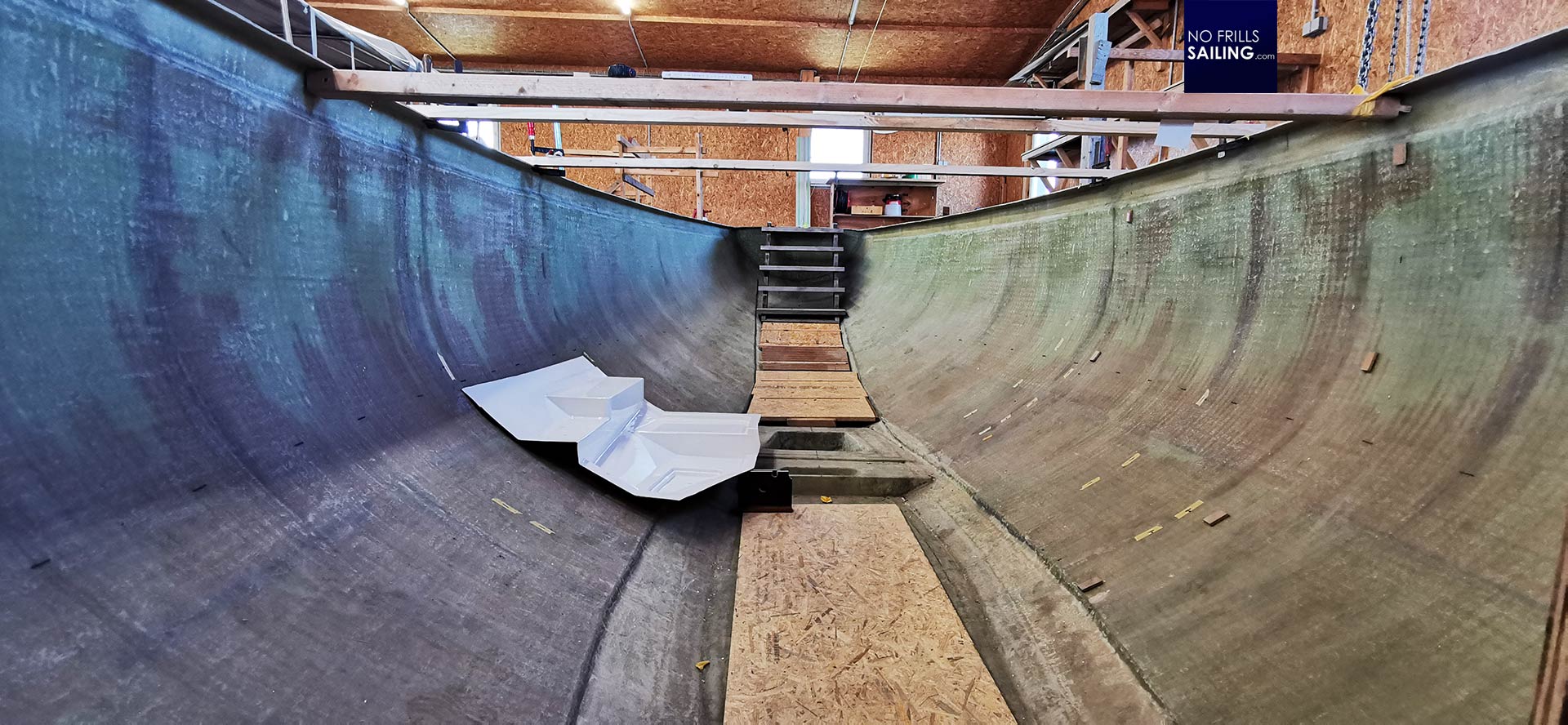
Every day now will bring something new. Jonas tells me, that once the boat´s leveling will be finished, the works in the bulkheads and furniture will start. More and more parts will be manufactured, fitted, customized and adjusted. More and more the cabins will take shape. With the engine standing by the next big step will also be the mounting of the Diesel, fuel tank, batteries and the piping will commence. Lots of milestones to be reached in the coming weeks.
A Speciality: „Norlin White” Gelcoat
Just as I was about to say goodbye to the crew, Jonas invites me to follow him into the storage room. Something special arrived, he teases. The room contains all of the chemical stuff needed in a shipyard: Paint, Acetone, thinners and such. He kneels down and points to a 10 liter-metal can (or was it a 20 liter mini barrel?) by Voss Chemie, a big German chemical producer: “This is a custom blend Gelcoat especially for your boat”, he says proudly and shows a GRP test drilling disc. Apparently, the Swedish shipyard back then in 2018 has used a Gelcoat that nobody knows of here in Germany. “It came with a handwritten note, but we couldn´t decipher it. No standard RAL would fit. So we had to make our own”, Jonas smiles.
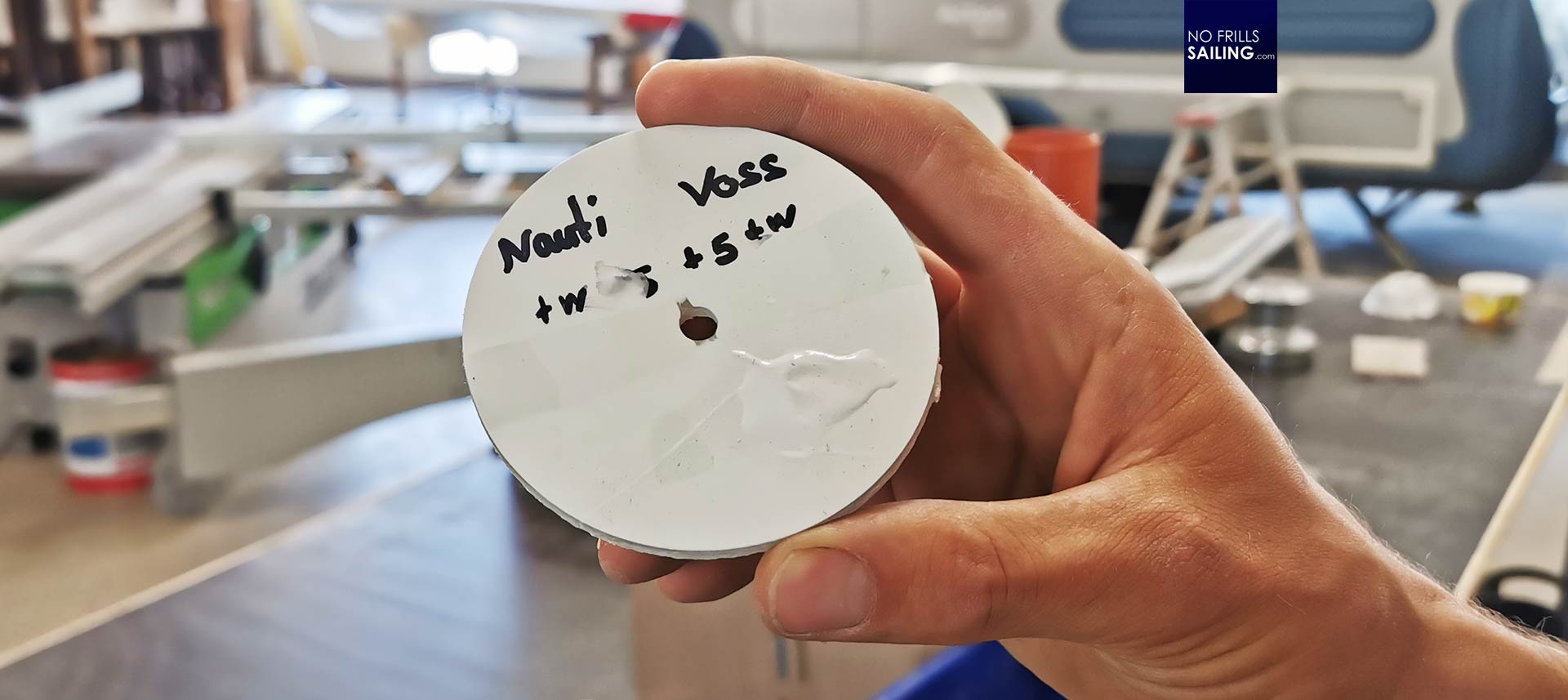
So here we are, how lovely – and how much of a dedication this reveals. These guys don´t give in or satisfy themselves with standard. They run the extra mile and strive for the perfect outcome. Just as they meticulously adjust the 13 meter hull inch by inch to achieve a perfect leveled boat, they had a company making a perfectly matching Gelcoat. Driving home to Luebeck again I have this wonderfully warm feeling of satisfaction in my belly. This is a feeling of deep trust: These guys really take pride in their work. It was the best decision to invest in this project!
You may like to read the following articles too:
In the yards: Dufour Yachts, Beneteau, RM-Yachts and Allures/Garcia
More yard visits: Seascape, X-Yachts, Berckemeyer Yachts and MAT of Turkey
All Omega 42-articles by clicking on the hashtag #omega42